Применение подвижных гидромониторных агрегатов для отработки крутых угольных пластов
Автор: Сергеев Сергей Васильевич, Мельник Владимир Васильевич
Журнал: Горные науки и технологии @gornye-nauki-tekhnologii
Статья в выпуске: 2, 2013 года.
Бесплатный доступ
В статье обоснована целесообразность применения подвижных гидромониторных агрегатов в различных горно-геологических условиях. Представлены три варианта технологических схем выемки угля подвижными гидромониторными агрегатами. Сформулированы основные технологические требования к технике и технологии выемки угля подвижными гидромониторными анрегатами.
Гидромонитор, гидравлическое разрушение, агрегат, угольный пласт, технологическая схема
Короткий адрес: https://sciup.org/140215705
IDR: 140215705
Текст научной статьи Применение подвижных гидромониторных агрегатов для отработки крутых угольных пластов
В результате теоретических и экспериментальных исследований, проведенных во ВНИИГидроугле и МГГУ[1 ,22 ,23], производительность гидромонитора по выемке по современным представлениям определяется по формуле
П в К о Кl * м Q , (1)
где К о - коэффициент отжима и самообрушения, зависящий от мощности пласта и угла падения, оценивающий рост производительности гидромонитора, развитием фронта очистных работ; К l – коэффициент, учитывающий рабочую длину струи; Ψ м - массовое отношение угля к воде в гидросмеси по выемке для условного пласта; представляет собой отношение массы отбитого угля к массе израсходованной воды, взятых за один и тот же промежуток времени (консистенция); Q - расход воды.
Производительность гидромонитора по забою определяется по следующей формуле
Пз зПв , где ηз - коэффициент использования гидромонитора по забою.
Для пластов пологого падения коэффициент использования гидромонитора по забою равняется
7/ 1,04 0,024P 0,12R 0,042m 0,006Ф ,(3)
где Р - давление подводимой к гидромонитору воды; Ry - условный предел прочности угля; m - мощность пласта; φ - угол падения пласта.
Л 1,07 0,024P 0,1R 0,03m 0,005ф ,(4)
В пульпе массовое отношение угля к воде зависит от давления и находится по следующей формуле
5,7 10 3 m

Из анализа формулы (2) с учетом формул (1) и (5), т.е. зависимость
П з 5,7 103 и з К 0 К l
P ' 2
V R y J
Q ,
следует, что производительность гидромонитора повышается при увеличении расхода и давления технологической воды. Получено увеличение производительности при увеличении расхода воды, созданы гидромониторы 12ГД-2 и 12ГП-2 [2,3]. Эти гидромониторы также, как и гидромонитор ГМДЦ-3, предназначены для работы с давлением 12 МПа, но имеют повышенный расход воды (ГМДЦ-3 - 0,05 м3/с, у 12ГД-2 и 12ГП-2 - 0,1 м3/с). Производительность увеличена в 1,5 - 2 раза. Серийный гидромонитор 12ГД-2 широко используется на гидрошахтах, 12ГП-2 принят к серийному производству. Опытно-промышленная проверка работы на повышенных давлениях также подтвердила положение об увеличении производительности [2, 4, 5]. В связи с этим созданы гидромониторы на давление 16 MПа ГМДЦ-4 с расходом 0,05 м3/с и 16ГД с расходом 0,1 м3/с .
При проведении экспериментальных исследований и наблюдении за промышленным использованием гидроотбойки были установлены зависимости для коэффициентов использования гидромонитора по забою [5, 6, 7], позднее уточненные [1]. Согласно зависимостям (3, 4) при повышении давления коэффициент использования уменьшается. Причем эти зависимости получены
для пластов крутого и пологого падения
(рис. 1).
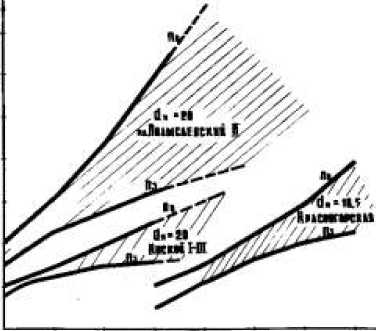
Т I J « * II У tt P.*i
Рис. 1. Зависимость производительности гидромонитора от давления технологической воды.
Физический смысл падения коэффициента использования исследован теоретически и экспериментально [4, 5, 6, 7, 8, 9, 10]. Коэффициент исполь-зования представляет собой отношение
Т в
П з в ,
з
При этом
ТТ+Т в о с ,
Т з Т в + Твс , (9)
где Т в - время, затрачиваемое на отбойку и выгрузку угля из забоя (смыв); Т з - время подачи воды в забой; Т о - время, затрачиваемое на отбойку; Т с - время, затрачиваемое на выгрузку угля из забоя (смыв); Т вс -время, затрачиваемое на вспомогательные операции (разбучивание, разбивка негабаритов, перепуск угля, оконтуривание выработки, управление кровлей, осмотр забоя, перепуск породы); указанные вспомогательные операции производятся во время подачи воды в забой.
