Повышение эксплуатационной стойкости деталей сельскохозяйственного машиностроения с применением вторичного сырья
Автор: Марков А.В.
Журнал: Агротехника и энергообеспечение @agrotech-orel
Рубрика: Научно-техническое обеспечение процессов и производств в АПК и промышленности
Статья в выпуске: 5 (9), 2015 года.
Бесплатный доступ
Рассмотрены материалы, применяемые при изготовлении боеприпасов и их применимость для упрочнения деталей сельскохозяйственной техники. Предложена технология утилизации боеприпасов и разделение детонационной шихты на магнитную и немагнитную фракции, которые рекомендуется использовать для модифицирования и упрочнения деталей сельскохозяйственной техники при восстановлении наплавкой.
Эксплуатация сельскохозяйственной техники, стойкость, вторичное сырьё, боеприпасы, восстановление деталей наплавкой
Короткий адрес: https://sciup.org/14770116
IDR: 14770116
Текст научной статьи Повышение эксплуатационной стойкости деталей сельскохозяйственного машиностроения с применением вторичного сырья
Введение. Боеприпасы после их изготовления на предприятиях промышленности и проведения различных испытаний подлежат хранению на складах, базах и арсеналах. При этом назначается гарантийный срок хранения, в течение которого обеспечивается сохранность их технических характеристик и боевых свойств. В процессе хранения осуществляются контроль качественного состояния и регламентные работы, в том числе ремонт боеприпасов, связанный с удалением коррозии на металлических поверхностях корпусов, заменой смазки, а также ремонтом деревянной упаковки и др. Списанные боеприпасы требуют более тщательного контроля при дальнейшем хранении. Сроки контрольных испытаний сокращаются, повышается трудоемкость регламентных работ, необходимы более квалифицированные специалисты для обслуживания. Поэтому затраты на хранение списанных боеприпасов возрастают. При этом сроки дальнейшего хранения становятся неопределенными. Если, например, списанная техника может храниться достаточно долго и практический ущерб от этого невелик, так как ценность представляет, главным образом, металлозатраты на его хранение и они малы, то боеприпасы нельзя оставлять без надежной охраны, организованной противопожарной службы, системы контроля качественного их состояния [1-2].
Таким образом, уменьшение запасов боеприпасов за счет списания их части, отслужившей гарантийные сроки хранения, не только не сокращает, а, наоборот, увеличивает затраты на хранение. Это относится как к отдельному виду боеприпасов, так и к системе их хранения в целом.
Материалы и методы исследования. Предварительные оценки показывают, что затраты на хранение списанных боеприпасов могут увеличиться на 10— 20 % по сравнению с затратами, у которых срок годности не истек.
Целью исследования является анализ типов боеприпасов и способов утилизации с истекшим сроком хранения, установление их возможного химического состава получаемой шихты и ее разделения на фракции с последующим использованием для повышения качества изделий при их производстве и восстановлении.
Для реализации поставленной цели рассмотрим исходный материал и получаемую шихту от утилизации 12,7мм патронов с обычной пулей.
Такой патрон состоит из гильзы, пули и пороховой композиции. Проанализируем каждую составляющую.
К гильзовым материалам предъявляются следующие основные требования:
-
- высокая пластичность, которая допускает обработку давлением в холодном состоянии и деформацию гильзы при выстреле без нарушения прочности;
-
- высокая прочность, необходимая для проведения операций вытяжки и обеспечения необходимой жесткости гильзы (патрона), которая имеет относительно тонкие стенки;
-
- склонность к упрочнению в процессе обработки давлением и высокая упругость, необходимая для обеспечения легкой экстракции гильзы из патронника после выстрела;
-
- стабильность механических свойств со временем и устойчивость против старения (самопроизвольного растрескивания);
-
- высокая антикоррозийная стойкость, необходимая в процессе изготовления и хранения исходного материала, полуфабрикатов и готовых изделий;
-
- простота термической обработки в процессе производства и устойчивость к действию высокой температуры при выстреле;
-
- химическая нейтральность порохового заряда.
