Погрешность определения напряжённо-деформированного состояния режущего инструмента
Автор: Кротинов Н.Б., Якимов М.В.
Журнал: Известия Самарского научного центра Российской академии наук @izvestiya-ssc
Рубрика: Машиностроение и машиноведение
Статья в выпуске: 3 т.24, 2022 года.
Бесплатный доступ
В данной статье рассматриваются различные способы определения напряжённо-деформированного состояния токарного резца при использовании аналитических моделей сопротивления материалов и метода конечных элементов с различной степенью приближения к реальным условиям. Определена абсолютная и относительная погрешность этих способов, где за эталон принимался метод конечных элементов с использованием подробной 3D-модели. Приведены рекомендации областей использования данных методов.
Напряжённо-деформированное состояние, погрешность определения, сопротивление материалов, метод конечных элементов, токарный расточной резец
Короткий адрес: https://sciup.org/148325119
IDR: 148325119 | DOI: 10.37313/1990-5378-2022-24-3-29-33
Текст научной статьи Погрешность определения напряжённо-деформированного состояния режущего инструмента
При проектировании конструкции и технологии изготовления режущих инструментов на этапе прочностного расчёта, расчёта погрешности обработки и выполнения других задач, важным является достоверное определение напряжённо-деформированного состояния (НДС). Для этого применяются методики сопромата, методы конечно-элементного анализа, эмпирические, феноменологические и пр. При этом используются различные по своей сложности схемы нагружения с различной степенью приближения к реальным условиям. Понятно, что большее приближение даёт большую достоверность, но при этом увеличиваются и затраты: временные и финансовые, связанные с наличием соответствующей аппаратуры и квалификации исследователя. И здесь встаёт вопрос о рациональности использования тех или иных методик для достижения поставленной перед исследователем цели. Должен быть выбор между ценой и качеством определения НДС.
Целью данной работы является определение относительной погрешности расчёта НДС токарного расточного резца при использовании аналитических моделей сопротивления материалов и метода конечных элементов с различной степенью приближения к реальным условиям.
тангенциальная составляющая Pz, приводящая к изгибу резца .
Самым простым вариантом для определения действующих напряжений является использование плоской модели, в которой резец представляется как балка с защемлённым концом с вылетом l , испытывающая изгибающие нагрузки от тангенциальной составляющей Pz , действующей на главную режущую кромку (см. рис. 1) [1].
Напряжения на изгиб определяются, как:
аи=^,Па, (1)
где М изг – изгибающий момент, действующий на резец в зоне крепления резца в резцедержателе станка; W – момент сопротивления резания при изгибе.
M,, = p,i,HM,
_ Tr DS n w =--- – для круглого сечения, где D – ди- аметр державки, м.
Подставим их в первую формулу и получим: - для резцов с прямоугольным сечением:
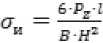
;
- для резцов с круглым сечением:
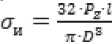
.
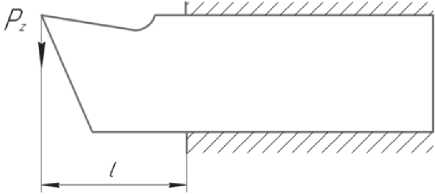
Рис. 1. Схема для расчёта напряжений резца при использовании плоской модели
Тангенциальную составляющую силы резания Pz можно приближённо определить по формуле:
Pz = 10-k - F, Н, (4)
где k – коэффициент резания, зависящий от свойств обрабатываемого материала; F– пло- щадь поперечного сечения стружки, зависящая от подачи s (мм/об) и глубины резания t (мм): F = t.s, мм2.
Приведённый расчёт на плоский изгиб – простой, но неточный, так как на резец действу- ют также осевая и радиальная составляющие силы резания Рх и Ру, создающие дополнительные нагрузки на изгиб, кручение и сжатие. В результате такого сложного сопротивления, напряжения резца увеличиваются, по мнению авторов [2], в зависимости от величины углов в плане, примерно в два раза. Кроме того, данная схема предполагает, что наиболее опасным яв- ляется сечение державки, отстоящее от вершины резца на расстоянии вылета l. В некоторых конструкциях может оказаться, что наиболее слабым является головка резца в месте выреза под пластину.
