Повышение эффективности шлифования ёлочных замковых соединений лопаток турбокомпрессоров
Автор: Скрябин Владимир Александрович
Журнал: Инженерные технологии и системы @vestnik-mrsu
Рубрика: Машиностроение
Статья в выпуске: 1, 2015 года.
Бесплатный доступ
В статье рассматриваются вопросы повышения шлифования ёлочных замковых соединений лопаток турбокомпрессоров. Приводятся результаты теоретических и экспериментальных исследований эффективности мощности шлифования профиля лопаток турбокомпрессора дизеля. Отмечается, что при шлифовании ЕЗС с непрерывной правкой кругов алмазными роликами при встречном направлении вращения кругов и роликов шероховатость обработанной поверхности и волнистость снижаются, а производительность труда и стойкость инструмента возрастают по сравнению с попутным направлением вращения кругов и роликов. Результаты работы, отраженные в статье, внедрены в виде технологии финишной абразивной обработки и программного обеспечения в ОАО «Пензадизельмаш» и ОАО «СКБТ» (г. Пенза), применение которых позволило повысить показатели качества рабочих поверхностей деталей.
Технология обработки, теоретические и экспериментальные исследования, непрерывная правка, алмазные ролики, параметры шероховатости и волнистости, эффективность мощности процесса шлифования, ёлочное замковое соединение лопаток турбокомпрессора
Короткий адрес: https://sciup.org/14720145
IDR: 14720145 | DOI: 10.15507/VMU.025.201501.071
Текст научной статьи Повышение эффективности шлифования ёлочных замковых соединений лопаток турбокомпрессоров
ВЕСТНИК Мордовского университета | Том 25 | № 1 | 2015
повышением качества при одновременном снижении ее себестоимости.
Специфика современных задач производства определяется еще и тем, что требуется сокращение сроков обновления производственной номенклатуры деталей, увеличение ее сложности, повышение стабильности основных параметров машин и их надежности. Все это является актуальным при производстве дизельных двигателей, увеличение мощности которых связано с изготовлением качественных высоконапорных турбокомпрессоров (ТК).
Одним из главных конструктивных элементов, определяющих ресурс и надежность работы ТК, является ёлочное хвостовое соединение с торцовым соединением лопатки ТК с диском. Турбинные лопатки изготавливаются из труднообрабатываемых литейных сплавов на никелевой основе с высокими прочностными характеристиками (жаропрочностью и износостойкостью), что значительно увеличивает трудоемкость их изготовления при использовании традиционных методов механической обработки и не обеспечивает в должной мере показатели качества.
Эти методы характеризуются низкой степенью автоматизации производства, малой стойкостью лезвийного инструмента и его высокой стоимостью и не позволяют повысить производительность обработки путем интенсификации режимов резания, что может привести к снижению качественных характеристик деталей.
В современном машиностроительном производстве благодаря созданию шлифовальных станков повышенной жесткости и производительности для повышения точности и надежности изделий разрабатываются и успешно осваиваются новые способы шлифования. Наиболее перспективным является метод глубинного шлифования труднообрабатываемых материалов, позволяющий повысить эффективность механической обработки деталей типа лопаток ТК, в том числе за счет использования специальных плоскошлифовальных станков с ЧПУ.
Для глубинного шлифования сложнопрофильных деталей из труднообрабатываемых материалов необходимо соответствующее оборудование, которое должно быть виброустойчивым, иметь повышенную мощность главного привода, высокую статическую и динамическую жесткость. Данным критериям отвечает оборудование, выпускаемое фирмой ABA-Werk , – плоскошлифовальные двухшпиндельные станки на базе модели FUV-1060N с ЧПУ, а также станки Липецкого станкостроительного завода – плоскошлифовальные двухшпиндельные модели ЛШ-233М с системой ЧПУ Sinumeric 840D .
Применение такого оборудования при обработке ёлочного профиля хвостовика лопаток ТК обеспечивает за- данную производительность процесса обработки, величину параметра шеро-
ховатости Ra = 0,8–1,25 мкм, при этом отсутствуют фазово-структурные изме- нения в поверхностном слое металла [1], а геометрическая точность размеров соответствует шестому квалитету.
