Построение цифрового изображения структуры поверхности по профиллограмме для определения её характеристик в соответствии с ГОСТ Р ИСО 25178-2- 2014
Автор: Абрамов А.Д., Носов Н.В., Андрюхина Т.Н.
Журнал: Известия Самарского научного центра Российской академии наук @izvestiya-ssc
Рубрика: Машиностроение и машиноведение
Статья в выпуске: 4-2 т.25, 2023 года.
Бесплатный доступ
В статье рассмотрены новые требования к характеристикам микрогеометрии рабочих поверхностей деталей машин в соответствии с ГОСТ Р ИСО 25178-2- 2014. Показано, что для вычисления таких характеристик необходимо иметь информацию о трёхмерном распределении параметров микрорельефа, то есть перейти от профильных параметров микрогеометрии к параметрам её структура. В связи с этим в статье рассмотрено применение программного метода формирования структура поверхности на основе профилограмм, полученных более простыми устройствами.
Структура, микрорельеф, поверхность, изображение, цифровая обработка, зашумление, генератор псевдослучайных чисел
Короткий адрес: https://sciup.org/148327964
IDR: 148327964 | DOI: 10.37313/1990-5378-2023-25-4(2)-270-277
Текст научной статьи Построение цифрового изображения структуры поверхности по профиллограмме для определения её характеристик в соответствии с ГОСТ Р ИСО 25178-2- 2014
ющую роль в надежности и долговечности промышленных изделий при их эксплуатации [1-3]. В связи с этим важную роль приобретают и вопросы контроля параметров микрогеометрии поверхности изделий как на этапе их изготовления, а также и в процессе их эксплуатации. До недавнего времени основными документами, регламентирующими набор необходимых показателей микрогеометрии поверхности деталей характеризующими её качество, являлись ГОСТ 2789 – 73 и ГОСТ 25142 – 82, а также ISO 468:1982. При этом предполагалось, что сами показатели определялись на основе информации, полученной, как правило, профильными методами, в частности с помощью щуповых приборов – профилографов. Достоинства и недостатки этих методов рассмотрены в работах [4-5].
Однако, непрерывный рост требований к качеству выпускаемой продукции машиностроения определил разработку и внедрения в производство, в дополнении к рассмотренным выше ГОСТам, нового ГОСТ Р ИСО 25178-2— 2014, который утвержден и введен в действие Приказом Федерального агентства по техническому регулированию и метрологии от 12 декабря 2014 г. № 2059-ст 4 Настоящий стандарт идентичен международному стандарту ИСО 25178-2:2012 «Геометрические характеристики изделий (GPS). Структура поверхности. Ареал. Часть 2. Термины, определения и параметры структуры поверхности» (ISO 25178-2 «Geometrical Product Specifications (GPS) — Surface texture: Profile method — Part 2: Terms, definitions and surface texture parameters»).
В этом стандарте введены новые определения для характеристики поверхности, которые можно представить в виде диаграммы, приведенной на рисунке 1.
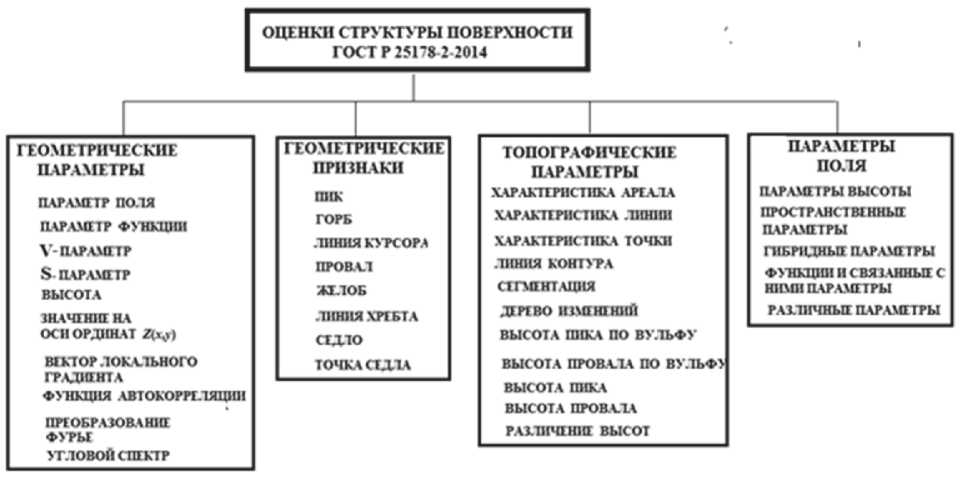
Рис. 1. Диаграмма оценок параметров структуры поверхности согласно ГОСТ Р 25178-2-2014
Как следует из приведенной диаграммы, новые параметры (признаки) существенно отличаются от параметров шероховатости, которые рассматривались в ГОСТ 2789 – 73 и ГОСТ 25142 – 82 и требуют для их вычисления наличие информации о трёхмерном описании высотных параметров поверхности. Очевидно, что применение профилографов в классическом варианте для получения информации о микрогеометрии исследуемой поверхности не позволяет использовать эту информацию для вычисления параметров структуры поверхности согласно приведенной диаграммы на рис. 1.
