Определение показателя трения в процессе прямого прессования проволочного и пруткового припоя ПОИН-52
Автор: Радионова Людмила Владимировна, Фаизов Сергей Радиевич, Громов Дмитрий Владимирович, Ердаков Иван Николаевич, Сиверин Олег Олегович
Журнал: Вестник Южно-Уральского государственного университета. Серия: Металлургия @vestnik-susu-metallurgy
Рубрика: Обработка металлов давлением. Технологии и машины обработки давлением
Статья в выпуске: 3 т.21, 2021 года.
Бесплатный доступ
В любом процессе обработки металлов давлением имеет место внешнее трение на контакте инструмента и обрабатываемого материала. Под влиянием сил трения возрастает усилие деформации, разогревается и интенсивно изнашивается инструмент, увеличивается неравномерность деформации и, как следствие, возникает разнородность микроструктуры обрабатываемого металла, возникают растягивающие напряжения, которые иногда приводят к нарушению сплошности изделия. В настоящей работе исследуется влияние контактного трения на процесс прямого прессования прутков и проволоки из сплава ПОИн-52. С помощью математического моделирования исследовано влияние коэффициента трения на усилие в процессе прессования прутков Ø8,0 и 15,0 мм, а также проволоки Ø2,0 мм. Показано, что с увеличением коэффициента трения на преодоление силы трения скольжения на контактной поверхности обрабатываемого металла с контейнером и с матрицей тратится до 60 % усилия, необходимого для прессования исследуемого сплава. В ходе экспериментальных исследований показано, что применение смазочных материалов, а именно графитовой (графит - С) и молибденовой (дисульфид молибдена - MoS2) смазки, позволяет снизить коэффициент трения более чем в 10 раз. С определенной долей допущения можно говорить о том, что при прессовании припоя ПОИн-52 с использованием стального контейнера без применения смазки коэффициент трения равен 0,5, а при применении графитовой или молибденовой смазки коэффициент трения будет принимать значения, близкие к 0,05. С помощью результатов экспериментальных исследований путем подбора были определены показатели трения по законам Кулона, Зибеля и Леванова, которые могут быть применены для компьютерного моделирования в пакете Qform процесса прямого прессования припоя ПОИн-52 с использованием стального контейнера без применения смазки и с применением графитовой и молибденовой смазки. Учет достоверной величины показателя трения при компьютерном моделировании позволит существенно повысить точность расчетов.
Прямое прессование, коэффициент трения, припой, проволока, пруток, усилие прессования, сила трения
Короткий адрес: https://sciup.org/147235291
IDR: 147235291 | DOI: 10.14529/met210307
Текст научной статьи Определение показателя трения в процессе прямого прессования проволочного и пруткового припоя ПОИН-52
В любом процессе обработки металлов давлением, будь это прокатка, волочение или прессование, смещаемый объем деформируемого тела стремится к некоторому перемещению по поверхности инструмента. При этом возникают силы трения, затрудняющие это перемещение. Контактное или внешнее трение сказывается на энергосиловых параметрах процессов [1–5]. Под влиянием сил трения в ряде случаев усилие деформации возрастает в несколько раз по сравнению с тем усилием, которое обусловлено истинным сопротивлением металла деформации. Кроме того, действие сил трения приводит к неравномерной деформации металла, что является причиной разнородности его структуры, возникновению растягивающих напряжений, которые иногда приводят к нарушению сплошности изделия [6–8]. От характера и величины сил трения зависит степень износа инструмента и качество поверхности изделия [9–11].
В прессовании для снижения влияния контактного трения на энергосиловые параметры процесса применяется метод обратного прессования. Это позволяет снизить энергосиловые параметры прессования и эффективно использовать мощности оборудования, но приводит к усложнению конструкции применяемого оборудования [12, 13].
Снижение коэффициента трения на контакте заготовка–контейнер при прямом прессовании позволяет не только снизить усилия, но и оказывает влияние на температуру и напряженно-деформированное состояние экструдируемого металла [14–16].