Конечным результатом процесса глубинного шлифования ёлочного профиля хвостовика лопаток является его эффективность, которая достигается за счет правильного выбора характеристик круга, режимов шлифования, метода и режимов правки круга, построения циклов шлифования и соблюдения условий шлифования сложнопрофильных поверхностей деталей.
Одним из проблемных вопросов финишной обработки деталей является обработка турбинных лопаток. Лопатка ТК дизеля является наиболее нагруженной деталью, работающей в тяжелых условиях, что определяет длительность службы ТК, т. е. его ресурс. Хвостовик лопатки кроме растяжения и изгиба от центробежных сил, изгиба и кручения от газового потока испытывает также термические напряжения, быстрый нагрев в момент запуска и быстрое охлаждение при остановке двигателя.
Статические напряжения во время работы лопатки в ТК достигают величи- ны порядка 150–200 МПа. Хвостовик лопатки работает при температурах, изменяющихся в диапазонах 450–600 ºС. Перепад температуры от хвостовика к концу пера лопатки составляет 150–200 ºС. Вибрационные напряжения обычно составляют 40–60 МПа.
Конструкции хвостовых соединений весьма разнообразны и применяются исходя из условий обеспечения необходимой прочности, с учетом технологии их изготовления. В транспортном машиностроении при производстве ТК широкое применение получили ёлочные замковые соединения (ЕЗС) с торцовым соединением. Применение ЕЗС с малым числом зубьев и с достаточно большими радиусами скруглений позволяет более равномерно распределять нагрузку по зубьям и сводить к минимуму концентрацию напряжений.
ЕЗС в зависимости от формы профиля корневого сечения лопатки могут выполняться прямыми, когда ось хвостовика перпендикулярна плоскости диска, и косыми, когда ось хвостовика составляет определенный угол, не равный 90º с плоскостью диска и по дуге окружности.
Вид хвостовика лопатки определяет величину выступания кромок корневого сечения, так как их свисание затрудняет соединение лопаток с диском и снижает усталостную прочность корневой части лопатки. Конструкция ЕЗС должна допускать качание лопатки в диапазоне 0,5– 0,8 мм после ее соединения с пазом диска. Лопатки крепятся в пазе диска с помощью клина-замка, который фиксирует их от смещения в осевом направлении.
Основным недостатком ЕЗС является большая зависимость его работоспособности от правильности соблюдения геометрических параметров и качественных показателей при его изготовлении. Таким образом, надежность лопатки ТК при эксплуатации зависит не только от конструктивной прочности (сопротивление циклическим и длительным статическим разрушающим нагрузкам), но и от технологии ее изго- товления, которая оказывает непосредственное влияние на качество поверхностного слоя. Наличие в поверхностном слое ЕЗС остаточных напряжений, наклепа, искажений и фрагментации зерен вызывает активизацию процессов окисления, выгорание легирующих элементов и рекристаллизацию. Все это приводит к снижению жаропрочных свойств, сопротивлению усталости и как следствие – к преждевременному разрушению лопаток.
В настоящее время на предприятиях тяжелого и транспортного машиностроения, занимающихся выпуском ТК для дизелей различного назначения (ОАО «Пензадизельмаш», ОАО «СКБТ», ОАО «Коломенский машиностроительный завод», ОАО «Брянский машиностроительный завод» и др.), используются различные методы изготовления ЕЗС лопаток ТК: фрезерование, протягивание, глубинное шлифование.
Одним из наиболее перспективных является метод глубинного шлифования с непрерывной правкой за два рабочих хода на специальных шлифовальных станках с ЧПУ – одношпиндельном ЛШ183М и двухшпиндельном ЛШ233М. В качестве режущего инструмента используются высокопористые круги 3П 500 × 25 × 203 25А 10П ВМ212К5 ПГ класса точности А, 1кл. 35 м/с. Обработка деталей производится с технологическими режимами: υ = 30 м/с; υ = 200 мм/мин; с СОТС АКВОЛк – 10 М. д
В качестве правящего инструмента применяются алмазные правящие ролики (АР) АС65Т, АС82Т, АС-132 зернистостью 10. Материал лопаток ТК – труднообрабатываемый жаропрочный литейный сплав АНВ300 и жаропрочная сталь 31X19Н9, а также сплав на никелевой основе XН70ВМТЮ (ЭИ-617).
