Прогрессивные технологии и способы упрочнения рабочего инструмента для прессования труднодеформируемых композиционных порошковых материалов
Автор: Самодурова Марина Николаевна, Серебряков Иван Сергеевич
Журнал: Вестник Южно-Уральского государственного университета. Серия: Металлургия @vestnik-susu-metallurgy
Рубрика: Порошковая металлургия и композиционные материалы
Статья в выпуске: 2 т.16, 2016 года.
Бесплатный доступ
Проведен анализ научной литературы, рассмотрены основные механизмы износа пресс-форм для холодного прессования порошков и представлены прогрессивные способы упрочнения рабочего инструмента для прессования труднодеформируемых композиционных материалов. На основе литературного обзора отечественной и зарубежной научной литературы и экспериментальных данных, полученных в Институте гидродинамики им. М.А. Лаврентьева СО РАН, предложены детонационное напыление и холодное газодинамическое напыление покрытий как способы повышения износостойкости и прочности пресс-форм. Кроме того, приведен технологический процесс детонационного напыления покрытия при помощи разработанного в России автоматизированного комплекса CCDS2000, а также представлено сравнение холодного газодинамического напыления с другими известными способами нанесения покрытий. Авторы раскрывают основную проблему нанесения покрытий детонационным и холодным газодинамическим методами на рабочий инструмент для прессования порошковых материалов, а также главные факторы, от которых зависят качественные характеристики покрытия. Затронутая тема актуальна для науки и многих отраслей промышленности, так как повышение износостойкости, прочности и срока службы инструментальной оснастки позволяет сократить расходы предприятия и снизить время на обслуживание технологического оборудования.
Защитные покрытия, детонационное напыление, холодное газодинамическое напыление, износостойкие покрытия
Короткий адрес: https://sciup.org/147157008
IDR: 147157008 | DOI: 10.14529/met160216
Текст научной статьи Прогрессивные технологии и способы упрочнения рабочего инструмента для прессования труднодеформируемых композиционных порошковых материалов
Развитие техники и, в частности, машиностроения придает проблеме уменьшения изнашивания инструментальной оснастки огромную значимость с точки зрения экономии материальных ресурсов. В порошковой металлургии около 7–10 % себестоимости изделия приходится на инструмент.
Вопросы износа пресс-форм рассматриваются в ряде работ. Сам термин «износ пресс-форм» следует понимать в широком смысле. Сюда относится весь комплекс явлений, протекающих на контактной поверхности и приводящих в конечном итоге к выходу пресс-формы из строя. Обобщение опубликованных работ и исследований позволяют выделить основные причины выбраковки пресс-форм при эксплуатации. В зависимости от конкретных особенностей процесса (материал, заготовки и инструмент, конфигурация и размеры, скоростной режим деформации и т. д.) характер и вид износа контактной поверхности могут существенно изменяться [1].
Рассмотрим виды износа контактной поверхности пресс-форм.
Пресс-формы для холодного прессования порошков, работающие в тяжелых условиях, часто подвергаются повышенному абразивному износу и механической усталости, что требует внедрения инновационных материалов и технологий, которые позволят повысить износостойкость, прочность и срок службы инструментальной оснастки.
Равномерный абразивный износ протекает одновременно по всему периметру пресс-формы или на её отдельных участках, где имеют место значительное перемещение заготовки относительно поверхности и большие удельные давления, и усиливается с повышением скорости деформации. Абразивный износ вызывается механическим зацеплением микронеровностей на поверхности инструментальной оснастки при полусухом трении, контактным схватыванием (адгезией) в микрообъемах, многократной деформацией и усталостным разрушением выступающих элементов микрорельефа, хрупким отрывом, а также твердыми мелкодисперсными абразивными частицами, попадающими в пограничный слой (износ эрозионного типа) [1].
При холодной обработке материалов давлением абразивный износ зачастую является ведущим фактором, определяющим износ инструмента [1]. Абразивный износ приводит к потере геометрических размеров пуансонов, матриц и стержней пресс-формы.
При достаточно большом количестве циклов нагружения происхождение трещин, как правило, связано с разрушением усталостного типа от повторного нагружения. При значительных напряжениях трещины могут появиться и при первых циклах в результате механического удара [1].