Результаты исследований. Наиболее полно удовлетворяет перечисленным требованиям латунь марок Л68 и Л70, однако она является дорогостоящим и дефицитным материалом, подверженным самопроизвольному растрескиванию, что затрудняет длительное хранение патронов и требует специальных мер, которые позволяют замедлить процесс их деградации [3].
Латуни Л68 и Л70 обладают наиболее высокими механическими свойствами: σ в =300-350МПа; δ 5 =50-55 %; твердость 50-60 НВ; поперечное сужение 45-50 %.
Химический состав латуней Л68 и Л70, применяемых для изготовления гильз, приведен в табл.1.
Таблица 1 - Химический состав гильзовый латуни, %
Содержание компонентов, % |
||
Л68 |
Л70 |
|
Медь |
67-70 |
69-72 |
Цинк |
33-30 |
31-28 |
Железо |
0,1 |
0,1 |
Свинец |
0,03 |
0,03 |
Фосфор, мышьяк, олово |
0,005 |
0,005 |
Сера, сурьма, висмут |
0,002 |
0,002 |
Дешевым и недефицитным материалом, который не подвержен самопроизвольному растрескиванию, является малоуглеродестая сталь. Она несколько уступает латуни. Сталь обладает меньшей упругостью, склонностью к коррозии, труднее обрабатывается давлением. Стальные гильзы не могут храниться без антикоррозионного покрытия.
Для упрощения технологического процесса изготовления стальных гильз получила применение малоуглеродестая сталь, покрытая с одной или двух сторон томпаком, толщина которого составляет 4-6% от сечения основного стального слоя.
Биметалл является хорошим гильзовым материалом по сравнению с другим стальным материалом, но применение его также связано с расходом дорогостоящего сплава - томпака. Томпак - сплав содержит 89-91 % меди и 11-9 % цинка.
Часть этих расходов составляют безвозвратные потери в виде отходов при изготовлении заготовок для гильз, обрезков полуфабрикатов и т.п. Кроме того, биметалл имеет специфический недостаток, что ограничивает его применение для изготовления крупных гильз, которые требуют больших усилий при обработке.
Свертка заготовки в колпачок и вытяжка стенок гильзы приводит томпак к изгибу и сдвигу матрицей относительно основного стального слоя к краю полуфабриката.
При изготовлении гильз из биметалла не удается сохранить целостность томпакового покрытия на всей поверхности готовой гильзы. В гильзе с выступающим фланцем томпак снимается на корпусе в закраины при штамповке дна и на боковой поверхности фланца, торцов дула в результате их обточки. У гильз с невыступающим фланцем томпак снимается при проведении кольцевой проточки. В указанных местах сталь оказывается не защищенной и подвергается интенсивной коррозии, что требует наносить на эти зоны антикоррозионное покрытие.
С учетом преимуществ и недостатков, перечисленных гильзовых материалов, наблюдается тенденция перехода на холоднокатаную малоуглеродистую сталь для изготовления гильз с последующим лаковым их покрытием.
Химический состав сталей, применяемых для изготовления гильз, приведен в табл. 2
Таблица 2 - Химический состав гильзовый стали, %
Составляющие сплава |
Покрывающий слой |
Холоднокатаная сталь |
Углерод |
0,11-0,20 |
0,11 |
Марганец |
0,35-0,90 |
0,35-0,55 |
Хром |
0,15 |
0,15-0,20 |
Никель |
0,30 |
0,20-0,30 |
Кремний |
0,08 |
0,08-0,13 |
Медь |
0,20 |
0,20 |
Сера |
0,04 |
0,03-0,04 |
Фосфор |
0,035 |
0,025-0,035 |
Конструкции современных пуль патронов стрелкового оружия разнообразны, они делятся на обычные и специальные. Специальные пули по сочетанию видов действий разделяются на две группы:
-
- пули простого действия (обычные - со свинцовым или стальным сердечником; специальные - бронебойные, зажигательные, трассирующие, разрывные и т.п.);
-
- пули комбинированного действия (бронебойно -трассирующие, бронебойно - зажигательные, осколочно -зажигательные, зажигательно - трассирующие, пристрелочно -зажигательные, бронебойно - зажигательные - трассирующие и т.п.).