На практике для получения трёхмерных изображений в технических системах, в частности в робототехнике, широкое распространение получили системы стереозрения [6]. Однако, применение этих средств для получения 3D изображений исследуемого микрорельефа прецизионных поверхностей, имеющих шероховатость от меньше 0,15 мкм не представляется возможном в виду ограниченной разрешающей способности оптических систем, накладываемой на них дифракционным эффектом. Согласно литературным данным [7, 8] разрешающая способность объектива микроскопа зависит от значений нуме-рической (числовой) апертуры (A) объектива и конденсора и длины волны источника света (λ). Для пучка лучей, параллельных оптической оси микроскопа, разрешающую способность объектива микроскопа определяют по формуле d = λ/A.
Для наклонных лучей разрешающая способность в 2 раза выше:
d = λ /2 A , где λ – длина волны, нм; А – числовая апертура объектива.
Длина волны лучей источника света в видимой части спектра может меняться от 0,4 мкм
(400 нм) для фиолетовых лучей до 0,7 мкм (700 нм) для красных. При освещении объекта наклонными лучами разрешающая способность объектива микроскопа в 2 раза выше, чем при освещении прямо падающими лучами. Освещая препарат синими лучами ( λ = 0,47 мкм), т. е. применяя в осветителе синий светофильтр, можно изучать более тонкие структуры, чем при освещении обычным белым светом. Например: для объектива с A =1,4 при освещении белым светом ( λ = 0,55 мкм) диаметр наименьшей видимой частицы при прямо падающем свете равен 0,39 мкм, при косом освещении – 0,20 мкм, а при освещении синим светом – 0,34 и 0,17 мкм, соответственно. Максимальное разрешение, которое можно получить при использовании светового микроскопа, 0,20 – 0,35 мкм. Увеличить разрешающую способность можно при использовании ультрафиолетового света (длина волны 0,26 – 0,28 мкм), однако и в этом случае разрешение меньше, чем 0,13 – 0,14 мкм получить не удастся.
Для получения трёхмерных изображений с высокой разрешающей способностью в настоящее время используются интерферометры и конфокальные микроскопы [9-11], которые позволяют получать разрешение порядка 5нм. Однако эта аппаратура имеет значительные габариты, относительную сложность в эксплуатации и её использование возможно только в лабораторных условия. Кроме того, разработка и использование программного обеспечения для получения трёхмерных изображений с помощью этой аппаратуры требует привлечение специалистов высокой квалификации.
В связи с этим в предлагаемой статье рассматривается метод получения цифрового изображения исследуемого микрорельефа с помощью более простых и доступных средств получения
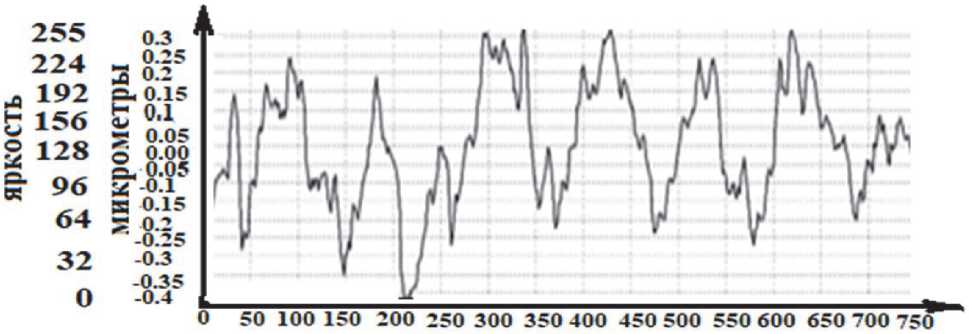
микрометры
Рис. 2a. Вид профилограммы информации о структуре поверхности, а именно с помощью профилографа. Для построения 3D модели изображений исследуемого микрорельефа прецизионных поверхностей используется профилограмма поверхности, полученная стандартными ГОСТовскими методами. Вид такой профилограммы приведен на рис. 2a.
