Повышение качества поверхностного слоя деталей горных машин при металлообработке
Автор: Соловых Данила Янисович, Островский Михаил Сергеевич
Журнал: Горные науки и технологии @gornye-nauki-tekhnologii
Статья в выпуске: 5, 2010 года.
Бесплатный доступ
Работа посвящена улучшению качества поверхностного слоя деталей горных машин с помощью системы ПРОЭмулятор, путем контроля вибраций системы и в частности режущего инструмента. Предложена система адаптивного контроля вибраций для системы ПРОЭмулятор.
Проэмулятор, качество поверхности, вибрации, инструмент, датчики, адаптивная система, шероховатость, волнистость, точность обработки
Короткий адрес: https://sciup.org/140215139
IDR: 140215139
Текст научной статьи Повышение качества поверхностного слоя деталей горных машин при металлообработке
Эксплуатационные свойства деталей машин и долговечность их работы взначительной степени зависят от состояния их поверхности. В отличие от теоретической поверхности деталей, изображаемых на чертеже, реальная поверхность всегда имеет неровности различной формы и высоты, образующиеся в процессе обработки.
Качество поверхности характеризуется шероховатостью, волнистостью и физико-механическими свойствами поверхностного слоя. Шероховатостью поверхности (микрогеометрией) называют совокупность неровностей с относительно малыми шагами на базовой длине, образующих рельеф поверхности детали.
Волнистость поверхности — это периодически повторяющиеся и близкие по размерам неровности, расстояние между которыми значительно больше, чем у шероховатостей. Высота волны может изменяться от 0,5 до 509 мк, шаг — от 1 до 15 мм; форма ее близка к синусоиде.
Волнистость поверхности вызывается колебаниями системы СПИД и неравномерностью процесса резания.
Шероховатость и волнистость поверхности взаимосвязаны с точностью размеров; при высокой точности шероховатость и волнистость имеют малые величины. В основном по этим Двум факторам и оценивают качество поверхности.
Неровность поверхности уменьшает площадь фактического касания двухсопрягаемых поверхностей, поэтому в начальный период работы соединения возникают значительные удельные давления, которые ухудшают условия смазки и, как следствие, вызывают более интенсивное изнашивание поверхностей .
Микронеровности поверхности являются местом концентрации напряжений, поэтому более шероховатые поверхности имеют меньшую усталостную прочность в условиях циклической нагрузки. Особенно сильно шероховатость поверхности влияет на предел выносливости детали в местах концентрации напряжений.
Грубо обработанные поверхности более подвержены коррозии, особенно в атмосферных условиях, так как коррозия наиболее интенсивно протекает на дне микронеровностей и мелких надрезов.
От шероховатости поверхности зависит и стабильность неподвижных посадок. При запрессовке детали наблюдается сглаживание микронеровностей, приводящее к уменьшению фактического натяга. В связи с этим уменьшение прочности соединения деталей обнаруживается при более шероховатых поверхностях.
С другой стороны, слишком большое снижение шероховатости приводит к ухудшению условий смазки, так как наочень чистых поверхностях плохо удерживается смазочный слой.
Все выше сказанное говорит нам о том, что нужно искать путь повышения точности обработки и контроля получаемой поверхности.
Возможны три пути повышения точности обработки:
-
1) снижение чувствительности системы к входным воздействиям;
-
2) уменьшение уровня входных воздействии;
-
3) применение систем с обратной связью - управляющее воздействие компенсирует смешение формообразующей вершины инструмента вследствие силовых и кинематических воздействий (наиболее перспективный).
В процессе обработки сама деталь, инструмент и узлы станка, находясь в относительном движении, представляют собой сложную динамическую технологическую систему, поведение которой заранее определить практически невозможно. Наиболее преспективным направлением для снижения уровня вибраций технологической системы является направление с применением систем адаптивного управления.
Система адаптивного 3-х контурного контроля вибраций (на базе системы ПРОЭмулятор) позваляет постоянно получать данные о виброустойчивости системы. На станке помимо датчиков контроля перемещения, устанавливается датчик контроля вибрации. Датчик непрерывно передает данные в ПРОЭмулятор, который фильтрует и рассчитывает входные данные, отображает на десплее картину процесса и предупреждает о повышении или понижении уровня вибрации.