Разработанный способ мелкосерийного производства пруткового и проволочного припоя из сплава ПОИн-52 показал его пер- спективность [17], но, в свою очередь, при реализации и отработке технологии изготовления было выявлено, что предлагаемую технологию можно совершенствовать [16], что позволит дополнительно повысить эффективность процесса и качество готовой продукции.
Целью настоящей работы является исследование влияния контактного трения на процесс прямого прессования прутков и проволоки из сплава ПОИн-52.
В работах [12–14] энергозатраты на процесс прессования (при пренебрежении силами трения скольжения на контактной поверхности пресс-штемпеля и контейнера) предлагается оценивать в виде суммы сил:
Р = Р деф + FT p , (1) где Где ф - усилие, осуществляющее формоизменение (пластическую деформацию); Гг р — усилия, преодолевающие силы трения скольжения на контактной поверхности обрабатываемого металла с контейнером и с матрицей.
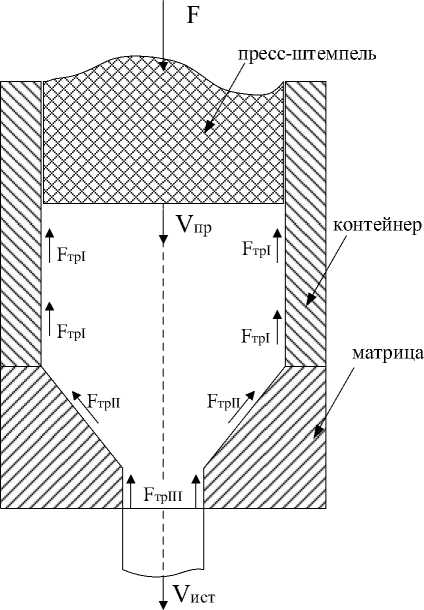
Рис. 1. Схема действия сил трения в очаге деформации при прямом прессовании
Сила трения /тр определяется особенностью геометрии очага деформации (рис. 1) и состоит из трех частей – усилия, направленного на преодоление трения скольжения обрабатываемого металла о контейнер Гтр1, о по верхность матрицы Гтр11 и о калибрующий поясок матрицы Гтр111:
Г р = Г тр1 + Г тр11 + Г трщ . (2)
Согласно закону трения Кулона, напряжение трения т пропорционально нормальному напряжению на поверхности контактирующих тел а л и не зависит от сопротивления деформации металла o s, т. е.
т = f • О п , (3)
где f - коэффициент трения, изменяющийся в пределах от 0,1 до 0,5.
При условии рассмотрения формирования сил трения по закону Зибеля напряжение трения т пропорционально среднему по области пластической деформации сопротивлению деформации сдвига о т и не зависит от приложенного нормального напряжения оп , т. е.
т = Ф • от , (4)
где ф , в отличие от кулоновского коэффициента трения, называют показателем трения, изменяющимся в пределах от 0,2 до 1.
Составляющие сил трения могут быть найдены:
-
Г тр 1 5 g • т Л • О кон • £ра с • f • ° твх ;
-
Г тр11 5 м • т 4-sina • (О к°н О вых ) • f • О тср ;
-
Г тр111 5 к • т П • О вых • ^ кп • f • О твых ,
где f - коэффициент (показатель) трения; 5б, 5м, 5к - площадь боковой поверхности втулки контейнера, матрицы и ее калибрующего пояска; О кон - диаметр контейнера; Овых - диаметр проволоки (прутка) на выходе из матрицы; £рас - длина распрессованной заготовки; £кп - длина калибрующего пояска матрицы; о твх , о тср , о твых - сопротивление пластического сдвига заготовки в контейнере, матрице и в калибрующем пояске соответственно.