На этой профилограмме значениям полученных высотных параметров в микрометрах ставятся в соответствие значения яркостного сигнала, показанные слева на рис. 2a. Эти значения яркостного сигнала в относительных безразмерных единицах будут соответствовать стандартным видеосигналам, используемым в мониторах персональных компьютеров. Далее эти цифровые значения сигнала, расположенные вдоль оси профилограммы «микрометры» вводятся в компьютер в виде одномерного массива. При этом количество элементов этого массива будет определять размер формируемого изображения в пикселях по оси X. Этот одномерный массив рассматривается как одна случайная реализация видеосигнала вдоль горизонтальной оси X, как бы полученного с видеокамеры, а его повторение вдоль оси Y позволит сформировать цифровую модель исследуемой поверхности. Затем с использованием программных средств библиотеки OpenCV [12] строится трёхмерное изображение исследуемого микрорельефа, то есть сигнал яркости и будет отображать высотный параметр микрорельефа. Для этого в компьютер вводится какое-либо полутоновое изображение в формате BMP. При этом размер одномерного массива должен соответствовать размеру изображения по оси X. В общем случае размер изображения по оси Y может задаваться пользователем произвольно. В данном конкретном случае было использовано изображение участка исследуемой поверхности с размерами 3×2,5мм, а формат изображения этого участка составлял 320×240 пикселей. Отметим также, что для этого микрорельефа, полученного шлифованием, и была записана профилограмма, приведенная на рис. 1. Цифровое изображение этого микрорельефа приведено на рис. 2b, а характерный график видеосигнала для этого изображения приведен на рис. 3
Для программного построения цифрового изображения этого же микрорельефа высотные значения с профилограммы были использована последовательно 4 раза для формирования одномерного массива. В результате была построена цифровая модель исследуемой поверхности микрорельефа. При этом каждая строка изображения строится по исходной профилограмме, приведенной на рис. 4, а вид полученного видеосигнала с этого изображения см. рис. 5.
Как видно из рис. 5 характер видеосигнала полностью повторяет рисунок профилограммы по шагу, что дает полное основание утверждать, что 3 D модель исследуемой поверхности, полученная в результате программного метода вполне адекватна реальному микрорельефу исследуемой поверхности, а полученная 3D модель микрорельефа может быть использован для вычисления его характеристик в соответствии с новым ГОСТ Р ИСО 25178-2— 2014. Следует также отметить, что использование обычного изображения ис-
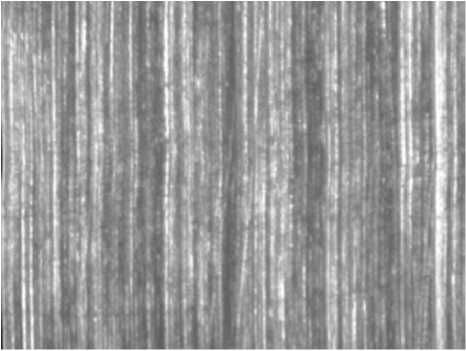
Рис. 2b. Изображение микрорельефа исследуемого участка поверхности
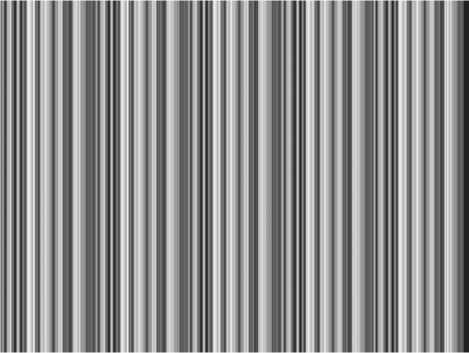
Рис. 4. Изображение микрорельефа, построенного по профилограмме
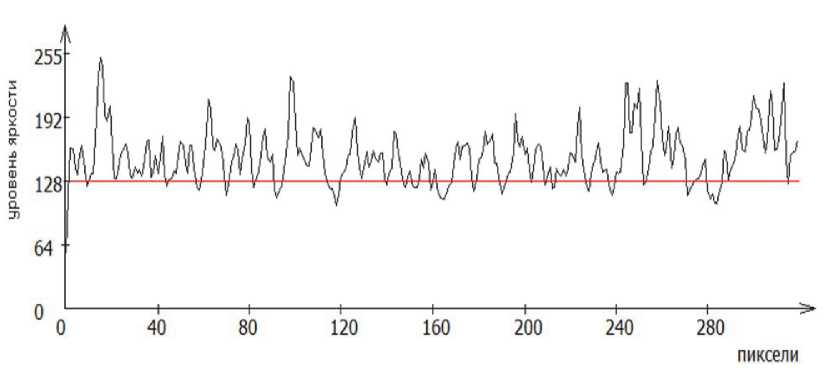
Рис. 3. Вид видеосигнала для изображения исследуемого микрорельефа с шагом 10-12 Пк
следуемого микрорельефа, приведенного на рис. 2b, не может служить источником достоверной информации для непосредственного вычисления структурных характеристик исследуемого микрорельефа. Отмеченное обстоятельство вытекает из сильных отличий видеосигнала, приведенного на рис. 3 и профилограммы., что так же подтверждает ранее сделанные выводы о применимости обычной микроскопии для вычисления структурных параметров микрорельефа.
