Особенности формирования сварного шва жаропрочного сплава ХН45ВМТЮБР в зависимости от режимов лазерной сварки
Автор: Баранов Дмитрий Александрович, Паркин Анатолий Алексеевич, Жаткин Сергей Сергеевич
Журнал: Известия Самарского научного центра Российской академии наук @izvestiya-ssc
Рубрика: Машиностроение и машиноведение
Статья в выпуске: 4-2 т.20, 2018 года.
Бесплатный доступ
В работе представлены результаты исследований влияния мощности и скорости движения лазерного пучка на форму и размеры сварного шва жаропрочного сплава ХН45ВМТЮБР после сварки СО2-лазером в различных режимах. Установлено, что при мощностях лазерного излучения выше 3 кВт во всем диапазоне скоростей сварки глубина сварного шва растет в основном за счет роста глубины парового канала. В сварных швах при мощности ЛИ 3 кВт и выше наблюдаются поры сферической формы и образование микротрещин в ЗТВ у границы сварного шва размерами от 0,1 до 0,3 мм. Показано влияние тепловложения на размеры и форму сварного шва.
Сплав хн45вмтюбр, лазерная сварка, жаропрочные сплавы, макроструктура шва, форма шва
Короткий адрес: https://sciup.org/148314020
IDR: 148314020
Текст научной статьи Особенности формирования сварного шва жаропрочного сплава ХН45ВМТЮБР в зависимости от режимов лазерной сварки
Жаропрочные сплавы, применяемые при производстве газотурбинных двигателей (ГТД), часто имеют пониженную свариваемость, что проявляется в образовании трещин и необратимом снижении жаропрочности [5-7]. Повышение качества сварных швов жаропрочных сплавов возможно за счет сокращения времени высокотемпературного нагрева путем снижения погонной энергии [3, 4]. В результате этого уменьшается растворение упрочняющих фаз в околошовной зоне и выпадения этих фаз в процессе охлаждения в шве [9, 10]. По базовой технологии узлы из жаропрочного сплава ХН45ВМТЮБР, такие как внутренний корпус (рис. 1), свариваются дуговой сваркой неплавя-щимся электродом в среде защитных газов (90% аргон+10% гелий) [8].
Дуговая сварка имеет ряд недостатков:
-
- повышенное тепловложение в свариваемый материал изделия;
-
- значительная зона термического влияния;
-
- возникновение больших сварочных напряжений, вызывающих коробление изделия;
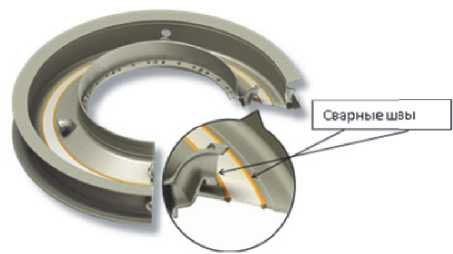
Рис. 1. Внутренний корпус
-
- низкий уровень автоматизации и более слабый контроль за параметрами сварки.
Альтернативой в этом случае может служить лазерная сварка, обладающая рядом достоинств:
-
- минимальное тепловое влияние, незначительная зона термического влияния и связанная с этим меньшая вероятность образования трещин и коробления изделия;
-
- высокое качество, равномерность, повторяемость и прочность металла сварных швов;
-
- гибкость в управлении лазерным пучком с возможностью использования волоконной оптики и сварки труднодоступных областей, не достижимых никаким другими методами;
-
- высокая скорость сварки и, соответственно, производительность процесса; простота и автоматизации процесса сварки [11-13].
На форму и размеры сварного шва влияют следующие факторы:
-
- тип источника нагрева (лазерное излучение, электронный луч, сварочная или плазменная дуга, газовое пламя и т.д.);
-
- мощность источника нагрева;
-
- скорость сварки;
-
- теплофизические свойства свариваемых материалов;
-
- исходная температура свариваемых материалов (сварка идет без или с подогревом материала);
-
- размеры и форма свариваемых заготовок.
В большинстве случаев лазерная и электроннолучевая сварка проводятся в режиме так называемого «кинжального» проплавления, при котором формируется глубокий сварной шов с верхней «грибовидной» частью [15]. Сварной шов в режиме кинжального проплавления образуется за счет испарения материала и образования плазмы на поверхности. Высокие температуры на поверхности и давление паров обуславливают расширение верхней области сварного шва по сравнению с его нижней частью, формируя тем самым «грибовидную» форму шва.