В работе [14] нами представлена математическая модель прямого прессования припоя из легкоплавких материалов, позволяющая определять энергосиловые режимы прессования проволоки и прутков различного диаметра. Результаты математического моделирования прессования прутков ∅8,0 и 15,0 мм, а также проволоки ∅2,0 мм представлены в табл. 1. С помощью разработанной математической модели были проведены аналитические исследования влияния коэффициента трения на усилия в процессе прессования. Результаты исследований приведены на рис. 2–4. Как видно из графиков, приведенных на рис. 2–4, повышение коэффициента трения существенно влияет на начальное усилие прессования. Площадь контакта заготовки с контейнером в начальный момент прессова- ния наибольшая, и требуется усилие для преодоления сил трения FтрI. С уменьшением площади контакта заготовки с контейнером
Таблица 1
Результаты расчета на математической модели
Параметр |
Размерность |
Величина |
||
Эксп. 1 |
Эксп. 2 |
Эксп. 3 |
||
Исходные данные |
||||
Диаметр заготовки (прутка), D вх |
мм |
30 |
30 |
20 |
Диаметр прутка (проволоки), D вых |
мм |
15 |
8 |
2 |
Длина заготовки, L |
мм |
120 |
120 |
120 |
Диаметр контейнера, D кон |
мм |
31 |
32 |
21,8 |
Скорость прессования, V пр |
мм/с |
12 |
3,5 |
0,5 |
Сопротивление деформации заготовки, σ |
МПа |
10,5 |
10,5 |
10,5 |
Полуугол матрицы, α |
° |
33,5 |
40 |
18,4 |
Длина калибрующего пояска, LKn |
мм |
5 |
5 |
5 |
Коэффициет трения, f |
– |
0,5 |
0,5 |
0,5 |
Результаты расчета |
||||
Коэффициент вытяжки, μ |
– |
4,3 |
16,0 |
118,8 |
Скорость истечения, V ист |
мм/с |
51 |
56 |
59 |
Усилие в момент начала прессования, F н |
кН |
92,8 |
106 |
105 |
Усилие в момент завершения прессования, F к |
кН |
41,0 |
51,3 |
71,9 |
Усилия деформации, F деф |
Н |
