Определение технологических параметров процесса штамповки крутоизогнутых отводов
Автор: Попов Игорь Петрович, Николенко Кирилл Анатольевич, Николенко Константин Анатольевич, Латушкин Илья Анатольевич, Яшин Василий Владимирович
Журнал: Известия Самарского научного центра Российской академии наук @izvestiya-ssc
Рубрика: Машиностроение и машиноведение
Статья в выпуске: 1-3 т.19, 2017 года.
Бесплатный доступ
Представлены аналитические зависимости для расчета процесса штамповка крутоизогнутых отводов из различных материалов. Описана технология изготовления крутоизогнутых отводов. Разработана конструкция и описана работа промышленной штамповой оснастки.
Технология, технологические параметры, штамповая оснастка, крутоизогнутый отвод, размеры заготовки, усилие процесса, предельные параметры процесса
Короткий адрес: https://sciup.org/148205072
IDR: 148205072
Текст научной статьи Определение технологических параметров процесса штамповки крутоизогнутых отводов
штампов позволит обеспечить низкую себестоимость продукции и высокое качество изделия.
Геометрия и технологически размеры крутоизогнутых отводов представлены на рис. 1.
ТЕХНОЛОГИЯ ПРОИЗВОДСТВА
И КОНСТРУКЦИЯ ПРОМЫШЛЕННОЙ ОСНАСТКИ
Разработанная технология позволяет снизить себестоимость изделия на 15 – 20%. Это достигается за счет интенсификации технологического процесса, использования универсального оборудования вместо специализированного и жесткой инструментальной оснастки.
Технология производства отводов включает следующие операции:
Первый комплекс операций: Резка заготовки в меру; Резка выходного торца; Резка торца передающего усилие; Резка площадки под толкатель; Зачистка торцев;
Второй комплекс операций: Обезжиривание; Лакировка (Первый слой); Сушка в печи при температуре 30-40 градусов 5-10 минут; Лакировка (Второй слой); Сушка; Покрытие смазкой (покрытие смазкой осуществляется непосредственно перед штамповкой. Смазка: мыльный раствор-графит. Коэффициент трения - 0,7.)
Третий комплекс операций: Штамповка в инструментальном штампе на универсальном оборудовании. Должна соблюдаться следующая последовательность: установка детали в штампе; обжатие полуматрицами с фиксацией обжимными болтами; штамповка; развенчивание полуматриц; поворот эксцентрика; снятие отштампованного изделия с оправки;
Четвертый комплекс операций: Отчистка полученного изделия от лака и смазки; Обрезка торцев (осуществляется в дисковых пилах при помощи обрезной матрицы); Зачистка торцев; Механическая полировка обработка поверхности детали.
Условное обозначе н ие и геометрические размеры |
Условный диамет р прохода, мм Dy |
Наруж н ый диаметр, мм Dн |
Тол щ ина сте н ки, м м s |
Рад и ус ги б а, м м Rг. с р. |
Угол гиба, градусы 9 0 |
36 |
38 |
0,8 … 1,5 |
5 7 |
15 30 45 60 75 90 |
|
42 |
44 |
0,8 … 1 |
6 6 |
||
50 |
53 |
0,8 … 1,5 |
7 0 |
||
63 |
66 |
0,8 … 1,5 |
9 9 |
||
70 |
76 |
1 … 2 |
1 1 4 |
||
76 |
79 |
1 … 3 |
1 1 8 |
||
80 |
84 |
1,5 … 2,5 |
1 2 6 |
Рис. 1. Номенклатура изделия «Отвод крутоизогнутый»
Конструкция опытно-промышленного штампа проектировалась с учетом результатов предварительного эксперимента проведенного на экспериментальном штампе. Штамповая оснастка спроектирована для изготовления отвода с относительным радиусом кривизны Rотн = 1,5 при толщине стенки исходной трубной заготовки S = 3 мм и диаметра Dн = 79. Общий вид штампа представлен на рис. 2.
Опытно-промышленный штамп состоит из нижней плиты (8) к которой при помощи опоры ходовых винтов (7) крепятся ходовые винты (4). К винтам при помощи фиксаторов крепится разъемные полуматрицы (5) и составные части наружной направляющей втулки (2). Полуматрицы (5) имеют возможность перемещаться. Направление перемещение осуществляется при помощи задней и передней направляющей. В передней направляющей размещается жесткая составная оправка (6). Нижняя часть оправки жестко закреплена, верхняя имеет возможность вращаться на эксцентрике (9). Эксцентрик (9) и внутренняя направляющая втулка (3) одновременно является нижним замком и верхним замком, фиксирующим в рабочем положении составную оправку.
