Особенности формирования структуры и трибологических свойств карбидосодержащих покрытий при плазменной наплавке
Автор: Жаткин Сергей Сергеевич, Паркин Анатолий Алексеевич, Климов Вадим Геннадьевич
Журнал: Известия Самарского научного центра Российской академии наук @izvestiya-ssc
Рубрика: Машиностроение и машиноведение
Статья в выпуске: 4-2 т.18, 2016 года.
Бесплатный доступ
Представлены результаты исследований структуры и износостойкости карбидосодержащих композиционных покрытий Micro-Melt NT-60 и WOKA PTA-6040 после плазменной порошковой наплавки в различных режимах.
Плазменная наплавка, износостойкость, микроструктура, микротвердость, рентгеноспектральный микроанализ
Короткий адрес: https://sciup.org/148205728
IDR: 148205728
Текст научной статьи Особенности формирования структуры и трибологических свойств карбидосодержащих покрытий при плазменной наплавке
Известно, что высокие механические характеристики деталей и изделий часто обеспечивается наличием в них карбидообразуюших элементов и их структурой. В настоящее время известна широкая группа твердых сплавов и композиционных материалов с карбидным содержанием, обладающих высокой твердостью и износостойкостью. В качестве способа формирования износостойких карбидосодержащих покрытий интенсивно применяется технология плазменной наплавки, характеризующаяся минимальным воздействием на заготовку и регулированием толщины наплавленного слоя в широких пределах.
В данной работе представлены результаты исследований влияния структуры плазменно-наплавленных композиционных материалов на основе карбида вольфрама Micro Melt NT-60 фирмы CARPENTER и WOKA PTA-6040 на износостойкость полученных покрытий.
Состав исходных наплавляемых порошков представлен в табл. 1.
МЕТОДИКИ ЭКСПЕРИМЕНТА
Наплавка на цилиндрические образцы из стали 19ХГНМА диаметром 52 мм и толщиной 15 мм проводилась на плазменной установке ARC-06В в защитном газе при токе дуги 70-100 А и расходе порошка 16 г/мин. Диаметр сопла плазмотрона составлял 2,4 мм. Микроструктуру и микроанализ зон плазменной наплавки исследовали на растровом электронном микроскопе JSM-6390LV/ LGS фирмы JEOL .
Испытания на линейный износ проводились локально в четырех участках кольцевой зоны на-
плавки (рис. 1) [1-2]. Точка 1 соответствует началу, а точка 4 – концу наплавленного кольца. Контртело было изготовлено из стали 40Х (закалка до HRC 46-48) в виде трубки внешним диаметром 6 мм и толщиной стенки 1 мм. Испытания проводились при нормальной нагрузке в 45 кгс в течение 10 минут с частотой вращения шпинделя 600 об/ мин. При испытаниях использовалась алмазная паста АСМ-3/2-НОМГ с алмазным порошком дисперсностью 2-3 мкм.
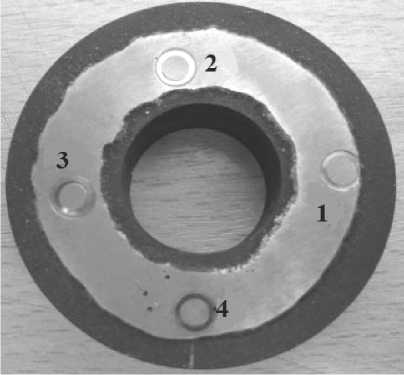
Рис. 1. Расположение зон трения:
1 – начало наплавки; 4 – конец наплавки
РЕЗУЛЬТАТЫ ИССЛЕДОВАНИЙ И ИХ АНАЛИЗ
Фотографии структуры зон наплавки порошковых материалов WOKA PTA-6040 и Micro-Melt NT-60 представлены на рис. 2.
