Оптимизация условий контактирования полимерпорошковых подшипников скольжения
Автор: Шучев Константин Григорьевич, Зориев Илья Андреевич, Овечкин Игорь Викторович, Шевцова Мария Сергеевна, Иванов Сергей Иванович
Журнал: Вестник Донского государственного технического университета @vestnik-donstu
Рубрика: Технические науки
Статья в выпуске: 4 (47) т.10, 2010 года.
Бесплатный доступ
Установлено оптимальное соотношение площадей полимера и металлокерамики в зоне трения для разработанной конструкции полимерпорошковых подшипников скольжения с комбинированной рабочей поверхностью, способной удерживать смазку в порах порошковой матрицы.
Подшипник скольжения, полимерпорошковая поверхность
Короткий адрес: https://sciup.org/14249384
IDR: 14249384
Текст научной статьи Оптимизация условий контактирования полимерпорошковых подшипников скольжения
Введение. Надежность, экономичность, а во многих случаях и габаритные размеры машин, зависят от конструкции опор трения, поэтому к подшипниковым узлам предъявляют повышенные требования, обусловленные увеличением частоты вращения, статических и динамических нагрузок, а также необходимостью значительного увеличения их ресурса.
Известны широко применяемые в различных машинах порошковые пористые подшипники скольжения, пропитанные жидкими смазочными материалами [1]. Эти подшипники работают в условиях самосмазывания, что обеспечивается выделением масла из пор в результате его терморасширения при нагреве в процессе трения.
К недостаткам подобных подшипников в пусковой период следует отнести образование прямого контакта стального вала с порошковой втулкой, так как подшипник еще не нагрелся, и затруднения в выделении смазочного материала из пор в связи с их перекрытием валом, испытывающим действие рабочих нагрузок. Перекрытие пор в период выбега и останова вала также является недостатком, так как затрудняет возврат смазочного материала в поры после его охлаждения. Это существенно увеличивает утечку масла.
Конструкция и технология изготовления подшипников. Перечисленные недостатки можно компенсировать полимерпорошковыми подшипниками скольжения с принципиально иной макроструктурой рабочей поверхности [2, 3]. Разработанные конструкции подшипников (рис. 1) имеют на рабочей поверхности порошковой матрицы полимерные вставки, выступающие на 5–8 мкм.
Рис. 1. Полимерпорошковые подшипники: а – радиальный; б – упорный; D – диаметр подшипника; d – диаметр полимерной вставки; D 1 – диаметр резервуара для запасов смазки; D 2 , D 3 – диаметры кольцевых рядов вставок; D н – наружный диаметр радиального подшипника; В – ширина подшипника
Таким образом, рабочая поверхность подшипника является составной, а сам подшипник представляет собой макрокомпозит, в котором в порошковой матрице (ЖГр1, 5Д2, 5К0,8) закреплены полиамидные (П-6) вставки.
Технология изготовления порошковых заготовок подшипников включает стандартные операции: формование и спекание. Для радиальных подшипников таким способом изготавливают втулки, а для упорных – диски с центральным отверстием. Далее в порошковой матрице сверлят отверстия и нарезают резьбу. Заготовки подшипников устанавливают в литьевую пресс-форму, и все отверстия одновременно заливают заподлицо термопластичным полимером. Затем рабочую поверхность подшипников обрабатывают поверхностным пластическим деформированием: радиальные подшипники – дорнованием [4], упорные – выглаживанием [5]. Дорнование выполняется с относительными натягами 0,0010–0,0015, а выглаживание с нормальным усилием 1,2–2,0 кН. В обоих случаях пористая матрица, уплотняясь, деформируется пластически, а полиамидные вставки испытывают стесненную упругую деформацию. В результате на рабочей поверхности подшипников образуются полимерные выступы требуемой высоты. Готовые подшипники пропитывают жидким смазочным материалом (Тп-22С) на специальной установке.
Методика. Экспериментальные исследования оптимальной макроструктуры поверхности полимер-порошковых упорных подшипников выполняли на машине трения модели Т-11, а радиальных – на специальном стенде (рис. 2).