Эксцентриком (9) оправка устанавливается в рабочее положение. На внутреннюю направляющую втулку (3) насаживается заготовка. При вращении ходовых винтов (4) осуществляется перемещение разъемных матриц (5) до смыкания, приводящее к упругому обжатию заготовки. На торец заготовки устанавливается нажимной пуансон (1). При включении пресса осуществляется перемещение нажимной пуансон (1), т.е. передача деформирующего усилия от пресса в торец заготовки. Нажимной пуансон (1) проталкивает заготовку на заданный угол. Про-
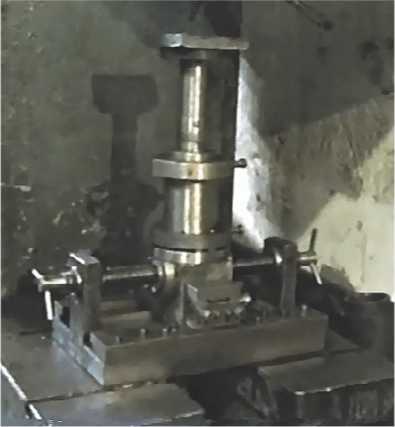
a
Рис. 2. Опытно-промышленный штамп для формообразования тонкостенных крутоизогнутых отводов:
1 – нажимной пуансон; 2 – наружная направляющая втулка; 3 – внутренняя направляющая втулка;
4 – ходовые винты; 5 – разъемные полуматрицы; 6 – внутренняя жесткая оправка;
7 – опоры ходовых винтов; 8 – основание штампа; 9 – эксцентрик.
а – внешний вид штамповой оснастки, б – трехмерная модель штамповой оснастки выполненная с применением системы «КОМПАС»
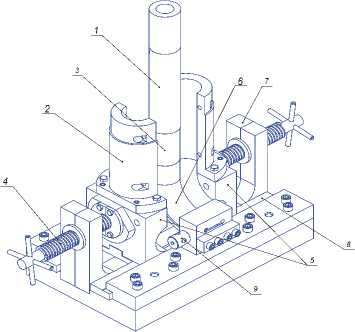
б
цесс завершается при образовании достаточных припусков на обрезку. После завершения процесса ходовые винты раскручиваются и раскрывают разъемные полуматрицы. Верхний замок удаляется. Эксцентрик поворачивается, уменьшая поперечное сечение жесткой оправки, после чего заготовка беспрепятственно извлекается из штампа.
При реализации новой технологии необходимо выполнение ряда технологических расчетов. Такой комплекс расчетов складывается в методику проектирования технологического процесса для реализации которой необходимы аналитические зависимости, позволяющие определять технологические параметры для изделий различной номенклатуры (см. рис. 1).
Для изготовления крутоизогнутых отводов необходимо выполнить расчет следующих технологических параметров: формы и размеров заготовки; силовых параметров процесса; определить предельные возможности штамповки.
АНАЛИТИЧЕСКАЯ ЗАВИСИМОСТЬДЛЯ РАСЧЕТА РАЗМЕРА ЗАГОТОВКИ
Результаты, полученные при анализе напряженно-деформированного состояния с помощью конечно-элементного комплекса ANSYS/ LS-DYNA, позволили установить ряд допущения, положенных в основу для вывода аналитической зависимости при определении технологических параметров. Применен метод совместного решения уравнений равновесия и условия пластичности.
Для определения размеров заготовки использовано условие постоянства длин образующих. Форма заготовки и значение поправочных коэффициентов для расчета в зависимости от материала детали представлена на рисунке 3.
Расчет размеров заготовки производили по следующим формулам:
L max* = ( 1 - K max ) L max - длина заготовки, соответствует длине максимальной образующей заготовка с учетом поправочного коэффициента, где L max - длина заготовки, рассчитанная из условия постоянства длин образующих.
, Л Tu * Ku
£ u* = arctg - угол скоса заготовки
Ds - e со стороны передающего усилие торца с учетом поправочного коэффициента;
Tv * Kv gv* = arctg------- - угол скоса заготовки Ds со стороны выходного торца с учетом поправочного коэффициента, где Tu * и Tv * - катеты, противолежащие углу скоса заготовки со стороны торца передающего усилие и выходного торца соответственно.
Диаметр заготовки – Dз и толщина – s соответствует диаметру и толщине трубы, из которой изготавливается заготовка.
Размеры контактной поверхности приложения усилия (Fe и е) определяются из условия равенства усилий, одно из которых приложено к торцу заготовки, а другое образовано силами трения по поверхности контакта заготовки с инструментом. При этом суммарная площадь трения равна площади средней поверхности заготовки.
АНАЛИТИЧЕСКАЯ ЗАВИСИМОСТЬ ДЛЯ РАСЧЕТА УСИЛИЯ ПРОЦЕССА
Для определения усилия формообразования определено максимальное меридиональное напряжение на торце приложения усилия (площадки под толкатель):
R
^ Т = а - ( exP (- f a ) - 1 ) .
R e
Площадь торца заготовки для приложения внешнего усилия:
Р fn 2 SDs
Fe =
Высота дуги, ограничивающая площадь торца заготовки:
n (1
e = R„ I 1 - cos где 6cp - угол, ограничивающий величину скоса.
