Пути повышения точности при создании современных технологий многоинструментальной обработки
Автор: Кондратьев Александр Игоревич, Проничев Николай Дмитриевич
Журнал: Известия Самарского научного центра Российской академии наук @izvestiya-ssc
Рубрика: Механика и машиностроение
Статья в выпуске: 6-3 т.15, 2013 года.
Бесплатный доступ
В работе рассмотрены пути повышения точности при создании современных технологий, влияние технологических факторов и их информационные моделирование.
Современные инновационные технологии, много инструментальное оборудование, погрешность, технологическая система
Короткий адрес: https://sciup.org/148202618
IDR: 148202618
Текст научной статьи Пути повышения точности при создании современных технологий многоинструментальной обработки
При проектировании инновационных технологий необходимо решать вопросы повышения эффективности использования оборудования и инструментальных средств, которые используются при изготовлении деталей.
Для механической обработки в современном производстве широко внедряются многоинструментальные обрабатывающие центры с числовым программным управлением, которые имеют, существенны преимущества:
. высокую точность и жесткость технологической системы;
. широкие технологические возможности системы привязки программы к обрабатываемой заготовке и инструменту;
. возможность формирования большого количества размеров по I технологической схеме;
. использование режущего инструмента с повышенными технологическими возможностями (позволяющими уменьшить силы резания и снизить температуру в зоне обработки).
Современное много инструментальное оборудование обеспечивает высокую точность и жесткость за счет конструктивных особенностей, таких как применение современных типов приводов, использование новых типов линеек отсчитывающих положение стола или инструментального магазина, применение датчиков угловых положений, позволяющих с высокой точностью производить обработку, как по размерам поверхностей, так и по расположению.
Используемые интегрированные методы контроля и системы привязки инструментальных блоков на много инструментальных обраба-
тывающих центрах позволяют во время обработки, отслеживать положение заготовки и контролировать точность геометрических размеров [1].
При формировании большого количества размеров в одной операции с одной установки используется оптимальное количество инструментов, что обеспечивает группирование переходов и уменьшает погрешности связанные с базированием заготовки.
Применение современного металлорежущего инструмента, адаптированного под конкретные виды обработки требует его оптимизации с учетом точностных параметров, позволяет корректировать структуру технологического процесса, однако при этом необходимо анализировать условия проявления первичных погрешностей.
Их значимость в современных условиях обусловлена рядом технологических факторов. Рассматривая эти факторы, возможно, выявить природу их появления, и предложить пути устранения технологическими средствами, так и воздействием на зону обработки.
Каждый фактор вызывает образование характерных первичных погрешностей, к числу которых относятся:
. погрешности обработки, возникающие в результате упругих деформаций технологической системы под влиянием усилий резания;
. погрешности обработки, возникающие в результате температурных деформаций отдельных звеньев технологической системы;
. погрешности в результате действия внутренних напряжений в материале заготовки.
Из всего комплекса факторов, определяющих результативную погрешность обработки особую роль играют погрешности, вызываемые деформациями технологической системы.
В отличие от усилий закрепления, представляющие собой статическую нагрузку, усилия резания во многих случаях изменяются по величине и направлению, точки приложения их в про- цессе обработки непрерывно перемещаются. Эта особенность действие усилий резания вызывает непрерывное изменение деформации технологической системы, влекущее за собой искажение размера и формы обрабатываемой поверхности. Изменение деформации обусловливается также тем, что жесткость технологической системы обычно зависит от приложения нагрузки на различных участках заготовки.
При недостаточной жесткости детали искажения формы обработанной поверхности могут достигать значительных величин. В условиях создания технологических процессов механической обработки указанных деталей необходимо учитывать величину искажений в зависимости от принятой схемы закрепления.
На точность механической обработки влияют так же температурные деформации обрабатываемой заготовки. Нагрев происходит в результате выделения тепла в процессе резания. Разность между величиной внутренних напряжений растяжения при охлаждении и внутренних напряжений сжатия при нагревании определяет величину тепловых растягивающих остаточных напряжений поверхностного слоя. Тепловые остаточные напряжения растяжения могут возникнуть в поверхностном слое обрабатываемого изделия только в том случае, если внутренние напряжения, возникающие при нагревании, превзойдут по своей величине предел текучести данного материала и в нем произойдут термопластические деформации.
