Особенности подхода при определении распределения плотности в прессуемых образцах из порошкообразных смесей
Автор: Потапенко А.Н., Требукова Н.С., Семернин А.Н.
Журнал: Известия Самарского научного центра Российской академии наук @izvestiya-ssc
Рубрика: Современные технологии в промышленности и строительстве
Статья в выпуске: 4-3 т.12, 2010 года.
Бесплатный доступ
Рассмотрен подход, связанный с определением областей с неравномерной плотностью в прессуемых образцах из порошкообразных смесей на основе вычислительных экспериментов и с возможностью его применения для проектирования пресс-форм.
Прессование, плотность, математическое моделирование, автоматизированная система
Короткий адрес: https://sciup.org/148199434
IDR: 148199434
Текст научной статьи Особенности подхода при определении распределения плотности в прессуемых образцах из порошкообразных смесей
Известно, что однородное уплотнение достигается только при всестороннем постоянном прессовании, что в теоретическом плане возможно только для жидкости. Анализ известных и специально поставленных экспериментальных исследований [2] распределения плотности ρ при одностороннем прессовании с учётом неподвижной формы показывает, что распределение ρ в целом не равномерно в вертикальном сечении образца с учётом приложения давления в этом же направлении, причём экспериментальные данные при одностороннем прессовании показывают, что распределение ρ может быть неравномерно не только в вертикальном сечении образца, но и в горизонтальном его сечении. Эти результаты о распределении плотности образца при одновременном двухстороннем давлении и с учётом неподвижной формы показывают, что распределение ρ более равномерно в вертикальном сечении образца, чем при одностороннем прессовании.
Цель данной работы заключается в разработке подхода для определения распределения плотности в сечениях прессуемых образцов из различных порошкообразных смесей, зависящей от многих факторов, в том числе и от способа прессования.
Существует подход [3, 4], позволяющий с помощью математического моделирования определять распределения плотности в горизонтальных и вертикальных сечениях образцов, полученных из порошкообразных смесей. С помощью вычислительного эксперимента имеется возможность получения картины распределения плотности в образцах, что позволяет в целом судить о их прочности. На основе подхода [3] были выполнены исследования распределения плотности образцов при одностороннем и двухстороннем давлениях с неподвижной формой для получения изделий с более равномерной плотностью с использованием следующего уравнения
# tJL + v '
9 x 2 9 t 9 x 2
^^^^^^B
f 9y 9 2 y ] 9 2 y
+ 2 a l ^ —- + v —— I--5- = 0 V 9 x 9 1 9 x J 9 1 2
где i 92 = E/p , E - модуль упругости смеси; p – плотность данной смеси; ψ – сжатие смеси в сечении x в момент времени t ; ν = η / ρ , причём η – коэффициент динамической вязкости смеси; 2 α = fξ/R , причём f – коэффициент трения смеси о стенки пресс-формы; ξ – коэффициент бокового распора порошкообразной смеси; R – гидравлический радиус пресс-формы.
Для учета внешнего воздействия на порошкообразную смесь при перемещении штампа h 1 ( t ) под воздействием усилия прессования происходит сжатие смеси ψ 1 ( t ), изменяющееся во времени, например, по S-образной характеристике. При этом принимается следующее нестационарное условие в виде зависимости [3]:
f
L i ( t ) = L о 1
V
1 + - 1 e ^ t / T 0
V 1 о J
\
J
где τ0 – постоянная времени, характеризующая процесс изменения ψ1(t) во времени; ψ0 – максимальное сжатие смеси. Результаты расчёта при прессовании силикатных образцов приве- дены на рис. 1 с учётом данных [3].
