Предотвращение трещин в литых заготовках за счет учета дилатации в процессе их термической обработки
Автор: Иванов Михаил Александрович, Швецов Владимир Иванович
Журнал: Вестник Южно-Уральского государственного университета. Серия: Металлургия @vestnik-susu-metallurgy
Статья в выпуске: 2 т.13, 2013 года.
Бесплатный доступ
Работа посвящена изучению механизма образования трещин в крупных стальных отливках в период их изготовления и термической обработки. Приведены данные по реальной промышленной отливке, а также технологические режимы, позволяющие предотвратить образование трещин при её изготовлении и термической обработке.
Трещины, литье, заготовка, дилатация, термическая обработка
Короткий адрес: https://sciup.org/147156835
IDR: 147156835
Текст научной статьи Предотвращение трещин в литых заготовках за счет учета дилатации в процессе их термической обработки
Общепринято, что одной из причин образования трещин в крупных стальных отливках является неравномерность деформаций в отдельных участках в пределах одной отливки [1–3]. Однако в отливках нередко встречаются трещины, образующиеся по другому механизму в периоды их термической обработки. Брак таких изделий обходится производству в десятки раз дороже вследствие дополнительных затрат на выполненный объем механической обработки, а также на возможные штрафные санкции и аварийные ситуации.
Типичная ситуация сложилась в производстве крупного металлургического литья, когда заготовки бандажей диаметром 800 мм и высотой от 410 до 710 мм начали отливать центробежным способом с вертикальной осью вращения металлической формы. На начало договора скорость вращения формы при заливке ее расплавом и последующем его затвердевании регулировали от 230 до 270 об/мин в течение двух часов, затем снижали до 200 об/мин и заканчивали при 175 об/мин. Общее время заливки и затвердевания сплава при вращении формы не превышало четырех часов. Температуру металла при заливке корректировали в зависимости от содержания углерода в стали, которое колебалось от 1,4 до 1,9 %. Извлекали отливки из формы при температурах 850–900 °C на свободной поверхности и загружали их в колодцы, разогретые до 710–750 °C. Выдерживали при этих температурах 8–10 часов, после этого печь выключали и охлаждали отливку до 100 °C.
Несмотря на привлекательность принятого технологического процесса и смягчающие режимы охлаждения, качество отливок оказалось низким. Высокая дефектность и брак ставили под сомнение рентабельность производства. Из залитых 176 отливок годных оказалось 132 шт. или 75 %, из них 32 % были подвергнуты ремонту по трещинам, из оставшихся 43 шт. или 24,4 % – окончательный брак: 25 шт. или 58% по трещинам, 11 шт. или 25,2% по усадочным раковинам, остальные 7 шт. по недоливу, шлаковым раковинам, по уходу металла и по засору. Из этих цифр ясно, что технология была не отработана. Кроме того, усложнял про- изводство трудноудаляемый пригар на торцовых поверхностях, вплоть до проникновения металла в зазоры между кирпичами, которые используются для футеровки поддона и крышки. Все это указывало на высокое давление, обусловленное скоростью вращения формы при формировании отливки.
Стремление к уменьшению разностенности и предотвращению усадочных раковин в отливках привело к обоснованию повышенных скоростей вращения формы в начале освоения технологии с 260 об/мин на стадии ее заливки для бандажа высотой 410 мм и 320 об/мин для бандажа с высотой 710 мм. Расчетные значения коэффициента гравитации (К) составляли, соответственно, 30,2 и 45,78. При этом расчетная разностенность не превышала 13,8 мм, что вполне удовлетворяло механиков по объему механической обработки заготовок бандажей.
Для сглаживания негативных явлений (высокой разностенности и недостаточного питания отливок) при снижении режимов вращения изложниц применили заливку электропечного шлака после заполнения изложниц расчетной массой металла, что способствовало улучшению питания и стабилизации коэффициента разностенности, который укладывался в пределы допустимых значений 27,88 для бандажей с Н = 410 мм и 37,95 для Н = 710 мм. Кроме этого, в связи с большими колебаниями содержаний углерода, который связан с температурами ликвидус и солидус, а также с началом линейной усадки и выделения карбидов, провоцирующих образование трещин, были нормированы температуры металла при заливке.
Принятый режим вращения изложниц на центробежной машине с учетом результатов анализа после заливки их металлом приведен в таблице.
Как видно из таблицы, повышенное давление за счет вращения было перенесено на второй час после заливки формы сплавом, когда толщина затвердевшего слоя по расчетам составляет 200–250 мм. Дополнительная нагрузка не вызывает разрушений в отливке.
