Особенности автоматизации загрузки сырьевой мельницы в составе систем АСДУ
Автор: Сибирцева Н.Б., Потапенко А.Н., Семернин А.Н.
Журнал: Известия Самарского научного центра Российской академии наук @izvestiya-ssc
Рубрика: Общие проблемы машиностроения
Статья в выпуске: 1-3 т.13, 2011 года.
Бесплатный доступ
В состав автоматизированных систем управления процессом измельчения входят локальные системы автоматизации загрузки мельниц, системы централизованных маслостанций и др. На базе этого типа локальных систем автоматизации представлены возможности их частичного объединения с целью автоматизации процесса загрузки мельниц.
Автоматизированная система мельницы, система смазки, контроллеры, автоматическое регулирование
Короткий адрес: https://sciup.org/148199695
IDR: 148199695
Текст научной статьи Особенности автоматизации загрузки сырьевой мельницы в составе систем АСДУ
Рис. 1. Обобщенная блок-схема АСДУ процессом измельчения
В структуру обобщенной АСДУ процессом измельчения в виде распределенного объекта управления (РОУ) входят следующие системы и элементы: локальные САР1, САР2, …, САР i , включающие локальные регуляторы ЛР1, ЛР2, …, ЛР i , датчики технологических параметров (Д1,…, Д n ), исполнительные механизмы (ИМ1, ИМ2,…, ИМ i ), регулирующие клапаны (РО1, РО2, … РО i ) и др. Кроме того, в состав АСДУ также входят промышленные контроллеры среднего уровня КСУ1, КСУ2 … КСУ i , связанные с локальными регуляторами ЛР i . В связи с большим количеством мельниц, задействованных в процессе измельчения и распределённостью оборудования каждой мельницы в АСДУ используется интеграция различных сетей, например, на базе RS-485, технологий Ethernet и др. В системе управления используются HUB i – устройства, служащие для
«разветвления» сигналов в сегменте сети. Через сети Ethernet (ЛВС) с помощью ПК i главные специалисты предприятия, операторы, технологи, разработчики системы на базе автоматизированных рабочих мест (АРМ) получают непосредственный доступ к информации от объектов. Удаленный доступ к обзору систем автоматизации возможен на базе Internet.
Верхний уровень АСДУ предназначен для наблюдения, регулирования, получения информации и архивирования данных по процессам, протекающим в распределенных системах и объектах. На этом уровне происходит взаимодействие диспетчера с различными процессами на основе человеко-машинного интерфейса, реализованного с помощью технологий SCADA-систем. На этом уровне АСДУ расположен ЦПУ на базе сервера с АРМ диспетчера, а также и другие АРМы. Автоматизация управления на нижнем уровне обеспечивает локальную стабилизацию или изменение технологических параметров процесса по заданной программе, постоянную или оптимальную производительность агрегатов или оборудования, а также автоматический контроль различных параметров, сигнализацию, регистрацию, блокировку и т.д. С появлением программируемых микропроцессорных систем получили распространение конфигурируемые распределенные системы DCS (Distributed Control Systems – распределенные системы управления) на базе различных типов контроллеров. Для этого уровня автоматизации характерны контроллеры универсальные, специализированные, программно-логического типа и др. Контроллеры с ПИД-регуляторами (на основе пропорционально-интегрально- дифференциального закона регулирования) вырабатывают выходные сигналы Yi, которые рассчитываются по формуле [3]:
Y = — • i X p
AE, 1 v
E + T--- + E, • At i Д i изм
A t изм T u i = 0
• 100%,
где Xp – полоса пропорциональности; Ei – отклонение; τД – постоянная времени дифференцирования; τи – постоянная времени интегрирования; ΔЕi – разность между двумя соседними измерениями Ei и Ei-1; Δtизм – время между n двумя соседними измерениями ti и h-1 ; ^ Ei -i=0
накопленная в i -й момент времени сумма отклонений регулируемой величины от заданной. Если какие-то из составляющих универсального закона регулирования (уравнение (1)) не используются, то регулятор становится пропорционально-интегральным (ПИ-регулятором), пропорциональным (П-регулятором) и т.п.
В состав локальных систем нижнего уровня АСДУ входят также САР для обеспечения смазки трущихся частей механизмов мельницы на основе централизованных мас-лостанций. Для определения поступления первичной информации от датчика давления, находящегося в одной из систем централизованной смазки, в автоматизированной системе загрузки мельницы выполним анализ особенностей функционирования основных систем смазки. Схема системы централизованной смазки мельницы с применением насосов высокого и низкого давления представлена на рис. 2.
