Применение серебра (обзор)
Автор: Денисова Л.Т., Белоусова Н.В., Денисов В.М., Иванов В.В.
Журнал: Журнал Сибирского федерального университета. Серия: Техника и технологии @technologies-sfu
Статья в выпуске: 3 т.2, 2009 года.
Бесплатный доступ
Проведен обзор работ, посвященных применению, начиная с древних времен и до настоящего времени. Сделан анализ использования серебра в различных областях техники, биологии, медицины, в производстве ювелирных изделий. Отмечены особенности свойств и применения наносеребра.
Серебро, электроконтакты, припой, полупроводники, наносеребро, стекла, медицина, биология, ювелирное дело
Короткий адрес: https://sciup.org/146114500
IDR: 146114500
Текст научной статьи Применение серебра (обзор)
Серебро известно еще с древних времен и всегда играло достаточно большую роль в нашей жизни [1]. Лидийский царь Крез (561-546 гг. до н.э.), о несметных богатствах которого слагали легенды, впервые ввел золото и серебро как монетные металлы [2]. Широкое использование серебра связано, в первую очередь, с его химическими и физическими свойствами, красивым внешним видом. Серебро и его сплавы применяются в различных областях техники, биологии и медицины, производстве ювелирных изделий. На основе серебра созданы припои с уникальными эксплуатационными свойствами (пайка вакуумных приборов, керамических и композиционных материалов, соединений разнородных материалов, обладающих весьма различными коэффициентами теплопроводности). При этом чем выше требования к коррозионной стойкости паяного шва, тем с более высоким содержанием серебра применяются припои [3-5].
1. Традиционные применения серебра
Фотография
Почти все соединения серебра (Ag(I)) на свету разлагаются до свободного серебра и при этом окрашиваются в серый или черный цвет, что используется в фотографии [1]. Лишь в последнее время на изготовление кино- и фотоматериалов с созданием цифровой техники стало расходоваться меньшее количество серебра. Варианты переработки отходов такого производства рассмотрены в [6, 7].
Катализ
Серебро и его сплавы используются в качестве катализаторов. Катализаторы Ag/оксиды металлов эффективно восстанавливают NO в избытке кислорода. Установлена важная роль восстановителей в селективном каталитическом восстановлении NO (эффективность восстановления зависит от типа восстановителя) [8]. Известно, что алюмооксидный носитель не является индифферентным по отношению к нанесенным на него металлам (Pt, Pd, Ag), оказывая тем самым заметное влияние на их свойства и степень взаимодействия с поверхностью [9, 10]. Изучению особенностей взаимодействия в системе Ag-Al 2 O 3 посвящен ряд работ [11-13]. Данные по установлению взаимосвязи каталитической активности и концентрации кислотных центров поверхности серебряных катализаторов приведены в [9].
Использование серебра в электротехнике
Большое количество серебра идет на изготовление электроконтактных материалов для нужд электротехники и электроники [14, 15]. Они весьма разнообразны по назначению, области применения, характеру работы: скользящие и разрывные; контакты, предназначенные для вакуумных выключателей и для работы в газе (воздух, элегаз), в масле, для высоковольтной и низковольтной аппаратуры и т.п.
Разрывные электроконтакты низковольтной (до 1000 В) аппаратуры - основной потребитель серебра в этой области техники - изготавливают, как правило, из материалов с содержанием Ag около 80-90 %, в то время как в высоковольтных электроаппаратах используется медь.
Работоспособность и надежность электрических контактов в значительной степени определяется физическими и связанными с ними химическими процессами, имеющими место при их работе [16-33].
Одним из главных факторов, определяющих срок службы коммутационных аппаратов, является износ контактов, обусловленный переходным процессом при размыкании электрической цепи – дуговым разрядом. Считается обычно, что при размыкании тока более 0,5 А и напряжении более 15 – 20 В между контактами возникает электрическая дуга, вызывающая так называемую дуговую эрозию контактного материала. Прерывание меньших значений тока и напряжения сопровождается только небольшими искрами и может приводить к «мостиковой эрозии», характерной для слаботочных реле. При этом наблюдается перенос материала с одного электрода на другой с образованием кратеров и наростов в зависимости от полярности и материала контактов. Образованию дуги часто предшествует мостиковая стадия процесса. В момент размыкания цепи в точках контактирования локально выделяется тепло, металл плавится и между расходящимися поверхностями вытягивается жидкий мостик. Так как через него течет весь ток, он разогревается до температуры кипения металла и разбрызгивается, при этом часть металла вылетает за пределы межконтактного промежутка.
Оптимальным выбором материала электроконтактов можно в определенной степени влиять на процесс развития и гашения дугового разряда. Материал с высоким свойством дуго-гашения слабее подвержен дуговой эрозии. Наличие этого свойства – одно из требований к контактному материалу. Ряд других требований, с точки зрения ослабления воздействия дуговых разрядов на износ, также следует из изложенного: высокие тепло- и электропроводность. В условиях слабого теплоотвода катодное пятно может разогреваться за счет джоулева тепла – 251 – до высоких температур, обеспечивающих термоэмиссию электронов в катодный слой, снижая тем самым способность к восстановлению прочности дугового промежутка и затягивая время горения дуги.
