Повышение эффективности рабочего процесса молотковых дробилок закрытого типа
Автор: Коношин И.В., Звеков А.В.
Журнал: Агротехника и энергообеспечение @agrotech-orel
Рубрика: Научно-техническое обеспечение процессов и производств в сельском хозяйстве
Статья в выпуске: 1 (1), 2014 года.
Бесплатный доступ
В статье указаны основные недостатки молотковых дробилок закрытого типа с цилиндрическим исполнением решета, причины этих недостатков и мероприятия по их устранению. Представлены конструктивно-технологические схемы дробильных устройств молотковых дробилок с сегментным исполнением решета, приведена сравнительная оценка эффективности применения сегментного решета по сравнению с цилиндрическим.
Концентрированные корма, модуль помола, дерть, помольная характеристика, продуктово-воздушный слой, молотковая дробилка закрытого типа, дробильная камера, дробильное устройство, цилиндрическое решето, сегментное решето, подача материала, затраты энергии на измельчение
Короткий адрес: https://sciup.org/14769892
IDR: 14769892
Текст научной статьи Повышение эффективности рабочего процесса молотковых дробилок закрытого типа
Значительную роль в создании продовольственной безопасности играет животноводческая отрасль. Уровень производства продукции животноводства зависит от многих факторов, и прежде всего от создания прочной кормовой базы в полной мере отвечающей потребительским требованиям, что в свою очередь требует совершенствования средств механизации процесса производства и переработки кормов. Таким образом, повышение уровня механизации производственных процессов и качества готовых кормов является важной задачей в животноводстве.
В основе большинства технологий кормопроизводства лежит такая операция как измельчение компонентов кормовой смеси. Кормовая смесь, соответствующая зоотехническим требованиям и имеющая определенный гранулометрический состав, обладает лучшей усвояемостью и позволяет рационально использовать кормовое сырье, в том числе и концентрированные корма.
В состав концентрированных и комбинированных кормов входит в основном фуражное зерно злаковых культур. Вопрос эффективного измельчения зерна, с точки зрения качества продукта, и энергозатрат на его производство, до настоящего времени остается актуальным. Поэтому основным направлением в совершенствовании рабочего процесса измельчающих машин является создание таких их конструктивно-технологических схем, которые позволяли бы достичь, высоких значений производительности, однородности гранулометрического состава зерновой дерти при возможно низких энергозатратах.
В настоящее время в комбикормовой промышленности и на животноводческих фермах при производстве муки основное применение нашли измельчители ударного действия – молотковые дробилки. Молотковые дробилки, предназначенные для измельчения зерна, имеют большое разнообразие конструкций. Достаточно широкое распространение получили дробилки, рабочий процесс в которых организован по закрытому типу, что обусловлено простотой их конструкции, динамичностью рабочих режимов, меньшей стоимостью, возможностью организации пневматической загрузки и выгрузки материала и т. д. [1, 2]. Зернодробилки закрытого типа, в основном, являются решётными – решето и деки (при наличии) полностью охватывают ротор, материал удаляется по мере измельчения до заданного размера через отверстия решета.
Общими недостатками дробилок закрытого типа являются относительно низкие показатели качества готового продукта, производительности и большие затраты энергии на измельчение. Причины указанных недостатков по нашему мнению и мнению многих авторов заложены в конструктивном несовершенстве машин.
При использовании решета правильной цилиндрической формы в молотковых дробилках происходит послойное разделение измельчаемого материала в дробильной камере. Крупные частицы при круговом движении располагаются в основном на рабочей поверхности решета, а мелкие вытесняются в зону воздействия молотков. Располагаясь в зазоре между концами молотков и рабочей поверхностью решета, крупные частицы препятствуют своевременному выходу готового продукта из камеры измельчения, при этом сами не попадают под удары молотков. При этом в зарешетное пространство выходят и недоизмельченные и переизмельченные частицы зерна, причем стремление избавиться от переизмельчения ведет к появлению еще большего количества недоизмельченных частиц и наоборот.
Данные положения позволяют утверждать, что одним из условий повышения эффективности работы дробилок закрытого типа является изменение поведения продуктово-воздушного слоя внутри рабочей камеры. С целью выполнения данного условия определена задача научного исследования - разработать или усовершенствовать конструктивно-технологическую схему дробилки за счет изменения формы решета, и тем самым повлиять на поведение продуктово-воздушного слоя внутри рабочей камеры.
Для решения данной задачи на рисунке 1 предложены схемы молотковых дробилок с использованием сегментного решета [3], что позволит повлиять на распределение крупных и мелких частиц продукта внутри зоны измельчения и облегчить выход готового продукта. Согласно схемам, дробильные устройства молотковых дробилок могут включать в себя следующие основные части: раму 1, на которой установлена дробильная камера 2 , сегментное решето 3 , ротор 5 с шарнирно подвешенными молотками 4 , корпус 6, загрузочный бункер 7 , заслонку 8 , загрузочную горловину 9 , выгрузную горловину 10 , вентилятор 11 и всасывающий трубопровод 12 .
