Процессы заполнения форм при центробежной заливке титан-алюминиевых интерметаллидных сплавов
Автор: Кулаков Борис Алексеевич, Дубровин Виталий Константинович, Чесноков Андрей Анатольевич, Карпинский Андрей Владимирович
Журнал: Вестник Южно-Уральского государственного университета. Серия: Металлургия @vestnik-susu-metallurgy
Статья в выпуске: 39 (298), 2012 года.
Бесплатный доступ
Представлены результаты расчетного анализа скоростных режимов движения титан-алюминиевого расплава в полостях литейной формы при различных условиях центробежной заливки.
Интерметаллидный сплав, титан, центробежная заливка, литейная форма
Короткий адрес: https://sciup.org/147156760
IDR: 147156760
Текст научной статьи Процессы заполнения форм при центробежной заливке титан-алюминиевых интерметаллидных сплавов
Плавка и заливка титан-алюминиевых интер-металлидных сплавов ведется в специальных вакуумных плавильно-заливочных установках (ПЗУ). Для мелких по массе и габаритам отливок используются ПЗУ, в которых вылив металла из плавильного керамического тигля и заполнение формы происходит под действием центробежных сил. Схема такой установки изображена на рис. 1.
Металл плавится в керамическом тигле 2 под воздействием вихревых токов индуктора 3. После расплавления сплава и достижения температуры заливки индуктор отходит вниз, освобождая тигель, и начинается вращение тигля одновременно с формой. После набора необходимой скорости металл под действием центробежных сил выливается из тигля и заполняет форму 1. Противовес 6 необходим для устойчивой балансировки установки.
При заливке металла в форму важно, чтобы металл заполнял ее без завихрений и разбрызгиваний, которые приводят к неспаям в отливке, раз- мыванию рабочей поверхности формы и загрязнению отливки неметаллическими включениями.
Важнейшим параметром, влияющим на весь процесс заливки в центробежной установке, является скорость вращения тигля и формы, обеспечивающая подъем металла в тигле и его последующий вылив в форму, т. е. центробежная сила должна быть больше силы тяжести расплава (веса расплава). Расчет проводили по формуле:
ω≥
2 gh cos α
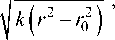
где ω – угловая скорость вращения тигля и формы, 1/с; g – ускорение свободного падения, м/с 2 ; h – высота подъема металла (высота тигля), м; k – коэффициент сопротивления ( k = 0,7); r – расстояние до дальней стенки тигля, м; r 0 – расстояние до ближней стенки тигля, м; α – угол наклона стенки тигля, градус ( α = 10°).