При обработке материалов, способных к фазовым превращениям, нагревание поверхностного слоя сопровождается не только термическим изменениями металла, вызывающими появление тепловых остаточных напряжений растяжения, но иногда одновременно и структурными превращениями металла, связанными с изменением удельных объемов поверхностных слоев [2].
Наличие в поверхностном слое металла изделия, обработанного резанием, на разных глубинах зон с различной структурой, а, следовательно, и с разными удельными объемами, приводит к возникновению в этих зонах значительных по величине остаточных напряжений различного знака.
При реализации инновационных технологий действие этих трех факторов является наиболее значимым, так как проявляется в условиях их взаимного влияния и требуют глубокого изучения.
В данной работе проводились экспериментальные исследования по проверке сходимости результатов, полученных с помощью теоретических методов, с данными, полученными экспериментально. На основе полученных результатов необходимо создавать модели высокого уровня, позволяющие исследовать действие каждого фактора.
Объектами исследований являлись:
. зависимости, полученные на с использования методы конечных элементов (МКЭ) для расчета средней температуры на поверхности твердого тела, в том числе и на участке, где происходит его соприкосновение с другими телами;
. закономерности изменения точности формы при токарной обработке тонкостенных деталей (с учетом их закрепления).
Исследование тепловых процессов в технологических системах тесно связано с проведением экспериментов по измерению температур на различных участках инструмента, заготовки или оборудования, а также с определением мощности и плотности тепловых потоков. Такие эксперименты необходимы, с одной стороны, для решения тех или иных задач опытным путем, а с другой – для проверки правильности и корректирования результатов теоритических построений, предназначенных для определения расчетным путем температур или характеристик источников выделения в зоне обработки [3].
При изучении тепловых процессов в процессе эксперимента определялись следующие характеристики:
. локальные температуры, в зоне обработке, т.е. температуры на небольшом участке твердого тела (условно в точке);
. среднее температуры на поверхности твердого тела, в том числе и на участке, где происходит его соприкосновение с другими телами (в зоне резания);
. законы распределения температур в различных зонах поверхности твердого тела.
Целью исследования являлось определение температуры на поверхности заготовки и на участке, где происходит соприкосновение обрабатываемой детали и режущего инструмента, т.е. в зоне резания.
После проведения расчетно-экспериментального исследования определения температуры в зоне резания получены следующие результаты:
. С увеличением скорости резания тепловой поток на поверхности возрастает, так как пропорционально скорости увеличивается общее количество теплоты, выделяемой в зоне резания.
. Часть тепла резания, поступающего в обрабатываемую деталь, существенно зависит от подачи. При увеличении подачи температура снижается, что может быть объяснено пропорциональным увеличением длины площадки контакта стружки с передней поверхностью.
. При обработке сталей температура резания сравнительно низкая не только из-за малой нагрузки, но и вследствие большой теплопроводности стали. И, наоборот, при резании титана, обладающего низкой теплопроводностью, значи- тельно повышается температура резания сравнительно с конструкционными сталями.
В результате выполненного анализа тепловых потоков и температур в зоне резания в зависимости от скорости установлены температурные ограничения при токарной обработке труднообрабатываемых материалов.
На основании проведенных исследований разработана методика измерения температуры в зоне резания в любых условиях токарной обработки различных труднообрабатываемых материалов.
При моделировании процессов, протекающих в детали при той или иной технологической операции, ряд необходимых параметров можно получить только опытным путем. Основными данными, требуемыми для распределения температуры по поверхности модели, является температура поверхности в двух контрольных точках. Указанные параметры определяют экспериментальным методом на образцах, изготовленных из материала детали. Так как деталью является цилиндрическое кольцо, то по его форме более удобно осуществлять построение модели средствами Ansys (рис. 1).
В настоящей работе была разработка методики экспериментального исследования тепловых процессов, в зоне резания с использование конечно – элементарного моделирования.
