Повышение устойчивости оснований выемочных участков при изменении фракционного состава выпускаемой руды
Автор: Копылов Александр Сергеевич
Журнал: Горные науки и технологии @gornye-nauki-tekhnologii
Статья в выпуске: 4, 2013 года.
Бесплатный доступ
В статье рассмотрены определение площади скальных контактов при донном выпуске рудной массы. Выведен коэффициент скальных контактов (Кс.к.). Рассмотрены силы, действующие на выпускные воронки. Выведена зависимость раздавливающих и скалывающих сил на устойчивость выпускных воронок. Определѐн наиболее рациональный фракционный состав отбиваемой руды при известной прочности на скалывание τм и соответствующей высоте отбиваемого слоя руды. При рекомендуемом фракционном составе можно увеличить количество выпускаемой отбитой горной массы в 1,31 раза в сравнении с производственными.
Выпуск руды, раздавливающие силы, скальные контакты, фракционный состав, высота столба отбитой руды, параметры
Короткий адрес: https://sciup.org/140215740
IDR: 140215740
Текст научной статьи Повышение устойчивости оснований выемочных участков при изменении фракционного состава выпускаемой руды
Для определения необходимой устойчивости выпускных выработок произведена оценка влияния веса столба отбитой горной массы на их износ. При этом определены условия необходимой прочности и устойчивости оснований блоков, разрушаемых за счёт давления веса столба отбитой горной массы.
В 50-х гг. проф. К.В. Руппенейтом исследовался механизм передачи сил горного давления между соседними блоками-отдельностями в трещиноватом массиве горных пород. Были выполнены эксперименты по заполнению трещин между блоками массива жидким воском или жидким свинцом. После остывания воска или свинца породный массив аккуратно разбирался, чтобы извлечь ”слепок” скальных контактов. В результате многих опытов К.В. Руппенейтом установлено, что площадь непосредственно скальных контактов, а именно – отверстий в ”слепках” – составляет всего 3 – 4 % от поверхности всей трещины между блоками в массиве. Передача сил давления осуществляется через точечные соприкосновения блоков, а в основном, поверхность трещины свободна от передачи сил давления между блоками [9].
На основе физического моделирования определена площадь скальных контактов, но именно между столбом отбитой горной массы и поверхностью выпускных воронок и на этой основе обеспечить их устойчивость, подобрав наиболее рациональный фракционный состав.
Имеется несколько вариантов конструкций оснований блоков: для выпуска и доставки руды ПДМ, траншеи и воронки для ВДПУ и скреперной доставки [4]. В инструкции рассмотрены наименее устойчивые из них – воронки выпуска различного диаметра.
При выпуске руды контакты движущихся кусков горной массы с поверхностью воронки образуются лишь по поверхностям их соприкосновения. Нагрузка от веса столба отбитой горной массы действует не на всю поверхность воронки, а лишь на места контактов кусков руды с её поверхностью. Поэтому на основе физического моделирования определялась площадь скальных контактов кусков отбитой горной массы с поверхностью воронки; при этом обеспечивалось геометрическое, динамическое и функциональное подобие модели натуре, в которых соблюдались размеры воронок и фракционный состав. При динамическом подобии соблюдался объёмный вес руды, представленной кварцитами и магнетитами. При функциональном моделировании соблюдался вес столба отбитой руды высотой 100 м. Исследования проводились на моделях, выполненных в масштабе 1:50 от натурных.
Определение площади скальных контактов производилось путём сканирования на компьютере поверхности развёрнутого усечённого конуса – развёрнутой воронки выпуска с тёмными пятнами скальных контактов, при различном соотношении фракций в отбитой горной массе. Далее, с помощью компьютера, определялась их абсолютная и относительная площадь. Некоторые сканированные поверхности развёрнутого усечённого конуса – выпускной воронки приведены в табл.1 (тёмные пятна – скальные контакты кусков отбитой руды).
Таблица 1.
1 вариант |
2 вариант |
■ ; ; . \ ‘ B 1 - i J |
|
3 вариант |
4 вариант |
^№^ |
|
5 вариант |
6 вариант |
At ^ ' A' - f ^'^ r X JA: '**-'’ ' V - ' ^ |
Продолжение табл. 1.
