Прогнозирование безопасности технических систем
Автор: Лепеш Григорий Васильевич, Моисеев Евгений Николаевич
Журнал: Технико-технологические проблемы сервиса @ttps
Рубрика: Диагностика и ремонт
Статья в выпуске: 2 (48), 2019 года.
Бесплатный доступ
СТАТЬЕ РАССМАТРИВАЮТСЯ СОВРЕМЕННЫЕ ПОДХОДЫ ОБЕСПЕЧЕНИЯ БЕЗОПАСНОСТИ ТЕХНИЧЕСКИХ СИСТЕМ, ОСНОВАННЫЕ НА ПРОГНОЗИРОВАНИИ ДОПУСТИМОГО РИСКА. НА ПРИМЕРЕ ТЕХНОЛОГИЧЕСКОГО ПРОЦЕССА АВТОСКРЕПЛЕНИЯ ТРУБЫ ПРОВОДИТСЯ ОЦЕНКА ВЛИЯНИЯ ТЕХНОЛОГИЧЕСКИХ ПАРАМЕТРОВ НА ВЕРОЯТНОСТЬ ДОСТИЖЕНИЯ ЕЕ ПРЕДЕЛЬНОГО СОСТОЯНИЯ, ПРИВОДЯЩЕГО К РИСКУ ВОЗМОЖНОГО РАЗРУШЕНИЯ.
Техническое состояние, прочность, технический риск, вероятностный подход, напряжения, нагружение, деформации, разрушение
Короткий адрес: https://sciup.org/148318805
IDR: 148318805
Текст научной статьи Прогнозирование безопасности технических систем
Введение. При проектировании технических систем (ТС) как гражданского, так и оборонного назначения исходят из того, что все ее подсистемы и элементы в течение всего срока эксплуатации будут работать в штатном режиме, т.е. обеспечивать прочность, ресурс и надежность, заложенные в назначенных запасах прочности. На практике оказывается, что любая ТС, даже самая совершенная, может оказаться в запредельных условиях функционирования и выйти из строя по причине аварии, зачастую сопровождающейся значительным материальным или иным ущербом. Таким образом существует некий технический риск ее эксплуатации, обусловленный ее реальным состоянием.
Технический риск можно рассматривать, как комплексный показатель надежности элементов технической системы и техносферы в целом. Он выражает вероятность аварии или катастрофы при эксплуатации машин, меха- низмов или реализации технологических про- цессов:
_ дт й т = Т(7У где Дт - технический риск;
ДТ - число происшествий вследствие отказов техники в единицу времени t на идентичных технических системах и объектах;
Т - число идентичных технических систем и объектов, подверженных общему фактору риска f.
Основные источники и причины появления факторов технического риска приведены в табл. 1.
Таблица 1 – Источники и причины появления факторов технического риска
№ п/ п |
Источник технического риска |
Причины появления факторов риска |
1 |
НИОКР |
Необоснованность выбора направления развития технических систем в направлении обеспечения безопасности. Ошибки в обосновании конструктивных схем, в выборе материалов, в вычислении внешних воздействий и в расчетах запасов прочности. Неточность имеющихся статистических данных и существующих оценок; несовершенство математических моделей. Не предусмотрены специальные средства обеспечения безопасности. |
2 |
Технологическая подготовка производства и производство |
Недостаточный учет техники безопасности. Неправильное технологическое обеспечение изготовления и контроля качества изделия, в том числе: производства заготовок, механообработки, термической обработки, сборки и др.. Несовершенство используемого производственного и контрольно-измерительного оборудования. |
3 |
Эксплуатация |
Нарушение режимов эксплуатации и правил хранения. Использование не по назначению. Неправильная организация работ по техническому обслуживанию. |
4 |
Персонал |
Недостаточная дисциплина и/или квалификация персонала. Слабая стресс-устойчивость в конфликтных и чрезвычайных ситуациях |
Причинами риска могут быть также различного рода нештатные ситуации, связанные с опасными факторами внешней среды (объективные факторы) либо действием оператора (субъективный фактор), а также износ или усталость элементов технической системы в процессе ее продолжительной эксплуатации. Не редко причиной аварии являются скрытые дефекты, которые не обнаружены на стадии изготовления, либо появившиеся в процессе эксплуатации от случайного воздействия опасных факторов.