При обработке ЕЗС лопаток ТК методом глубинного шлифования основными недостатками являются износ и засаливание абразивных кругов, что приводит к теплонапряженности процесса обработки и как следствие – к низкой производительности. Одним из методов
Серия « Естественные и технические науки »
устранения этих недостатков является непрерывная правка абразивных кругов АР, а также свойства и количество подводимой смазочно-охлаждающей жидкости (СОТС). Использование непрерывной правки АР как на черновом, так и на чистовом переходах сопряжено с возникновением дополнительных вибраций в технологической системе.
Результаты исследований показывают, что при шлифовании ЕЗС с непрерывной правкой кругов АР при встречном направлении вращения кругов и роликов шероховатость обработанной поверхности и волнистость снижаются, а производительность труда и стойкость инструмента возрастают по сравнению с попутным направлением вращения кругов и роликов.
Обработка профиля ЕЗС лопатки (рис. 1) производилась на специальном плоскошлифовальном станке модели ЛШ233М (рис. 2) при встречном и попутном направлениях вращения абразивного круга и АР (рис. 3). Скорости вращения абразивного круга υкр и АР υрол при шлифовании принимались постоянными для обеспечения равномерного износа шлифовального круга.
ВЕСТНИК Мордовского университета | Том 25 | № 1 | 2015
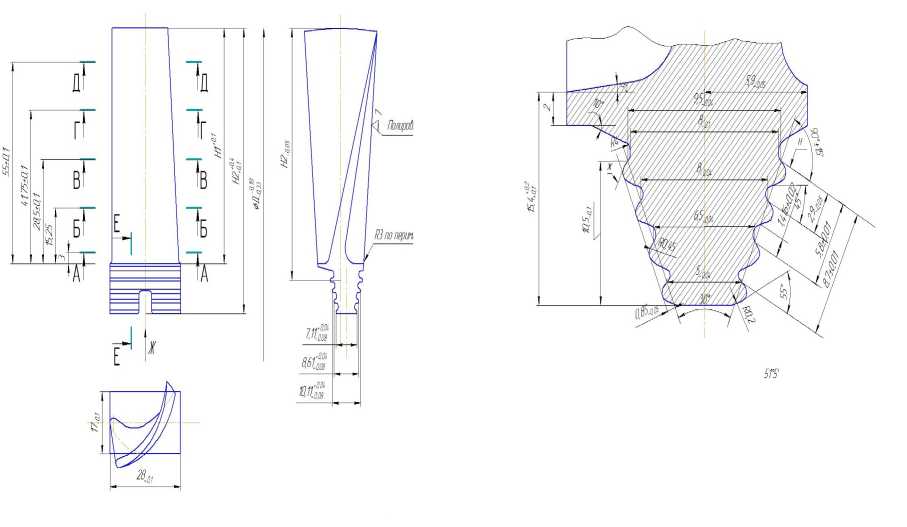
Р и с. 1. Чертеж профиля ЕЗС турбинной лопатки
Режимы шлифования и правки при попутном вращении правящего АР принимались следующие:
-
1. Черновой переход:
припуск на обработку, мм – Z = 1,4–1,8;
скорость круга, м/с – υкр = 25;
скорость подачи стола станка
-
с деталью, мм/мин – υд = 80;
-
2.Чистовой переход:
подача ролика на круг, мм на 10 оборотов шлифованного круга – 0,006.
припуск на обработку, мм – Z = 0,1–0,16;
скорость круга, м/с – υкр = 26–28;
скорость подачи стола станка с деталью, мм/мин – υд = 200–400;
подача ролика на круг, мм на 10 оборотов шлифованного круга – 0,004.
При встречном вращении ролика и круга:
-
1. Черновой переход:
-
2. Чистовой переход:
припуск на обработку, мм – Z = 1,5–2,0;
скорость круга, м/с – υкр = 27;
скорость подачи стола станка с деталью, мм/мин – υд = 100;
подача ролика на круг, мм на 10 оборотов шлифованного круга – 0,004.