Одним из лучших материалов для пульных оболочек считается мельхиор ( 78,5-80,5 % меди и 21,5-19,5 % никеля).
Наряду с биметаллом широко применяют неплакированную томпаком холоднокатаную малоуглеродистую сталь. Изготовленные из нее оболочки покрывают тонким слоем меди или латуни (наносят электролитическим или контактным способом) а также лакируют для недопущения коррозии и интенсивного износа ствола при стрельбе.
Среди обычных пуль можно встретить безоболочковые (сплошные),оболочковые со свинцовым или стальным сердечником.
Наиболее простое строение имеют безоболочковые пули. Сплошные свинцовые пули применялись в прошлом веке, в настоящее время их используют для спортивного оружия.
Оболочковые пули состоят из мягкого (свинцового) сердечника и прочной оболочки. Толщина стенок оболочки современных пуль находится в пределах: To = (0,06 ... 0,08) d, где d – диаметр пули.
Пули со стальным сердечником имеют в строении три элемента. При их производстве экономится свинец (заменяют сталью) и уменьшается его деформация для увеличения пробивного действия.
Бронебойные пули применяют для стрельбы по бронированным целям. Характерной особенностью бронебойных пуль является наличие в их конструкции бронебойного сердечника высокой прочности и твердости. Между оболочкой и сердечником находится мягкая свинцовая рубашка, облегчающая врезание пули в нарезы. Это предотвращает канал ствола от интенсивного износа.
Бронебойные пули выгодно сочетать с другими видами действия, например, зажигательными и трассирующими. Поэтому бронебойные сердечники встречаются в бронебойно - зажигательных и бронебойно - зажигательно -трассирующих пулях. Конструктивными характеристиками бронебойных, как и других видов пуль с аналогичным сердечником, является сочетание веса и диаметра сердечника: Mg = Md, где Mg- вес сердечника; Md-диаметр сердечника.
В существующих пулях Md увеличивается с калибром и находятся в следующих пределах для пули:
-
- бронебойной Mg = 0,55 - 0,60
-
- бронебойно - зажигательной с металлическим сердечником Mg=0,6-0,65.
-
- бронебойно - зажигательной с карбидовальфрамовым сердечником Mg=0,65-0,75.
Относительный вес сердечника характеризует бронебойные свойства. Чем он больше, тем выше бронебойные свойства пули.
Относительный диаметр сердечника характеризует наполнение пули и чаще всего находится в пределах 0,75-0,85 возможного его увеличения с изменением калибра.
Главная часть бронебойного сердечника определяется его радиусом равным ro=(1,5...2,0)do, что позволяет обеспечить необходимую заостренность вершины и удовлетворительную его прочность при ударе в цель.
Трассирующие пули, применяют для корректировки огня и целеуказания при стрельбе из автоматического оружия. Все они характеризуются наличием специального состава, который воспламеняется от пороховых газов при движении пули по каналу ствола. При полете пули, горя в воздухе, обозначается траектория.
Длина трассирующего действия определяется как: LT = UTT, где UT - скорость горения трассирующего состава в пулях(3-4мм/с);
T - необходимое время горения трассера.
Диаметр выхода пламени подбирается опытным путем и составляет 0,25-0,5 внутреннего диаметра трассера. Выполнен анализ материалов, которые применяют для производства пуль. Материал пульных оболочек приведен в табл.3.
