Подготовка производства блочно - модульных фрез с использованием 3D - прототипирования
Автор: Попок Н.Н., Портянко С.А.
Журнал: Вестник Витебского государственного технологического университета @vestnik-vstu
Рубрика: Технология и оборудование легкой промышленности и машиностроения
Статья в выпуске: 1 (40), 2021 года.
Бесплатный доступ
Объект исследования - подготовка производства блочно - модульных фрез с использованием 3D - прототипирования. Целью работы является выработка рекомендаций по подготовке производства с использованием 3D - прототипирования; изготовлению экспериментальных образцов БМФ. Рассматриваются основные конструктивные элементы и схема формирования блочно - модульных фрез, проанализированы формы корпусных модулей и стружкоотводящих канавок, а также методы изготовления фрез, приведены технологический маршрут 3D - печати блоков резцовых и корпусных модулей и технологическая схема сборки фрез, дана оценка соответствия параметров точности размеров макетов фрез заданным на чертеже и приведены рекомендации по использованию марок пластиковых материалов для изготовления макетов фрез.
Моделирование, подготовка производства, производство, блочно-модульная фреза, технологический маршрут, 3d-прототипирование, макет
Короткий адрес: https://sciup.org/142231211
IDR: 142231211 | DOI: 10.24412/2079-7958-2021-1-94-106
Текст научной статьи Подготовка производства блочно - модульных фрез с использованием 3D - прототипирования
Полоцкий государственный университет
В связи с диверсификацией и кастомизацией выпускаемой машиностроительными предприятиями продукции возрастают требования по сокращению временных и финансовых затрат на подготовку производства, поэтому выработка рекомендаций по подготовке производства с использованием 3D-прототипирования и изготовлению экспериментальных образцов является актуальной темой исследований. Предлагаются различные организационные формы технологических процессов – типовые, групповые, гибкие и мобильные [1], основанные на принципах унификации, модульности и автоматизации быстро-перестраиваемого оборудования и оснастки; учитываются изменения в методологии научных исследований процессов (научная подготовка), связанные с широким использованием элек- тронных средств, искусственного интеллекта и т. п. [2, 3, 4, 5, 6, 7]. Одним из перспективных направлений совершенствования конструкторской и технологической подготовки производства является применение 3D-моделей (макетов) экспериментальных образцов продукции, получаемых послойным синтезом (аддитивные технологии) [8, 9, 10, 11]. Рассмотрим некоторые особенности использования 3D-макетирования экспериментальных образцов на примере подготовки производства сборной технологической оснастки – блочно-модульных фрез.
Основная часть
Предлагаемые к производству конструкции сборных режущих инструментов включают блоки и модули, из которых формируются блочно-модульные фрезы (БМФ) различных типов по схеме на рисунке 1.
Формирование БМФ предусматривает выбор пластины режущей (ПР) исходя из формы обрабатываемой поверхности и конструктивного элемента детали, свойств материалов, режимов обработки и т.д. ПР устанавливается в блок резцовый (БР), отличительной особенностью которого является [12] технологичность присоединительных (базирующих) поверхностей державки – выполняются открытыми, для установки ПР и зажимного элемента в виде клиноприхвата. БР в свою очередь устанавливается в модуль корпусной МК по цилиндрическим (базирующим) поверхностям и зажимается или прихватным, или одно-двухклиновым механизмами. МК может быть снабжен модулем балансировочным (МБ), включающем или эксцентриковые втулки для установки блоков резцовых, или заглушки-грузики, устанавливаемые в корпусном модуле, или балансировочные кольца со спиральными пазами и шариками, а сам МК с помощью модуля присоединительного (МП) в виде державки, оправки, хвостовика и т. п. устанавливается в резцедержателе, шпинделе, палете, инструментальном магазине и т. п. станка. Преимущество предлагаемой системы сборных режущих инструментов по сравнению с аналогами состоит в использовании унифицированного БР, который может быть установлен в различные типы режущих инструментов (токарные, осевые, фрезерные, расточные и т. д.), что обеспечивает сокращение финансовых и временных затрат как на этапе изготовления, так и на этапе эксплуатации режущего инструмента.
Однако при внедрении в производство этой системы сборных режущих инструментов требуется тщательная отработка конструкций и тех-

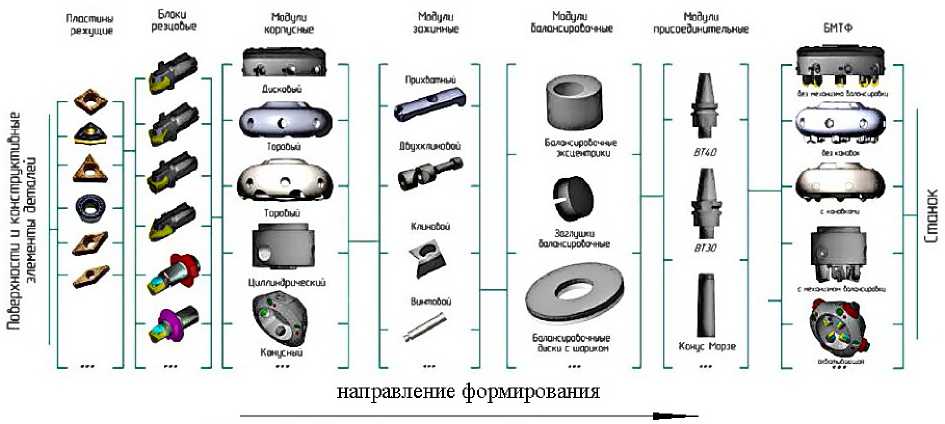
Рисунок 1 – Схема формирования блочно-модульных фрез
нологий их изготовления. Поэтому предлагается включать в этапы конструкторской и технологической подготовки производства БМФ макетирование экспериментальных образцов на 3D-принтере. Причем на этих этапах могут быть изготовлены конструкции из различных материалов – пластиковых и металлических, а также их комбинации, применены при изготовлении традиционные, субтрактивные, аддитивные и «гибридные» технологии. Была поставлена задача спроектировать и изготовить державки БР и МК различных форм и из различных пластиковых материалов, провести анализ полученных экспериментальных образцов и оценить влияние на полученные размеры образцов усадки материала, и с учетом этого предложить новые конструкции БМФ.