припуск на обработку, мм – Z = 0,05–0,1; скорость круга, м/с – υкр = 27–30;
скорость подачи стола станка с деталью, мм/мин – υд = 300–500;
подача ролика на круг, мм на 10 оборотов шлифованного круга – 0,002.
Измерение амплитуды и частоты колебаний, влияющих на виброустойчивость технологической системы, осуществлялось с помощью фотоэлектрической линейки станка на верхней и нижней шпиндельных бабках, шпинделях механизма непрерывной правки станка, усилителя колебаний М60Т, регулятора ПИ19 и осциллографа Н-117/1,5.
Силы резания Рz и РY измерялись с помощью динамометра УДМ100, усилителя 8АН4 и осциллографа Н-117/1,5. Параметры шероховатости и волнистости измерялись на профилометре АБРИС-ПМ7. Для повышения производительности и качества процесса глу- бинного шлифования ЕЗС лопаток ТК большое значение имеет определение тангенциальной составляющей силы резания.
Анализ результатов исследований [1] показал, что в зависимости от числа ступеней ЕЗС (4, 5, 6), припуска на обработку при непрерывной правке АР обеспечивается высокая режущая способность абразивного круга, при этом амплитуда колебаний возрастает при попутной правке из-за колебания соотношения скоростей круга и роликов в пределах 0,8–0,9. Экспериментальные исследования показали, что шероховатость ( R a) и волнистость ( Wz ), шаг волнистости ( S m волн ) поверхности при попутном направ. ле.нии вращения кругов и роликов будут выше, чем при встречном направлении вращения шлифовальных кругов и роликов. При этом составляющие сил резания Р z и Р Y и их рассеивание увеличиваются.
Серия « Естественные и технические науки »
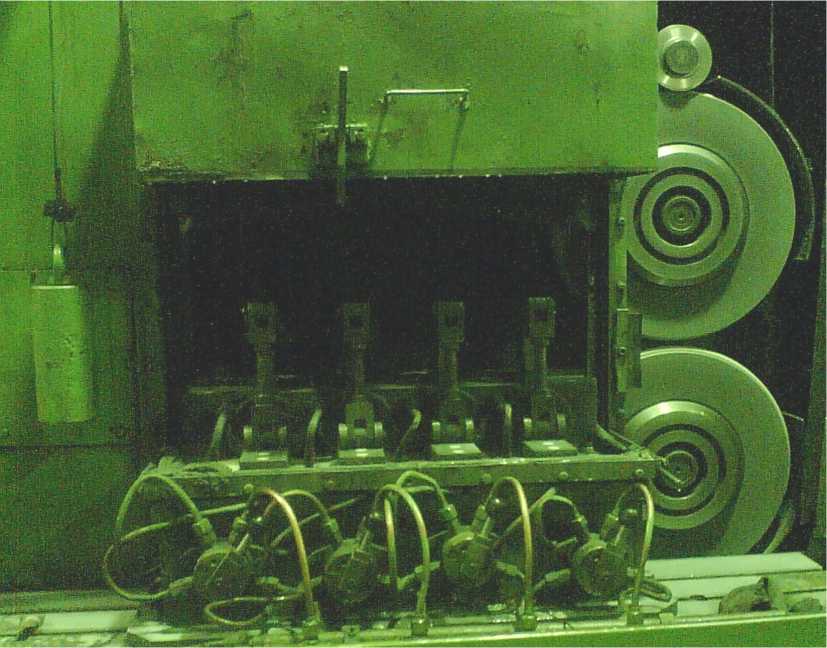
Р и с. 2. Вид рабочей зоны станка ЛШ233М
А