В результате многократного повторения циклов замыкания-размыкания (В-О) вся поверхность контактов обрабатывается дугой. Это сопровождается высокотемпературными процессами взаимодействия твердого и жидкого металла с компонентами атмосферы и плазмой дуги с образованием оксидов и других плохопроводящих соединений. В результате на рабочих поверхностях образуется так называемый слой наработки толщиной до десятков и сотен микрометров, состоящий из продуктов окисления, застывших микрокапель металла, атмосферных частиц, пузырьков газа и т.п. Этот слой в дальнейшем оказывает определяющее влияние на контактное сопротивление в замкнутом состоянии и вообще на работоспособность контактной пары.
Условия работы электроконтактов в замкнутом состоянии определяются совокупностью теплофизических процессов в площадке их соприкосновения. Эта площадка представляет собой только кажущуюся контактную площадь. Истинный механический контакт поверхностей осуществляется на отдельных участках - контактных пятнах, площадь которых может состав -лять десятые и сотые доли процента от кажущейся площади соприкосновения.
От площади контактирования в значительной степени зависит весьма важная характеристика контактов - переходное сопротивление R K . Сложным образом на величину R K влияет температура. Рабочая температура контактных элементов (или ее превышение над температурой окружающей среды ∆ Т) нормируется [34].
Другие эффекты проявляются при длительном прохождении токов перегрузки. Результат – проплавление контактных площадок и их сваривание. Каждому материалу соответствует величина граничного тока сваривания [35]. При прохождении сквозь контакты токов, близких к критическим, все контакты в той или иной степени свариваются. Кроме того, существует «холодное сваривание» при длительной работе на номинальных токах. Поэтому свойство сваривания характеризуется также отрывным усилием приварившихся контактов F св .
Эрозионный износ и сваривание наблюдаются не только при размыкании цепи, но и при включении. В момент включения контакты упруго деформируются и коммутационное устройство из-за пружинящего эффекта на короткое время размыкается. Размыкания могут многократно (2-5 колебаний) повторяться, а амплитуда таких колебаний достигает 0,2 мм [36]. Это явление называют вибрацией или дребезгом контактов. Во время дребезга возникает короткая дуга и проявляются все эффекты, с ней связанные, в том числе и сваривание.
Рассмотренные физические явления и их следствия в виде действующих разрушающих факторов, которые имеют место при работе электрических контактов, позволяют сформулировать требования к материалу и его свойствам (электрофизическим, теплофизическим, механическим и химическим).
Разрушающие факторы: электрическая дуга, искра, прохождение номинального тока, токов перегрузки и короткого замыкания, динамические нагрузки различной природы и термические напряжения, коррозионное действие среды.
Результаты воздействия разрушающих факторов на материал контакта: плавление материала, испарение, разбрызгивание, перенос материала с контакта на контакт, пластическая де-– 252 – формация; образование трещин, отколов, раковин, кратеров, осаждение капелек из брызг и паров; сварка, холодная сварка, задиры, вырывы, выкрашивания; химическое взаимодействие с атмосферой, образование слоев наработки.
Физико-химические свойства контактного материала, снижающие отрицательное влияние воздействия разрушающих факторов:
-
• высокие температуры плавления Т пл и кипения Т кип , теплоты плавления Q^ и испарения Q исп , теплоемкость с р , теплопроводность λ ;
-
• низкая упругость паров, высокое поверхностное натяжение расплава;
-
• высокие электропроводность ϖ , работа выхода электрона А е , потенциал ионизации ϕ ;
-
• высокие прочность, усталостная прочность, ударная вязкость; оптимальная твердость;
-
• высокие коррозионная стойкость, летучесть продуктов коррозии и их электропроводность, оптимальные прочность поверхностных слоев и сила их связи с основой.
Концентрированное выражение все перечисленные физико-химические свойства электро-контактного материала находят в кратких формулировках основных служебных свойств электрического контакта:
-
• высокая электроэрозионная стойкость под воздействием дуги;
-
• низкое и стабильное переходное сопротивление при работе в коррозионно-активной атмосфере;
-
• низкая склонность к свариванию под действием дуги, тока, динамических и статических нагрузок;
-
• высокая механическая износостойкость.
Сопоставление всего комплекса требований к свойствам материала показывает их многообразие и противоречивость. Казалось бы, взаимоисключающие свойства, несовместимые в одном металле, удается объединить в композитах, псевдосплавах, которые получают методами порошковой металлургии [37]. Тем не менее ясно, что основой электроконтактного материала могут служить лишь благородные металлы и, в какой-то степени, медь, обладающие набором ключевых свойств.
К настоящему времени разработаны сотни электроконтактных материалов на основе благородных металлов и меди, но наибольшие объемы производства приходятся на электроконтакты с серебром. Причина этого понятна: серебро, кроме высоких тепло- и электропроводности, пластичности, имеет малое сродство к кислороду, а его оксиды Ag 2 O и AgO разлагаются уже при небольшом нагревании до 470 К [4, 38]. К тому же они имеют относительно малое удельное сопротивление – соответственно 1,0 и 0,012 Ом∙см при комнатной температуре [39, 40]. Вследствие этого серебро обеспечивает низкое переходное сопротивление контактной пары. При окислении поверхности контактные области стягивания тока нагреваются (вплоть до нескольких сотен градусов [41]), оксиды разлагаются и металлический контакт восстанавливается.
Материалы для электроконтактов на основе серебра используются как в виде чисто -го металла, его сплавов, так и гетерофазных композитов с металлами, оксидами, карбидами и т.п. Области применения отдельных композиций перечислены далее по тексту, а также приведены в таблицах, основанных на информации из ряда источников [4, 20-22, 25, 26, 30, 36-38, 42].