В наплавленном слое наблюдается зона растворенных карбидов в никеле (в верхней части), а также седиментация карбидов, что наиболее заметно в покрытии WOKA PTA-6040 из-за их более крупных размеров, чем в Micro-Melt NT-60 . По данным проведенных измерений средний размер
Таблица 1. Химический состав WOKA PTA-6040 и Micro-Melt NT-60
Наименование материала |
Содержание, % по массе |
|||||||
Co |
Ni |
C |
Cr |
V |
Mo |
Si |
Карбид вольфрама |
|
Micro-Melt NT-60 |
0,5 |
35 (основа) |
1,6-2,9 |
0,35 |
0,45 |
0,8 |
^— |
60 |
WOKA PTA-6040 |
2,2 |
30 (основа) |
3,5-5,3 |
1,5 |
0,45 |
^— |
0,6 |
60 |
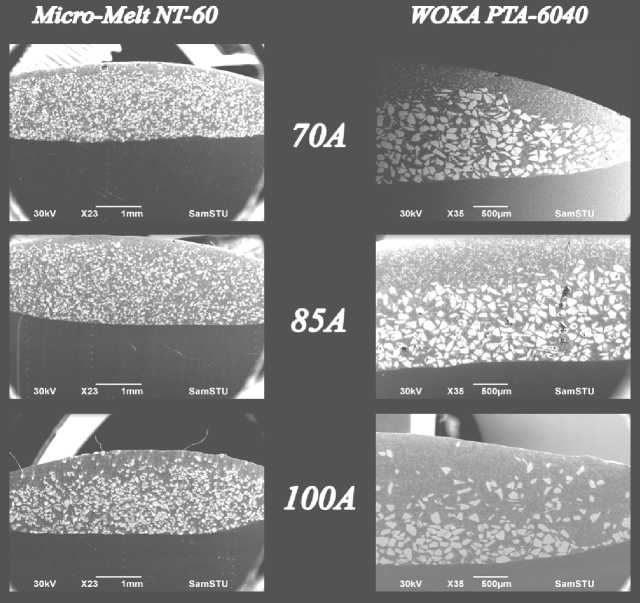
Рис. 2. Структура наплавленных покрытий WOKA PTA-6040 и Micro-Melt NT-60 в зависимости от тока плазменной дуги карбидов в покрытии Micro-Melt NT-60 составлял 70 - 90 мкм, а в WOKA PTA-6040 - 120 – 170 мкм.
Седиментация протекает активнее при токе дуги 100 А из-за более высокой температуры и меньшей вязкости никеля.
Процесс седиментации оказывает существенное влияние на износостойкость наплавленного материала, что подтверждается данными испытаний на послойный локальный износ покрытия WOKA PTA-6040 по высоте от верха зоны наплавки (табл. 2).
В целом с ростом тока дуги величина износа в рамках одного уровня трения по высоте наплавки возрастает, что обусловлено растворением и распадом карбидов вольфрама. При токах дуги 85А и 100 А в верхней части наплавленного валика износ максимальный, т. к. здесь температура нагрева максимальна и поэтому распад исходных карбидов и их растворение в никеле возрастают. Процесс седиментации также обедняет верхние слои зоны наплавки, где температура максимальна, а вязкость расплава минимальна.
В средней части наплавленного валика (отступ от верха валика – 1000мкм) при всех токах дуги износ уменьшился, что связано с уменьшением размеров карбидов вольфрама, увели-
Таблица 2. Величина износа WOKA PTA-6040 по высоте зоны наплавки
При токе плазменной дуги 100 А ближе к границе сплавления (низ зоны наплавки) концентрация карбидов (особенно ближе к центру наплавки), максимальна и, соответственно, износ минимальный.
Одной из особенностей наплавки плазменной дугой на торцевую поверхность цилиндрической заготовки является различие в характере нагрева внутреннего и внешнего края наплавляемой дорожки, что обусловлено различием в скоростях их движения при вращении образца и, как следствие, различием во времени нагрева, и, соответственно, температурой нагрева зоны наплавки. Экспериментально установлено, что величина износа существенно отличается по ширине наплавленной дорожки - она значительно больше на ее внутреннем крае, чем на внешнем [3]. В табл. 3 представлены результаты испытаний наплавленного Micro-Melt NT-60 в различных зонах (рис. 1) при токах плазменной дуги 70А, 85А и 100А.
Более высокий износ по внутреннему краю наплавленной дорожки обусловлен существенным его перегревом по сравнению с внешним краем, приводящему к более интенсивному распаду карбидов здесь. Аналогично с ростом тока дуги до 85-100 А из-за более интенсивного нагрева и распада карбидов происходит значительное увеличение величины износа. При этом снижается разброс его значений по внутреннему и внешнему краю наплавленной дорожки. При токах дуги 85А и 100А (рис. 2) произошло уменьшение плотности карбидов, что привело к увеличению величины износа наплавленных зон.
На износостойкость наплавленного материала оказывает существенное влияние целый ряд параметров, например, микротвердость поверхностного наплавленного слоя, величина ее разброса, концентрация и равномерность распределения карбидных частиц по наплавленному слою. На рис. 3 показаны наиболее характерные структура наплавленного материала CARPENTER MicroMelt NT-60 на отдельных участках 4-х зон трения образца в соответствии с рисунком 1 при токах плазменной дуги 70А, 85А и 100А. Зоны трения показаны слева направо от начала к концу наплавки.