Реальное состояние ТС следует определять уровнем ее техногенной безопасности. На практике различают три уровня технического состояния объектов [1]:
– штатные, характеризующиеся низким риском возникновения техногенных катастроф при нормальной ситуации в эксплуатации;
– аварийные, характеризующиеся высоким риском возникновения техногенных катастроф при любой ситуации в эксплуатации;
– катастрофические состояния, характеризующиеся чрезвычайно высоким риском возникновения техногенных катастроф при эксплуатации.
Любая ТС в процессе эксплуатации последовательно проходит три перечисленные уровни состояния, причем риски нарастают экспоненциально [1]. Для обеспечении ее безопасности технической системы на всех стадиях жизненного цикла, особенно в случаях, когда возможен высокий риск возникновения техногенных, природно-техногенных и антропогенных аварий и катастроф необходимо проводить диагностику и мониторинг состояния объектов и рисков их эксплуатации.
До недавнего времени ТС (машины и оборудование, инженерные системы), либо эксплуатировались до выхода их из строя [реактивное профилактическое обслуживание (РП)], либо обслуживались по регламенту [система планово-предупредительных ремонтов (ППР)], т.е. осуществлялось плановопрофилактическое техническое обслуживание [2].
Недостатки обеих подходов очевидны из практики эксплуатации – либо обслуживание по регламенту выполняется без фактической необходимости (половина из числа всего оборудования), либо возникают аварийные ситуации, приводящие к несанкционированной остановке функционирования системы. Тем не менее на практике применяют методики, которые позволяют определить рациональные сроки и объемы профилактических мер, обеспечивающих наименьшие экономические потери при выходе из строя такой техники [6]. При этом ущерб, связанный с рисками катастроф, как правило, не учитывается.
«Защищенность» [3] ТС характеризуется заложенными при проектировании запасами прочности, а также надежностью и безопасностью ее функционирования в условиях высокого уровня неопределенности, связанной наличием источников технического риска (табл. 1). В соответствии с этим методы обеспечения защищенности при проектировании ТС можно разделить на три различных подхода, причем принципиально различающихся друг от друга [3]:
-
1) Нормативный подход, основанный на обеспечении запасов прочности по принятым критериям.
-
2) Вероятностный подход, основанный на критериях надежности, чаще всего на оценке вероятности достижения предельного состояния.
-
3) Подход по критерию рисков к обеспечению защищенности, основанный на оценке вероятности реализации предельных состояний с учетом ущерба от такой реализации.
Используем обозначения, приведенные в работе [3]:
9 (x1,x2,^,xm,X i ,X2 ,-,X k ) — функция состояния системы, где: хг,х2 , -.,хт - случайные переменные состояния системы, Z i ,X2,-,Xk — детерминированные параметры, значения которых выбираются при проектировании. Тогда функция предельных состояний будет записываться в виде:
9 (X 1 ,X2 ,-,X m ,X i , X 2 ,-X k ) = 1, (2)
причем условие обеспечения защищенности принимает вид:
9 (X i ,X 2 , ^,X m ,X i ,X 2 , -X k ) < 1, (3) а условие разрушения:
9 (X i ,X 2 ,-,X m ,X i ,X 2 ,-Xk)>1- (4)
При нормативном подходе все случайные переменные заменяются детерминированными значениями, представляющими собой, как правило, средние значения (математические ожидания) тогда, обозначая
Е ( x1),E(x2), ,„,E(xm) , запишем условие обеспечения защищенности через детерминированную функцию:
00 (x 1 >x 2 , “•>X ki' ) =
9 {E (X i ),E (X 2 ), -,E(X m ),X i ,X 2 , -.X k }- (5)
В правой части неравенства (5) вводится множитель, представляющий собой предписанный нормативный (предельно допустимый) запас [и] > 1. Тогда условие обеспечения защищенности (3) перепишем в виде:
И-д 0 ( х1,х2,-хк1 ) < 1. (6)
Неравенство (6) означает, что при проектировании необходимо выбрать назначаемые конструктором параметры
E(Xi),E(x2),-,E(Xm),Xi,X2,-Xki, чтобы при заданном предельно-допустимом нормативном запасе [и] обеспечить его выполнение. Выбор [и], характеризующего уровень неопределенности, во многом зависит от величины ущерба, ожидаемого в случае достижения предельных состояний. Так, при проектировании большинства технических устройств, материальный ущерб от достижения предельных состояний относительно невысок (большинство технологических машин, подъемно-транспортное оборудование, малая авиационная техника и др.), коэффициент запаса составляет 1,25 - 2,00, а для более крупной техники, предельное состояние которой грозит появлением чрезвычайных ситуаций с большим материальным ущербом и/или потерями большого количества людей, значение коэффициента запаса может быть значительно увеличено (3,33 - 5,56 для железнодорожного транспорта, для крупного металлургического оборудования и др.[1]).