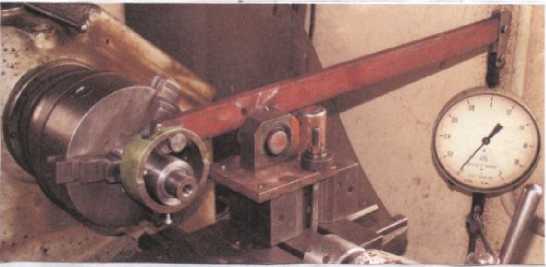
Рис. 2. Испытательный стенд для радиальных подшипников
Стенд смонтирован на токарно-винторезном станке модели Е400-1000. С его помощью можно определять температуру поверхности контакта (термопара ХК), силу трения (пьезоэлектрический датчик РZТ-5) и ресурс подшипника.
Машина трения позволяет выводить на дисплей компьютера, сохранять и распечатывать протоколы испытаний с информацией о силе трения, температуре в зоне контакта и толщине смазочной пленки.
Примеры образцов исследуемых полимерпорошковых подшипников представлены на рис. 3.
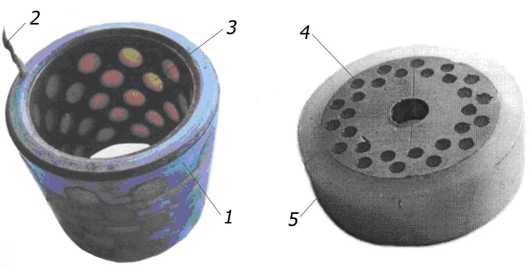
Рис. 3. Экспериментальные образцы подшипников:
1, 5 – порошковая матрица; 2 – термопара; 3, 4 – полимерные вставки
Все экспериментальные исследования реализовывались по полнофакторным 2-уровневым рототабельным линейным и квадратичным экспериментальным планам, а их результаты статистически обрабатывались.
Результаты исследований. Основное влияние на ресурс подшипников оказывают условия контактирования, определяемые, в первую очередь, соотношением на рабочей поверхности площадей полимера и порошковой матрицы. Это соотношение оценивается коэффициентом топологии, определяемым выражением
K = S п / S , (1)
где S п и S – соответственно суммарная площадь полимерных вставок и площадь всего подшипника.
В качестве критерия оптимальности коэффициента топологии принимается минимальное значение силы или коэффициента трения.
Результаты экспериментальных исследований на машине трения позволили получить для упорных подшипников адекватную модель зависимости силы трения от коэффициента топологии и параметра нагружения в следующем виде:
F = 4,318 – 16,724 K + 0,725( PV ) + 16,057 K 2 + 2,08 K ( PV ), (2)
где ( РV ) – параметр нагружения, МПа·м/с.
Для радиальных полимерпорошковых подшипников аналогичная регрессионная модель для коэффициента трения получена по результатам стендовых исследований:
f = 0,106 – 0,259 K – 0,007σ + 0,266 K 2 + 0,008 K σ, (3)
где σ – контактное напряжение, МПа.
Графическая интерпретация моделей зависимости (2) приведена на рис. 4.
' F Н
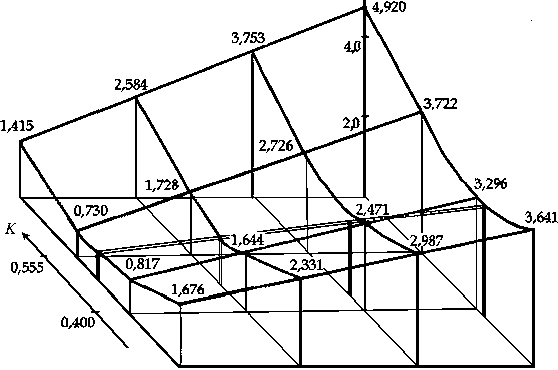
0,929, 1Д60, P1' МПа- м/с
Рис. 4. Оптимум коэффициента топологии
Исследования на экстремум выражений (1) и (2) позволили получить зависимости оптимального значения коэффициента топологии от нагрузочных параметров:
– для упорных подшипников
K = [16,724 – 2,08( PV )]/32,114; (4)
– для радиальных
K = [0,259 – 0,008( PV )]/0,533. (5)
Расчеты показывают, что коэффициент топологии в исследованном диапазоне нагрузок для упорных подшипников находится в интервале 0,4–0,5, а для радиальных – в интервале 0,42–0,46 и изменяется аналогично в зависимости от нагрузки, уменьшаясь с ее ростом.