Однако, полученное изображение 3D модели исследуемой поверхности не вполне адекватно отражает настоящий микрорельеф этой поверхности, так как каждая последующая строка данного изображения полностью повторяет предыдущую, построенную по исходной профилограмме. Для того, чтобы устранить отмеченный недостаток при по -строении изображения нам необходимо бы было иметь набор профилограмм, последовательно полученных с исследуемого микрорельефа по коор -динате Y. Например, для построения изображения формата 100×100 пикселей потребовалось бы получить 100 профилограмм, последовательно снятых по координате Y с анализируемого участка поверхности с шагом в один мм/пиксель. Естественно, что выполнить такие измерения на существующих в настоящее время профилографов/профилометрах не представляется возможным. В связи с этим в данной работе был предложен подход к построению 3D модели исследуемой поверхности, заключающийся в использовании генератора псевдослучайных чисел (ГПСЧ) [13] для зашумления каждой последующей строки строящегося изображения. Такой генератор реализован в языке программирования С++. Следует также отметить, что этот язык используется и для составления программ средствами OpenCV. Фрагмент программы при использовании ГПСЧ для за-щумления строк изображения приведен ниже.
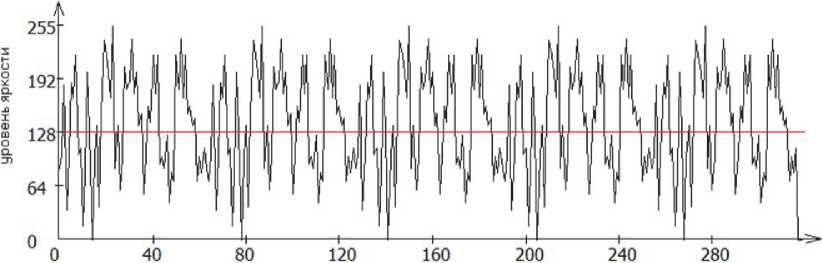
пиксели
Рис. 5. Вид видеосигнала для изображение цифровой [6] модели микрорельефа с шагом 10-12 Пк
//ВЫПОЛНЯЕМ РАНДОМИЗАЦИЮ ГПСЧ srand(rand_value);
{ ‘
}
//ПОКАЗЫВАЕМ СОЗДАННЫЙ МИКРОРЕЛЬЕФ imshow("CФOPM.PEЛЬEФ_2", img );
//ЗАПОМИНАЕМ СОЗДАННЫЙ МИКРОРЕЛЬЕФ imwrite("CФOPMИPOBAHHOE ЗАШУМЛЁННОЕ ИЗOБPAЖEHИE.bmp", img );
В данной программе предусмотрены разные проценты защумления строк изображения. Результаты программного формирования 3D изображений исследуемой поверхности с разной степенью зашумления строк изображения генератором ГПСЧ приведены на рис. 6, а графики видеосигналов для разных строк зашумленного изображения при состоянии ГПСЧ +rand() % 150 приведены на рис. 7.