31 647 |
46 848 |
65 784 |
Сила трения, F тр |
Н |
61 171 |
59 168 |
39 384 |
в контейнере F трI |
Н |
57 432 |
55 637 |
36 297 |
в матрице F трII |
Н |
2621 |
2935 |
2938 |
в калибр. пояске F трII |
Н |
1119 |
597 |
149 |
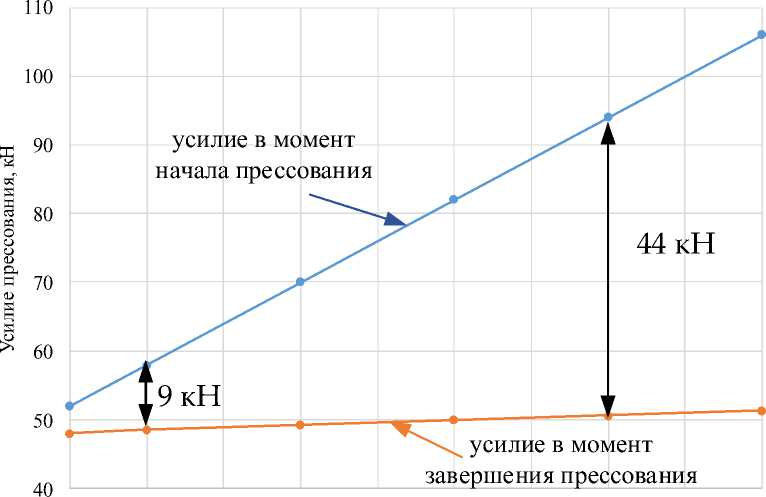
0,05 0,1 0,15 0,2 0,25 0,3 0,35 0,4 0,45 0,5
Коэффициент трения
Рис. 3. Изменение усилия прессования проволоки ∅ 8,0 мм в зависимости от коэффициента трения
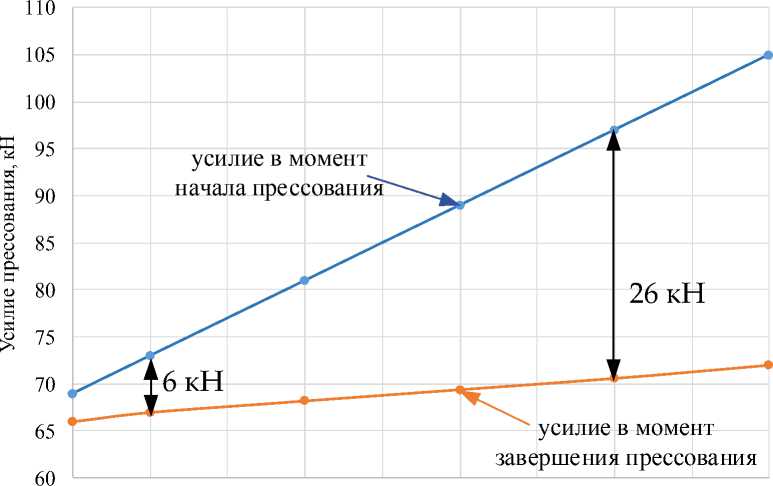
0,05 0,1 0,15 0,2 0,25 0,3 0,35 0,4 0,45 0,5
Коэффициент трения
Рис. 4. Изменение усилия прессования проволоки ∅ 2,0 мм в зависимости от коэффициента трения
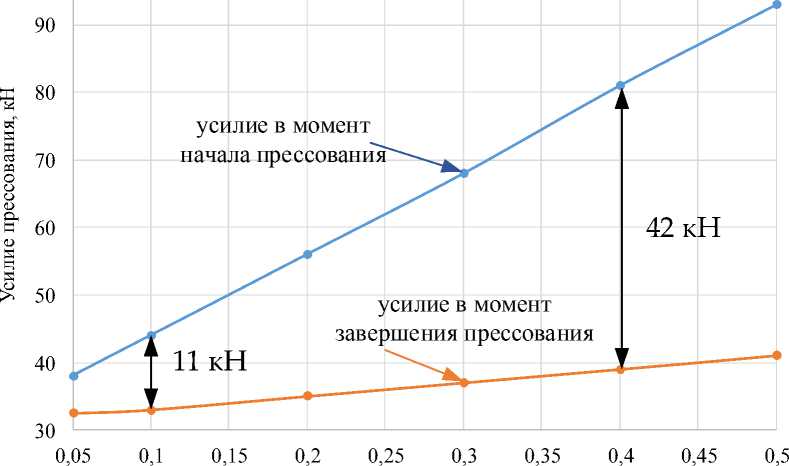
Коэффициент трения
Рис. 2. Изменение усилия прессования проволоки ∅ 15,0 мм в зависимости от коэффициента трения
составляющая FтрI тоже уменьшается и разница между «усилием в момент начала прессования» и «усилием в момент завершения прессования» сокращается. Снижение значения коэффициента трения позволяет сущест- венно, а именно до 60 %, снизить усилие прессования, которое расходуется на преодоление сил трения и приводит к повышению температуры на контакте заготовки с контейнером.
Для подтверждения результатов аналитических исследований, а также определения коэффициента трения экспериментальным путем были проведены лабораторные исследования процесса прессования при различных условиях трения. Гидравлический пресс Д2428, на котором осуществлялся процесс прессования, оснащен системой измерения усилия прессования и хранения полученных данных [14]. Экспериментальные исследования проводились при прессовании прутков ∅ 8,0 мм из заготовки ∅ 30,0 мм при одинаковой скорости прессования. Результаты замера усилий прессования прутков ∅ 8,0 мм при различных условиях трения представлены на рис. 5–7.
