Определение технологических факторов прокатки, способствующих возникновению дефектов поверхности на трубах
Автор: Черных Иван Николаевич, Струин Дмитрий Олегович, Шкуратов Евгений Александрович
Журнал: Вестник Южно-Уральского государственного университета. Серия: Металлургия @vestnik-susu-metallurgy
Рубрика: Обработка металлов давлением. Технологии и машины обработки давлением
Статья в выпуске: 3 т.18, 2018 года.
Бесплатный доступ
Наиболее производительным и современным является способ получения труб на трубопрокатных агрегатах с использованием непрерывных раскатных станов с удерживаемой оправкой. Производство бесшовных труб горячей прокаткой на таких агрегатах может сопровождаться возникновением дефектов на поверхности труб, что приводит к увеличению количества бракованной продукции. С учётом современного уровня техники процесс дефектообразования при производстве труб изучен недостаточно. Дефекты возникают на поверхности труб при осуществлении прокатки в станах линии трубопрокатного агрегата. Характерными видами дефектов поверхности являются раковина-вдав, плена трубопрокатная на наружной и внутренней поверхности труб, а также поперечный разрыв металла. В данной статье рассмотрено качество труб наружным диаметром в диапазоне 219÷325 мм с толщиной стенки в диапазоне значений 8÷24 мм, получаемых прокаткой на агрегатах, имеющих в линии непрерывные раскатные станы с 2- и 3-валковыми калибрами. Качество рассмотрено с точки зрения влияния технологических факторов прокатки (коэффициент вытяжки, обжатие по наружному диаметру, толщине стенки и проч.) на количество брака по отдельным видам дефектов поверхности. В качестве универсального, ранее мало изученного, по величине которого можно судить об уровне дефектности технологии, рассмотрен фактор соотношения деформаций по диаметру к деформации по толщине стенки в раскатном стане. Статистическими методами получен ряд моделей, руководствуясь которыми можно прогнозировать ожидаемый уровень брака по дефектам поверхности при производстве бесшовных труб, а также подбирать условия деформирования, минимизирующие количество брака.
Качество труб, трубопрокатный агрегат, дефекты поверхности, технологические факторы прокатки
Короткий адрес: https://sciup.org/147232505
IDR: 147232505 | DOI: 10.14529/met180306
Текст научной статьи Определение технологических факторов прокатки, способствующих возникновению дефектов поверхности на трубах
Производство бесшовных труб горячей прокаткой на современных трубопрокатных агрегатах (ТПА) сопровождается возникновением дефектов поверхности различного вида [1]. Наличие дефектов приводит к преждевременному выходу из строя конструкций, составленных из таких труб [2].
В зависимости от глубины залегания, расположения по поверхности и требований стандартов наличие дефектов поверхности может приводить к браку при производстве труб [3]. Это обосновывает актуальность проведения исследований в области дефектообразования.
Перспективной для подобных исследований является технология получения труб с
использованием современных ТПА с непрерывными раскатными станами [4]. Массив имеющейся научно-технической информации с учётом индивидуальных особенностей ТПА может быть применён в виде общих рекомендаций по снижению количества брака. С другой стороны, выполненный анализ позволил выявить для ТПА с любым составом оборудования факторы, влияющие на возникновение дефектов [5–14]: степень тонкостенности раската; частные и суммарные значения коэффициента вытяжки; изменение наружного диаметра и толщины стенки.