Серебро – слаботочные реле различного назначения, сигнальная аппаратура, контакты вспомогательных цепей, термостаты, бытовые приборы, управление флуоресцентными лампами, командоконтроллеры, нагреватели воды, светоустановочные аппараты; покрытия электроосаждением на контактные детали устройств радио- и электронной техники, работающих в бездуговом режиме.
Серебро-медь - реле, сигнальная аппаратура, светотехнические выключатели, радиоаппаратура.
Серебро-медь-никель – стенные бытовые выключатели, реле уличных сигналов, тепловые выключатели, преобразователи тока, выключатели связи, реле автоматики, выключатели и реле авиационные легконагруженные, электромагнитные счетчики, управление флюоресцентными лампами, автомобильные и железнодорожные сигнальные реле, регуляторы освещения.
Серебро-кадмий - реле, бензино- и маслоизмерители, контрольные реле легко- и среднена-груженные авиационного оборудования, выключатели перегрузки и термостаты холодильников, уличные сигналы, тепловые выключатели, стартеры.
Серебро-кадмий-никель-железо – реле-регуляторы напряжения, автоприборы.
Серебро-кадмий-никель, серебро-кадмий-индий – реле в диапазоне токов 0-30 А.
Серебро-палладий - сигнальная аппаратура, телефонные реле и номеронабиратели, регуляторы напряжения, управление флюоресцентными лампами, бензино- и маслоизмерители, защитные устройства электродвигателей, выключатели холодильников и термостатов, контактные кольца.
Серебро-платина – радиоаппаратура, приборы автоматики и радио, радиовибраторы и устройства питания от сети радиоаппаратуры, электромагнитные счетчики.
Серебро-магний-никель, серебро-золото-магний-никель, серебро-магний-цирконий, серебро-магний-никель-цирконий, серебро-палладий-магний - заменители контактов из сплавов платина-иридий, золото-палладий-платина, золото-никель, золото-платина в малогабаритных и миниатюрных электромагнитных реле радиоэлектроники.
Серебро-оксид циркония – микровыключатели, реле на токи в диапазоне 0,01-100 А.
Существенное улучшение электроконтактных свойств серебра путем его легирования невозможно, поскольку достигаемое при этом улучшение твердости, износостойкости обязательно сопровождается снижением температуры плавления, тепло- и электропроводности. Композиционные материалы сочетают свойства отдельных компонентов без их значительного снижения (электро- и теплопроводность, температура плавления) и имеют, как правило, прочное каркасное строение.
Поэтому основные типы применяемых в настоящее время электроконтактных систем являются гетерогенными композиционными материалами с компонентами, ограниченно растворимыми в твердой фазе. Наибольшие объемы промышленного выпуска электроконтактной продукции приходятся на системы: Ag-CdO, Ag-SnO 2 , Ag-Ni, Ag-W(WC), Ag-C [4, 26, 36-38, 41]. Типичные примеры составов и качественная оценка служебных свойств [43] приведены в табл. 1. Типичные примеры применения материалов к различным типам аппаратов сведены в табл. 2.
Обозначения в таблице: Св - стойкость против сваривания, Кс - контактное сопротивление, Э - эрозионная стойкость, Пд - подвижность дуги, Дг - дугогасящие свойства; о - отличное, у – удовлетворительное, п – плохое.
Таблица 1. Типичные примеры и электроконтактные свойства композиционных материалов на основе серебра
Типичные составы |
Основные свойства |
||||
Св |
Кс |
Э |
Пд |
Дг |
|
Ag-10CdO |
у |
о |
у |
о |
о |
Ag-15CdO |
о |
о |
о |
у |
о |
Ag-12SnO2In2O3 мд |
о |
п |
о |
у |
у |
Ag-12SnO2Bi2O3 мд |
о |
п |
о |
у |
у |
Ag-12SnO 2 WO 3 |
о |
у |
о |
у |
у |
Ag-12SnO 2 MoO 2 |
о |
о |
о |
у |
у |
Ag-8ZnO |
о |
п |
о |
у |
у |
Ag-(10-20)Ni |
п |
о |
п |
о |
у |
Ag-(30-40)Ni |
у |
у |
у |
о |
у |
Ag-(3-5)C |
о |
о |
п |
п |
у |
Ag-(50-70)W |
у |
п |
о |
п |
п |
Итак, разрывные электроконтакты, основой которых является серебро, в качестве функциональной добавки, придающей контактам высокий уровень служебных свойств, часто используются оксиды металлов. Наиболее эффективными в этом отношении признаны: оксид кадмия (CdO), используемый для этих целей уже более 60 лет (впервые предложен в 1939 г. [44]), и диоксид олова (SnO 2 – предложен в 1949 г. [45]). Диоксид олова широко используется только в последние десятилетия, приходя на замену токсичному оксиду кадмия. По этой системе опубликовано множество патентов, см., например [46]. Нашли также некоторое применение оксиды меди и цинка [47-50].
Для больших токов и относительно высоких напряжений используют композиции с тугоплавкими металлами Mo, W (табл. 1, 2) и карбидами WC, TiC [51].
Еще в 1939 г. для тяжелонагруженных реле был предложен материал Ag-Ni [52]. Контакт-детали из этого псевдосплава широко используются и в настоящее время. Их область применения охватывает средненагруженные контакторы и магнитные пускатели, реле автоматики железных дорог. В паре с контактом Ag-C он имеет прекрасные характеристики сваривания и применяется в автоматических выключателях. Есть также предложения использовать псевдосплавы с железом [53, 54].