Единичные трещины выявляются на пресс-форме в виде микро- и макроскопических разрывов. Причины их появления весьма разнообразны. При большом количестве циклов нагружения это связано обычно с металлургическими (чрезмерная загрязненность, наследственная крупнозернис-тость), технологическими (высокий уровень остаточных напряжений), конструктивными (неправильный расчет пресс-формы на прочность, наличие концентраторов напряжений) и другими дефектами [1].
Трещины могут возникать от чрезмерных напряжений, возникающих при попадании металла с более высоким пределом прочности [1].
Появление трещин существенно интенсифицирует местный износ. С другой стороны, наличие отдельных дефектов, возникающих в процессе схватывания или местного абразивного износа, способствует появлению трещин. Следовательно, оба вида износа дополняют и ускоряют друг друга [2].
Кроме того, внедрение инновационных технологий и материалов для создания эффективных защитных покрытий на инструментальной оснастке является необходимым требованием для обеспечения конкурентоспособности ведущих отечественных предприятий. Такими технологиями являются активно развивающееся детонационное и холодное газодинамическое напыление.
Детонационное газотермическое напыление является одним из термических методов напыления, который используется для получения износостойких функциональных покрытий на поверхностях деталей машин и механизмов. Детонационное напыление является практически единственной технологией, позволяющей создавать толстые (более 100 мкм) многофункциональные покрытия (в том числе многослойные и градиентные) из всех видов керамических, металлокерамических и металлических наноструктурированных и наноком-позиционных материалов. Покрытия характеризуются повышенной адгезией и плотностью, а их напыление производится при ограниченном термическом воздействии на напыляемое изделие. Вышеуказанные результаты получают путём качественного улучшения традиционной технологии детонационного напыления посредством компьютерной автоматизации всего процесса в целом и каждой его составляющей в отдельности.
Лидером в разработке детонационных установок нового поколения бесспорно является Институт гидродинамики им. М.А. Лаврентьева СО РАН, где разработана уникальная автоматизированная установка детонационного напыления нового поколения с компьютерным управлением газораспределительной системы и дозаторов порошка, обеспечивающим высокоточное и стабильное управление технологическим процессом (рис. 2).
Немаловажным преимуществом автоматизированных детонационных установок является возможность нанесения равномерного покрытия на сложные многогранные поверхности.
Трехкоординатная система сканирования CCDS2000 позволяет в автоматическом режиме обрабатывать сложную трехмерную поверхность. Программируется сканирование для формирования однородного по толщине слоя покрытия высокого качества. Возможно формирование покрытия с заданным профилем по толщине [4].
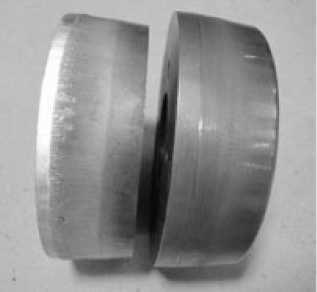
Рис. 1. Износ детали пресс-формы после 7000 циклов нагружения [3]
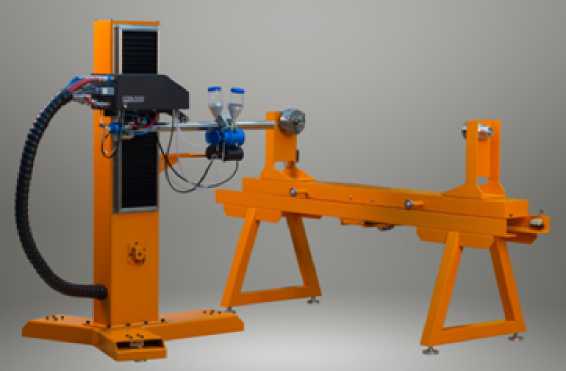
Рис. 2. Автоматизированная установка детонационного напыления
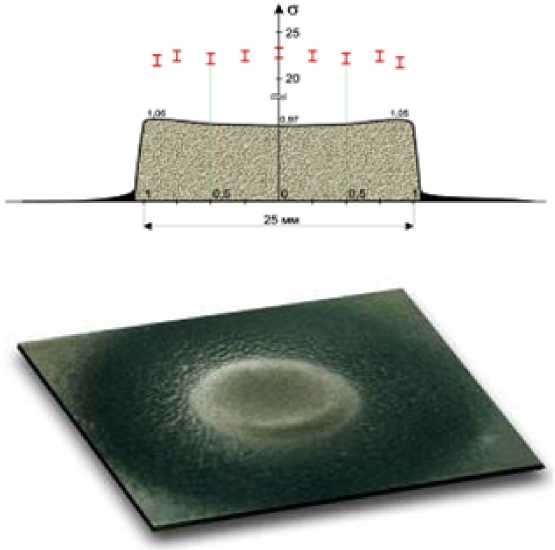
Рис. 3. Пятно напыления [4]
Детонационный комплекс CCDS2000 имеет модульную конструкцию с компьютерным блоком управления, автономной системой охлаждения и компактной пушкой (весом менее 20 кг), что позволяет монтировать ее как на специализированном роботе-манипуляторе, так и на промышленном роботе. CCDS2000 отличается высокоточной многоканальной системой газопитания, дозированной локальной подачей порошка и компьютерным управлением пушкой и манипулятором. Возможна работа на любом газовом топливе, включая реализацию режима SuperD-Gun на бинарном топливе [4].