Проведенный анализ конструкций резцовых блоков, картриджей, резцовых вставок и т.д. показал, что используется различная конфигурация корпусов. Присоединительные поверхности и конструктивные элементы блоков резцовых выполняются цилиндрическими, коническими, плоскими, с рифлениями и т. п.; в поперечном сечении могут иметь вид окружностей, некруглых и гранных элементов, овалов, прямоугольников, квадратов, трапеций и т. п.. Исходя из принципа технологичности конструкций резцового блока при его изготовлении и сборке были выбраны цилиндрические присоединительные поверхности державки для установки в модуль корпусной и открытые прямоугольные пазы для установки пластины режущей и модуля зажимного.
Возможные варианты конструкций модулей корпусных предложены в таблице 1 (столбец 2). Учтены формулы, описывающие формы МК (столбец 3), и направления потоков смазочно-охлаждающей технологической среды (СОТС) при вращении МК (столбец 4). Последовательно рассмотрены варианты исполнения МК от простых форм (№ п/п 1–6 – диск, цилиндр и т. д.), до их комбинации (№ п/п 7–14). При этом учитывались требования, с одной стороны, по функциональному назначению фрез – необходимость эффективного резания и размещения в МК таких конструктивных элементов, как БР, МЗ, МБ, МП, ограничения их габаритных размеров, и выполнения стружко-потокоотводящих канавок технологичными методами, а, с другой стороны, по максимальному обеспечению обтекаемости форы МК смазочно-охлаждающей технологической средой, учитывающей высокую частоту вращения фрез на современных станках с ЧПУ (порядка 10-40 тыс. мин1). На основании результатов моделирования работы фрез различных форм установлено, что наиболее предпочтительными формами обтекаемости являются формы в виде сочетания двух торовых поверхностей (№ п/п 14).
Для отработки конструкций фрез и технологий их изготовления были отпечатаны макеты корпусов в виде сочетания цилиндров, дисков, усеченных конусов и сопрягаемых торов (рисунок 2).
Исследования макетов БМФ на этапе научной подготовки производства позволяют оценить эргономические и аэродинамические свойства фрез; определить преимущества и недостатки технологии сборки; трудоемкость конструкторской и технологической подготовки производства традиционными, «гибридными» методами и с использованием 3D-печати. Структурная схема выбора методов изготовления БМФ представлена на рисунке 3.
Эта схема включает выбор методов: традиционного (Т), заключающегося в механической обработке металла, аддитивного (А) – 3D-печа-ти из пластикового материала с последующей постобработкой. Сочетание (Т) и (А) методов обеспечивает изготовление фрез «гибридным» (Г) методом, при котором учитывается не только функциональное назначение конструкций фрез, но и возможность взаимозаменяемости материалов конструктивных элементов в различных комбинациях, например, пластиковый корпус и металлические блоки резцовые. Данная схема отражает вариативность принятия инженерных решений на этапах конструкторской и технологической подготовки производства. Использование традиционных методов в единичном и мелкосерийном производствах приводит к увеличению стоимости подготовки производства. Когда же изделия печатаются на 3D-принтере, практически нет разницы в стоимости его единицы – то есть не важно требуются 1–3 или 100 ед ., поскольку нет затрат на инструменты, приспособления и т. д.