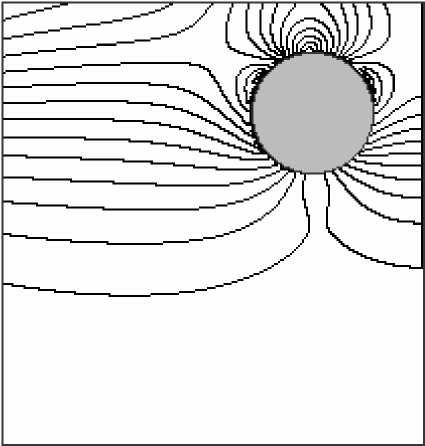
Рис. 1. Распределение линий равного уровня p * (представлено в относительных величинах)
Анализ результатов (рис. 1) показывает, что асимметричное расположение в верхней части пресс-формы вкладыша цилиндрической формы приводит к существенной концентрации p * в различных направлениях после прессования образца. При этом наблюдаются характерные зоны распределения плотности по бокам вкладыша и в его верхней и нижней частях. Такого типа концентрации плотности по различным сторонам вкладыша при последующей термообработке могут привести к появлению трещин, а возможно даже к разрушению образца с учётом зоны распределения плотности по вкладышу вблизи его боковой поверхности. Таким образом, имеется возможность определения областей с неравномерной плотностью при прессовании полуфабрикатов, особенно это важно для элементов приборостроительной промышленности, например, при прессовании различных элементов для приёмопередающих устройств, телекоммуникационных систем и др. Однако определить распределение плотности, например, в керамических полуфабрикатах после прессования в вертикальных и горизонтальных сечениях весьма сложно, причём как с помощью экспериментальных исследований, так и на основе вычислительных экспериментов. Это связано с тем, что для вычислительных экспериментов не определены постоянные коэффициенты, входящие в уравнение (1). Коэффициенты предлагается определять и корректировать в процессе производства на основании опытных данных. Для получения такой информации необходимо использовать современные подходы автоматизированного мониторинга исследуемых процессов на базе автоматизированных систем нижнего уровня, входящих в состав многоуровневой автоматизированной системы управления технологическим процессом (АСУТП) производства керамических изделий.
Структура АСУТП (рис. 2) среднего и верхнего уровней содержит контроллеры среднего уровня КСУi, … КСУj, связанные с контроллерами регулирующих устройств РУi, …, РУn нижнего уровня на основе интерфейса RS-485, устройства для «разветвления» сигналов в сегменте сети HUBBi, …, HUBj. С учётом территориально-распределённого оборудования при производстве керамических изделий в АСУТП используется интеграция различных сетей, например, на базе RS-485 и технологий Ethernet локальной вычислительной сети (ЛВС). В структуре системы имеются автоматизированные рабочие места (АРМ) специалистов предприятия АРМk и операторов управле- ния распределёнными объектами АРМi,…, АРМj (туннельным сушилом, туннельной печью, гидравлическим прессом и др.), центральный пульт управления ЦПУ на базе сервера с АРМ диспетчера, персональные компьютеры ПКy,…, ПКn в сети ЛВС и персональные компьютеры ПКi,…, ПКm в сети Internet с учётом возможного удалённого доступа к информации АСУТП и др.
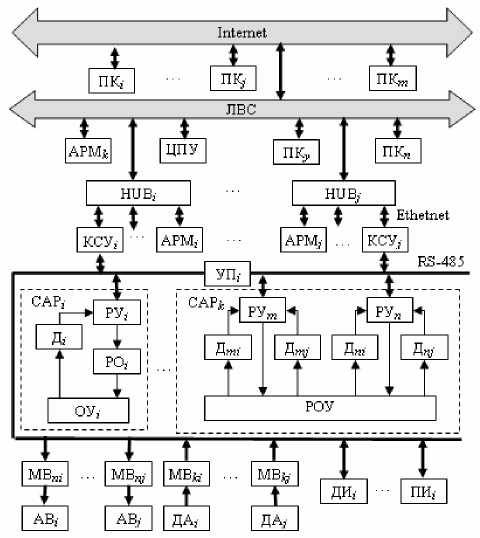
Рис. 2. Блок-схема АСУТП производства керамических изделий
Структура АСУТП нижнего уровня содержит следующие элементы, входящие в состав локальных систем автоматического регулирования САРi,…, САРk (см. рис. 2): датчики технологических параметров Дi, …, Дnj, объекты управления ОУi (для процесса производства шамотного огнеупорного кирпича – это туннельное сушило, туннельная печь, гидравлический пресс двойного действия (РОУ) и др.), регулирующие устройства РУi, …, РУn на базе контроллеров, регулирующие органы РОi. В автоматизированной системе предусмотрено управление типа старт/стоп агрегатами или оборудованием АВi,…, АВj системы через модули ввода/вывода аналоговых и/или дискретных сигналов МВni, …, МВnj, а также применение автоматизированной системы мониторинга на базе аналоговых датчиков технологических параметров ДАi,…,ДАj через модули вво-да/вывода аналоговых сигналов МВki, …, МВkj, «интеллектуальных» датчиков ДИi и «интеллектуальных» измерительных приборов ПИj и др. В структуре АСУТП на нижнем уровне используется промышленная сеть на основе RS485, в которой установлены усилители-повторители сигнала УПi.