Рабочий цикл автоматизированной установки детонационного напыления складывается из следующих операций:
– открытый с одного конца ствол заполняется взрывчатой газовой смесью;
– в ствол вводится порция порошка;
– взрывчатой смесь поджигается у закрытого конца ствола – в результате возбуждается само-поддерживающаяся детонационная волна;
– продукты взрыва разгоняют и разогревают порошок, как правило, до плавления;
– при столкновении с деталью частицы порошка прочно соединяются с ее поверхностью и образуют покрытие толщиной до 10 мкм;
– наращивается покрытие серией выстрелов, в течение которой деталь перемещается с помощью манипулятора [4].
На рис. 3 показано формирование микронных (5–10 мкм) слоев наложением [4].
Большую значимость технологии детонационного напыления придает возможность напыления различных износостойких покрытий на рабочую поверхность инструментальной оснастки. В первую очередь интерес представлет популярный износостойкий материал WC-Co. В работах [5–10] порошок WC-Co наносился для исследования технологических параметров напыления, износостойкости, фазового состава и его изменения после напыления, влияния термической обработки. Результаты работ показывают непревзойденную износостойкость детонационных покрытий, высокую прочность адгезии покрытия к подложке. В работе [9] показано, что термообработка покрытия WC-Co приводит к увеличению микротвердости и износостойкости. Отметим, что при неоптимизи-рованных параметрах напыления, авторы отмечали разложение карбида вольфрама и увеличение фазы W2C. В работах [11–13] изучались детонационные покрытия из WC-Co-Cr: оптимизация технологических параметров, микроструктуры и дефекты покрытий, износостойкость покрытий. Результаты показывают очень хорошую износостойкость покрытий, особенно после алмазного шлифования. Эксплуатационные характеристики напыленного материала близки к спеченному материалу, однако в неоптимизированных режимах авторы наблюдали большое количество дефектов: микротрещины, пустоты, окислы следы износа (от напыления).
Испытания различных образцов с покрытием и без покрытия на износостойкость корундовым абразивом показывают высокие результаты по твердости и износостойкости образцов с покрытием WC/Co [14] (см. таблицу, рис. 4).
Результаты испытаний на износ [14]
Твёрдость |
Износ, мм3/1000 об. |
|
Сталь 45 |
30 HRC |
107 |
Х12МФ |
63 HRC |
90 |
Покрытие WC/Co |
89 HRA |
2,1 |
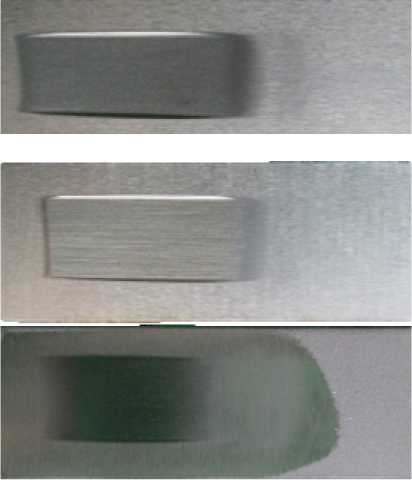
Рис. 4. Испытания на износ [14]
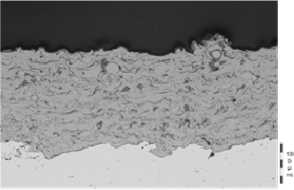
а)
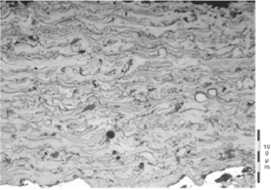
б)
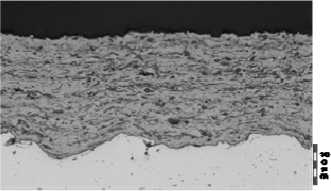
в)
Рис. 5. Детонационные покрытия: а – покрытие из углеродистой стали с добавкой вюстита и магнетита, HV 0.3 = 400;
б – покрытие типа сталь-молибден для увеличения стойкости к истиранию, HV 0.3 = 400; в – металлокерамическое покрытие HV = 500. Улучшения: стойкость к абразивному износу и истиранию
Фотографии детонационных покрытий пре дставлены на рис. 5.