С учетом зависимости (9) коэффициент использование гидромонитора Тв , (10)
з Т вс Т в
Или П з 1 , (11)
1+ Твс Т в
В результате хронометражных наблюдений установлено [5, 10, 11, 12], что на шахте "Грамотеинская" коэффициент использования находился в пределах η 3 = 0,67 - 0,85; на шахте "Юбилейная" η 3 = 0,638 - 0,88. Эти цифры получены при давлении воды до 10 МПа. Разброс данных объясняется тем, что они получены для равных пластов и участков.
Представив формулы (3) и (4) в виде
77 з А 0,024 Р , (12)
где А - величина, включающая прочие факторы, независящие от давления;
Р - давление, МПа; можно спрогнозировать значение η 3 при 16 МПа, получив А из приведенные выше цифр коэффициентов использования.
Для шахты "Инская" (бывшая Грамотеинская" № 3 – 4) при давлении 16 МПа (А = 0,91 - 0,98) η 3 = 0,526 - 0,596.
Для шахты "Юбилейная" при давлении 16 МПа (А = 0,878 - 1,12) η 3 = 0,494 - 0,736.
Из формул (11) и (12) следует, что
Т вс 1~Т1 1 А0,024Р, (13)
Т з з
Из зависимости (13), с учетом спрогнозированных значений, коэффициентов использование воды следует, что от времени подачи воды в забой, время, затрачиваемое на вспомогательные операции, будет составлять при давлении 16 МПа: для шахты "Инская" 40 % - 47 %; для шахты "Юбилейная" 26 % - 50 %.
Зависимости η 3 = f (Р) и Т вс /Т з = f (Р) приведены на рис. 2 и 3.
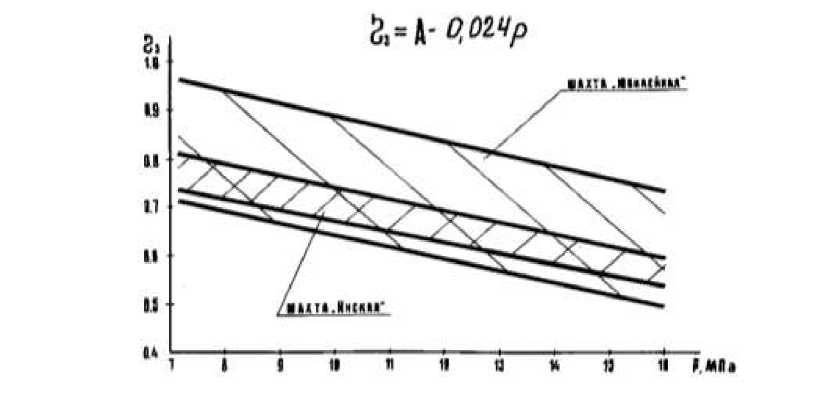
Рис. 2. Зависимость коэффициента использования по забою от давления.
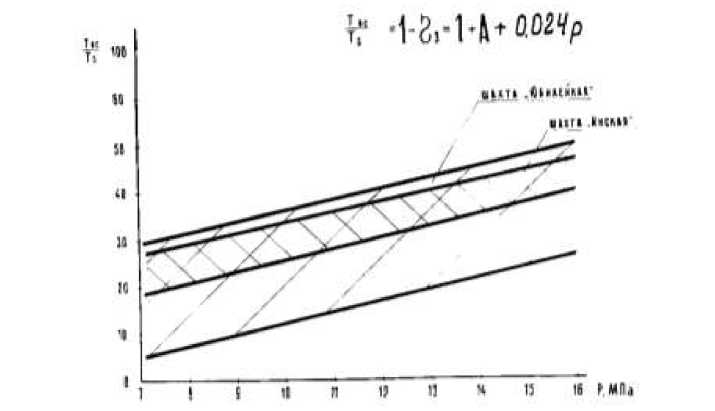
Рис. 3. Зависимость вспомогательных работ от давления.
Таким образом, помимо увеличения давления и расхода воды существенным резервом увеличения производительности гидромонитора является увеличение коэффициента использования, конкретно -уменьшение времени, затрачиваемого на вспомогательные операции. Исследователи [1, 5, 10, 11, 12] выделяли следующие операции при гидроотбойке: Зарубка; Отбойка; Выгрузка угля из заводки (смыв); Разбучивание; Разбивка негабаритов; Перепуск пульпы; Осмотр забоя; Оконтуривание выработки; Перепуск порода; Недобычные и ремонтные операции, не требующие отключения гидромонитора; Переключения воды.
Первые три операции вводят во время Тв и определяют производительность по выемке, последние - в Твс, а все вместе составляют время Тз и определяют производительность по забою.
Задача повышения производительности за счет повышения коэффициента использования может быть решена следующие путями: ликвидация некоторых вспомогательных операций; уменьшение времени, затрачиваемого на одну или несколько вспомогательных операций;
совмещение каких-либо вспомогательных операций по времени с основным процессом отбойки [9].
Остановимся более подробно на операциях составляющих гидроотбойку.