Таблица 3 - Химический состав компонентов пульных оболочек, %
Материал |
Содержание компо нентов, % |
||||||||
С |
Mn |
Al |
Cr |
Ni |
Si |
Cu |
S 1 |
P |
|
не более |
|||||||||
Биметалл 1 |
0,120,20 |
0,350,6 |
- |
0,15 |
0,30 |
0,08 |
0,2 |
0,04 |
0,035 |
Биметалл 3 |
< 0,11 |
0,350,90 |
- |
0,15 |
0,30 |
0,08 |
0,2 |
0,04 |
0,045 |
Сталь 10сп |
0,050,12 |
0,300,50 |
- |
0,15 |
0,25 |
0,60 |
0,2 |
0,095 |
0,030 |
Сталь 10кп |
0,080,13 |
0,250,50 |
0,020,07 |
0,15 |
0,25 |
0,13 |
0,2 |
0,030 |
0,025 |
Сталь 20кп |
0,120,20 |
0,300,50 |
- |
0,15 |
0,25 |
0,06 |
0,2 |
0,035 |
0,030 |
Сталь 20 |
0,160,22 |
0,200,40 |
0,020,07 |
0,15 |
0,25 |
0,13 |
0,2 |
0,030 |
0,25 |
Их механические свойства:
-
- σ B 270-370Н/ мм2;
-
- δ 5 - 29%.
Материал оболочки свинцовых пуль должен удовлетворять следующим требованиям:
-
- совмещать высокую пластичность с достаточной прочностью, необходимой для обеспечения врезания пули в нарезы и заполнения
ею поперечного сечения канала ствола;
-
- позволить обеспечить необходимый вес пули при минимальных ее размерах;
-
- отличаться хорошим качеством обработки штамповкой;
-
- относительной дешевизной.
Этим требованиям за исключением последнего, удовлетворяет свинец с добавкой 1-2 % сурьмы, этот сплав и получил широкое применение. Добавка сурьмы повышает твердость сплава. Удельный вес этого материала 11,3-11,4 г/см3, температура плавления 3300С.Для производства стальных сердечников обычных пуль применяют малоуглеродистую сталь, допускается ее штамповка в холодном состоянии (табл.4).
Таблица 4 - Химический состав металла сердечников пуль, %
Материал |
Содержание компонентов, % |
|||||||
С |
Mn |
Si |
Cr |
Ni |
S |
P |
Cu |
|
Сталь 10 |
0,070,15 |
0,350,65 |
0,170,37 |
0,15 |
0,30 |
0,045 |
0,04 |
- |
Сталь 15 |
0,13 |
0,44 |
0,26 |
0,15 |
0,17 |
0,026 |
0,018 |
- |
Сталь 20 |
0,180,25 |
0,6-0,9 |
0,170,37 |
0,15 |
0,30 |
0,045 |
0,45 |
0,20 |
Сталь 25 |
0,270,35 |
0,5-0,8 |
0,170,35 |
0,15 |
0,30 |
0,045 |
0,40 |
- |
Кроме рассмотренных выше материалов для изготовления бронебойных сердечников применяют и такие, которые обладают в готовом виде высокой твердостью в сочетании с достаточной вязкостью и большим удельным весом. Широкое применение для этих целей получили также различные марки высокоуглеродистых инструментальных и легированных сталей, а также металлокерамические сплавы (табл. 5 и 6).
Стальные сердечники изготавливают из прутковых заготовок путем механической обработки резанием или шлифовкой с последующей термической обработкой - закалкой и низкотемпературным отпуском для уменьшения остаточных внутренних напряжений и повышения прочности. Твердость стального сердечника находится в пределах 64-67HRC. Благоприятно влияет на пробивное действие чистота обработки, особенно головной части сердечника.
Металлокерамические сердечники изготавливают из порошковой смеси путем предварительного прессования и последующего спекания при высокой температуре. Основу таких смесей составляют порошки металлов: карбид вольфрама с добавкой
4-6% кобальта или никеля. Такой сплав имеет следующие свойства: 87-90 HRA, удельный вес 14,5-14,7 г/см3.
