Оптимизация технологии глиноземного производства в филиале ОАО «СУАЛ» «УАЗ - СУАЛ» при переработке боксита СТБР
Автор: Пустынных Е.В., Нифонтов А.А., Пересторонин А.В., Панов А.В.
Журнал: Журнал Сибирского федерального университета. Серия: Техника и технологии @technologies-sfu
Статья в выпуске: 5 т.7, 2014 года.
Бесплатный доступ
Представлены данные по переработке боксита СТБР в глиноземном производстве филиала ОАО «СУАЛ» «УАЗ-СУАЛ», показаны результаты опытно-промышленных испытаний на переделах: размол, автоклавное выщелачивание, сгущение и промывка красного шлама при изменении сырьевой корзины глиноземного производства и реализация результатов опытно промышленных испытаний в глиноземном производстве.
Глиноземное производство, боксит стбр, помол, содовыделение, кристалл соды, автоклавное выщелачивание
Короткий адрес: https://sciup.org/146114870
IDR: 146114870
Текст научной статьи Оптимизация технологии глиноземного производства в филиале ОАО «СУАЛ» «УАЗ - СУАЛ» при переработке боксита СТБР
В промышленном масштабе в филиале ОАО «СУАЛ» «УАЗ-СУАЛ» бокситы Средне-Тиманской группы (СТБР) начали перерабатывать с 1998 г. при одновременном вводе в производство с бокситом Северо-Уральского бокситового рудника (СУБР). Для определения эффективности и уточнения параметров переработки такого сырья применительно к условиям «УАЗа» в середине 1995 г. на завод была поставлена опытная партия боксита в количестве 12 тыс. т, на которой проведены промышленные испытания 9–23 августа 1995 г. С 1998 г. филиал ОАО «СУАЛ» «УАЗ-СУАЛ» перерабатывает боксит СТБР в промышленном масштабе с постепенным увеличением его доли в сырьевой корзине предприятия, и в июле 2012 г. был осуществлен переход на переработку 100 % боксита СТБР.
Особенности минералогии
Бокситы Вежаю-Ворыквинского месторождения, в настоящее время перерабатываемые на «УАЗе», относятся к бемит-шамозит-гематитовому типу с небольшой примесью ди
Таблица 1. Состав различных партий бокситов СТБР
Главным глиноземсодержащим минералом бокситов СТБР является бемит, более химически активная форма гидроксида алюминия по сравнению с диаспором бокситов СУБРа (табл. 1). Содержание бемита в бокситах в среднем варьируется от 40 до 56 %. Диаспор содержится в небольшом количестве – 1-4 %. Кремнийсодержащие минералы представлены шамозитом, каолинитом и гидрослюдой. Содержание данных минералов колеблется значительно, что служит отличительной особенностью всех бокситов Средне-Тиманской группы [1].
Низкомодульным бокситам присуще более высокое содержание шамозита. Химический состав шамозитов очень непостоянен. Соотношение FeO и Fe2O3 в шамозите меняется, что определяет его растворимость в щелочно-алюминатных растворах. По нашим данным, при температуре ~235 °С шамозит разлагается не более чем на 20 %, а в отдельных случаях практически полностью переходит в красный шлам. Следует отметить, что для бокситов с более высоким содержанием шамозита характерна наибольшая степень его разложения.
Основным железосодержащим минералом в бокситах СТБР является гематит. Содержание гетита в среднем составляет 4-5 %, однако в шамозитизированных бокситах достигает 8÷10 %.
Так как добыча боксита СТБР производится открытым способом, влажность боксита в среднем по году равна 17÷18 % (в переходные периоды достигает 19÷20 %), а в отдельных партиях поднимается до 23 %. Бокситы Среднего Тимана характеризуются повышенным содержанием цинка, содержание которого варьируется от 0,02 до 0,061 % [2].