В данной работе приводятся результаты исследований влияния мощности и скорости лазерной сварки на размеры и форму сварного шва жаропрочного сплава ХН45ВМТЮБР.
МЕТОДИКА ИССЛЕДОВАНИЙ
Имитация сварки образцов проводилась на лазерном СО 2 -комплексе TruLaserCELL 7020 (TRUMPF - Германия) импульсно-периодическим излучением с фокусирующей линзой F = 270 мм. Защитным газом служил гелий с расходом 12 – 14 л/мин, который подавался специальным соплом впереди лазерного луча. Диаметр луча колебался в пределах 0,3 – 0,35 мм. Мощность лазерного излучения изменялась в пределах 2,5 - 4,0 кВт при скоростях лазерной сварки 16,6 мм/с; 25,0 мм/с; 33,3 мм/с и 41,6 мм/с. Свариваемые образцы (заготовки) размером 150х270мм толщиной 6,0 мм из сплава ХН45ВМТЮБР [14] вырезались из листового материала, рис. 2.
После сварки для исследований образцы по всей длине сварного шва разрезались на участки длиной 15 мм.
Химический состав и процентное содержание по массе легирующих элементов исследуемого сплава приведены в табл. 1.
Форма и размеры лазерных сварных швов определялись на основе данных металлографических исследований поперечных сечений сварных швов всех образцов. Металлографические исследования проводилось в двух поперечных сечениях: в начале и в конце каждого сварного шва при помощи металлографического микроскопа Axio Observer фирмы СarlZeiss.
РЕЗУЛЬТАТЫ ИССЛЕДОВАНИЙ И ИХ АНАЛИЗ
На рис. 3 показана схема обозначения параметров сварного шва. Результаты измерений параметров сварных швов в зависимости от режимов сварки представлены в табл. 2.
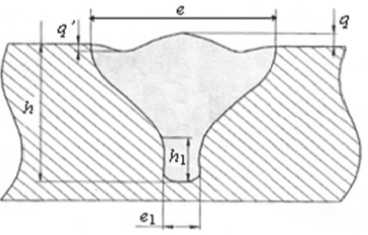
Рис. 3. Схема обозначения параметров лазерного сварного шва:
e – ширина сварного шва, e 1 – ширина корня сварного шва (парового канала); q – выпуклость сварного шва; q ’ – вогнутость сварного шва; h – глубина сварного шва; h 1 – глубина парового канала
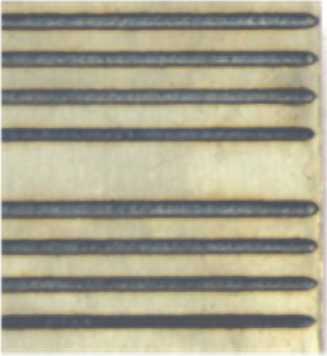
Рис. 2. Фрагмент образца из сплава ХН45ВМТЮБР со сварными лазерными швами
Из анализа данных таблицы 2 по формированию сварного шва сплава ХН45ВМТЮБР в зависимости от мощности и скорости движения лазерного пучка видно:
-
1. В указанном диапазоне скоростей ширина шва e падает с увеличением скорости лазерной сварки от 3.55 мм до 2,2 мм. В то же время, при скорости сварки v св = 41,6 мм/с ширина шва становится равной 2,1 – 2,2 мм во всем диапазоне мощностей лазерного излучения от 2,5 кВт до 4,0 кВт. То есть зависит, в основном, от скорости сварки или времени формирования «грибовид-ности» шва [15], которое определяет размер и форму сварного шва в верхней его части.
-
2. Глубина сварного шва h также уменьшается с ростом скорости сварки в диапазоне от 16,6 мм/с до 41,6 мм/с от 3,1 до 2,5 мм при мощности
Таблица 1. Химический состав сплава ХН45ВМТЮБР, ТУ14-1-1059-2004 [14]
-
3. При мощности ЛИ 3 кВт (плотность мощности 4,25×1010 Вт/м2) начинает резко возрастать глубина парового канала от 2,6 мм до 4,5 мм при мощности ЛИ 4 кВт.
