Покровно-рафинирующие флюсы для выплавки медематричных композиционных сплавов
Автор: Бабкин В.Г., Трунова А.И.
Журнал: Журнал Сибирского федерального университета. Серия: Техника и технологии @technologies-sfu
Статья в выпуске: 6 т.9, 2016 года.
Бесплатный доступ
Исследованы требования, предъявляемые к покровно-рафинирующим флюсам, применяющимся при выплавке медематричных композиционных сплавов (КС). Предложен наиболее эффективный состав флюса, защищающего расплав не только от окисления кислородом, но и от проникновения водорода, что позволяет значительно повысить механические свойства готового изделия.
Медематричные композиционные сплавы, покровно-рафинирующий флюс, синтез упрочняющих фаз
Короткий адрес: https://sciup.org/146115117
IDR: 146115117 | DOI: 10.17516/1999-494X-2016-9-6-836-844
Текст научной статьи Покровно-рафинирующие флюсы для выплавки медематричных композиционных сплавов
Композиционные сплавы на основе меди, упрочненные частицами карбидов, боридов и других тугоплавких соединений, применяются в электротехнике в качестве контактного материала для высоковольтных выключателей, электродов сварочных машин, силовых кабелей и других изделий электротехнического назначения.
Наиболее эффективным способом получения литых композиционных материалов является метод синтеза упрочняющей фазы в матричном расплаве [1, 2]. Однако плавка меди и медных сплавов в открытых плавильных печах приводит к насыщению сплава кислородом, что существенно снижает механические характеристики литых изделий (на рис. 1 показано снижение пластичности литой меди при насыщении ее кислородом) и скорость формирования упрочняющих ультрадисперсных фаз в реакциях in-situ. В частности, растворение хрома при синтезе в расплаве меди упрочняющих фаз происходит замедленно, что обусловлено ограниченной растворимостью хрома в меди. При этом хром активно окисляется с образованием плотной оксидной пленки. В результате угар хрома может составлять ~ 60 % [3].
В предыдущих работах методом термического анализа нами было исследовано насыщение расплава меди кислородом в кислородсодержащей газовой фазе и возможность его раскисления наноразмерным алмазографитом, входящим в состав реакционной смеси, применяемой для синтеза карбида хрома при получении медематричных композитов [4]. Показана высокая рафинирующая способность алмазографита, позволяющая существенно повысить пластичность меди и медематричных композитов. Вместе с тем снижение содержания кислорода в меди приводит к повышению растворимости водорода в обычных условиях плавки, что способствует образованию пористости в литых изделиях при кристаллизации. Поэтому одним из основных условий получения качественных композиционных сплавов является ведение процесса плавки под защитным слоем покровного флюса. Для защиты меди и сплавов от окисления чаще всего в качестве материалов покровного слоя применяют древесный уголь в виде кусков до 30-80 мм, восстанавливают Cu2O по реакциям (1), (2) [5]:
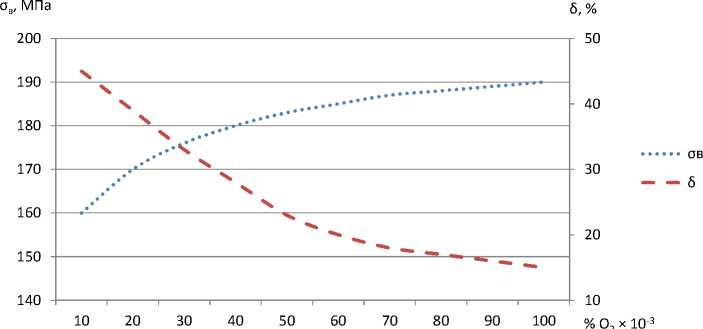
Рис. 1. Влияние насыщения литой меди кислородом на предел прочности (σв) и относительное удлинение (δ)
2Cu2O + С ^ 4Cu + C02, △Gfioo = -221,4 кДж/моль, (1)
Cu^O \ CO > 2Cu + CO2, ДС^юо = -99,4 кДж/моль. (2)
Применение для раскисления меди наноразмерного алмазографита позволяет увеличить площадь поверхности соприкосновения раскислителя с расплавом и ускорить процесс восстановления.