Для определения фактического усилия прессования нужно от полученных значений отнять поправочную величину 15 кН. Связано это с особенностями тарировки гидравлического пресса. При прессовании заготовки ∅ 30,0 мм в пруток ∅ 8,0 мм без смазки усилие в момент начала прессования составляет 105 кН, а в момент завершения прессования – 47 кН. Согласно рис. 3 такие значения усилий прессования, с небольшой погрешностью, соответствуют коэффициенту трения 0,5. Применение смазочных материалов, а именно графитовой (графит – С) и молибденовой (дисульфид молибдена – MoS 2 ) смазки, которые используются при холодном волочении [18],
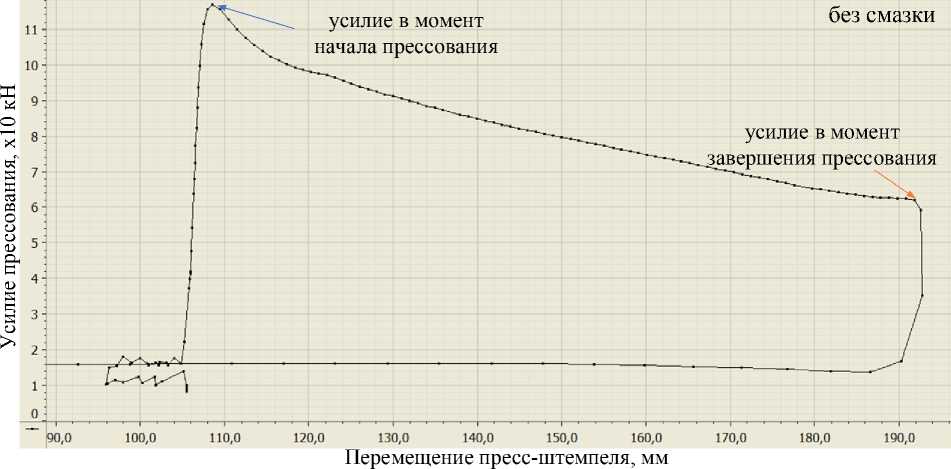
Рис. 5. Усилие в процессе прессования прутка ∅ 8,0 мм без применения смазки

Рис. 6. Усилие в процессе прессования прутка ∅ 8,0 мм с применением молибденовой смазки
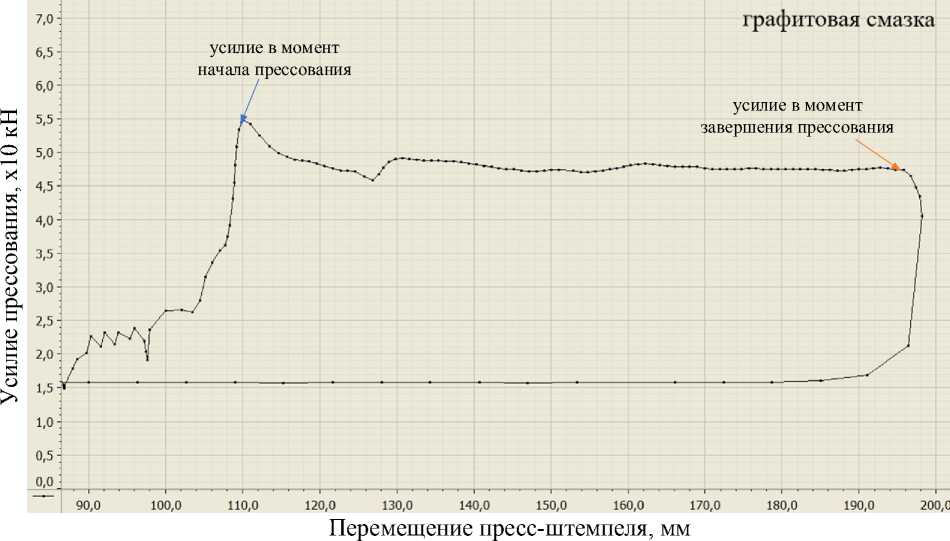
Рис. 7. Усилие в процессе прессования прутка ∅ 8,0 мм с применением графитовой смазки
привело к существенному падению усилия прессования в начальный момент и изменению значительной части графика с наклонного на горизонтальный на стадии установившегося течения (см. рис. 6 и 7).
Сравнение результатов экспериментального определения усилия прессования прутка ∅ 8,0 мм без применения смазки (см. рис. 5) и результатов математического моделирования (см. рис. 3) позволяет установить, что коэффициент трения соответствует значению 0,5. Усилие прессования в начальный момент при расчете и при экспериментальном определении равно 105 кН, а вот в момент завершения прессования расчетное значение равно 51 кН, а экспериментальное – 47 кН. Расхождение между расчетным и экспериментальных значением в данном случае составляет 7 %.