Неизвестный входной параметр Тр. (температуру резания) возможно определить в ходе решения обратной задачи теплопроводности на основании данных экспериментальных исследований. Решение сводится к поиску таких значений температур, для которых экспериментально -расчетные значения контролируемых параметров становятся наиболее близкими.
Температура резания определялась методом экстраполяции ее значений в зону вершины резца по результатам измерений температуры в двух точках на поверхности заготовки, что существенно упрощает проведение исследований, однако снижает точность полученных результатов.
Блок-схема экспериментально расчетного подхода показана на рис. 2.
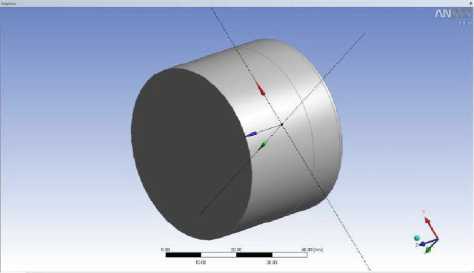
Рис. 1. Трехмерная модель
Контролируемыми параметрами являлись экспериментально установленные значения температур в двух точках (Т2 и Т3) на расстоянии L1 и L2 от источника тепла. При известных величинах длины от контакта инструмента с обрабатываемым материалом вычислялись значения температуры поверхности детали в зоне резания Т1. При этом температура резания Тр., являющейся искомым параметром подбиралась таким образом, чтобы обеспечивалось совпадение экспериментально – расчетных значений температур Т2 и Т3 в контрольных точках.
Одним из главнейших факторов, определяющих процесс резания, — теплота, образующаяся в результате работы резания. Законы теплообразования объясняют ряд явлений, связанных с нагрузкой резца, его стойкостью, качеством обработанной поверхности. [4]
При моделировании необходимо решить линейную нестационарную задачу теплопроводности, определяемую в общем случае уравнением:
дО д 2 0 дг0 дХ
— — а • (—у + 2 + 2- ) ∂ τ ∂ x ∂ y ∂ z
Необходимость решения нестационарной задачи, дает возможность проследить динамику изменения температуры по поверхности детали, что позволяет, сопоставляя расчетные и экспериментальные данные, оценить адекватность модели.
При резании заготовок малой длины за время одного прохода температурный режим в контрольных точках успевает измениться незначительно, что позволяет использовании стационарную модель.
Для расчета температуры на поверхности заготовки необходимо из геометрической модели (рис. 1) создать конечно-элементарную модель.
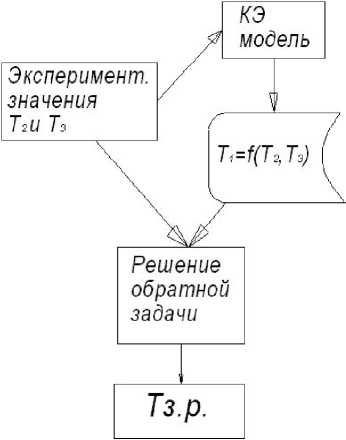
Рис. 2. Блок-схема экспериментально-расчетного метода определения температуры резания
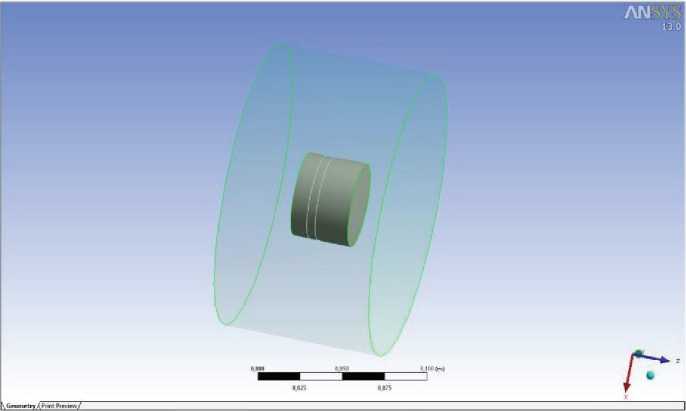
Рис. 3. Имитация объема воздуха и детали
Одним из этапов являлась положение конечно – элементарной сетки и задание теплового потока на поверхности заготовки. Так как в процессе резания источник тепла перемещается, как правило, по спирали с малым шагом то целесообразно задавать распределение тепла на поверхность детали от широкого кольца.
