Повышение эффективности процесса электролитического хромирования
Автор: Груба Оксана Николаевна, Векессер Наталья Александровна
Журнал: Вестник Южно-Уральского государственного университета. Серия: Химия @vestnik-susu-chemistry
Рубрика: Физическая химия
Статья в выпуске: 1 т.14, 2022 года.
Бесплатный доступ
Проблема повышения надежности и долговечности машин, механизмов и приборов - общая для всех областей техники. Эта проблема может быть решена нанесением износостойких покрытий и сплавов на основе хрома. Метод электрохимического хромирования обладает рядом существенных недостатков: низкий выход по току хрома; самая низкая среди гальванических процессов рассеивающая способность; высокая энергоемкость; наличие высоких внутренних напряжений хромовых покрытий; наводороживание осадков хрома и сплава основы. Поэтому в настоящее время проводится большое количество исследований, направленных интенсификацию процессов хромирования. Данная работа направлена на изучение возможностей оптимизации процесса хромирования путем изменения состава электролита. Проведена классификация используемых в настоящее время электролитов хромирования по следующим параметрам: состав электролита, условия проведения процесса, катодный выход по току и качество, получаемых покрытий. На основании проведенных авторами экспериментальных исследований показана возможность интенсификации процесса электролитического хромирования из водных растворов за счет изменения состава электролита. Изучено влияние ряда анионов ( SO42- , SiF62- , Cl- , F- , NH2SO3- , PO43- , IO3- , I2O74- ) на качество осадков и выход по току. Предложены способы усовершенствования наиболее популярных универсальных электролитов.
Электрохимическое хромирование, хромовый ангидрид, активный анион, универсальный электролит, сверхсульфатный электролит, тетрахроматный электролит
Короткий адрес: https://sciup.org/147236617
IDR: 147236617 | DOI: 10.14529/chem220113
Текст научной статьи Повышение эффективности процесса электролитического хромирования
Процесс электролитического хромирования широко применяется для повышения износостойкости трущихся деталей, защиты их от коррозии способом защитно-декоративной отделки. Над его совершенствованием ведется постоянная работа. Появляются более эффективные электролиты и режимы работы, разрабатываются методы повышения механических свойств хромированных деталей, в результате чего расширяется область применения хромирования.
В настоящее время исследования по электрохимическому хромированию ведутся в трех направлениях: изучение возможностей интенсификации процесса хромирования, исследование механических свойств и эксплуатационных качеств хромовых покрытий, механизация и автоматизация процесса хромирования.
Данная работа направлена на изучение возможностей оптимизации процесса хромирования путем изменения состава электролита.
Характерная особенность электрохимически осажденного хрома - зависимость его свойств от условий электроосаждения. В зависимости от условий проведения электролиза (температура электролита и плотность тока) можно получить осадки хрома, различные по своим физическим свойствам, главным образом по твердости и отражательной способности [1–3]. Характер и количество трещин в хромовом осадке также можно регулировать режимом электролиза.
Различают три вида электрохимических осадков хрома: молочный, блестящий и матовый. У молочного осадка наименьшая твердость, малая пористость и наибольшая пластичность. В тонких слоях сетки трещин не появляется, осадок хорошо полируется и может быть доведен до зеркального блеска. Блестящий хром - хрупкий, имеет высокую твердость и износостойкость. Матовые покрытия не имеют практического значения в силу низких физико-химических свойств.
Положение границ областей хромовых осадков различного типа определяется, главным образом, концентрацией электролита [1, 2].
Литературный обзор
Подбор условий проведения хромирования усложняется тем, что области получения наиболее твердых и наиболее износостойких покрытий располагаются на диаграмме «плотность тока – температура электролита» параллельно, т. е. не совпадают.