Проверка выдвинутой гипотезы эффективности использования предлагаемого сегментного решета в сравнении с цилиндрическим, применяемым в серийно выпускаемых зернодробилках производилась на изготовленной экспериментальной установке по схеме на рисунке 1, а .
Сравнительная оценка рабочего процесса молотковой дробилки с цилиндрическим исполнением решета и сегментным решетом проводилась при следующих показателях и значениях конструктивно-режимных параметров измельчителя:
-
1. Измельчаемый материал – зерно ячменя, как наиболее прочный и трудноразрушаемый материала по сравнению с другими зерновыми [4 и др.] влажностью до 14 %.
-
2. В экспериментах изменяли подачу материала Q , кг/ч, как показатель, определяющий пропускную способность дробилки.
б
-
3. Качество готового продукта оценивали по модулю помола, как альтернативу степени измельчения.
-
4. Значение окружной скорости молотков vМ приняли равным 75 м/с.
-
5. Значение максимального радиального зазора S max приняли равным 15 мм, как среднего из диапазона зазоров между концами молотков и ситовой поверхностью, часто исследуемых в научных работах.
-
6. Эксперименты проводили с решетами, диаметр отверстий которых составлял d ОТВ. – 3,6 мм; 5 мм и 7 мм, при диаметре ротора
а
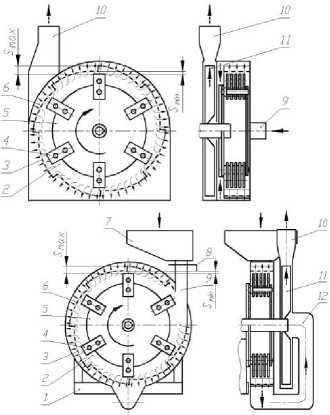
г
в а – загрузка исходного материала радиальная самотеком, выгрузка готового продукта самотеком; б – загрузка исходного материала тангенциальная самотеком; в – пневмозагрузка-выгрузка материала; г – загрузка исходного материала тангенциальная самотеком, выгрузка готового продукта пневматическая; 1 – рама; 2 – дробильная камера; 3 – сегментное решето; 4 – молотки; 5 – ротор; 6 – корпус; 7 –загрузочный бункер; 8 – заслонка; 9 – загрузочная горловина; 10 – выгрузная горловина; 11 – вентилятор; 12 – всасывающий трубопровод
Рисунок 1 – Конструктивно-технологические схемы дробильных устройств молотковых дробилок с сегментным решетом
по концам молотков D6 = 0,5 м, ширине рабочей камеры L = 90 мм, количестве осей подвеса молотков J = 6 и осевой самотечной подаче материала.
В результате исследований были получены графические зависимости затрат энергии на измельчение N ИЗМ. , кВт·ч, и модуля помола М , мм, от подачи материала Q , кг/ч, (рисунки 2, 3).
Анализ графиков зависимости затрат энергии на измельчение от подачи материала позволяет выделить для решет с диаметром отверстий 7 мм (рисунок 2, а ) и 5 мм (рисунок 2, б ) две характерные точки, где работа дробилки с цилиндрическим и сегментным исполнением решет имеют одинаковые показатели:
-
- для решет с диаметром отверстий 7 мм точка 1 при Q = 1100 кг/ч и NИЗ м . = 3,28 кВт^ч; точка 2 при Q = 2235 кг/ч и NИЗ м . = 10,53 кВт^ч;
-
- для решет с диаметром отверстий 5 мм точка 1 при Q = 1100 кг/ч и NИЗм, = 7,5 кВт^ч; точка 2 при Q = 1278 кг/ч и NИЗ м. = 12,8 кВт^ч.
Указанные точки позволяют выделить на графиках три условные зоны, характеризующие эффективность работы усовершенствованной молотковой дробилки по затратам энергии:
-
- I зона - зона условно эффективной работы, т. к. затраты энергии на измельчение продукта в усовершенствованном варианте ниже, чем в базовом, это наблюдается при малой подаче материала в дробильную камеру, а следовательно заведомо неэффективном использовании машины.
-
- II зона - зона неэффективной работы, т. к. затраты энергии на измельчение продукта в усовершенствованном варианте выше, чем в базовом;
-
- III зона - зона эффективной работы, так как затраты энергии на измельчение продукта при высоких показателях производительности в усовершенствованном варианте ниже, чем в базовом.
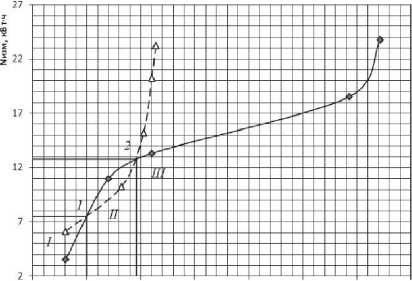
900 1100 1300 1500 1700 1900 2100 2300
—♦—сегментное решето —Д— цилиндрическое решето Q, кг/ч б а – диаметр сит 7 мм; б – диаметр сит 5 мм Рисунок 2 – Зависимость затрат энергии на измельчение NИЗМ. кВт·ч, от подачи материала Q, кг/ч
Исследования помольных характеристик готового продукта дали следующие результаты (рисунок 3).
