Получение расклинивающего материала (пропанта) для нефтедобывающей промышленности из металлургических шлаков
Автор: Адилов Галымжан Алибекович, Поволоцкий Александр Давидович, Зырянов Сергей Владимирович, Рощин Василий Ефимович
Журнал: Вестник Южно-Уральского государственного университета. Серия: Металлургия @vestnik-susu-metallurgy
Рубрика: Металлургия техногенных и вторичных ресурсов
Статья в выпуске: 1 т.18, 2018 года.
Бесплатный доступ
Для повышения эффективности отдачи нефтяных скважин с применением технологии гидроразрыва пласта трещины, создаваемые в ходе гидроразрыва, заполняют расклинивающим материалом (пропантом). При этом эффективность нефтеотдачи скважин возрастает за счёт предупреждения смыкания трещин под действием горного давления. В качестве пропанта используют различные керамические материалы в виде гранул диаметром от 0,5 до 1,2 мм. Для изготовления пропантов целесообразно использовать отходы металлургического производства в виде шлаков, образующихся в различных плавильных агрегатах - доменных печах, конвертерах и сталеплавильных печах, а также при получении ферросплавов. Складирование этих шлаков требует больших территорий и сопряжено с экологическими проблемами. В данной статье изучена возможность получения высокопрочных магнезиально-кварцевых пропантов из смеси шлаков доменного производства с добавками недефицитных природных материалов - кварцита и магнезита. Технология получения пропантов опробована в лабораторных условиях. Шлаковую смесь расплавляли в индукционной печи с графитовым тиглем. Расплав гранулировали на специально разработанной центрифуге. Полученные гранулы испытаны по основным показателям, предусмотренным стандартом. Изучены макро- и микроструктура пропантов, водопоглощение, сопротивление раздавливанию, кислотостойкость. По всем показателям, за исключением кислотостойкости, пропанты показали вполне приемлемые свойства.
Пропанты, металлургический шлак, оксидный расплав, грануляция
Короткий адрес: https://sciup.org/147157127
IDR: 147157127 | DOI: 10.14529/met180108
Текст научной статьи Получение расклинивающего материала (пропанта) для нефтедобывающей промышленности из металлургических шлаков
Использование пропантов – гранулообразного материала, применяемого в нефтедобывающей промышленности в качестве расклинивающего элемента для повышения эффективности отдачи скважин при использовании технологии гидроразрыва пластов, непрерывно увеличивается. Применяемая в настоящее время многуступенчатая технология производства керамических пропантов предусматривает использование специального сырья, в том числе импортируемого боксита, каолина, высоких затрат энергии, сложного импортного оборудования. В связи с этим актуальным является разработка технологии производства пропантов из дешевого и доступного сырья с использованием простого и эффективного оборудования.
Цель работы – разработка состава и технологии пропантов для нефтяных скважин на основе шлаковых отходов металлургического производства.
Процесс получения пропантов включает плавление шлака, корректировку его состава, центробежное распыление на гранулы требуемого размера, термическую обработку, сепарацию. В случае использования шлака непосредственно после металлургической печи, что более предпочтительно, перед распылением расплав сливается в миксер, куда подаются добавки. В качестве сырья можно использовать шлаки химического состава, изменяющегося в широком диапазоне, однако предпочтительным является сырье с минимальным содержанием оксидов железа и преобладанием кремнезема.
На разработанном экспериментальном оборудовании из доменных шлаков получены образцы пропантов, по основным показателям, соответствующие требованиям ГОСТ
Р 54571–2011 «Пропанты магнезиально-кварцевые».
Экспериментальная часть
В качестве исходного материала использовали складированные отвальные доменные шлаки. Состав шлака по результатам определения в 3 пробах приведён в табл. 1.
