Preventing cracks when casting steel slag ladles
Автор: Ivanov M.A., Shvetsov V.I.
Журнал: Вестник Южно-Уральского государственного университета. Серия: Металлургия @vestnik-susu-metallurgy
Статья в выпуске: 2 т.14, 2014 года.
Бесплатный доступ
The paper is dedicated to the improvement of large steel casting technology where slag ladle casting is taken as an example. The temperature measurement of the crystallization process of casting is held. The causes of the formation of cracks are reviewed. To prevent the formation of cracks the recommendations are developed to improve the casting technology.
Crack, casting, slag ladle
Короткий адрес: https://sciup.org/147156864
IDR: 147156864
Текст научной статьи Preventing cracks when casting steel slag ladles
Slag ladles were cast in sandy- cl a y f o r m s from self-hardening soluble-glas s m i x tu re (S G S ) with th e dome u p. Th e f o r m s w e re po ur ed u s ing t h e s ipho n g at ing s y s te m comp o sed of cera m ics . T h e s y st em co n s i sted o f a f unn el , a riser, a run n er gate located ar ou n d th e core on th e lower di a meter o f th e cavity of m o l d an d cho k es t h at ca m e in to t he m old cavi t y from the bott o m .
Th e re we re fo un d t w o typ e s of cr a cks i n c a s t i n g s [3]: v er tic al crac k s a n d horizon t al crac k s t hat were in con j u n ct i on wi t h th e s u p por t r in g in s la g lad le s of th e capacities of 11 m3 and 16 m3 whi ch is s h ow n in Fig. 1.
Fig. 1. The view of the slag ladle with the capacity of 11 m3
The measures to prevent cracks were introduced into the technological process, i.e. the installation of the internal refrigerators in hot nodes of mates with the support ring; the dispersal of the metal feed along the casting perimeter (bottom diameter); the application of SGS which provides the best ductility at temperatures of steel crystallization; the disrupting of the mold at high temperatures.
Despite the measures introduced into the process a number of slag ladles (about 7 %) were damaged by cracks. The correction of cracks required additional costs. Moreover, the appearance of operational cracks into the places of usual occurrence of hot cracks, even when they were not detected, indicated the common reason of weakness and premature failure of the operation of separate parts of slag ladles.
To determine the cause of the operational crack formation, it was necessary: to study the macrostructure of templates cut from castings (Fig. 2a); to investigate the influence of refrigerators (Fig. 2b) and the casting microstructure (Fig. 3); to identify and research the effect of the mold casting modes.
The calculations of the mold casting modes of different authors (Table 1) showed the significant differences in the duration of the casting process. If we exclude the lowest speed of casting process of the shortest duration тс, the fluctuations of the average duration don’t seem large (35–41 s).
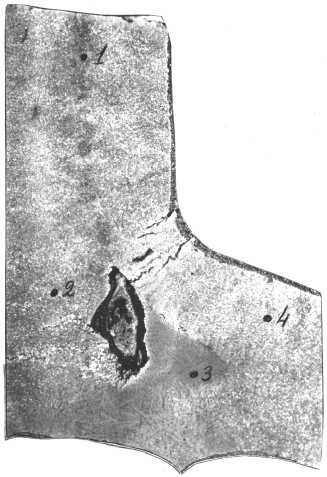
a
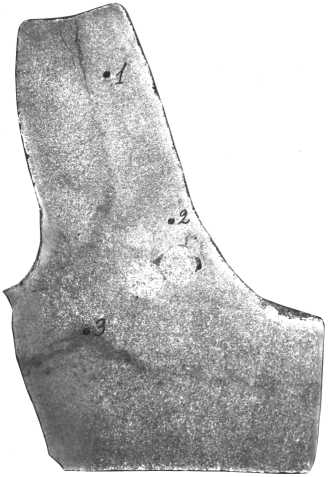
b
Fig. 2. Macrostructure of two templates (etched with 50 % HCl)
Table 1
Calculated values of the duration of the casting process ( t c ) of slag ladles of capacity of 11 and 16 m 3