Дополнительным подтверждением наличия оптимума коэффициента топологии является максимум толщины стабильной смазочной пленки Н, измеренной при исследованиях на машине трения Т-11 (рис. 5).
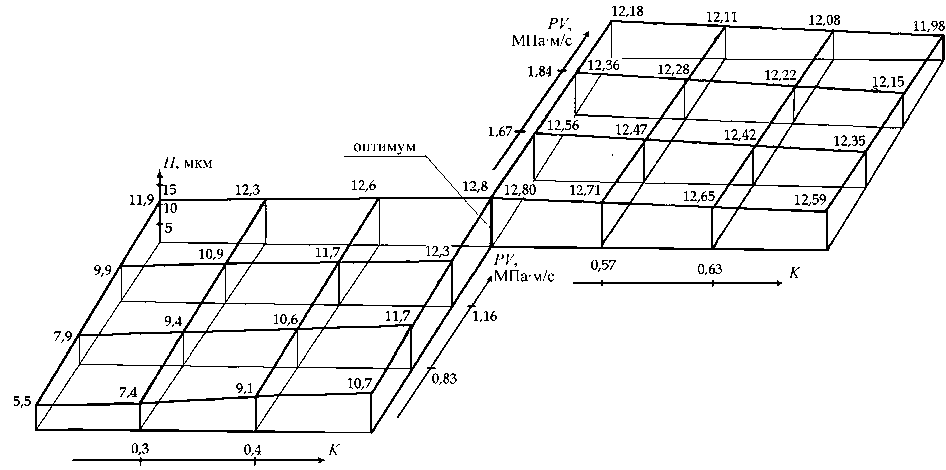
Рис. 5. Влияние коэффициента K и параметра нагрузки ( PV ) на толщину масляной пленки (масло Тп-22С)
Здесь использован метод перевала и получены две модели со средней погрешностью 2,1 %:
Н = 15,0( PV )–0,24 K 0,32
1,34lg( PV ) , H = 13,25( PV ) –0,17 K -90,05 + 0,22lg( PV ) .
Следует отметить, что поверхность отклика в области экстремума имеет малую кривизну и поэтому можно говорить об экстремальной зоне с толщиной смазочной пленки до 12,7 мкм. Тогда наибольшую толщину пленки масла обеспечивает коэффициент топологии, равный 0,45–0,50.
Физический смысл полученных закономерностей состоит в следующем. Слишком малая площадь полимерных вставок не обеспечивает достаточной несущей способности подшипника, так как деформируясь, не препятствует возникновению в зоне трения металлического контакта «вал – втулка». Это ограничение значения коэффициента топологии снизу. С другой стороны, слишком большая площадь полимерных вставок ограничивает маслоемкость порошковой матрицы и масловыделение, что существенно снижает ресурс работы подшипника в условиях самосмазы-вания. Это ограничение значения коэффициента топологии сверху.
Учитывая имеющиеся погрешности экспериментальных результатов, и то, что с изменением K в пределах 10 % сила трения колеблется всего в пределах 7,1 %, причем с ростом нагружения чувствительность силы трения к вариациям коэффициента K снижается, считаем, что рекомендуемое значение K опт составит 0,45±0,05.
Стендовые испытания и промышленная проверка в опорах специализированного смесителя эпоксидных компаундов полимерпорошковых подшипников подтвердили полученные результаты. Ресурс разработанных полимерпорошковых подшипников в сравнении со стандартными порошковыми увеличился в 2,5 раза.
Выводы . 1. Разработаны новые (патенты 2008–2009 гг.) макрокомпозиционные полимерпорош-ковые подшипники скольжения, обеспечивающие существенное повышение ресурса при их эксплуатации.