Углеродотермическое восстановление более прочных оксидов SiO2, PbO, CaO, Al2O3 и др., имеющихся в технической меди и медном ломе, не происходит, о чем свидетельствует термодинамический анализ реакций (3-4):
СаО + 3С = СаС2 + СО, AG0 = 433836 - 192,2Т, Дж,(3)
Si2О + 3С = SiC + 2СО, AG0 = 526573 - 344,2Т, Дж,(4)
/3А12О3 + 3С = 1/3А14С3 + 2СО, AG0 = 804703 - 321,5Т, Дж.(5)
Для этих реакций температуры, при которых AG0=0, соответственно составляют 2257, 1530, 2503 К.
Целью настоящей работы является исследование и разработка состава флюса, обеспечивающего не только раскисление меди, но и рафинирование металла от содержащихся в нем примесей, что особенно актуально при утилизации бракованных слитков и переплава вторичного сырья. Температура плавления флюса не должна превышать 900 °С, и при температуре приготовления композиционных сплавов 1200-1300 °С флюс должен иметь достаточную жидкотекучесть и хорошую кроющую способность. Физико-химические свойства флюса должны обеспечивать его агрессивность, т.е. растворять оксиды примесей металлов, а также растворять оксид хрома и улучшать его усвоение. Во флюсе не должны находиться легколетучие хлориды и фториды, что особенно важно с экологической точки зрения. Составляющие флюса должны быть достаточно инертны к углеродсодержащему покрову, а также к компонентам расплава.
Одновременно решалась задача защиты расплава меди от насыщения водородом и получения высококачественных медематричных композиционных сплавов. В качестве эффективного раскислителя в составе покровно-рафинирующего флюса применили наноразмерный алмазо-графит, который ускоряет процесс восстановления оксида меди благодаря высокой удельной поверхности и химической активности. Поскольку углерод не восстанавливает термодинамически прочные оксиды, имеющиеся в расплаве или образовавшиеся в результате окисления металлических примесей, для их удаления обычно применяют фториды кальция и натрия, которые при 800 °С образуют эвтектику. Для снижения токсичности этой системы рекомендуется вместо NaF применять криолит (Na3AlF6). Солевой сплав эвтектического состава (80 %CaF2 + 20 % Na3AlF6) плавится при 900 °С и образует при плавке меди жидкий покров, изолирующий металл от атмосферы. В этом случае обеспечивается достаточно надежная защита расплава меди от окисления, поскольку этот процесс будет контролироваться диффузией катионов металлов через слой флюса. Флюс содержит фторид кальция CaF2 и криолит, которые хорошо растворяют оксидные включения. Поверхностное натяжение фторида кальция составляет 250 мДж/м2, а криолита - 148 мДж/м2. Поверхностное натяжение флюса системы 80CaF2
-20Na3AlF6, определенное методом аддитивности, составило ~230 мДж/м2 [6]. Криолит в этой системе является поверхностно-активным компонентом.
Известно, что удаление оксидных неметаллических включений определяется соотношением поверхностных энергий (σ) на границах раздела фаз σ Cu-в , σ Cu-ф и σ ф-в . С термодинамической точки зрения этот п роцесс обусловлен убылью свободной энергии системы.
Убыль свободной энергии Гиббса [ -AG] в процессе удаления включений:
“ КСи-ф + К ф-в + ^ Си-в , (6)
где К . :К: . К - межфазное натяжение да границе фаз соответственно жидкий металл—жидкий флюс, жидкий флюс-оксидная фаза (включение), жидкий металл-оксидная фаза.
AG < 0 , если К си-в > К си-ф +К ф-в
К с и -в. > К с и -ф > К ф-в •
Работа разделения фаз, отнесенная К единице поверхности их раздела (W), может слу— жить основой характеристикой экстрагирования включения флюсом.