Технологические проблемы и пути оптимизации технологии
При освоении боксита СТБР в существующей технологической схеме глиноземного производства «УАЗа» возник ряд технологических проблем, потребовавших первоочередного решения:
-
- высокое содержание влаги в боксите, особенно в переходные периоды;
-
- повышенное газовыделение в процессе автоклавного выщелачивания;
-
- увеличение количества шлама при переходе на переработку боксита с кремневым модулем ~ 6,5 единиц;
-
- быстрое зарастание автоклавов и транспортных перетоков автоклавных батарей;
-
- повышенный фон кремнезема, переходящего в щелочно-алюминатный раствор в процессе автоклавного выщелачивания;
-
- повышенное содержание железа в товарном глинозёме за счёт мелкодисперсного и растворимого железа;
-
- повышенное содержание микропримесей, таких как цинк, фтор, марганец [2].
Определены основные пути оптимизации действующей технологии:
-
- загрубление помола боксита;
-
- снижение концентрации оборотного раствора, оптимизация процесса содовыделе-ния;
-
- снижение дозировочного модуля;
-
- снижение температуры автоклавного выщелачивания боксита текущего поступления до ~228 °С;
-
- определение наиболее эффективных реагентов для разделения пульпы красного шлама;
-
- увеличение межпромывочного периода выпарных батарей.
Загрубление помола боксита
По исследованиям, проведенным специалистами ОАО «РУСАЛ ВАМИ», измельчаемость боксита СТБР в 1,3÷1,5 раза выше, чем боксита СУБР, и его переработка в отделении размола «УАЗа» по действующей технологии (спроектированной на ввод в производство боксита СУБР) приводит к значительному переизмельчению боксита СТБР. При этом содержание фракции «–56 мкм» в бокситовой пульпе достигает 87÷89 %.
Для загрубления помола боксита СТБР на одном из технологических участков глиноземного производства проведены испытания и в настоящее время используется схема с сокращенным количеством песковых мельниц: 2÷3 вводящие мельницы (Ø2,7 х L 3,6 м) и одна песковая трубная мельниц (Ø2,2 х L12,0 м) с двухстадийной классификацией бокситовой пульпы. Использование предлагаемой схемы в производстве позволило снизить переизмельчение и повысить крупность бокситовой пульпы по классу «+160 мкм» до 3,5 %, при этом производительность мельниц участка возросла ~на 30 %.
В данный момент в цехе подготовки сырья проходят промышленные испытания по применению схемы одностадийной классификации пульпы. По предварительным результатам использование данной схемы для загрубления помола боксита достаточно эффективно и снижает удельный расход электроэнергии.
Снижение концентрации оборотного раствора, содовыделение, изменение межпромывочного периода
Промышленные испытания по снижению концентрации каустической щелочи в оборотном растворе были первоначально проведены при переработке смеси бокситов СУБР и СТБР – 527 – в соотношении 1:3 и 3:2. Снижение концентрации с 295÷301 до 285÷291 г/дм3 привело к увеличению производительности выпарных батарей по слабому раствору до ~ 6 % и увеличению межпромывочного цикла выпарных батарей на ~ 20 %. Общее снижение расхода 7 атм. пара было достигнуто на уровне 0,032÷0,05 Гкал на 1 т глинозема. Однако на переделе автоклавного выщелачивания было отмечено снижение химического извлечения Al2O3 из боксита в расчете от теоретически возможного в среднем на 0,51÷0,71 % и увеличение расхода сырой пульпы на ~ 3,7 % в расчете на 1 т глинозема.
Переработка 100 % бокситов СТБР привела к изменению физических и химических свойств алюминатных растворов и снизила содержание соды в них, что вызвало ухудшение фильтруемости и снижение скорости ее осаждения на узле отделения соды. Одним из возможных вариантов решения данной проблемы является подача содовой затравки [4]. Для улучшения фильтруемости и увеличения скорости осаждения впервые в промышленном масштабе была опробована технология роста кристалла соды при введении в продукционный выпарной аппарат содовой затравки [3]. Испытания проводили в трех режимах по содержанию твердой фазы в упаренном алюминатном растворе: 80 (без содовой затравки), 130 (1-й режим), 145 г/дм3 (2-й режим) на выпарной батаре № 21 участка № 11, для чего был смонтирован узел подачи сгущенной содовой пульпы из содоотстойника на выпарную батарею. По результатам испытаний построены зависимости, показывающие изменение во времени плотности упаренной пульпы и концентрации Na2Oку (рис. 1–4).
