Получение порошковых углеродных композитных наноматериалов термическим разложением ароматических карбоксилатов Fe (III)
Автор: Толстогузов Д.С., Жеребцов Д.А., Тарасов А.М., Паладий М.А.
Журнал: Вестник Южно-Уральского государственного университета. Серия: Химия @vestnik-susu-chemistry
Рубрика: Физическая химия
Статья в выпуске: 1 т.16, 2024 года.
Бесплатный доступ
В статье рассматриваются основные способы получения углеродных композитных наноматериалов и выделяется метод термолиза как один из основных методов. Для понимания сущности процессов термического разложения как метода синтеза углеродных наноматериалов были рассмотрены ароматические карбоксилаты железа (III). Это 8-гидроксихинолинат, бензоат, салицилат, фталат, п-аминобензоат железа (III). В статье подробно рассматривается методика синтеза этих карбоксилатов железа (III) в простых условиях. Процесс термического разложения проводился в двух средах (воздушная как окислительная и аргоновая как нейтральная) для сравнения получаемых продуктов. Для подробного изучения процессов разложения карбоксилатов железа (III) использовались методы термического анализа (ТГ и ДСК) на синхронном термоанализаторе Netzsch 449 Jupiter. Для изучения морфологии и состава продуктов применялись методы рентгенофазового анализа, оптической и сканирующей электронной микроскопии и рентгенофлуоресцентного микроанализа. Использовались приборы: рентгеновский дифрактометр Rigaku Ultima IV и сканирующий электронный микроскоп с приставкой элементного микроанализа Jeol JSM-7001F. По полученным результатам были рассчитаны предполагаемые формулы исходных карбоксилатов железа (III). Также были предложены механизмы процессов, протекающих при термическом разложении ароматических карбоксилатов железа (III). Для более точного определения состава продуктов синтеза карбоксилатов железа (III) и более точного описания процессов термического разложения этих солей также были подвергнуты термическому разложению и соответствующие ароматические карбоновые кислоты. В приложении к статье находятся данные для более точной интерпретации результатов и более подробного описания процессов термического разложения.
Карбоксилаты железа, карбонизация, термический анализ, продукты термолиза
Короткий адрес: https://sciup.org/147243268
IDR: 147243268 | DOI: 10.14529/chem240113
Текст научной статьи Получение порошковых углеродных композитных наноматериалов термическим разложением ароматических карбоксилатов Fe (III)
Известны несколько методов синтеза углеродных наноматериалов. Это термические методы [1, 5–9], CVD [2–4, 6], плазмохимический [6], электродуговые [4] и др. К направлению термических методов относят пиролиз и карбонизацию. Как можно заметить, термические методы остаются одними из основных для получения ряда материалов. Применяют углеродные наноматериалы в очистке сточных вод [1, 6], электрохимических приложениях [2], как катализаторы [6].
В работе [10] исследуются методы синтеза карбоксилатов железа и наночастиц окислов Fe при пиролизе полученных карбоксилатов. При разложении солей [11–16] образуются оксиды Fe либо элементное Fe. При этом для данных солей была достаточной для разложения температура ниже 600 °С. Авторы [17] исследуют процессы термического разложения различных оксалатов металлов, в том числе Fe+2 и Fe+3, в атмосфере азота и кислорода при нагреве до 800 °С.
Рассматривая термограммы карбоксилатов железа [20–28], можно выделить следующие моменты. Основным продуктом термического разложения карбоксилатов Fe является Fe2O3 [20–22, 26–28] в разных температурных интервалов. В работах [23–25] получают металлические наночастицы Fe, Ni, Cu методом термического разложения соответствующих карбоксилатов. В результате образуются частицы металлов размерами до 10 нм, образующие кластеры (агломераты) размером до нескольких микрон. В работах [29–33] показаны особенности термического разложения ароматических карбоновых кислот. Эти сведения важны при интерпретации термограмм соответствующих солей.
Целью данной работы является интерпретация процессов (и соответствующих температур, тепловых эффектов и изменений массы) при термолизе пяти органических солей железа, а также определение морфологии и структуры нанокомпозитов, образующихся при их термолизе в аргоне.
Экспериментальная часть
Для проведения работы были синтезированы ароматические карбоксилаты (салицилаты, бензоаты, 8-гидроксихинолинаты, фталаты, п-аминобензоаты) железа (III) по методике [18, 19]. Для синтеза использовались химически чистые FeCl3·9H2O, салицилат и бензоат Na, 8-гидроксихинолин, фталевая и п-аминобензойная кислоты, NaOH. В качестве растворителей использовались вода и 1,4-диоксан. Соли переходных металлов и NaOH растворяли в воде, а кислоты растворяли в 1,4-диоксане при нагревании до 80 °С. Растворы NaOH и кислоты смешивали в стехиометрическом соотношении для получения однозамещенного карбоксилата натрия. Салицилат и бензоат натрия растворяли в 1,4-диоксане при нагревании до 80 °С. Выход продукта реакций составлял 70–90 %. Реакции протекали мгновенно, растворы карбоксилатов железа (III)
окрашивались в красно- б у рый цвет. В течение нескольких суток происходил о ис п а ре ни е р а с тво рит е ля при к омн а тн о й тем пер атуре. Затем полученные продукты перекрис та ллиз овы в а ли и з г орячего 1,4-ди о к с ан а д ля очистк и от NaCl.
