Расчет основных параметров устройства для переработки полимерных отходов
Автор: Сынюк О.Н., Кулик Т.И.
Журнал: Вестник Витебского государственного технологического университета @vestnik-vstu
Рубрика: Технология и оборудование легкой промышленности и машиностроения
Статья в выпуске: 2 (33), 2017 года.
Бесплатный доступ
В статье рассматривается проблема переработки полимерных отходов на валковых устройствах с возможностью дальнейшего их использования в качестве армирующих элементов композитных материалов. Целью исследования является разработка рациональной конструкции устройства для обеспечения качественного расщепления аморфно-кристаллических полимеров с минимальными энергетическими затратами. Разработана математическая модель процесса деформации полимерного материала между зубчатыми валками устройства, получены аналитические зависимости величины относительной деформации сжатия материала в зависимости от конструктивных параметров зубчатых валков. В результате проведенных исследований предложены оптимальные значения диаметра зубчатых валков, высоты зубьев и угла профиля зубьев для переработки наиболее распространенных полимерных материалов - полиэтилена, полиэтилентерефталата, полипропилена. Разработанные рекомендации могут быть использованы для изготовления энергоэффективного перерабатывающего оборудования.
Переработка отходов, конструктивные параметры, полимерные отходы, механическое расщепление, валковые устройства, энергоэффективность
Короткий адрес: https://sciup.org/142212348
IDR: 142212348
Текст научной статьи Расчет основных параметров устройства для переработки полимерных отходов
ПОЛИМЕРНЫЕ ОТХОДЫ, ПЕРЕРАБОТКА ОТХОДОВ, МЕХАНИЧЕСКОЕ РАСЩЕПЛЕНИЕ, ВАЛКОВЫЕ УСТРОЙСТВА, КОНСТРУКТИВНЫЕ ПАРАМЕТРЫ, ЭНЕРГОЭФФЕКТИВНОСТЬ
В статье рассматривается проблема переработки полимерных отходов на валковых устройствах c возможностью дальнейшего их использования в качестве армирующих элементов композитных материалов. Целью исследования является разработка рациональной конструкции устройства для обеспечения качественного расщепления аморфно-кристаллических полимеров с минимальными энергетическими затратами. Разработана математическая модель процесса деформации полимерного материала между зубчатыми валками устройства, получены аналитические зависимости величины относительной деформации сжатия материала в зависимости от конструктивных параметров зубчатых валков. В результате проведенных исследований предложены оптимальные значения диаметра зубчатых валков, высоты зубьев и угла профиля зубьев для переработки наиболее распространенных полимерных материалов – полиэтилена, полиэтилентерефталата, полипропилена. Разработанные рекомендации могут быть использованы для изготовления энергоэффективного перерабатывающего оборудования.
polymer waste, waste processing, mecha NICAL SPLITTING, ROLLER DEVICES, CONSTRUCTIVE PARAMETERS, ENERGY EFFICIENCY
The article considers the problem of processing polymeric waste on roller machines with the possibility of further use as reinforcing elements of composite materials. The aim of the study is to develop a rational design of the device to ensure the qualitative splitting of amorphous-crystalline polymers with minimal energy costs. A mathematical model of the deformation process of polymeric material between the gear rolls is developed, and analytical dependences of the value of the relative deformation of the material compression are obtained depending on the design parameters of the gear rolls. As a result of the research, the optimal values of the diameter of the toothed rolls, the tooth heights and the profile angle of the teeth for the processing of the most common polymeric materials (polyethylene, polyethylene terephthalate, polypropylene) are proposed. The developed recommendations can be used for manufacturing energy-efficient processing equipment.
В современном мире непрерывно увеличивается потребление пластмасс, в связи с чем особое значение приобретает проблема их утилизации.