Возможность формализации статистических данных о количестве брака по дефектам
Таблица 1
Значения коэффициента корреляции rxy
Фактор |
Обозначение |
Диапазон варьирования |
Вид дефекта поверхности |
|||||
ДП |
С 1 |
РНТ |
ПНТ |
ПВТ |
РВТ |
|||
В составе ТПА: раскатной стан с 3-валковыми клетями |
||||||||
Степень тонкостенности |
D/S ГТ |
9,95÷40,6 |
–0,33 |
0,42 |
–0,2 |
–0,24 |
–0,3 |
–0,29 |
D/S НС |
14,4÷50,2 |
–0,28 |
0,44 |
–0,25 |
–0,2 |
–0,25 |
–0,27 |
|
D/S ИС |
13,5÷47,4 |
–0,29 |
0,44 |
–0,24 |
–0,21 |
–0,26 |
–0,27 |
|
Изменение наружного диаметра |
δ D НС |
9,3÷12,9 |
0,16 |
0,05 |
0,4 |
–0,14 |
0 |
0,12 |
δ D ИС |
1,7÷5,6 |
–0,16 |
–0,01 |
–0,41 |
0,13 |
0 |
–0,14 |
|
Σδ D ИС, КС |
3,5÷24,9 |
0,41 |
0 |
–0,33 |
0,32 |
0,39 |
0,26 |
|
Изменение толщины стенки |
δ S НС |
40,3÷71,5 |
–0,24 |
0,37 |
–0,14 |
–0,23 |
–0,2 |
–0,27 |
Соотношение деформаций по диаметру к деформации по толщине стенки |
δ D/ δ S КС |
–0,3÷–3,8 |
–0,39 |
–0,24 |
0,3 |
–0,24 |
0,31 |
–0,18 |
Коэффициент вытяжки |
μ НС |
1,8÷3,8 |
–0,24 |
0,49 |
–0,17 |
–0,25 |
–0,24 |
–0,27 |
μ ПС, НС |
3,6÷10,8 |
–0,31 |
0,38 |
–0,24 |
–0,2 |
–0,28 |
–0,26 |
|
μ ТПА |
3,6÷12,2 |
–0,23 |
0,4 |
–0,29 |
–0,14 |
–0,2 |
–0,22 |
|
В составе ТПА: раскатной стан с 2-валковыми клетями |
||||||||
Степень тонкостенности |
D/S ГТ |
11,4÷40,6 |
0,64 |
0,76 |
0,5 |
0,33 |
0,52 |
0,02 |
D/S ПС |
7,8÷13,8 |
0,6 |
0,7 |
0,45 |
0,33 |
0,5 |
0,04 |
|
D/S НС |
12,1÷47,8 |
0,66 |
0,78 |
0,52 |
0,29 |
0,53 |
–0,03 |
|
Изменение толщины стенки |
δ S НС |
45,7÷75,9 |
0,53 |
0,56 |
0,44 |
0,35 |
0,38 |
0,01 |
Соотношение деформаций по диаметру к деформации по толщине стенки |
δ D/ δ S НС |
0,2÷0,3 |
–0,58 |
–0,65 |
–0,44 |
–0,33 |
–0,49 |
–0,06 |
Коэффициент вытяжки |
μ ПС |
2,3÷3,7 |
0,45 |
0,39 |
0,31 |
0,47 |
0,37 |
0,29 |
μ НС |
2,1÷4,6 |
0,6 |
0,68 |
0,5 |
0,32 |
0,44 |
–0,05 |
|
μ ПС, НС |
4,7÷15,8 |
0,6 |
0,65 |
0,46 |
0,41 |
0,46 |
0,08 |
|
μ ТПА |
4,8÷16,8 |
0,6 |
0,66 |
0,47 |
0,39 |
0,46 |
0,05 |
Обработка металлов давлением… поверхности относительно технологических факторов прокатки показана в источниках [6, 14].
Для предварительной оценки связи между факторами и браком по отдельным видам дефектов использовался коэффициент парной корреляции r xy [15]. Для исследуемых выборок и уровней значимости α = 0,05 и α = 0,1 принимаются значения ǀ rxy ǀ ≥ 0,42 и ǀ rxy ǀ ≥ 0,34 (табл. 1). Если r xy ≥ 0, то рост фактора будет способствовать увеличению количества брака и наоборот.