По лу че нн ые к а р б о кс и л а ты были исследованы на синхронном терм и чес к ом а н а лиз а то р е Netzsch STA 449 F1 J up i t er. П р едварительно была произведена оценка чист оты полу ч енны х со еди не н ий м е тод о м рентге нофлуоресцентного анализа на рентгеновском э н е ргод и с п е рс ионн ом спектрометре Oxford INCA X - max 80, а также методом рентгенофазового анализа на рентгенов ском по ро шк о в ом ди фр ак том е тре Ri g a k u U lt i ma IV. Термическое исследование проводилось в к ор у н дов ом тиг ле п р и на г р е в ании об ра зц о в м асс ой о т 1 0 д о 15 мг в интервале температур от 30 до 900 °С в дв у х в ари а нтах атмосферы в печи термоанализатора: возд у х и A r . С к ор ость н а г р ев а сос тав л ял а 1 0 К / мин . После термолиза солей фазовый состав прод ук тов их разложения изучался м е тодом р ентг еноф а зового анализа, морфология металлооксидны х ф а з – методом ска н иру ющ е й э ле к тронн о й м ик рос ко п ии на м ик роско п е J e o l J SM-7001F, а их состав – на рентгенов ском эне рго д исперс и о н но м с п е к тром е т р е Oxford INCA X-max 80.
Результаты и обсуждения
Анализ химического со став а карбоксилатов выявил в них незначительную при м ес ь NaCl, которая не превышала 1 масс. %. Те рм ический анализ карбоксилатов Fe(III) подробно ра с см о т рен на т е рмо г ра м м е ра з ло ж ени я ф та лата Fe ( I II) (рис. 1 , 2). Проведен подробный анализ термического разложения фталата железа ( I II) в и н те р ва ле темп ера ту р от 25 °С до 900 °С в атмосфере аргона и воздуха.
Пр оц е с с ы ра з л о же н ия с о ли проте кают в шесть этапов в атмосфере аргона (Ar) и в четыре ступ е ни в а тм о сфере в о зд уха (воздух). В процессе термического разложения в случаях (Ar) и (в оз ду х) в и нтер в але те м п е ра ту р от 60 д о 205 °С происходит потеря массы образца величиной 19,88 % (Ar) и 19,04 % (О 2 ) (по кривой ТГ) при дегидратации примеси фтале в ой к и с ло ты .
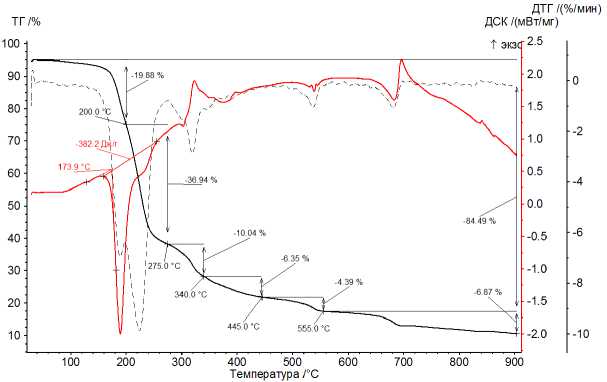
Рис. 1. Диаграмма ТГ-ДСК термического распада фталата железа (III) при нагревании образца в атмосфере Ar
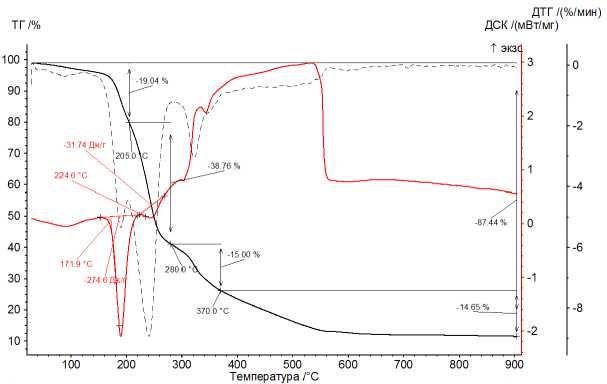
Рис. 2. Диаграмма ТГ-ДСК термического распада фталата железа (III) при нагревании образца в атмосфере воздуха
Визуальный осмотр и электронная микроскопия не выявили признаков плавления в образовавшихся продуктах. Тем не менее, сходство в первых двух этапов позволяет предполагать, что они относятся к примеси чистой фталевой кислоты и происходящим с ней процессам.