На нижнем уровне АСУТП для исследования особенностей процесса прессования керамических изделий из порошкообразных смесей в структуру САР k включаются дополнительные датчики для экспериментальных исследований в виде быстродействующих оптических линейных энкодеров ДИ k и датчиков давления ДИ m типа «Метран-150». Датчики давления ДИ m входят соответственно в контуры регулирования РУ m верхнего прессующего механизма и контуры регулирования РУ n нижнего прессующего механизма гидравлического пресса. Эти датчики установлены в гидравлических системах низкого и высокого давления соответственно для перемещения верхнего и нижнего штампов. Линейные энкодеры ДИ k установлены с учетом перемещения верхней траверсы со штампом и прессующей траверсы с нижним штампом относительно неподвижных колонн гидравлического пресса. Первичная информация с линейных энкодеров ДИ k и датчиков давления ДИ m , являющихся датчиками «интеллектуального» типа, поступает в систему автоматизированного мониторинга АСУТП.
Экспериментальные исследования в натурных условиях на базе автоматизированных систем нижнего уровня АСУТП, на основе «интеллектуальных» датчиков технологических параметров, осуществляющих непрерывно или с минимальным интервалом усреднения измерение параметров процесса, а затем с помощью контроллеров КСУ, осуществляющих в заданном цикле интервала усреднения круглосуточный сбор измерительных данных с этих датчиков, накопление, обработку и передачу их в систему автоматизации, будет получена информация, необходимая для углублённого исследования формуемых с помощью гидравлических прессов керамических изделий из порошкообразных смесей, а также для определения и коррекции коэффициентов в уравнении (1). Следует отметить, что при прессовании полуфабрикатов необходимо учитывать способ прессования. Результаты [3] показали, что характер распределения ρ более равномерен в вертикальном сечении образца при двухстороннем давлении, прикладываемом последовательно, чем при одностороннем, т.е. такой метод прессования является наиболее предпочтительным. Полученные результаты согласуются с экспериментальными данными [2].
Выводы: для получения практических результатов с учётом особенностей процессов прессования полуфабрикатов необходимо развивать математическую модель [3] в направлении её применения для различных порошкообразных смесей. В настоящее время известны постоянные коэффициенты только для прессования силикатных изделий. Важно разработать методику экспериментального определения распределения ρ в образцах с выходом на вычислительный эксперимент.
Список литературы Особенности подхода при определении распределения плотности в прессуемых образцах из порошкообразных смесей
- Зейфман, М.И. Изготовление силикатного кирпича и силикатных ячеистых материалов/М.И. Зейфман. -М.: Стройиздат, 1990. 184 с.
- Hulsenderg, D. Maschinelle Formgebung von Keramic/D. Hulsenderg, H-G. Kruger, T. Rothis, G. Ferriere. -VEB, Deutscher Verlag fur Grundstoffindustrie, Leipzig, 1980. (Механизация процессов формования керамических изделий/Д. Хюльзенберг, Х-Г. Крюгер, Т. Рётиг, Г. Ферриер. -М.: Стройизд., 1984. 263 с.
- Potapenko, A.N. Modeling and Optimization Possibilities for the Process of Compaction of Objects with Cavities/A.N. Potapenko, A.G. Titov, Potapenko E.A.//In a book: Materials and Processing Trends for PM, Components in Transportation. -Munich, Germany: EPMA, 2000. V. 1. P. 102-110.
- Ломакин, В.В. Автоматизация производства силикатного кирпича на базе программно-аппаратных комплексов управления/Автореф. дис. канд. тех. наук: спец. 05.13.06. -Белгород, 2002. 18 с.