7 вариант
8 вариант
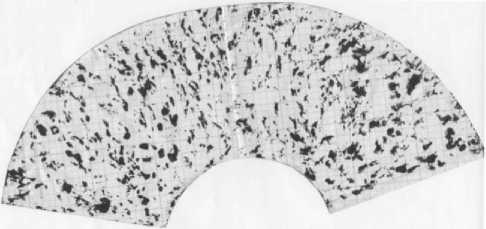
9 вариант
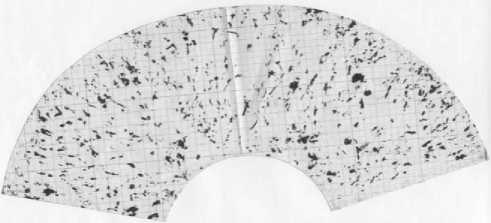
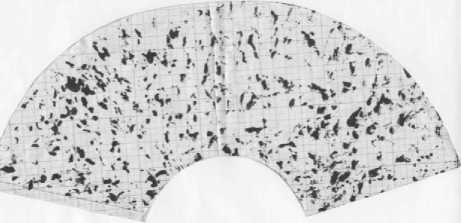
10 вариант
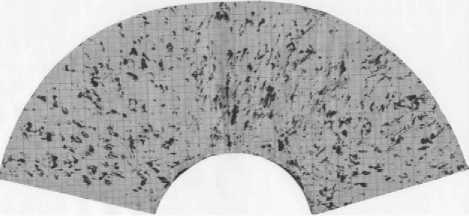
Обработка результатов сводилась к исключению систематических погрешностей (ошибок) и определению надёжности полученных результатов. Полученные результаты приведены в табл.2 (средние значения вариантов).
М 1: 50 Таблица 2.
№№ вариантов |
% соприкосновения контактов |
S, см2 |
Коэффициент скальных контактов (К с.к. ) |
|||
1 половина |
2 половина |
Итого |
воронки |
контакта |
||
1 |
11,41 % |
11,94 % |
11,7 % |
423,0 |
49,4 |
0,12 |
2 |
9,39 % |
6,55 % |
7,97 % |
33,72 |
0,08 |
|
3 |
8,34 % |
6,68 % |
7,51 % |
31,8 |
0,075 |
|
4 |
8,01 % |
11,1 % |
9,55 % |
40,4 |
0,095 |
|
5 |
8,85 % |
5,34 % |
7,09 % |
30,0 |
0,07 |
|
6 |
13,33 % |
8,3 % |
10,83 % |
45,8 |
0,11 |
|
7 |
16,34 % |
18,36 % |
17,35 % |
73,4 |
0,17 |
|
8 |
13,41 % |
12,93 % |
13,17 % |
55,7 |
0,13 |
|
9 |
10,86 % |
9,92 % |
10,4 % |
44,0 |
0,1 |
|
10 |
14,29 % |
14,23 % |
14,26 % |
60,31 |
0,14 |
-
1 вариант: dкус.= 4 мм – заполнение воронки – 100 %;
-
2 вариант: d кус. = 10 мм – 100 %;
-
3 вариант: d кус. = 14 мм – 100 %;
-
4 вариант: d кус. = 4 мм – 50 %; 14 мм – 50 %;
-
5 вариант: d кус. = 2 мм-2%; 4 мм- 3%; 10 мм-5%;14 мм-70%; 20 мм-20%;
-
6 вариант: d кус. = 2 мм-20%;4 мм-25%;10 мм-25%;14 мм-20%;20 мм-10%;
-
7 вариант: d кус. = 2 мм-20%;4 мм-35%;10 мм-35%;14 мм-8%;20 мм-2%;
-
8 вариант: d кус. = 2 мм-14%;4 мм-40%;10 мм-20%;14 мм-18%;20 мм-8%;
-
9 вариант: d кус. = 2 мм-10%;4 мм-50%;10 мм-10%;14 мм-15%;20 мм-15%;
-
10 вариант: d кус. = 2 мм-11%; 4 мм-60%;10 мм-12%;14 мм-12%;20 мм-5%.
Коэффициент скальных контактов Кс.к. определялся как отношение суммарной площади скальных контактов к площади воронки: Кс.к. = Sс.к. / вор.
Как известно, условие устойчивости оснований блоков на контакте с выпускаемой рудой:
F нагр. ≤ [ σ м ], (1)
где Fнагр. – нагрузка, приходящаяся на единицу площади воронки, МПа; [ σ м ] – прочность на одноосное сжатие массива горных пород в основаниях блока, МПа.
Акад. Г.М.Малаховым [1] прочность породного массива на одноосное сжатие определена как: [ σ м ] = 100∙f∙К Σ , где К Σ – коэффициент, учитывающий ослабление прочностных свойств массива,
КΣ = 1 – (Кгеол. + Кп.н. + Квт. + Ки. + … + Кдоб.) , с учётом ослабления массива из-за геологической неоднородности, ведения подготовительно-нарезных работ, работ по вторичному дроблению, истирания потоком горной массы при выпуске, ведения очистных работ и т.п.
Проф. Е.В. Кузьминым были рассмотрены силы, действующие на поверхность выпускной воронки [3]:
─ определяется нагрузка на днище блока, исходя из условия, что воронки выпуска находятся под давлением пород и руды весом:
π2 в. разр. γ , где Р – вес столба горной массы, приходящейся на воронку выпуска, т;
D в. – диаметр воронки, м;
Н разр. – высота столба горной массы, действующего на днище блока, м;
─ определяется площадь поверхности воронки, на которую действует столб горной массы весом Р:
S вор.
π
L вор.
(D в. + D вор. ),
Dв . - Dвор .