Применение смазочных материалов приводит к падению усилия в момент начала прессования с 105 до 40 кН (см. рис. 5–7). Усилие прессования в 40 кН соответствует коэффициенту трения менее 0,05, т. е. коэффициент трения уменьшился более чем в 10 раз (см. рис. 3). При этом стоит отметить, что на стадии установившегося течения усилие прессования ниже на 2–3 кН при применении графитовой смазки по сравнению с молибденовой. Разница между теоретическим усилием в начале прессования и в конце прессования составляет 4 кН, а при экспериментальных исследованиях – 5 кН.
Наличие пика на кривой зависимости усилия от хода пресс-штемпеля (см. рис. 5–7) объясняется рядом причин: в первую очередь, переходом от контактного трения покоя к трению скольжения, а во-вторую – переходом от упругой к пластической деформации [19–20].
С определенной долей допущения можно говорить о том, что при прессовании припоя ПОИн-52 с использованием стального контейнера без применения смазки коэффициент трения равен 0,5, а при применении графитовой или молибденовой смазки коэффициент трения будет принимать значение 0,05.
Пакет для компьютерного моделирования процессов обработки металлов давления Qform [21], в основе которого лежит метод конечных элементов, позволяет учитывать трение по законам Кулона, Зибеля и Леванова. Используя результаты экспериментальных исследований, путем подбора определили показатели трения.
На рис. 8 приведены результаты компьютерного моделирования в пакете Qform процесса прессования заготовки ∅ 30,0 мм в пруток ∅ 8,0 мм без смазки и с применением смазки в сравнении с результатами экспериментальных исследований.
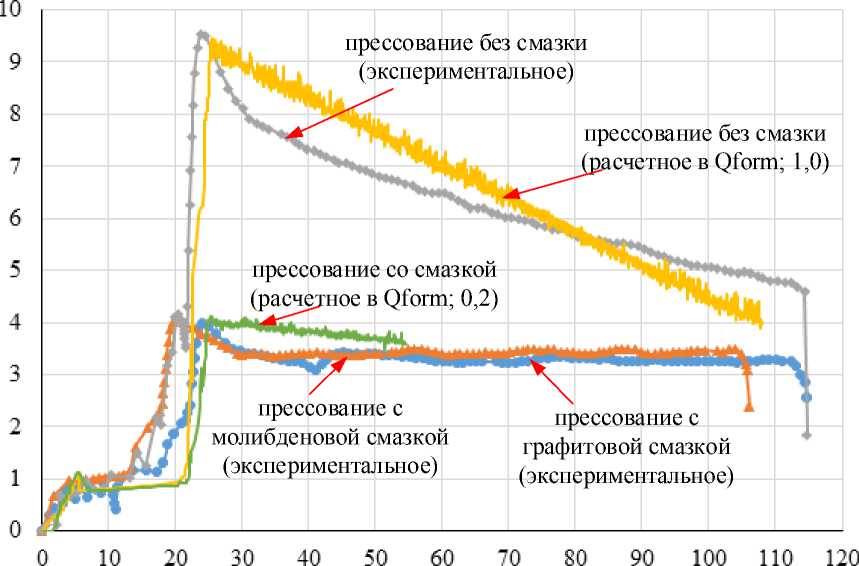
Перемещение пресс-штемпеля; мм
Рис. 8. Сравнение изменения усилия прессования при различных условиях контактного трения, полученного экспериментальным путем и при компьютерном моделировании в Qform
Таблица 2
Показатели (коэффициенты) трения для моделирования прямого прессовании припоя ПОИн-52 с использованием стального контейнера
Условия трения |
Кулон |
Зибель |
Леванов |
Б ез смазки |
0,5 |
1,0 |
1,0 |
М олибденовая смазка |
0,05 |
0,2 |
0,2 |
Г рафитовая смазка |
0,05 |
0,2 |
0,2 |
В табл. 2 приведены показатели трения, рекомендуемые для использования при моделировании процесса прямого прессовании припоя ПОИн-52 с использованием стального контейнера.