-
2. В результате триботехнических исследований установлено оптимальное соотношение площадей полимерных вставок и порошковой матрицы на рабочей поверхности подшипника в зависимости от уровня режимов нагружения.
-
3. Полученное оптимальное значение коэффициента топологии обеспечивает повышенное выделение смазочного материала, стабильную толщину масляной пленки и низкое значение силы трения.
-
4. Промышленные испытания упорного полимерпорошкового подшипника подтвердили его высокие триботехнические характеристики и ресурс работы в режиме самосмазывания.
Список литературы Оптимизация условий контактирования полимерпорошковых подшипников скольжения
- Зозуля В.Д. Эксплуатационные свойства порошковых подшипников./В.Д. Зозуля. -Киев: Наук. думка, 1989. -288 с.
- Пат. 87478 Российская Федерация, МПК F 16С 17/04. Упорный подшипник скольжения/С.Н. Шевцов, И.Б. Сайко, В.А. Кохановский, И.В. Овечкин. -№ 2009122006/22; заявл. 08.06.09; опубл. 10.10.09; Бюл. № 28.
- Пат. 83303 Российская Федерация, МПК F 16С 33/04. Подшипник скольжения/С.Н. Шевцов, И.Б. Сайко, М.Б. Флек, А.А. Клименко, В.В. Сибирский. -№ 2008144976; заявл. 13.11.08; опубл. 27.05.09; Бюл. № 15.
- Сайко И.Б. Повышение качества прессовой посадки подшипников скольжения из спеченных порошковых материалов/И.Б. Сайко, И.А. Зориев, С.Н. Шевцов//Изв. Волгогр. техн. ун-та. Сер.: Прогрессивные технологии в машиностроении. -Волгоград, 2006. -№ 4(19). -С. 56.
- Овечкин И.В. Конструкторско-технологическое обеспечение триботехнических характеристик металлополимерных упорных подшипников скольжения/И.В. Овечкин//Тр. I междунар. науч.-техн. конф. «Совершенствование существующих и создание новых технологий в машиностроении и авиастроении», 1-3 июня 2009 г./ЮНЦ РАН -ОАО «Роствертол». -Ростов н/Д, 2009. -С. 235-244.
- Zozulya V.D. Ekspluatacionnye svoistva poroshkovyh podshipnikov./V.D. Zozulya. -Kiev: Nauk. dumka, 1989. -288 s. -in Russian.
- Pat. 87478 Rossiiskaya Federaciya, MPK F 16S 17/04. Upornyi podshipnik skol'jeniya/S.N. Shev-cov, I.B. Saiko, V.A. Kohanovskii, I.V. Ovechkin. -№ 2009122006/22; zayavl. 08.06.09; opubl. 10.10.09; Byul. № 28. -in Russian.
- Pat. 83303 Rossiiskaya Federaciya, MPK F 16S 33/04. Podshipnik skol'jeniya/S.N. Shevcov, I.B. Saiko, M.B. Flek, A.A. Klimenko, V.V. Sibirskii. -№ 2008144976; zayavl. 13.11.08; opubl. 27.05.09; Byul. № 15. -in Russian.
- Saiko I.B. Povyshenie kachestva pressovoi posadki podshipnikov skol'jeniya iz spechennyh poroshkovyh materialov/I.B. Saiko, I.A. Zoriev, S.N. Shevcov//Izv. Volgogr. tehn. un-ta. Ser.: Progressivnye tehnologii v mashinostroenii. -Volgograd, 2006. -№ 4(19). -S. 56. -in Russian.
- Ovechkin I.V. Konstruktorsko-tehnologicheskoe obespechenie tribotehnicheskih harakteristik metallopolimernyh upornyh podshipnikov skol'jeniya/I.V. Ovechkin//Tr. I mejdunar. nauch.-tehn. konf. «Sovershenstvovanie suschestvuyuschih i sozdanie novyh tehnologii v mashinostroenii i aviastroenii», 1-3 iyunya 2009 g./YuNC RAN -OAO «Rostvertol». -Rostov n/D, 2009. -S. 235-244. -in Russian.