при L вор. = ,
2 cosα где Dвор. – диаметр выпускного отверстия, м;
L вор. – длина боковой поверхности воронки, м;
α - угол наклона боковой поверхности воронки к горизонту, град.
Отсюда
π 22
S вор. = 4 cos α ( Dв . Dвор .)
Рассмотрим силы, действующие на стенки выпускной воронки.
Разрушающая составляющая (Рразр.) определяется из выражения:
Р разр. = Р∙cos α
Отсюда нагрузка, приходящаяся на единицу площади воронки:
Р разр
Fнагр. ≥ вор
После подстановки в условие (1) выражений (2) и (3) получаем:
Н разр . D в 2 . γ cos 2 α
F нагр. ≥ 2 2
р в . вор .
На основании табл. 2 преобразуем выражение (4) и запишем условие прочности пород на поверхности воронки при действии раздавливающих сил столба руды и пород при выпуске по площади скальных контактов, а также, используя полученную Г.М. Малаховым [5] зависимость давления потока руды от рода выпуска, вводим коэффициент Кдин., учитывающий динамику процесса выпуска, Кдин. ≤ 1, получаем:
γ Н разр . Dв 2 . cos 2 α
[ σ м ] ≥ 2 2
р в . в ор .
дин .
КК с . к .
Анализируя выражение (5) можно выявить основные факторы, влияющие на состояние воронок в днище блока при выпуске руды в конкретных горно-геологических условиях.
В конкретных условиях подземных рудников для оценки износа воронок выпуска, по скальным контактам, требуется определить, какая высота столба может быть допустимой для крепости имеющихся горных пород. Для этого зависимость (5) выражается относительно отбитой руды (Н разр. ) в виде [3]:
Н разр. ≤
[ σ м ]( D в 2 - D в 2 ор . )
γ D 2 cos 2 α в
КК К р с . к . ∑
, м дин .
Поскольку основания блока представляют собой массив, изрезанный выпускными воронками, имеющими наклонные боковые поверхности к горизонту, то, как известно, имеется также сила, действующая на скалывание (срез) пород весом столба отбитой горной массы (рис.1). Необходимо определить какая из вышеперечисленных сил оказывает наибольшее разрушающее действие на основание блока при выпуске горной массы, и уже исходя из этих сведений определить допустимую высоту отбиваемого рудного слоя при отработке рудной залежи.
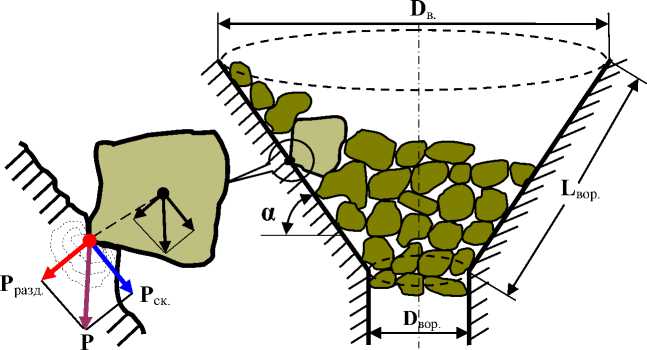
Рис. 1. К расчёту скалывающей составляющей (Рск.) сил давления столба разрушенной горной массы, действующего на поверхность воронки, где Dв - диаметр воронки, м; Dвор. – диаметр воронки в горловине, м; α - угол наклона боковой поверхности воронки к горизонту, град.; Lвор.- длина боковой поверхности воронки, м; Р – вес столба горной массы, приходящийся на воронку выпуска, т.
Скалывающая сила по наклонной поверхности воронки:
Р ск. = Р∙sin α .
(7) Рассматривая действие скалывающей силы (7) получено:
γ Н разр . D в 2 cos α ⋅ sin α К дин .
[ τ м ] ≥ К ( D 2 - D 2 ) К К , (8)
р в в о р. с.к . ∑ где γ – средневзвешенный объёмный вес горной массы, т/м3; Нразр.– высота столба отбитой горной массы, м; Кдин. – коэффициент, учитывающий динамику выпуска горной массы (Кдин. ≤ 1); Кр – средневзвешенный коэффициент разрыхления горной массы.
Соответственно, предельная высота столба определяется:
[τм](Dв2-Dв2ор.) Кр Кс.к. К∑ разр. γDв2 cosα⋅sinα Кдин.
Для оценки прочности основания блока и установления основных причин разрушения воронок принимаем исходные данные: К р = 1,5; γ = 3,2 т/м3 (для кварцитов и магнетитовых руд); D в = 8 м; D вор. = 2,5 м; α = 65°; К дин. = 0,82; К с.к. = 0,07 и 0,17; К Σ = 0,4.
-
а) Покажем пример определения прочного основания блока при действии раздавливающей составляющей от веса столба высотой Нразр.= 100 м (этажное обрушение) при полученных граничных величинах
коэффициентов скальных контактов Кс.к.= 0,07: при этом σ м ≥ 12,5 МПа. При К с.к. = 0,17 : σ м ≥ 5,1 МПа.