Шихта для пропантов представляла из себя смесь доменного шлака (45 % масс.), кварцита (45 %), магнезита (10 %). Предварительно на лабораторном оборудовании произвели измельчение шихтовых материалов. Полученную шихту сушили для удаления влаги. Далее в индукционной печи в графитовом тигле шихту расплавили, а расплав подвергли грануляции на специально сконструированной и изготовленной центрифуге. Полученный материал разделяли на фракции 0,2…0,63 мм, 0,63…1,0 мм, 1,0…1,6 мм, 1,6…2,5 мм и 2,5…4 мм, 12…18 мм, 8…12 мм и 5…8 мм. Далее проводили термообработку.
Полученные пропанты проверяли на соответствие стандарту по нескольким параметрам:
-
1) подвергали химическому и структурному анализу;
-
2) определяли водопоглащение и сопротивление раздавливанию;
-
3) определяли кислотостойкость.
Для проведения химического состава и структурного анализа пропанты заливали эпоксидной смолой, изготавливали микрошлифы, которые изучали на электронном микроскопе JeolJSM-7001F. Вид пропантов на шлифе и результаты определения химического состава показаны на рис. 1.
Сведения о микроструктуре пропантов разного состава представляет рис. 2. Видно, что с повышением содержания магнезии структура пропантов становится более мелкой. Размер зерен при содержании 11 % MgO около 1 мкм, а при 16 % MgO около 0,5 мкм.
Водопоглощение – это отношение массы воды, поглощенной пористым телом при его полном насыщении, к массе сухого образца. Определение проводили по методике согласно ГОСТ 2409–84 с использованием кипячения образцов в воде и последующего взвешивания. Оно показало полное отсутствие водо-поглощения, что свидетельствует об отсутствии открытой пористости [1].
Сопротивление раздавливанию пропантов – это массовая доля гранул, разрушенных под воздействием заданной сжимающей нагрузки. Эта эксплуатационная характеристика зависит от нескольких факторов: структуры кристаллической решетки материала, наличия в ней дефектов, размера и распределения фаз после термической обработки. Испытания
Таблица 1
Состав доменного шлака, % масс.
Na 2 O |
MgO |
Al2O3 |
SiO 2 |
K 2 O |