Структурная схема трех контурной системы регулирования режимов резания (Адаптивная система управления)
Зй контур |
|
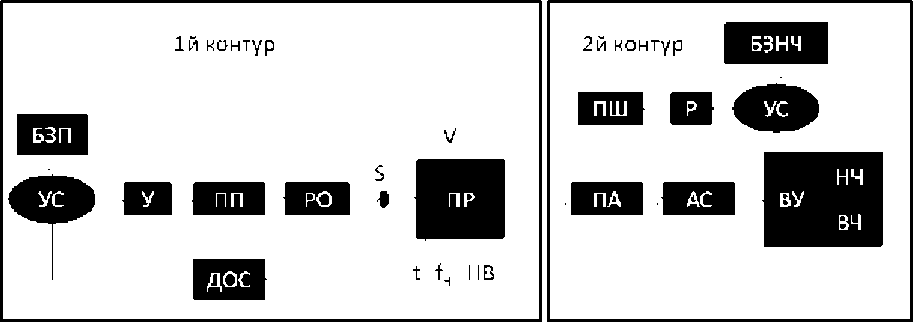
БЗП – блок задания перемещений
УС – устройство сравнения
У – усилитель
ПП – привод подач
РО – рабочий орган
ДОС – датчик обратной связи
ПР – процесс резания
ПА – датчик вибраций (Пьезоакселерометр)
АС –анализатор спектра
ВУ – вычислительное устройство
БЗНЧ – блок задания низких частот
Р – регулятор
ПШ – привод шпинделя
БЗВЧ– блок задания высоких частот
Рис. 1
На фоне этих данных система предлагает повысить или понизить режимы обработки детали.
Одной из важнейших проблем, влияющих на качество поверхности являются вибрации режущего инструмента, резко ухудшающие качество изделий, снижающие производительность обработки и стойкость инструмента.
Режущий инструмент совершает вибрации в области средних и высоких частот, часто являясь наиболее слабым звеном технологической системы. Технолог не располагает материалами по динамическим характеристикам резцов по этому выбор режущего инструмента основан на предложении безвибрационного процесса резания при расчетных, оптимальных по производительности и точности условиях выполнения технологической операцию. Это часто не оправдывается, так как вибрации возникают чаще всего при высокопроизводительных режимах резания.
В результате рекомендаций по режимам резания, имеющиеся в справочниках, теряют свою силу, и возникает необходимость определения режимов резания, удовлетворяющих данному типу инструмента и данному станку.
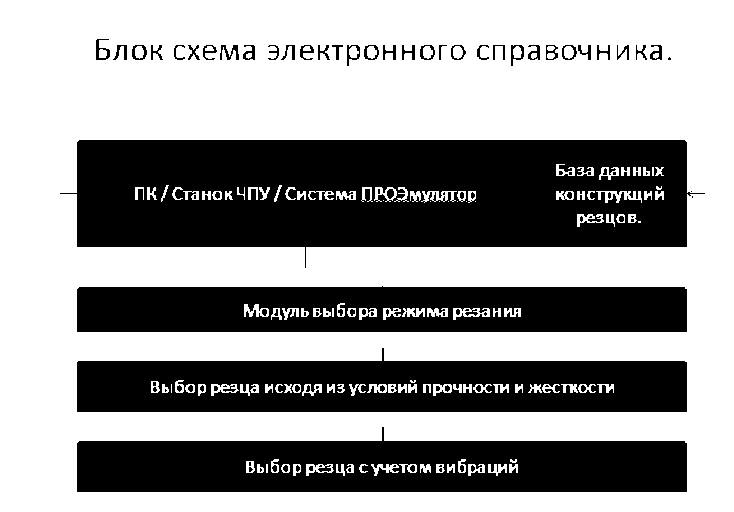
Рис. 2
Новый пакет дополнений к системе ПроЭмулятор изменяет методику выбора резцов, ориентированнуюна предупреждение появления виброколебаний без отступления от расчетных режимов резания, конструкции и геометрии инструмента.
Литературы
-
1. Вибрации в технике. Справочник в 6-ти томах. – М.:
-
2. Кудинов В.А. Динамика станков. – М.: Машиностроение, 1967.
-
3. Васин С.А. Прогнозирование виброустойчивости инструмента при точении и фрезеровании. – М.: Машиностроение, 2006г.
-
4. Интернет-ресурс http://www.proemulator.ru/ ООО «Техстанко-21»
-
5. Интернет-ресурс http://algoholo.ru/ ООО «Алгоритм-опто»
Машиностроение, 1978.
Список литературы Повышение качества поверхностного слоя деталей горных машин при металлообработке
- Вибрации в технике. Справочник в 6-ти томах. -М.: Машиностроение, 1978.
- Кудинов В.А. Динамика станков. -М.: Машиностроение, 1967.
- Васин С.А. Прогнозирование виброустойчивости инструмента при точении и фрезеровании. -М.: Машиностроение, 2006.
- Интернет-ресурс http://www.proemulator.ru/ООО «Техстанко-21»
- Интернет-ресурс http://algoholo.ru/ООО «Алгоритм-опто»