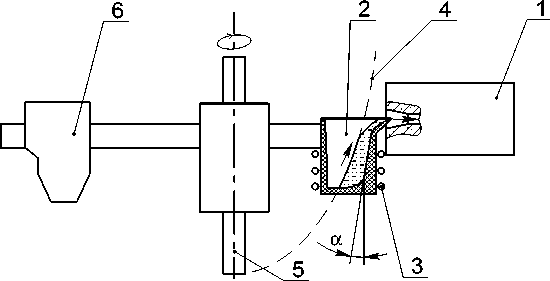
Рис. 1. Схема плавильно-заливочного механизма: 1 – литейная форма; 2 – керамический плавильный тигель с расплавом металла; 3 – индуктор; 4 – форма свободной поверхности металла; 5 – ось вращения; 6 – противовес
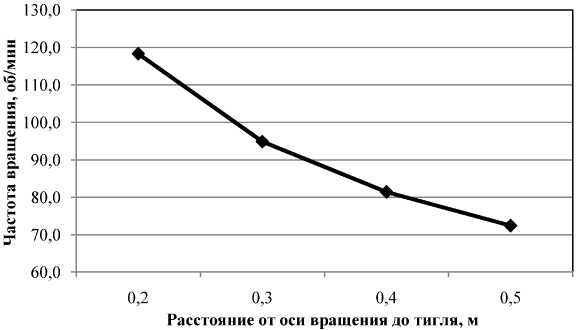
Рис. 2. Минимальная скорость вращения, необходимая для заливки форм
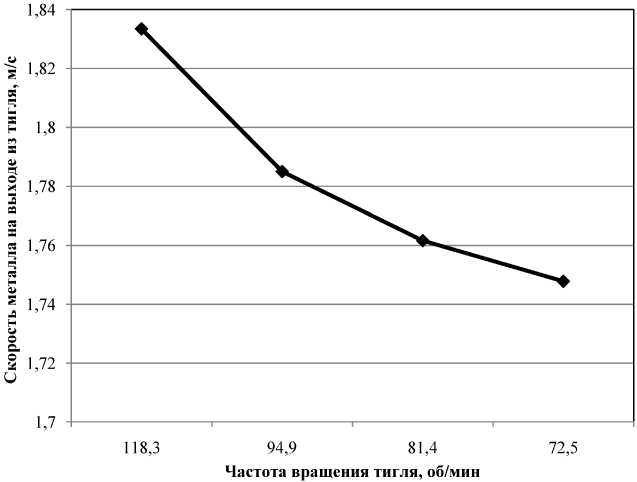
Рис. 3. Линейная скорость металла на выходе из тигля
Для расчетов приняли тигель высотой 8 см и с диаметром основания 4 см.
Проведенный расчет выявил минимальную скорость вращения тигля, необходимую для заполнения формы металлом на различных расстояниях от оси вращения. Полученные данные представлены на рис. 2.
Полученная минимальная скорость вращения тигля и формы обеспечивает полную выливку металла из тигля высотой 8 см и диаметром основания 4 см. С увеличением расстояния от оси вращения до тигля необходима меньшая скорость вращения.
В зависимости от угловой скорости вращения тигля и формы соответственно будет изменяться и линейная скорость движения металла в стояке и в отливке.
Для расчета линейной скорости металла на выходе из тигля при минимально допустимой скорости вращения тигля и формы воспользуемся формулой:
V = 2ahh , (2) где V – скорость металла на выходе из тигля, м/с; а – ускорение металла в верхней точке тигля, м/с 2 .
Ускорение рассчитывается:
а = а ц - g cos а , (3) где а ц – центробежное радиальное ускорение, равное to 2 r , м/с2.
Результаты представлены на рис. 3.
С уменьшением скорости вращения тигля на сплав все сильнее воздействуют гравитационные силы притяжения, и линейная скорость сплава на выходе из тигля снижается.
При расчете скорости течения металла в стояке используем две различные схемы расположения отливок, представленные на рис. 4.
Для расчета скорости течения металла в стояке воспользовались формулой:
V = V V 0 + 2 а ц s , (4)
где V0 - начальная скорость металла (скорость на выходе из тигля), м/с; s - путь, пройденный металлом в стояке, м.
Результаты расчета скорости движения расплава при различных угловых скоростях вращения формы для первой схемы расположения отливок представлены на рис. 5.