Таблица 1 – Варианты форм корпусов и направлений потоков жидкостей и газов
№ п/п |
Форма корпуса |
Формула описания формы |
Направление потоков при вращении корпуса |
№ п/п |
Форма корпуса |
Формула описания формы |
Направление потоков при вращении корпуса |
1 |
2 |
3 |
4 |
1 |
2 |
3 |
4 |
1 |
1___________________________________________________________________________________________________________________________________________________________________________________________________________________________________________________1 |
22 X- + y- = 1 a 2 b 2 |
/и X |
2 |
22 X- + У- = 1 a 2 b 2 |
Уь X |
|
диск |
цилиндр |
||||||
3 |
x 2 y 2 z 2 —т +— т +— т = 0 a 2 b 2 c 2 |
Vv X |
4 + |
X- + y- + z- = r 2 |
У>1 X |
||
конус |
шар |
||||||
5 |
(___L_® |
(л:2 +y2 + z2 + + Л2+г2)2- ^^(У+У^О |
Ук X |
6 |
x 2 y 2 z 2 —г +— т +—г = 1 a 2 b 2 c 2 |
X |
|
тор |
эллипсоид |
||||||
7 |
22 X- + y- =1 a 2 b 2 |
4 1 i X |
8 |
—^-4--y4--5- — 0 a2 b1 c- a2 У |
У\х X |
||
диск + цилиндр |
конус + цилиндр |
||||||
9 |
x 2 y 2 z 2 -+ + + = 0 a 2 b 2 c 2 |
УК X |
10 |
( rv 1 |
222 xyz ”+ + TT + = 0 abc |
\ X |
|
два конуса |
три конуса |
||||||
11 |
у yw+ + f? + yf- -4л-2 lv v2^ 0 77'7Z^ 1 |
X |
12 |
ii+£+ii=o a? b1 c1 (У+.У2 +z2 + + Д2+г2)2- -4x2 (№ + /) = 0 |
X |
||
тор + цилиндр |
тор и конус |
||||||
13 |
-i2 У У а2 У |
1 X |
14 |
(л-2 + у1 +-z’-t- +В? + г2У- -4л:2(;1:2 + У) = 0 |
__J |
||
эллипсоид + цилиндр |
два тора |
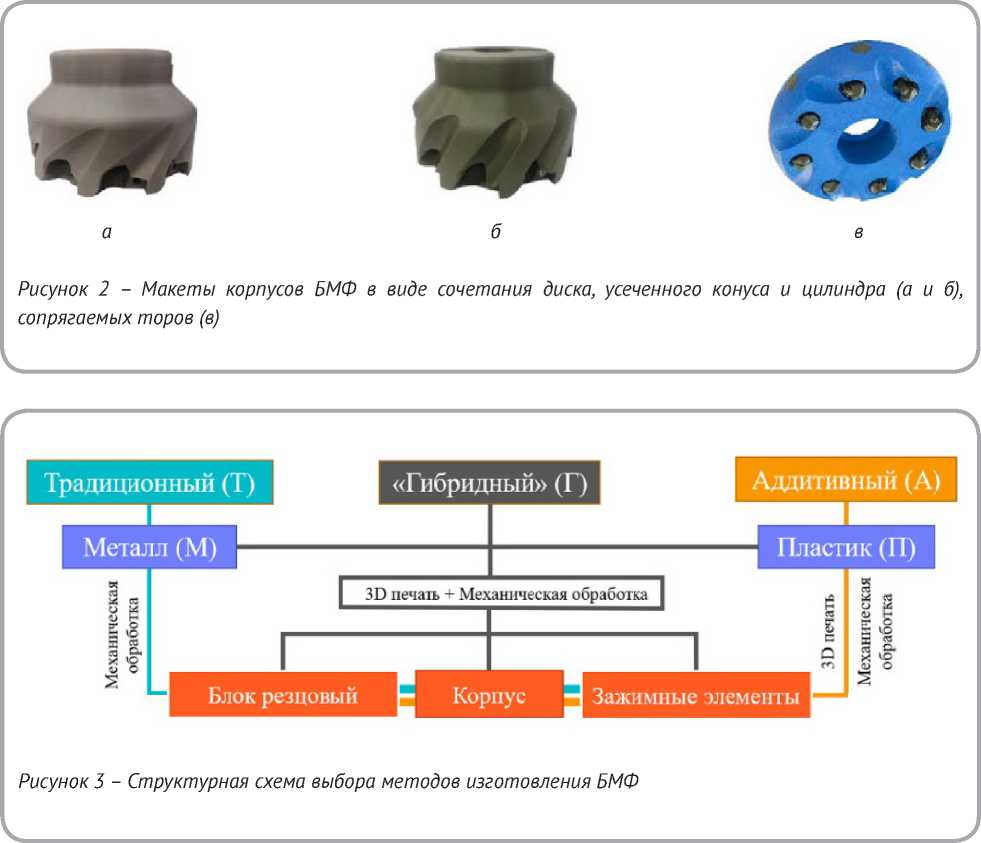
Были отпечатаны макеты блоков резцовых из различных пластиковых материалов (рисунок 4), свойства которых изучались применительно к эксплуатации вращающихся режущих инструментов. 3D-печать блоков резцовых позволяет осуществить быстрый переход от экспериментальных к опытным образцам изделия.
Технологический маршрут изготовления БМФ может быть составлен в целом на изделие, его конструктивные элементы (сборочные единицы), на «гибридную» конструкцию, включающую или конструктивные элементы из различных материалов, или субтрконтрактивные и аддитивные операции изготовления отдельных конструктивных элементов, которые затем собираются традиционными технологическими методами.
Например, для единичного и мелкосерийного типов производства технологический маршрут на отдельные конструктивные элементы БМФ из пластиковых материалов включает операции: 1) подготовка к 3D-печати; 2) 3D-печать деталей; 3) постобработка.