После всех перечисленных технологических корректив оставались радиальные трещины, кото-
Режим вращения изложниц при центробежном способе получения бандажей
Высота бандажа, мм |
Скорость вращения изложницы, об/мин |
||||
Заливка |
1-й час после заливки |
2-й час после заливки |
3-й час после заливки |
4-й час после заливки |
|
410 |
200 |
200 |
230 |
200 |
0 |
565 |
230 |
230 |
270 |
200 |
175 |
710 |
230 |
230 |
270 |
200 |
175 |
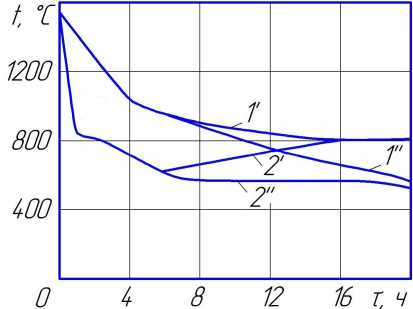
а)
Рис.1. Режим охлаждения (а) и усадка слоев бандажа(б): 1’, 2’ – действующий режим; 1’’, 2’’ – предлагаемый режим, соответственно внутреннего и наружного слоев
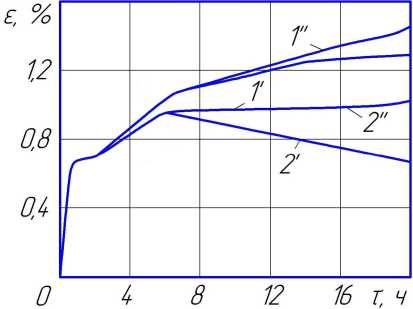
б)
рые выявлялись после сфероидизирующего отжига (отпуска) в нагретых колодцах. Анализ режимов нагрева и охлаждения в колодцах и связанных с этим явлениях дилатации показал, что начальный режим охлаждения в колодцах вызывает растягивающие напряжения в поверхностном слое отливок и может быть причиной образования радиальных трещин. Это хорошо просматривается по графикам температурных кривых и дилатации (линейной усадки) (рис. 1). В стремлении уменьшить скорость охлаждения в период отпуска и совместить его со сфероидизирующим отжигом, температуру в колодце перед посадкой отливок в них подняли до 730 °C, а температура отливки в это время со стороны свободной поверхности выдерживалась в пределах 800–900 °C и по ней осуществлялся контроль температурного режима. Расчетами и измерениями температур поверхностей отливок и атмосферы колодцев было установлено, что при действующем режиме охлаждения отливок в формах наружный поверхностный слой имеет температуру 650–700 °C, а внутренний (свободный) 860–900 °C. Такое состояние отливки в процессе отпуска приводит к повышению напряжений за счет снижения температуры внутренних слоев отливок и повышения наружных.
На рис. 1, а показан действующий режим охлаждения внутреннего (1) и наружного (2) слоев. Цифрами с одним штрихом обозначается действующий режим, с двумя штрихами – предложенный вариант. С соответствующим обозначением показаны расчетные результаты дилатации на рис. 1, б. Линейную усадку, в том числе коэффициенты усадки, определили экспериментально. На основе проведенных исследований температуру в печах перед посадкой отливок снизили до 550 °C с последующей выдержкой в течение 10 часов, после чего печь выключается и отливка охлаждается до 100 °C, а дальнейшее охлаждение осуществляется вне печи до температуры окружающей среды. При таком режиме отпуска обеспечивается смягчение напряженного состояния отливки, что видно по рис. 1, а и б, где кривая дилатации, обозначенная 2’’ показывает минимальную температурную деформацию. По такому режиму обработали более 20 отливок. Случаев образования радиальных трещин не выявлено.
Таким образом, трещины в бандажах высотой 410 и 710 мм с диаметром 800 мм удалось полностью предотвратить за счет оптимизации скорости вращения изложницы (формы) и отработанной температуры посадки отливок в термические колодцы для отпуска после извлечения их из форм.
Список литературы Предотвращение трещин в литых заготовках за счет учета дилатации в процессе их термической обработки
- Василевский, П. Ф. Технология стального литья/П. Ф. Василевский. -М.: Машиностроение, -1974. -408 с.
- Развитие теории трещиноустойчивости отливок/М.А. Иванов, В.И. Швецов, Е.Л. Волосатова, Д.В. Изотов//Вестник Южно-Урал. гос. ун-та. Сер. «Металлургия». -2011. -Вып. 17. -№ 36 (253). -С. 48-50.
- Иванов, М.А. Условия образования и предотвращения трещин в отливках из стали/М.А. Иванов, В.И. Швецов, Е.Л. Волосатова//Наука ЮУрГУ: материалы 63-й науч. конф. Секции техн. наук: в 2 т. -Челябинск: Издат. центр ЮУрГУ, 2011. -Т. 2. -С. 123-127.
- Vasilevskiy P.F. Tekhnologiya stal'nogo lit'ya [Technology Of Steel Castings]. Moscow, Mashinostroenie, 1974. 408 p.
- Ivanov M.A., Shvetsov V.I., Volosatova E.L., Izotov D.V. Advancing the Theory of Crack Resistance of Castings [Razvitie teorii treshchinoustoychivosti otlivok]. Bulletin of the South Ural State University. Series “Metallurgy”, 2011, no. 36, issue 17, pp. 48-50.
- Ivanov M.A., Shvetsov V.I., Volosatova E.L. Conditions of Formation and Prevention of Cracks in the Castings of Steel [Usloviya obrazovaniya i predotvrashcheniya treshchin v otlivkakh iz stali]. Nauka YuUrGU: Materialy 63-y nauchnoy konferentsii. Sektsii tekhnicheskikh nauk [Science in the South Ural State University: Materials of the 63th Scientific Conference. Sections of Engineering]. Vol. 2. Chelyabinsk, SUSU Publ., 2011, pp. 123-127.