-
б) Устанавливается необходимая прочность на скалывание, используя выражение (8), при этом получается: при К с.к. = 0,07 : τ м ≥ 26,3 МПа; при К с.к. = 0,17 : τ м ≥ 10,8 МПа.
Из приведённого следует, что при воздействии кусков отбитой руды на наклонную поверхность воронки выпуска разрушение поверхности воронки происходит в первую очередь за счёт скалывающей составляющей сил веса столба отбитой горной массы. Расчёты показывают, что столб горной массы создаёт скалывающее усилие, в 2,1 раза выше, чем при раздавливании.
Далее рассмотрено действие раздавливающей силы от веса столба Н разр. = 200 м: при К ск = 0,07: о м > 25,0 МПа; при К.;. 0,17: о м > 10,2 МПа. От действия скалывающей силы при Кс.к.= 0,07 : τ м ≥ 52,6 МПа; при Кс.к.= 0,17 : τ м ≥ 21,6 МПа.
Далее рассмотрено действие раздавливающей силы от веса столба Н разр. = 300 м: при !< 0,07: О м > 37,2 МПа; при К с ^ = 0,17: О м > 15,3 МПа. От действия скалывающей силы при К с.к. = 0,07 : τ м ≥ 78,7 МПа; при К с.к. = 0,17 : τ м ≥ 32,4 МПа.
Аналогично производим расчёты действия раздавливающей и скалывающей сил от веса столба отбитой горной массы при размерах воронок Dв. = 14 м и Dв. = 20 м. Полученные данные приведены в табл. 3.
Таблица 3.
Размеры воронок |
Высота столба разрушенной горной массы, м |
Раздавливающая составляющая, σ м , МПа |
Скалывающая составляющая, τ м , МПа |
||
при К с.к. = 0,07 |
при К с.к. = 0,17 |
при К с.к. = 0,07 |
при К с.к. = 0,17 |
||
D в. = 8 м, D в. = 2,5 м, α = 65° |
100 |
12,5 |
5,1 |
26,3 |
10,8 |
200 |
25,0 |
10,2 |
52,6 |
21,6 |
|
300 |
37,2 |
15,3 |
78,7 |
32,4 |
|
D в. = 14 м, D в. = 2,5 м, α = 65° |
100 |
11,6 |
4,8 |
24,5 |
10,1 |
200 |
23,2 |
9,6 |
49,0 |
20,2 |
|
300 |
34,8 |
14,4 |
73,5 |
30,3 |
|
D в. = 20 м, D в. = 2,5 м, α = 65° |
100 |
11,4 |
4,7 |
24,1 |
9,9 |
200 |
22,8 |
9,4 |
48,2 |
19,8 |
|
300 |
34,2 |
14,1 |
72,3 |
29,7 |
По полученным результатам приведены соответствующие графические зависимости (рис.2).
а) б)
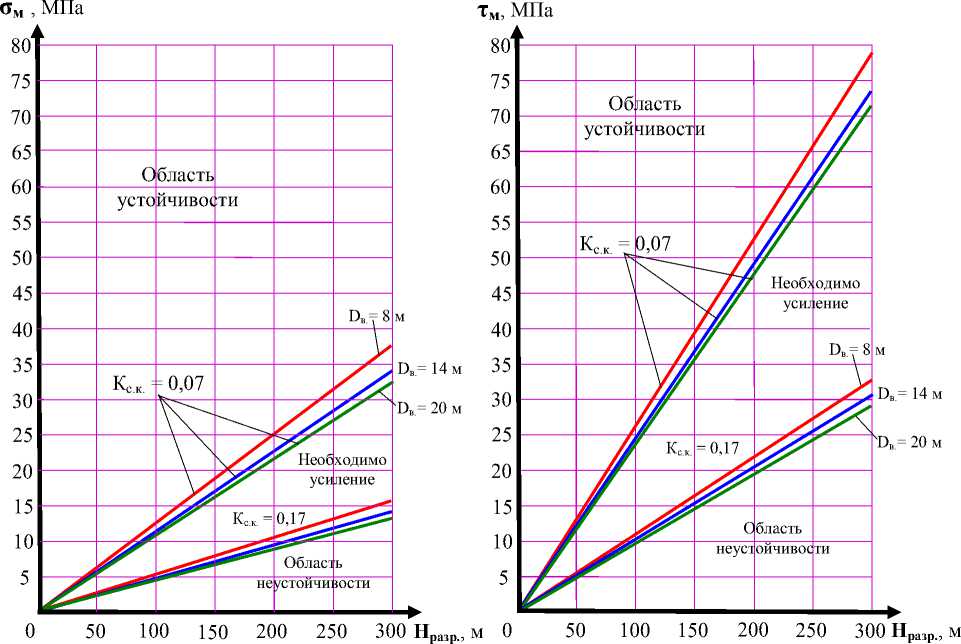
Рис. 2. Графики зависимости прочности основания блока для различных размеров воронок (Dв.) при различной высоте разрушенной горной массы (Нразр.) и при разных величинах Кс.к. по условию а) раздавливания (о м ); б) скалывания (т м ).
