Повышение ресурса соединений сварных узлов и конструкций железнодорожной техники
Автор: Зарезин Владимир Евгеньевич
Журнал: Технико-технологические проблемы сервиса @ttps
Рубрика: Диагностика и ремонт
Статья в выпуске: 4 (34), 2015 года.
Бесплатный доступ
В статье приведены наиболее распространённые способы уплотнения и снятия напряжения в зонах сварных соединений. На основе анализа показана эффективность использования способа ультразвуковой ударной обработки.
Сварные соединения, поверхностное уплотнение, остаточные напряжения, ультразвуковая ударная обработка
Короткий адрес: https://sciup.org/148186275
IDR: 148186275
Текст научной статьи Повышение ресурса соединений сварных узлов и конструкций железнодорожной техники
Наиболее слабыми звеньями конструкций являются сварные соединения, содержащие концентраторы напряжений – источники возникновения усталостных трещин, зоны с ослабленным сопротивлением хрупкому разрушению и наличием остаточных сварочных напряжений (ОСН) высокого уровня.
Как показывает статистика, 70 ÷ 80 % отказов в сварных конструкциях связано со сварными соединениями, хотя объем зоны сварных соединений в современных конструкциях не превышает 1,0 ÷ 1,5 % общего объема [1]. Отсюда следует, что к ответственному сварному соединению – детали грузоподъемной машины, отвалу бульдозера и т.п. должны предъявляться жесткие требования по качеству его выполнения.
Из опыта эксплуатации грузоподъемного оборудования и землеройных машин следует, что основными причинами неисправностей металлических конструкций в них является наличие трещин и свищей, которые расположены, в основном, в районе сварных швов. Вышеуказанные дефекты образуются в результате коррозионного воздействия агрессивных сред, а также могут возникать при проведении сварочных работ, в основном, на монтажных сварных швах (непровары, шлаковые включения и т.д.) -это, так называемые, технические дефекты. Ли- квидация локальных очагов и сквозных дефектов является одной из актуальных задач современной ремонтной технологии транспортного оборудования.
Основой применения технологии стали исследования влияния режимов и методов поверхностного упрочнения на остаточные напряжения, по результатам усталостных и коррозионно-усталостных испытаний и опыта внедрения процесса упрочнения.
Упрочнению подвергаются сварные соединения конструкций (корпусных) изготовленных из малоуглеродистых, низколегированных и высокопрочных сталей, а так же сплавов алюминия и титана.
Поверхностное упрочнение сварных соединений является технологической операцией, направленной на создание в зоне перехода наплавленного металла в основной металл пластических деформаций сжатия с целью снижения коэффициента концентрации напряжений, и тем самым повышения циклической долговечности сварного соединения в (1,8 ÷ 3,5 раза), коррозионно-механической прочности и долговечности сварной конструкции. Пластические деформации сжатия создаются с помощью игл – ударников, металлической дроби, металлических щеток и других видов ударников с использованием специального оборудования.
Поверхностное упрочнение следует применять на сварных соединениях конструкций, работающих в условиях повышенной коррозии и вибрации, при циклических нагрузках, в ответственных сварных соединениях. В некоторых особо ответственных конструкциях, а также конструкциях предъявляющих повышенные требования к точности их установки рекомендуется дополнительно проводить послойное упрочнение (проколачивание) сварных швов за исключением корневого прохода. Поверхностное упрочнение на ответственных стыковых соединениях, работающих в условиях циклической нагрузки, рекомендуется выполнять с двух сторон. В случае применения поверхностного упрочнения в основном для повышения коррозионной стойкости сварного соединения рекомендуется выполнять обработку в обязательном порядке с двух сторон.
Металлическое тело характеризуется напряженным состоянием, обусловленным неоднородностью пластических, линейных или объемных деформаций. Возникновение и перераспределение остаточных напряжений всегда связано с деформацией детали или конструкции, которая в общем случае определяется изменением взаимного расположения материальных точек внутри или на поверхности изделия. Возникающая деформация может быть временной или необратимой, вызываемой соответственно временными (возникающими под действием внешней нагрузки и исчезающими после ее снятия) или внутренними необратимыми (возникающими и уравновешивающими в пределах данного тела без воздействия внешней нагрузки) напряжениями.
