Применение разрушающих методов испытаний для контроля качества строительных конструкций
Автор: Коротин А.И., Лазарев А.Л., Святкина Г.Н., Танякин И.А.
Журнал: Огарёв-online @ogarev-online
Статья в выпуске: 11 т.5, 2017 года.
Бесплатный доступ
Приведены основные принципы контроля качества соединений строительных конструкций в современных условиях. Представлены реальные результаты работ по разрушающему контролю качества ответственных конструкций.
Изделий и конструкций, контроль качества, методы контроля строительных материалов, разрушающие испытания, структура материала
Короткий адрес: https://sciup.org/147249352
IDR: 147249352
Текст научной статьи Применение разрушающих методов испытаний для контроля качества строительных конструкций
Надежность и долговечность строительных конструкций не возможна без обеспечения надежной совместной работы их элементов, без потери прочности, жесткости, устойчивости и пространственной геометрической их неизменности. Выполнение узлов конструкций зачастую обеспечивается объединением в одно целое материала конструкции и соединительного элемента. Для обеспечения надежности конструкций и узлов должны применяться методы контроля и испытания материала конструкции и соединительных элементов узлов. Качество материала определяется состоянием его структурных составляющих как на микро, так и на макроуровнях.
Структура материала определяется его внутренним строением. Внутреннее строение строительных материалов определяется пространственным расположением частиц разной степени дисперсности (измельченности) с совокупностью устойчивых взаимных связей и порядком сцепления их между собой. Кроме того, в понятие структуры входит расположение пор, капилляров, поверхностей раздела фаз, микротрещин и других структурных элементов.
Качество строительных материалов определяется совокупностью свойств, удовлетворяющих определенные потребности в соответствии с назначением конкретного строительного материала. Уровень качества определяется соответствующими показателями, представляющими собой количественную характеристику одного или нескольких свойств 1
конкретных строительных материалов, которые определяют их качество применительно к конкретным условиям изготовления и эксплуатации. Показатели по количеству характеризуемых параметров качества подразделяются на единичные и комплексные. Единичный показатель качества характеризуется только одним свойством (например, прочность или твердость). Комплексный показатель характеризуется сразу несколькими значимыми свойствами материала. При этом изделие или конструкция считается качественной только в том случае, если весь комплекс оцениваемых свойств удовлетворяет установленным требованиям качества. Характерными комплексными показателями качества материала являются химический состав, физико-механические свойства материала, его микро- и макроструктура. Комплексные показатели качества устанавливаются нормативными документами [1].
Свойства строительных материалов, определяющие их качество, зависят от структуры материалов, которая в свою очередь, зависит от их химического состава. Поэтому при контроле качества строительных материалов и изделий определяют свойства и состав, а также оценивают их структуру.
Существуют различные методы изучения структуры материалов. Макроструктура, в целом, характеризуется их фазовым составом. Исследование макроструктуры выполняют, как правило, органолептическими методами. При визуальном осмотре выявляют зоны и участки, различающиеся пористостью, окраской, зерновым составом и другими особенностями, а также различные дефекты макроструктуры. Анализ и исследование микроструктуры производится с помощью разнообразной приборной базы. Выделяют три типа микроструктур: кристаллическую, аморфную и смешанную.
Применяемые методы контроля качества строительных материалов в современных условиях подразделяются на разрушающие и неразрушающие [2]. По стадиям определения качества строительных материалов и конструкций различают контроль предварительный, промежуточный и окончательный. При предварительном контроле оценивается качество исходных компонентов, при промежуточном — соблюдение установленного технологического процесса производства или монтажа конструкций. Окончательный контроль определяет качество конечного продукта, которым может быть строительный материал, изделие, конструкция или здание (сооружение) и соответствие их определенным стандартам. Изделия и конструкции, имеющие дефекты и отклонения от стандартов считаются браком [3].
В работе выполнен комплексный контроль качества сварных соединений газопровода, выполненного автоматической сваркой на объекте «Южный коридор» из труб класса прочности К60 диаметром 1420 мм и толщиной стенки 21,6 мм. Контроль включал в себя все 2
три этапа: предварительный (контроль сварочных материалов), промежуточный (контроль процесса сварки) и окончательный (разрушающий контроль сварных соединений) [4]. Для проверки качества выполнения шва и обеспечения внутренней геометрии слоев выполнялся контроля сварного соединения по макрошлифам.