Условия экстрагирования включения флюсом:
И/а (ф-в) > ^ а (Си-ф) > W q (Си-в) . (7)
Для оценки рафинирующей способности флюса в работе исследовали физико-химические свойства солей, входящих в состав комплексного флюса, и кинетику его растекания по поверхности оксидных включений. Установлено, что криолит в составе флюса действует как поверхностно-активное вещество, снижающее межфазное натяжение на границе металл-флюс и флюс-включение и улучшает смачивание включений, а фториды кальция в этой системе являются поверхностно-неактивными, повышая межфазное натяжение на границе с флюсом и металлом. Присутствующие в шихте оксиды, нерастворимые в металле, всплывают на поверхность, смачиваются флюсом и переходят в шлак. Следует отметить, что фториды Al и Ca могут в небольших количествах растворять Al2O3, SiO2, PbO, ZnO, SnO2 и др. При этом вязкость шлака повышается и его можно практически полностью удалить с поверхности металлического расплава. Наличие графита в составе флюса обеспечивает съем шлака с минимальным захватом жидкого металла с зеркала ванны печи.
Оксидные включения удаляются в том случае, если они смачиваются флюсом лучше, чем жидким металлом. На рис. 2 видим, что скорости растекания флюса по подложкам из оксидов в первые 2∙10-2с весьма велики и составляют 17-25 см/с. В этот период времени наиболее интенсивно происходит изменение контактных углов. Скорость смачивания и растекания заметно уменьшается со временем и через 0,04-0,1 с становится незначительной. Значения контактных углов в этой области приняты для расчета работы адгезии флюса включением.
Для расчета поверхностных натяжений флюса к включению температурные зависимости поверхностного натяжения флюса системы 80CaF2 + 20 Na3AlF6 и краевых углов солевого расплава на графите и некоторых оксидах определяли из соотношения [6]:
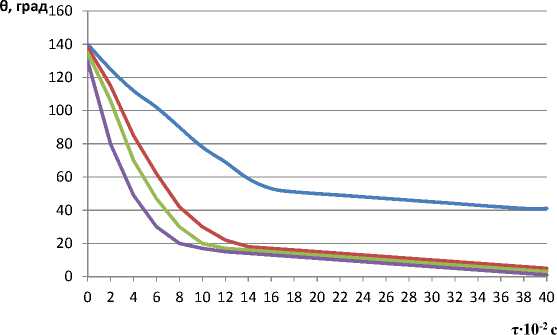
— Графит
----AI2O3
SiO2
---MgO
Рис. 2. Изменение краевых углов смачивания при растекании флюса по графиту и некоторым оксидам
Таблица 1. Температурные зависимости поверхностного натяжения флюса и краевых углов солевого расплава на графите и некоторых оксидах
t, °C |
Расчетные и экспериментальные значения поверхностных свойств |
||||||
σ фг , мДж/м2 |
Θ, град |
W a , мДж/м2 |
|||||
Al 2 O 3 |
SiO 2 |
графит |
SiO 2 |
Al 2 O 3 |
графит |
||
1100 |
230 |
15 |
11 |
40 |
452 |
456 |
406 |
1200 |
217 |
12 |
9 |
33 |
429 |
431 |
399 |
1300 |
204 |
8 |
5 |
25 |
406 |
407 |
388 |
^ = 230 - 0,128(1-100), wa = СТфг(1 + COS0).
Из данных табл. 1 следует, что величина адгезии флюса к включению достаточно велика. Это означает, что флюс будет хорошо экстрагировать включения из расплава.
При расчете поверхностных свойств меди к флюсу использовали правило Антонова [7]:
^ 1 ,2 = О 1 о 2 ,
где σ1 2 – межфазное натяжение на границе расслаивающихся жидкостей; σ1 – поверхностное , натяжение первой жидкости (расплав меди); σ2 – поверхностное натяжение второй жидкости
(солевой расплав).
