Определение величин остаточных напряжений по значению остаточного прогиба образца, подвергнутого термопластическому упрочнению
Автор: Круцило Виталий Григорьевич, Дедов Николай Иванович, Якимов Михаил Владимирович
Журнал: Известия Самарского научного центра Российской академии наук @izvestiya-ssc
Рубрика: Машиностроение и машиноведение
Статья в выпуске: 4-2 т.20, 2018 года.
Бесплатный доступ
В статье приведены методики определения остаточных напряжений: расчетная, экспериментальная методом травления и с использованием образцов-свидетелей.
Остаточные напряжения, термопластическое упрочнение, образцы-свидетели, прогибы образцов
Короткий адрес: https://sciup.org/148314023
IDR: 148314023
Текст научной статьи Определение величин остаточных напряжений по значению остаточного прогиба образца, подвергнутого термопластическому упрочнению
Термопластическое упрочнение (ТПУ) используется при изготовлении ответственных деталей, работающих при повышенных температурах и знакопеременных нагрузках, типа лопаток и дисков турбин газотурбинных двигателей (ГТД). За счет формирования в поверхностном слое благоприятных сжимающих остаточных напряжений с большой их глубиной залегания при минимальных пластических деформациях повышается надежность и долговечность упрочненных деталей. Подробно процесс ТПУ описан в работе [1]. Схематично технология ТПУ представлена на рис. 1.
Для реализации технологии ТПУ были разработаны установки и способы упрочнения, которые защищены патентами [2-7]. Различные аспекты технологии ТПУ описаны в работах [11-15].
ОБСУЖДЕНИЯ И РЕЗУЛЬТАТЫ
Критерием качества упрочнения является соответствие параметров эпюры остаточных напряжений указанным в технических условиях. В первую очередь максимальные по абсолютной величине сжимающие остаточные напряжения σ и глубина активной части эпюры h . Эти ост max H параметры можно определить различными методами:
-
- расчетным;
-
- экспериментальным;
Якимов Михаил Владимирович, ассистент.
-
- с использованием образцов-свидетелей.
Расчетный метод подробно изложен в работе [8]. Он основан на технологических параметрах процесса ТПУ: температуре нагрева θ , времени выдержки при этой температуре τ и давлении охлаждающей жидкости p .
Кроме технологических параметров не менее важными являются химический состав, физико-механические и теплофизические свойства материала упрочняемой детали. Все теоретические и экспериментальные исследования были проведены на деталях и образцах из сплава ЭИ893. Свойства этого сплава приведены в таблицах 1-3.
Из таблиц видно, что физико-механические свойства значительно зависят от температуры нагрева, что необходимо учитывать в расчетах.
На рис. 2 приведены эпюры остаточных напряжений, рассчитанные при различных, приближенных к реальным, условиях. Основные параметры выбирались:
-
- постоянными при T=20 oС;
-
- средние в интервале температур Т=20 ÷ 700 oС;
-
- с учетом влияния температуры.
На рис. 2 нанесена также эпюра остаточных напряжений, полученных опытным путем [8].
Сопоставление позволяет сделать заключение, что наилучшее приближение к опытной эпюре остаточных напряжений наблюдается в том случае, если при расчетах учитывается влияние температуры на физико-технологические параметры.
Экспериментальные исследования проводились по методике Давиденкова Н.Н. [9] с уточнениями Биргера И.А. [10]. Образцы для исследований вырезались из натурных лопаток (рис. 3) и плит определенной толщины.