Предварительное исследование показало:
– влияние одинаковых факторов на количество брака при производстве труб в разных ТПА может быть противоположно;
– влияние технологических факторов прокатки на вероятность возникновения брака по дефекту вида поперечный разрыв металла одинаково вне зависимости от вида ТПА;
– прокатка в линии ТПА с использованием калибровочного стана потенциально влияет на количество брака по отдельным видам дефектов. В частности, при увеличении сум-
Примечание. ГТ – готовая труба; ПС – прошивной стан; НС – непрерывный раскатной стан; ИС – стан-извлекатель оправки; КС – калибровочный стан; ДП – дефекты поверхности; С – поперечный разрыв металла; РНТ и РВТ – раковина-вдав на наружной и внутренней поверхности трубы; ПНТ и ПВТ – плена трубопрокатная на наружной и внутренней поверхности трубы.
Таблица 2
Виды полученных моделей
№ модели |
Вид модели |
Формула |
1 |
Линейная |
y = ax + b |
2 |
Полиномиальная |
y = ax 2 + bx + c |
3 |
Экспоненциальная |
y = ae bx |
4 |
Степенная |
y = ax b |
Таблица 3
К оценке адекватности полученных моделей для ТПА с 2-валковым раскатным станом
Вид ДП |
Фактор |
№ модели (табл. 2) |
Коэффициенты модели |
Оценка адекватности |
||||
a |
b |
c |
F |
α |
2 ост |
|||
ДП |
δ D/ δ S НС |
3 |
34,51 |
–17,84 |
– |
13,19 |
0÷0,05 |
0,01 |
D/S ПС |
1 |
0,137 |
–0,94 |
– |
1,39 |
0,2÷0,3 |
0,05 |
|
μ ПС |
1 |
0,589 |
–1,274 |
– |
1,41 |
0,05 |
||
μ НС |
3 |
0,023 |
0,813 |
– |
1,36 |
0,06 |
||
ПНТ |
δ D/ δ S НС |
1 |
–7,838 |
2,686 |
– |
2,51 |
0,1÷0,2 |
0,08 |
μ ПС |
2 |
0,506 |
–2,358 |
2,727 |
1,43 |
0,2÷0,3 |
0,08 |
|
μ ПС, НС |
1 |
0,093 |
–0,496 |
– |
1,53 |
0,08 |
||
μ ТПА |
1 |
0,087 |
–0,498 |
– |
1,5 |
0,08 |
||
ПВТ |
D/S ПС |
1 |
0,153 |
–1,091 |
– |
10,48 |
0÷0,05 |
0,01 |
δ D/ δ S НС |
1 |
–5,537 |
1,987 |
– |
6,47 |
0,01 |
||
μ ПС |
1 |
0,775 |
–1,793 |
– |
4,65 |
0,05÷0,1 |
0,03 |
|
μ ПС, НС |
3 |
0,038 |
0,192 |
– |
1,43 |
0,2÷0,3 |
0,04 |
|
μ ТПА |
2 |
0,007 |
–0,103 |
0,575 |
1,78 |
0,03 |
||
С |
D/S НС |
2 |
0,002 |
–0,096 |
1,08 |
8,42 |
0÷0,05 |
0,03 |
δ S НС |
3 |
4·10–15 |
0,44 |
– |
348,69 |
4·10–4 |
||
δ D/ δ S НС |
2 |
88,5 |
–53,7 |
8,043 |
16,51 |
0,01 |
||
μ НС |
2 |
0,396 |
–2,249 |
3,114 |
19,12 |
0,01 |
||
μ ПС, НС |
3 |
1·10–8 |
1,189 |
– |
10,79 |
0,03 |
||
μ ТПА |
2 |
0,018 |
–0,325 |
1,333 |
6,47 |
0,02 |
||
D/S ПС |
1 |
0,192 |
–1,824 |
– |
2,38 |
0,1÷0,2 |
0,06 |
|
D/S ГТ |
1 |
0,033 |
–0,652 |
– |
1,41 |
0,2÷0,3 |
0,09 |
Таблица 4
К оценке адекватности полученных моделей для ТПА с 3-валковым раскатным станом
– увеличение соотношения деформаций по диаметру к деформации по толщине стенки [10] может способствовать снижению количества брака.