Для осаждения твердых износостойких покрытий значительной толщины предложен [4] так называемый сверхсульфатный электролит хромирования, обладающий высокой рассеивающей способностью и стабильностью. Содержание серной кислоты по отношению к хромовому ангидриду устанавливают в пределах 12–25 % при начальной концентрации трехвалентного хрома 20– 40 г/л. Выход по току составляет 20–25 %. Осадки имеют низкие внутренние напряжения, микротвердость их достигает 1200–1600 кг/см2.
С целью интенсификации хромирования предложено большое количество электролитов на основе растворов хрома (VI), в которые вводятся различные неорганические добавки: кремнесодержащие соединения [5], цинк, кадмий, магний, алюминий. Это позволяет повысить выход по току до 17–20 %.
Имеется обширный класс органических веществ, которые можно использовать в качестве добавок для интенсификации процесса хромирования. В [6, 7] были предложены и исследованы электролиты хромирования на основе растворов хромовой кислоты с добавками галловой кислоты и метиленового голубого следующих составов (г/л):
-
1) хромовый ангидрид 200–50,
серная кислота2–3, галловая кислота2–3;
-
2) хромовый ангидрид 200–250,
серная кислота2–3, метиленовый голубой1–6.
Температура осаждения для первого варианта 45–55 °С, для второго – 60–70 °С.
Указанные добавки значительно расширяют верхний предел допустимых плотностей тока получения качественных хромовых осадков, введение их в электролит хромирования приводит к уменьшению внутренних напряжений на 25–30 %.
Исследование микроструктуры показало, что увеличение содержания галловой кислоты от 0,5 до 3 г/л способствует выравниванию поверхности осадка, при этом практически исчезает сетка трещин и питтинг. Аналогичный эффект наблюдается при введении от 1 до 5 г/л метиленового голубого. Осадки получаются более гладкими и блестящими по сравнению с осадками, полученными без добавок.
По мнению автора [8], все перечисленные свойства осадков связаны со специфическим воздействием добавок на структуру и свойства прикатодной пленки электролита, образующейся в ходе электролиза. Добавки вызывают ее стабилизацию и тем самым способствуют увеличению выхода хрома по току. Так, например, в присутствии галловой кислоты (2 г/л) при температуре электролита 50 °С выход по току увеличивается на 25 %, а в присутствии метиленового голубого (2–5 г/л) при температуре электролита 70 °С выход по току увеличивается на 15 % по сравнению с выходом по току хрома из стандартного электролита.
Было изучено влияние органической добавки на физико-механические свойства осадков хрома и на проведение процесса электролиза [9]. В качестве базового электролита был использован стандартный электролит хромирования следующего состава (г/л): хромовый ангидрид 250, серная кислота 2,5, добавка 2–6.
Введение добавки позволило получать качественные осадки при температуре 15–25 °С в диапазоне плотностей тока от 50 до 1000 А/дм2. Выход по току хрома увеличивается с возрастанием плотности тока в диапазоне от 100 до 800 A/дм2 от 27 до 50 %. При этом ниже 100 A/дм2 получаются матовые осадки, выше – блестящие. Сетка трещин на поверхности с увеличением плотности тока уменьшается и выше 400 A/дм2 практически исчезает. Осадки приобретают волокнистую структуру с высокой степенью измельчения структуры.
Существует целый ряд соединений, использование которых позволяет значительно интенсифицировать процесс хромирования, получать качественные осадки хрома с требуемыми физикомеханическими свойствами
Большая чувствительность хромовых электролитов к содержанию в них сульфат-ионов, трудность их контроля и поддерживания на постоянном уровне послужили основанием к созданию электролитов с автоматически регулируемой концентрацией этих ионов. Саморегулирующиеся электролиты хромирования [10] отличаются более высоким выходом по току, большей кроющей способностью и агрессивностью вследствие действия фторид-иона, входящего в состав электролита. Эти электролиты не требуют частого корректирования, позволяют применять высокие плотности тока и дают блестящие осадки при больших толщинах. Постоянное соотношение между анионами хромовой кислоты и сульфат-ионами поддерживается с помощью малорастворимых солей сернокислого стронция или бария и кремнефтористого кальция, взятых в избыточном количестве [1]. Авторами [9] предложен следующий состав саморегулирующегося электролита хромирования (г/л):
хромовый ангидрид 400–420;
углекислый кальций 67–75;
сернокислый кобальт 15–20.