Постановка задачи обеспечения прочности
Достижение предельного состояния механических элементов машин представляет угрозу их разрушения. Для исследования причин отказов разрушение механических элементов машин целесообразно подразделить на две группы:
-
- разрушения, зависящие от смазки (износ при истирании, заедании, усталостное выкрашивание);
-
- разрушения силового характера (пластическое течение, излом).
Исследование причин отказов ТС по разрушению элементов ТС производят по оценке напряженно-деформированного состояния (НДС) - совокупности внутренних напряжений и деформаций, возникающих при действии на техническую систему внешних нагрузок, температурных полей и других факторов. НДС определяется расчётными и экспериментальными методами в виде распределения напряжений ст, деформаций £ и перемещений и в конструкции и является основанием для оценки прочности и ресурса конструкций на всех этапах жизненного цикла [1].
Оценку НДС в современных условиях проводят с помощью метода конечных элементов. В настоящее время для моделирования НДС применяется множество видов программного обеспечения, среди которого наибольшее распространение получили программные продукты, интегрированные в CAD системы, такие как: КОМПАС — 3D, S о I id Works, А и to d esklnvento г , An sys.
Причиной разрушения деталей ТС часто является, как правило, неравномерное распределение нагрузки по объему детали. В результате этого возникают локальные концентрации напряжений вблизи прилегающей к концентраторам поверхности, величина которых достигает критических значений и противоречит условию защищенности (3, 6). В ряде случаев это приводит к пластической деформации, интенсивному износу или к поломке детали. Для обеспечения условия (6) конструктор вынужден проектировать конфигурации деталей таким образом, чтобы напряжения и деформации распределялись по их объему относительно равномерно. Причем уровень напряжений соответствовал условию (6), которое выполняется как за счет снижения напряжений, так и за счет повышения механических свойств материала. Для этой цели в арсенале конструктора имеется множество «инструментов». Фактически ему приходится решать оптимизационную задачу по наилучшему выбору множества переменных хг,х2, ...,Хт,Х1,Х2,-,Хк и назначать коэффициенты запаса п, причем как с учетом значений Е(хх),Е (х2), .^,Е(хт) для случайных величин, так и других числовых значений законов их распределения. В качестве варьируемых переменных в этой задаче будут выступать - геометрия (размеры) детали и механические свойства ее материала.
Рассмотрим относительно простой пример нагружения трубы в технологическом процессе ее автоскрепления [2] (автофретирования). Технология нашла широкое применение для повышения прочностных характеристик металлических деталей цилиндрической формы (сосудов, труб, артиллерийских стволов и т.п.). Идея автоскрепления заключается в том, что в процессе изготовления деталь подвергается нагрузке внутренним давлением, что приводит к пластической деформации и появлению остаточных сжимающих напряжений, которые компенсируют растягивающие напряжения рабочей нагрузки.
Предварительную нагрузку цилиндра создают внутренним гидравлическим давлением (иногда взрывом или дорнованием), величина которого выше рабочего так, чтобы во внутренних слоях стенки цилиндра возникли пластические деформации, а в наружных – остались упругие деформации. После снятия давления во внешних слоях цилиндра также сохраняются упругие напряжения растяжения, а во внутренних – сжатия. Способ автоскрепления применим для сплошных толстостенных цилиндров. Он позволяет увеличить рабочее давление р при той же толщине стенки или уменьшить толщину стенки при том же давлении.
На рис. 1 приведена картина напряжений, рассчитанных в ANSYS при нагружении заготовки гидравлическим давлением 1200 МПа . Из картины видно, что наибольшие значения интенсивностей напряжений находятся на внутренней части трубы, а наименьшие – на внешней. После снятия нагрузки с трубы (рис. 2) наибольшие значения интенсивностей напряжений остаются на внутренней части трубы.