Плавление о -фталевой кислоты при быстром нагревании происходит при 200–211 °С, особенности её поведения при термическом разложении описаны в [34–36]. Дегидратация кислоты должна сопровождаться потерей лишь 10,83 масс. %, но наблюдаемая потеря в три раза выше, что позволяет предполагать испарение не только молекул воды, но и её ассоциатов с молекулами кислоты или ангидрида.
На второй ступени наблюдается потеря массы образца величиной 36,94 % (Ar) и 38,76 % (воздух) от исходной массы при температурах 200–275 °С (Ar) и 205–280 °С (воздух).
На последующих ступенях происходит дальнейшее снижение массы. Выше 300 °С в атмосфере воздуха происходит горение образца до температуры 600 °С. К этому моменту сгорание образца заканчивается, поэтому продуктом является Fe 2 O 3 . В атмосфере аргона потеря массы при нагреве продолжается до 900 °С.
Общая потеря массы образца составляет 84,94 % (Ar) и 87,44 % (воздух) от исходной массы образца. Можно предположить, что протекающие процессы очень схожи, поэтому схожими будут и продукты термического распада.
Однако по результатам рентгенофазового анализа основными твёрдыми продуктами термического распада этой соли являются Fe 3 С (87 %) и Fe (3 %) для случая (Ar) и смесь Fe 2 O 3 (90 %) + Fe 3 O 4 (10 %) для случая (воздух). Дифрактограммы твёрдых продуктов термолиза фталата Fe(III) представлены на рис. 3, 4.
#
##
*Fe
#Fe3C
#
*
* Fe2O3
# Fe3O4
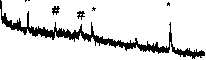
20 40 60 80
2 9, °
* **
2 9,o
Рис. 3. Дифрактограмма твёрдых продуктов термического распада фталата Fe (III) при 900 °С в Ar
Рис. 4. Дифрактограмма твёрдых продуктов термического распада фталата Fe (III) при 900 °С на воздухе
Методом сканирующей электронной микроскопии был проведён анализ продуктов термолиза фталата железа (III) (рис. 5, 6).
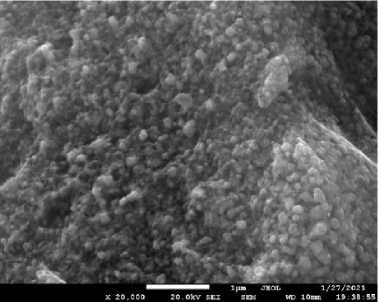
Рис. 5. Изображение продуктов термолиза фталата железа (III) после разложения при 900 °С (х20000) в аргоне
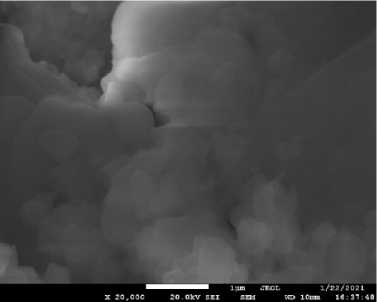
Рис. 6. Изображение продуктов термолиза фталата железа (III) после разложения при 900 °С (х20000) на воздухе
Как видно по микрофотографиям, частицы твёрдых продуктов термолиза фталата железа (III) на воздухе крупнее частиц продуктов термолиза в аргоне. В аргоне образовавшиеся частицы имеют сферическую форму и размер 20–200 нм. В случае разложения на воздухе размер частиц составлял 0,4–4 мкм.
По измеренным массовым долям образующегося на воздухе оксида железа можно предложить несколько вариантов формул исходного соединения (табл. 1). Вариант Fe 2 (OН) 2 (Phthal)(HPhthal) 2 ближе других к наблюдаемым потерям массы, если учесть эффекты, внесенные примесью свободной кислоты. Остаток Fe 2 O 3 составляет 12,56 масс. % (см. рис. 2), что соответствует 15 масс. % Fe 2 O 3 для чистого образца соли, если учитывать разбавление фталевой кислотой на 19–20 масс. %.
Таблица 1 Гипотетические формулы полученного фталата железа
Величина |
Fe(HPhthal)3 |
FeO(HPhthal) |
Fe 2 (OН) 2 (Phthal)(HPhthal) 2 |
Молярная масса соли, г/моль |
467 |
237 |
640 |
% Н2О в виде ОН-групп |
0 |
0 |
5,31 |
Число молекул воды |
0 |
0 |
0 |
% Fe 2 O 3 |
14,52 |
33,76 |
25,00 |
На рис. 7–16 приведены термограммы ароматических карбоксилатов Fe (III).
В табл. 2 указаны процессы термического разложения перечисленных солей и характеристика продуктов термолиза в двух атмосферах.