Разбучивание. Причиной, необходимости разбучивание желобов или почвы штрека с остановкой процесса выемки, но без прекращения подачи воды в забой, является появлением в желобах, находящихся сзади гидромонитора (по ходу движения пульпы), или на почве выработки крупных кусков угля. При этом гидродинамической силы безнапорно движущейся воды недостаточно для появления сдвигающей уголь и породу силы. Выход негабаритов, а также переизмельченного угля существенным образом зависит от управления движением струи по забою [13]. При больших расстояниях между врубовыми щелями вероятность выхода негабаритов увеличивается, при .малых увеличивается выход переизмельчённого угля. Применение программных устройств уменьшает вероятность выхода негабаритов и увеличивает производительность гидромонитора на 25 - 50 % [14].
Уголь в заходке в период отбойки верхней её части скапливается на почве в размерах, обусловленных углом естественного откоса. При этом присутствие в отбитой массе негабаритов способствует скопление большей массы угля, что может сопровождаться забучиванием гидромонитора, как негабаритами, так и массой мелкого угля, подплывающего к гидромонитору, одновременно с негабаритами.
Пути для уменьшения или ликвидации затрат времени на дробление негабаритов следующее: дробление негабаритов одновременно с выемкой угля, при этом механизм дробления должен быть расположен перед гидромонитором; программное управление с корректировкой программы движения струи по забою, желательно с обратной связью от забоя [15]; выгрузка угля из забоя, предотвращение скапливания угля в заходке за счет инициирования постоянного движения пульпы из заходки.
Перепуск пульпы. Перепуск пульпы сбоку от гидромонитора в транспортную систему производится вручную. Процесс состоит помимо разбивки негабаритов вручную из разборки мелкого угля, скопившегося у препятствия - гидромонитора, т.е. гидромониторщик вынужден помимо дробления затрачивать время на выпуск мелкого угля, который обладает хорошей способностью к гидротранспорту.
Пути для уменьшения или ликвидации затрат времени на перепуск пульпы следующие: проведение выработок под углом больше, чем 3 - 5°, принятых в существующих системах с расположением гидромонитора, поднятым над почвой; лассификация угля на транспортируемый (который сразу же перепускается в транспортную систему) и негабариты, которые подвергаются дроблению; подъем агрегата над почвой выработки для уменьшения возможности забучивания.
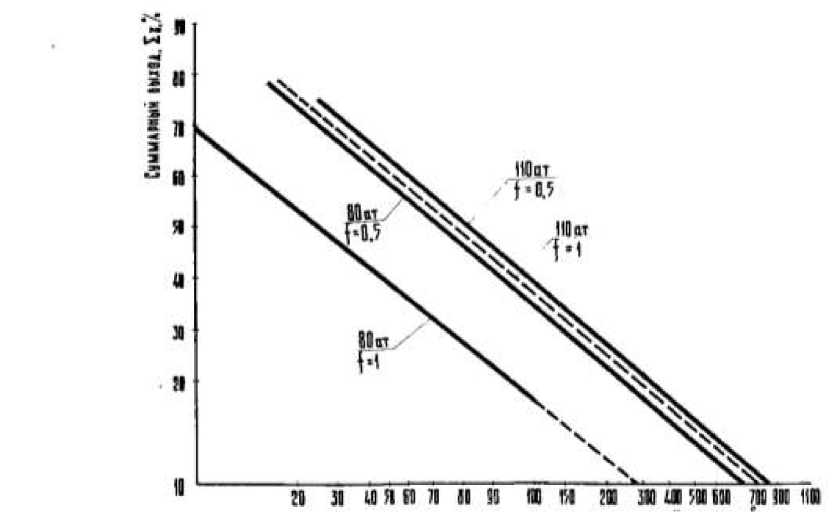
Рис.4. Гранулометрический состав угля при гидроотбойке.
Осмотр забоя. Осмотр забоя производится постоянно и является важной и необходимой операцией. Четкая информация о состоянии забоя, качестве отбойки, подвигании забоя уменьшит потери, предотвратит выпуск породы, предотвратит несвоевременное обрушение.
Уменьшение времени на осмотр или полная его ликвидация возможна при: использовании системы обратной связи между грудью забоя и гидромонитором; степени применения программного управления движением струи, так как в этом случае с большей точностью (по сравнению с ручным управлением) гидромониторщик знает о месте нахождения струи.
Оконтуривание выработки. Процесс оконтуривания можно в значительной мере уменьшить за счет: оконтуривание механическим органом до подачи воды в забой; использования обратной связи от забоя.
Перепуск породы. Перепуск породы, увеличивающей зольность угля, является нежелательной операцией. Сократить до минимума его можно за счет программного управления стволом и обратной связи от забоя.
Предотвращение забучивания породой выемочной печи и гидромонитора возможно также за счет увеличения угла наклона выработок.
Недобычные и ремонтные операции, не требующие отключения гидромонитора, как исследовалось paнеe [5, 11], можно уменьшить за счет повышения надежности оборудования, своевременного проведения планово-предупредительных ремонтов, правильной организации работы, внедрение приборов учета угля.