Средние показатели работы выпарной батареи при работе с содовой затравкой и без нее представлены в табл. 2.
Снижение дозировочного модуля
Проведены промышленные испытания по снижению каустического модуля выщелоченной пульпы с 1,59÷1,67 до 1,53÷1,61 ед. При переработке боксита СТБР с кремниевым модулем 6,6÷7,3 ед. наблюдалось снижение степени извлечения Al 2 O 3 из боксита в раствор на ~2,2 %. Снижение каустического модуля выщелоченной пульпы позволило понизить модуль алюминатного раствора, поступающего в систему декомпозиции, на 0,02÷0,04 ед. и, соответственно, увеличить наработку гидроксида до ~4,5 %.
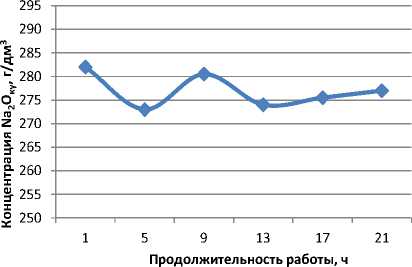
Рис. 1. Изменение концентрации Na2Oку от времени (1-й режим)
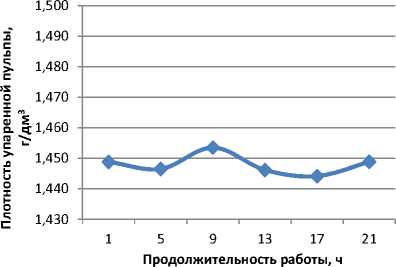
Рис. 2. Изменение плотности упаренной пульпы от времени (1-й режим)
Таблица 2. Средние показатели работы выпарной батареи
Анализируемая среда |
Без содовой затравки |
1-й режим |
2-й режим |
Содержание твердой фазы в упаренной пульпе, г/дм3 |
80 |
130 |
145 |
Межпромывочный период, ч |
17,5 |
24,3 |
44,3 |
Средний размер кристалла соды, мм |
0,179 |
0,300 |
0,398 |
Концентрация Na 2 O ку, г/дм3 |
285,12 |
277,15 |
283,95 |
Плотность упаренного раствора, г/дм3 |
1,430 |
1,448 |
1,472 |
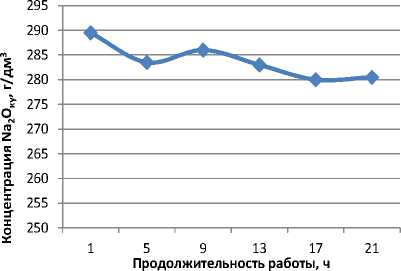
Рис. 3. Изменение концентрации Na2Oку от времени (2-й режим)
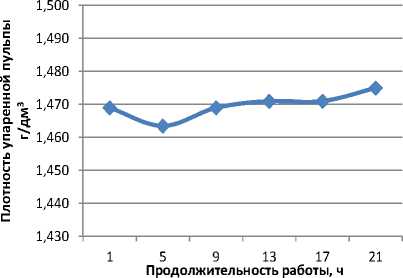
Рис. 4. Изменение плотности упаренной пульпы от времени (2-й режим)
Снижение температуры автоклавного выщелачивания боксита до 230÷228 °С
Температура обработки боксита СТБР щелочно-алюминатным раствором – один из основных факторов, определяющих степень извлечения Al 2 O 3 . Целью проведения промышленных испытаний в январе-мае 2013 г. являлось определение возможности снижения температуры выщелачивания до 230÷228 °С при сохранении регламентированных значений дозировочного модуля и химического извлечения Al2O3 из боксита в раствор. Испытания показали, что при выщелачивании боксита СТБР с кремниевым модулем ~6,35 ед. при температуре ~228 °С снижения степени извлечения Al2O3 из боксита в раствор не отмечено, при этом извлечение глинозема в раствор в среднем составляет более 97,0 % от теоретически возможного. Периодически было зафиксировано резкое снижение химического извлечения Al2O3 на 1,5÷2,0 %, обусловленное, вероятно, неравномерностью минералогического состава тиманского боксита по содержанию в нем диаспора.