Изучение микроструктуры покрытий позвол я ет говорить высокой степени однородности п о крытия и дает возможность изучить размеры и форму ст руктурных элементов покрытия.
Другим не менее интересным в изучении явл я ется метод холодного газодинамического напыл ения покрытий. Холодное газодинамическое нап ы ление (ХГН) является методом термического нап ы ления металлических и металлокерамических п окрыти й в основном за счет кинетической энергии газа проходящего через сопло Лаваля, а также п о догрева порошка до температур, существенно ниже температуры плавления. В данном случае покрытие (толщина покрытия более 100 мкм) формируется в процессе взаимодействия высокоскоростных частиц
(скорость частиц от 600 до 1000 м/с) находящихся в твердом состоянии, с поверхностью изделия. Одним из основных достоинств ХГН является прямой «перенос» состава и микроструктуры напыляемого порошка в покрытие, так как окисление, плавление, термическое разложение отсутствуют. ХГН является идеальной технологией для создания нанострук-турированных и нанокомпозиционных покрытий. ХГН позволяет получить слои до нескольких миллиметров за один проход (производительность до 50 кг порошка в час) на металлические и керамические изделия.
Сравнение основных параметров двухфазного потока, при котором реализуется метод ХГН, с параметрами, присущими традиционным методам напыления, показывает, что они существенно различаются (рис. 6).
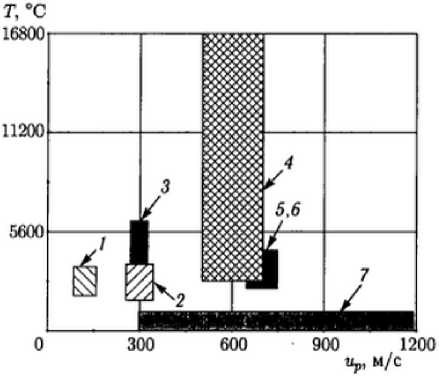
Рис. 6. Диаграмма используемых значений температуры и скорости частиц для сравнения различных методов напыления: 1 – низкоскоростной газопламенный; 2 – высокоскоростной газопламенный; 3 – элек-тродуговой; 4 – плазменный; 5, 6 – детонационный и высокоскоростной жидкотопливный; 7 – ХГН [15]
Данная диаграмма показывает, что наличие высоких температур в струе не является обязательным условием и покрытия можно получать из частиц, имеющих температуру значительно меньше их температуры плавления, а это открывает широкие возможности для создания новых технологий и техники напыления [15].
Большое число работ посвящено свойствам нанесенных методом ХГН покрытий. В результате экспериментов были успешно нанесены покрытия практически из всех типов металлов (Al, Cu, Zn, Mo, Ta, Ti, Cr, Nb, Zr, Ag, Fe и многих других) и сплавов, широко применяющихся в промышленности [16–23]. В качестве обобщающих характеристик ХГН покрытий можно выделить:
-
1) низкое в сравнении с другими способами порошкового напыления содержание оксидов;
-
2) высокая электропроводность, практически равная электропроводности материала до напыления;
-
3) высокая теплопроводность, практически равная теплопроводности материала до напыления;
-
4) слабые, в сравнении с другими методами порошкового напыления, остаточные напряжения;
-
5) низкая пористость покрытия.
Нанесение многокомпонентных покрытий является новым направлением для исследователей ХГН. Напыление такого рода покрытий осуществляется двумя способами.
Первый способ заключается в напылении частиц, имеющих сложную многокомпонентную внутреннюю структуру (в том числе наноразмер-ную структуру). Напыление такого рода порошков позволяет получать покрытия с уникальными свойствами, которые невозможно получить с помощью напыления однокомпонентных частиц.