Значительным резервом увеличения производительности гидромонитора является уменьшение времени, затрачиваемого на выгрузку угля, т.е. повышение производительности по выемке. В приведенных выше исследованиях, составленных на основе хронометражных наблюдений, 107
процесс выгрузки (смыва) отдельно не выделялся. Принималось, что [5]
производительность гидромонитора по выемке оценивает потенциальные возможности технологии. Однако основной показатель гидроотбойки -массовое отношение угля в гидросмеси при этом ниже требуемой в течение таких операций, как зарубка и отбойка и, наоборот, выше в течение операции "смыв", что способствует забучиванию гидромонитора, снижению массового отношения транспортной системе и появлению такой операции, как перепуск пульпы. Более того неправильное ведение операций смыв может привести к полному забучиванию гидромонитора или даже аварии.
Таким образом для увеличения производительности гидромонитора необходима выгрузка угля из забоя, производимая не струей гидромонитора, а каким-либо другим органом одновременно с процессом гидравлической отбойки. Однако при этом производительность по забою может не приблизиться к технической производительности гидромонитора, т.к. операция выгрузки (смыва) может остаться.
Действительно, повышение производитель-ности по выемке скажется на повышении массового отношения угля к воде в гидросмеси - Ψ, которое не может увеличиваться безгранично. Для определенных горных условий существует предельное массовое отношение Ψпр, удовлетворяющее условиям безнапорного транспорта по конкретной транспортной системе гидрошахты. В пульпе
М тв
Мв , где Мтв - масса транспортируемого угля; Мв - масса транспортирующей воды причем в идеальном случае
М в Q t T ,
где tT - время, в течение которого расход воды Q транспортирует массу отбитого угля МТВ.
Производительность гидромонитора по забою
Пз Мтв ,
з где tв - время подачи воды
Тогда с учетом (1), (2), (14), (15), (16)
13К0Кl 1, tвtТ
При стремлении всю массу отбитого угля транспортировать с предельно возможным массовым отношением, получаемым в забое, т.е.
tвtT, получаем ограничение для коэффициента использования гидромонитора по забою лз
р
К 0 К l
Исходя из того, что коэффициент Кl, учитывающий рабочую длину струи
К К 1 Р К 2
Кl 12, dН
где d Н - диаметр насадки, тогда
d
" з КзР Н КН ,
Таким образом, повышение коэффициента использования гидромонитора по забою ограничивается диаметром насадки, т.е. необходимым расходом воды, или, для данных горно-геологических условий, существует определенное оптимальное давление воды (при соответствующем расходе).
Технологические требования к гидромониторной установке.
Помимо изложенных выше требований на создание гидромониторной установки накладываются требования, обусловленные условиями её применения в существующих шахтах и для конкретных систем разработок.
Размеры агрегата. Размеры подготовительных выработок, применяемых в настоящее время на гидрошахтах (ширина не более 2,5 м), клети, удобство маневрирования требуют от агрегата ширины при транспорте не более 1400 мм. Расширение возможностей применения агрегата с точки зрения мощностей пластов требуют высоты не более 1500 мм.
Подвижность агрегата. Применяемые гидромониторы во время гидроотбойки не имеют возможности передвигаться. По окончании гидроотбойки передвижение гидромонитора возможно только после разрешения диспетчером на отключение воды (закрытие задвижки), причем в этот период продолжается бесполезный сброс высоконапорной воды. Посла отключения следуют производимые вручную работы по отсоединению гидромонитора, разборки части става, передвижки гидромонитора, подключения его, уборки става и т.д. Эти работы повторяются после отработки каждой заходки. Применение самоходного гидромонитора позволит сократить только операцию по передвижка гидромонитора. Во время отработки заходки также возникает требование передвижения гидромонитора без отключения подачи высоконапорной воды, например, для осуществления контакта струи с забоем под углом 90°, при котором производительность гидромонитора выше (отработка стружками). Т.е. желательная минимальная подвижность гидромонитора во время подачи воды - 6 м (длина заходки).
Расположение агрегата. Появление в забое во время отбойки недробимых предметов (стоек, затяжек, кусков породы) возможно. Эти предметы могут являться причиной забучивания. Целесообразно во время движения пульпы, имея в виду, что дробилка находится перед машиной, поднять машину над почвой выработки и дать возможность не дробимым предметам пройти в транспортную систему шахты. Очевидно, что величина подъема машины должна быть близка к классификационной щели. Из опыта работы известно, что куски размером 200-250 мм транспортируются удовлетворительно. Таким образом, эту величину можно определить как высоту поднятия машины и классификационную щель.
Инициирование движения. Куски угля и недробимых - предметов имеют неправильную форму. В зоне под машиной при повороте куска может произойти заклинивание, сопровождающееся забучиванием. Целесообразно инициировать движение пульпы в стесненном пространстве. Такими приемами могут быть установка струй, направленных в сторону движения пульпы, или движение механических элементов, например, перемещения подвижных частей ходовой тележки.
Защита от перегрузок. Поскольку выход гидросмеси из заходки и привод её к дробилке не равномерен, поскольку к дробилке могут подойти недробимые предметы (деревянная стойка, анкер, кусок породы), то механизм дробления должен быть защищен от перегрузки, возможной поломки. Такая возможность может быть осуществлена реверсированием ротора дробилки, кратковременным увеличением классификационной щели, эвакуацией недробимых предметов в сторону, перпендикулярную движению потока пульпы.