Для резцов с малым сечением среза и большим вылетом (отрезных, расточных) производится также проверка на жёсткость. Здесь стрела прогиба f (см. рис. 2) находится, как [2]:
P !a f = , м, (5)
где Е – модуль упругости материала державки резца ((200...220) . 109 Па); I – момент инерции державки:
т B^ 4
-
- для прямоугольного сечения Z = , м ;
-
- для круглого сечения I = ---- , M.
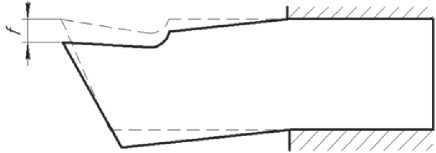
Рис. 2. Схема для расчёта прогиба резца при использовании плоской модели
Более достоверным способом расчёта НДС является метод конечных элементов. Но здесь требуется наличие соответствующей квалификации исследователя, автоматизированное рабочее место с программным обеспечением, 3D-модель исследуемого изделия. Однако и тут погрешность расчёта зависит от множества факторов: типа конечных элементов, параметров сетки, контактных параметров и пр.
Наиболее простой вариант - отыскать на сайтах производителей модель требуемого инструмента и подвергнуть её расчёту. Про- блема заключается в том, что модель создана, как правило, упрощённо, с низкой детализацией. Например, на рисунке 3, в сечении расточного резца S25T-CTFPR видно, что рычаг крепления 2 режущей пластины 3 к корпусу 1 не имеет отверстия под винт, отсутствует сам винт крепления, обязательный для данной конструкции. По сути, конструкция является монолитной. Всё это, безусловно, должно сказаться на погрешности расчёта НДС, вопрос только – в какой степени.
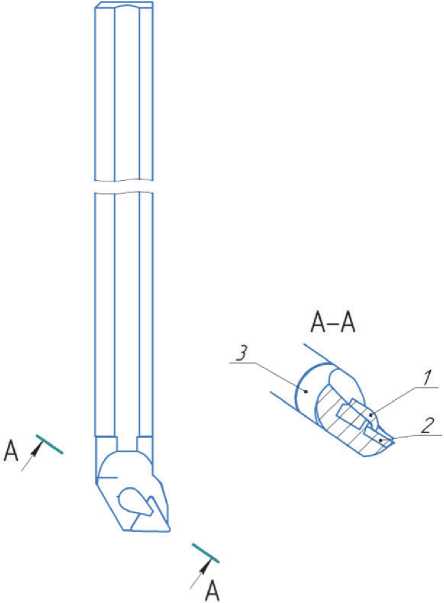
Рис. 3. Эскиз модели расточного резца S25T-CTFPR с сайта производителя [3]:
1 – корпус; 2 – рычаг крепления;
3 – режущая пластина
Ещё один вариант – это расчёт напряжённо-деформированного состояния сборной 3D-модели с полной детализацией, включающей металлорежущую пластину, элементы её крепления и необходимые пазы, канавки и отверстия. Здесь погрешности расчёта сведены к минимуму, однако такой подход является наиболее трудоёмким.
МЕТОДИКА ИССЛЕДОВАНИЙ
Для определения погрешности расчёта НДС токарного расточного резца использовалось три подхода: использование плоской модели расчёта резца по формулам сопромата, монолитная 3D-модель – методом конечных элементов и подробная 3D-модель – также методом конечных элементов. За эталон, относительно которо- го рассчитывалась относительная погрешность, принимался последний метод.
Расчёт 3D-модели токарного расточного резца производился в модуле прочностного конечно-элементного экспресс-анализа APM FEM по рекомендациям авторов [4, 5].
Исходные данные. Расточной резец S16M-PCLNR 09. Подача s=0,3 мм/об; глубина резания t=3 мм, коэффициент резания k=164, Вылет вершины резца l=75мм. Диаметр державки D=16 мм.
Тангенциальная составляющая силы резания, по ф.4, составила P z ≈1500 Н. Напряжения и деформации для первого варианта определялись по формулам 3 и 5; результаты занесены в таблицу.