Анализ кривых ТГ-ДСК термического разложения ароматических карбоксилатов железа (III)
Таблица 2
Соли |
Характеристика продуктов термолиза (твёрдый остаток) |
Описание термического разложения |
||
Состав остатка и размер зерна металлсодержащего компонента в остатке |
Количество ступеней на кривой ТГ-ДСК, температурные интервалы процесса термолиза |
|||
воздух |
Ar |
воздух |
Ar |
|
1 |
2 |
3 |
4 |
5 |
8-гидрокси-хинолинат железа (III) Fe 2 O(OH) (8OHQ) 3 |
100 % Fe 2 O 3 . ОКР частиц Fe 2 O 3 : 34 нм. Размер частиц: 0,8–5 мкм |
60 % Fe 3 C, 10 % FeO, 30 % Fe 3 O 4 , ОКР частиц Fe 3 C: 39 нм. ОКР частиц FeО: 10 нм. ОКР частиц Fe 3 О 4 : 2 нм. Размер частиц: 0,2–2 мкм |
6 ступеней. Потеря 8-гид-роксихинолина при 100–305 °С, потеря массы 6,08 %. В интервале температур 369– 435 °С происходит окисление образца. Общая потеря массы 71,8 % |
5 ступеней. Потеря 8-гидроксихинолина при 100–250 °С, потеря массы 5,27 %. При 327 °С происходит плавление образца. Общая потеря массы 46,32 % |
Бензоат железа (III) Fe2O(benz)4 |
100 % Fe 2 O 3 ОКР частиц: 20 нм. Размер частиц: 0,2–1,0 мкм |
23 % Fe, 77 % углерода. ОКР частиц Fe: 38 нм. Размер частиц: 30–600 нм |
7 ступеней. Испарение бензойной кислоты при 60–140 °С с потерей массы в 4,93 %. К окончанию разложения при 690 °С образуется Fe 2 O 3 . Общая потеря массы 79,96 % |
7 ступеней. Испарение бензойной кислоты при 80– 135 °С с потерей массы в 4,87 %. При разложении 500– 900 °С образуется Fe. Общая потеря массы в 63,96 % |
Окончание табл. 2
1 |
2 |
3 |
4 |
5 |
Фталат железа (III) Fe 2 (OН) 2 (Phthal) (HPhthal) 2 |
87 % Fe 3 С, 3 % Fe. ОКР частиц: 4 нм. Размер частиц: 0,4–4 мкм. |
90 % Fe 2 O 3 , 10 % Fe 3 O 4 . ОКР частиц Fe2O3: 30 нм, ОКР частиц Fe3O4: 90 нм. Размер частиц: 20–200 нм |
4 ступени. Испарение фталевой кислоты при 100–204 °С с потерей массы 18,56 %. Свыше 600 °С потери массы нет, образовались оксиды Fe. Общая потеря массы в 87,44 % |
5 ступеней. Испарение фталевой кислоты 100– 198 °С с потерей массы в 18,63 %. Общая потеря массы в 84,43 % |
Салицилат железа (III) Fe 2 О(ОН)(HSal) 3 |
100 % Fe 2 O 3 . ОКР частиц: 40 нм. Размер частиц: 0,1–0,8 мкм. |
61 % Fe 3 C, 22 % Fe, 17 % Fe 3 O 4 . ОКР частиц Fe3C: 27 нм, ОКР частиц Fe: 40 нм, ОКР частиц Fe3O4: 15 нм Размер частиц: 40–400 нм |
5 ступеней. Испарение салициловой кислоты при 100–180 °С. Потеря массы 65,28 %. Общая потеря массы в 73,27 % |
4 ступени. Испарение салициловой кислоты при 100– 180 °С. Потеря массы 6,83 %. Общая потеря массы 78,42 % |
п-аминобензоат железа (III) безводный Fe 2 О(OH) 2 (pАB) 2 |
80 % Fe3O4, 10 % Fe 3 C 10 % FeO ОКР частиц Fe 3 O 4 : 15 нм. ОКР частиц Fe 3 C: 15 нм ОКР частиц FeO: 20 нм Размер частиц: 30–120 нм |
90 % Fe 3 C. ОКР частиц: 20 нм. Размер частиц: 120–600 нм |
5 ступеней. Испарение п -аминобензой-ной кислоты при 60–185 °С, потеря массы в 10,21 %. Общая потеря массы в 65,46 % |
4 ступени. Испарение п -аминобензой-ной кислоты при 60– 185 °С, потеря массы в 9,98 %. Общая потеря массы в 67,31 % |
Количество ступеней термического разложения, исходя из данных табл. 2, не зависит от характера газовой атмосферы над образцом. Для каждой соли можно выделить повторяемость в числе ступеней разложения. Получается, что на процесс термолиза карбоксилатов Fe(III) влияет только строение органического аниона, в данном случае, заместителей в бензольном кольце.
При дальнейшем нагревании некоторые образцы (кроме фталата железа (III)) плавились в интервале температур от 200 до 400 °С. Также для некоторых образцов (фталата железа (III)) была характерна полимеризация из расплава в интервале температур от 300 до 400 °С. При дальнейшем нагреве происходил пиролиз с образованием аморфного углерода и формированием оксидов железа и карбида железа (в атмосфере Ar) либо полное окисление твёрдого остатка (в атмосфере воздуха) с образованием оксидов железа и карбида железа.