-
4. Изменение параметров сварного шва в начале и в конце дорожки сварного шва наиболее заметны при мощностях лазерного излучения равным 2,5 - 3,0 кВт. При этом в большинстве случаев параметры сварного шва (прежде всего, ширина и глубина) возрастают в конце дорожки, что обусловлено ростом температуры нагрева материала в процессе сварки. С ростом скорости сварки до 33,3 мм/с и 41,6 мм/с различия в параметрах сварного шва в начале и в конце дорожки минимальны, поскольку за счет
Элемент |
Ni |
Cr |
Al |
Mo |
W |
Ti |
Nb |
Si |
Cu |
V |
Fe |
Содержание, % |
43,0-47,0 |
14,0-6,0 |
0,9-1,4 |
4,0-5,2 |
2,5-3,5 |
1,9-2,4 |
0,8-1,5 |
<0,3 |
<0,25 |
<0,1 |
Остальное |
Таблица 2. Зависимость параметров сварного шва от Р ЛИ и v св
Мощность лазерного излучения кВт |
||||||||||||||||
Р ди |
2.5 |
3,0 |
3,5 |
4,0 |
||||||||||||
Скорость сварки мм/с |
||||||||||||||||
Параметры, мм |
16,6 |
25 |
33,3 |
41,6 |
16,6 |
25 |
33,3 |
41,6 |
16,6 |
25 |
33,3 |
41,6 |
16,6 |
25 |
33,3 |
41,6 |
е н |
3,55 |
3,32 |
2,58 |
2,2 |
4,15 |
3,65 |
2,67 |
2,1 |
4,35 |
3,60 |
2,39 |
2,2 |
3,32 |
2,75 |
2,65 |
2,1 |
e K |
3.75 |
3.23 |
2,80 |
2,1 |
4,29 |
3,10 |
2,70 |
2,2 |
4,5 |
3,35 |
2,67 |
2,23 |
4,0 |
3,22 |
2,72 |
2,33 |
e 1H |
1,1 |
0,92 |
0,7 |
0,6 |
1,00 |
1,0 |
1,0 |
0,6 |
1,23 |
1,1 |
0,93 |
0,85 |
1,28 |
1,05 |
0,95 |
0,83 |
e 1K |
1,12 |
0,93 |
0,75 |
0,55 |
1,34 |
1,19 |
0,85 |
0,84 |
1,40 |
1,18 |
1,0 |
0,82 |
1,44 |
1,3 |
1,0 |
0,85 |
h H |
3,0 |
2,85 |
2,6 |
2,55 |
3,7 |
3,4 |
3,6 |
3,75 |
4,6 |
4,0 |
4,5 |
4,4 |
5,5 |
4,5 |
5,3 |
5,25 |
h K |
3,1 |
2,85 |
2,5 |
2,55 |
4,1 |
4,4 |
3,8 |
3,8 |
4,4 |
5,0 |
4,6 |
4,55 |
7,6 |
5,8 |
5,95 |
5,5 |
h 1H |
1,7 |
1,85 |
1,7 |
1,7 |
2,4 |
2,3 |
2,6 |
2,6 |
2,9 |
2,8 |
3,3 |
3,4 |
4,2 |
3,35 |
4,1 |
4,5 |
h 1K |
1,8 |
1,9 |
1,6 |
1,9 |
2,7 |
3,15 |
2,8 |
3,0 |
3,2 |
3,6 |
3,6 |
3,7 |
5,5 |
4,1 |
4,8 |
4,6 |
q H |
0,35 |
0,25 |
0,2 |
0,1 |
0,4 |
0,4 |
0,55 |
0,3 |
0,7 |
0,5 |
0,7 |
0,45 |
0,7 |
0,4 |
0,5 |
0,4 |
q K |
0,3 |
0,25 |
0,2 |
0,2 |
0,5 |
0,3 |
0,4 |
0,3 |
0,4 |
0,4 |
0,4 |
0,35 |
- |
0,1 |
0,45 |
0,45 |
Примечание: Нижний индекс Н в параметрах сварного шва соответствует началу дорожки сварного шва, а индекс К – соответственно концу дорожки
ЛИ 2,5 кВт. При этом, глубина парового канала практически не изменяется, а изменение размеров сварного шва связано с изменением верхней его «грибовидной» части. С ростом мощности ЛИ и уменьшением скорости сварки глубина проплавления возрастает и достигает своего максимума – более 6 мм при мощности 4,0 кВт и скорости сварки – 16, 6 мм/с.
Увеличение глубины сварного шва обусловлено ростом глубины парового канала h 1 , табл. 2.
сокращения времени воздействия глубина прогрева уменьшается.