Ж, = 01 + 02 - ai,2, где Wa – адгезия фаз при контакте двух взаимно насыщенных жидкостей (система медь-флюс).
Высокие значения межфазного натяжения меди на границе с солевым расплавом свидетельствуют о сильном притяжении поверхностных атомов меди объемом металла и сравни- тельно слабом взаимодействии их с ближайшими ионами флюса. Вместе с тем взаимодействие между металлической и солевой фазами не слишком слабое. Адгезия фаз, найденная по значениям поверхностного натяжения металла, равновесного с солью, меньше, чем в системе флюс-включение, и соответствует требованиям экстрагирования включения флюсом.
При расчете адгезии меди к включению использовали температурные зависимости поверхностного натяжения и краевых углов расплава меди на графите и некоторых оксидах, взя- тые из литературы [8].
^к(Си) = 1300 - 0,264(t - 1085^),(11)
-л,^. 238 0.08 л,(12)
^ '
^Cu-графит = 144 — 0,0017t-
Из данных табл. 3 следует, что работа адгезии меди к включениям имеет наименьшие значения.
На основании проведенных расчетов можно сказать, что флюс хорошо экстрагирует и удаляет включения из расплава.
Для приготовления композиционных сплавов системы Cu-Cr3C2 использовали техническую медь марки М3, порошок хрома ПХ1С, а также наноразмерный алмазографитовый порошок (НП-АГ), полученный при детонации углеродсодержащих взрывчатых веществ.
Сплавы системы Cu-Cr3C2 получали в индукционной тигельной печи с графитовым тиглем. Зеркало расплава покрывали флюсом и после снятия шкала, без предварительного раскисле-
Таблица 2. Поверхностные свойства расплава меди на границе с флюсом
t, °C |
Расчетные значения поверхностных свойств |
|||
σ Cu-г , мДж/м2 |
σ ф-г , мДж/м2 |
σ Cu-ф , мДж/м2 |
W a , мДж/м2 |
|
1100 |
1296 |
230 |
1148 |
378 |
1200 |
1251 |
217 |
1116 |
352 |
1300 |
1243 |
204 |
1121 |
326 |
Таблица 3. Поверхностные свойства расплава меди на границе с графитом и оксидами алюминия и кремния
t, °C |
Расчетные значения поверхностных свойств |
||||||
σ фг , мДж/м2 |
Θ, град |
W a , мДж/м2 |
|||||
Al 2 O 3 |
SiO 2 |
графит |
SiO 2 |
Al 2 O 3 |
графит |
||
1100 |
1296 |
145 |
149 |
142 |
234 |
185 |
275 |
1200 |
1251 |
138 |
140 |
142 |
321 |
293 |
265 |
1300 |
1243 |
132 |
133 |
142 |
411 |
395 |
264 |
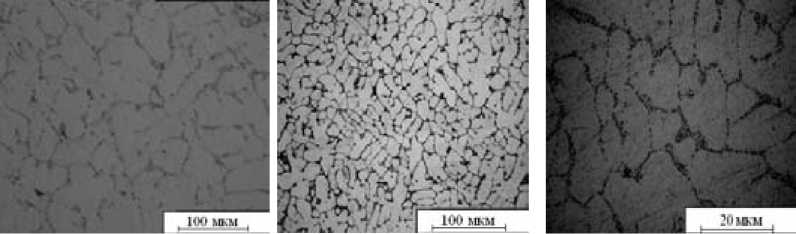
а) чистая медь
б) Cu-0,2 %Cr 3 C 2
в) Cu-3 %Cr 3 C 2
Рис. 3. Микроструктура литой меди (травл. FeCl3)
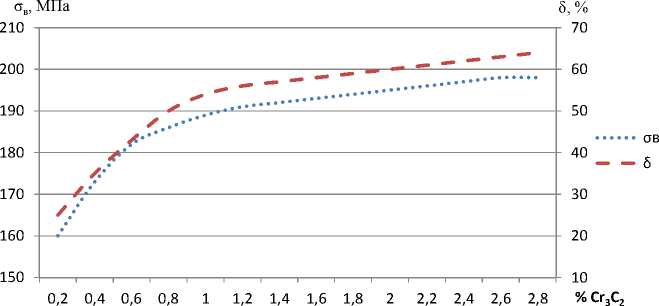
Рис. 4. В и (σв) и относительное удлинение (δ)
ния, при 1350 °С вводили в медной фольге с помощью колокольчика смесь порошкообразного хрома (фракции до 1 мм) и алмазографитового порошка для синтеза в системе карбида хрома. Расплав разливали в металлический кокиль и из полученных цилиндрических слитков готовили образцы для термического анализа, металлографических исследований и механических испытаний.