Коэффициент трения оказывает существенное влияние на температурные условия процесса прессования, следовательно, учет его достоверной величины при компьютерном моделировании позволит существенно повысить точность расчетов.
Заключение
С помощью математического моделирования исследовано влияние коэффициента трения на усилие в процессе прессования прутков ∅8,0 и 15,0 мм, а также проволоки ∅2,0 мм. Установлено, что с увеличением коэффициента трения на преодоление силы тре- ния скольжения на контактной поверхности обрабатываемого металла с контейнером и с матрицей тратится до 60 % усилия, необходимого для прессования исследуемого сплава. В ходе экспериментальных исследований показано, что применение смазочных материалов, а именно графитовой (графит – С) и молибденовой (дисульфид молибдена – MoS2) смазки, позволяет снизить коэффициент трения более чем в 10 раз. С определенной долей допущения установлено, что при прессовании припоя ПОИн-52 с использованием стального контейнера без применения смазки коэффициент трения равен 0,5, а при применении графитовой или молибденовой смазки коэффициент трения принимает значения, близкие к 0,05. Используя результаты экспериментальных исследований, путем подбора определили показатели трения по законам
Кулона, Зибеля и Леванова, которые могут быть применены для компьютерного моделирования в пакете Qform процесса прямого прессования припоя ПОИн-52 с использованием стального контейнера без применения смазки и с применением графитовой и молибденовой смазки. Учет достоверной величины показателя трения при компьютерном моделировании позволит существенно повысить точность получаемых результатов.
Список литературы Определение показателя трения в процессе прямого прессования проволочного и пруткового припоя ПОИН-52
- Петров, А.Н. Теория обработки металлов давлением: штампы, износ и смазочные материалы: учеб. пособие для вузов / А.Н. Петров, П.А. Петров, М.А. Петров. – 2-е изд., испр. и доп. – М.: Изд-во Юрайт, 2020. – 130 с. – (Высшее образование) // ЭБС Юрайт [сайт]. – https://urait.ru/bcode/446675 (дата обращения: 10.07.2021).
- Воронцов, А.Л. Теория и расчеты процессов обработки металлов давлением: учеб. пособие: в 2 т. / А.Л. Воронцов. – М.: Изд-во МГТУ им. Н.Э. Баумана, 2014. – Т. 2. – 441 с.
- Каргин, В.Р. Теория обработки металлов давлением: учеб. пособие / В.Р. Каргин. – Самара: СамГУ, 2019. – 112 с. // Лань: электронно-библиотечная система. – https://e.lanbook.com/book/148619 (дата обращения: 10.07.2021).
- О возможности снижения мощности, расходуемой на процесс прокатки проволоки на совмещенном прокатно-волочильном стане / А.А. Радионов, Л.В. Радионова, В.А. Харитонов, О.С. Малахов // Электротехнические системы и комплексы. – Магнитогорск: МГТУ, 2005. – № 10. – С. 63–70.
- New technological lubricants for steel wire drawing / L.V. Radionova, V.A. Kharitonov, V.I. Zyuzin, L.D. Rol'shchikov // Steel in Translation. – 2001. – No. 12. – P. 49–50.
- Радионова, Л.В. Разработка технологии производства высокопрочной проволоки с повышенными пластическими свойствами из углеродистых сталей: дис. … канд. техн. наук / Л.В. Радионова. – Магнитогорск, 2001. – 137 с.
- Харитонов, В.А. Проектирование ресурсосберегающих технологий производства высокопрочной углеродистой проволоки на основе моделирования: моногр. / В.А. Харитонов, Л.В. Радионова. – Магнитогорск: ГОУ ВПО «МГТУ», 2008. – 171 с.
- Неравномерность и локализация пластической деформации в процессах обработки металлов давлением / Г.С. Бурханов, В.С. Юсупов, А.Е. Шелест и др. // Металлы. – 2012. – № 4. – С. 39–46.