Для расчета усилия необходимо учесть упрочнение. Упрочнение учтем линейной зави-
Форма заго т овки |
Матери а л |
З н ачение по п равочных коэффициентов |
||
_________________ Lmx* _________________ |
||||
Km ax |
Ku |
Kv |
||
12Х18Н1 0 Т |
0 , 055 |
1.1. |
0.64 |
|
ОТ4 |
0 .04 |
1.32 |
0.52 |
|
АМгб М |
0 ,05 |
1.21 |
0.56 |
Рис. 3. Форма заготовки и значение поправочных коэффициентов для расчета размеров заготовки в зависимости от материала детали симостью. В качестве интенсивности деформаций примем деформацию сдвига. Деформация сдвига определяется из геометрических соотношений, по размерам исходной заготовки и готовой детали, когда торцы детали приняли форму сечения в виде кольца.
Таким образом, усилие, необходимое для проталкивания заготовки в гарантированный зазор жесткой инструментальной оснастки определяется следующей зависимостью:
р
прот
п2 f2 (^ TO + П у ) sD g R p
2 Re ’ где γ – интенсивность деформаций; f – коэффициент трения; α – угол формообразования; Rρ – радиус кривизны детали; Rθ – радиус детали.
В табл. 1 приведены значения теоретического усилия процесса формообразования в сравнении с установленным максимальным экспериментальным значением для различных материалов.
АНАЛИТИЧЕСКАЯ ЗАВИСИМОСТЬ ДЛЯ РАСЧЕТА ПРЕДЕЛЬНОЙ СТЕПЕНИ ДЕФОРМАЦИИ
Для определения предельной степени деформации выбран критерий Томленова. Считая, согласно предварительному анализу в ANSYS/ LS-DYNA, что наибольшее значение интенсивности деформаций имеет место на кромке в области минимального радиуса формообразования, при условии, что схема напряженно-деформированного состояния близка к линейной, за интенсивность деформаций принята макси- мальная деформация тангенциального растяжения, а за интенсивность напряжений тангенциальное напряжение растяжения. Таким образом, величина деформации на торце равна величине тангенциальной деформации элемента и определена аналитической зависимостью:
Т ^о f f/ 2 П Т f п ( 1,5 ( а + b ) - хь Ь ) )))
E„ = —TO exp f -----Ln I — ------
-
6 П V J ^ f I 2nR„l
V V v TOJ v 6j))
где – a, b – полуоси эллипса, образованного в результате скоса торца;
при E θ max = E θ ≤ δ p – разрушения не наблюдается;
при E θ max = E θ ≥ δ p – наблюдается разрешение в виде разрыва кромки.
В табл. 2 приведены результаты предельной штамповка отводов из различных материалов.
ВЫВОДЫ
-
1. Представлена разработанная технология и изготовленная штамповая оснастка для формообразования крутоизогнутых отводов на универсальном оборудовании. Данный подход к изготовлению отводов снижает себестоимость изделия на 15 – 20 % за счет интенсификации технологического процесса, использования универсального оборудования и жесткой инструментальной оснастки.
-
2. Показаны выведенные зависимости для расчета технологических параметров: размеры заготовки, усилие процесса, предельные параметры процесса. Полученные теоретические зависимости показали хорошую сходимость с результатами экспериментальными исследований.
Таблица 1. Сравнение теоретического и экспериментального усилия формообразования
Марка материала |
Теоретическое усилие штамповки, т |
Максимальное экспериментальное усилие штамповки, т |
12X18H10T |
8,8б |
7,2 |
0T4 |
12,1 |
б,3 (Разрушается при формообразовании) |
АМгбМ |
11,3 |
5,1 (Разрушается при формообразовании) |
Таблица 2. Значения предельных параметров штамповки
Марка материала |
Рассчитанное значение тангенциальной деформации - Е 6 , % |
Относительное удлинение при испытаниях на растяжение - 8 p , % |
Оценка разрушения при штамповке |
12Х18Н10Т |
43 |
52 |
E 6< 8 р - штамповка без разрушения |
ОТ4 |
23 |
8 |
Е 6 > 8 р - наблюдается |
АМгбМ |
31 |
20 |
разрушение торца |
Список литературы Определение технологических параметров процесса штамповки крутоизогнутых отводов
- Попов И.П., Маслов В.Д., Николенко К.А., Брусин В.Д., Михеев В.А., Хритин А.А. Устройство для формообразования крутоизогнутых отводов: Пат. RU 2294807 C1 (РФ). 2007.
- Маслов В.Д., Николенко К.А., Николенко К.А., Мисюра В.Д. Устройство для формообразования крутоизогнутых отводов: Пат. RU 130241 U1 (РФ). 2013.
- Маслов В.Д., Николенко К.А., Мисюра В.Д. Об изготовлении тонкостенных крутоизогнутых отводов из коррозионностойкой стали//Арматуростроение. 2014. № 1. С. 44-52.
- Маслов В.Д., Николенко К.А. Моделирование процессов листовой штамповки в программном комплексе ANSYS/LS-DYNA; Учебное пособие. Самара: Изд-во Самар. гос. аэрокосм. ун-та, 2007. 80 с.