Подбор реагентов для эффективного разделения пульпы красного шлама
Боксит СТБР характеризуется увеличенным шламообразованием и высоким удельным расходом флокулянта. Для снижения удельной стоимости обработки красного шлама при со-– 529 – хранении заданных технологических параметров проводятся промышленные испытания по подбору наиболее эффективных реагентов и оптимальных параметров процесса (содержание твердого в пульпе питания сгустителей, дозировка и ввод флокулянта в различные точки, рН раствора для приготовления реагента).
Проблемы зарастания
Переработка 100 % боксита СТБР приводит к увеличенному зарастанию технологического оборудования:
-
- забивка автоматических и ручных сдувок на автоклавных батареях;
-
- заиливание выносных сифонов автоклавных батарей с верхним подводом пара;
-
- уменьшение периодов работы автоклавных батарей между чистками с 5-6 до 3-4 месяцев;
-
- увеличение количества чисток трубопроводов сырой пульпы.
Проблемы зарастания решаются увеличением количества чисток, но для сохранения коэффициента использования оборудования снижено время чистки и ремонта с 14 до 9 дней за счет механизации (применение установок высокого давления «Woma», «Hammelman») и организации многосменной работы. Проводится подбор реагентов для проведения химической очистки теплообменного оборудования.
Дальнейшие направления работ по оптимизации технологии
-
1. Отработка технологии получения средних щелоков для выщелачивания боксита СТБР путем смешения оборотных растворов различных концентраций. Определена концентрация оборотного раствора для низко- и высококонцентрированного упаривания. Низкоконцентрированное упаривание осуществляется до концентрации 240 г/л по каустической щелочи. Для выделения соды концентрация оборотного раствора составляет 300 г/л по каустической щелочи.
-
2. Перевод пяти корпусных батарей для получения низкоконцентрированного оборотного раствора без содовыделения.
-
3. Увеличение корпусности выпарных батарей участка № 3 с трех до четырех и пяти.
-
4. Проведение промышленных испытаний по снижению модуля выщелоченной пульпы без значительного снижения химического извлечения.
Результаты работы
В таблице 3 представлены основные расходные коэффициенты на 1 т глинозема при переработке смеси бокситов в соотношении 50/50 и при 100 % СТБР.
Выводы
-
1. В июле 2012 г. был осуществлен переход на переработку 100 % боксита СТБР в глиноземном производстве филиала ОАО «СУАЛ» «УАЗ – СУАЛ».
-
2. Содержание основных минералов бокситов СТБР значительно колеблется, что вызывает периодическое снижение химического извлечения Al2O3 на 1,5^2,0 % на переделе автоклавного выщелачивания.
-
3. Определены основные технологические проблемы при изменении сырьевой корзины, показаны пути решения технологических проблем, проведен ряд опытно-промышленных испытаний, произведена корректировка технологических режимов на переделах: размол, автоклавное выщелачивание, сгущение и промывка красного шлама, содовыделение.
-
4. Достигнуто снижение расхода теплоэнергии на 6,75 % и электроэнергии на 5,12 % при переработке 100 % боксита СТБР относительно работы глиноземного производства при переработке шихты 50 % боксита СУБР и 50 % боксита СТБР.
Таблица 3. Средние показатели работы глиноземного производства «УАЗа»
Наименование |
Единицы измерения |
50 СУБР / 50 СТБР 5 месяцев 2012 г. |
100 % СТБР 5 месяцев 2013 г. |
Боксит ( сух) |
т |
2,4460 |
2,5834 |
Теплоэнергия |
Гкал |
3,5544 |
3,3148 |
Электроэнергия |
Квт |
422,46 |
400,84 |
Сода |
кг |
108,85 |
147,15 |
Флокулянт |
кг |
0,7110 |
0,9373 |
Известь |
т |
0,0527 |
0,1074 |