При КЭ моделировании использовались элементы с параболической аппроксимацией, содержащие 10 узлов, каждый из которых имеет одну степень свободы. Такой тип элементов предназначен для решения теплофизических задач и обеспечивает достаточно точное решение при свободной разбивке твердотельной модели.
Для имитации реальных условий обработки создавался объем воздуха и объем детали в одной системе (рис. 3).
При точении массивными резцами период нестационарного теплообмена не велик. Тепловые потоки, проходящие через поверхности контакта «резец – заготовка - стружка», быстро стабилизируется и температура контактных поверхностей в дальнейшем изменяется незначительно. В этой связи, полагая, что температура резания не зависит от времени, на контактных поверхностях инструмента устанавливаются граничные условия первого рода.
в( x, y, z) = Ta..
Характер распределения температуры вдоль контактных площадок инструмента можно не учитывать, так как это не оказывает влияние на результат решения задачи в точках, достаточно удаленных от источника тепловой нагрузки.
С использованием разработанной модели были исследованы изменения температуры по длине заготовки в продольном сечении на поверхности детали (рис. 5), на расстоянии 5 мм от поверхности (рис. 5 ) и в поперечном сечении по всему сечению детали (рис. 5).
Из графиков, представленных на рис. 5, видно, что температура от длины заготовки изменяется по параболическому закону. Разница максимальных температур в зоне резания на поверхности заготовки и 5 мм от поверхности составила 15 С.
Таким образом, разработанная методика определения температуры резания при токарной
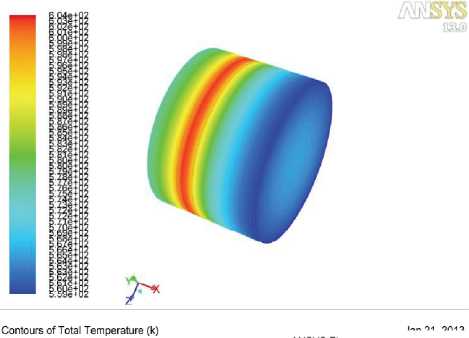
Jan 21,2013
ANSYS FLUENT 13,0 (3d, pbns, ske)
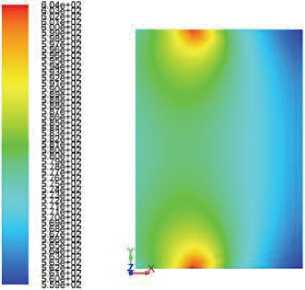
Рис. 4. Распределение температуры по поверхности детали
6.03еЮ2
6.00е+02
5.98е+02
6.00е+02
5.95е+02
5.90е+02
5.856+02
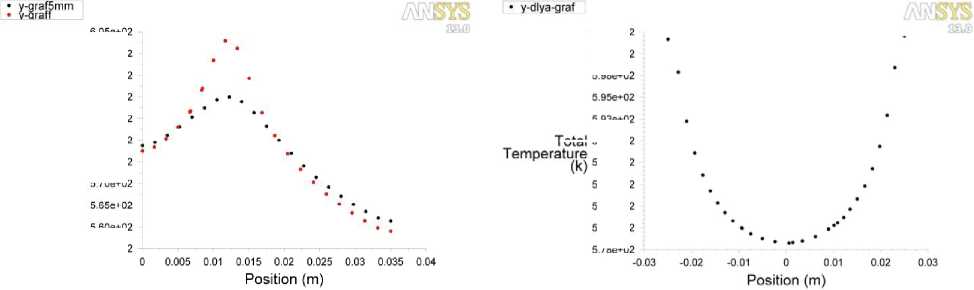
578е+02
5.606+02
5.55е+02
Total Temperature
Jan 21, 2013
ANSYS FLUENT 13.0 (3d. pbns, ske)
6056+02
Total 5 80e+02 Temperature
^J 5.75e+02
5.706+02
Рис. 5. Зависимость изменение температуры от длины заготовки
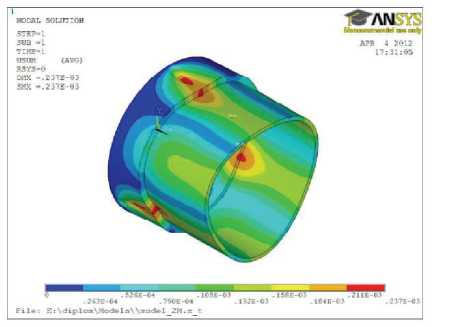
5.936+02
Total 5.90е+02
5.886+02
5.856+02
5.836+02
5.806+02
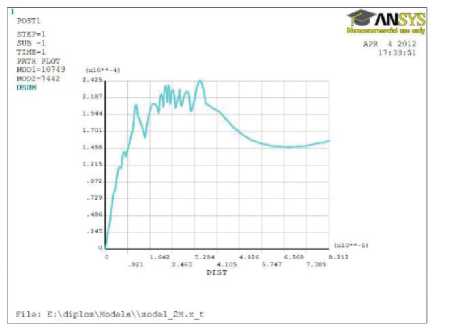
Рис. 6. Распределение перемещений кольца от усилия зажима и график зависимости перемещения от силы для тонкостенного кольца
обработке, которая основана на сопоставлении экспериментальных результатов, полученных в процессе резания, с данными, результатов конечно-элементного моделирования обрабатываемой заготовки, обеспечивает получение результатов имеющих точность достаточную для инженерного анализа технологических процессов.