Так для решет с диаметром отверстий 7 мм при подаче материала 2235 кг/ч (зона III (рисунок 2, а )) модуль помола составил 2,27 мм. Данная величина подачи оказалась максимально возможной и дальнейшее её увеличение приводило к остановке машины. При использовании сегментного решета устойчивая работа молотковой дробилки наблюдалась до 2350 кг/ч. при этом модуль помола составил 2,06 мм (рисунок 3, а ).
Аналогично для решет с диаметром отверстий 5 мм граничная величина подачи составила 1360 кг/ч, модуль помола 2,2 мм. При сегментном решете максимально возможная подача составила 2100 кг/ч, модуль помола составил 1,48 мм (рисунок 3, б).
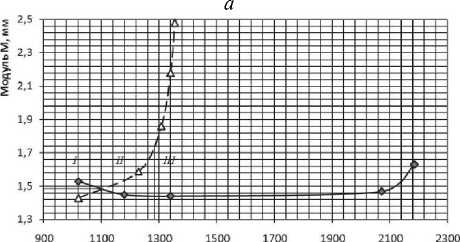
—О—сегментное решето—Д— цилиндрическое решето б
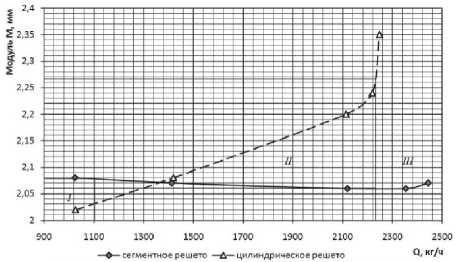
а - диаметр сит 7 мм; б - диаметр сит 5 мм Рисунок 3 - Зависимость модуля помола М , мм, от подачи материала Q , кг/ч
Следует указать, что при использовании решета с диаметром отверстий 7 мм в первом варианте помольная характеристика готового продукта при максимально возможной подаче не отвечала требованиям ГОСТ 9268-90, согласно которому для взрослого поголовья крупного рогатого скота массовая доля остатка на сите с отверстиями диаметром 3 мм допускается до 25%, так как содержание в дерти частиц более 3 мм при подаче 2235 кг/ч составляла более 25%. Дерть, полученная при использовании сегментного решета, содержала эти же частицы до 23,68%, что находится в пределах нормы. Пылевидных частиц в первом случае содержалось в среднем до 4,57%, во втором – до 3,07%.
При установке решет с диаметром отверстий 5 мм при различных величинах подачи был получен материал со следующими помольными характеристиками:
-
- в базовом варианте установки решет содержание в дерти частиц более 3 мм составила до 20%, пылевидной фракции до 14,76%, переход в завальный режим при Q1 > 1360 кг/ч;
-
- в усовершенствованном варианте установки решет содержание в дерти частиц более 3 мм составило до 7,48%, пылевидной фракции до 6,98%, переход в завальный режим при Q2 > 2150 кг/ч.
Результаты сравнительных исследований работы молотковой дробилки с циллиндрическим и сегментным исполнением решет позволили выявить следующие положительные качества усовершенствованной конструкции решета:
-
- сегментное исполнение решета с диаметром отверстий от 5 до 7 мм позволяет обеспечить более качественный выход готового продукта при высоких величинах подачи материала;
-
- при изменении подачи материала дробилка с сегментным исполнением решета имеет более плавный характер изменения энергетических показателей и показателей помольной характеристики готового продукта, что особенно важно для измельчителей с нестабилизированной подачей материала таких, например, как дробилок с пневмозагрузкой-выгрузкой;
-
- использование сегментного решета позволяет получать готовый продукт с более выровненным гранулометрическим составом.
Список литературы Повышение эффективности рабочего процесса молотковых дробилок закрытого типа
- Зверев СВ. Производство комбикормов непосредственно в хозяйствах//Техника и оборудование для села. 2000. №5. С. 13-16.
- Коротчиков П.Х. Новое оборудование для переработки фуражного зерна в хозяйствах//Тракторы и сельскохозяйственные машины. 1996. №3. С. 8-9.
- Коношин И.В. Молотковая дробилка./Коношин И.В., Звеков А.В./Патент на изобретение РФ 2287371 -№2005109616/03; Заявлен 04.04.2004, Опубл. 20.11.2006, Бюл. №32.
- Глебов Л.А. Повышение эффективности измельчителя компонентов комбикормов/Л.А. Глебов. -М.: 1ЩИИТЭИ Минзага СССР, 1984. -28с.