Если коэффициент корреляции ǀ r xy ǀ = 1, можно говорить с максимальной достоверностью, что зависимость между сравниваемыми величинами является линейной. Большинство значений коэффициента корреляции в табл. 1 свидетельствует о нелинейной зависимости.
Сами факторы могут быть зависимыми или независимыми величинами. Проверка проводилась также с использованием коэффициента парной корреляции r xy . Коэффициент корреляции r xy между факторами табл. 1 принимает значения в диапазоне от 0,75 до 1, что говорит о наличии высокой степени связи между ними. Следовательно, зависимость между количеством брака при производстве труб и фактором может быть описана уравнением от одной переменной.
Задача по определению вида эмпирической зависимости решается с использованием метода наименьших квадратов (МНК). В настоящее время метод МНК реализован в ряде компьютерных программ.
В [15] в качестве рекомендации при обработке статистических данных предлагается использовать интервальную группировку данных. То есть весь диапазон варьирования фактора (см. табл. 1) разбивается на несколько равных отрезков, в каждом из которых вычисляется среднее значение фактора и средневзвешенное значение параметра отклика (количество брака). Для определения шага разбиения с учётом объёма выборки n пользуются эмпирическими формулами, в частности формулой Стерджесса [6, 15]:
K - 1 + 3,3221g n .
Уровень брака при производстве труб в разных ТПА различен. Для сравнения рассматриваемых технологий и оценки вероятности возникновения максимальное значение брака по отдельному виду дефектов поверхности при производстве труб приравнивалось к 1, остальные значения после группировки данных вычислялись в долях относительно максимального.
После получения моделей, отражающих зависимость количества брака при производстве труб от выбранных факторов (см. табл. 1), производилась их оценка с использованием F -критерия Фишера и величины остаточной дисперсии. Значения эмпирических коэффициентов a , b , c для полученных моделей (табл. 2) с указанием уровня достоверности α сведены в табл. 3, 4.
Исследование показало (см. табл. 3, 4):
– наибольший комплекс технологических факторов оказывает влияние на формирование брака по дефекту поверхности вида поперечный разрыв металла;
– для обеих линий ТПА количество брака по причине дефекта поверхности вида поперечный разрыв металла увеличивается с ростом относительного обжатия толщины стенки в раскатном стане δS НС и суммарного коэффициента вытяжки при прошивке и раскатке μ ПС, НС (рис. 1);
– дефекты вида поперечный разрыв металла (рис. 1а) возникают при прокатке труб в раскатном стане при коэффициенте вытяжки на участке оправочных станов (рис. 1б), равном 8,0 и 12,2 для линии ТПА с 2-валковым и 3-валковым непрерывным раскатным станом с удерживаемой оправкой;
– соотношение деформаций по диаметру к деформации по толщине стенки в линии ТПА с 2-валковым раскатным станом оказывает влияние на появление брака по большинству исследуемых видов дефектов (рис. 2а). Подобным фактором для линии ТП может
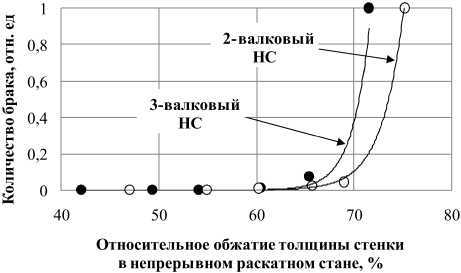
а)
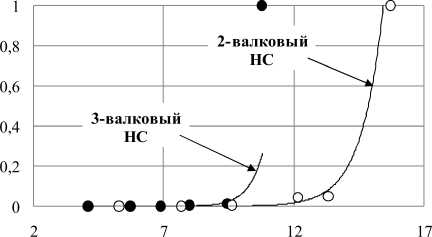
Коэффициент вытяжки при прошивке и раскатке
б)
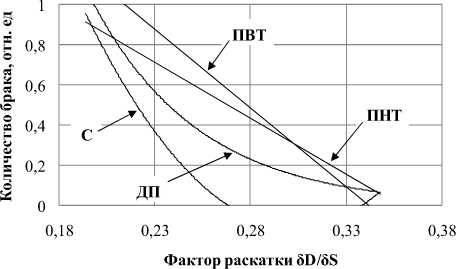
а)