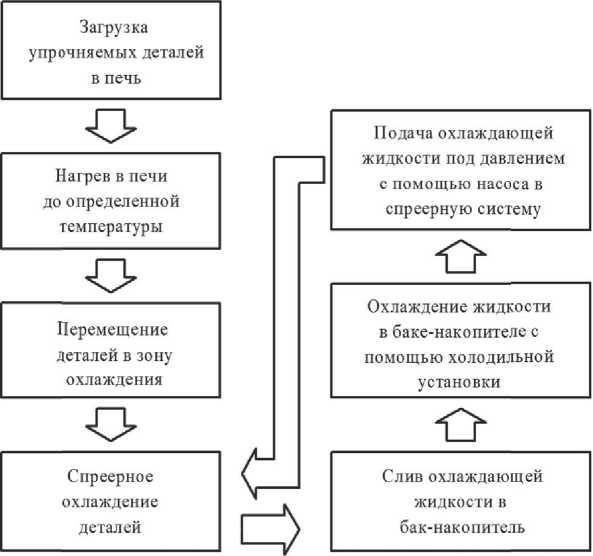
Рис. 1. Блок-схема технологического процесса термопластического упрочнения детали
Таблица 1. Марочный химический состав, %
C |
Si |
Mn |
Cr |
Ni |
W |
Mo |
Ti |
Al |
B |
Ce |
S |
P |
не более |
по расчету |
не более |
||||||||||
0,08 |
0,5 |
0,5 |
15 17 |
Основная |
8-10 |
4-5 |
1,2 1,6 |
1,2 1,6 |
0,010 |
0,025 |
- |
- |
Таблица 2. Нормы механических свойств при 20 0С сортового материала
Обработка |
Температура испытания, ° C |
^ в |
^ 0,2 |
δ |
ψ |
a H , кгс • м 2 см |
кгс / мм 2 |
% |
|||||
не менее |
||||||
1180 ° C, 2 ч, воздух; |
20 |
90 |
60 |
15 |
20 |
7 |
80° ° C, 12 ч, воздух |
750 |
55 |
- |
8 |
12 |
- |
Определение остаточных напряжений методом травления имеет свои особенности, которые описаны ниже.
Установка для определения прогибов состоит из корпуса 1, на котором смонтированы все основные узлы приспособления (рис. 4).
Узел 2 для крепления исследуемого образца 3, имеющий способность перемещаться по направляющим корпуса 1 в зависимости от длины образца, узел 4 для крепления балочки 5, позволяющий задавать начальный прогиб балочки (f=1,0 мм), необходимый для постоянного контакта ее с образцом. Балочка представляет собой упругую стальную пластинку толщиной 0,3 мм, с обеих сторон которой прикреплены тен- зодатчики, являющиеся активным сопротивлением, меняющимся в процессе деформации ба-лочки (образца). Она выполняет роль одного из двух плеч мостовой схемы сопротивлений (T1, T4) (Рис. 3.2), другим плечом которой (T2, T3) является система сопротивлений регистрирующего прибора (например, КСП-4, ЭПП-09М). Таким образом, датчик-мост состоит из четырех тензодатчиков T1 - T4, потенциометра R, служащего для балансировки моста, и блока питания Б.
Этот метод достаточно широко апробирован и его достоверность не вызывает сомнений. Однако он имеет существенные недостатки: разрушение изделия, трудоемкость процесса, опасность из-за использования сильнодействующих кислот.
Таблица 3. Физические свойства сплава
Удельный вес, г / см |
8,794 |
|||||||||||||
Модуль упругости E • 10 - 4, кгс / мм 2 |
20 ° C |
75° ° C |
8°° ° C |
|||||||||||
2,23 |
1,74 |
1,65 |
||||||||||||
Коэффициент линейного 6 расширения а 10 |
2° - 10° ° C |
2° - 75° ° C |
||||||||||||
11,3 |
14,4 |
|||||||||||||
Теплопроводность, кал / см • сек • град |
2° ° C |
2°° ° C |
3°° ° C |
4°° ° C |
5°° ° C |
6°° ° C |
7°° ° C |
8°° ° C |
||||||
0,030 |
0,031 |
0,033 |