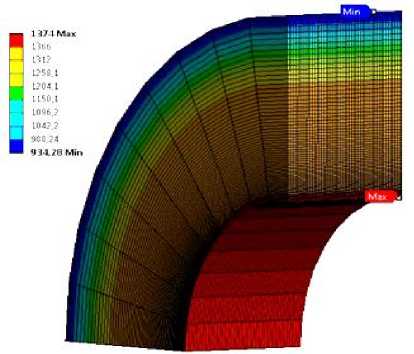
Рисунок 1 – Интенсивности напряжений (в МПа) при нагружении заготовки трубы давлением автоскрепления р = = 1200 МПа
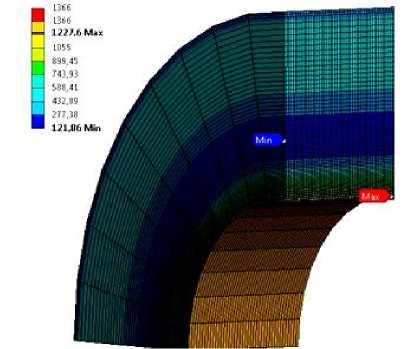
Рисунок 2 – Интенсивности напряжений (в МПа) при разгрузке заготовки трубы (после нагружения давлением автоскрепления ра = 1200 МПа)
На рис. 3 приведены эпюры интенсивности напряжений автоскрепленной трубы ( р а = 1200 МПа), нагруженной рабочим давлением р = 600 МПа, откуда следует, что наиболее нагруженные внутренние слои неавтоскре-пленной трубы у автоскрепленной трубы разгружены, а максимум эквивалентных напряжений, в последнем случае, смещен к наружной поверхности трубы.
Особенностью эффекта от нагружения трубы при автоскреплении является то, что начиная с некоторого уровня давления автоскрепления он увеличивается вместе с ростом нагрузки (рис. 4). Однако, по мере распространения пластической деформации по глубине стенки, возникает риск разрушения трубы в процессе автоскрепления, связанный с моментом выхода пластических деформаций на ее наружную поверхность. Степень риска можно оценить производной от радиальной деформа- ции по приращению давления автоскрепления (рис. 5).
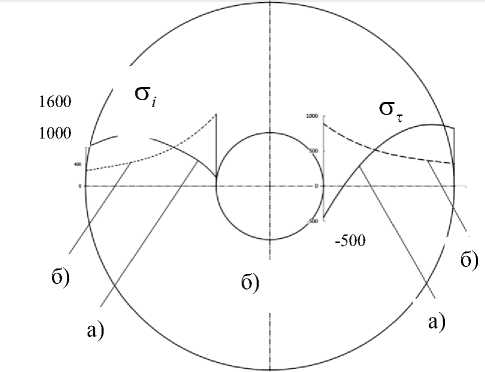
Рисунок 3 – Интенсивности напряжений при р = 600 МПа: а) – автоскрепленной трубы;
б) – неавтоскрепленной трубы
Из рисунка 5 следует, что по мере развития зоны пластической деформации, угроза разрушения нарастает в геометрической прогрессии и в данном примере к моменту давления в F а ≥1200 МПа процесс становится практически неуправляемый.
В качестве функции состояния (6) д о, характеризующей условие защищенности [и]∙So (Zi , /2,…Zki)≤1 можно выбрать отношение конечной радиальную деформацию трубы l/^ , мм, к предельной, соответствующей выходу пластических деформаций на наружную поверхность [ U^ ], мм,
50=[ ]․ (7)
Параметрами этой функции будут являться – геометрия трубы (наружный и внутренние диаметры), комплекс механических свойств (рис. 6), характеризующих ее упругость E , прочность о пц, 0*02 , о %, о в и пластичность £ пц , ^02 , E % , E в , 6 (табл.3), а также давление автоскрепления F а. А условием защищенности – условие (6).
Основной проблемой оценки защищенности в рассматриваемом примере является выбор коэффициентов запаса. Коэффициент запаса по разрушаемому рабочему давлению может быть выбран в соответствии с изложенными рекомендациями с учетом вероятности появления чрезвычайных ситуаций и размером материального ущерба от разрушения ТС. К тому же, как правило, его значение обосновывается опытной эксплуатацией ТС.
