Перспективные способы подготовки литейных графитов
Автор: Мамина Л.И., Гильманшина Т.Р., Беляев С.В., Королева Г.А., Лыткина С.И.
Журнал: Журнал Сибирского федерального университета. Серия: Техника и технологии @technologies-sfu
Статья в выпуске: 4 т.7, 2014 года.
Бесплатный доступ
Разработаны и впервые применены отдельные (обогащение, десульфурация и окисление) и комплексные способы повышения качества скрытокристаллического графита. Даны рекомендации использования разработанных технологий в зависимости от дальнейшей области применения графита.
Скрытокристаллический графит, обогащение, десульфурация, окисление, комплексные технологии подготовки графита
Короткий адрес: https://sciup.org/146114864
IDR: 146114864
Текст научной статьи Перспективные способы подготовки литейных графитов
Красноярский край имеет богатые углеродом (в среднем 83 %) месторождения графита: Фатьяниховское, Ногинское и Курейское. Основным минералом в этих рудах является графит, второстепенными – нерудные минералы, сульфиды и углистое вещество. Элементный и минералогический состав исследуемого графита представлен в табл. 1.
Графит Курейского месторождения представлен плотными тонкорассланцованными и массивными разностями графита. Сланцеватость обусловлена чередованием матовых слоев скрытокристаллического графита с прослойками мелко- и крупночешуйчатого графита, которые выглядят более блестящими. Порода легко раскалывается по плоскостям сланцеватости на плитки, поверхность которых имеет довольно яркий полиметаллический блеск.
Большую часть запасов графита составляет разновидность руд массивной или почти массивной текстуры. Сланцеватость либо не выражена совершенно, либо едва заметно намечается немногочисленными участками одинаково ориентированных чешуек графита или параллельными друг другу линзами сульфидов и других зольных минералов. Распределяются эти минералы по всем классам крупности. Содержание сростков графита с примесями уменьшается только в классе – 0,08 мм, а это говорит о том, что требуется тонкое измельчение руды перед флотацией. Наличие таких сростков проявляется практически во всех классах крупности [1–3].
Высокое содержание зольных примесей исключает возможность использования графита в отраслях, где требуется повышенная чистота – для производства электротехнических, антифрикционных изделий, графитоколлоидных препаратов, смазочно-охлаждающих жидкостей, электродов, тиглей, футеровок, форм и т.д.
Таблица 1. Химический и минеральный состав графита ГЛС-2 (К)
Марка графита |
Зольность, % |
Химический элемент, % |
Минеральный состав |
||||||
Fe |
S |
Si |
Al |
Ca |
K |
Ti |
|||
ГЛС-2 (К) |
15-20 |
5,6 |
1,0 |
1,8 |
1,1 |
2,2 |
0,7 |
0,16 |
кварц (SiO 2 ); кальцит (CaCO 3 ); сульфит железа (FeS); мусковит (Si 3 AlO 10 (OH) 2 ); каолинит (Al 2 Si 4 O 5 (OH) 4 ) |
– основные операции;
– вспомогательные
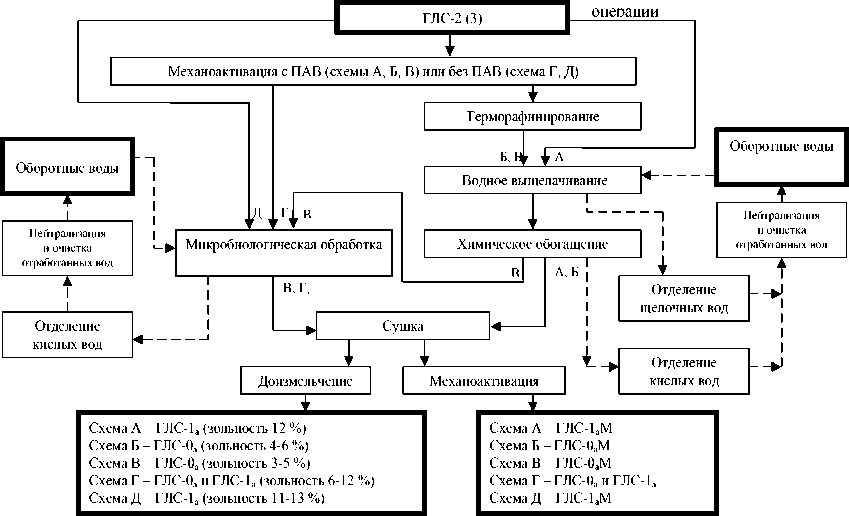
Рис. 1. Схемы обогащения скрытокристаллического графита
Однако применение традиционных технологий для скрытокристаллического графита оказалось практически невозможным из-за его текстурно-структурных особенностей.
Повышение качества такого графита связано с поиском новых нетрадиционных способов его обогащения. Поэтому нами для скрытокристаллического графита были разработаны такие способы обогащения, как флотационный, механоактивация, микробиологическое выщелачивание, химическое обогащение, паровоздушный, окислительное выщелачивание и их сочетания (рис. 1).
Разработанные технологии позволяют снизить зольность скрытокристаллического графита с 20–25 до 1–10 % в зависимости от области его применения.