Как можно наблюдать, для каждой соли характерны одинаковые процессы при термолизе в разных атмосферах. Для карбоксилатов Fe, разлагавшихся в атмосфере воздуха, на кривой ДСК наблюдается процесс окисления. Он отображен в виде возрастания и убывания функции (трапе-циедальная форма) отклика на кривой ДСК в интервале температур в среднем от 300 до 700 °С.
Высокая общая потеря массы от 50 до 80 % указывает на постепенное разложение до аморфного углерода и потерю части металлсодержащих твёрдых продуктов вследствие их улетучивания. При сравнении общих потерь масс видно, что на воздухе потеря массы выше, чем в аргоне для 8-гидроксихинолината, фталата и бензоата железа (III). Это означает, что наличие окислительной атмосферы ускоряет разложение кислотных остатков до простых летучих продуктов (СО 2 , СО, Н 2 О). В атмосфере аргона же происходит постепенный распад с выделением более сложных газообразных продуктов термолиза.
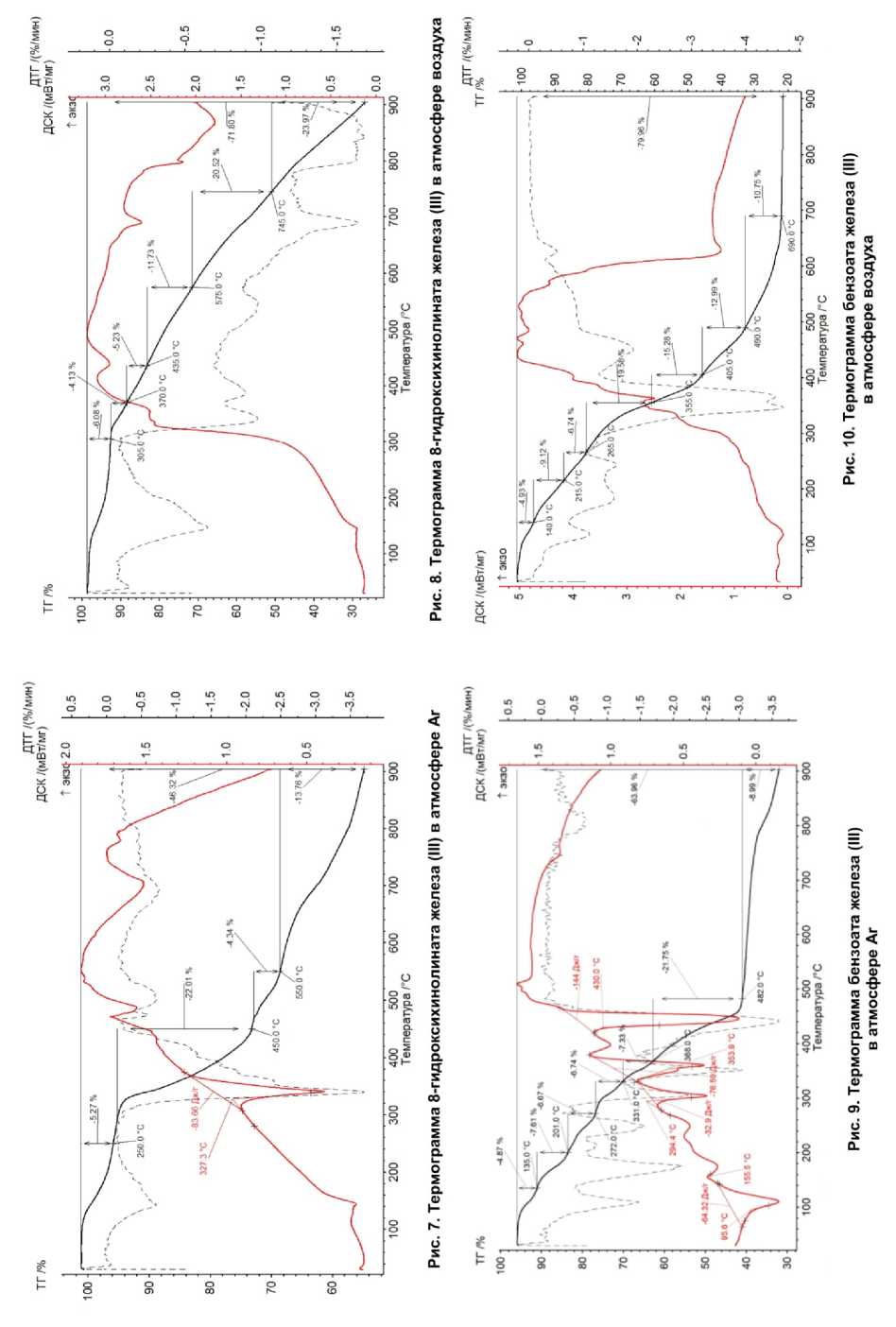
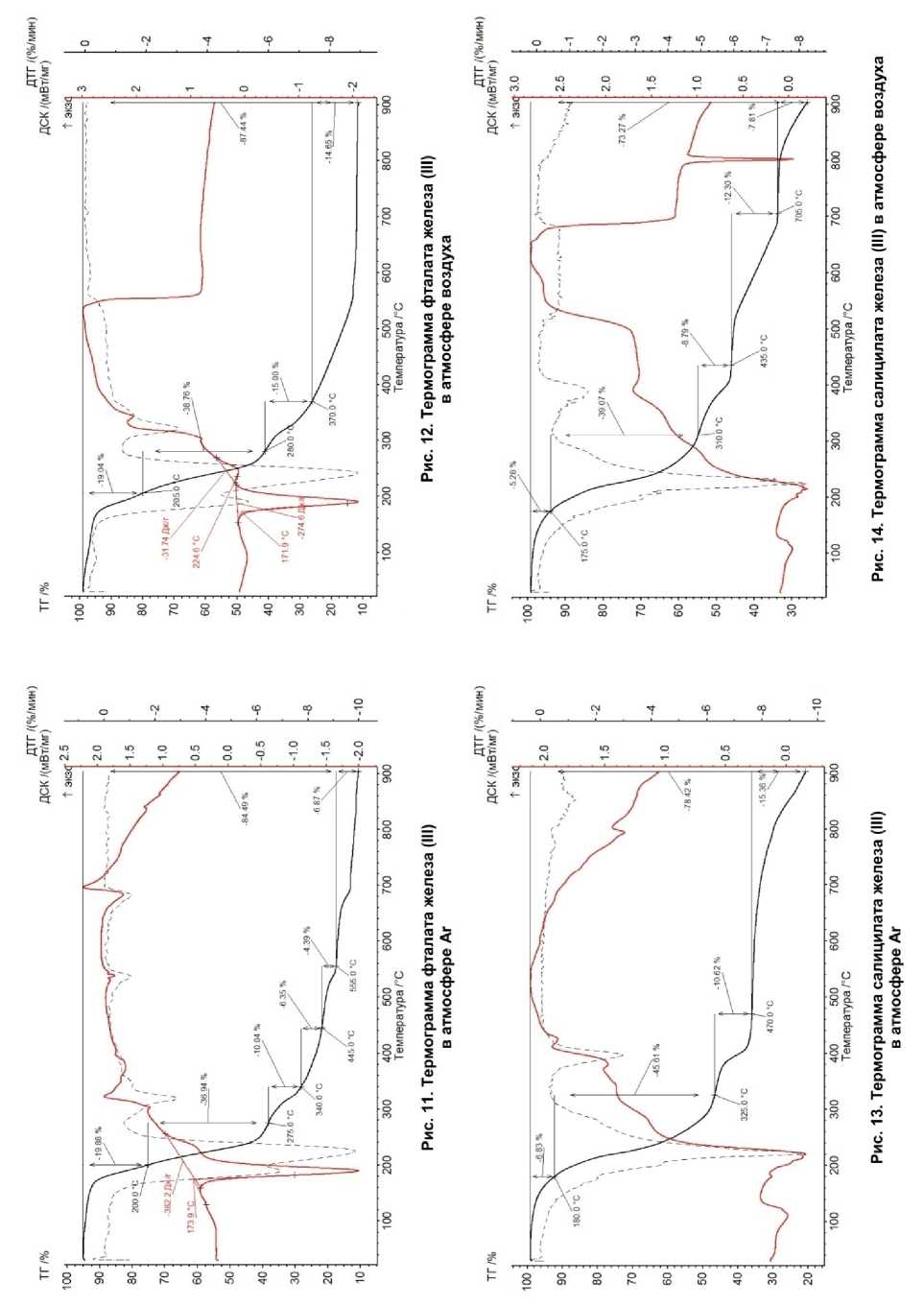
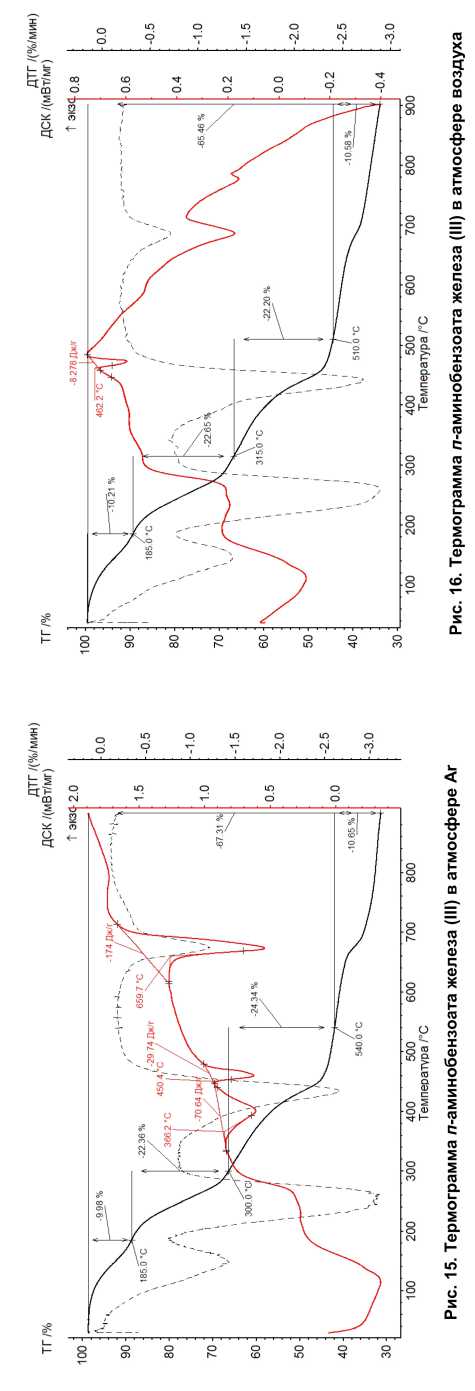
В результате термического разложения карбоксилатов Fe (III) основными твёрдыми продуктами являются оксиды и карбиды железа и углерод. Причём углерод в продуктах характерен для разложения в атмосфере аргона, так как атмосфера является нейтральной и происходит пиролиз солей. Кислород остаётся от аниона соли и входит в состав оксидов железа.