- Чулкин, С.Г. Анализ современных представлений и подходов при оценке износостойкости и долговечности материалов в различных условиях внешнего трения / С.Г. Чулкин // Трение, износ, смазка. – 1999. – Т. 1, № 2. – С. 47–51.
- Совершенствование геометрии волочильного канала с целью повышения стойкости инструмента и качества полос из нихрома / А.И. Снигирев, Л.М. Железняк, Н.А. Снигирев, В.Л. Дымшаков // Производство проката. – 2014. – № 12. – С. 24–28.
- Добров, И.В. Механика процесса внешнего трения при волочении полосы в монолитной волоке / Добров И.В. // Машиностроение: сетевой электронный научный журнал. – 2015. – Т. 3. № 2. – С. 32–39.
- Теория и технология прессования алюминиевых сплавов: учеб. пособие / В.Р. Каргин, А.Ф. Гречникова, Я.А. Ерисов, Ю.С. Старостин. – Самара: Изд-во СГАУ, 2015. – 80 с.
- Логинов, Ю.Н. Прессование как метод интенсивной деформации металлов и сплавов: учеб. пособие / Ю.Н. Логинов. – Екатеринбург: УрФУ, 2016. – 156 с. // Лань: электронно-библиотечная система. – https://e.lanbook.com/book/99055 (дата обращения: 06.05.2020).
- Математическое моделирование энергосиловых параметров прямого прессования легкоплавких материалов / Л.В. Радионова, С.Р. Фаизов, В.Д. Лезин, А.Е. Сарафанов // Вестник ЮУрГУ. Серия «Металлургия». – 2020. – Т. 20, № 2. – С. 71–79. DOI: 10.14529/met200207
- Компьютерное моделирование температурных режимов при полунепрерывном прямом прессовании легкоплавких материалов / Л.В. Радионова, С.Р. Фаизов, Д.В. Громов, И.Н. Ердаков // Вестник ЮУрГУ. Серия «Металлургия». – 2020. – Т. 20, № 4. – С. 30–38. DOI: 10.14529/met200404
- Оптимизация процесса прямого прессования проволоки из сплава ПОИн-52 методом обобщенного приведенного градиента / Л.В. Радионова, С.Р. Фаизов, И.Н. Ердаков, А.В. Брык // Вестник ЮУрГУ. Серия «Металлургия». – 2021. – Т. 21, № 1. – С. 54–65. DOI: 10.14529/met210106
- Глебов, Л.А. Припой ПОИн-52: исследование процесса и разработка технологии мелкосерийного производства проволоки / Л.А. Глебов, Л.В. Радионова, С.С. Фаизов // Magnitogorsk Rolling Practice 2019: материалы IV молодежной научно-практической конференции / под ред. А.Г. Корчунова. – Магнитогорск: Изд-во Магнитогорск. гос. техн. ун-та им. Г.И. Носова, 2019. – С. 54–56.
- Харитонов, В.А. Ресурсосбережение при производстве проволоки / В.А. Харитонов, В.И. Зюзин, А.К. Белан. – Магнитогорск: МГТУ, 2003. – 194 с.
- Visco-Plastic Flow of Metal in Dynamic Conditions of Complex Strain Scheme / A. Korbel, W. Bochniak, P. Ostachowski et al. // Metallurgical and Materials Transactions A. – 2011. – Vol. 42. – P. 2881–2897. DOI: 10.1007/s11661-011-0688-x
- Григорьев, А.А. Расчет технологических параметров экструзии брикетов порошков алюминия / А.А. Григорьев, А.И. Дмитрюк // Научно-технические ведомости СПбПУ. Естественные и инженерные науки. – 2020. – Т. 26, № 1. – С. 53–61. DOI: 10.18721/JEST.26105
- Стебунов, С.А. 25 лет программе моделирования процессов обработки металлов давлением QForm / С.А. Стебунов // КШП. ОМД. – 2016. – № 11. – С. 3–4.