В стояке металл разгоняется под действием центробежных сил, при большей скорости вращения тигля и формы разгон происходит быстрее. При длине стояка 200 мм скорость возрастает практически в два раза от начальной скорости при выходе из тигля, поэтому необходимо стремиться к минимальной длине стояка во избежа-
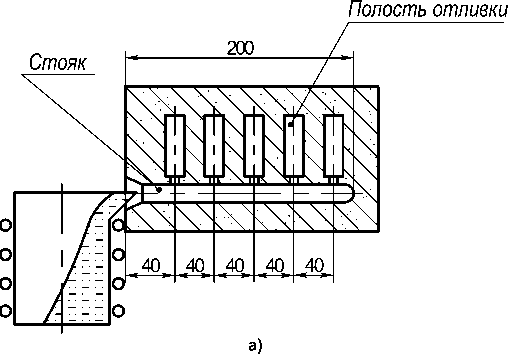
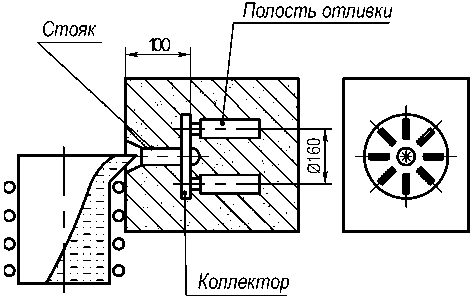
б)
Рис. 4. Расположение отливок в форме: а – схема I; б – схема II
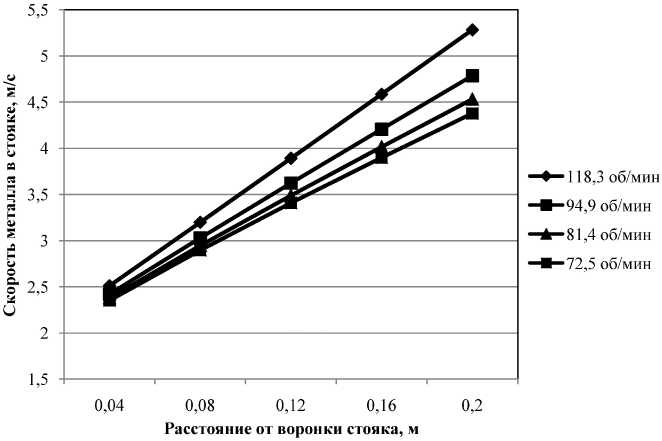
Рис. 5. Линейная скорость металла в стояке (схема I)
ние турбулентных потоков металла и размыва формы.
При второй схеме расположения отливок скорость в стояке получилась в два раза меньше благодаря меньшей в два раза длине стояка, результаты представлены в таблице.
В зависимости от скорости металла в стояке и расположения полостей отливок также будет изменяться скорость движения расплава в рабочей части формы (полости отливки) и в коллекторе (схема II).
Скорость подъема металла в отливку по схеме I рассчитана по формуле:
V = 4V 0 —2gh отл , (5)
где V 0 – начальная скорость металла (скорость в стояке в месте расположения отливки), м/с; h отл – высота отливки.
Для расчета взяли высоту отливки «лопатка турбинная» ~ 10 см.
Скорость металла в полости отливки ниже, чем в стояке под соответствующей полостью, так как эту скорость тормозит ускорение свободного падения. Скорость течения расплава возрастает по мере удаления от оси вращения (рис. 6).
Для расположения отливок по схеме II сначала были рассчитаны скорости течения металла в коллекторе по формуле (5) в точках с максимально различными условиями протекания расплава (верхняя и нижняя). Результаты представлены на рис . 7.