В табл. 3 представлены результаты расчетов расхода мощности лазерного излучения P ЛИ на миллиметр глубины проплавления сварного шва и энергии лазерного излучения W ЛИ на длине дорожки l =80 миллиметров сварного шва при различных скоростях сварки и мощностях лазерного излучения в начале и конце шва.
Из табл. 3 видно, что расход мощности для проплавления 1 мм глубины при мощности лазерного излучения P ЛИ = 2,5 кВт с ростом скорости сварки от 16,6 мм/с до 41,6 мм/с увеличивается в 1,2 раза, в то же время расход энергии W на сварку шва длиной 80 мм уменьшается вначале сварного шва в 2,27 раза, а в конце шва - в 2,21 раза.
При мощностях лазерного излучения P ЛИ = 3,0, 3,5 и 4,0 кВт расход мощности для проплавления 1 мм глубины с ростом скорости сварки от 16,6 мм/с до 41,6 мм/с изменяется очень слабо, что может быть связано с незаметным уширением парового канала.
Однако изменение расхода энергии W на сварку шва длиной 80 мм остается значитель-
Таблица 3. Отношение P ЛИ /h , кВт/мм и энергии W ЛИ на 80 мм длины сварного шва
АНАЛИЗ ФОРМЫ, РАЗМЕРОВИ МАКРОСТРУКТУРЫ ЛАЗЕРНЫХ ШВОВ
На рис. 4 представлена структура основного металла.
В основном свариваемом сплаве наблюдается довольно однородная структура, форма зерен в основном четырехгранная ближе к ромбической с четкими границами.
На рис. 5 представлена макроструктура и форма сварных швов в конце свариваемой дорожки, полученных при скорости сварки v св = 16,6 мм/с и различных мощностях.
Структура сварного шва в верхней его области в переходной зоне от «грибовидной» [15] части к паровому каналу (рис. 5а) характеризуется неоднородностью и наличием крупной
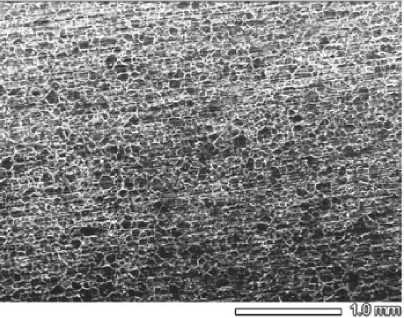
Рис. 4. Макроструктура основного металла сплава ХН45ВМТЮБР поры диаметром до 0,35 – 0,4 мм, образующейся после конденсации и кристаллизации металла в зоне парового канала [15]. Образование микротрещин в ЗТВ и сварном шве практически не наблюдается.
В конце сварного шва длиной 80 мм при мощности P ЛИ = 4,0 кВт и скорости сварки v св = 16,6 мм/с произошло сквозное проплавление образца толщиной 6 мм, при этом пор в сварном шве практически не наблюдается.
На рис. 6 представлены форма, размеры и дефекты сварных швов, полученных при мощ-
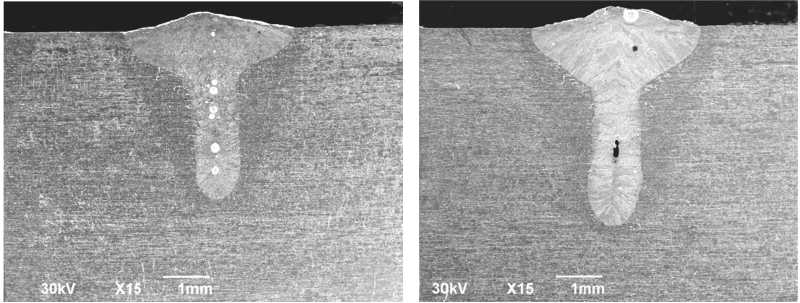
a
б
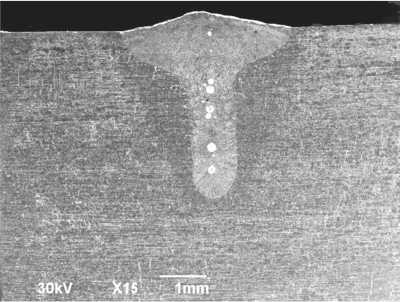
a
Рис. 6. Форма и размер лазерного сварного шва в начале шва: а – Р = 3,0 кВт, v св = 25 мм/с; б – Р = 3,5 кВт, vсв = 25 мм/с
Рис. 5. Макроструктура и форма лазерного шва в конце зоны сварки при скорости v св = 16,6 мм/с: а – P ЛИ= 3 кВт; б – Р = 4 кВт
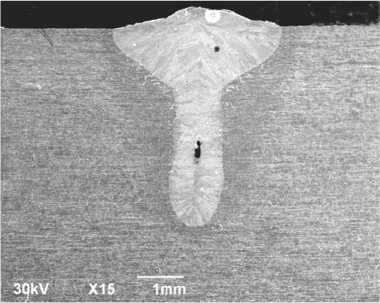
б
ности лазерного излучения Р = 3,0 кВт, Р = 3,5 кВт и скорости сварки v св = 25 мм/с.