No. |
Calculation formula |
Author |
Duration tc , s |
|
11 m3 |
16 m3 |
|||
1 |
zc = (16 - 2.36)V^ ; |
Yu.A. Nekhendzi [1] |
189–297 |
222–348 |
2 |
T c = 1.117^ ; |
S.V. Russiyan [5] |
140 |
165 |
3 |
tc = (1 ^ 1.35)G 0. 447 |
B.B. Gulyaev [4] |
56–76 |
65–88 |
4 |
T c = 1.57/5oG o |
G.M. Dubitskiy [5] |
163 |
181 |
5 |
T c = XGo |
N.N. Mishchenko [5] |
109 |
120 |
6 |
t = / C1S1(t c — t1)Rc \ 2 c \1.13im(tc — tm)/ |
G.F. Balandin [5] |
94 |
94 |
7 |
T c = 1.35 75 o G o |
P.F. Vasilevskiy [2] |
146 |
162 |
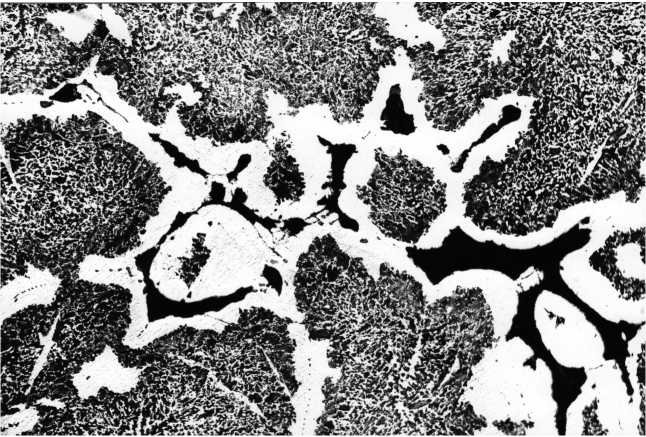
Fig. 3. Destruction and occurrence of eutectic sulphides on boundaries of primary grains ( x 100)
However, the zones with high burning-in were detected on the casting surface. This results from the significant differences between the heating of casting in the sections and is explained by the prolonged exposure of metal stream from relevant chokes.
By measuring the temperature regimes of casting in the marked areas it was founded that the difference in the duration of crystallization of steel 30L taking place in the period of cooling, which is considered the most dangerous one in terms of hot crack forming [6], reached 35 min and the temperature of 75 °C (Fig. 4, 5).
This difference in cooling further increases with the decrease in the speed of casting. The duration of the casting in the production of 11 m3 slag ladles was within 3.5–4.5 min. The duration of the casting in the production of 16 m3 slag ladles was more than 5 min. To verify the substantial impact of the duration of the casting on the process of cracking, one mold for the ladle of 16.5 m3 was filled in for 13 min 20 s (see Fig. 6, 7, 8).
Later the dispersed siphon gating system was replaced with a tangent choke, which ensured the uniform cooling due to the circle flow of metal.
The differences in the range of crystallization temperature reached 83 °C. Hot crack with a maximum opening at the bottom of the casting equal to ~ 50 mm (Fig. 6) became a sufficient evidence of the need to limit the duration of the casting for ladles of 11 m3 within 2 min and for ladles of 16 m3 and 16.5 m3 within 3 min. The temperature of the steel during casting must be maintained in the range of 1530–1580 °C.
The same effect is obtained with similar castings in Magnitogorsk. It was done by increasing the speed of mold filling that was achieved by locating two stops and two risers on opposite sides of the casting with separate branches of the runner gate. The process of casting was strictly regulated. The desired temperature of metal and the high speed of casting coming through two risers create the conditions for the uniform flows from all the chokes located on both sides of the runner gate. It prevents local overheating and reduces the unevenness of deformation of the zones that are formed in case of uneven liquid flow from chokes. The deformation localization coefficient in this case is close to 1 in all the areas between the streams of metal that are formed when the metal comes from the chokes. Other plants producing similar products have adopted this technique.
Иванов М.А., Швецов В.И.