0,037 |
0,041 |
0,048 |
0,056 |
0,065 |
|||||||
Электропроводность 1 Г\ 4 — 1 — 1 • 10 , ом • см |
2°° ° C |
3°° ° C |
4°° ° C |
5°° ° C |
6°° ° C |
7°° ° C |
8°° ° C |
|||||||
0,716 |
0,711 |
0,705 |
0,700 |
0,700 |
0,707 |
0,718 |
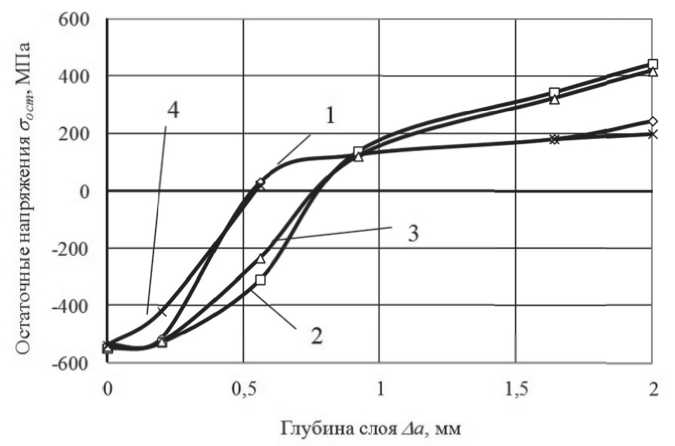
Рис. 2. Остаточные напряжения после ТПУ (материал ЭИ893; Тупр=700 оС):
1 – расчет; λ = λ (T); С=С(T); 2 – расчет; λ = λ 200С; С=С20оС; 3 – расчет; λ = λ m0; С=Сm; 4 – эксперимент
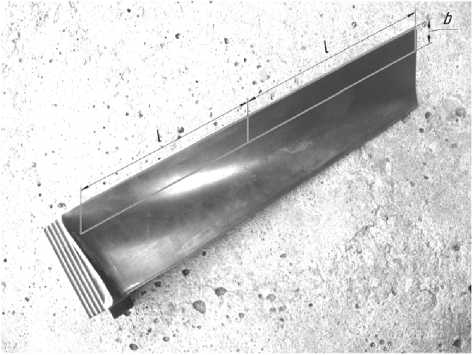
Рис. 3. Разметка профильной части лопатки
Метод с использование образцов-свидетелей позволяет для исследований остаточных напряжений не разрушать упрочняемые натурные детали. Так как эпюры остаточных напряжений при термопластическом упрочнении весьма ти-
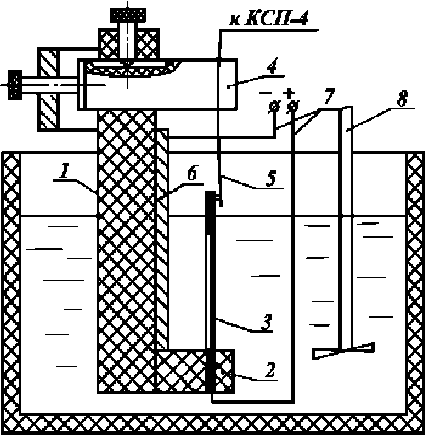
Рис. 4. Схема установки для определения остаточных напряжений на призматических образцах

Рис. 5. Схема технологического процесса упрочнения образцов-свидетелей
пичны [11], то параметры этих эпюр можно рассчитать по прогибу образцов-свидетелей после упрочнения.
На рис. 5 показана схема использования образцов-свидетелей при термопластическом упрочнении.
На рис. 6 приведена эпюры распределения остаточных напряжений экспериментально полученные методом Н. Н. Давиденкова и аппроксимированные двумя вариантами. Остаточные напряжения по толщине образца самоуравнове-шенные.
Значения экспериментальных величин, используемых при проверке корректности методики приведены в таблице 4.
Ниже приводится методика расчета эпюры остаточных напряжений по прогибам образцов-свидетелей при различных аппроксимациях эпюр. Для проверки данной методики используются конкретные данные экспериментов.
Изгибающий момент в поперечном сечении образца соответствующий остаточным напряжениям определяется интегральным выражением, которое в данном случае разбивается на два интеграла
h y h - h y
M = b J о y ydy + b J о ydy , 00
где о y - функция напряжения на участке упрочнения, о - функция напряжения на упругом участке.
Рассмотрим прямоугольную и треугольную формы аппроксимации экспериментально построенного профиля остаточных напряжений в упрочненном слое.
Из условия самоуравновешенности напряжений определим наибольшие остаточные напряжения по формулам:
^ p max
2а h max
h — h y
2 • 600 • 2
2 - 0 . 6
= 514 . 28 МПа
для прямоугольного профиля,
^ pmax
^ mox h y h — hy
600 • 0 . 6
2 - 0 . 6
= 257 . 14 МПа
для треугольного профиля.