CaO |
|
1 |
0,6 |
14 |
13 |
39 |
1,0 |
32 |
2 |
0,7 |
4 |
9 |
45 |
1,3 |
40 |
3 |
0,6 |
9 |
12 |
42 |
1,1 |
35 |
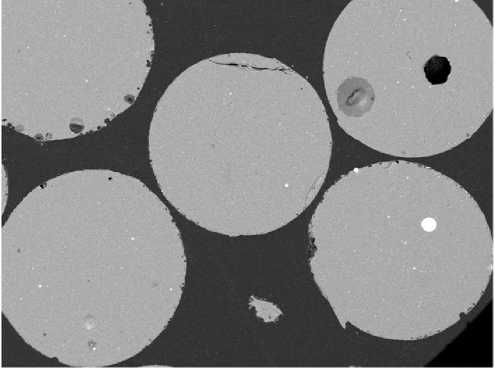
Электронное изображение 1
Рис. 1. Вид пропантов в разрезе на шлифе и их состав, % масс:
Na 2 O MgO Al 2 O 3 SiO 2 K 2 O CaO FeO
2,1 11 11 56 1,0 18 1,1
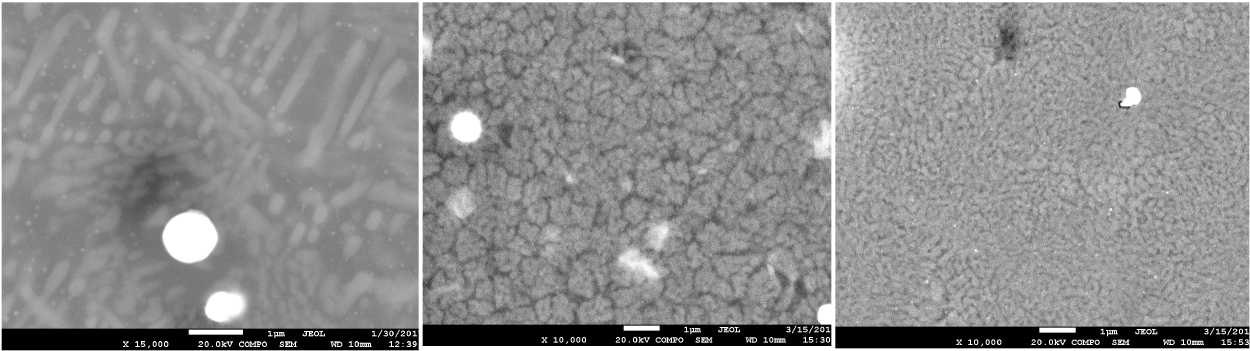
а) б ) в )
Рис. 2. Структура пропантов с разным содержанием MgO, % масс.: а – 6, б – 11, в – 16
проводили на гидравлической машине для испытаний на сжатие. Она обеспечивает постепенное и плавное увеличение усилия и оборудована системой измерения приложенного усилия с погрешностью не более 2 % [1–3].
Пробу пропантов просеивали на лабораторном вибраторе в течение 10 мин через набор сит номеров 12 и 20 для фракции 12…20; 16 и 20 (фракция 16…20); 16 и 30 (фракция 16…30); 20 и 40 (фракция 20…40); 40 и 70 (фракция 40…70). Пропанты, оставшиеся на верхнем сите и прошедшие через нижнее сито, отбрасывали, а остальные использовали для испытания. Серию испытаний проводили на восьми навесках: по две параллельные навески при удельных давлениях 51,7; 68,9; 86,1 и 103,3 Н/мм2.
Просеянные пропанты взвешивали с точностью до 0,1 г и засыпали в приспособление для раздавливания, перемещая точку истечения пропантов для обеспечения максимального удельного давления, которое необходимо поддерживать в течение 2 мин. Затем приспособление снимали с испытательной машины и с помощью кисточки его содержимое переносили на набор сит. После рассева в течение
-
10 мин на вибраторе взвешивали раздавленные гранулы пропантов из поддона с точностью до 0,1 г и определяли долю разрушенных ровной поверхности. Для этого поверхность загруженных пропантов выравнивали поворотом пуансона на 180° без применения усилия. Затем, не встряхивая, помещали приспособление для раздавливания в машину для испытания на сжатие. Образец равномерно нагружали в течение 1 мин до заданного для гранул усилия и рассчитывали количество разрушенных гранул по формуле
N = (m1/ m2)·100 %, где m1 – масса разрушенных гранул; m2 – масса гранул до испытания.