Из графиков рис. 2 следует, что при увеличении диаметра выпускной воронки уменьшается удельная нагрузка на её поверхность, повышается устойчивость оснований рудных блоков за счёт увеличения площади поверхности воронки, уменьшается изрезанность днища, снижаются затраты на проведение подготовительно-нарезных работ и улучшаются показатели выпуска руды.
Из рис.2 (а,б) также следует, что если по набору параметров σ – Н (τ – Н) рудник (месторождение, очистной блок) попадают в верхнюю область (область устойчивости), то независимо от фракционного состава, полученного при отбойке, основание блока не будет разрушено столбом горной массы. Если по набору σ – Н (τ – Н) эти параметры очистного блока оказываются между двумя лучами, образованными К с.к. = 0,07 и К с.к. = 0,17, то здесь об устойчивости пород воронок заведомо говорить что-то определённое сложно: необходимо принимать меры для поддержания воронок в рабочем состоянии, стараться получить наилучший фракционный состав при отбойке, использовать крепление выпускных выработок и др. Если же по набору σ – Н (τ – Н) очистной блок попадает в нижний сектор (область неустойчивости), то здесь вполне очевидно, что в таком сочетании параметров выпустить руду из блока не удастся – 43
воронки будут разрушены столбом выпускаемой руды. Для данной прочности горных пород системы разработки с донным выпуском неприемлемы.
Из графиков (рис. 2) также видно, что при рассмотрении действия скалывающей составляющей устойчивая область для пород воронки значительно меньше, чем при действии раздавливающей, а при бόльшей величине К с.к. = 0,17 происходит меньшее разрушение основания блока при выпуске руды. Следовательно, одним из путей повышения устойчивости воронок выпуска является получение такого фракционного состава руды при отбойке, который обеспечит максимальную величину скальных контактов.
Для различных типов горных пород [8] показаны величины раздавливающих и скалывающих усилий при высоте столба разрушенных горных пород Н разр. = 100 м, при самом благоприятном К с.к. = 0,17 (табл. 4).
Таблица 4.
Типы горных пород |
Объёмный вес, γ, г/см3 |
Раздавливающая составляющая, σ м. , МПа |
Скалывающая составляющая, τ м , МПа |
1) Кварциты маршализиро-ванные, выщелоченные |
3,2 |
5,1 |
10,8 |
2) Кварциты гематито-магнетитовые, полуокисленные |
3,41 |
5,02 |
10,6 |
3) Кварциты железистые, джеспилиты |
3,6 |
5,8 |
12,2 |
4) Кварциты ожелезнённые |
2,4 |
3,8 |
8,1 |
5) Руды гидрогематитовые |
3,21 |
5,2 |
11,0 |
6) Руда карбонатная гематито-мартитовая |
4,11 |
6,6 |
14,0 |
7) Руда гематито-мартитовая железная (окисленная) |
4,45 |
7,1 |
15,0 |
8) Руды магнетитовые |
2,89 – 3,93 |
4,6 – 6,3 |
9,8 – 13,3 |
9) Магнетит мелкозернистый |
4,19 |
6,7 |
14,2 |
10) Марганцевая руда |
1,8 – 4,0 |
2,9 – 6,4 |
6,1 – 13,5 |
11) Роговики скарнированные пироксеном |
2,83 – 3,3 |
4,5 – 5,3 |
9,6 – 11,2 |
12) Диорит-порфиры |
3,4 |
5,5 |
11,5 |
13) Гнейсы |
2,66 – 2,79 |
4,3 – 4,45 |
9,0 – 9,4 |
14) Амфиболиты |
2,9 |
4,6 |
9,8 |
15) Порфириты |
3,3 |
5,3 |
11,2 |
16) Туфобрекчия |
3,0 |
4,8 |
10,2 |
17) Скарн оруденелый |
3,59 |
5,8 |
12,2 |
18) Скарны |
3,38 |
5,4 |
11,4 |
19) Известняки |
2,72 |
4,4 |
9,2 |
20) Руда апатитовая |
2,68 – 3,95 |
4,3 – 6,4 |
9,1 – 13,4 |
На основании расчётов установлена зависимость допустимого предельного выпускаемого объёма горной массы от величины коэффициента скальных контактов (рис.4).
Для сопоставления полученных результатов с производственными данными использована инструкция, разработанная Криворожским НИГРИ [6], позволяющая регламентировать размеры конструктивных элементов системы разработки, обеспечивающие их устойчивость в период выпуска, в которой параметры массива днища блока определены по условию раздавливания. Сопоставление результатов по определению высоты подэтажа для различных рудников Кривбасса, полученных в соответствии с инструкцией НИГРИ, с расчётными данными по изложенной выше методике, приведено в табл. 5.
Таблица 5.