Внутренние напряжения делятся: на напряжения I рода или уравновешивающиеся в пределах областей, размеры которых одного порядка с размерами тела, (вызываемые неоднородностью силового, температурного или материального поля внутри тела в зависимости от своей природы); напряжения II рода или кристаллитные, уравновешивающиеся в объемах одного порядка с размерами зерен и напряжения III рода или элементарные, уравновешивающиеся в объемах одного порядка с элементарной кристаллической ячейкой [2].
При изготовлении металлического изделия в течение длительного технологического процесса под влиянием различных технологических операций, вызывающих изменения в металле, возникают внутренние напряжения. В некоторых случаях внутренние напряжения создаются преднамеренно для улучшения качественных характеристик изделия (поверхностный наклеп, закалка, химико-термическая обработка), а при литье, штамповке, сварке, механической обработке возникающие внутренние напряжения, наоборот, снижают стабильность изделия, вследствие чего снижается качество продукции.
Возникновение остаточных напряжений связано с различными процессами, происходящими в металле. В течение одной технологической операции могут действовать один или несколько факторов различной природы.
Рассматривая возникновение остаточных напряжений при сварке, можно выявить следующее, что в большинстве случаев сварные конструкции состоят из большого числа элементов и сварных швов, внутренние напряжения которых взаимодействуют и могут распределяться различным образом. Последовательность приварки и жесткость элементов существенно влияют на остаточные напряжения.
Характерными особенностями сварки являются ее локальный характер, высокие скорости нагрева до температур, превышающих температуры плавления металла (3000° С при газовой и 4000° С при электродуговой сварке), что вызывает температурные напряжения, неоднородные структурные преобразования в шве и зонах термического влияния, изменение растворимости газов, окружающих сварной шов. Объем зоны распределения остаточных напряжений зависит от мощности и продолжительности нагрева, а также от структурных превращений, происходящих в зоне, непосредственно примыкающей к сварному шву (20 ÷ 25 мм при электродуговой и 80 мм при газовой сварке).
Вследствие структурных превращений изменяется удельный объем, так как при нагреве переход перлита и феррита в аустенит сопровождается уменьшением удельного объема, а при охлаждении превращение аустенита в мартенсит сопровождается значительным увеличением удельного объема. Кроме того, вследствие неравномерного охлаждения деталей, структурные превращения во всем объеме происходят не одновременно, и по мере охлаждения всего сечения распределение структурных напряжений изменяется. В низкоуглеродистых сталях распад аустенита при остывании происходит при температуре 600° С и мало влияет на остаточные напряжения, а в легированных сталях при остывании распад аустенита происходит при более низких температурах, когда металл находится в упругом состоянии и вызывает структурные остаточные напряжения, т.е. величина остаточных напряжений, вызванных фазовыми превращениями, зависит от химического состава стали.
В каждом изделии со временем происходит процесс релаксации, (т.е. снятие остаточных напряжений) основанный на термодинамической нестабильности структуры металла с остаточными напряжениями и происходящей без внешнего воздействия или под воздействием нагрева, статических и циклических нагру- зок, что приводит к изменению геометрических размеров изделия.
В общем случае переход структуры металла из нестабильного состояния к более стабильному происходит вследствие возрастания общей энергии металла, сообщаемой изделию в виде тепловой или колебательной. Тепловая энергия передается непосредственно от источника, а колебательная при циклическом погружении рассеивается в изделии из-за его демпфирующей способности.
При переходе атома в состояние, харак-теризируемое энергией, значение которой ниже на AF = F 1 — F 2 (результирующее изменение свободной энергии или движущая сила), преодолевается энергетический барьер AF А, представляющий собой свободную энергию активности реакции (рис.1).