Данный способ является сравнительно новым и его появление связано в первую очередь с возникновением технологической возможности изготавливать сложные порошки с внутренней структурой в промышленных масштабах. В этой связи можно выделить сравнительно небольшое количество работ, посвященных данной теме [24–26].
Второй способ, значительно более простой и дешевый, заключается в напылении покрытий, состоящих из смесей микродисперсных однокомпонентных порошков [27–29]. Такие покрытия также могут обеспечить уникальные свойства с возможностью их варьирования в широком диапазоне путем изменения состава напыляемой смеси по толщине покрытия.
Учитывая вышеприведенные данные можно отметить, как положительные, так и отрицательные стороны технологии детонационного напыления и холодного газодинамического напыления. Вопрос об улучшении эксплуатационных характеристик полученных покрытий дополнительными методами обработки, изучение и исследование этой проблемы, остается открытым. Авторы, в основном, заключают, что качественные характеристики покрытий зависят в равной доле от самого напыляемого материала, так и от параметров напыления (т. е. сравнение порошкового материала и материала покрытия, микроструктурного и фазового состояния покрытия и литого материала, а также преимущества полученного микроструктурного состояния покрытия). Поэтому всё важнее становится отработка технологических параметров процессов и изучения их влияния на эксплуатационные характеристики инструментальной оснастки.
Список литературы Прогрессивные технологии и способы упрочнения рабочего инструмента для прессования труднодеформируемых композиционных порошковых материалов
- Трахтенберг Б.Ф. Стойкость штампов и пути её повышения. Куйбышев: Куйбышев. кн. изд-во, 1964. 280 с.
- Крагельский И.В. Трение и износ. М.: Машиностроение, 1968. 480 с.
- Purington M. A Flair for Coatings. The Tube & Pipe Journal (2011). Available at: http://www.thefabricator.com/article/tubepipefabrication/a-flair-for-coatings (accessed 12 April 2016).
- Технология и оборудование детонационного напыления. -http://www.hydro.nsc.ru/technology/techn3.php.
- Ненашев М.В., Ганигин С.Ю., Журавлев А.Н., Дьяконов А.С., Белокоровкин С.А., Карякин Д.Ю. Перспективные технологии, свойства и применение детонационных покрытий. Вестник Самарского государственного аэрокосмического университета им. академика С.П. Королёва (НИУ). 2011. № 3. С. 197-203.
- Ahmed R., Hadfield M. Rolling Contact Fatigue Performance of Detonation Gun Coated Elements. Tribology International, 1997, vol. 30, pp. 129-137. DOI: DOI: 10.1016/0301-679X(96)00036-9
- Babu Suresh P., Basu Bikramjit, Sundara¬rajan G. Processing-Structure-Property Correlation and Decarburization Phenomenon in Detonation Sprayed WC-12Co Coatings. Acta Materialia, 2008, vol. 56, no. 18, pp. 5012-5026. DOI: DOI: 10.1016/j.actamat.2008.06.023
- Wang Y. Friction and Wear Performances of Detonation-Gun-and Plasma-Sprayed Ceramic and Cermet Hard Coatings Under Dry Friction. Wear, 1993, vol. 161, no. 1-2, pp. 69-78. DOI: DOI: 10.1016/0043-1648(93)90454-T
- Park S.Y., Kim M.C., Park C.G. Mechanical Properties and Microstructure Evolution of the Nano WC-Co Coatings Fabricated by Detonation Gun Spraying with Post Heat Treatment. Materials Science and Engineering A, 2007, vol. 449-451, pp. 894-897. DOI: DOI: 10.1016/j.msea.2006.02.444
- Du H., Hua W., Liu J., Gong J., Sun Ch., Wen L. Influence of Process Variables on the Qualities of Detonation Gun Sprayed WC-Co Coatings. Materials Science and Engineering A, 2005, vol. 408, pp. 202-210. DOI: DOI: 10.1016/j.msea.2005.08.008
- Murthy J.K.N., Rao D.S., Venkataraman B. Effect of Grinding on the Erosion Behavior of WC-Co-Cr Coating Deposited by HVOF and Detonation Gun Spray Processes. Wear, 2001, vol. 249, pp. 592-600 DOI: 10.1016/S0043-1648(01)00682-2
- Pervushin D., Smurov I. Development of Multimaterial Coatings by Cold Spray and Gas Detonation Spraying. Surface and Coatings Technology, 2010, vol. 205, no. 4, pp. 1108-1114 DOI: 10.1016/j.surfcoat.2010.07.092
- Wood R.J.K, Mellor B.G., Binfield M.L. Sand Erosion Performance of Detonation Gun Applied Tungsten Carbide/Cobalt-Chromium Coatings. Wear, 1997, vol. 211, no. 1, pp. 70-83 DOI: 10.1016/S0043-1648(97)00071-9
- Ульяницкий В.Ю. Детонационное напыление -для решения задач водородной энергетики. Альтернативная энергетика и экология. 2006. № 9. С. 108-113.