Выбор коэффициента запаса по давлению автоскрепления зависит от вариативных факторов, определяющих стабильность самого процесса автоскрепления, к которым относятся все перечисленные факторы. Для этого следует применять вероятностный подход.
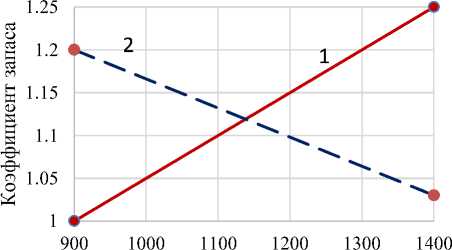
Давление автоскрепления
Процесс Автоскрепление
Рисунок 4 – Зависимость коэффициента запаса от давления автоскрепления: 1 – по разрушающему рабочему давлению; 2 – по разрушающему давлению автоскрепления.
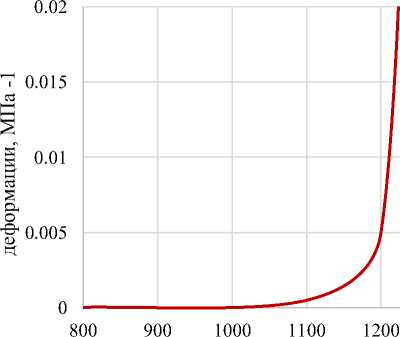
Давление автоскрепления , МПа
Рисунок 5 – Скорость изменения максимальных деформаций на внутренней поверхности заготовки трубы от величины нагрузки
Таблица 3 – Механические характеристики материала
№ п/ п |
Наименование |
Напряжение, МПа |
Деформация |
1. |
Предел пропорциональности |
σ пц |
ε пц |
2. |
Предел текучести |
σ 0,2 |
ε 0,2 |
3. |
При наибольших деформациях в процессе нагружения |
σ % |
ε % |
4. |
В точке наибольших напряжений |
σ в |
ε в |
5. |
Относительное удлинение |
- |
δ |
6. |
Модуль упругости |
E |
- |
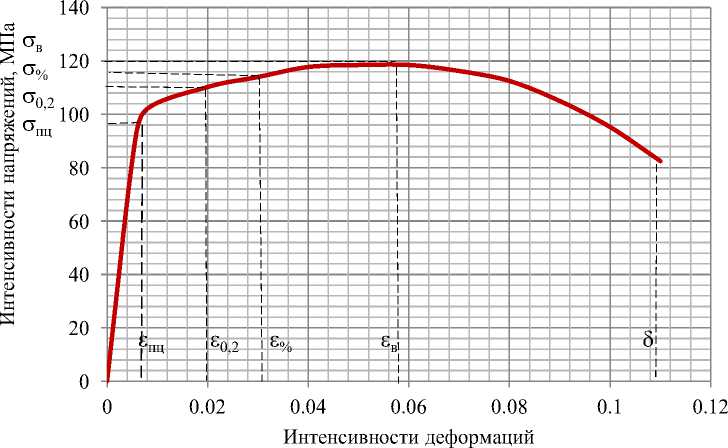
Рисунок 6 – Диаграмма деформирования
Вероятностный подход к обеспечению защищенности ТС
Будем учитывать, что в реальных условиях производства параметры, входящие в функцию (6) будут заданы соотношением некоррелированных и распределенных по нормальному закону величин нагрузки р Э и несущей способности :
д ( fпр , ^ а) = ^а /^пр -1= 0, тогда условие обеспечения защищенности запишется в виде:
р а ≤1․ (8)
пр
Пусть в процессе моделирования предельного состояния НДС трубы, нагружаемой внутренним давлением Р а в среде Ansys получено значение математического ожидания
Е { Р пр} = 1400 МПа и среднеквадратичное отклонение s^пр =100 МПа. Отметим, что при моделировании некоррелируемыми параметрами следует принимать значения геометрических размеров трубы с учетом технологических допусков на размеры, а также отклонения формы и расположения поверхностей. Все механические характеристики являются зависимыми, а их значения в каждом конкретном случае производства трубных заготовок следует определять эмпирически. Числовые характеристики закона распределения давления автоскрепления Е { Р а} и S { Р а} определяются требованиями, предъявляемыми к технологическому оборудованию, осуществляющему технологический процесс автоскрепления. В качестве примера примем Е { Р а } =1200 МПа и S { Р а }=50 МПа.