При закреплении нежестких заготовок, помимо их возможного смещения, наблюдается деформация общего характера, которая охватывает более или менее значительные участки, непосредственно находящиеся в зоне обработки. В этом случае поверхности, подвергаемые обработке, получают соответствующие искажения формы.
В работе проводилось исследование влияния остаточных деформаций, возникающих в процессе закрепления заготовки в трехкулачковый патрон, на точность формы тонкостенных колец.
В программе Ansys была проанализирована модель закрепления тонкостенного кольца.
В результате проведенного исследования выявлена связь между деформациями тонкостенных колец и усилия зажима при их консольном закреплении. Одним из элементов разработки инновационных технологических процессов меха- нической обработки материалов необходимо использовать моделирование физических и температурных влияний на поверхность заготовки. В рамках данной работы отработаны режимы для обработки маложестких деталей типа “кольцо” при различных условиях закрепления. Рассмотрены остаточные деформации передающиеся на всю длину заготовки при закреплении, а разработана компьютерная модель процесса закрепления колец, позволившая провести исследования возникающих погрешностей.
Список литературы Пути повышения точности при создании современных технологий многоинструментальной обработки
- Анализ проблем, возникающих при создании технологий токарно-фрезерной обработки в аэрокосмической отрасли/А.И. Кондратьев, А.И. Кузнецов, Н.Д. Проничев//Тез. докл. симпозиума с международным участием “Самолетостроение. Проблемы и переспективы”. 2011. С. 320.
- Повышение эффективности технологической подготовки производства при использовании обратных постпроцессоров (виртуальных станков)/А.И. Кондратьев, В.Г. Смелов, Н.Д. Проничев, О.С. Суркова//Материалы докл. междунар. науч.-тех. конф. “Проблемы и перспективы развития двигателестроения”. Самара: Самар. гос. аэрокосм. ун-т, 2011. Ч.2. С. 320-322.
- Хаймович А.И., Кузнецов А.В. Аналитическое моделирование силового режима высокоскоростного фрезерования материала с вязкопластическим//Тез. докл. симпозиума с международным участием “Самолетостроение. Проблемы и перспективы”. 2011. С. 402.
- Анализ точностных параметров токарно-фрезерного оборудования изменяющегося в процессе эксплуатации при изготовлении высокоточных деталей ГТД/А.И. Кондратьев, А.И. Кузнецов, Н.Д. Проничев//Международный научно-технический форум, посвященный 100-летию ОАО “КУЗНЕЦОВ” и 70-летию СГАУ. 2012. С. 240 -243.