Согласно исследованию морфологии продуктов термолиза можно заключить, что размер образующихся кристаллических частиц доходил до 5 мкм. При этом размер области когерентного рассеяния был значительно меньше и находился в нанометровой размерности. Анализируя морфологию твёрдых продуктов термолиза, можно заметить, что зернистость и форма твёрдых продуктов термолиза зависит не от атмосферы термолиза, а от кислотного остатка. В случае с Fe 2 O(benz) 4 в Ar частицы Fe приняли сферическую форму, в остальных случаях подобного не произошло.
Заключение
В результате анализа термического разложения рассмотренных карбоксилатов железа (III) были выявлены следующие закономерности. Во-первых, общая потеря массы на воздухе выше, чем в аргоне при термолизе соли для некоторых солей. Во-вторых, число ступеней разложения зависит от природы ароматического карбоксилатного остатка соли. В-третьих, основные пики на кривых ДСК для одной соли в разных атмосферах повторяются. Небольшое различие наблюдается в температурах и энтальпии происходящих на рассматриваемых этапах процессов. Это свидетельствует о схожести протекающего термолиза независимо от атмосферы, в которой происходит разложение. В-четвёртых, состав продуктов разложения схож для термолиза в обоих условиях. Так, во многих случаях продуктами были оксиды железа и карбид железа. Это значит, что кислород от кислотного остатка прочно связан с атомом железа и вместе с железом остаётся в твёрдых продуктах