Для применения нормативного подхода заменим неопределенные величины F а и F пр в условии (10) на их математические ожидания Е { F а} и Е { F пр}, а для учета связанных с этой заменой неопределенностей введем предельно допустимый запас [ п ] >1․
[ п ]⋅ Е { Р а}⁄ Е^пр ≤1, (9)
или: [п] ≤Е{Рпр}/ Е{Ра}, т.е. привести к обычному условию обеспечения защищенности, вида: [п] ≤п , где п= {Рпр}/ Е{Ра} – фактиче ский запас, который должен быть не ниже нормативного предельно допустимого запаса [п]. Однако введение допустимого запаса [п] не может полностью исключить возможность разрушения системы. Остается нерешенным вопрос о том, какая предельная вероятность отказа [Q^i ] соответствует заданному нормативному запасу [п].
Вероятностный подход, подробно описанный в работе [1] основывается на том, что ТС считается защищенной, если выполняется условие:
Q ≤ |/л„], (10) где q – расчетная вероятность отказа системы, а [Q^] – предельно допустимое значение вероятности отказа ТС данного типа. Вероятность разрушения Q определяется областью перекрытия графиков плотностей распределения величин F пр и Fа (рис.6). В случае нормальных законов распределения конфигурация этой области зависит от математических ожиданий E{Fа} } и E{Fпр} и от среднеквадратичных отклонений S{Fа} и S{Fпр} Q (p =φ V{пр} ,S^F пр , s{^а},…․|χ ․ Плотность вероятности Рисунок 6 – Плотности вероятностей распределения Ф(Fа) и Ф(F пр) Для рассматриваемого частного случая, когда величины Fа иFпр являются некоррелиро- ванными и распределены по нормальному за- кону, вероятность разрушения можно рассчи- тать по формуле [5]: E{Pпр - {Pа} (s{Pа}) 2+ №пр})2 1400 - 1200 1400 - 1200 =Ф- =Ф- √505+1005 √502 +1002. = Ф(-1,79) = 0,0367․ Здесь Ф(X)= 1 √2 X_mexp(- t2/ 2)dt– нор- мальная функция распределения. Полученные значения вероятности раз- рушения явно не допустимы для организации технологического процесса автоскрепления. Очевидно, что в данном примере необходимо ужесточить требования к механическим свойствам трубы для того, чтобы снизить 5{Fпр}. Так при значении sfjпр =50 МПа получим Qip = Ф(-2,82) =0,024. Подобные действия можно производить по отношению к ужесточению параметров технологического процесса. Например при значениях sfjпр = 5{Fа}=25 МПа получим практически нулевую вероятность разрушения Q . Однако получить подобные разбросы практически нереально. На практике для рассматриваемого случая нормально распределенных, некоррелированных величин Fа иFпр при варьировании параметрами χ средне квадратичные отклонения sfjпр и 5{Fа} являются постоянными, поэтому вероятность разрушения зависит только от величин математических ожиданий E{Fпр} и E{Fа}. Таким образом, обеспечить безопасность рассматриваемого технологического процесса возможно только путем сохранения значительного диапазона между величинами {Fпр} и E{Fа}, оставаясь при этом в рамках получения значимого эффекта процесса автоскрепления. Предельная величина вероятности отказа устанавливается в зависимости от таких факторов как величина ущерба, который может наступить в случае отказа, социальной значимости системы и срока ее эксплуатации. Международной научно-информационной ассоциацией строительной индустрии (CIRIA-Constraction Industry Research and Information Assosiation) для сложных инженерных сооружений (плотин, мостов, шельфовых платформ) принята следующая формула для оценки предельно допустимой расчетной вероятности отказа (разрушения) системы: 10~4fs ∙t Ы =10 ∙ -k , ∙ где t – расчетный срок эксплуатации системы; L – среднее количество людей, которые могут погибнуть в случае разрушение системы; kHp – коэффициент, учитывающий отказы, связанные с человеческим фактором (обычно принимают = 10); ^S– коэффициент социальной значимости системы (см. табл. 2) [4]. Таким образом, вели- чина обычно оказывается в диапазоне 10-5 10-7. – Часто в нормативных документах фигурирует, так называемая, теоретическая