Процесс подготовки к 3D-печати включает следующие этапы настройки программного продукта в Simplify 3D:
-
1) присваивается имя процесса, степень заполнения объекта и обновляется профиль настроек;
-
2) назначается диаметр сопла принтера, коэффициент величины экструзии, а также ее ширина; задается величина подъема сопла над печатающимся объектом;
-
3) в группе настроек «слой» задается высота слоя печати (как правило, величина, равная 1/2 диаметра сопла), количество внешних сплошных слоев и внешних параметров; выбирается при-
Рисунок 4 – Внешний вид державки блока резцового из различных марок пластиковых материалов: а – ABS-GF; б – ABS; в – PLA; г – SBS; д – Pet
вязка стартовых точек начала печати к вымышленной точке с координатами « X » и « Y »;
-
4) выбирается тип (форма) внутреннего заполнения модели (линии, треугольники, сетка, волны, сотовое заполнение); а также настройка материала поддержки, который помогает напечатать нависающие элементы модели;
-
5) настраивается температура печати, стола;
-
6) настраивается скорость и система охлаждения модели при печати;
-
7) расширенные настройки высоты начала и окончания процесса, настройки поведения слайсера при обработке моделей, содержащих ошибки, настройки печати тонких стенок.
На операции 3D-печати деталей осуществляется следующая последовательность переходов:
-
1) передать 3D-модель прототипа в формате STL в программное обеспечение 3D-принтера;
-
2) расположить модель в виртуальной рабочей зоне;
-
3) сгенерировать элементы вспомогательных конструкций (из специального материала поддержки);
-
4) произвести расчёт путей перемещения печатной головки;
-
5) произвести расчёт времени выращивания прототипа;
-
6) разогреть стол до температуры 60–120 градусов;
-
7) печатать изделие, выдерживая температуру экструдера 210–285 градусов, скорость перемещения сопла – 40 мм/с , согласно исходной 3D-модели;
-
8) убрать вспомогательные конструкции. Основные характеристики 3D-печати деталей БМФ представлены в таблице 2.
Как следует из таблицы 2, основное время печати всех элементов БМФ составляет 19 ч 22 мин (1153 мин); длина пластиковой нити – 149716,4 мм (149,7 м); количество материала печати – 452,61 г (0,45261 кг). Основные затраты печати пластиковых деталей БМФ при стоимости 1 г материалла ≈ 10 копеек составляет порядка ≈ 45,3 бел. руб.
Технологическая схема сборки напечатанных конструктивных элементов БМФ включает следующие операции (рисунок 5): 005 Комплектовочная; 010 Сборочная «Блока резцового»; 015 Сборочная «Зажимного модуля»; 020 Сборочная «БМФ».
Последовательность сборки БМФ: 1) процесс сборки БР начинается со сборки прихвата и штифта с образованием прихвата в сборе; в отверстии прихвата позиционируется штифт с предварительно установленной режущей пластиной, ограничивая перемещение штифта вдоль посадочной поверхности. Полученная сборочная единица устанавливается в пазу державки по посадке и закрепляется с помощью винта с шайбой, обеспечивая прижим основания и боковой поверхности пластины к установочной и направляющей поверхностям державки; 2) сборка БМФ начинается со вставки механизма зажима (сборочная единица: сухарь упорный и резьбовой с винтом) в соответствующие отверстия МК, с предварительно поджатым винтом. Затем последовательно вставляются БР в базирующие отверстия МК с ориентацией пластин, режущих на заданный угол наклона режущей кромки, осуществляется настройка радиального и торцового биения БР с помощью регулировочных винтов и поворота БР вокруг собственной оси, и окончательно закрепляется БР механизмом зажима; 3) заключительным этапом сборки является установка балансировочных заглушек.
Таблица 2 – Основные характеристики 3D-печати деталей БМФ |
|||||
Деталь |
Характеристики 3D-печати |
Деталь |
Характеристики 3D-печати |
Деталь |
Характеристики 3D-печати |
го ГО ГО * 0J С1 |
Время печати: 85 мин ; Длина нити: 5108 мм ; Количество материала: 15,4 г |
н -е- X н 3 |
Время печати: 4 мин ; Длина нити: 65,9 мм ; Количество материала: 0,2 г |
н го со X X 1= |
Время печати: 18 мин ; Длина нити: 1052,9 мм ; Количество материала: 3,7 г |
го ю >х го 3 |
Время печати: 1 мин ; Длина нити: 70 мм ; Количество материала: 0,21 г |
S 2 О О ей Ю О Н ХГ X СП х ГП О- |
Время печати: 11 мин ; Длина нити: 370,8 мм ; Количество материала: 1,1 г |
>х .0 О О. го ГО О X ^ и $ о. |
Время печати: 21 мин ; Длина нити: 1511 мм ; Количество материала: 4,6 г |
>х X о с о. го X |
Время печати: 17 мин ; Длина нити: 1052,2 мм ; Количество материала: 4 г |
о о I 1 го ^ н X X СП |
Время печати: 24 мин ; Длина нити: 1321,0 мм ; Количество материала: 4 г |
СК го X о го го о 3 О- >> X Е X го го го LD |
Время печати: 14 мин ; Длина нити: 788 мм ; Количество материала: 2,4 г |
U И |
Время печати: 958 мин ; Длина нити: 138377 мм ; Количество материала: 417 г |
Этап сборки изделия обеспечивает выявление погрешностей изготовления отдельных конструктивных элементов, соответствия их точности и качества заданным параметрам на чертежах деталей. При этом такие особенности 3D-печати деталей, как, например, тепловая усадка материала, структура и шероховатость получаемых поверхностей позволяют отработать на экспериментальных образцах исполнение отдельных конструктивных элементов и скорректировать чертеж 3D-модели. Поэтому были проведены исследования точностных параметров экспериментальных образцов блоков резцовых и модулей корпусных БМФ.