Процесс ведут при плотности тока 150–200 А/дм2 и температуре 18–23 °С. Это обеспечивает повышение производительности процесса и качества осадков хрома. Выход металла по току при этом составляет 40±2 %, а микротвердость покрытий во всем интервале плотностей тока достигает 900–1250 кг/см2 с одновременным повышением их износостойкости.
В области высоких температур (выше 60 °С) в саморегулирующихся электролитах возможно получение хромовых покрытий, имеющих сатинообразный вид без трещин. Такие покрытия легко полируются до зеркального блеска, имеют высокие защитные свойства и износоустойчивость.
Известны саморегулирующийся электролит хромирования, в состав которого входят (г/л):
хромовый ангидрид 150–350;
сернокислый стронций 6;
окись хрома 30.
В присутствии избытка не растворяющихся твердых окиси хрома и сульфата стронция кислотность раствора и содержание в нем сульфат-ионов будет находиться на заданном уровне за счет автоматического растворения соответствующих количеств этих соединений в момент, когда их концентрация в растворе упадет ниже требующейся для обеспечения насыщения последнего. Температура ванны при электролизе 17–23 °С, плотности тока 10–100 А/дм2, выход хрома по току при работе на указанном режиме достигает 33–43 %.
Определенный интерес представляют электролиты тетрахроматного типа, в которых часть хромовой кислоты нейтрализуется щелочью или солями, так что основным компонентом этих электролитов является тетрахромат-ион. Типовой состав такой ванны следующий (г/л):
хромовый ангидрид 300;
гидроксид натрия 58–60;
серная кислота 0,6–0,75;
этиловый спирт 1 мл/л.
Процесс электролиза ведут при катодной плотности тока 20–80 A/дм2 и температуре электролита 16–24 °С. Ведение процесса при низкой температуре электролита и высокой плотности тока способствует более высокому выходу хрома по току (30–35 %). Осадки хрома, полученные из таких электролитов, по сравнению с осадками из других хромовых ванн имеют пониженную твердость (350–400 кг/см2), относительно высокую пластичность [11], меньшую пористость. Внешний вид осадков матовый, но они сравнительно легко полируются. Кроме того, тетрахро-матные электролиты отличаются высокой кроющей способностью.
Указанные отличительные черты тетрахроматного электролита позволяют его рекомендовать для нанесения защитно-декоративных покрытий небольшой толщины.
Использование тетрахроматного электролита для нанесения толстослойных покрытий при износостойком хромировании нецелесообразно, т.к. покрытия имеют низкую износостойкость и высокие внутренние напряжения в толстых слоях [10]. Так, некоторые авторы отмечают, что в покрытиях относительно большой толщины (свыше 50 мкм) наблюдаются разрывы [13].
Твердость и ковкость можно значительно увеличить введением в электролит оксид магния или вольфрамата натрия [14]. Эти добавки не вступают в реакцию с металлом катода, но, вероятно, взаимодействуют с катодной пленкой во время отложения осадка. Выход по току возрастает до 35–40 %. Кроме того, в таком электролите меньше проявляется зависимость выхода по току от температуры.
Из-за разложения тетрахроматов при повышении температуры (выше 25 °С) и снижения концентрации серной кислоты происходит нарушение стабильности электролитов. По аналогии с саморегулирующимися электролитами, в них вместо серной кислоты вводили сульфат стронция или сульфат и карбонат кальция (г/л):
хромовый ангидрид350;
стронция сульфат50;
кальций сульфат6.