Для получения образцов для испытаний из каждого пятисотого стыка вырезают элемент для получения макрошлифа (рис. 1). Осуществляется шлифование и травление поверхности для проведения испытаний. Заключение по результатам испытаний сводится в типовую таблицу (см. табл. 1).
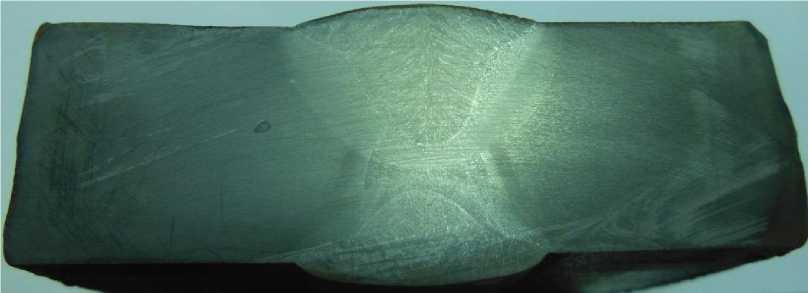
Рис. 1. Макрошлиф для исследования геометрических параметров сварного соединения.
Таблица 1
Протокол оценки геометрических параметров сварного шва и сплошности соединения по макрошлифам
Номер соединения |
№КСС-13, стык №Б-800 |
||||||
Основной металл |
Труба Ø1420x21,6 мм из стали класса прочности К60 |
||||||
Сварочный материал |
OK Autrod 12.24, Ø3,0 мм + флюс OK Flux 10.71 |
||||||
Методика испытаний |
СТО Газпром 2-2.2-115-2007 |
||||||
Тип образца |
Макрошлиф |
||||||
Номер образца |
Геометрические параметры шва |
||||||
a – перекрытие слоев шва. мм |
с – смещение осей слоев от условной оси , мм |
h H – глубина проплавления первого наружного слоя шва, мм |
h в – глубина проплавления внутреннего слоя шва, мм |
В н – ширина облицовочного слоя шва, мм |
В в – ширина внутреннего слоя шва, мм |
||
КСС-13 |
3,7 |
1,0 |
12,7 |
10,3 |
21,7 |
21,8 |
|
Требования |
≥3,0 |
1,0 |
>12,3 |
≤12,3 |
20,0±3,0 |
20,0±3,0 |
|
Заключение: по результатам проведенных измерений геометрических размеров шва стыковое сварное соединение соответствует требованиям СТО Газпром 2-2.2-115-2007. Нормируемые параметры находятся в пределах допуска, регламентированного НД. Несплавлений, нор, шлаковых включений, выходящих на поверхность шлифа, не обнаружено. |
Интересным примером разрушающих испытаний болтовых соединений металлоконструкций является работа, выполненная авторами настоящей статьи, по испытанию болтов М27х140 класса прочности 10.9 в комплекте с гайками и шайбами производства ММК-МЕТИЗ. Исследование партии болтов включало следующие испытания [5; 6]: определение твердости; испытание болтов на разрыв на косой шайбе; определение коэффициента закручивания (болтокомплект).
Измерения твердости по методу Бринелля проведены на торце стержней болтов на твердомере Константа. Результаты представлены в таблице 2.
Результаты измерения твердости болтов
Таблица 2
Условный № болта |
Твердость (измерение в трех точках), НВ |
||
1 |
2 |
3 |
|
1 |
340 |
347 |
351 |
2 |
344 |
342 |
348 |
3 |
359 |
360 |
355 |
По результатам испытаний был сделан вывод, что исследованные болты М27х140 по твердости удовлетворяют требованиям, предъявляемым ГОСТ Р52643-2006 к высокопрочным болтам из стали 40Х класса прочности 10.9.
Определение коэффициента закручивания проводили на пяти болтокомплектах (болт М27х140, гайка М27, две шайбы) с применением предельного динамометрического ключа. Отсчет величины осевого усилия натяжения испытываемого болта производился по шкале измерительного прибора, отградуированного с ценой деления до 500 Нм. Испытания проводились по методике, изложенной в ГОСТ 52643- 2006 (приложение Е), с адаптацией под реальные условия испытаний и применяемое оборудование.
Перед проведением испытаний для снижения погрешности болты и гайки специальным образом обрабатывались. Первоначально производилась очистка от технологической смазки и загрязнений окунанием в емкость с бурлящим щелочным раствором при температуре не менее 90 °С на 10-15 мин. Затем смывка остатков щелочного раствора окунанием в емкость с бурлящей водой при температуре не менее 90°С на 10-15 мин и выдержка при температуре не ниже 20 °С до полного высыхания. Смазка производилась окунанием в емкость со смазочным составом из 80 % неэтилированного бензина по ГОСТ Р 51866 и 20% минерального масла при температуре состава 20°С.