Скорость течения металла в стояке (схема II)
Cкорость вращения тигля и формы, об/мин |
118,3 |
94,9 |
81,4 |
72,5 |
Линейная скорость движения расплава в стояке, м/с |
3,07 |
2,9 |
2,8 |
2,7 |
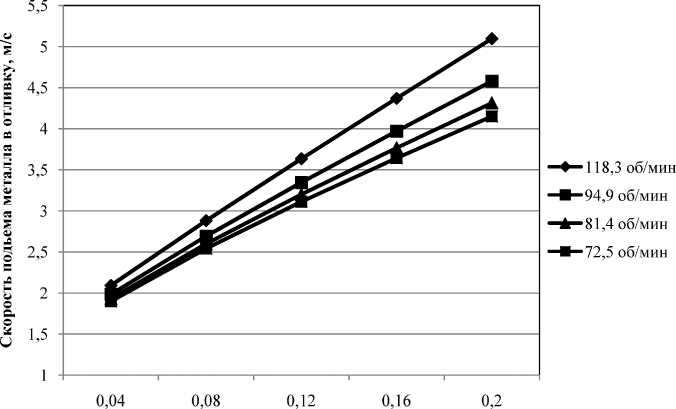
Расположение отливки от воронки стояка, м
Рис. 6. Линейная скорость металла в отливке (схема I)
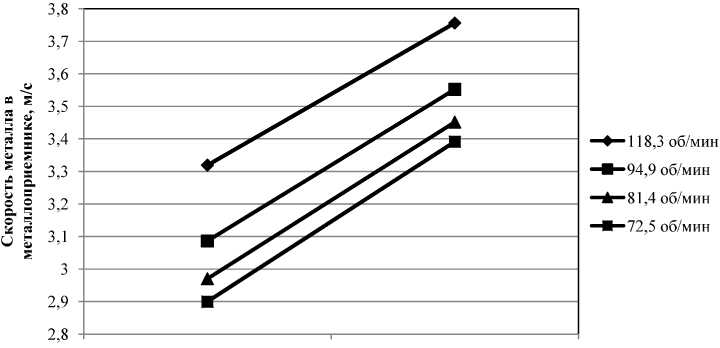
Низ Расположение отливки Верх
Рис. 7. Линейная скорость металла в металлоприемнике (схема II)
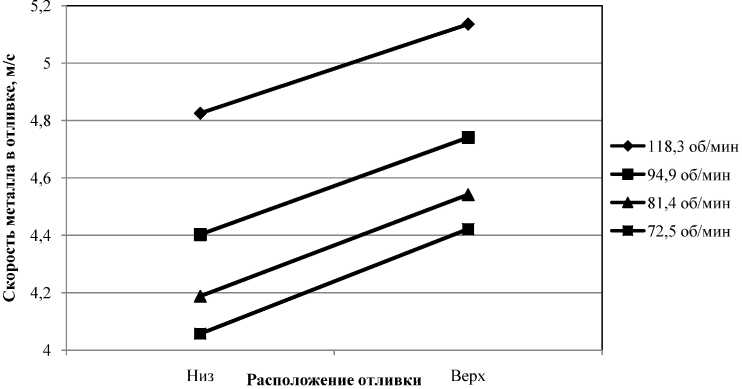
Рис. 8. Линейная скорость металла в отливках (схема II)
Рассчитанные скорости течения металла в отливках, находящихся в максимально различных условиях, представлены на рис. 8.
Таким образом, результаты проведенных расчетов показали следующие закономерности. При первом варианте расположения отливок каждая форма отливки будет заполняться металлом при различных скоростях в зависимости от расстояния до центра вращения, а ближний к центру вращения элемент отливки будет являться прибылью для дальнего. Ликвационные явления для каждой отливки также будут своими и отличаться друг от друга.
При втором варианте, когда металл попадает в полость отливки из дискового коллектора, скорости заполнения всех отливок будут практически одинаковы, перепад скоростей уменьшается с 2–3 м/с (при первой схеме) до 0,4 м/с (при второй схеме), питание всех отливок одинакового направления, ликвационные процессы подобные. Для экономии металла дисковый коллектор можно разбить на отдельные сектора под одну или две отливки на каждом в зависимости от их габаритов, а также сократить длину стояка до минимума.
Следует отметить, что представленные скорости вращения являются минимально допустимыми для вылива металла из тигля, в производственных условиях данный параметр будет дополнительно уточняться в зависимости от жидкотекучести сплава, конфигурации и толщины стенок получаемой отливки.
Список литературы Процессы заполнения форм при центробежной заливке титан-алюминиевых интерметаллидных сплавов
- Юдин С.Б. Центробежное литье: моногр./С.Б. Юдин, М.М. Левин, С.Е. Розенфельд. -М.: Машиностроение, 1972. -280 с.
- Специальные способы литья: справ./под общ. ред. В.А. Ефимова. -М.: Машиностроение, 1991. -436 с.