Наименование рудника |
Данные НИГРИ |
Расчётные данные |
||||
Мощность рудной залежи, м |
Давление обрушенных горных пород, σ м. , МПа |
Высота подэтажа, Н п. , м |
Давление на скалывание τ м , МПа при К с.к. = 0,07 |
Давление на скалывание τ м , МПа при К с.к. = 0,17 |
Высота подэтажа, Н п. , м |
|
1) Первомайский |
90 |
5,6 |
35 |
25,2 |
10,4 |
25 |
2) им.Ленина |
80 |
4,3 |
40 |
22,6 |
9,3 |
30 |
3) им.Р.Люксембург |
100 |
6,0 |
30 |
29,7 |
12,2 |
20 |
4) им.Фрунзе |
70 |
7,2 |
40 |
20,2 |
8,3 |
35 |
5) им.К.Либкнехта |
25 |
6,5 |
25 |
7,3 |
3,0 |
40 |
6) им.ХХ Партсъезда |
60 |
7,4 |
30 |
17,6 |
7,2 |
30 |
7) им.Кирова |
100 |
7,8 |
40 |
30,8 |
12,7 |
20 |
8) им.Дзержинского |
100 |
6,7 |
40 |
28,5 |
12,0 |
20 |
9) «Ингулец» |
50 |
6,3 |
30 |
14,0 |
6,0 |
30 |
Из табл.5 следует, что принятая высота подэтажа для рудников им. ХХ Партсъезда и «Ингулец» близка расчётным величинам, а на руднике им. К. Либкнехта высота подэтажа ниже расчётной. На остальных рудниках высота подэтажа выше расчётной, и поэтому происходили преждевременные разрушения оснований рудных блоков. В целом имеется близкое совпадение.
Для систем разработки с обрушением руды и вмещающих пород акад. Малаховым Г.М. [5] определено, что отношение общей высоты столба руды и налегающих пород к высоте обрушенной рудной массы в оптимальном случае должно быть равно 2,7÷3,5, в зависимости от фракционного состава и крепости руд. Следовательно, для этих систем, зная общую высоту отбитой горной массы Н разр. , можно определить оптимальную допустимую высоту отбиваемого слоя руды в этаже.
Компьютерным путём выполнен анализ различных вариантов фракционного состава с изменением удельного веса каждой фракции.
Каждый из рассмотренных фракционных составов является наиболее характерным для рудников Горной Шории, Абаканского РУ, рудников Кривбасса.
Наибольшая величина Кс . к . будет соответствовать грансоставу, в котором руда представлена только мелкими фракциями. В реальности этого достичь при отбойке невозможно, поэтому рекомендации сводятся к следующему: на основе произведённых расчётов устанавливается наиболее рациональный фракционный состав отбиваемой руды при известной прочности на скалывание тм и соответствующей высоте отбиваемого слоя руды (табл. 6).
Таблица 6.
Давление на скалывание, Т м , МПа |
Высота отбитой горной массы, Н разр. , м |
Высота слоя отбитой, РУДЫ, Н р.с. , м |
Фракционный состав горной массы (м) % |
Коэфф. скальных контактов ( К с.к. ) |
Т м = 10,8 МПа Кварциты, Руды магнетитовые, |
41 |
13 |
4ус = 0,1 м-2%; 0,2 м-3%; 0,5 м-5%; 0,7 м-70%; 1,0 м-20% |
0,07 |
65 |
21 |
dv „. 0,1 м-20%; 0,2 м-25%; 0,5 м-25%; 0,7 м-20%; 1,0 м-10% |
0,11 |
|
100 |
32 |
4ус = 0,1 м-20%; 0,2 м-35%; 0,5 м-35%; 0,7 м-8%; 1,0 м-2% |
0,17 |
|
76 |
25 |
d кус. = 0,1 м-14%; 0,2 м-40%; 0,5 м-20%; 0,7 м-18%; 1,0 м-8% |
0,13 |
|
59 |
19 |
4ус = 0,1 м-10%; 0,2 м-50%; 0,5 м-10%; 0,7 м-15%; 1,0 м-15% |
0,1 |
|
82 |
26 |
dv „. 0,1 м-11%; 0,2 м-60%; 0,5 м-12%; 0,7 м-12%; 1,0 м-5% |
0,14 |
Из табл.6 видно, что при коэффициенте скальных контактов Кс . к . = 0,17 выявляется наибольшая высота слоя отбитой руды и рациональный фракционный состав отбиваемой руды, который рекомендуется для составления паспорта БВР.
В промышленных условиях скважинной отбойки, при неравномерном размещении ВВ по отбиваемому массиву, отбитая горная масса обычно представлена несколькими фракциями в разных пропорциях. Для крепких горных пород и рассматриваемых параметров оснований блоков, наиболее целесообразным фракционным составом разрушаемой горной массы в диссертации рекомендуется: 0,1 м - 20 %; 0,2 м - 35 %; 0,5 м - 35 %; 0,7 м - 8 %; 1 м - 2 %. Это соответствует условиям, определённым проф. В.Р. Именитовым [2], заключающимся в том, что если при отбойке руды обеспечивается кондиционные куски размером до 0,6 м, то выход негабарита составляет не более 2% при высоте рудного слоя более 25 м. Рекомендуемый фракционный состав, в силу наличия большого количества мелких фракций, потребует наименьшего вторичного дробления и работ по ликвидации зависаний, которые, в свою очередь, приводят к меньшему разрушающему воздействию на выпускные выработки.