ВЕСТНИК Мордовского университета | Том 25 | № 1 | 2015
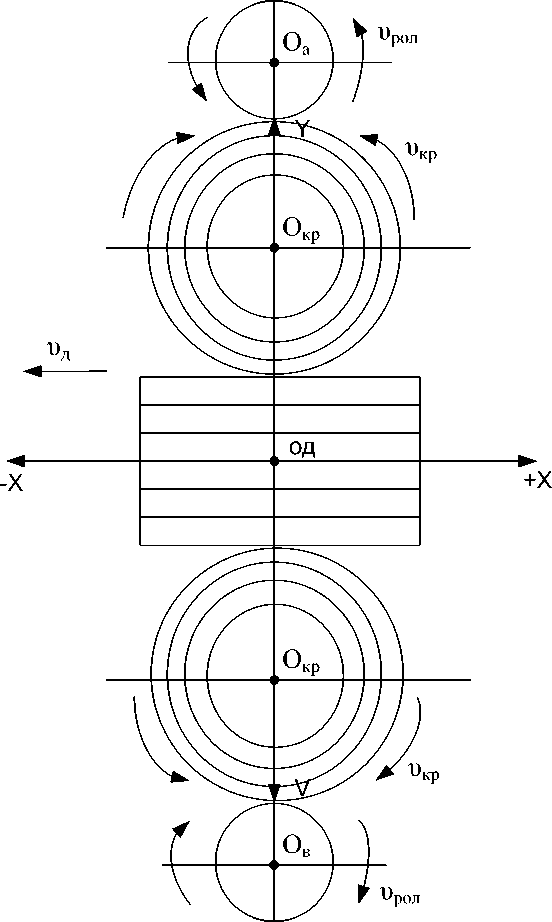
В
Р и с. 3. Схема обработки лопаток при встречном и попутном вращении кругов и АР
Для определения тангенциальной составляющей P z силы резания воспользуемся эмпирической зависимостью [Там же]:
P z = C P x tx P x S j x n Z Pz (cos g ) X Pz x L (1)
где CP – коэффициент, учитывающий обрабатываемый материал и условия его обработки; t – глубина резания, мм; Spr – продольная подача, мм/об; n – скорость резания, м/с; L – длина обрабатываемой детали, м; g – угол, определяющий форму профиля.
Для определения этой силы (рис. 4) выделим бесконечно малый элемент обрабатываемой детали высотой dx , координата которого X крит . При его шлифовании будет возникать элементарная сила:
dPz = C P x tx P x S Y x n Z z (cos g ) X z x dL (2)
Серия « Естественные и технические науки »
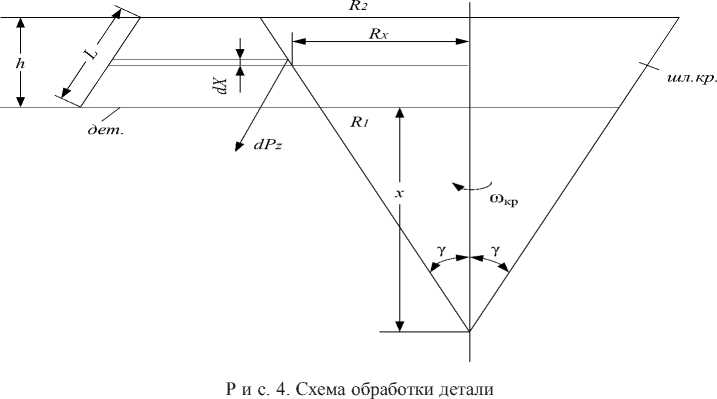
Скорость резания обрабатываемого элемента будет равна v = w,1] xR =w,,, xXxtgA, shl.kr. x shl.kr. gg, где wshl.kr. – угловая скорость шлифовального круга, рад/с.
Поскольку dL = dX / cos γ, то выражению (1) можно придать следующий вид:
dP = CP x tx P x S Y x z z pr.
dx cos g
= A x X4 dx ,
Интегрируя полученное выражение, определяем результирующую касательную силу Pz :
R 2
P z = A J XZp- dx = A x
R 1
XZp P + 1
Z P z +1
R 1
Учитывая, что для труднообрабатываемых материалов турбинных лопаток [1–2] коэффициенты
CP = 98x10 3 ; Xp = 0,6; Yp = 0,65;
Pz Pz Pz
Zp =—0,5, получаем следующее:
где
A = C P x tx P
cos g
Pz = 2x A x[V x 1 R 2 = 2x A x( JR - Jr. ). L J R 1 V V
С учетом габаритов обрабатываемой детали и шлифовального круга получаем:
P z = 2х A х (^0,25 х tg 25°
- V0,245 х tg 25°) = 6,9 х 10 —3 A.