Коэффициент закручивания определялся путем измерения фактического крутящего момента, приложенного к гайке, в момент достижения в теле болта нормативного усилия натяжения. Была изготовлена оригинальная испытательная установка, смонтированная на 4
разрывной машине EU 40. Фактический крутящий момент определялся комбинированным устройством на основе динамометра ДПУ-500-2 и динамометрического стрелочного ключа Tohnichi DBR4500N-S.
При проведении испытаний крутящий момент создавался закручиванием гайки со скоростью закручивания не более 10 об/мин. Коэффициент закручивания К определяют по формуле:
К = 1000 —
Nd где M – фактический крутящий момент, приложенный к гайке, создающий в теле болта нормативное усилие натяжения, Н·м; N – нормативное усилие натяжения болта; d – наружный диаметр резьбы болта, равный 27 мм.
Значения нормативных усилий натяжения для болтов различных классов прочности приведены в таблице Е.1 ГОСТ Р 52643-2006. Согласно указанной таблицы, для болтов М27 класса прочности 10.9 нормативное усилие натяжения болта равно 335000 Н.
Исследованные болтокомплекты имеют коэффициенты закручивания 0,168; 0,160; 0,160; 0,170; 0,165, среднее значение К3=0,16; крутящий момент 1520, 1450, 1450, 1540 и 1490 Нм, т.е. удовлетворяют требованиям ГОСТ Р 52643-2006 (0,14 < К< 0,17).
Определение прочности на разрыв на косой шайбе проводилось при испытании пяти болтов с применением косой шайбы, изготовленной в соответствии с положениями п.8.6 ГОСТ Р 52627-2006. Результаты испытаний представлены в таблице 3.
Результаты испытания болтов на разрыв на косой шайбе
Таблица 3
Условный № болта |
Начальная площадь поперечного сечения, мм2 |
Нагрузка разрушающая, Н |
Прочность на разрыв, Н/мм2 |
Место разрушения |
Результат испытания (соответствует/не соответствует требованиям ГОСТ Р 52627-2006 |
1 |
426,2 |
467000 |
1096 |
Стержень болта по резьбе |
Соответствует |
2 |
426,2 |
490000 |
1150 |
Соответствует |
|
3 |
426,2 |
490000 |
1150 |
Соответствует |
|
4 |
426,2 |
481600 |
1130 |
Соответствует |
|
5 |
426,2 |
490100 |
1150 |
Соответствует |
Результаты эксперимента наглядно демонстрируют актуальность проведения разрушающих испытаний образцов-спутников элементов и узлов строительных конструкций, например, для отработки технологии изготовления конструкций и узлов. Подобные методы испытаний дают четкую визуализацию работы элементов под эксплуатационными нагрузками. Кроме того, в работе показана необходимость адаптации методик к реальным условиям при проведении испытаний и применяемому испытательному оборудованию.
Список литературы Применение разрушающих методов испытаний для контроля качества строительных конструкций
- Корчагина О. А. Материаловедение: оценка качества строительных материалов. -Тамбов: Изд-во ГОУ ВПО ТГТУ, 2010. -96 с.
- Коротин А. И., Лазарев А. Л., Святкина Г. Н. Ультразвуковой контроль металлических конструкций: учебное пособие. -Саранск.: Изд-во Мордов. ун-та, 2015. -112 с.
- Коротин А. И., Лазарев А. Л., Святкина Г. Н. Применение УЗ методов контроля для оценки качества соединений металлических конструкций в современных //Огарев-online. Раздел «Технические науки». -2015. -№ 13. -Режим доступа: http://journal.mrsu.ru/arts/primenenie-ultrazvukovyx-metodov-kontrolya-dlya-ocenki-kachestva-soedinenij-metallicheskix-konstrukcij-v-sovremennyx-usloviyax. EDN: TZHRZV
- СТО Газпром 2-2.2-115-2007 Инструкция по сварке магистральных газопроводов с рабочим давлением до 9,8 МПа включительно.
- ГОСТ Р 52643-2006 Болты и гайки высокопрочные и шайбы для металлических конструкций. Общие технические условия.
- ГОСТ Р 52627-2006 (ИСО 898-1:1999) Болты, винты и шпильки. Механические свойства и методы испытаний.