Мелкие фракции составляют 55 % (0,1 м – 20 %; 0,2 м – 35 %); при движении они проникают в пространство между крупными, острые выступы крупных скалываются при движении за счёт раздавливания соседними кусками, происходит более полная упаковка фракций, в результате чего происходит бόльшее число контактов кусков отбитой руды с поверхностью выпускного отверстия.
Полученные результаты позволяют при проектировании горных работ определить оптимальную высоту отбиваемого слоя в системах с массовым обрушением, а также в камерных системах, при отработке мощных рудных залежей, и предотвращать опасность досрочного износа оснований блоков при выпуске отбитой горной массы.
Основываясь этими данными определены технологические показатели, обеспечивающие получение рационального фракционного состава (К с.к. = 0,17) отбиваемой горной массы, который обеспечивает наименьшее разрушающее воздействие на основание выемочных участков при наибольшей высоте отбиваемого рудного слоя (табл. 7).
Таблица 7.
Категория горных пород |
Мощность рудной залежи , Мр. , м |
Расположение скважин |
Диаметр скважин, мм |
Расстояние между скважинами, м |
Плотность заряда, г/см3 |
Коэфф. заряжания (недоза-ряда) |
Кол-во подэтажей |
Способ упрочнения оснований руд. блоков |
Мягкие (f ≤ 3) |
10 |
Веерное |
70 |
2,5 – 3,0 |
1,1 |
0,8 |
1 |
Набрызг-бетон |
20 |
2 |
|||||||
30 |
М р . |
|||||||
40 |
||||||||
50 |
2,7 * 3,5 |
|||||||
60 |
||||||||
Средние трещиноватые (f = 4 – 9) |
10 |
Веерное |
70 |
2,5 – 3,0 |
1,1 |
0,8 |
1 |
Набрызг-бетон |
20 |
||||||||
30 |
90 |
2,5 |
1,1 |
Анкерное |
||||
40 |
Параллельное |
2 |
||||||
50 |
105 |
2,5 |
1,1 |
0,85 |
||||
60 |
||||||||
70 |
Параллельно-сближенное |
145 |
2,0 |
1,15 |
0,9 |
Инъек-ционно-анкерное |
||
80 |
М р . 2,7 * 3,5 |
|||||||
90 |
||||||||
> 100 |
1,5 |
1,2 |
||||||
Крепкие трещиноватые (f > 10) |
10 |
Веерное |
90 |
2,0 |
1,1 |
0,8 |
1 |
─ |
20 |
||||||||
30 |
||||||||
40 |
Параллельное |
105 |
1,15 |
0,85 |
При увеличении дополнит. износа ─ инъек-ционно-анкерное |
|||
50 |
1,5 |
М р . |
||||||
60 |
||||||||
70 |
Параллельно-сближенное |
145 |
0,9 |
|||||
80 |
2,7 * 3,5 |
|||||||
90 |
||||||||
> 100 |
1,2 |
Для определения оптимальных параметров отработки блока разработана номограмма (рис. 3).
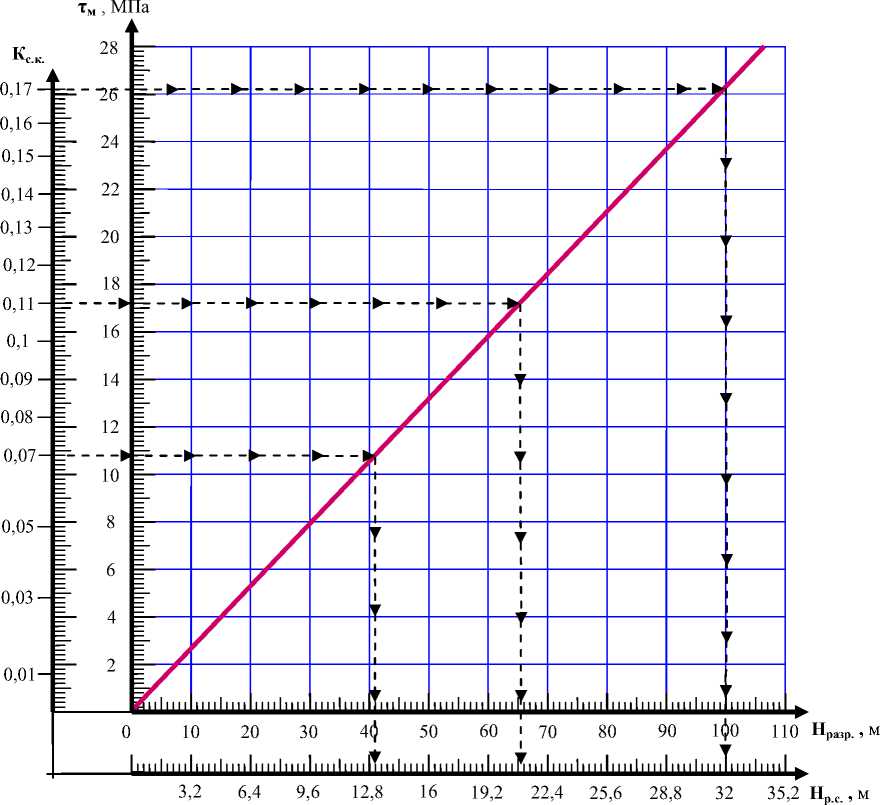
Рис.3. Номограмма определения оптимальных параметров отработки блока при различных коэффициентах скальных контактов.