Таблица 5 - Химический состав сталей бронебойных сердечников, %
Марка стали |
Содержание компонентов, % |
||||||
С |
Mn |
Si |
Cr |
Ni |
S |
P |
|
У10А |
0,951,04 |
0,150,30 |
0,150,3 |
0,15 |
0,20 |
< 0,02 |
< 0,03 |
У12А |
1,10 1,25 |
0,150,25 |
0,30 |
0,20 |
0,25 |
< 0,02 |
< 0,03 |
У12ХА |
1,15 1,25 |
0,35 |
0,30 |
1,45 1,65 |
0,30 |
< 0,03 |
< 0,03 |
Таблица 6 - Химический состав твердых сплавов
Номер сплава |
Содержание компонентов, % |
|||||
W |
C |
Cr |
Ni |
Co |
Fе |
|
1 |
86,7-87,3 |
> 5,3 |
< 0,1 |
- |
6,0-6,5 |
1,5 |
2 |
87-88 |
> 5,2 |
< 0,1 |
6,0 |
- |
1,5 |
3 |
86,2-87 |
5,4-6,0 |
< 0,25 |
3,5-4,5 |
- |
1,2 |
В бронебойных пулях применяют рубашки, которые являются мягкой опорой для оболочки и составляют необходимые условия для врезки пули в нарезы. Материал рубашки должен обладать высокой пластичностью. Для этого применяется чистый свинец без примесей сурьмы. Другие металлические элементы пуль (стаканчик, кольцо и т.п.) изготавливают из малоуглеродистой стали (иногда плакированной томпаком), что позволяет применять штамповку. В трассирующих пулях применяют два состава – трассирующий (основной) и вспомогательный (зажигательный). К трассирующему составу предъявляют следующие требования. Он должен хорошо воспламеняться от пороховых газов или воспламинительного состава, отличаться большой силой света при небольшой скорости горения; хорошо прессоваться в трассеры, не обладать взрывчатыми свойствами; иметь небольшой удельный вес, а также характеризоваться относительной дешевизной.
В качестве горючих веществ применяют алюминий (пудру), магний или сплавы этих металлов, которые обладают высокой активностью в соединении с кислородом. В качестве окислителей применяют вещества, богатые кислородом, которые сравнительно легко отдают его при высоких температурах (окись бария, кальция, натрия, нитраты бария, калия, стронция).В зависимости от рецептуры трассирующего состава получают разный цвет пламени. Соли бария с различным горючим придают пламени светло- зеленый цвет, соли стронция - красный, натрия - желтый. Предпочтение отдается красному цвету, который обеспечивает хорошую видимость трассы ночью и в яркую солнечную погоду днем.
К зажигательным составам предъявляют другие требования, чем к трассирующим составам. Для них требуются:
-
- хорошая воспламеняемость от пороховых газов при движении пули по каналу ствола;
-
- достаточно высокая температура горения, которая необходима для надежного зажигания состава;
-
- высокая механическая прочность в запрессованном виде с недопущением разрушения от тряски;
-
- отсутствие склонности к гигроскопичности;
-
- отсутствие вредного воздействия продуктов распада на поверхности канала ствола;
-
- низкая скорость горения.
Зажигательные смеси состоят из тех же компонентов, что и трассирующие. К каждому трассирующему составу подбирают свой зажигательный состав [4].
В состав пороха обычно входит 91-96% пироксилина, 1,2-5% летучих веществ (спирт, эфир и вода) , 1,0-1,5% стабилизатора (дифениламин) для увеличения стойкости при хранении, 2-6% флегматизатора для замедления горения наружных слоев пороховых зёрен, 0,2-0,3% графит и пламегасящие присадки. Такой порох изготавливают в виде пластинок, лент, колец, трубок и зёрен с одним или несколькими каналами; применяют в стрелковом оружии и артиллерии. Основными недостатками пироксилинового пороха являются: изменения содержания остаточного растворителя и влаги при хранении. Это отрицательно сказывается на их баллистических характеристиках. Кроме того, он отличается длительностью технологического цикла производства (от 6-10 дней до 1 месяца).
В зависимости от присадок и назначения помимо обычного пироксилинового имеются специальные виды пороха: пламегасящие, малогигроскопичные, малоградиентные (не зависят от скорости горения температуры заряда); малоэрозионные (с пониженным разгарно-эрозионным воздействием на канал ствола);
флегматизированные (с пониженной скоростью горения поверхностных слоев); пористые и другие. Процесс производства пироксилинового пороха предусматривает растворение (желатинизацию) пироксилина, прессование полученной пороховой массы и резку для придания пороховым элементам определённой формы и размеров, удаление избыточного растворителя и состоит из ряда последовательных операций.