Рис. 2. Влияние технологических факторов прокатки на количество брака по различным видам дефектов: а) соотношения суммарных деформаций по наружному диаметру и толщине стенки в непрерывном раскатном стане; б) суммарной степени редуцирования наружного диаметра в стане-извлекателе оправки и калибровочном стане
Рис. 1. Влияние технологических факторов прокатки на количество брака по дефекту вида поперечный разрыв металла: а) суммарного относительного обжатия толщины стенки в непрерывном раскатном стане; б) суммарного коэффициента вытяжки процессов прошивки и раскатки
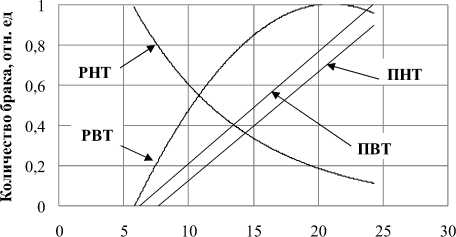
Суммарная степень редуцирования
б)
также выступать параметр суммарной степени редуцирования в станах ИС и КС Σδ D ИС, КС (рис. 2б). Факторы, влияние которых показано на рис. 2, являются оценочными. Повлиять на их величину, на уровень дефектности в целом и по отдельным видам дефектов можно за счёт факторов прокатки в прошивном и непрерывном оправочном станах. Соответствующие модели приведены в табл. 3, 4;
– наличие отдельно стоящего в линии ТПА калибровочного стана и прокатка в нём с увеличением степени редуцирования наружного диаметра способствует уменьшению количества брака по дефекту вида раковина-вдав на наружной поверхности (см. рис. 2б).
Выводы
-
1. Рассмотрено качество бесшовных горячекатаных труб, получаемых прокаткой с использованием современных ТПА с непрерывными раскатными станами с удерживаемой оправкой.
-
2. Получен ряд моделей, отражающих зависимость количества брака от технологических параметров прокатки в линии ТПА.
-
3. Различные комбинации факторов прокатки на участке прошивной – непрерывный стан влияют на формирование конечной картины брака при производстве труб как по дефектам поверхности в целом, так и по отдельным видам дефектов. Увеличение степени редуцирования наружного диаметра при прокатке с использованием отдельно стоящего калибровочного стана в линии ТПА способствует уменьшению количества брака по дефекту вида раковина-вдав на наружной поверхности.
-
4. Дефект вида поперечный разрыв металла вне зависимости от конструкции непрерывного стана возникает при величине суммарного обжатия толщины стенки свыше 60 %. При этом его появление связано с качеством гильзы.
-
5. Количество брака по дефекту вида поперечный разрыв металла частично формиру-
- ется за счёт трансформации из дефектов другого вида, поскольку зависит от тех же факторов, что и количество брака по дефектам вида плена наружная и внутренняя трубопрокатная.
-
6. В целом полученный ряд моделей согласуется с имеющимися в научно-технической литературе данными. С этой точки зрения модели уточнены с учётом режимов прокатки, применяемых на современных ТПА.
-
7. Мало исследованными с учётом современного оборудования ТПА технологическими факторами прокатки, влияющими на формирование брака, являются полученные модели для факторов соотношения деформаций по диаметру к деформации по толщине стенки и суммарной степени редуцирования наружного диаметра в стане-извлекателе оправки и калибровочном стане.
-
8. Руководствуясь полученными моделями, можно прогнозировать ожидаемый уровень брака по дефектам поверхности при производстве бесшовных труб прокаткой на современных ТПА, а также подбирать условия деформирования, минимизирующие количество брака по дефектам поверхности.