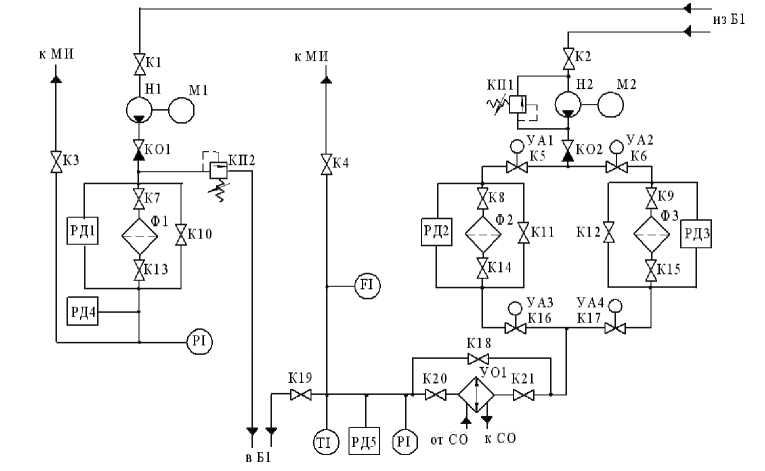
Рис. 2. Схема основной части маслосмазки подшипника мельницы
В исследуемом случае первичная информация, получаемая с датчиков давления в гидросистемах смазки мельницы, будет использована не только для локальных САР загрузки мельницы, но и будет доступна операторам этих мельниц. Обозначения элементов системы смазки подшипника на схеме (см. рис. 2) следующие: шаровые краны К1-К4, К7-К15, К18-К21, электроприводы М1 и М2 соответственно насосов высокого (ВД) Н1 и низкого давления (НД) Н2 мельницы, предохранительные клапаны КП1 и КП2, клапаны обратные КО1 и КО2, клапаны К5, К6, К16, К17 с соответствующими электромагнитными приводами УА1-УА4, маслофильтры Ф1-Ф3, реле перепада давления РД1-РД3, реле-давления РД4 и РД5, маслоохладитель УО1, приборы для измерения соответственно расхода FI, давления РI и температуры ТI. Дополнительные обозначения следующие: мельница МИ (подача мас-лосмазки к подшипнику мельницы), маслобак Б1 и связь с системой охлаждения СО масло-смазки. Уровень загрузки мельницы может контролироваться [4] по потребляемой мощности электродвигателя мельницы Р пр или по давлению маслосмазки в опорных подшипниках мельницы р м (рис. 3). Для мельниц само-измельчения стабилизация уровня загрузки барабана исходным материалом обеспечивается путём воздействия на частоту вращения привода питателя.
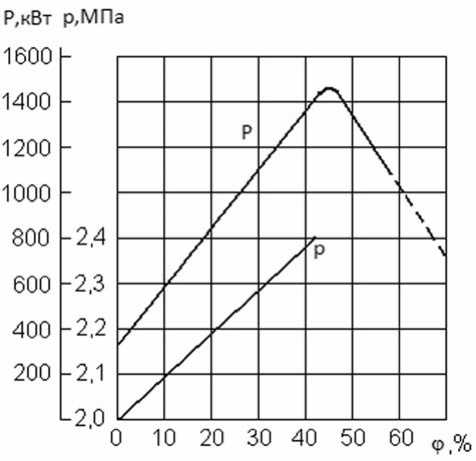
Рис. 3. Пример зависимостей Р пр и р м для мельницы самоизмельчения
Из статических характеристик можно выделить два канала регулирования «потребляемая мощность Рпр – частота вращения привода питателя» или «давление масла рм – частота вращения привода питателя». Анализ автоматизированной системы смазки мельницы показывает следующее. Во-первых, возможно получение первичной информации от датчика давления, находящегося в одной из систем централизованной смазки, для использования этой информации в автоматизированной системе загрузки мельницы, так как изменяется давление при изменении степени загрузки мельниц типа «Гидрофол» и других типов сырьевых мельниц. Во-вторых, для получения функциональной связи между загрузкой мельницы и давлением в гидросистеме насо-са/насосов систем централизованной смазки необходимо обеспечить стабилизацию расхода жидкого масла в системах смазки мельницы. В-третьих, необходимо предусмотреть компенсацию возмущающих воздействий в работе систем централизованной смазки с учетом нагрева или охлаждения масла в различные периоды года.
Основные контролируемые параметры процесса охлаждения входного подшипника мельницы с помощью централизованной системы смазки с учётом схемы на рис. 2, следующие (с учетом старта главного электродвигателя мельницы и при допустимых значениях): 1) входные:
у 1 – давление (расход) масла насоса ВД (больше минимального);
у 2 - давление (расход) масла насоса ВД (меньше максимального);
у 3 - давление (расход) масла насоса НД (больше минимального);
у 4 - давление (расход) масла насоса НД (меньше максимального);
-
2) выходные:
-
х 1 – температура подшипника мельницы (меньше максимального);
-
х 2 – насос ВД включён (более 3 мин.);
-
х 3 – насос НД включён (более 3 мин.);
-
х 4 – перепад давления на маслофильтре в системе насоса ВД (фильтр не засорён перепад давления меньше заданного);
-
х 5 – перепад давления на маслофильтре в системе насоса НД (фильтр не засорён перепад давления меньше заданного);
-
х 6 – температура масла в баке (больше минимальной);
-
х 7 – температура масла в баке (меньше максимальной);
-
х 8 – температура масла подшипника в системе подачи насоса НД (меньше максимальной);
-
х 9 – циркуляция (расход) масла в системе насоса НД;
-
х 10 – уровень масла в баке (больше минимального).