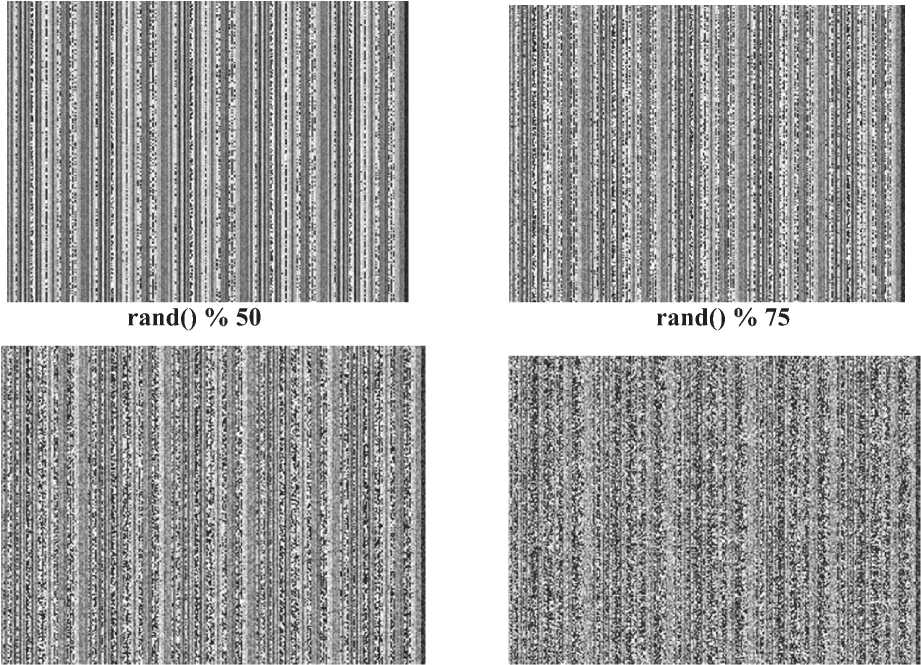
rand() %100 rand() % 150
Рис. 6. Изображения программно сформированных 3D изображений исследуемой поверхности с разной степенью зашумления ГПСЧ
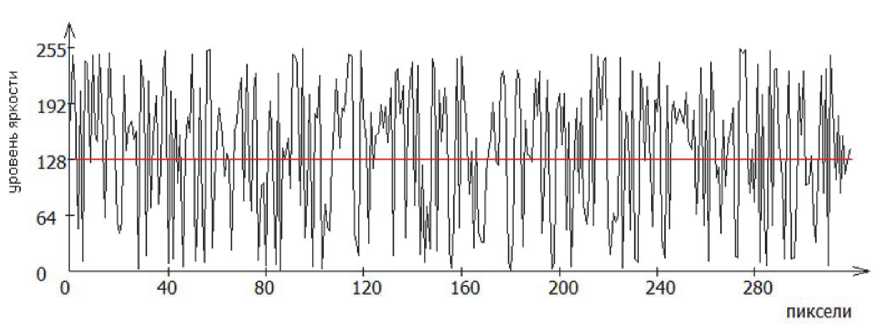
для строки №50, с шагом 9-10 пк
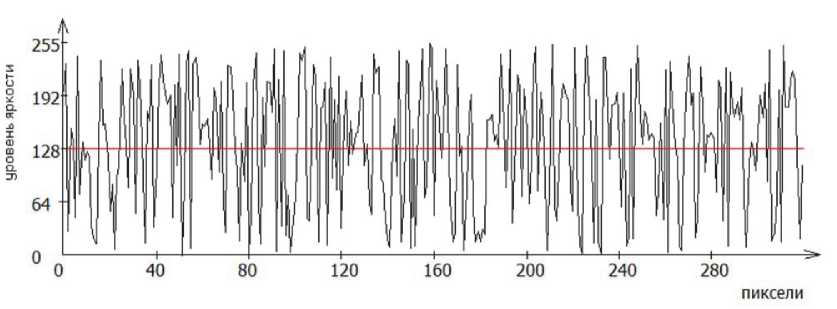
для строки №120 с шагом 7-8 пк
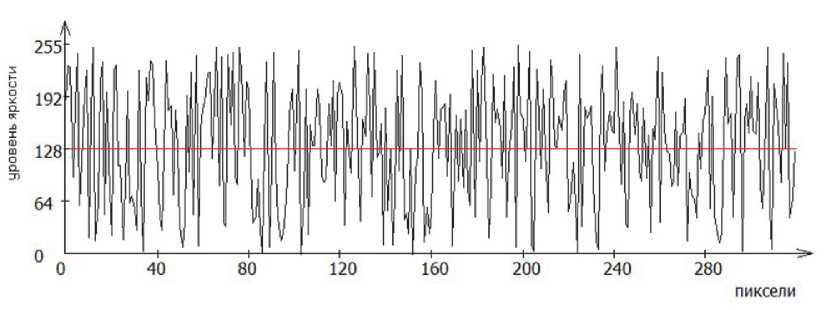
для строки №200 с шагом 6-7пк
Рис. 7. Графики видеосигналов для разных строк зашумлённого изображения
Как видно из приведенных графиков, видеосигналы для разных строк существенно отличаются друг от друга, что более реально отражает структуру реального микрорельефа. Таким образом, рассмотренный программный метод построения изображений позволяет получить цифровую модель структуры исследуемой поверхности для дальнейших вычислений её характеристик в соответствии с новым ГОСТ Р ИСО 25178-2— 2014 не прибегая к использованию сложной и дорогостоящей оптико-электронной аппаратуре. Кроме того, предложенный метод позволяет и прогнозировать качество исполнения технологической операции формирования структуры микрорельефа через процент зашумления изображения, то тесть оценивать влияние случайной компоненты в формировании микрорельефа.
Список литературы Построение цифрового изображения структуры поверхности по профиллограмме для определения её характеристик в соответствии с ГОСТ Р ИСО 25178-2- 2014
- Суслов, А.Г. Качество поверхностного слоя деталей машин / А.Г. Суслов. – М.: Машиностроение, 2000. – 320 с.
- Клевцов, Г.В. Влияние поверхностной обработки на микрорельеф и структурные изменения материала в поверхностном слое / Г.В. Клевцов, О.А. Фролов, Н.А. Клевцова // Фундаментальные исследования. – 2005. – № 4. – С. 71-73.
- Приходько, В.М. Формирование эксплуатационных свойств деталей машин ультразвуковыми методами: монография / В.М. Приходько, И.А. Меделяев, Д.С. Фатюхин. – М.: МАДИ, 2015. – 264 с.