Применение гидромониторного агрегата в технологических системах.
В соответствии с рекомендациями по технологии очистных работ на пологих и наклонных пластах гидрошахт [16] гидромониторный агрегат может работать в существующих системах разработки.
Система разработки длинными диагональными столбами с выемкой односторонними заходками (рис. 5).
Сущность системы заключается в том, что выемку угля осуществляют из выемочных столбов, расположенных диагонально к линии простирания пласта, а очистные работы сосредотачивают в 1-2 и более выемочных столбов крыла яруса (этажа). Выемочные столбы образуют посредством проведения между этажными (ярусными) аккомулирующим и вентиляционным штреками нарезных выработок ложной формы поперечного сечения, которые для обеспечения запасного выхода, и проветривания очистных забоев соединяют между собой стойками, предусмотренными ПБ.
Выемку угля производят односторонними заходками, размеры которых и других элементов системы разработки зависят от горногеологических, горнотехнических и организационных факторов. Наибольшеая диагональ заходки ограничивается рабочей длиной струи, т.е. 15-20 м.
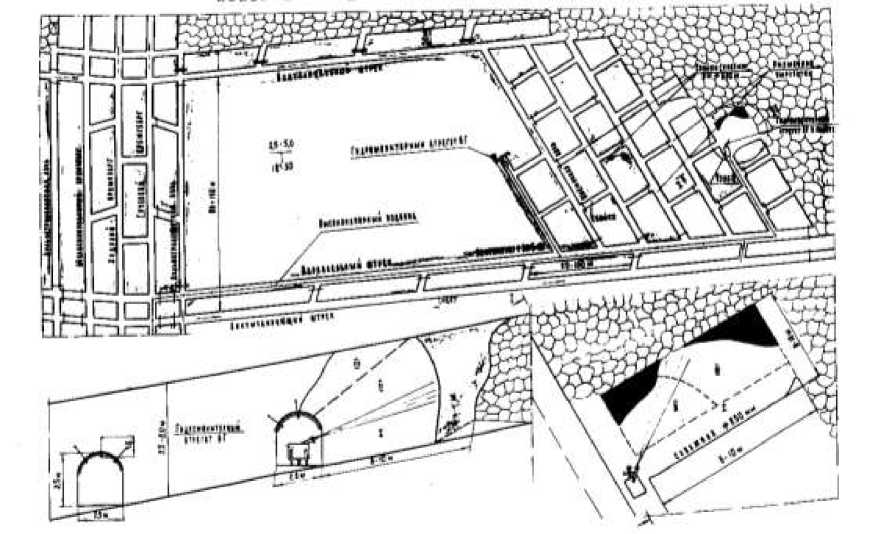
Рис. 5. Длинные столбы по простиранию с гидравлической выемкой диагональных полос угля односторонними заходками.
Очистные и нарезные работы могут выполнятся гидромониторным агрегатом. Погашение между ярусных целиков угля осуществляется одновременно с очистной выемкой заходок в выемочных столбах.
Очистные забои эксплуатируют без крепление, нарезные - с креплением легкого вида или без него. Проветривание очистных забоев -за счет общешахтной депрессии, нарезных - с применением ВМП.
Система разработки длинными диагональными столбами с выемкой двусторонними заходками (рис. 6).
Сущность систем разработки заключается в том, что гидромониторную выемку угля осуществляют двусторонними заходками из длинных диагонально расположенных выемочных печей, проводимых от параллельного или аккумулирующего штрека до вентиляционного.
Выемочные печи сбивают между собой сбойками через расстояние, равное одной передвижке гидромониторного агрегата.
Выемку угля осуществляет двумя гидромониторными агрегатами. Один агрегат осуществляет выемку, другой, находящийся в нижней выработке, в период выемки работает в качестве дробилки. Вода подводится только к одному агрегату. В первую очередь извлекают столб со стороны нетронутого массива, расширяют сбойку, по которой осуществляют транспорт гидросмеси, что значительно повышают безопасность ведения работ в очистном забое.
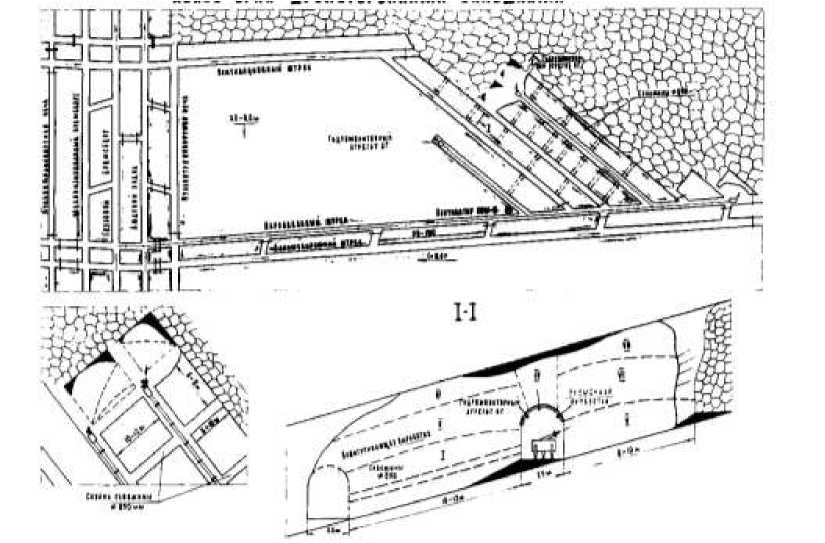
Рис. 6. Длинные столбы по простиранию с гидравлической выемкой диагональных полос угля двухсторонними заходками.