Температура 16–20 °С; катодная плотность тока 10–50 А/дм2; выход по току 25–35 %.
Избыток малорастворимого сульфата кальция позволил поддерживать концентрацию сульфат-ионов в электролите постоянной, составляющей 0,5–1,5 % от содержания анионов хромовой кислоты. Осадки из такого электролита малопористы, легко полируются, имеют высокую адгезию и коррозионную стойкость.
Для получения блестящих хромовых покрытий на стальных, медных и латунных изделиях предложен [3] тетрахроматный электролит, содержащий карбонат натрия и добавки циануровой кислоты (г/л):
хромовый ангидрид300;
серная кислота0,8;
натрий карбонат280;
циануровая кислота1.
Температура 25–30 °С; катодная плотность тока 5–10 А/дм2; выход по току 25–30 %.
Известен также саморегулирующийся тетрахроматный электролит с добавкой сернокислого кобальта (г/л) [10, 15]:
хромовый ангидрид 380–420;
карбонат кальция 60–75;
сульфат кобальта 18–20.
Авторы отмечают высокую производительность электролита: катодная плотность тока i к = 100–300 A/дм2, выход по току хрома 35–40 %, скорость осаждения 0,18–0,50 мм/час.
В тетрахроматные электролиты целесообразно вводить фторид аммония для расширения интервала допустимых температур и получения блестящих покрытий в широком диапазоне плотностей тока [3]. Состав электролита, г/л:
хромовый ангидрид 300–350;
трехвалентный хром 5–6;
серная кислота 0,7–2,3;
фторид аммония 1–12.
Режим электролиза: температура 18–40 °С, плотность тока 3–55 А/дм2. Максимально возможный выход по току (38–40 %) достигается в электролите с содержанием серной кислоты на верхнем уровне концентрации при температуре 20 °С и плотности тока 30–58А/дм2.
Покрытия с зеркальным блеском получаются при содержании аммония 5–6 г/л, температуре 20–37 °С и плотности тока 3–20 А/дм2. Электролит обладает высокой рассеивающей способностью и рекомендуется для хромирования медных и омедненных деталей с подслоем никеля, прямого хромирования деталей из алюминия, его сплавов и цинкового литья.
При практическом использовании тетрахроматных электролитов возникают трудности, связанные с охлаждением электролита; несравненно легче поддерживать температуру 50–55 °С, чем 20–22 °С при высокой плотности тока. Серьезным недостатком является трудность доведения до блеска матовых хромовых покрытий, получаемых из тетрахроматных электролитов.
Установлена практическая возможность электроосаждения хрома из растворов перхлората хрома (III) в присутствии карбамида и карбоната аммония [1, 3]. Состав электролита, г/л:
перхлорат хрома (III) 300–350;
карбамид 100–120;
карбонат аммония 30–35.
Из электролита (pH = 1) можно осадить блестящие осадки хрома толщиной до 3 мм в течение 15 минут. При исследовании механизма электроосаждения хрома из растворов, содержащих соединения хрома (III) с различными анионами: хлорат-, нитрат-, хлорид; сульфит-, сульфат-, формиат-, ацетат-, оксалат- и др. Установлено, что только сульфат-анион способствует быстрому протеканию электрохимических реакций катодного выделения металлического хрома. По-видимому, процесс электровосстановления хрома зависит не от прочности комплексных соединений, а от состояния поверхности катода, определяемого химической природой анионов, входящих в состав комплекса.
Электролиты хромирования на основе трехвалентных соединений хрома обладают рядом положительных свойств: более высокий в сравнении с растворами хрома (VI) электрохимический эквивалент, нетоксичность растворов, низкие рабочие температуры [16, 17].Однако водные растворы электролитов хромирования обладают низкой буферной емкостью и вследствие этого склонны к образованию гидроокисных соединений на катоде за счет подщелачивания прикатод-ного слоя при совместном с хромом выделении водорода, что снижает качество осадков. Рядом авторов [6, 7] был предложен электролит на смешанном водно-органическом растворителе. Осаждение хрома производилось из электролита, содержащего хлориды хрома, алюминия и борную кислоту. Растворителем служила смесь диметилформамида (ДМФА) и воды в объемном соотношении 3:7.