В сварном шве, сформированном при мощности лазерного излучения 3 кВт, строго по оси сварного шва наблюдаются светлые дефекты сферической формы, в целом увеличивающиеся по размеру с приближение к корню шва. Данные дефекты, расположенные по оси сварного шва, уменьшают его прочность, особенно при динамических нагрузках.
В верхней части сварного шва, полученного при мощности лазерного излучения 3,5 кВт, имеется пора сферической формы размером до 100 мкм, в центральной части имеется вытянутый вдоль оси сварного шва дефект, напоминающий пору.
В целом, при обеих указанных мощностях лазерного излучения формируется выпуклый сварной шов.
В зоне термического влияния ниже «грибовидной» зоны наблюдается образование микротрещин, прорастающие до края сварного шва, что может быть связано с высоким уровнем напряжений, возникающих под действием значительных градиентов температур.
На рис. 7 представлены формы, размер и макроструктура сварных швов, сформированных при скорости сварки v св = 41.6 мм/с.
Сварные швы выпуклые, в которых наблюдаются поры различной формы, расположенные ближе к корню шва. В зоне термического влияния, как и в предыдущем случае, под «грибовидной» частью сварного шва возникают микротрещины, а в сварном шве (ближе к корню) наблюдаются поры.
Следует остановиться на формировании сварного шва в начале и в конце дорожки. На рис. 8 и 9 представлена форма сварного шва в начале и в конце дорожки при различных мощностях и скоростях движения лазерного пучка. При скорости 25 мм/с «грибовидная» форма сварного шва в начале дорожки более выражена, чем в конце дорожки (рис. 8) Отношение ширины сварного шва к ширине парового канала e / e1 составляет 3,65 в начале дорожки, в то время как в конце дорожки оно равно 2,6 (табл. 2). Очевидно, что уменьшение «грибовидности» верхней части сварного шва обусловлено повышенным тепловложением в конце дорожки и, соответственно, расширением парового канала при скоростях сварки 25 мм/с и ниже. При скорости сварки 41,6 мм/с различия в форме и параметрах сварного шва (рис. 9, табл.2) в начале и в конце дорожки практически отсутствуют, что обусловлено сокращением времени воздействия и, соответственно, уменьшением области прогрева материала.
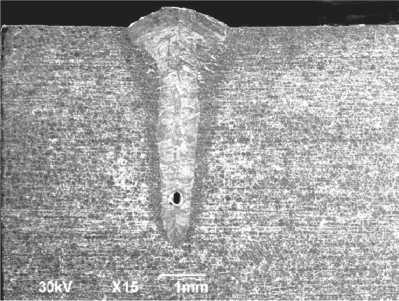
а
Рис. 7. а - конец шва P = 3 кВт, v св = 41,6 мм/с; б - конец шва - Р = 2.5 кВт, v св = 41.6 мм/с
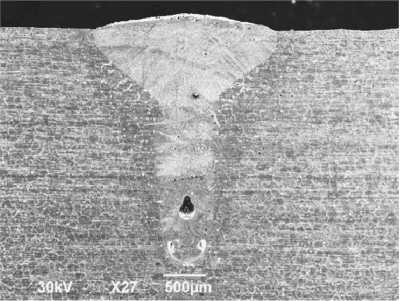
б
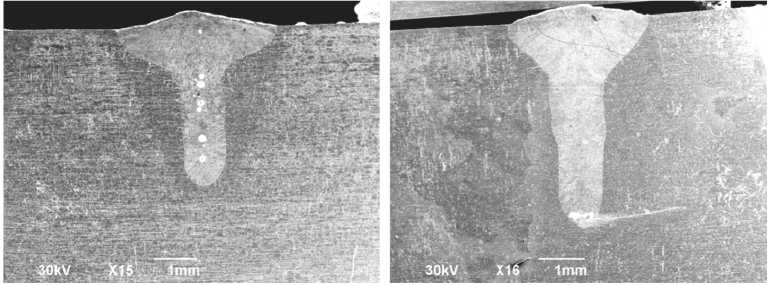
а
б
Рис. 8. Форма сварного шва при мощности ЛИ P ЛИ = 3 кВт и скорости сварки v св = 25 мм/с: а – начало сварного шва, б – конец сварного шва