Точность линейных размеров 3D-модели и соответствие их чертежу обеспечивается, в первую очередь, настройкой программного приложения Simplify 3D для последующей печати на 3D-принтере. Наиболее важные параметры настройки, как отмечено выше, относятся к экструдеру, формированию и заполнению слоев материала, температуре и охлаждению при печати.
Оценка соответствия параметров точности размеров макетов БМФ заданным на чертеже размерам осуществлялась с использованием видеоизмерительного микроскопа модели NVM-4030D фирмы NORGAU на примере 10 державок блока резцового и 2 корпусных модуля из различных пластиковых материалов. На рисунке 6 представлены эскизы державки и корпуса с обозначением позиций линейных и угловых размеров.
Указанные на чертеже позиции от 1 до 11 соответствуют последовательности измерения линейных размеров модели «Державка» блока резцового из разных пластиковых материалов. Полученные результаты измерений линейных размеров представлены в таблице 3.
Анализ полученных результатов, фрагменты которых представлены в виде графиков отклонений линейных размеров от номинальных для различных материалов, показаны на рисунке 7, позволяет сделать выводы о том, что степень усадки минимальна для пластикового материала марки SBS – отклонение линейных и угловых размеров не превышают соответственно 0,64 и 0,15 %, максимальные отклонения установлены для пластика марки ABS-GF.
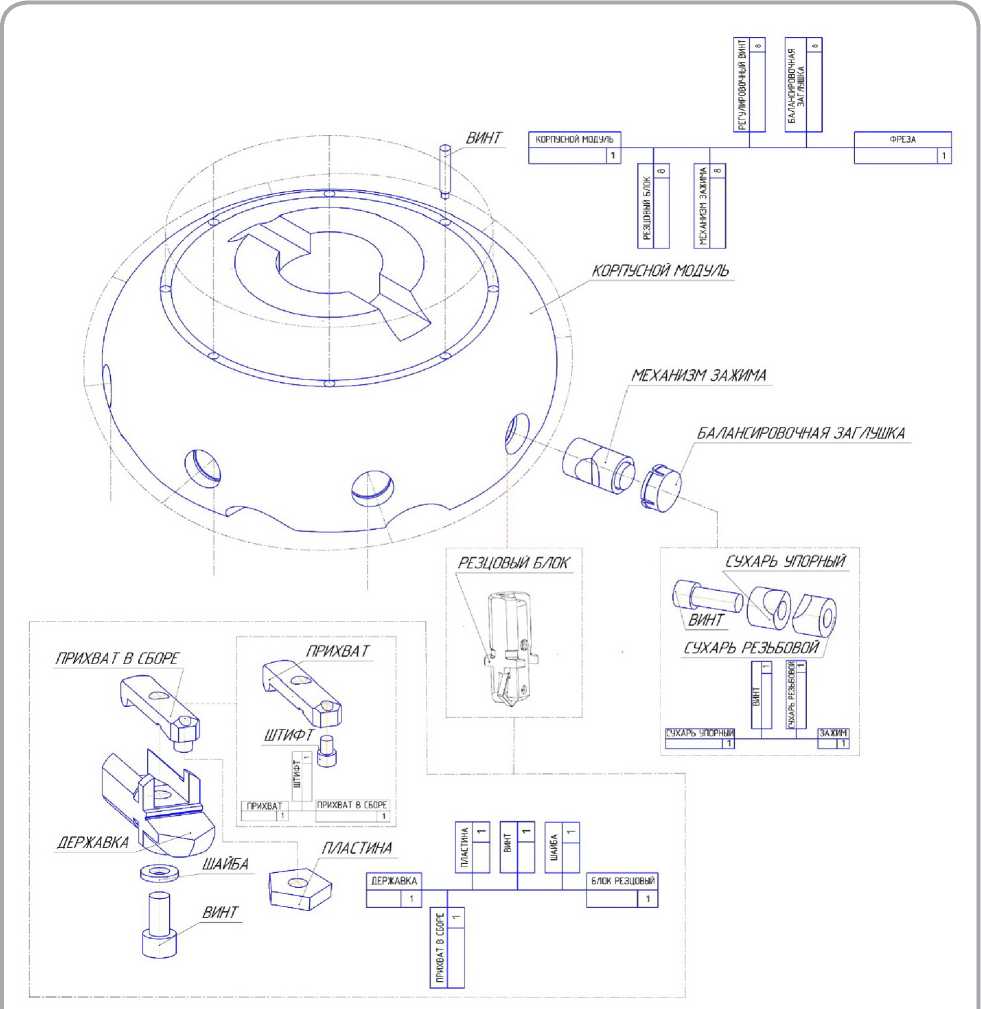
Рисунок 5 – Технологическая схема сборки БМФ
Значения погрешностей линейных размеров для каждой марки материалов представлены в таблице 4.
Исходя из полученных результатов измерений значений угловых и линейных размеров напечатанных моделей «Державка» блока резцового и модуля корпусного, следует, что наилучшими для изготовления модели являются пластиковые материалы марок SBS и PLA, обеспечивающие наименьшее искажение размеров.