Список литературы Определение технологических факторов прокатки, способствующих возникновению дефектов поверхности на трубах
- Дефекты стальных слитков и проката: справочное издание / В.В. Правосудович, В.П. Сокуренко, В.Н. Данченко и др. - М.: Интермет Инжиниринг, 2006. - 384 с.
- Establishment of a database and a classification of the defects in the metal of pipes according to their severity / M. Bettayeb, E. Bouali, N. Abdelbaki, M. Gaceb // 20th International Congress of Chemical and Process Engineering CHISA 2012. - Prague, Czech Republic, 2012. - P. 607-615.
- ГОСТ Р 53383-2009. Трубы стальные бесшовные горячедеформированные. Технические условия. - М.: Стандартинформ, 2009. - 21 с.
- Лубе, И.И. Исследование и совершенствование технологии горячей прокатки труб из непрерывнолитой заготовки на агрегатах с непрерывным станом: автореф. … дис. канд. техн. наук: 05.16.05 / И.И. Лубе. - М., 2010. - 21 с.
- Пластометрические исследования металлов / Н.А. Мочалов, А.М. Галкин, С.Н. Мочалов, Д.Ю. Парфенов. - М.: Интермет Инжиниринг, 2003. - 318 с.
- Статистический анализ брака наружной поверхности котельных труб / Ю.В. Зильберг, В.Г. Чус, А.С. Кагарлицкий и др. // Обработка металлов давлением: сб. науч. тр. - М.: Металлургия, 1976. - Вып. 59. - С. 257-273.
- Зильберг, Ю.В. Формоизменение поверхностных дефектов заготовки при производстве труб на ТПА с непрерывным станом / Ю.В. Зильберг, Б.В. Гнездилов // Сталь. - 1984. - № 9. - С. 59-61.
- Использование программного продукта с открытым кодом для выявления причин дефектообразования при изготовлении прецизионных труб / С.И. Паршаков, А.А. Богатов, А.В. Серебряков и др. // Труды XVII Международной научно-технической конференции «ТРУБЫ-2009». - Челябинск: ОАО «РосНИТИ», 2009. - С. 305-309.
- Галкин, С.П. К вопросу о выборе типа прошивного стана / С.П. Галкин, А.В. Гончарук, Б.А. Романцев // Сталь. - 2012. - № 1. - С. 42-46.
- Видоизменение дефектов горячепрессованных труб при холодной пильгерной прокатке / А.А. Терещенко, О.Ю. Кравченко, А.В. Скрынник, Я.В. Фролов // Пластическая деформация металлов. - 2014. - Т. 2. - С. 160-163.
- Минаев, А.А. Специфика использования катаной и непрерывнолитой заготовки для производства труб / А.А. Минаев, М. Захур, Ю.В. Коновалов // Производство проката. - 2005. - № 4. - С. 29-37.
- Глазунова, Н.А. Классификация по видам дефекта «продир» на внутренней поверхности горячекатаных труб / Н.А. Глазунова, О.В. Рожкова, И.А. Ковалева // Литье и металлургия. - Минск: Изд-во БНТИ, 2014. - № 1 (74). - С. 28-32.
- Матвеев, Б.Н. Совершенствование производства труб из высоколегированных сталей // Сталь. - 2000. - № 3. - С. 56-58.
- Чуев, А.А. Пути решения проблем повышения качества поверхности труб, прокатываемых на ТПА-140 с двухклетевым станом продольной прокатки / А.А. Чуев, В.Н. Данченко // Металлургическая и горнорудная промышленность. - Днепропетровск: НИИ Укрметаллургинформ, 2012. - № 3. - С. 49-53.
- Фастовец, Н.О. Математическая статистика. Примеры, задачи и типовые задания: учеб. пособие для нефтегазового образования / Н.О. Фастовец, М.А. Попов. - М., 2012. - 99 с.