Параметры сетки конечных элементов использовались следующие [5]:
-
1. Десятиузловые тетраэдры (использование 10-узловых тетраэдров позволяет использовать больший шаг разбиения по сравнению с 4-узло-выми, что экономит память и ресурсы компьютера при обеспечении точности расчёта).
-
2. Максимальная длина стороны элемента 2 мм (величина, характеризующая размер конечного элемента (тетраэдра)).
-
3. Максимальный коэффициент сгущения на поверхности 2 (определяет, насколько следующий элемент можно сделать (где необходимо) меньше).
-
4. Коэффициент разрежения в объеме 1,5 (степень увеличения стороны тетраэдра при генерации сетки вглубь объема твердотельной модели).
Тип расчёта – статический.
РЕЗУЛЬТАТЫ И ИХ ОБСУЖДЕНИЕ
В результате расчёта НДС, приведённого в таблице и на рисунках 4 и 5, получили следующее.
По методике сопромата погрешность расчёта изгибающих напряжений относительно эталона составила 30%; их величина оказалась сильно заниженной. При использовании этого подхода в конструировании рекомендуется использовать коэффициент запаса прочности не менее трёх, что, конечно же, приведёт к менее эффективному коэффициенту использования материала, но сохранит надёжность. А вот величина прогиба (деформации) вершины резца оказалась практически идентичной эталону.
При использовании монолитной 3D-модели погрешность расчёта изгибающих напряжений, относительно эталона, составила 21%; их величина, наоборот, оказалась завышенной и коэффициент запаса здесь рекомендуется брать равным единице. Относительная погрешность деформаций в данном случае составила 33% и также оказалась завышенной. Причины такого расхождения пока не ясны.
Если внимательно посмотреть на рисунок 5, то можно увидеть, что максимальная величина напряжений при расчёте сборной 3D-модели находится не в месте крепления державки резца, а в месте крепления сменной режущей пластины (СМП) и сильно отличается в большую сторону (3331 МПа по сравнению с 280 МПа и 1141 МПа). Этот факт говорит о том, что плоская модель сопромата и метод конечных элементов с монолитной 3D-моделью не адекватно оценивают напряжения в целом для сборного инстру-
Таблица. Результаты исследования погрешности определения НДС
Определяемый параметр |
Плоская модель |
Монолитная 3D-модель |
Сборная 3D-модель |
Напряжение а и , МПа |
280 |
1141 |
940 |
Деформация f , мм |
0,328 |
0,435 |