На рис. 3 представлена микростуктура полученных образцов с различным количеством карбида хрома. Анализ литой структуры свидетельствует, что небольшие добавки синтезированных в расплаве частиц карбида хрома выполняют роль модификаторов I рода, измельчающих зерно (рис. 3 б ). На рис. 3 в изображена микроструктура образца с содержанием до 3 % карбида хрома. Наблюдается достаточно равномерное распределение частиц по объему матрицы. Средний размер упрочняющей фазы менее 1 мкм.
На рис. 4 изображена зависимость содержания карбида хрома в литой меди марки М3 на предел прочности (σ в ) и относительное удлинение (δ).
Из приведенных данных следует, что с повышением содержания карбида хрома, синтезированного в расплаве меди, повышается прочность и в 2-3,5 раза возрастает пластичность – 842 – медематричного композита по сравнению не только с пластичностью меди общего назначения, но и рафинированной фосфором катодной медью.
Выводы
Получен эффективный покровно-рафинирующий флюс, который защищает расплав меди не только от кислорода, но и от водорода.
Исследовано влияние содержания карбида хрома в композиционном материале на его физико-механические свойства.
Анализ литой структуры образцов с различным содержанием упрочняющей фазы позволил установить модифицирующее влияние при их небольшом количестве (до 0,2 мас. %) на измельчение зерна. Повышенное содержание нано- и микроразмерных частиц Cr3C2 приводит к получению дисперсно-упрочненных медематричных композитов.
Список литературы Покровно-рафинирующие флюсы для выплавки медематричных композиционных сплавов
- Бабкин В.Г., Терентьев Н.А., Перфильева А.И. Литые металломатричные композиционные материалы электротехнического назначения. Журнал СФУ. Техника и технологии, 2014, 7(4), 416-423
- Бодрова Л.Е., Гойда Э.Ю., Пастухов Э.А., Григорьева Т.Ф., Шубин А.Б. Новые способы упрочнения хромовой бронзы. Перспективные материалы, 2014, 9, 66-71
- Мысик Р.К., Сулицин А.В., Брусницин С.В., Ожгихин И.В. Проблемы производства литых заготовок из меди. Журнал СФУ. Техника и технологии, 2014, 7(4), 394-399
- Бабкин В.Г., Трунова А.И. Технологические особенности получения и свойства медематричных композиционных сплавов электротехнического назначения. Труды XII съезда литейщиков России. Нижний Новгород, 2015, 212-217
- Ловшенко Ф.Г., Ловшенко Г.Ф., Лозиков И.А. Литые хромсодержащие бронзы, получаемые с применением механически легированных лигатур. Литье и металлургия, 2012, 3(67), 131-135
- Справочник металлурга по цветным металлам. Производство алюминия. М.: Металлургия, 1971, 560 с.
- Попель С.И. Поверхностные явления в расплавах. М.: Металлургия, 1994, 440 с.
- Каниболоцкий Д.С., Верховлюк А.М., Железняк А.В. Взаимодействие меди, цинка, марганца и их сплавов с огнеупорными материалами. Процессы литья, 2015, 1 (109), 7-19