Нарезные выработки проводят теми же агрегатами. Форма нарезных выработок может быть различной: арочной, прямоугольной, трапециевидной и др. Крепление нарезных выработок можно осуществлять всеми известными видами крепей, но предпочтительнее анкерная, в том числе из полимерных материалов.
Проветривание очистных забоев осуществляет за счет общешахтной депрессии, а нарезных - вентиляторами устного проветривания.
Отработку междуэтажных целиков осуществляют по мере отработки выемочных столбов теми же агрегатами, которые ведут очистную выемку угля в столбах.
Система разработки длинными столбами по падению с двусторонний выемкой столбов (рис. 7).
Сущность системы заключается в том, что выемку угля осуществляют двусторонними заходками из выемочных столбов, расположенных по падению пласта между параллельными или аккумулирующими и вентиляционными штреками. Столбы оконтуривают выемочными печами, расстояние между которыми определяется главным образом эффективной длиной гидромониторной струи. Выемочные печи сбивают между собой сбойками, предназначенными, для проветривания, перемещения материалов и оборудования, а также служащих запасными выводами.
В качестве выемочных средств используются гидромониторные агрегаты АГ. При отработке столбов гидромониторным агрегатом с одной позиции производят выемку заходки по обе стороны от печи, причем в начале со стороны нетронутого массива угля, а затем со стороны обрушенного пространства, что позволяет максимально долго сохранять горную выработку.
Нарезные выработки могут проводиться таким же гидромониторным агрегатом.
Крепление горных выработок можно производить всеми известными типами крепи, но предпочтительнее анкерная крепь, в том числе из полимерных материалов.
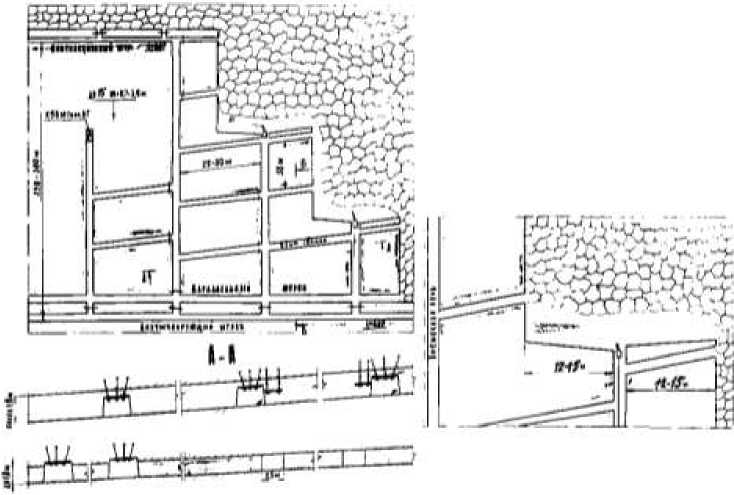
Рис. 7. Технологическая схема очистной выемки угля двусторонними заходками.
Следовательно, гидромониторный агрегат должен обеспечивать высоко-производительную отбойку угля с массовым отношением угля к воде в гидросмеси, соответствующим гидротранспорту гидросмеси по почве выработок или по желобам, соответстввнно1:3 или 1:2.
Гидромониторный агрегат должен обеспечивать выгрузку угля из забоя. Максимально возможные затраты по времени и по энергии должны быть возложены не на основную струю, а на вспомогательный орган -например, механический орган или дополнительную струю. При нисходящей отработки заходки выгрузка может: производиться за счет гравитационных сил.
Должна обеспечиваться классификация угля на уголь, который можно сразу же погружать в транспортную систему (класс – 200 - 250 мм), и уголь, который необходимо подвергать дроблению перед погрузкой в транспортную систему.
Гидромониторный агрегат должен обеспечивать Дробление угля (класса – 200 - 250 мм).
Гидромониторный агрегат должен обеспечивать погрузку угля (гидросмесь) в транспортную систему. Погрузка должна осуществляться и инициироваться на трассе движения близкой к дробилке или, при отсутствии таковой, к гидромонитору. Узлы гидромониторного агрегата должны быть установлены на ходовой тележке. Рассматривались два вида ходовых тележек: ходовая тележка на гусеничном ходу и родовая тележка на шнековом (роторно-винтовом) ходу. В связи с отсутствием какого-либо опыта работы шнекового хода в условиях гидрошахт, а также невозможностью использования серийных тележек или их узлов был принят вариант использования ходовой тележке на гусеничном году комбайна К56-МГ.