Композит Ag-Ni получают прямым смешением порошков Ag и Ni и совместным осаждением солей из растворов. Детально технология этих псевдосплавов описана в [55] и включает обязательную холодную деформацию после твердофазного спекания порошков (экструзию, прокатку, волочение). Таким путем получают текстурированный материал с упорядоченно-ориентированной структурой [4]. Контакты системы Ag-Ni кроме высокой пластичности и хорошей прирабатываемости обладают также высокими тепло- и электропроводностью, коррозионной и эрозионной стойкостью, стабильным и низким переходным сопротивлением.
Возможно получение материала Ag-Ni внутренним окислением [4]. Разработан способ получения мелкодисперсной смеси порошков 0,5 – 1 мкм помолом смеси солей в вибромельнице – 255 –
Таблица 2. Типичные приложения контактных материалов к различным типам низковольтных аппаратов
Большое преимущество контактов Ag-Ni – их технологичность: они не нуждаются в дополнительном слое (так называемом подслое) для пайки на контактодержатель. Немаловажное обстоятельство – возможность экономии до 40 % серебра. В связи с этим до сих пор продолжаются работы по совершенствованию материала [57-59]. Ранее [60] изучены контакты состава Ag-10Ni-3C, показавшие не только высокое сопротивление привариванию, но и высокую скорость эрозии в дуге. Авторы [57] к той же основе добавляли малое количество графита – 0,5 и 1 %. Выяснилось, что скорость эрозии в аппарате и свариваемость заметно возрастают. В патентах [58, 59] предлагается в композицию Ag-Ni ввести оксид никеля, что, по мнению авторов, улучшает служебные свойства контактного материала.
Таблица 3. Свойства некоторых серебросодержащих сплавов и композиционных материалов электроконтактного назначения (состав, мас. %)
сЗ S & 5 2 |
g Н о Н С |
о н |
S 5 8 S 2 у ч о £ Й ч » Н Q § Я 2 g С л 8 |
* н « я ® Н 5 у Й л и & 2 о с |
s ООН |
сЗ 2 ч и |
5 х СО \ Н Щ |
1 |
2 |
3 |
4 |
5 |
6 |
7 |
8 |
Ag |
10,5 |
960 |
1,59 |
4,1 |
419 |
79 |
3-7 |
Ag-10Cd |
10,3 |
910-925 |
4,3 |
1,4 |
150 |
60 |
3,6-10 |
Ag-15Cd |
10,1 |
850-875 |
4,8 |
2 |
109 |
60 |
4,0-11,5 |
Ag-3Cu |
10,4 |
900-934 |
1,92 |
3,2 |
385 |
85 |
4,5-9,5 |
Ag-5Cu |
10,4 |
905-940 |
1,96 |
3 |
380 |
85 |
5-10 |
Ag-10Cu |
10,3 |
779-875 |
2,08 |
2,8 |
335 |
85 |
6,5-12 |
Ag-20Cu |
10,2 |
779-810 |
2,17 |
2,7 |
335 |
85 |
8-13 |
Ag-30Pd |
10,9 |
1150-1220 |
15,6 |
0,4 |
60 |
116 |
7-14 |
Ag-40Pd |
11,1 |
1225-1285 |
20 |
0,36 |
46 |
134 |
7,5-15 |
Ag-50Pd |
11,2 |
1290-1340 |
33,3 |
0,23 |
33,5 |
137 |
8-16 |
Ag-60Pd |
11,4 |
1330-1385 |
41,7 |
29,3 |
10-18 |
||
Ag-30Pd-5Cu |
10,8 |
1120-1165 |
15,4 |
0,37 |
108 |
9-17 |
|
Ag-0,15Ni |
10,5 |
960 |
1,7 |
4 |
414 |
85 |
4,5-9 |
Ag-10Ni |
10,2 |
960 |
2,0 |
3,5 |
310 |
84 |
5-11 |
Ag-20Ni |
10,0 |
960 |
2,2 |
3,5 |
270 |
98 |
6-10,5 |
Ag-30Ni |
9,8 |
960 |
2,4 |
3,4 |
240 |
115 |
6,5-11,5 |
Ag-40Ni |
9,7 |
960 |
2,7 |
2,9 |
210 |
129 |
7,5-12 |
Ag-50Ni |
9,6 |
960 |
3,1 |
185 |
145 |
7,5-13 |
|
Ag-60Ni |
9,4 |
960 |
3,7 |
155 |
160 |
8-14 |
|
Ag-70Ni |
9,3 |
960 |
4,0 |
140 |
170 |
8-15,5 |
|
Ag-3C |
9,0 |
960 |
2,1 |
3,5 |
325 |
4,2 |
|
Ag-5C |
8,5 |
960 |
2,3 |
3,3 |
318 |
4,0 |
|
Ag-10C |
7,4 |
960 |
2,9 |
3,1 |
|||
Ag-15C |
6,5 |
960 |
4,5 |
2,6 |
|||
Ag-25C |
5,1 |
960 |
14,5 |
||||
Ag-50C |
3,2 |
960 |
23 |
||||
Ag-70C |
2,6 |
960 |
53 |
||||
Ag-90C |
2,14 |
960 |
87 |
||||
Свойства некоторых материалов для скользящих контактов |
|||||||
Ag-5Cu-10C |
6,8 |
905-940 |
4,7 |
||||
Ag-48,5Cu-3C |
8,3 |
779-875 |
4,0 |
5,2 |
|||
Ag-47,5Cu-7C |
7,4 |
779-875 |
8,0 |
||||
Ag-35Cu-30C |
4,2 |
779-815 |
63,6 |
||||
Ag-69,75Cu-5C |
8,2 |
779-945 |
3,2 |
5,2 |
|||
Ag-72Cu-3C |
8,3 |
779-960 |
5,3 |
7,1 |
Ряд серебросодержащих составов материалов электроконтактного назначения и их свойства обобщены в табл. 3 [26].