предельно допустимая вероятность отказа [^^ т, которая оценивается без учета возможных ошибок или несанкционированных воздействий со стороны человека которая оценивается как [1]: к l-10^ (12) Таблица 2 - Коэффициент социальной значимости для различных типов технических систем [1] Тип системы 5.s Объекты массового скопления людей (спортивные комплексы, торговые центры) 0,005 Плотины Жилые здания, офисные центры, промышленные объекты 0,005 0,05 Мосты 0,5 Буровые вышки, шельфовые установки 5 Обеспечение защищенности по критерию риска В настоящее время для оценки защищенности сложных ТС широко применяются модели, основанные на теории рисков, которые позволяют реализовать комплексный подход к обеспечению защищенности по отношению как вероятности достижения предельных состояний ТС, так и связанные с этим ущербы. В большинстве случаев проектируемая система считается защищенной, если расчетная величина общего экономического риска Rэ оказывается меньшей предельно допустимого значения [RЭ], установленного для данного случая нормативными документами: Rэ< [Лэ]. (13) Под общим экономическим риском, как правило, понимается функционал в форме произведения вероятности отказа Q^(Y|X) и последствий отказа системы U^(YVx): R(Y|x) =QVW)^ U^lx). (14) Здесь вероятность достижения предельного состояния Q^(Y|X) •определяется согласно выражению (11), а подсчет ущербов от отказов технических систем является отдельной задачей, решаемой с помощью специальных методик оценки ущербов при техногенных авариях [4]. Для рассматриваемого случая технологического процесса автоскрепления оценка в объеме данного исследования не проводилась. Для всех стадий создания и эксплуатации потенциально опасных объектов техниче- ской системы (разработка технического задания, проектирование, изготовление и эксплуатация) необходимо проводить оценку технического риска. Точность оценки в большой степени зависит от точности определения фактического состояния ТС – от достоверной информации о параметрах и характеристиках, важнейшие из которых: напряжения, температура, скрытые дефекты. Для определения этих величин применяются множественные средства диагностики [2,5], наиболее информативные из которых: ультразвуковые, магнитопорошковые, рентгеновские, томографические, вибродиагно-стические, акустические, эмиссионные, голографические, тепловизионные, тензометрические.
Список литературы Прогнозирование безопасности технических систем
- Махутов Н.А., Гаденин М.М.Техногенная безопасность: диагностика и мониторинг потенциально опасного оборудования и рисков его эксплуатации.// Промышленная безопасность, [интернет-ресурс] URL: http://federalbook.ru/files/FS/Soderjanie/FS-26/ VI/ Mahutov.pdf (дата обращения 5.05.2019)
- Махутов Н.А. Конструкционная прочность, ресурс и техногенная безопасность. Новосибирск. Наука. - 2005. В 2 ч. Часть 1. Критерии прочности и ресурса. 494 с. Часть 2 Обоснование ресурса и безопасности. 620 с.
- Методики оценки рисков чрезвычайных ситуаций и нормативы приемлемого риска чрезвычайных ситуаций. Руководство по оценке рисков чрезвычайных ситуаций техногенного характера, в том числе при эксплуатации критически важных объектов Российской Федерации. Утверждены Первым заместителем Министра РФ по делам гражданской оборрны, чрезвычайным ситуациям и ликвидации последствий стихийных бедствий Р.Х. Цаликовым 9 января 2008 г. № 1-4-60-9. 102 с.
- Лепеш, Г.В. Оперативный контроль и диагностика оборудования/ Г.В. Лепеш, В.Н.Куртов, Н.Г.Мотылев и др.// Технико-технологические проблемы сервиса. - 2009. № 3(9). с.8 - 16.
- Лепеш, Г.В. Современные методы и средства диагностики технологических машин и оборудования // Технико-технологические проблемы сервиса. 2015 г. №4(34), с.3
- Лепеш Г.В., Зайцев А.С., Моисеев Е.Н. Моделирование процесса автоскрепления толстостенных труб// Технико-технологические проблемы сервиса. 2015 г. №1(31), с.38- 44.