Рассматривалось два варианта использования тележки с точки зрения привода: серийно применяемая - с электроприводом и та же тележка с заменой электропривода на гидропривод. Применение гидропривода принесет следующие положительные качества: уменьшение массы ориентировочно на 1000 кг, искровзрывобезопасность, освобождение пространства для размещения аппаратуры автоматики, улучшение видимости работающего гидромонитора, повышение надежности (нет причины отказов электрооборудования из-за попадания влаги). В связи с недостаточной разработкой гидропривода и низшей стадией её выполнения принимается вариант с электроприводом.
Гидромониторный агрегат должен быть самоходным не только при передвижении от заходки к заходке когда вода не подается, но, желательно, в процессе отработки заводки, т.е. в пределах 6 - 8 м. Принципиально желательно решение задачи по обеспечению самоходности за максимально возможное время подачи воды, т.е. на всю длину выемочной печи. В настоящее время такие решения не опробованы в шахте. Ведется работа по обеспечению эффективного передвижения в пределах одной заходки.
Для обеспечения высокопроизводительной гидроотбойки принимается гидромонитор с рабочим давлением 16МПа, подачей воды 0,1 м3/с. Так как заданные габариты агрегата по высоте (1500 мм) серийный гидромонитор не обеспечивает, в конструкцию гидромонитора необходимо внести ряд изменений кардинально изменяющих стояк с уменьшением по высоте до размеров, близкие к диаметру ствола.
Для обеспечения обработки угля в нижележащих заходках гидромонитор должен иметь угол качения вниз 30-45° и перемещаться на один из бортов агрегата. Предпочтительным является его авангардное выдвижение для приближения точки качания к дробилке.
Гидромонитор должен быть оборудован системой программного управления с возможностью корректировки программы. В настоящее время на стадии подготовки к серийному производству находятся две таких системы: пневмогидравлическая система управления самоходным гидромонитором 12ГП-2 и электрогидравлическая система гидромонитором с импульсным повысителем давления ГПИ. В агрегате может быть применена, как одна, так и другая.
Обеспечение выгрузки угля из забоя предлагалось производить несколькими вариантами: расположением в забое выгружающих шнеков, труб с насадками, подающими воду по ходу движения пульпы, стрела комбайна с коронкой своим вращением препятствующим застою пульпы в заходке, авангардным выдвижением дробилки, уменьшающим скопление отбитого угля, обычно до попадания в него струи расположенного под углом естественного откоса.
Принято целесообразным использовать вариант со - стрелой комбайна. Применение стрелы комбайна расширяет возможности гидромониторного агрегата. Агрегат может сам нарезать выемочные печи, оконтуривать выработки. При расположении его в параллельной выемочной печи в системе с выемкой угля двухсторонними заводками он может принимать на себя пульпу, работая как дробильный агрегат. Универсальность агрегата позволит не использовать другие машины.
Классификация угля обеспечивается установкой дробилки над почвой выработки на требуемой высоте. Вращение ротора дробилки обеспечивает беспрепятственное, прохождение мелкого угля, в то время как крупный уголь будет подвергаться дроблению. В случае возможного забучивания или попадания недробимых предметов дробилка должна подниматься или реверсироваться. С тем, чтобы раздробленный уголь не остановился в зоне за дробилкой, машина должна подыматься на аутригерах, увеличивая клиренс на 150 - 250 мм.
Наиболее целесообразным для осуществления дробления использовать валковую зубчатую дробилку. Изучение известных дробилок, применяемых для дробления угля [17, 18] с точки зрения затрат энергии на тонну дробимого угля показало, что валковая зубчатая дробилка однороторная или двухроторная имеет наименьшие затраты энергии. Такие дробилки применяются и в шахтах для аналогичных целей [19, 20].
Дробление угля будет наиболее эффективным тогда, когда вся пульпа подойдет к дробилке. Одним из решений увеличения фронта дробления при обеспечении минимальных размеров дробилки, в транспортном положении является осуществление разворота оси дробилки навстречу потоку и телескопическая раздвижка оси дробилки.
При этом возможно некоторое качание дробилки в горизонтальной плоскости для дополнительного разбучивания откоса угля.
Для погрузки угля в транспортную систему предложено [21] использовать гусеничную тележку в поднятом на аутригерах положении. Движущиеся в этот период гусеницы инициируют движение пульпы, способствуют устранению забучивания в пространстве под тележкой. Так как пространство между бортом выработки и агрегатом будет заилено, пульпа основной своей массой будет двигаться под тележкой, сохраняя оптимальное массовое отношение угля к воде. В качестве дополнительной меры эвакуации угля из под машины предлагается под дном тележки расположить трубу с насадками, направленными по ходу движения пульпы. Струи дополнительно будут инициировать движение пульпы, способствовать разбучиванию угля.
Следовательно в статье осуществлено технологическое обоснование необходимости создания подвижного гидромониторного агрегата.
Список литературы Применение подвижных гидромониторных агрегатов для отработки крутых угольных пластов
- Временная инструкция расчета производительности гидромониторной выемки угля в очистных забоях для действующих и проектируемых гидрошахт и гидроучастков Кузбасса. -Новокузнецк, 1983. -38 с.