На черновом переходе шлифование осуществляется при следующих режимах: угловая скорость вращения шлифовального круга w shl kr = 101 rad/c^ ;
глубина шлифования t =2 мм;
продольная подача Spr . = 0,104
mm ob .
В этом случае
A = 98x10 3 х 2 0,6 х 0,104 0,65 х
х(101- tg 25°) Z z х
0,51
х(--,----) = 5 477.
cos25°
Следовательно,
P z = 6,9х10 - 3 х5475 = 38 H .
На чистовом переходе:
W shikr . = 121,2 radC ;
ВЕСТНИК Мордовского университета | Том 25 | № 1 | 2015
t = 0,1 mm ;
S = 0,207 MMOb .
A = 98х103 х 0,1 0,6 х 0,207 0,65 х
х(121,2 х tg 25°) 0 5 х —1— = 1290;
cos25°
P z = 6,9 х10 - 3 х1290 = 8,9 H .
Определение тангенциальной составляющей силы резания необходимо для определения эффективной мощности процесса глубинного шлифования, оценки производительности и качества обработки вышеуказанных деталей и сум- марных затрат. Одним из важнейших выходных параметров процесса правки при глубинном шлифовании лопатки является его мощность, которая определяется в зависимости от силы резания при непрерывной правке абразивных кругов АР.
Для определения силы резания, возникающей при правке абразивного круга АР, выделим бесконечно малый элемент высотой dX с координатой X (рис. 5). Элементарную силу резания можно определить с помощью эмпирической зависимости [2]:
4,5 х 10-7 х E2-05 х Vp-0-65 х hf х Dr dPz =----------------------------dp-dВ, (4)
( V - + 1)хп
Vp где E – модуль упругости абразивного круга, МПа; Vp – скорость ролика, м/с; Vkr – скорость круга, м/с; hf – фактическая глубина резания, мм; Dkr. – диаметр круга, мм; dp– диаметр ролика, мм; dB – ширина ролика, мм; n– множитель, показывающий, во сколько раз глубина резания больше поперечной подачи.
Из рис. 5 видно, что
Rx = R 2 - X х tg g , rx = a - R 2 + X х tg g, где a – межосевое расстояние ролика и шлифовального круга. В этом случае скорости ролика и круга будут равны:
n kr . = w kr . х R x = w kr .( R 2 - X х tg A ), (5)
n p = w p х r x = w p ( a - R 2 + X х tg A ) , (6)
dB =
dX
cos g
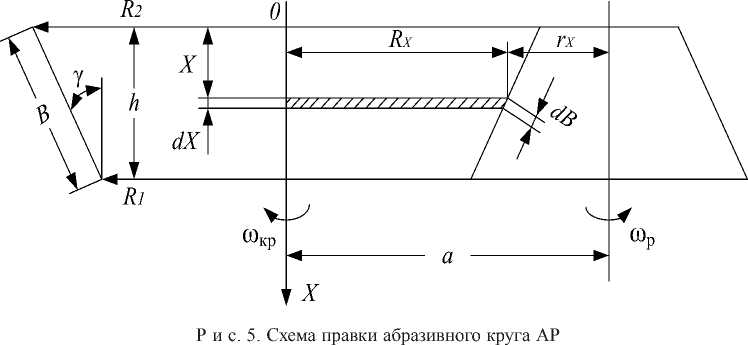
С учетом этих зависимостей сила резания будет определяться из следующих соотношений:
4,5x10 -7 x E 2,05 h ,
P z =/------------
4 R - X x tgg-0,65
x h fx — ',. ,—x[ w p ( a - R 2 + X x tg g )]
J a - R 2 + X x tg g 1J wkr.(R 2- X x tg g)+ 1
x n
w p ( a - R 2 + X x tg g )

R 2 - X x g g a - R 2 + X x tg g
dX 4,5x10-7 xE2,05 xh, x----=---------------x cos g n xcos g
x w p(a
R 2 + X x tg g ) x
-0,65
[ w p ( a - R 2 + X x tg g ) ]
w kr .( R 2 - X x tg g ) + w p( a - R 2 + X x tg g )
4,5x10 - 7 x E 2,05 x
n x cos g о w 68
w p hj. ( R 2 - X x tg g ) x [ w p (
-0,65
a - R 2 + X x tg g ) ] ---------------------x dX .