В локальных САР загрузки МИ разрабатывается подход для применения контроллера на базе ПИ-регулятора (уравнение (1) при т д = 0) с алгоритмом формирования управляющей команды на исполнительный механизм отличным от существующих, для которых структурная схема системы автоматизации ОУ имеет вид, показанный на рис. 4, при этом обозначения следующие:
Wп(p) - передаточная функция П-регулятора; Wи(p) - передаточная функция И-регулятора;
WHM(p) - передаточная функция исполнительного механизма;
Woс(p) - передаточная функция, например, датчика перемещения вала исполнительного механизма;
W po (p) - передаточная функция регулирующего органа;
Wov(p) - передаточная функция ОУ;
W д T п (p) - передаточная функция датчика технологического параметра.
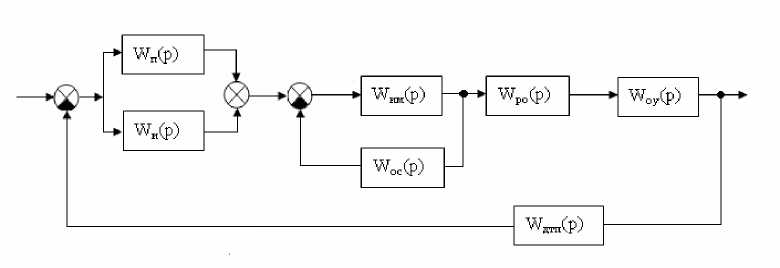
Рис. 4. Структурная схема промышленного ПИ-регулятора
ПИ-регулятор со структурой, как на рис. 4 (Wп(p) и Wи(p)), имеет не зависящие друг от друга параметры настройки к р и г и . Передаточная функция этого типа регулятора имеет следующий вид:
W™(p) = k p + 1 / г и р (2)
На практике широко применяется структура модернизированного ПИ-регулятора, реализующая закон регулирования в виде
Y ( t ) = kp
С т А
£ +--- f £ dt
Т '
V т ио 0 )
Здесь тио - принято называть постоянной времени изодрома или просто временем изодрома; £ - отклонение регулируемой величины ОУ от заданной.
Передаточная функция этого типа регулятора следующая:
W hh *(p) = К р ( г ио р + 1 )/ г ио р . (3)
Таким образом, ПИ-регулятор с WnH*(p) имеет взаимосвязанные параметры настройки постоянных регулятора в отличие от исходного. В целом эти регуляторы могут реализовать заданный закон регулирования, если объект управления типа теплового с ТЭНом для изменения температуры. Если ОУ иного типа и в структуре САР применяется исполнительный механизм, тогда для формирования управляющей команды необходимо учитывать динамические свойства этого исполнительного механизма. Как правило, коррекция осуществляется путём охвата исполнительного механизма (ИМ) отрицательной обратной связью на базе датчика перемещения вала ИМ. В разрабатываемой структурной схеме САР (см. рис. 4) для устранения датчика перемещения и модернизации алгоритма формирования управляющей команды вводится дополнительное устройство между ИМ и регулятором, позволяющее напрямую подавать управляющую команду от регулятора к ИМ и улучшающее качество регулирования.
Выводы: исследования процесса охлаждения подшипника мельницы в виде распределенного ОУ на основе математической модели как в [5] необходимы для стабилизации температуры жидкой смазки в трубопроводе магистрали системы маслосмазки, в которой расположен датчик давления, и в целом для системы регулирования уровня в МИ. Коммерциализация полученных результатов востребована предприятиями - производителями строительных материалов в Белгородской области, например, для сырьевых мельниц типа «Гидрофол», для ГОКов, например, для мельниц са-моизмельчения и др.
Список литературы Особенности автоматизации загрузки сырьевой мельницы в составе систем АСДУ
- Госман, А.И. Централизованные системы смазки для дробильно-измельчительного оборудования//Горная промышленность. 2004. №4. С. 29-32.
- Зябрев, М.А. Автоматизированные централизованные системы смазки горных и обогатительных машин/М.А. Зябрев, В.А. Зябрев, М.И. Шупиченко, М.В. Полянский//Материалы научно-практической конференции НПО «РИВС-2008». -СПб, 2008. С. 49-51.
- Компоненты автоматизации ОВЕН. Простой подход к современным решениям: каталог. 2007. 224 с.
- Троп, А.Е. Автоматическое управление технологическими процессами обогатительных фабрик/А.Е. Троп, В.З. Козин, Е.В. Прокофьев. -М.: Недра, 1986. 303 с.
- Сибирцева, Н.Б. Методы измерения уровня загрузки мельниц, основанные на физических процессах современных централизованных систем смазки/Н.Б. Сибирцева, А.Н. Потапенко, Н.А. Семилетов//Известия Самарского научного центра Российской академии наук. Т12. 2010. № 4(3). С. 694-697.