Для реализации поставленной в работе цели определили эффективный набор компонентов, состоящих из боеприпасов, для утилизации (табл.7).
Это патроны стрелкового оружия, пиротехнические средства, основные и дополнительные заряды к минометным выстрелам, а также другие боеприпасы, снаряженные порохами, что относятся к числу непригодных, но не опасных в обращении. По указанию снабжающего органа их могут отправлять на окружные склады или уничтожать на месте в военной части путем сжигания.
Выжигание пороха и сжигание боеприпасов проводили на специальных площадках, расположенных не ближе 1,5 км от складов, жилых и других зданий. Для этого площадку в радиусе 25 м расчищали от сухих деревьев, кустарника, сухой травы и окапывали канавой глубиной 0,25 м и шириной 0,5 м.
Таблица 7 - Подбор боеприпасов для утилизации
№ п.п |
Наименование боеприпасов |
В бункере объемом 1 м3 (не более) |
В бочке емкостью 200 л. (не более) |
1. |
Пистолетные патроны |
5000 шт. |
1000 шт. |
2. |
Автоматные патроны |
3500 шт. |
1000 шт. |
3. |
Винтовочные патроны |
2500 шт. |
1000 шт. |
4. |
Осветительные и сигнальные |
200 шт. |
100 шт. |
патроны |
|||
Взрывпакеты |
|||
5. |
Минометные заряды по массе |
50 шт. |
30 шт. |
6. |
пороха |
5 кг |
3 кг |
Сжигание пороха проводили в металлическом бункере объемом 1 м3 или в приспособленной металлической бочке емкостью не менее 200 литров.
Бункер или бочка должны иметь надежные крышки с загрузочными окнами. При съемных крышках разрешается наличие загрузочных отверстий. В этом случае крышка бункера или бочки должна иметь надежное крепление к корпусу.
Для нормального сжигания и выжигание пороха в крышке и боковых стенках бункера (бочки) должны быть отверстия диаметром 6 мм через каждые 50 мм. Такие отверстия делаются в дне бункера (бочки) для стекания компонентов с низкой температурой плавления. Бункер (бочка) устойчиво устанавливается на подложках из кирпичей.
Загрузку патронов к стрелковому оружию в бункер (бочку) проводили по желобу из укрытия (стенки, что не сгорает) под наблюдением руководителя работ. Зажигательные (основные) заряды к ним, сигнальные и осветительные патроны загружали связанными в пачки по 10-12 шт.
На загруженные в бункер (бочку) боеприпасы накладывали мелкие дрова, отходы бумаги и т.п. в количестве 10-15 кг. Для лучшего воспламенения добавляли бездымный порох.
Разгрузку бункера после утилизации проводили только после прекращения горения и разрывов патронов, а также полного его охлаждения. Шихту, полученную после выжигания пороха из патронов стрелкового оружия, очищали от золы, сортировали по роду металла, проверяли на безопасность и полноту сгорания пороха, срабатывания капсюлей.
Выполнены исследования по получению детонационной шихты, которая может быть использована как для модифицирования жидкого металла, так и при восстановительной наплавке изделий.
Для утилизации использовали 12,7мм патроны с обычной пулей, срок хранения которых истек, согласно действующей нормативной документации.
Патроны утилизировали методом сжигания при нагреве до температуры самопроизвольной их детонации с доступом кислорода без добавления вспомогательных детонирующих веществ. Полученная шихта представлена на рис 1.
Шихта при таком способе утилизации была разделена на первом этапе на две фракции: немагнитная и магнитная[5].
Проведенными экспериментами было установлено, что полученную методом сжигания шихту можно легко разделить по компонентам при следующих обработках: магнитной (отделяется фракция, содержащая окислы железа), не магнитная – просевом через сито (отделяется дисперсная углеродосодержащая фракция и медный порошок)и более грубая сфероидизированая фракция, содержащая медь, углерод и железо(рис.1, б, в и рис. 2).