- Алхимов А.П., Клинков С.В., Косарев В.Ф., Фомин В.М. Холодное газодинамическое напыление. Теория и практика. М.: Физматлит, 2010. 536 с.
- Hall P., Yang L., Brewer T., Buchheit T. Preparation and Mechanical Properties of Cold Spray Nanocrystalline Aluminum. Proc. Int. Therm. Spray Conf. Maastricht, 2008, pp. 479-480.
- Sansoucy E., Jodoin B., Richer P. Ajdelstajn L. Effect of Spraying Parameters on the Microstructure and Bond Strength of Cold Spray Aluminum Alloy Coatings. Proc. Int. Therm. Spray Conf. Washington, ASM Int., 2006.
- Sansoucy E., Jodoin B., Kim G.E. Mechanical Characteristics of Al-Co-Ce Coatings Produced by the Cold Spray Process. Journal of Thermal Spray Technology, 2007, vol. 16, pp. 651-660 DOI: 10.1007/s11666-007-9099-3
- Haynes J., Padley J., Karthikeyan J., Kay A. Cold Sprayed Discontinuously Reinforced Aluminum (DRA). Proc. Int. Therm. Spray Conf. Washington, ASM Int., 2006.
- Ajdelsztajn L., Zuniga A., Jodoin B., Lavernia E.J. Cold Spray of Al-Cu-Mg-Fe-Ni Alloy with Sc Addition. Journal of Thermal Spray Technology, 2006, vol. 15. pp. 184-190 DOI: 10.1361/105996306X107995
- Richer P., Jodoin B., Taylor K., Sansoucy E. Effect of Particle Geometry and Substrate Preparation in Cold Spray. Proc. of Thermal Spray Conf. Thermal Spray Connects: Explore Its Surfacing Potential. Basel, 2005, pp. 193-198.
- Jodoin B., Adjelsztajn L., Berube G., Villafuer¬te J. Cold Spray Deposition of Metastable Alloys. Proc. Int. Therm. Spray Conf. Washington, ASM Int, 2006.
- Sansoucy E. Adjelsztajn L., Sansoucy E., Marcoux P. Properties of SiC-Reinforced Aluminum Alloy Coatings Produced by the Cold Spray Deposition Process. Proc. Int. Therm. Spray Conf. Ohio, ASM Int., 2007
- Li Ch.-J., Li W.-Y., Ma W.-H. Characterization of Microstructure of Nanostructured Fe-Si Coating Deposited by Cold Spraying. Thermal Spray Solutions. Advances in Technology and Application. Düsseldorf, 2004.
- Ichikawa Y. Deposition Mechanism of Cold Sprayed MCrAlY Coatings Focused on Nanostructure. Proc. Int. Therm. Spray Conf. Maastricht, 2008, pp. 479-480.
- Wang H.-T, Li C.-J., Yang G.-J., Li Ch.-X., Zhang Q., Li W.-Y. Microstructural Characterization of Cold Sprayed Nanostructured FeAl Intermetallic Compound Coating and its Ball-Milled Feedstock Powder. Journal of Thermal Spray Technology, 2007, vol. 16, pp. 669-676 DOI: 10.1007/s11666-007-9089-5
- Wielage T. CGS Sprayed Filler Coatings for Brazing of Light Weight Alloys. Proc. of Thermal Spray Conf. Thermal spray connects: Explore Its Surfacing Potential. Basel, 2005, pp. 1245-1249.
- Wang H.T. Formation of Fe-Al Intermetallic Compound Coating Through Cold Spraying. Proc. Int. Therm. Spray Conf. Washington, ASM Int., 2006.
- Novoselova T., Fox P., Morgan R., O'Neill W. Experimental Study of Titanium/Aluminium Deposits Produced by Cold Gas Dynamic Spray. Surface and Coatings Technology, 2006, vol. 200, no. 8, pp. 2775-2783 DOI: 10.1016/j.surfcoat.2004.10.133