В некоторых применениях важнейшим свойством контактов является стойкость к свариванию, которое обеспечивает надежное отключение тока при аварийных ситуациях. Такое требование предъявляется к автоматическим выключателям, реле сигнализации железных дорог, терморегуляторам (например, электроутюгов) и т.п. Для этих целей используются спеченные материалы Ag-C с содержанием углерода в виде графита обычно в пределах 2-5 %, а иногда, в случае больших токов, до 10-20 % [4, 43, 61]. Присутствие в матрице 3-5 % С практически исключает приваривание контактов за счет разупрочнения материала и снижения площади соприкосновения металла. Твердость такого материала низка – HV ≅ 40 [36], а дуговая эрозия велика. Причины этого – малая прочность включений и отсутствие адгезионной связи матрицы и включений. Опубликованы [62] результаты исследований влияния технологических особенностей и размера частиц графита на свойства контактов Ag-5C. Уменьшение размеров графитовых включений ведет к росту потерь от воздействия дуги, но стойкость к свариванию возрастает.
Есть предложения [63] по введению углерода в виде волокон, которые, по-видимому, несколько упрочняют материал, по сравнению с добавками графита, что ведет к улучшению эксплуатационных свойств.
Для увеличения прочности в контакты с углеродом добавляют никель. Комбинированный контакт Ag-(10...30)Ni-3C сохраняет высокую стойкость против сваривания, низкое контактное сопротивление при лучших механических характеристиках и меньшей стоимости. Известен состав Ag-29Ni-3C-1Cd, имеющий НВ = 84 [4]. Дополнительное легирование кадмием несколько улучшает эрозионную стойкость. Здесь также сообщается об отрицательном эффекте измельчения графитовых частиц в таком материале.
Не умаляя значения других электроконтактных материалов, необходимо отметить доминирующее положение по совокупности служебных свойств контактов на основе композиций Ag-CdO. Используется материал уже более 60 лет, но, несмотря на его экологическую опасность, до настоящего времени продолжаются исследования, направленные на его совершенствование и углубленное изучение свойств [64-67].
По современным представлениям использование CdO в электроконтактном материале дает многогранный эффект: дисперсионное твердение улучшает механические свойства, присутствие частиц CdO в расплавленной ванне катодного пятна увеличивает вязкость расплава, уменьшая разбрызгивание, диссоциация CdO приводит к понижению тепловой нагрузки на матрицу и одновременно способствует понижению стабильности дуги и ее температуры; испарение и разложение CdO дают большой объем газа, который сдувает дугу и заставляет ее перемещаться по контакту, способствуя деконцентрации тепловой энергии (отдувной эффект). Кроме того, CdO, обладая высокой летучестью и малым удельным сопротивлением (r = 0,01...0,5 Ом см) [40], не создает изолирующей пленки на поверхности контакта, оставляя переходное сопротивление низким и стабильным. Кроме того, считается, что присутствие кислорода (являющегося мощным акцептором электронов) в плазме дуги способствует дугогашению за счет снижения в ней концентрации электронов.
Однако полной ясности в этом вопросе нет. Испытано множество других оксидных добавок, обладающих сходными свойствами, но ни один из них не сравним с CdO. Наглядный – 258 – пример – испытания материалов на основе серебра с добавками 12,5 об. % оксида в контакторе переменного тока U = 220 В, I = 160 А. Получены следующие значения эрозионного износа, г/циклх106 (всего сделано 20 000 циклов В-О) [36]:
Оксид-добавка CdO CuO Sb 2 0 3 ZnO МП 3 О 4 PbO
Cкорость эрозии 1,45 5,60 4,08 20,0 4,05 22,5
Единственный оксид, в какой-то мере составивший конкуренцию CdO (в значительной степени - из-за экологической безопасности), - оксид олова SnO 2 . Контакты с добавкой 12 % SnO 2 или SnO 2 +In 2 O 3 (Bi 2 O 3 , WO 3 , MoO 3 ) известны достаточно давно, они отвечают экологическим требованиям, и их изучение интенсивно продолжается (обычно в сравнении с Ag-CdO) [64, 66-70]. Судя по литературным данным, контакты Ag-SnO 2 обладают хорошими эрозионными характеристиками и в некоторых применениях вполне заменяют кадмиевые, хотя встречается много противоречивых результатов. Наряду с углубленным изучением фундаментальных особенностей электроконтактного поведения данной системы публикуется большое количество патентов с предложениями по новым составам и технологическим вариантам реализации статистически однородной, высокодисперсной микроструктуры композита (см. например, [48, 71-75]).
В работе [64] на основе исследований и анализа даются заключения по токовому диапазону применения серебро-оксидных композиций: Ag-CdO - 50-3000 А, Ag-SnO 2 - 500-3000 А, Ag-ZnO – 3000-5000 А. Ограниченно применим также материал с оксидом меди Ag-CuO [47, 64, 76]. Он иногда используется в сильно нагруженных контактах постоянного и переменного тока, переключателях тепловозов и т.п.