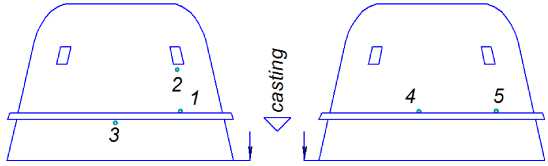
Fig. 4. The layout of points of thermocouples in the ladle of 11 m3
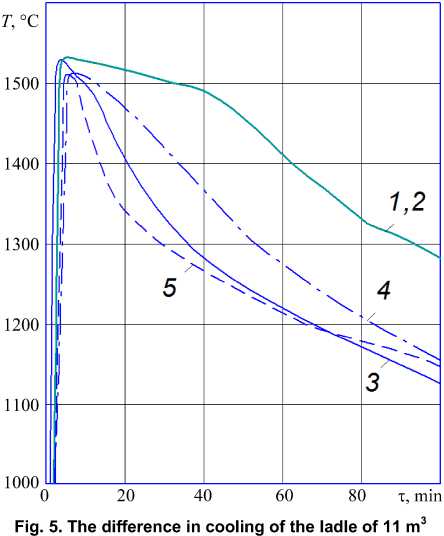
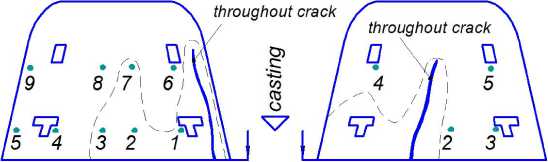
Fig. 6. The layout of thermocouples in the ladle of 16 m3 (indicated by numbers). The arrows show the sides of casting, dashed lines show the areas with an increased level of burning-in
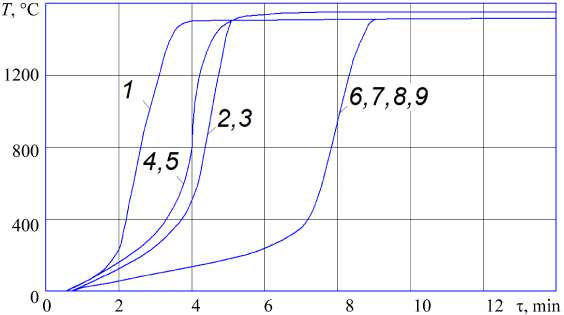
Fig. 7. The preheating of the mold for the ladle of 16.5 m3, tc = 13 min 20 s during the casting (the arrow and dashed lines) by the points in Fig. 6
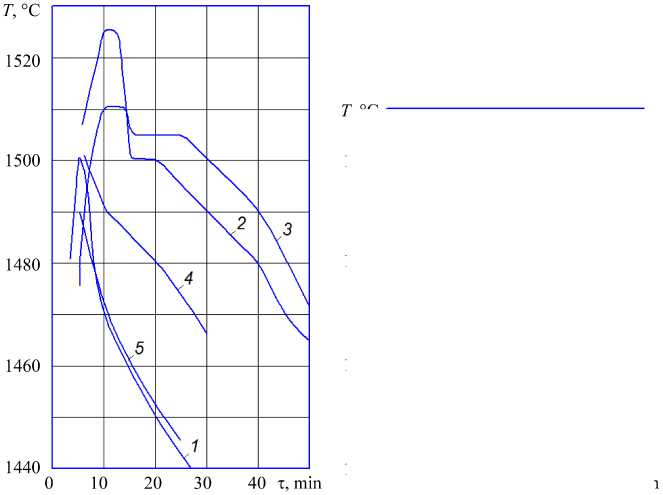
a
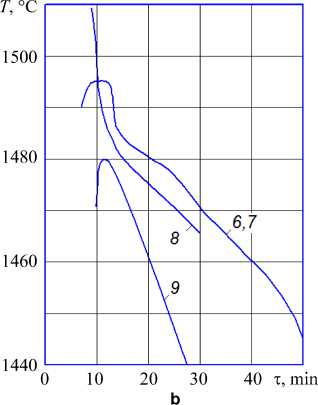
Fig. 8. The cooling of areas with an increased level of burning-in (strokes) on the right (a) and left (b) sides of the casting. Digits are the numbers of thermocouples
Thus, the major factor influencing crack formation is the uneven deformation caused by the lack of mass velocity of mold casting through the siphon runner gate system with the same section of the chokes and insufficient section of channels of other elements, in particular, the runner gate and the riser. The large mass of metal passed through the closest chokes and it was the reason for creating the uneven warming at the second stage of cooling. The difference in temperature preheating and cooling modes reached more than 70 °C at the crystallization range of hot locality.
This negative uneven preheating and cooling locations of the casting can be easily detected without calculations and eliminated by increasing the mass velocity of casting or with an oblique gating of chokes.
Список литературы Preventing cracks when casting steel slag ladles
- Нехендзи, Ю.А. Стальное литье: учеб./Ю.А. Нехендзи. -М.:Металлургиздат, 1948. -766 с.
- Василевский, П.Ф. Технология стального литья/П.Ф. Василевский. -М.:Машиностроение, 1974. -408 с.
- Иванов, М.А. Условия образования и предотвращения трещин в отливках из стали/М.А. Иванов, В.И. Швецов, Е.Л. Волосатова//Наука ЮУрГУ: материалы 63-й науч. конф. Секции технических наук: в 2 т. -Челябинск: Издат. центр ЮУрГУ, 2011. -Т. 2. -С. 123-127.
- Гуляев, Б.Б. Теория литейных процессов/Б.Б. Гуляев. -М.;Л.: Машиностроение, 1976. -214 с.
- Баландин, Г.Ф. Основы теории формирования отливки/Г.Ф. Баландин. -М.: Машиностроение, 1979. -Ч. II. -335 с.
- Развитие теории трещиноустойчивости отливок/М.А. Иванов, В.И. Швецов, Е.Л. Волосатова, Д.В. Изотов//Вестник ЮУрГУ. Серия «Металлургия». -2011. -Вып. 17, № 36. -С. 48-50.