Качество литейного графита определяется не только величиной зольности, но и составом зольных компонентов. Наиболее вредная примесь – сера, препятствующая графитизации чугуна, понижающая характеристики прочности и пластичности, уменьшающая химическую – 463 –
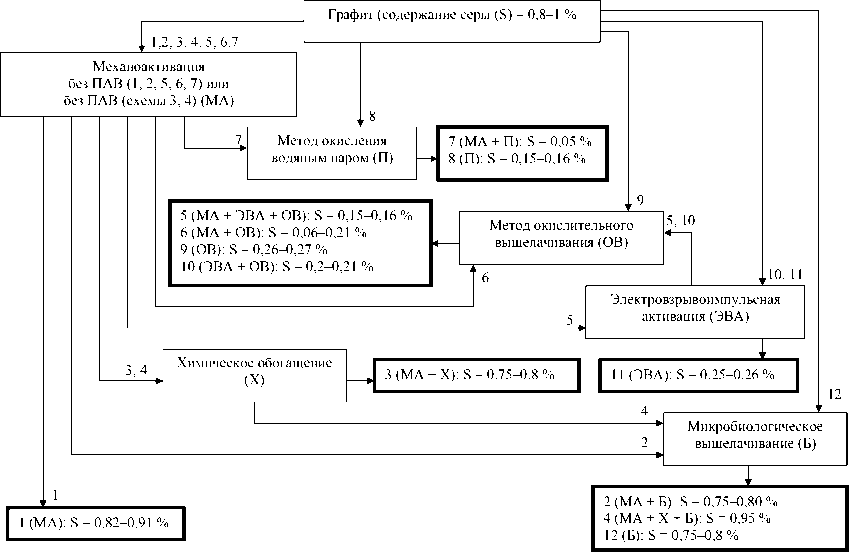
Рис. 2. Схемы десульфурации графита: 1–12 – номера технологических схем десульфурации стойкость чугуна. В связи с этим нами были разработаны технологии десульфурации скрытокристаллического графита (рис. 2).
Полученные данные свидетельствовали, что предварительная активация значительно интенсифицирует все последующие процессы извлечения серы из графита, более полно раскрывая ее из частиц пирита, пирротина и халькопирита. Комплексные методы десульфурации графита (механоактивация + паровоздушный метод; механоактивация + паровоздушный метод + окислительное выщелачивание; электровзрывоимпульсная активация + окислительное выщелачивание; механоактивация + электровзрывоимпульсная активация + окислительное выщелачивание) позволяют снизить содержание серы до 0,05 %.
При исследовании химического состава графита было отмечено, что наряду со снижением содержания серы уменьшается зольность образцов графита.
В последнее время много исследований направлено на получение окисленного и расширенного графитов.
Одним из перспективных направлений получения высококачественного графита является его окисление и расширение. Ранее проведенные работы показали эффективность применения новых его форм в составах противопригарных покрытий и в коагуляционно-сорбционных составах для очистки отработанных технических вод [4].
В графите, как и в ряде других кристаллических структур, прочна связь атомов внутри слоя, но сами слои связаны более слабыми силами, ван-дер-ваальсовыми. В такие слоистые кристаллы можно ввести дополнительные атомы или молекулы, которые раздвигают слои исходного кристалла. В результате образуются структуры, состоящие из чередующихся исхо- – 464 –
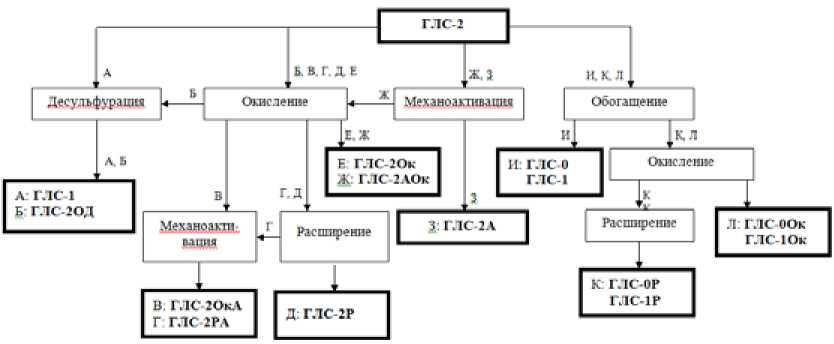
Рис. 3. Схемы комплексных технологий получения новых марок графита дных слоев и новых слоев введённых атомов или молекул. Эти соединения получили название «интеркалированные соединения внедрения», сам процесс введения дополнительных групп – «интеркалирование», вещества, внедренные в межплоскостное пространство графита, – «ин-теркалат» [5].
Поэтому был разработан ряд комплексных технологий на основе способа окисления и расширения графита (рис. 3).
В целом, любой из предложенных способов впервые применен в практике обогащения графита. Приоритет каждого из них определяется областью его применения. Так, для графитовых изделий, работающих в экстремальных условиях, необходим низкозольный графит с содержанием серы до 0,05 %. Для получения низкозольного графита лучше всего использовать комплексный механохимический способ с последующим микробиологическим выщелачиванием, что приводит к снижению зольности до 3–5 %, а для содержания серы до 0,05…1 % – ОВ-метод с предварительной механоактивацией. Для получения графитов, обладающих повышенной сорбционной емкостью, можно использовать окисление и расширение. Объединяя эти способы в единый техпроцесс очистки графита, мы можем получить графит необходимого количества для каждого конкретного вида продукции [6].