Наблюдается увеличение размера 5 и уменьшение размеров 10 и 11, что связано с влиянием материала поддержки на печать буртика и резьбового отверстия державки. Наружные нависающие элементы трехмерной модели «Державка» блока резцового в виде «буртиков» (позиция из-
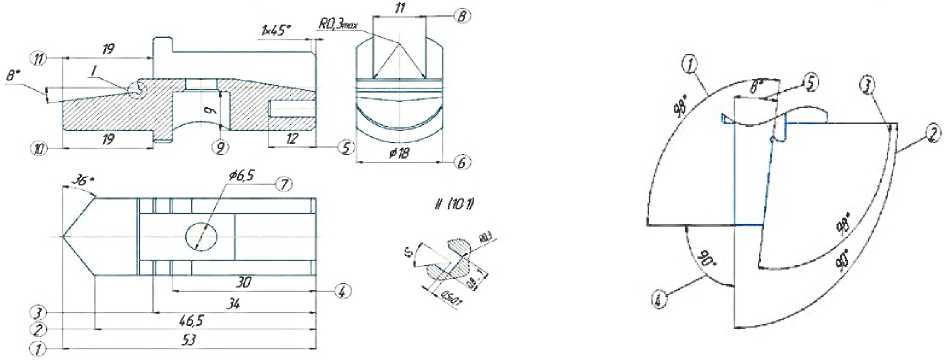
а
б
Рисунок 6 – Эскиз измерения линейных (а) и угловых (б) размеров державки
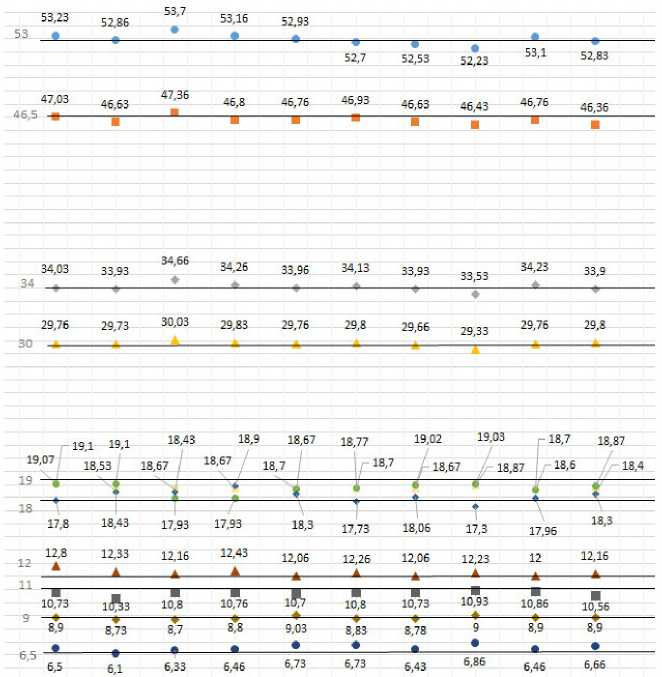
- 191 191 18'43 18'9 18167
12,33 12,16 12.43 12,06 12.26 12,06 12,23 12 12,16
6,1 6,33 6,46 6.73 6-73 6,43 686 6,46 6,66
29,76 29,73 30-03 29,83 29.76 29,8 29,66 29 33 29176 2918
зо -----------------------------------------------------------------------------;--------------
52,7 52,53 52,23 53,1 52183
47103 46,63 47_36 46.8 46 76 46 93 45 53 ^ 46 76 46 36
34,03 33,93 34,66 34,26 33,95 34,13 33 93 53 34,23 33,9
34 --------------------------------------------------------------------------------------
53,23 52,ю 53,7 53,16 52,93
53 е _______*_______•_______•__________
19,02 19,03 р 18,7 18 87
хДз ад 1076 1К ад адЗ Ю73 1036 1(^6
—♦------▼------♦------♦------♦------♦------*------♦------♦—
8,73 8,7 8,8 9,03 8,83 8,78 9 8,9 8,9
12,8
12 д
11 ■
10,73
9 —♦—
8,9
6,5 -*—
6,5
Рисунок 7 – График отклонений линейных размеров изделия от номинальных значений (сплошная линия) для различных пластиковых материалов
19,07 |
18,53 |
18,67 |
18,67 |
18,7 |
18,7 |
г 18.67 |
18.87 18,6 |
18,4 |
8 |
• |
|||||||
18 |
♦ |
17,8 18,43 17,93 17.93 18,3 1773 18,06 17,3 17,96
Таблица 3 – Линейные размеры модели «Державка» блока резцового
Материал
О c |
PA-GF |
PLA |
FLEX |
PET |
PETG |
PC |
ABC |
TPU-GF |
SBS |
ABS-GF |
|||||||||||
мм |
мм |
мм |
мм |
мм |
мм |
мм |
мм |
мм |
мм |
||||||||||||
1 |
2 |
3 |
4 |
5 |
6 |
7 |
8 |
9 |
10 |
||||||||||||
1 |
1 |
53,2 |
pq |
52,8 |
53,7 |
o |
53,2 |
S |
52,9 |
52,8 |
о |
52,5 |
Ln |
52,3 |
53,1 |
о |
52,8 |
||||
2 |
53,2 |
52,9 |
53,6 |
53,2 |
53,0 |
52,7 |
52,5 |
52,1 |
53,1 |
52,9 |
|||||||||||
3 |
53,3 |
52,9 |
53,8 |
53,1 |
52,9 |
52,6 |
52,6 |
52,3 |
53,1 |
52,8 |
|||||||||||
2 |
1 |
47,1 |
о |
46,6 |
47,4 |
m |
46,9 |
s |
46,7 |
46,6 |
46,6 |
46,6 |
46,8 |
s |
46,4 |
||||||
2 |
47,0 |
46,6 |
47,4 |
46,8 |
46,8 |
46,6 |
46,6 |
46,5 |
46,8 |
46,3 |
|||||||||||
3 |
47,0 |
47,6 |
47,3 |
46,7 |
46,8 |
46,7 |
46,7 |
46,4 |
46,7 |
46,4 |
|||||||||||
3 |
1 |
34,1 |
S. |
33,9 |
S\ |
34,6 |
S |
34,3 |
34,0 |
34,0 |
34,0 |
n |
Ln |
34,3 |
33,9 |
О |
|||||
2 |
34,0 |
33,9 |
34,7 |
34,1 |
34,1 |
33,9 |
33,9 |
33,6 |
34,2 |
33,9 |
|||||||||||
3 |
34,0 |
34,0 |
34,7 |
34,4 |
33,8 |
33,9 |
33,9 |
33,5 |
34,2 |
33,9 |
|||||||||||
4 |
1 |
29,7 |
S |
29,7 |
я" |
30,0 |
29,9 |
29,8 |
S |
29,6 |
s |