За результат испытаний принимают среднее арифметическое результатов двух параллельных определений при заданном удельном давлении. Результаты показаны в табл. 2
Сферичность и округлость гранул пропантов определяли по стандартной методике. Метод основан на визуальной оценке формы гранул, увеличенных с помощью микроскопа, путем сравнивания с диаграммой Крумбьена – Шлосса [4]. Для определения сферичности и округлости пропанты насыпают на лист белой
Сопротивление раздавливанию пропантов
Таблица 2
При давлении, МПа |
Фракция, мм |
Допустимое количество разрушенных зерен по ГОСТ 51761–2005, % |
Фактическое количество разрушенных зерен, % |
34,5 |
0,63…1,0 |
10 |
3 |
1,0…1,6 |
15 |
4 |
|
51,7 |
0,63…1,0 |
15 |
10 |
1,0…1,6 |
20 |
11 |
|
68,9 |
0,63…1,0 |
20 |
9 |
1,0…1,6 |
25 |
19 |
|
86,1 |
0,63…1,0 |
20 |
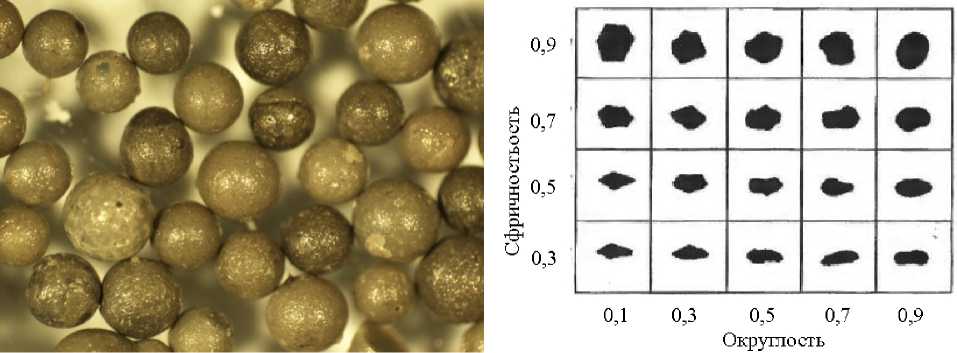
Рис. 3. Пропанты фракции 0,63^1 мм ( х 25) и диаграмма Крумбьена - Шлосса для визуального определения сферичности и округлости
бумаги, который помещают на предметный столик микроскопа. При соответствующем увеличении микроскопа определяют сферичность, а затем округлость каждой гранулы, сравнивая ее с диаграммой (рис. 3). За результат испытаний принимают средний арифметический результат. Согласно диаграмме Крумбьена – Шлосса коэффициент сферичности и округлости полученных пропантов составляет 0,9/0,9.
Испытания пропантов на кислото-стойкость проводили в Российском государственном университете (НИУ) им. И.М. Губкина и получили следующие результаты. Исследовали пропанты фракции 1,0…1,6 мм (условно 12/18) в смеси соляной и фторной кислот в концентрации 4:1 по методике стандарта ГОСТ Р 54571–2011. Согласно ГОСТ Р 54571–2011 температура теста 65 °С (±1 °С), навеска пропанта 5 г, объём смеси кислот – 100 мл, выдержка 30 мин. Расхождение на двух параллельных пробах должно быть не более 1 %. Растворимость полученных нами пропантов составила 14,8 и 19,4 %, что, согласно ГОСТ Р 54571–2011, выше максимально допустимого значения (не более 10 %) для магнезиально-кварцевых пропантов «Пропанты магнезиально-кварцевые. Технические условия».
Таким образом, результаты теста на ки-слотостойкость оказались неудовлетворительными, что, по-видимому, обусловлено относительно высоким содержанием в пропантах оксидов кальция.
Заключение
Разработаны состав и технология получения пропантов на основе металлургических шлаков. Пропанты на основе доменного шлака удовлетворяют требованиям стандарта по всем показателям за исключением химической стойкости. Поэтому они не могут использоваться в скважинах с кислотной средой. Использование полученных пропантов в скважинах с иными условиями эксплуатации требует дополнительного изучения. Для повышения кислотостойкости пропантов необходимо корректировать химический состав материала.
Список литературы Получение расклинивающего материала (пропанта) для нефтедобывающей промышленности из металлургических шлаков
- Потапова, А.П. Алюмосиликатные керамические пропанты на основе огнеупорного глиносодержащего сырья: дипломный проект/А. П. Потапова. -Томск, 2016. -77 с.
- Решетова, А.А. Керамические пропанты на основе природного алюмосиликатного сырья: дис. … канд. техн. наук/А.А. Решетова. -Томск, 2009. -188 с.
- Долгушин, В.А. Исследование и разработка технологии ограничения водопритока в трещине гидроразрыва: дис. … канд. техн. наук/В.А. Долгушин. -Тюмень, 2013.
- ГОСТ Р 51761-2005. Пропанты алюмосиликатные. Технические условия. -М: Стандартинформ, 2006. -31 с.