Для устранения местных повреждений защитно-декоративных покрытий, восстановления и повышения износостойких отдельных поверхностей крупногабаритных деталей целесообразно применять контактное хромирование. В настоящее время разработан неагрессивный электролит и режим контактного хромирования (г/л):
уксуснокислый хром 260–280;
муравьинокислый аммоний 375–400;
виннокислый калий-натрий 13–17.
Режим хромирования: pH 5,5–5,7; катодная плотность тока 270–300A/дм2, температура поступающего электролита 45 °С, расход электролита 0,28 л/мин. При этих условиях выход хрома по току достигает 25 %, микротвердость покрытий 930–1000 HV.
Известен электролит хромирования для нанесения покрытий натиранием [18], содержащий (г/л):
хромовый ангидрид 40–50;
муравьиная кислота (85%-ный раствор) 250–300;
аммиак (25%-ный раствор) 200–500;
бихромат калия 50–60.
Процесс ведут при плотности тока 150–400 A/дм2 и скорости перемещения анода относительно катода 3–5 м/мин.
Обсуждение результатов
Электрохимическое осаждение хрома существенно отличается от других гальванических процессов. Во время хромирования на катоде одновременно протекают процессы осаждения хрома; выделения водорода; восстановления шестивалентного хрома до трехвалентного; образования на поверхности катода тонкой пленки, состоящей из продуктов восстановления хромовой кислоты и активного аниона [3, 19, 20].
Хромирование производится из электролитов, содержащих не соли осаждаемых металлов, а смеси хромовых кислот ( H 2 Cr 2 O 7 и H 2 CrO 4). При этом установлено, что электролит должен содержать определенное количество активных анионов, чаще всего S02 , F", SiF^ , без которых хром не выделяется из растворов хромовой кислоты (рис. 1). При этом сами ионы не восстанавливаются и хорошо адсорбируются.
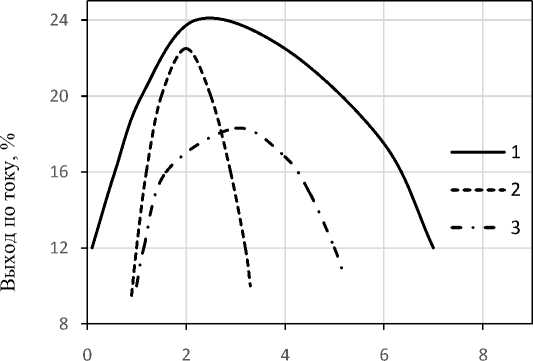
Относительная концентрация активного иона C a , %
Рис. 1. Влияние концентрации активного аниона C a на выход по току: 1 - SiFV, , 2 - F , 3 - SO2 ,
В работе изучалось влияние некоторых анионов на качество осадков и выход по току при осаждении хромовых покрытий из электролитов с различной концентрацией СгО з .
Не только тип, но и концентрация активного аниона оказывает влияние на процессы, проте-
2- кающие на катоде. На рис. 2 приведена зависимость выхода по току от концентрации ионов 504 для выделения хрома и водорода и образования трехвалентного хрома.

Относительная концентрация сульфат-иона SO4 2- , %
Рис. 2. Выход по току для частных катодных процессов в зависимости от концентрации сульфат-иона SO2- (содержание СгО з - 350 г/л, к = 15 А/дм2, t = 20 °C):
1 - образование трехвалентного хрома, 2 - выделение водорода, 3 – выделение хрома
В присутствии ионов 50^ в широком диапазоне концентраций осаждались блестящие покрытия.