- Цяпко Н.Ф. Развитие теории и техники гидроотбойки угля.//Гидромеханизация и гидротранспорт на угольных шахтах. -Вып. 36. Труды ВНИИГидроугля, 1975.
- Емельянов Ф.К., Форышев П.И., Никитин А.Н., Пучковский В.В. Результаты приемочных испытаний самоходного гидромонитора с дистанционно изменяемой программой 12ГП-2.//Гидравлическая добыча угля. -Вып. № 39. Труды ВНИИГидроугля. 1977.
- Киселев А.В., Хазов В.М., Плетнев О.Н., Сальников В.Р., Гефт Ю.Б. Результаты исследовательских эксплуатационных испытаний высоконапорной гидроотбойки струями давлением до 14 МПа в условиях пластов крутого падения.//Гидравлическая добыча угля.-Труды ВНИИГидроугля. -Вып. № 39, 1977.
- Комплексное исследование всех звеньев технологической цепи гидрошахты "Грамотеинская" № 3-4 с целью достижения уровня производительности труда 180-200 тонн на рабочего в месяц./Отчет по теме № 73. Инв.№ 1912. -Фонды ВНИИГидроугля, 1968.
- Гефт Ю.Б., Сорокин А.С. Определение коэффициента использования гидромонитора.//Теория и опыт гидравлической отбойки угля.-Труды ВНИИГидроугля. -Сборник № 6, 1969.
- Гефт Ю.Б., Плетнев О.Н., Хазов В.М., Цяпко Н.Ф. К вопросу вявления резервов производительности гидромонитора и энергоемкости гидроотбойки.//Вопросы гидравлической добычи угля. -Труды ВНИИГидроугля. -Вып. № 13 (дополнительный), 1968.
- Киселев А.В., Хазов В.М., Плетнев О.Н., Сальников В.Р., Гефт Ю.Б. Результаты исследовательских эксплуатационных испытаний высоконапорной гидроотбойки струями давлением до 14 МПа в условиях пластов крутого падения.//Гидравлическая добыча угля. -Труды ВНИИГидроугля -Вып. 39, 1977.
- Адамович О.Е., Жамилов Р.Н., Форышев П.И. К вопросу издания механизма дробления негабаритов при гидравлической выемке угля.//Гидромеханизация и гидротранспорт на угольных шахтах. -Научные труды. ВНИИГидроуголь. -Вып. 44, 1979.
- Исследование резервов гидрошахты "Байдаевская-Северная" № 1 с использованием данных хронометражных наблюдений 24-29 октября 1966 г. по распределению и потреблению высоконапорной воды./Отчет. Инв. № 1219. -Фонды ВНИИГидроугля, 1966.
- Исследование технологического процесса очистной выемки угля на шахте "Грамотеинская" № 3-4./Отчет по теме 73-П. Инв. № 1880. -Фонды ВНИИГидроугля, 1968.
- Пооперационные исследования технологического процесса во время проведения промышленного эксперимента эксплуатации блока очистных работ с показателями, характеризующими гидрошахту нового технико-экономического уровня./Отчет. -Фонды ВНИИгидроугля, 1974.
- Адамович О.Е. Зависимость производительности гидромонитора от схемы обработки забоя.//Гидравлическая добыча угля. -Труды ВНИИгидроуголь. -Вып.40, 1977.
- Гефт Ю.Б., Мясников А.Б., Плетнев О.H., Хазов В.М. Оценка влияния некоторых технологических операций на производительность гидромонитора.//Теория и опыт гидравлической отбойки угля. Вопросы гидравлической добычи угля. -Труды ВНИИгидроугля -Вып. № 6, 1969.
- Германская Г.В., Титов В.М. О возможности использования лазерного дальномера для обеспечения обратной связи между грудью забоя и гидромонитором. -Труды ВНИИгидроугля. -Вып.44, 1979.
- Технология очистных работ на пологих и наклонных пластах гидрошахт (рекомендации). Новокузнецк: ВНИИгидроуголь, 1982.
- Углеобогатительное оборудование. Каталог-справочник. -М:,1970.
- Оборудование для обогащения угля. Справочное пособие. Под общей редакцией Б.Ф. Братченко. -М.: Недра, 1979.
- Дэвид Парке, Артур Гриши. Подземная гидравлическая добыча угля. Перевод № 1011. -ВНИИгидроутоль. -№ 5, 1975. -61 с.
- Адамович О.Е., Жамилов Р.Н. Гидромониторный агрегат. Авт. свид. № 665085.
- Рощин В.Д., Пахтусов Г.А., Пахтусов Ю.Г., Чижов П.А. Промышленные испытания комбайна "Урал-38".//Горные машины и автоматика. -№ 6, 1973.
- Мельник В.В. Разработка технологических решений скважинной гидравлической добычи угля. Дис. докт. техн. наук. -М.: МГГУ, 2005. -397 с.
- Мельник В.В. Обоснование параметров технологии очистной выемки угля агрегатами на гидрошахтах. Автореф. дис. канд. техн. наук. -М: МГИ, 1987. -18 с.