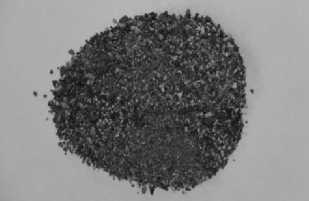
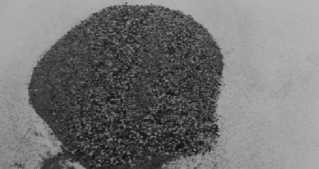
б - немагнитная фракция
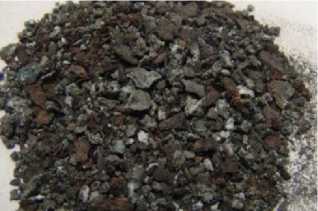
в - магнитная фракция
Рисунок 1 - Детонационная шихта от утилизации 12,7мм патронов с обычной пулей:
а – общий вид шихты, б - немагнитная фракция, в - магнитная фракция
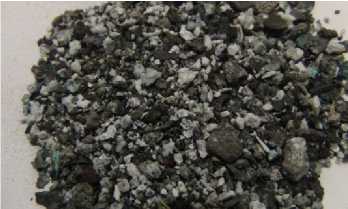
Рисунок 2 - Крупная фракция, содержащая Сu, C, Fe
Химический состав каждой фракции приведен в табл. 8.
Таблица 8 - Химический состав утилизированного сырья
Наименование фракций |
Химический состав фракций,% |
||
C |
Fe |
Cu |
|
Магнитная фракция |
2,87-4,5 |
31,15 |
6,10 |
Мелкая немагнитная фракция |
3,37-3,43 |
2,9 |
3,14 |
Крупная немагнитная фракция |
4,65-8,1 |
3,15 |
3,69 |
Из приведенных данных видно, что магнитная фракция состоит из C, Fe, Cu и может быть использована при выплавке металла и восстановительной наплавке.
Мелкая и крупная немагнитные фракции также могут быть использованы в виде шихты для выплавки изделий в том числе и из цветных металлов.
Такое разделение позволяет использовать полученное вторичное сырье для производства и восстановления различных изделий из черных и цветных металлов.
Выполненный анализ будет эффективным для использования в качестве вторичного сырья – детонационной шихты при легировании и модифицировании различных сплавов. Это позволит существенно сократить затраты на производство изделий и повысить их эксплуатационную стойкость за счет дополнительного легирования и модифицирования.
Выводы. Из приведенного анализа следует, что при таком большом наборе материалов, которые используются для пуль различного назначения, возможно, получать шихту, отличающего состава при утилизации. Поэтому для использования получаемой при утилизации шихты требуется обязательное определение ее химического состава и только после этого можно принять решение об ее использовании и выбрать методы разделения на компоненты, которые возможно будет эффективным использовать для конкретного назначения.
Список литературы Повышение эксплуатационной стойкости деталей сельскохозяйственного машиностроения с применением вторичного сырья
- Промышленные взрывчатые вещества на основе утилизированных боеприпасов: Учебное пособие для вузов./Под общей ред. Ю.Г. Щукина -М.: Недра, 1988. -319с.
- Мацеевич Б.В. Номенклатура и характеристика промышленных взрывчатых материалов./Б.В. Мацеевич-М.:Наука, 1986. -80с.
- Кирилов В.М. Патроны стрелкового оружия/В.М. Кирилов, В.М. Сабельников -Москва: Воениздат, 1980. -273с.
- Огарков Н.В. Порох/Н.В.Огарков//Советская военная энциклопедия -Москва: Воениздат, 1978. -Том 6. -678с.
- Марков А.В. Утилизация боеприпасов для вторичного использования при производстве и восстановлении деталей/А.В. Марков//Информационно-аналитический международный технический журнал «Промышленность в фокусе».-2013. -№8. -C. 52-55.