0,327 |
Абсолютная погрешность напряжения С и , МПа |
660 |
201 |
0 |
Абсолютная погрешность деформации, мм |
0,001 |
0,108 |
0 |
Относительная погрешность напряжения С и , % |
30 |
21 |
0 |
Относительная погрешность деформации, 5, % |
0,3 |
33 |
0 |
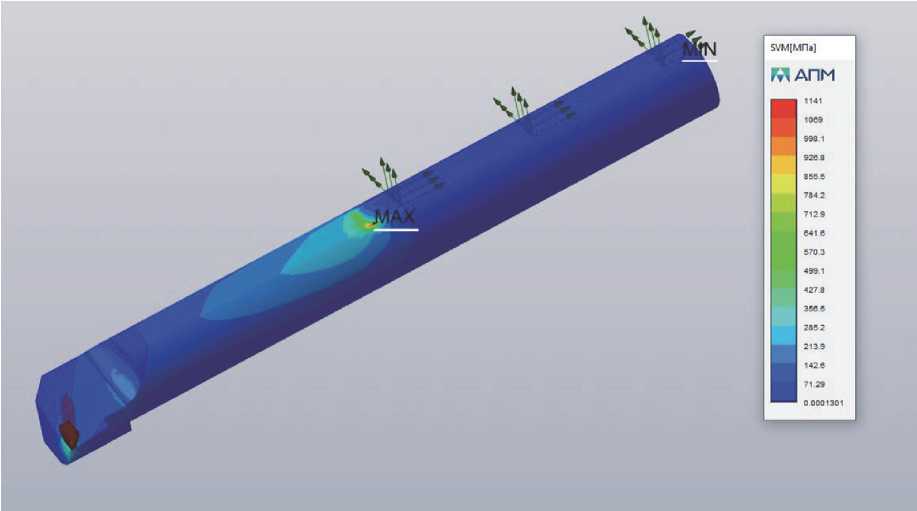
Рис. 4. Результаты расчёта напряжений монолитной 3D-модели
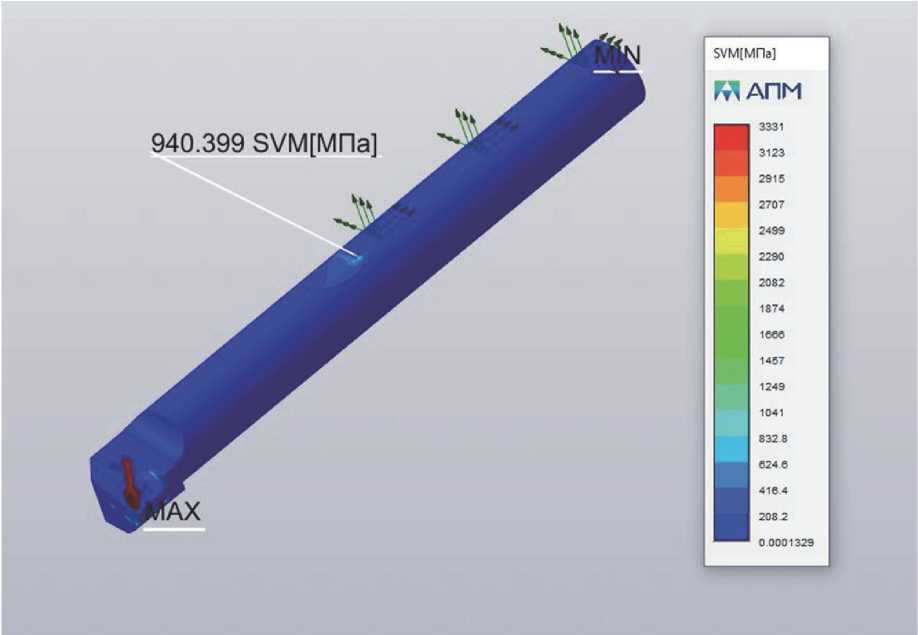
Рис. 5. Результаты расчёта напряжений сборной 3D-модели
мента с СМП и годятся только для цельных или составных конструкций резцов.
ВЫВОДЫ
-
1. При использовании плоской модели сопромата для расчёта изгибающих напряжений в державке резца рекомендуется принимать коэффициент запаса не менее трёх. Прогиб вер-
- шины резца под действием тангенциальной составляющей силы резания данная модель определяет адекватно.
-
2. При использовании метода конечных элементов с упрощённой (монолитной) 3D-моделью напряжения получаются немного завышенными, и коэффициент запаса рекомендуется брать равным единице. Погрешность величины прогиба резца также завышена.
-
3. Для расчёта статических напряжений от сил резания инструмента со сменными многогранными пластинами рекомендуется использовать метод конечных элементов с подробной 3D-моделью, поскольку максимальные напряжения могут возникать не в месте крепления державки в станке, а в месте крепления СМП.
Список литературы Погрешность определения напряжённо-деформированного состояния режущего инструмента
- Солоненко, В.Г. Резание металлов и режущие и инструменты: учеб. пособие / В.Г. Солоненко, А.А. Рыжкин. - М., Инфра-М, 2018. - 414 с.
- Алексеев, Г.А. Конструирование инструмента: учебник для машиностроительных техникумов / Г.А. Алексеев, В.А. Аршинов, Р.М. Кричевская [под общ. ред. Г.А. Алексеева]. - М.: Машиностроение, 1979. - 384 с.
- SANDVIK Coromant [Электронный ресурс]: Инструменты T-Max S. URL: https://www.sandvik.coromant.com/ru-ru/pages/default.aspx (дата обращения 29.06.2022).
- Кротинов, Н.Б. Прочностной анализ токарных резцов методом конечных элементов / Н.Б. Кротинов, А.Б. Косенко // Высокие технологии в машиностроении. Материалы XVIII Всероссийской научно-технической конференции с международным участием. - Самара: СамГТУ, 2021. - С. 154-156.
- APM FEM [Электронный ресурс]: Руководство пользователя. URL: https://apm.ru/downloads/188/APM-FEM.pdf (дата обращения 06.07.2022).