- Абрамов, А.Д. Оценка параметров микрорельефа поверхностей деталей машин на основе квазиоптимальных корреляционных алгоритмов / А.Д. Абрамов, Н.В. Носов // Вестник компьютерных и информационных технологий. – 2016. – № 9. – С19-25.
- Abramov A.D., Grishin R.G., Nosov N.V. Journal of Physics: The IV International Conference on Information Technology and Nanotechnology IOP Conf. Series: 2018. Volume 1096, conference 1. С. 168-175.
- Смирнов, А.В. Обход препятствий техническими средствами с использованием стереозрения / А.В. Смирнов, А.Ю. Беззубцев // Программные системы: Теория и приложения. – 2016. – № 4(31), – С. 331-346.
- ГОСТ 25502-82 Объективы. Метод определения фотографической разрешающей способности. Распространяется на объективы различного назначения и устанавливает метод определения фотографической разрешающей способности. Настоящий стандарт не распространяется на аэрообъективы и объективы специального назначения.
- Миланич, А.И. Предельное разрешение в оптике / А.И. Миланич, А.А. Баранов // Труды МФТИ. – 2012. – Т. 4. – № 2. – С. 117- 181.
- Азарова, В.В. Интерферометрический метод контроля прецизионных поверхностей и лазерных зеркал / В.В. Азарова, И.В. Чертович, Т.В. Цветкова // Тр. 1-й Всерос. школы-семинара. – М.: МИЭМ, 2010. – С. 209.
- Миланич А.И. Монохромный микроскоп сверхвысокого разрешения // Патент РФ № 2441291 от 27.01.2012.
- Либенсон, М.Н. Преодоление дифракционного предела в оптике / М.Н. Либенсон // Соросовский образовательный журнал. 2000. – Т. 6, – № 3. – С. 99-104.
- Кэлер, А. Изучаем OpenCV 3. Разработка программ компьютерного зрения на C++ с применением библиотеки OpenCV / А. Кэлер, Г. Брэдски. – М.: ДМК, 2017. – 826 с.
- Шилдт, Герберт. Полный справочник по C++, 4-е издание. – Пер. с англ. /, Герберт Шилдт. – М.: Издательский дом “Вильямс”, 2006. – 800 с.