Контакты системы Ag-CdO содержат, как правило, 10-15 мас. % CdO и производятся различными методами: (1) – традиционным смешением порошков Ag и CdO, (2) – совместным осаждением солей, (3) - внутренним окислением порошков сплава Ag-Cd или заготовки контакта из такого же сплава. Второй и третий способы дают мелкодисперсную структуру с размером включений 0,1-10 мкм, в то время как смешение порошков дает включения 30-50 мкм. Практически все свойства мелкодисперсного сплава выше, чем у традиционного (табл. 3). Особенно высока эрозионная стойкость: в 2-5 раз выше порошкового контакта [30]. На рис. 1 приведены зависимости твердости и удельного электрического износа контактов из материала 85Ag-15CdO от дисперсности частиц оксидной фазы [77]. Как видно, и прочностные свойства, и сопротивление дуговому износу весьма существенно зависят от этого параметра. Измельчение второй фазы в данном случае благоприятно.
Это пытаются объяснить особыми условиями формирования плазменных факелов на мелкодисперсных материалах Ag-CdO и Ag-Ni [78]. Еще одно возможное объяснение: скорость движения основания дуги на мелкодисперсных контактах выше, так как перескок места привязки дуги здесь облегчен [79, 80]. Концентрация тепла снижается, а значит, падает и тяжесть локальных повреждений поверхности. Это объяснение представляется более вероятным, хотя, по-видимому, и не исчерпывающим.
Технологические способы (2) и (3) дают приблизительно одинаковую дисперсность CdO (<1 мкм), но при тяжелых режимах работы оказался более предпочтительным спеченный материал. Плавленый, внутриокисленный контакт разрушается раньше из-за появления трещин, – 259 – as
CD
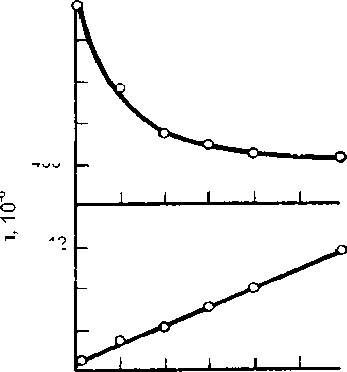
Средний размер частиц, мкм
0 50
Рис. 1. Влияние дисперсности включений оксидной фазы на служебные свойства контактов 85Ag-15CdO [77]
идущих с поверхности по границам зерен [36]. Несколько улучшает положение следующая за окислением холодная деформация.
Еще более сильное влияние оказывает структура материала на работоспособность слаботочных контактов. В табл. 4 приведены результаты исследования износа контактов из серебра (99,99 %) и сплава серебра с палладием (70 Ag-30 Pd) при коммутации постоянного тока I = 2 А, U = 24 В [81]. Те и другие контакты изготовлены двумя методами: литьем и порошковой металлургией.
Если не принимать во внимание различия химического состава на уровне малого содержания примесей, то контакты отличаются только структурой материала (плавленые – более крупнозернистые) и, в некоторой степени, прочностными свойствами, пластичностью. Однако характер износа существенно различен. На литых контактах наблюдается мощный перенос с катодного на анодный электрод с образованием кратера и пика соответственно, в то время как на порошковых скорость эрозии несравненно меньше на обоих электродах.
Более-менее полного, убедительного и обоснованного объяснения обнаруженному явлению не найдено. Это, однако, еще раз свидетельствует в пользу электроконтактных материа- лов, получаемых методами порошковой металлургии, позволяющими в широких пределах ва- рьировать состав и структуру материала за счет различных технологических вариантов.
Для улучшения качества пайки композитов на контактодержатель делают подслой из серебра или никеля, прессуя его одновременно с основным рабочим слоем материала. Толщина подслоя составляет обычно 0,15-0,25 мм.
Описана технология изготовления Ag-CdO и Ag-SnO 2 контактов из распыленных порошков Ag-Cd и Ag-Sn [66] (метод IOAP – internal oxidation of alloyed powder). Жидкий сплав при температуре около 1470 К распыляли водой под давлением 34 МПа с получением порошка размером – 44 мкм. Порошки окисляли при различных температурах от 753 до 973 К, от чего зависела морфология оксидных включений. Далее прессовали заготовки (Р = 175...700 МПа), спекали в течение часа при 1083 К, а затем допрессовывали (Р = 1230 МПа). Полученный материал, как сообщают, имел хорошие электроконтактные свойства.
Подобный процесс лежит в основе производства контактного материала, предложенного в патенте [73]: расплав Ag-Sn-Bi распыляется и далее порошок подвергается внутреннему окислению. Из внутриокисленного порошка прессуются заготовки, которые затем подвергают горячей экструзии и прокатке. Способ дает размер оксидных включений в диапазоне 0,1-1,0 мкм. Здесь же предложен и второй способ, приводящий приблизительно к тому же результату, который заключается в распылении растворов солей серебра и олова при температуре порядка 950 ° С. Полученный порошок далее используется для получения целевого материала.