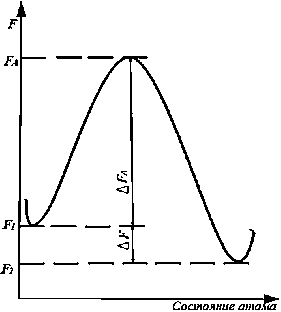
Рисунок 1 - Изменение свободной энергии атома, участвующего в превращении : F 1 , F 2 - свободная энергия в исходном и конечном состояниях соответственно; F A - максимальное значение свободной энергии
Скорость превращения определяется тепловыми флуктуациями, действующими на атом, и описываются соотношением
, (1)
где: К - постоянная Больцмана; Т - температура; С - постоянная.
Удобнее рассматривать термодинамику системы, пользуясь внутренней энергией активации ∆UA, связанной с ∆FA и энтропией активации AS A соотношением,
, (2)
Тогда где А - постоянная (частотный фактор).
Стабильными являются структуры с большими энергиями активации.
Выбор способа упрочнения в каждом конкретном случае обоснован требованиями качества поверхностного слоя, конструктивнотехнологическими особенностями упрочняемых узлов и условиями выполнения работы конструкций. Конкретный технологический метод выбирается с учетом возможности и доступности его применения в реальных производ- ственных условиях, наличии необходимого оборудования, обеспечения наиболее благоприятных санитарно-гигиенических условий труда, наименьшей трудоемкости и максимальной производительности процесса упрочнения.
По силе и глубине воздействия на сварное соединение способы обработки распределяются в следующей последовательности:
-
- обработка пучковым пневматическим молотком;
-
- ультразвуковая ударная обработка;
-
- обработка дробью и обработка щетками.
Для высокопрочных стальных и титановых конструкций упрочнение сварных конструкций рекомендуется выполнять пневмомолотом или ультразвуковой ударной обработкой (далее - УУО), для конструкций из малоуглеродистых сталей - обработка дробью, для конструкций из алюминиевых сплавов предпочтительнее - УУО, обработка дробью или быст-ровращающимися щетками. По производительности оборудования предпочтительно использовать УУО. По уровню шума и вибрации предпочтение отдается УУО, затем следует пневмомолот.
Работы по упрочнению проводятся после выполнения всех сварочных и правочных работ, а также испытаний.
При проведении сварочных работ после выполнения операции поверхностного упрочнения новые сварные соединения подвергаются повторной упрочняющей обработке.
Ультразвуковая ударная обработка является одним из перспективных способов импульсного воздействия поверхностного пласти-чесского деформирования (далее - ППД) на материалы и в частности, на сварные соединения. Она характеризуется многократным импульсным приложением нагрузки с высокой частотой (или суперпозицией частот). При этом обеспечивается снижение концентраций напряжений в сварном соединении, на обработанной поверхности создается упрочняющий слой с повышенной сопротивляемостью к усталостному разрушению, происходит перераспределение остаточных сварочных напряжений в сварном шве и околошовной зоне.
К основным характеристикам режима УУО, определяющим качество поверхностного слоя и коррозионную стойкость (эксплуатационные свойства), относятся: статическая сила прижима инструмента, амплитуда и частота колебаний волновода инструмента.
Результаты проведенных исследований показали, что процесс УУО представляет собой периодические следующие пачки (макроудары) микроударов. Частота следования макроударов - 20 ^ 200 Гц, частота следования микроударов в макроударах - 27 кГц. Таким образом, про- цесс УУО можно представить как частотно-модулированное ультразвуковое воздействие. Частота следования макроударов повышается с увеличением силы прижима инструмента, с уменьшением амплитуды колебаний волновода и уменьшением диаметра ударника. Продолжительность одного макроудара во всех случаях составляла примерно 1 мс. Пауза между макроударами – величина непостоянная даже при фиксированных параметрах инструмента и усилиях прижима.