Ионы СГ при концентрации СгОз в растворе выше 250 г/л вызывали образование покрытий серого цвета с достаточно высоким выходом по току. При низком содержании исследованных анионов в растворе выход по току был незначительным. С повышением содержания анионов в растворе выход по току увеличивался.
Для анионов S О2 , S iF2 и молярное отношение анион / СтО з , обеспечивающее высокий выход по току, составляет 0,01-0,02, а для СтО 3 ионов F" 0,06-0,12.
Из электролитов, содержащих 250 г/л СтОз и ионы NH2S^3, блестящие хромовые покрытия осаждались при молярном отношении NH2 SO3 /СтО з =0,1.
В присутствии ионов NO3 получали неметаллический осадок черного цвета при низком выходе по току.
Неметаллический осадок коричневого цвета получали также в присутствии H 3 BO 3 и ионов РО^".
С очень низким выходом по току осаждались покрытия серого цвета из электролитов, содер-жащихионы/О3 и 12О^ .
Каталитическим действием в процессе осаждения хрома обладают анионы, которые способны значительно увеличивать электропроводность раствора электролита, например, анионы SO4 2- , F".
Был запатентован электролит хромирования [21] высокой концентрации (до 1600 г/л СтОз), в который вводятся следующие анионы (в вес. % от концентрации СтОз); СГ0,3-5, F" 0,3-10 и (или) SO2 0,3-2. Добавляемые анионы выбираются из следующих соединений KCl, NaCl, NaF, MgCl 2 , CrCl 3 , H 2 SO 4 при температуре 20–60 °С, и катодной плотности тока i к = 10–270 A/дм2. Из электролита были получены покрытия хорошего качества с высоким выходом по току.
Наибольшее распространение получили электролиты на основе SO2" хромового ангидрида с добавкой серной кислоты, причем чаще всего количество серной кислоты составляет 1 % от количества хромового ангидрида – универсальные электролиты [12].
Процесс хромирования в универсальных электролитах имеет ряд недостатков: необходимость жесткого соблюдения режимных характеристик процесса электролиза из-за значительных колебаний в свойствах осадка при их изменении; низкое значение рассеивающей и кроющей способности электролитов; низкий катодный выход по току и значительное влияние на него параметров электролиза, особенно температуры; высокая чувствительность электролита к примесям ионов других металлов; высокая агрессивность раствора.
Усовершенствовать процесс получения хромовых покрытий в универсальных электролитах возможно следующими способами: оптимизация режима электролиза; изменение соотношения компонентов (сверхсульфатный электролит); введение ряда добавок; применение новых составов электролитов (тетрахроматные электролиты, на основе трехвалентных ионов хрома и др.).
Другая особенность процесса хромирования – тесная взаимосвязь температуры и плотности тока [12, 15, 21, 22]. Понижение температуры электролита увеличивает выход по току, но при температуре ниже 40 °С получаются осадки низкого качества. Поддерживать температуру 55– 60 °С при средних плотностях тока (около 50 А/дм2) сложно, так как электролит необходимо подогревать. Хромирование при такой же плотности тока (50 А/дм2) при температуре электролита ниже 30 °С, напротив, требует охлаждения электролита, так как происходит разогрев электролита джоулевым теплом. Как нам представляется, хромирование при температуре 40 °С будет экономически целесообразным, что подтверждается тепловым расчетом, так как разогрев электролита джоулевым теплом компенсируется рассеиванием тепла в окружающую среду. Проведенные исследования при температуре электролита 38–40 °С, плотности тока 50 А/дм2 и давлении абразивного инструмента 1 кг/см2 позволили получить выход по току 30 % (рис. 3). При этом получаются покрытия хорошего качества и не требуется ни дополнительного разогрева, ни дополнительного охлаждения.