Таблица 4. Сравнительная характеристика износа контактов, полученных различными методами
Материал контакта |
Метод изготовления |
Изменение массы электрода, A g x 10 8 , г/цикл В-О |
|
Анод |
Катод |
||
Ag |
Литье |
+49,0 |
-32,0 |
Ag |
Порошковый |
-15,0 |
-1,7 |
Ag-30Pd |
Литье |
+18,0 |
-22,0 |
Ag-30Pd |
Порошковый |
+2,2 |
-3,4 |
Улучшения качества материала пытаются достичь также малыми добавками оксидов, способствующих лучшему смачиванию CdO расплавом серебра: это например, оксиды меди, германия, тантала [65], добавленные в количестве 0,15...0,43 %. Добавка 0,15 % GeO 2 увеличивает стойкость к дуговой эрозии при длительной работе, в то время как Cu 2 O приводит к появлению трещин и ускоренному разрушению контактов. Отмечается, что все добавки приводят к росту эрозии на токах более 50 А, особенно Та 2 О 5 .
Интересный состав композиционного материала и способ его изготовления предложены в патентах [82, 83]: Ag-(4…15)CdO-(2…8)Ni. Тонкие включения никеля оксидированы, т.е. заключены в тонкую оболочку оксида никеля, что предотвращает деградацию материала из-за восстановления оксида кадмия никелем.
Изучено влияние добавок оксидов висмута, олова, индия и вольфрама в количестве 5 % к композиции Ag-10CdO [84]. Авторы измеряли эрозионную стойкость в условиях стационарного межконтактного промежутка при токовых нагрузках 100 и 150 А на контактах, приготовленных по одинаковой технологии. Скорость эрозии на контактах Ag-10CdO-5Bi 2 O 3 (относительно стандартного состава) снизилась почти в два раза. Такая же добавка SnO 2 почти не изменила износ, а добавки In 2 O 3 и WO 3 увеличили его, соответственно, в 1,9...2,4 и в 4,5...5,5 раз. Авторы объясняют эти результаты на основании металлографических и рентгенофазовых данных изменениями в слое наработки с учетом химического взаимодействия добавки с основой. Отмечается определяющая роль теплофизических свойств частиц-добавок в воздействии на эрозионные характеристики материала.
Эти же авторы изучали влияние деформации на структуру и эрозионную стойкость AgCdO-контактов [80]. Оказалось, что существует явная тенденция снижения стойкости к дуговому износу при увеличении предварительной деформации осадкой. После некоторой пороговой степени деформации (29...43 %) стойкость резко снижается (примерно в два раза). Авторы объясняют это появлением микронесплошностей в материале.
Изложенное демонстрирует многогранность материала электрического контакта. Даже в таком известном материале, как Ag-CdO, до сих пор находятся возможности его улучшения и неизвестные нюансы влияния состава, технологии и структуры (см. также, например, [82, 83]).
В табл. 5 приведен перечень основных электроконтактных материалов, применяемых и производимых в России [4, 38, 77]. Для сравнения здесь же перечислены материалы аналогичного назначения на медной основе. Электропроводность, твердость, плотность материалов, а следовательно, и их эрозионная стойкость существенно зависят от применяемой технологии. В – 261 –
Таблица 5. Материалы разрывных средне- и сильноточных контактов [4, 38, 77]
н § о $ —г О |
04 |
04 |
04 |
04 |
Я |
ад |
8 |
8 |
8 |
1 |
1 |
1 |
40 |
о |
8 |
1 |
1 |
1 |
||||
s „ н S о а к с С 5 2 с с |
ОО |
8 |
о |
m |
8 СЧ |
ад |
8 СЧ |
8 |
ад |
8 |
8 |
о |
о |
8 |
8 |
о |
||||||
н" 3 § й и 2 а Я ~р £ g и |
о |
m |
8 |
СЧ |
8 |
8 |
о |
% |
8 |
о |
8 |
|||||||||||
„ о у 2 ® m 2 Я о S >> а 2 с |
40 |
04 |
ОО о |
ОО о |
8 |
о |
04 О |
ОО О |
о" |
о" |
О |
о" |
о" |
40 О |
о" |
о |
§ |
§ |
||||
Як 02 Н |
о |
о |
о |
о |
8 |
о |
о |
ад |
8 |
о |
о |
8 |
О |
8 |
8 |
ад |
||||||
Л С |
8 8 |
о |
ад 8 |
о |
ад 8 |
8 |
о. |
оС |
ад оС |
оС |
ад" |
ад" |
04" |
ад 04" |
О |
40 ад" |
8 ад" |
8^ ад" |
8 ад" |
|||
02 Н о |
m |
04 оС 04 |
ОО |
ОО |
8 |
8 |
о |
о |
о |
S |
S |
ад 04 |
04 ОО 40 |
04 04 40 |
9° 8^ |
^ 9 |
04" 04 8 04" 04 |
04" 04 |
8 04 |
8 04 |
||
3 и |
СЧ |
< |
о О "Во < |
о О "Sb < |
о я о "Sb < |
о я о "Sb < |
2 "Sb < |
"Sb < |
2 "Sb < |
2 "Sb < |
2 "Sb < |
о "Sb < |
О "Sb < |
о "Sb < |
О 2 'Sb < |
2 "Во < |
я •о я О о 'Во < |
О и |
О и |
75 и 8 и |
75 и 8 и |
|
сЗ сЗ 2 |
2 |
2 < Ы |
ч < 2 |
2 ri < |
ОО 2 о о |
< 2 |
2 В m о р * ^ |
ч < |
< |
< |
8 = |
р |
ч < til |
< |
ч 2 |
S til |
2 |
2 tii |
Продолжение табл. 5
2. Новые применения серебра
В [85] сообщено о возможности создания высокочувствительных к СО сенсоров на основе наноструктур SnO 2 , легированных серебром. Для создания сенсоров сероводорода H 2 S использованы SnO 2 -Ag 2 O и SnO 2 -Ag [86].