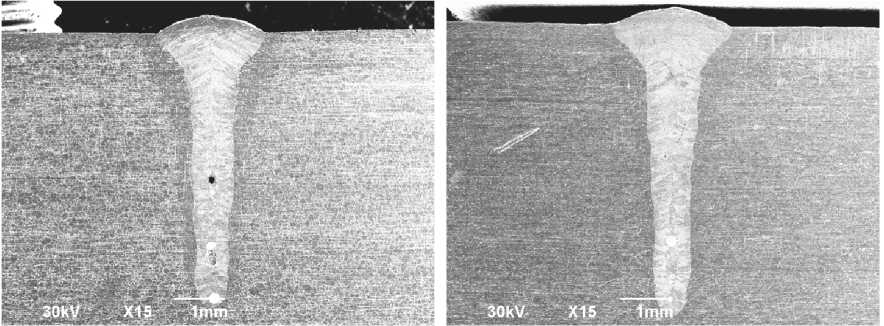
a
б
Рис. 9. Форма сварного шва при мощности ЛИ P ЛИ = 4 кВт и скорости сварки v св = 41,6 мм/с: а – начало сварного шва, б – конец сварного шва
ВЫВОДЫ
-
1. При лазерной сварке жаропрочного сплава ХН45ВМТЮБР практически во всех режимах лазерного воздействия, формируются выпуклые швы. Вогнутая поверхность шва возникает при сквозном проплавлении при скорости сварки v св = 16,6 мм/с и мощности Р ЛИ = 4.0 кВт.
-
2. Глубина сварного шва начинает расти при мощностях лазерного излучения выше 3 кВт во всем диапазоне скоростей сварки от 16,6 мм/с до 41,6 мм/с за счет роста глубины парового канала.
-
3. В сварных швах при мощности лазерного излучения 3 кВт и выше наблюдаются поры сферической формы и образование микротрещин в ЗТВ, размеры которых колеблются в пределах 0,1 - 0,3 мм.
-
4. Расход мощности лазерного излучения на проплавление 1 мм глубины сварного шва изменяется в пределах 0,7 – 1,0 кВт и в сильной степени зависит от мощности и скорости сварки v св . Наименьший расход мощности (0,53 – 0,73 кВт/мм) достигается при Р ЛИ = 4.0 кВт и скоростях сварки v св = 16,6 мм/с – 41,6 мм/с.
-
5. При скоростях движения лазерного пучка сплава ХН45ВМТЮБР 25 мм/с и ниже за счет роста тепловложения в материал в процессе сварки наблюдаются различия в форме и параметрах сварного шва в начале и в конце дорожки. С ростом скорости сварки выше 25 мм/с эти различия уменьшаются, что особенно заметно при скорости сварки 41,6 мм/с.
Список литературы Особенности формирования сварного шва жаропрочного сплава ХН45ВМТЮБР в зависимости от режимов лазерной сварки
- Сорокин Л.И. Свариваемость жаропрочных сплавов, применяемых вавиационных газотурбинных двигателей // Сварочное производство. 1997. № 4. С. 5-19.
- Баранов Д.А., Никитин К.В., Паркин А.А. и др. Структура сварного шва, сформированного при лазерной сварке Cr-Ni-сплава при производстве ГТД // Металлургия машиностроения. 2016. № 3. С. 46-48.
- Григорьянц А.Г., Шиганов И.Н., Мисюров А.И. Технологические процессы лазерной обработки: Учеб. пособие для вузов [под ред. А.Г. Григорьянца]. 2-е изд., стериотип. М.: Изд-во МГТУ им. Н.Э. Баумана, 2008. 664 с.
- M. Naffakh Shamanian, F. Ashrafizadeh, Dissimilar welding of AISI310 austenitic stain less steel to nickel-basedalloy Inconel657 // Journal of Materials Processing Technology, 209 (2009), P. 39.
- M. Naffakh Shamanian, F. Ashrafizadeh, Dissimilar welding of AISI310 austenitic stain less steel to nickel-basedalloy Inconel657 // Journal of Materials Processing Technology, 209 (2009), P. 39.