В последнее время большое внимание исследователей и практиков привлекает процесс гальванического осаждения металлов с одновременной абразивной обработкой, известный под названием гальванохонингования или гальваномеханической обработки [3, 5, 11–18, 23, 24]. Сущность способа состоит в том, что во время электролитического осаждения металла происходит непрерывное механическое активирование покрываемой поверхности. В зоне контакта абразив временно удаляет с покрываемой поверхности диффузионный слой, водородную пленку, а также различные примеси и загрязнения, тормозящие реакцию. При отводе зерен абразива контакт электролита с электродом восстанавливается, и снова происходит осаждение. Таким образом, многократный разрыв катодной пленки в значительной мере снимает диффузионные ограничения и дает возможность применять большую плотность тока, а, следовательно, получать и высокие скорости осаждения [13–15]. Например, было установлено, что при гальваномеханическом способе хромирования становится возможным нанесение качественных покрытий толщиной 0,7– 1,5 мм. При этом выход хрома по току увеличивается до 55–65 % при плотности тока 300–650 А/дм2, т. е. наблюдается повышение производительности процесса за счет увеличения допустимых плотностей тока [5, 11–14, 21, 25].
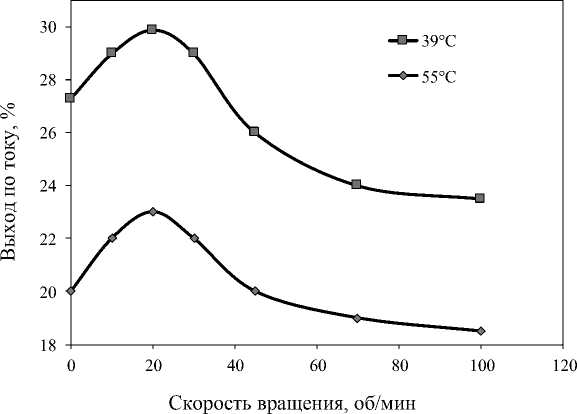
Рис. 3. Выход по току при температуре 39 и 55 °С при давлении абразивного инструмента 1 кг/см2
Заключение
-
1. Обобщена информация по электролитам хромирования, используемым в настоящее время. Выбор типа электролита (универсальный, саморегулирующийся, тетрахроматный, сверхсульфатный и др.), условий проведения процесса (катодная плотность тока, температура электролита) определяются требованиями к качеству получаемых покрытий (пористость, твердость, коррозионная и износостостойкость и т. п.)
-
2. Экспериментально показана возможность интенсификации процесса хромирования путем изменения состава электролита. Изучено влияние ряда активных анионов (S02 , SiF^ , Cl", F", NH2S03 , PO^ , /03, /204 ) на качество осадков и выход по току. Определены оптимальные значения относительного содержания активных ионов для получения высоких выходов по току (45 – 50 %) при сохранении качества получаемого покрытия.
-
3. Предложены способы усовершенствования универсальных электролитов: оптимизация режима проведения процесса электролиза (катодная плотность тока, температура электролита), применение новых составов электролитов (тетрахроматные электролиты, на основе трехвалентных ионов хрома и др.), введение добавок (оксид магния, вольфрамат натрия, фторид аммония и др.)
Список литературы Повышение эффективности процесса электролитического хромирования
- Шлугер, М.А. Гальванические покрытия в машиностроении: справочник. В 2 т. / М.А. Шлугер. – М.: Машиностроение, 1985. – Т. 1. – 240 с.
- Богорад, Л.Я. Хромирование / Л.Я. Богорад. – Л.: Машиностроение, 1984. – 97 с.
- Ажогин, Ф.Ф. Гальванотехника: справ. изд. / Ф.Ф. Ажогин, М.А. Беленький, И.Е. Галь и др. – М.: Металлургия, 1987. – 736 с.
- Шлугер, М.А. Гальванические покрытия в машиностроении: справочник. В 2 т. / М.А. Шлугер. – М.: Машиностроение, 1985 – Т. 2. – 248 с.