Авторами работы [87] показано, что легирование 3-5 масс. % Ag сверхпроводящей керамики YBaCuO приводит к увеличению ее микропластичности и прочности.
Для изменения электрофизических свойств элементарных полупроводников и полупроводниковых соединений применяют легирование серебром. Естественно, что на такие цели расходуется незначительное количество серебра. Но для понимания особенностей поведения Ag в таких материалах проводятся специальные исследования [88-93].
На основе галогенидов серебра созданы инфракрасные световоды [94, 95].
На основе серебра исследуются полупроводниковые соединения [96-100], халькогенидные [101-118], оксидные [119-121] и смешанные [122-125] стекла.
В последние годы уделяется много внимания наноматериалам, в том числе и из серебра [126-152]. Это связано с тем, что наночастицы серебра обладают уникальным набором ценных свойств, благодаря которым они служат материалом для создания электронных, оптических, сенсорных устройств нового поколения [140]. Тем не менее, не стабилизированные наночастицы серебра подвергаются быстрому окислению и легко агрегируют в растворах. Это, естественно, затрудняет их применение при создании сенсорных и оптических устройств. Поэтому много работ посвящено разработке методов получения эффективной стабилизации таких частиц и взаимодействию серебра с различными средами [133, 136, 138, 140, 146-148, 153-163].
С древности по настоящее время серебро (в последние годы - особенно наносеребро) применяется в медицине для лечения ран, язв, для стерилизации и увеличения сроков хранения лекарственных препаратов, в стоматологии, а также в биологии [1, 126, 164-188]. Препараты, содержащие серебро, активны против многих возбудителей раневых инфекций (Staphylococus spp., E. Coli, P. aeruginosa, Proteus spp., Klebsiella spp.).
Согласно [189, 190] серебро проявляет высокую бактерицидную активность как по отношению к аэробным и анаэробным макроорганизмам (в том числе и антибиотикорезистентным штаммам), так и к некоторым вирусам и грибам. При этом нужно принимать во внимание тот факт, что резистентность микроорганизмов редка, и ее можно преодолеть увеличением концентрации препарата. В то же время большие концентрации ионов серебра могут оказывать на организмы ядовитое действие. В течение длительного времени считалось однозначно доказанным, что лечебными свойствами обладают ионы Ag+, а не металлическое серебро. Тем не менее вопрос о механизме действия наночастиц серебра на вирусы, бактерии и клетки до настоящего времени остается окончательно не выясненным и требует дополнительных исследований.
При передозировке серебра возможно развитие аргирии (возникновение пигментаций кожи, слизистых оболочек, внутренних органов, глаз) [191]. Замечено, что люди с признаками аргирии не подвержены инфекционным заболеваниям.
При работе с антибиотиками установлено, что спектр их действий узок, а вредные микроорганизмы слишком быстро к ним адаптируются. Поэтому в последнее время уделяется пристальное внимание хорошо проверенным средствам терапии с участием серебра.
Серебро и сплавы на его основе используются для создания омических контактов к полупроводникам Ge, Si, GaAs, GaP, GaSb, CdS, ZnTe [192].
Фотоэмиссионные катоды с высокой эффективностью работают на следующих материалах: Ag-O-Cs, Bi-Ag-O-Cs [192].
В ювелирных изделиях по-прежнему важную роль играют серебро и сплавы на его основе [193-199].
Аналитическая химия серебра достаточно полно изложена в монографии [200], а также в более поздних трудах [174, 201]. Наночастицы серебра сами могут использоваться для усиления сигнала органических соединений в спектроскопии [140] и электрохимическом анализе биологических объектов [174].
Необычные оптические свойства частиц серебра использовали древние стекловары [140, 202]. В кубке Ликурга (IV век н.э.), находящегося в экспозиции Британского музея, в бронзовой оправе содержатся вставки из окрашенного стекла. Проведенный анализ этого стекла показал, что оно содержит металлические наночастицы со средним диаметром порядка 40 нм. В своем составе эти наночастицы содержат 70 % Ag и 30 % Au. Благодаря им стекла приобретают красный цвет в проходящем свете и зелено-серый – в отраженном [140]. Серебро применено для придания лимонно-желтого цвета стеклам, используемым в старых соборах Европы. Желтый цвет стеклу можно придать разными способами: оксидами железа (трудно добиться постоянства окраски); сульфидом кадмия (при некоторых условиях он превращается в оксид кадмия, что делает стекло непрозрачным); азотнокислым серебром (в процессе варки стекла из AgNO 3 выделяется мелкодисперсное серебро, равномерно распределенное по стеклу). В последнем случае образуется бесцветное стекло, а окраска появляется при наводке - повторном нагреве уже готовых изделий. Заметим, что с помощью солей серебра можно наносить золотистожелтую окраску на отдельные участки стеклянных изделий. Особенно хорошо окрашиваются высококачественные свинцовые стекла. Кроме коллоидного серебра, желтую окраску стеклам придают еще CrO 3 и NiO [203].
Заключение
Трудно перечислить все современные отрасли применения серебра. Тем не менее основной принцип его применения, обусловленный дефицитностью и высокой стоимостью («экономить везде, где это возможно, применять только там, где это абсолютно необходимо» [4]), еще никто не отменял, или, по крайней мере, не создал предпосылки для его отмены. Можно полагать, что будут выявлены новые области и направления применения серебра (как это было, например, с наносеребром).