Номограмма (рис.3) даёт возможность определить, при известных коэффициентах скальных контактов и высоте столба отбитой горной массы и, соответственно, отбитого рудного слоя, что такое-то давление на днище блока от скалывающей составляющей не приведёт его к досрочному разрушению.
Ключ пользования : При К с.к. = 0,17 и Нразр . = 100 м днище блока может сохранять устойчивость при создаваемом давлении τ м = 26,2 МПа.
Также, при известных коэффициентах скальных контактов, и, следовательно, фракционном составе отбиваемой горной массы можно определить количество выпускаемой руды, а также допустимый износ козырька при известных параметрах выпускной воронки и высоты столба отбиваемой горной массы (рис.4).
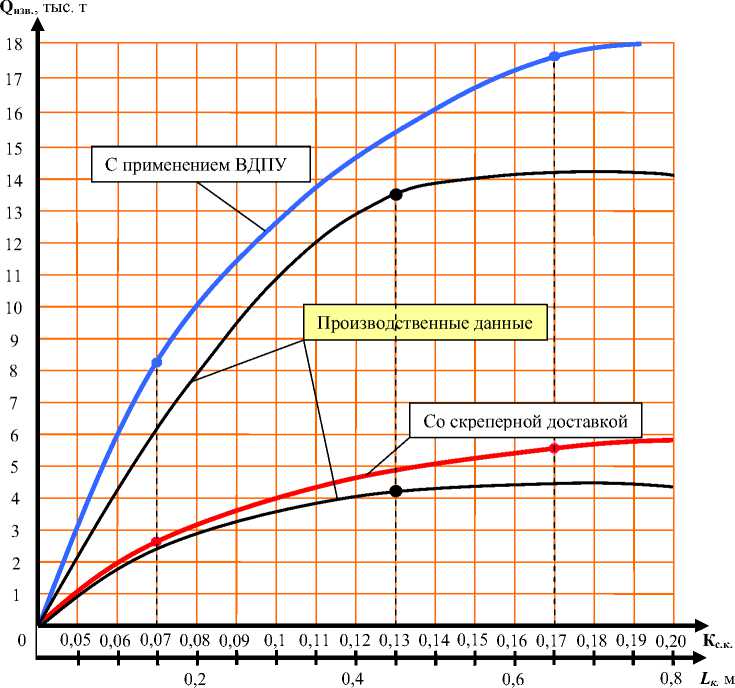
Рис.4. Зависимость количества выпускаемой руды Q изв. от фракционного состава (величины К с.к. ) и определение допустимого износа сопряжения выпускной и доставочной выработки (козырька) L к. (на примере одного пункта выпуска).
При рекомендуемом фракционном составе можно увеличить количество выпускаемой отбитой горной массы в 1,31 раза в сравнении с производственными.
Углетехиздат, 1956.
выпуск руды, раздавливающие силы, скальные контакты, фракционный состав, высота столба отбитой руды, параметры production of ore, forces were crushed, rock contacts, fractional composition, length of post chipped ore settings
Список литературы Повышение устойчивости оснований выемочных участков при изменении фракционного состава выпускаемой руды
- Агошков М.И., Малахов Г.М. Подземная разработка рудных месторождений. -М.: Недра, 1966.
- Именитов В.Р. Технология, механизация и организация производственных процессов при подземной разработке рудных месторождений. -М.: Недра, 1973.
- Кузьмин Е.В. Упрочнение горных пород при подземной добычи руд. -М.: Недра, 1991.
- Лушников В.И. и др. Совершенствование конструкций оснований блоков при системах с донным выпуском руды.//Горный журнал, №5, 1986.
- Малахов Г.М., Безух В.Р., Петренко П.Д. Теория и практика выпуска руды. -М.: Недра, 1968.
- Определение оптимальных конструктивных параметров системы подэтажного обрушения для рудников Кривбасса (инструкция). -Кривой Рог: НИГРИ, 1980.
- Отчѐт о геологоразведочных работах по Абаканскому железорудному месторождению за 1979 год. -Абаза, 1980.
- Ржевский М.М. Справочник (кадастр) физических свойств горных пород. -М.: Недра, 1975.
- Руппенейт К.В. Механические свойства горных пород. -М.: Углетехиздат, 1956.