- Покровская, Г.А. Теория и практика хромирования / Г.А. Покровская. – К.: КРДЭНТП, 1974. – 103 с.
- Фомичев, В.Т. Электроосаждение хрома из электролитов, содержащих органические добавки: автореферат дис. … д-ра техн наук / В.Т. Фомичев. – Новочеркасск: НГТУ, 1994. – 34 c.
- Фомичев, В.Т. Электроосажаение хрома из электролитов с органическими добавками // Материалы Всесоюзной науч.-техн. конференции «Технологии нанесения противокоррозионных покрытий» / В.Т. Фомичев, Е.В. Москвичева, A.M. Озеров. – Челябинск, 1985. – С. 36–37.
- Дасоян, М.А. Оборудование цехов электрохимических покрытий / М.А. Дасоян, И.Я. Пальмская. – Л.: Машиностроение, 1979. – 287 с.
- А. с. СССР № 336346 С25Д 704, 1972.
- Молчанов, В.Ф. Хромирование в саморегулирующихся электролитах / В.Ф. Молчанов. – К.: Техника, 1972. – 82 с.
- Макарова, Н.А. Металлопокрытия в автомобилестроении / Н.А. Макарова, М.А. Лебедева, В.Н. Набокова. – М.: Машиностроение, 1977. – 294 с.
- Яшпольский, А.М. Краткий справочник гальванотехника / А.М. Яшпольский, В.А.Ильин. – Л.: Машиностроение, 1981. – 269 с.
- Черкез, М.Б. Хромирование/ М.Б. Черкез, Л.Я. Богорад. – Л.: Машиностроение, 1978. – 100 с.
- Вейнер, Р. Гальваническое хромирование / Р. Вейнер; пер. с нем. И.Д. Груева и Е.В. Пла-скеева. – М.: Машиностроение, 1964. – 152 с.
- Справочник по электрохимии / под ред. А.М. Сухотина. – Л.: Химия, 1981. – 488 с.
- Виноградов, С.С. Экологически безопасное гальваническое производство / С.С. Виногра-дов; под ред. В.Н. Кудрявцева. – М.: Глобус, 2002. – 352 с.
- Автоматическая гальваническая установка для обработки цилиндрических стержней: пат. RU 2040594 С1, МПК C25F 7/00 (1995.01) / А.Г. Устюгов. Патентообладатель А.Г. Устюгов (RU). – Заявка: 5003780/26; заявл. 01.07.1991, опубл. 25.07.1995. – 7 с.
- Окулов, В.В. Экологические, технологические и экономические аспекты замены шести-валентных растворов хроматирования (пассивирования) / В.В. Окулов // Гальванотехника и обра-ботка поверхности – 2005. – Т. 13, № 2. – C. 35–41.
- Батищев, А.Н. Пособие гальваника-ремонтника / А.Н. Батищев. – М.: Колос, 1980. – 238 с.
- Лайнер, В.И. Защитные покрытия металлов / В.И. Лайнер. – М.: Металлургия, 1974. – 558 с.
- Солодкова, Л.Н. Электролитическое хромирование / Л.Н. Солодкова, В.Н. Кудрявцев. – М.: Глобус, 2007. – 191 с.
- Юдин, В.М. Нанесение гальванических покрытий при большой плотности тока / В.М. Юдин, Н.Н. Вихарев // Техника и оборудование для села. – 2011. – № 5. – С. 22–23.
- Солнцев, С.С. Защитные покрытия металлов при нагреве: справочное пособие / С.С. Солнцев. – Изд. 2-е, доп. – Либроком, 2009. – 248 с.
- Кондратов, Л.П. Технология материалов и покрытий / Л.П. Кондратов, Н.Н. Божко. – М.: МГУП, 2008. – 226 с.
- Вансовская, К.М. Гальванические покрытия / К.М. Вансовская. – Л.: Машиностроение, 1984. – 119 с.