совместно с аморфным углеродом и продуктами восстановления Fe 2 O 3 . Образовавшиеся частицы твёрдых продуктов в матрице из аморфного углерода обладают наноразмерами и, обладая подвижностью при высокой температуре, агломерировали до более крупных частиц.
Список литературы Получение порошковых углеродных композитных наноматериалов термическим разложением ароматических карбоксилатов Fe (III)
- Le V.T., Doan V.D., Tran V.A. et al. // Materials Research Bulletin. 2020. V. 129. P. 110913. DOI: 10.1016/j.materresbull.2020.110913.
- Ferial G., May A., Robiah Y., Raja N.O. // Synthesis, Technology and Applications of Carbon Nanomaterials. 2019. P. 1. DOI: 10.1016/B978-0-12-815757-2.00001-2.
- AliM., Li Y., SongB., YudongH. // Journal of Nanomaterials. 2011. P. 1. DOI: 10.1155/2011/685081.
- Yehia M.M., Ihsanullah A.S., Tareq Al-Ansari // A Review of Carbon Nanomaterials' Synthesis via the Chemical Vapor Deposition (CVD) Method / Materials. 2018. V. 11. P. 822. DOI: 10.3390/ma11050822.
- Temidayo O.A. // Bioinorganic Chemistry and Applications. 2018. P. 1. DOI: 10.1155/2018/9354708.
- Ремпель A.A. // Успехи химии. 2007. Т. 76, № 5. C. 474. DOI: 10.1070/RC2007v076n05ABEH003674.
- Помогайло A^., Розенберг A.C., Джардималиева Г.И. // Успехи химии. Т. 80, № 3. C. 272. DOI: 10.1070/RC2011v080n03ABEH004079.
- Помогайло A^., Розенберг A.C., Джардималиева Г.И. // Российский химический журнал. 2009. Т. 53, № 1. C. 140.