Самоуравновешенной системе остаточных напряжений соответствует напряженное состояние чистого изгиба. Изгибающие моменты в
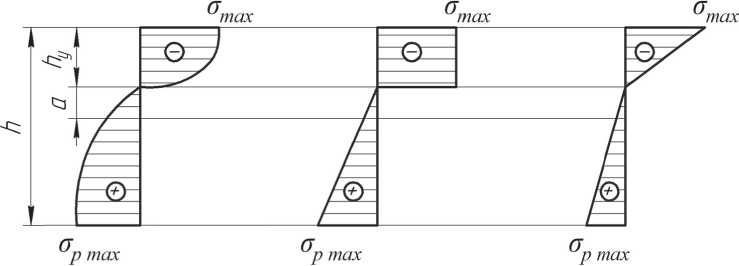
a) 6)
в)
Рис. 6. Эпюры остаточных напряжений по толщине образца после ТПУ: а) экспериментальный профиль, б) прямоугольный профиль, в) треугольный профиль
Таблица 4. Значения экспериментальных величин
M = । ^ max bh y ( 4 h - h y ) =
= 1600-10 - 0.6 (4 - 2 - 0.6) = 4440Hmm для прямоугольного профиля,
M = 1 a bM = 1600 - 10 • 2 • 0 . 6 = 2400 Hmm — max y —
для треугольного профиля.
Образцы, обработанные по методу термо-
пластического упрочнения, имеют выпуклость со стороны обработанной поверхности.
Для определения остаточного прогиба образ-
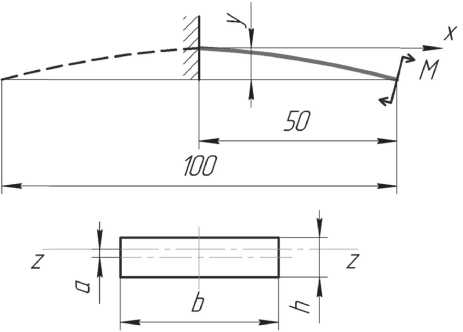
Рис. 7. Расчетная схема образца для определения прогиба и его поперечное сечение
ца после термопластического упрочнения примем балочную схему с учетом симметрии рис. 7. Для моделирования чистого изгиба консольную балку нагружаем изгибающим моментом, соот-
ветствующим остаточным напряжениям.
Прогиб свободного конца консольной балки определяем по формуле:
Ml1
EJz
4 . 44 • 0 . 052
2 - 1011 • 9 . 867 - 10 - 12
= 2 . 81 - 10 — 3 m
для прямоугольного профиля,
У =
Ml1
EJ z
2 . 4 • 0 . 052
2 - 1011 • 9 . 867 - 10 - 12
= 1 . 52 - 10 - 3 m
для треугольного профиля.
Для определения осевого момента инерции поперечного сечения образца нейтральную линию при изгибе принимаем совпадающей границей термопластического упрочнения (рис. 2).
Осевой момент инерции определяем по формуле
J = — + a2 bh = ^^ + 0 . 42 - 10 • 2 = 9 . 867 mm 4
z 12 12
где a=0.4мм – смещение нейтральной оси сечения относительно оси симметрии.
ВЫВОДЫ
Анализ результатов расчетов по данной методике показывает преимущество аппроксимации по варианту б (рис. 6). Погрешность данных, полученных при использовании данного метода, по сравнению с экспериментальными σ max и Q не превышает 10 %.
Список литературы Определение величин остаточных напряжений по значению остаточного прогиба образца, подвергнутого термопластическому упрочнению
- Кравченко Б.А., Круцило В.Г., Гутман Г.Н. Термопластическое упрочнение - резерв повышения прочности и надежности деталей машин: Монография / Самара: СамГТУ, 2000. 216 с.
- Патент РФ №2171857, 13.11.2000 Способ восстановления циклической прочности деталей газотурбинных двигателей из жаропрочных сплавов на основе никеля // Патент России № 2171857, 2000 / Кравченко Б.А., Россеев Н.И., Забродин Ю.В., Круцило В.Г., Медведев С.Д., Монахов А.В.
- Патент РФ №2170272, 26.06.2000 Установка для термопластического упрочнения лопаток // Патент России №2170272, 2000 / Кравченко Б.А., Круцило В.Г., Медведев С.Д., Монахов А.В. Россеев Н.И.
- Патент РФ №2351660, 26.02.2006 Способ термопластического упрочнения деталей и установка для его осуществления // Патент России №2351660, 2006 / Круцило В.Г.
- Патент РФ №2331674, 10.08.2006 Способ термопластического упрочнения сварных соединений // Патент России №2331674, 2006 / Круцило В.Г.