29,6 |
S |
29,4 |
29,7 |
s |
29,8 |
s |
|||
2 |
29,8 |
29,7 |
30,1 |
29,7 |
29,8 |
29,7 |
29,7 |
29,3 |
29,8 |
29,9 |
|||||||||||
3 |
29,8 |
29,8 |
30,0 |
29,9 |
29,7 |
29,7 |
29,7 |
29,3 |
29,8 |
29,7 |
|||||||||||
5 |
1 |
12,9 |
S |
12,4 |
12,1 |
S |
12,5 |
12,0 |
12,0 |
r§ |
12,0 |
n |
12,2 |
12,1 |
о |
12,1 |
S |
||||
2 |
12,7 |
12,3 |
12,3 |
12,4 |
12,1 |
12,1 |
12,1 |
12,4 |
12,0 |
12,2 |
|||||||||||
3 |
12,8 |
12,3 |
12,1 |
12,4 |
12,1 |
12,1 |
12,1 |
12,1 |
11,9 |
12,2 |
|||||||||||
6 |
1 |
17,8 |
s |
18,4 |
18,4 |
s' |
18,0 |
о |
18,3 |
s' |
18,1 |
18,1 |
s' |
17,4 |
о |
17,9 |
m |
18,3 |
s' |
||
2 |
17,7 |
18,5 |
18,5 |
17,8 |
18,2 |
18,0 |
18,0 |
17,2 |
18,0 |
18,4 |
|||||||||||
3 |
17,9 |
18,4 |
18,4 |
17,9 |
18,4 |
18,1 |
18,1 |
17,3 |
18,0 |
18,2 |
|||||||||||
7 |
1 |
6,4 |
о |
6,2 |
xO |
6,3 |
xO |
6,5 |
xO |
6,8 |
xO" |
6,4 |
xO" |
6,4 |
xO" |
6,8 |
s |
6,5 |
xO |
6,6 |
s |
2 |
6,7 |
6,0 |
6,4 |
6,5 |
6,6 |
6,5 |
6,5 |
6,9 |
6,4 |
6,7 |
|||||||||||
3 |
6,4 |
6,1 |
6,3 |
6,4 |
6,8 |
6,4 |
6,4 |
6,9 |
6,5 |
6,7 |
|||||||||||
8 |
1 |
10,7 |
о" |
10,4 |
о |
10,7 |
10,7 |
О |
10,7 |
o |
10,8 |
10,8 |
о |
10,9 |
о |
10,8 |
10,5 |
о |
|||
2 |
10,8 |
10,3 |
10,8 |
10,8 |
10,7 |
10,8 |
10,8 |
10,9 |
10,9 |
10,7 |
|||||||||||
3 |
10,7 |
10,3 |
10,9 |
10,8 |
10,7 |
10,6 |
10,6 |
11,0 |
10,9 |
10,5 |
|||||||||||
9 |
1 |
8,8 |
co" |
8,7 |
co" |
8,5 |
co" |
8,8 |
9,4 |
s |
8,8 |
co" |
8,8 |
S |
8,9 |
о |
9,1 |
co" |
9,1 |
co" |
|
2 |
9,0 |
8,8 |
8,8 |
8,8 |
8,7 |
8,7 |
8,7 |
9,1 |
8,8 |
8,8 |
|||||||||||
3 |
8,9 |
8,7 |
8,8 |
8,8 |
9,0 |
9,0 |
9,0 |
9,0 |
8,8 |
8,8 |
|||||||||||
10 |
1 |
19,2 |
О, |
18,4 |
s' |
18,8 |
s' |
18,8 |
s' |
18,6 |
s' |
18,7 |
s' |
18,7 |
s' |
19,0 |
s' |
18,7 |
s' |
18,5 |
s' |
2 |
18,9 |
18,6 |
18,6 |
18,6 |
18,8 |
18,6 |
18,6 |
18,8 |
18,8 |
18,3 |
|||||||||||
3 |
19,1 |
18,6 |
18,6 |
18,6 |
18,7 |
18,7 |
18,7 |
18,8 |
18,6 |
18,4 |
|||||||||||
11 |
1 |
19,1 |
О |
19,4 |
18,1 |
18,1 |
18,8 |
s' |
19,1 |
s' |
19,1 |
s |
19,1 |
18,6 |
s' |
18,9 |
|||||
2 |
19,2 |
19,1 |
17,8 |
17,8 |
18,4 |
19,2 |
19,2 |
18,9 |
18,7 |
18,7 |
|||||||||||
3 |
19,0 |
18,8 |
17,9 |
17,9 |
18,8 |
18,9 |
18,9 |
19,1 |
18,5 |
19,0 |
Заключение
-
1. Предложены структурные схемы формирования БМФ и выбора метода их изготовления,от-личительными особенностями которых является применение унифицированных конструкций блоков резцовых и корпусных модулей, субтрактивных, аддитивных и «гибридных» технологий, что обеспечивает использование рационального варианта исполнения сборного режущего инструмента, учитывающего условия обработки разнообразных поверхностей и конструктивных элементов деталей на станках с ЧПУ.