- Yan J., Wang H., Jin B., Zeng M. // Journal of Solid State Chemistry. 2021. V. 297. P. 122060. DOI: 10.1016/jjssc.2021.122060.
- Yu W.W., Falkner J.C., Yavuz C.T., Colvin V.L. // Chemical Communication. 2004. P. 2306. DOI: 10.1039/B409601K.
- Siqueira A.P.C., Ionashiro E.Y., Bannach G., De Souza A.R. et al. // Thermochimica Acta. 2021. V. 698. P. 178892. DOI: 10.1016/j.tca.2021.178892.
- Muraishi K., Takano T., Nagase К., Tanaka N. // Journal of Inorganic and Nuclear Chemistry. 1981. V. 43, No. 10. P. 2293. DOI: 10.1016/0022-1902(81)80252-7.
- Davis R., SchultzH.P. // J. Org. Chem. 1962. V. 27, No. 3. Р. 854. DOI: 10.1021/jo01050a039.
- Суздалев И.П., Максимов Ю.В., Буравцев В.Н., Имшенник В.К. и др. // Коллоидный журнал. 2000. Т. 62. C. 257.
- Sileo E.E., Morando P.I., Baumgartner W.C., Bless M.A. // Thermodinamica Acta. 1991. V. 184. P. 295. DOI: 10.1016/0040-6031(91)80031-d.
- Sánchez N.M., Klerk A. de // Thermochimica Acta. 2018. V. 662. Р. 23. DOI: 10.1016/j.tca.2018.01.015.
- Dollimore D., Griffiths D. L. // Journal of Thermal Analysis. 1970. V. 2. Р. 229.
- Фейизоглу А., Алтун О., Фиринци А., Туркы-Алмаз М. // Известия вузов. СевероКавказский регион. Естественные науки. 2003. № 3. С. 58.
- Джардималиева Г.И., Помогайло А.Д. // Успехи химии. 2008. Т. 77. № 3. С. 270. DOI: 10.1070/RC2008v077n03ABEH003682.
- Bassi P.S., Randhawa B.S., Jamwal H.S. // Thermochimica Acta. 1983. V. 69. P. 367. DOI: 10.1016/0040-6031(83)80343-8.
- Gorinchoy V., Shova S., Melnic E, Kravtsov V. et al. // Chem. J. Mold. 2013. V. 8, No. 2. P. 83. DOI: 10.19261/cjm.2013.08(2).10.
- Gorinchoy V., Zubareva V., Melnic E., Kravtsov V. // Chem. J. Mold. General, Industrial and Ecological Chemistry. 2018. V. 13, No. 1. P. 46. DOI: 10.19261/cjm.2018.483.
- Yudanova L.I., Logvinenko V.A., Sheludyakova L.A., Korolkov I.V. et al. // Russian Journal of Physical Chemistry A. 2019. V. 93, No. 7. Р. 1327. DOI: 10.1134/S003602441907032X.
- Yudanova L.I., Logvinenko V.A., Yudanova N.F., Rudina N.A. et al. // Russian Journal of Physical Chemistry A. 2016. V. 90, No. 6. Р. 1206. DOI: 10.1134/S0036024416060315.
- Yu Q., Zhao S., Asuha S. // Ceramics International. 2022. V. 48. P. 6556. DOI: 10.1016/j .ceramint.2021.11.203.
- Bassi P.S., Randhawa B.S., Bilaspuri G.K. // Journal of Therrnal Analysis. 1986. V. 31. Р. 1007. DOI: 10.1007/BF02119254.
- Galwey A.K. // Journal of the Chemical Society. 1965. Р. 4235.
- Bassi P.S., Uppal P., Bilaspuri G.K. // Journal of Thermal Analysis. 1997. V. 49. P. 703. DOI: 10.1007/bf01996754.
- Winter K., Barto D. // Canadian journal of chemistry. 1970. V. 48 (24). P. 3797. DOI: 10.1139/v70-641.
- Rajasekaran M., Anbusrinivasan P., Mojumdar S. C. // Journal of Thermal Analysis and Calorimetry. 2010. V. 100. P. 827. DOI: 10.1007/s10973-010-0761-5.
- Wesolowski M., Konarski T. // Journal of Thermal Analysis and Calorimetry. 1999. V. 55. P. 995. DOI: 10.1023/a:1010162607157.
- Radecki A., Wesolowsk M. // Journal of Thermal Analysis. 1976. V. 9. Р. 357. DOI: 10.1007/BF01909400.
- Teixeira J.A., Nunes W.D.G., Colman T.A.D., Nascimento A.L.C.S do, et al. // Thermochimica Acta. 2016. V. 624. P. 59. DOI: 10.1016/j.tca.2015.11.023.
- Кнунянца И.Л. М.: Советская энциклопедия, 1998. 783 с.
- Никольский Б.П. М.: Государственное научно-техническое издательство химической литературы, 1963.1168 с.
- Кнунянца И.Л. М.: Советская энциклопедия, 1983. 786 с.