Структура наплавленного материла при минимальном износе (рис. 3, а, зона трения 4) состоит из карбидов вольфрама среднего размера при их максимальной концентрации. В зоне №1 (начало наплавки) первичные карбиды вольфрама более крупные, а их концентрация невысокая и износ наплавленного материала здесь максимален.
Закономерность изменения износа от зоны №1 к зоне №4 при токе 85 А противоположна, то есть величина износа материала наплавки незначительно возрастает – от 20 мкм до 25 мкм за 10 минут испытаний, причем синхронно с уменьшением размеров карбидов вольфрама и их концентрации. Последнее обусловлено разогревом подложки в процессе наплавки, возрастанием скорости растворения карбидов в никелевой матрице и, соответственно, уменьшением эффективной поверхности карбидной фазы.
Таблица 3. Величина износа Micro-Melt NT-60 в различных зонах трения
№ зоны трения |
И 1 , мкм |
И 2 , мкм |
<И>, мкм |
Ц |
ДТоС |
I ц =70А |
|||||
1 |
58 |
29 |
43,5 |
0,11 |
10 |
2 |
29 |
27 |
28 |
0,09 |
11 |
3 |
15 |
33 |
24 |
0,09 |
7 |
4 |
8 |
5 |
6,5 |
0,071 |
8 |
<25,5> |
|||||
I ц = 85А |
|||||
1 |
51 |
20 |
35,5 |
0,1 |
10 |
2 |
50 |
22 |
36 |
0,1 |
11 |
3 |
55 |
23 |
39 |
0,11 |
7 |
4 |
58 |
25 |
41,5 |
0,1 |
8 |
<38> |
|||||
I ц = 100А |
|||||
1 |
62 |
21 |
41,5 |
0,077 |
8 |
2 |
65 |
15 |
40 |
0,069 |
6 |
3 |
59 |
13 |
36 |
0,054 |
5 |
4 |
56 |
12 |
34 |
0,046 |
8 |
<38> |
Примечание: И1 – усредненная величина износа внутреннего края наплавленной дорожки, И2 – усредненная величина износа внешнего края наплавленной дорожки; m - коэффициент трения, ∆ToС – изменение температуры в зоне трения
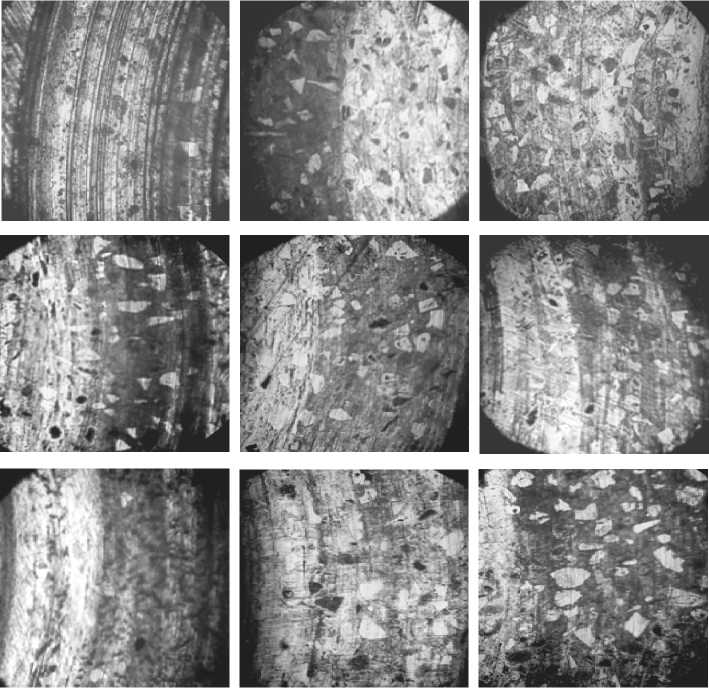
1 2 3
Рис. 3. Микроструктура и износ наплавленного материала CARPENTER Micro-Melt NT-60: а - ток плазменной дуги -70А; б - 85А; в - 100А; слева ^ направо - зоны трения 1 ^ 4
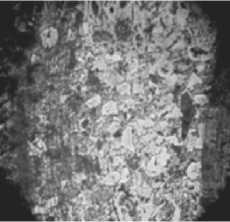
a
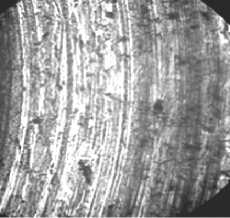
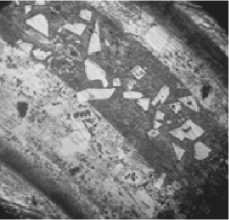
Износ наплавленного покрытия от зоны №1 к зоне №4 при токе наплавки 100 А уменьшается – от 21 мкм до 12 мкм за 10 минут испытаний, причем синхронно с увеличением размеров карбидов вольфрама и их концентрации. Данный фактор можно объяснить более интенсивным нагревом материала заготовки, соответственно уменьшением скорости охлаждения наплавленного материала и увеличением выделения и времени роста вторичных карбидов.