-
2. Разработаны конструкции блоков резцовых, модулей корпусных и балансировочных, отличающиеся оригинальными механизмами закрепления пластин режущих и статической балансировки, обтекаемыми формами поверхностей конструктивных элементов, что обеспе-
- чивает повышение надежности и точности БМФ в процессе резания.
-
3. Разработаны технологические маршруты изготовления фрез, включающие подготовку к 3D-печати, 3D-печать и постобработку, подробное описание операции 3D-печати, а также технологическую схему сборки БМФ, что позволяет рекомендовать аддитивную технологию для получения экспериментальных образцов сборных режущих инструментов на этапе подготовки серийного производства.
-
4. Полученные результаты экспериментальных исследований влияния усадки пластиковых материалов различных марок на линейные и угловые размеры деталей БМФ, включающие оценку отклонений от номинальных значений и погрешностей относительно размеров, заданных на чертежах деталей, позволили рекомендовать для изготовления экспериментальных образцов БМФ пластиковые материалы марок SBS и PLA.
Список литературы Подготовка производства блочно - модульных фрез с использованием 3D - прототипирования
- Дальский, A. M., Косилова, А. Г., Мещеряков, Р. К., Суслов, А. Г. (2001), Справочник технолога-машиностроителя, Москва, Машиностроение-1, 912 с.
- Глазьев, С. Ю., Львов, Д. С., Фетисов, Г. Г. (1992), Эволюция технико-экономических систем: возможности и границы централизованного регулирования, Москва, Наука, 207 с.
- Русецкий, А. М., Витязь, П. А., Хейфец, М. Л., Данилов, В. А., Киселев, Р. А., Крутько, В. С., Попок, Н. Н., Клименко, С. А. (2014), Конструирование и оснащение технологических комплексов, Минск, Беларус. навука, 316 с.
- Пашкевич, В. М. (2007), Повышение точности механической обработки и сборки изделий машиностроительного производства на основе построения и использования компьютерных обучающих систем, автореф. дис.... д-ра техн. наук: 05.02.08, Минск, 2007, 46 с.
- Бобров, В. Ф. (1962), Влияние угла наклона главной режущей кромки инструмента на процесс резания металлов, Москва, Машгиз, 152 с.
- Хмельницкий, Р. С., Анисимов, В. С., Гвоздь, Г. И. (2018), Автоматизация станочного оборудования для высокоскоростной обработки резанием, Перспективные направления развития технологии машиностроения и металлообработки, Тезисы докладов международной научно-технической конференции, Минск, Бизнессофсет, 2018, С. 111–112.
- Попок, Н. Н. (2019), Методология исследования процесса резания материалов в современных условиях развития машиностроения, Вестник ПГУ, Серия В, Прикладные науки, 2019, № 10, С. 21–30.
- Белоцерковский, С. М., Ништ, М. И., Котовский, В. Н. (2000), Трехмерное отрывное обтекание тел произвольной формы, Москва, Центр. аэродинам. ин-т им. Н.Е. Жуковского, 260 с.
- Андронов, П. Р., Гувернюк, С. В., Дынникова, Г. Я. (2006), Вихревые методы расчета нестационарных гидродинамических нагрузок, Москва, Изд-во Моск. ун-та, 184 с.
- Грубый, С. В. (2010), Моделирование процесса резания твердосплавными и алмазными резцами, Москва, МГТУ им. Н.Э. Баумана, 107 с.
- Грубый, С. В. (2014), Оптимизация процесса механической обработки и управление режимными параметрами, Москва, МГТУ им. Н.Э. Баумана, 149 с.
- Попок, Н. Н., Портянко, С. А. (2020), Методология исследования работоспособности фрезерных и осевых режущих инструментов на основе 3D прототипирования, Вестник ПГУ, Серия В, Прикладные науки, 2020, № 11, С. 29–39.