x R 2 + w 8 ( a - R 2) + ( w 8 - w 68 . ) x X x tg g
Однако этот интеграл не имеет точного аналитического решения. В связи с этим упростим подинтегральное выражение, приняв скорость ролика постоянной, что при малой высоте шлифованного круга приведет к незначительным погрешностям. Учитывая это, вышеуказанное выражение можно представить в следующем виде:
p = A h R 2 - X x tgg x dX , (8)
z 0 b + CX
4,5 x10-7 x E2,05 x w6 x n -0,65 где A =--------------------------;
n x cos g
b = wkr. x R2 + wp (a - R2);
C = ( w p - w kr .) x tg g .
Интегрируя последнее соотношение, получаем:
P = A х R 2 h d ( b + CX ) z = C 'I b + CX
х [ b + CX — b х ln( b + CX ) ] 0 =
. h XdX A х R h A х tg g
— A х tg g =[ln( b + CX )] o — к1 х 0 b + CX C C
A х R b + C х h A х tg g b
----2 х In—--- (CMC х h + b х In-------
C b C 2 b + C х h
—
(9) ).
Для осуществления режимов обработки будем иметь:
4,5 х 10 7 х E 2,05 х w p х h f х n p0,65
n•cos g
4,5 х 10 7 х (52 х 10 3 )205 х 524 х 0,08 х 28,9 х 10 0 65 10хcos25
= 1085.
b — w kr х R 2 + w p ( a — R 2) —
= 101 х 250 + 524 х (305 — 250) — 54 079;
Nshl_ —
8,9х 28,9
102 х 60
0,04kBm;
Npr
C = ( w p — w kr .) х tg g =
— (524 —101) х tg 25° —197.
Следовательно,
48,11 х 25
102 х 60
— 0,2kBm
Суммарная эффективная мощность процесса шлифования и правки круга определяется как:
„ 1085х 250 , 54 079 + 197 х10
P —--------х In------------- z 197 54079
1 08 5 х tg 25 (197 х 10 + 54 079 х 1972
—
—
ВЕСТНИК Мордовского университета | Том 25 | № 1 | 2015
х ln----------------) — 48,11H.
54 079 + 10х197
В первом приближении мощность шлифования лопатки и правки абразивного круга определяется следующим образом:
PZir х n kr . kr .
“ 102х60
P7 х v
N — ^p--p pr 102 х 60,
где PZP — 48,11H ; n P — 25 m /с ;
P zkr . — 8,9H; nkr— 28,9 m /c ;
N e— N shi . + N pr . —
— 0,04 + 0,20 — 0,24kBm.
Учитывая ранее проведенные исследования эффективности мощности шлифования профиля лопаток ТК дизеля можно сделать вывод, что суммарная мощность при шлифовании профиля и непрерывной правке круга в 2–3 раза меньше мощности привода станка, что при шлифовании замка профиля лопаток и правке шлифовального круга, с точки зрения энергетических затрат, свидетельствует о достаточно высокой эффективности процесса глубинного шлифования.
Результаты работы внедрены в виде технологии и программного обеспечения глубинного шлифования ЕЗС лопаток ТК на ОАО «Пензадизельмаш» и ОАО «СКБТ» (г. Пенза), что позволило повысить показатели качества рабочих поверхностей деталей.
Экономический эффект от внедрения разработки достигнут путем увеличения ресурса работы в 1,4–1,5 раза.
Поступила 25.04.2014 г.
Об авторе :
About the author :
Серия « Естественные и технические науки »
Список литературы Повышение эффективности шлифования ёлочных замковых соединений лопаток турбокомпрессоров
- Жук, А. П. Особенности технологии обработки хвостовика лопаток турбокомпрессоров/A. П. Жук, В. А. Скрябин, А. С. Репин//Машиностроитель. -2006. -№ 7. -С. 26-28.
- Коломеец, В. В. Алмазные правящие ролики при врезном шлифовании деталей машин/B. В. Коломеец, Б. И. Полутан -Киев: Наук. думка, 1983. -144 с.
- Оптимизация технологии глубинного шлифования/С. С. Силин . -Москва: Машиностроение, 1989. -120 с.