В целом в плазменно-порошковых наплавленных покрытиях возникает неравномерное распределение твердой карбидной фазы по объему зоны наплавки, то есть возникают участки наплавленного материала с различной структурой, соответственно, твёрдостью и износостойкостью. Указанный факт установлен и подтвержден экспериментально, табл. 3.
Сравнительная характеристика средней величины износа наплавленных материалов представлена в табл. 4.
В обоих случаях с ростом тока дуги средняя величина износа возрастает, но наиболее сильно это наблюдается для Micro-Melt NT-60. Повышенный износ последнего может быть обусловлен не только меньшим размером карбидов, но и их твердостью. По результатам измерения микротвердости установлено, что твердость карбидов в наплавленном WOKA PTA-6040 достигает 20002400 кг/мм2, в то время как в Micro-Melt NT-60 ее величина не превышает 800 – 1200 кг/мм2. При этом за счет растворения карбидов твердость связки в WOKA PTA- 6040 составляет 700-900 кг/ мм2, а в Micro-Melt NT-60 400-500 кг/мм2, что соизмеримо с твердостью стальной подложки в зоне
Таблица 4. Сравнительная характеристика средней износостойкости наплавленных покрытий
Глубина шлифа под зону износа 1000 мкм |
||||||
Ток дуги 70 А |
Ток дуги 85 А |
Ток дуги 100 А |
||||
Материал |
Средняя величина износа, мкм |
Скорость износа, мкм\час |
Средняя величина износа, мкм |
Скорость износа, мкм\час |
Средняя величина износа, мкм |
Скорость износа, мкм\час |
WOKA PTA-6040 |
20 |
120 |
21 |
128 |
27 |
159 |
Micro-Melt NT-60 |
26 |
156 |
38 |
228 |
40 |
240 |
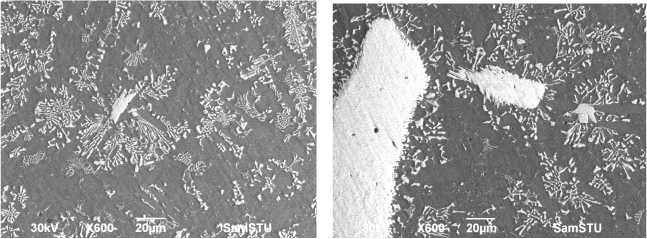
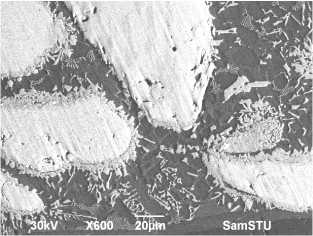
a
б
в
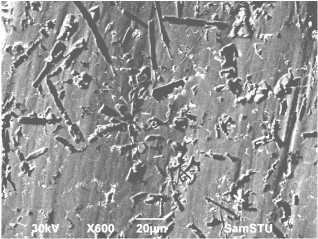
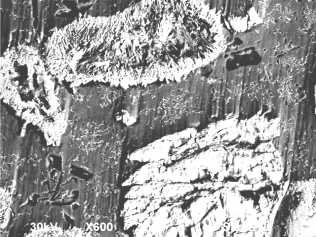
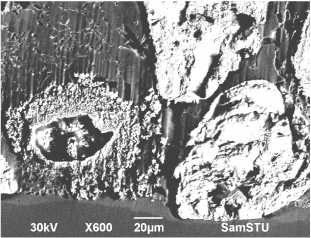
Список литературы Особенности формирования структуры и трибологических свойств карбидосодержащих покрытий при плазменной наплавке
- Жаткин С.С., Паркин А.А., Минаков Е.А. Влияние параметров плазменной дуги и материала заготовки на структуру и свойства наплавленного сплава Stellite 190 W//Известия МГТУ «МАМИ». 2013.№1(15). Т2, С. 38-46.
- Паркин А.А., Жаткин С.С., Минаков Е.А. Влияние структуры и свойств на износ покрытия Micro Melt NT-60 после плазменной порошковой наплавки//Известия Самарского научного центра Российской академии наук. 2011. Т. 13. №4(3). С. 847-852.