Опыт применения технологии УУО в промышленности показывает, что созданное оборудование и технология обеспечивает выполнение УУО на поверхности материала с образованием наклепанного слоя глубиной 0,8 – 1,0 мм, с наличием в нем сжимающих остаточных напряжений. В нижележащих слоях происходит частичная релаксация остаточных растягивающих напряжений. Вид обрабатываемых зон корпусных конструкций методом УУО показан на рис. 2. Схема выполнения предварительного валика сопряжения и ППД на тавровом сварном соединении показана на рис. 3. и этот же образец может являться образцом-свидетелем для приемки качества сварного соединения.
Процесс УУО сварной зоны имеет довольно высокую производительность – 18-20 м/час (для сравнения: производительность дробеструйной обработки до 18 м/час, проковка пучковым инструментом 6-8 м/час).
-
1 - предварительный валик сопряжения.
-
2 - линия сплавления валика с основным металлом, подвергнутая ППД.
-
3 - линия сплавления валика сопряжения с наплавленным металлом сварного шва, подвергнутая ППД.
Отличительной особенностью технологии УУО является невозможность при обработке сварного соединения образования дефектов, снижающих прочность сварного соединения из-за неправильного выбора режима обработки, неверной последовательности действий и квалификации оператора.
Отличительной особенностью оборудования для УУО является малый уровень излучаемого шума и вибраций на корпусе инструмента по сравнению с традиционными методами ППД (пневмопроковка, обдувка дробью и т.п.)
Использование технологии УУО обеспечивает снижение уровня остаточных сварочных напряжений (ОСН) на 25-40%, повышение циклической прочности сварных узлов в 2-4 раза, а срока службы сварной конструкции в 510 раз.
Дополнительный эффект приносит метод УУО при использовании его для повыше- ния коррозионной стойкости сталей, особенно при воздействии агрессивных сред. В результате измельчения зерна при УУО снижается склонность стали к межкристаллитной коррозии.
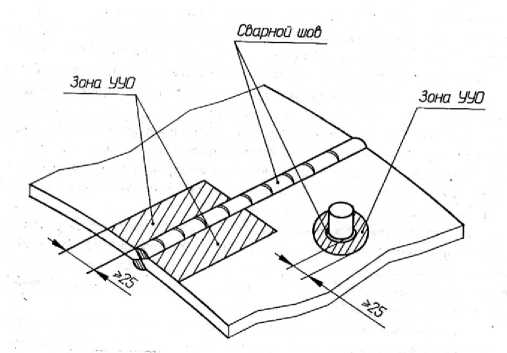
Рисунок 2 – Обрабатываемые зоны сварного шва корпусных конструкций
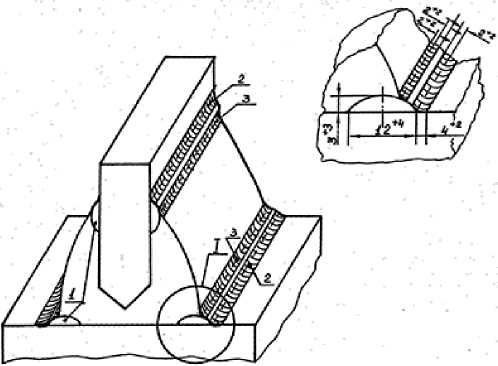
Рисунок 3 – Схема выполнения предварительного валика сопряжения и ППД на тавровом сварном соединении
Список литературы Повышение ресурса соединений сварных узлов и конструкций железнодорожной техники
- Махненко В.И. Совершенствование методов оценки остаточного ресурса сварных соединений конструкций длительного срока эксплуатации//Автоматическая сварка. 2003, №10-11, с. 112-121. (ИЭС им. Б.Е. Патона).
- Горынин И.В., Ильин А.В., Баранов А.В., Леонов В.П. Проблемы обеспечения прочности и ресурса морских ледостойких платформ шельфа Арктики//Автоматическая сварка. 2003, №10-11, с. 52-58.
- Зарезин В.Е. Возможности применения ультразвуковых технологий при эксплуатации и ремонте техники ЖДВ. Сборник статей научно-практических конференций; 27 ноября, 19 декабря 2014 г./ВИ (ЖДВ и ВОСО) -Петродворец, 2014. -156 с.