Полимерные отходы считаются наиболее экологически опасными, поскольку полимеры мало подвержены саморазложению. В нашей стране утилизации полимеров уделяется недостаточное внимание – чаще всего такие отходы хранятся на полигонах и свалках или сжигаются в печах с остальным твердым мусором, что в обоих случаях наносит существенный урон окружающей среде. Почва и вода, контактирующие с пластиком, насыщаются вредными химическими веществами (формальдегидом, фенолом, стиролом, уретаном и т. д.). Сжигание полимерных отходов вызывает выделение ядовитых газов, в том числе диоксина. Кроме того, важно учитывать, что подавляющее большинство пластиков производится из невозобновляемого углеводородного сырья, запасы которого ограничены. Поэтому, в условиях дефицита полимерного сырья, повторное использование материала имеет не только экологическое, но и экономическое значение – рециклинг полимеров позволяет существенно сэкономить первичное сырье и электроэнергию на производство [1–2]. Таким образом, использование вторичных ресурсов с максимальной эффективностью является крайне актуальным заданием, от решения которого зависит благополучие и безопасность как окружающей среды, так и всего человечества.
Значительная часть полимерных отходов может быть переработана для вторичного использования. Для этого необходимо выбрать рациональный способ переработки и эффективное оборудование для его реализации. Термические и химические методы утилизации полимеров, такие как пиролиз, крекинг, каталитический термолиз, деполимеризация являются эффективными, но весьма дорогостоящими технологиями, часто наносящими урон окружающей среде. Их применение оправдано в случае, когда отходы не находят практического использования и не могут быть переработаны в изделия либо введены в состав различных композиций. Поэтому наиболее распространенным и рациональным способом переработки полимерных отходов на сегодня остается механическая обработка. При таком способе отходы измельчают, очищают и подвергают агломерации или грануляции, после чего возвращают в производственный цикл. Таким образом, можно перерабатывать как отходы потребления, так и производственные отходы с дальнейшим использованием их в дорожном строительстве, в производстве строительных материалов, мебельной фурнитуры, емкостей и пленок для упаковки и т. д.
Существует большое количество машин для переработки полимерных отходов, позволяющее получить материал заданных параметров. К перерабатывающему оборудованию выдвигается ряд требований, среди которых основными являются: качество переработки, степень дисперсности исходного материала, энергозатраты на переработку единицы объема материала, производительность оборудования. В оборудовании для механического измельчения используются различные физические эффекты – раздавливание, истирание, расщепление, удар, резка, раскалывание, ультразвуковые, температурные, кавитационные [3].
Данная работа посвящена проектированию валковых устройств. Целью исследования является разработка рациональных конструктивных параметров устройства для обеспечения качественного дробления полимерных отходов с минимальными затратами энергии.
Принцип работы валковых дробилок состоит в том, что под действием сил трения материала происходит раздавливание его между цилиндрическими валками, вращающимися с одинаковой скоростью навстречу друг к другу с последующим отсеиванием измельченного вещества. Устройства такого типа имеют ряд преимуществ: однородность формы фракции на выходе, простую механическую конструкцию, экономичность и эффективность использования, высокую надежность и безопасность.
При расчете основных параметров непрерывного процесса переработки полимерных отходов в зубчатых валках могут встречаться два типа задач:
– при заданных геометрических размерах валков (радиус и длина рабочей части) и скоростях вращения необходимо определить производительность;
– при заданной производительности необходимо определить основные геометрические размеры зубчатых валков и оптимальную скорость их вращения.
В данной работе решается вторая задача.
В процессе воздействия на полимерный материал зубчатых валков последний подвергается таким деформациям: растяжения, сжатия и изги- бы [4]. Внутренний слой полимерного материала на вершине зубцов будет вытягиваться под действием растягивающих напряжений и сжиматься под действием напряжений изгиба (рисунок 1).
Таким образом, деформация растяжения внутреннего слоя будет компенсироваться деформацией его сжатия, а деформация наружного слоя полимерного материала увеличится за счет растяжения, имеющего место при изгибе. В результате того, что вершины и впадины зубцов имеют различные радиусы вращения, возникает тангенциальное напряжение, вызываемое силами трения.
Следовательно, при переработке полимерного материала в зубчатых валках мощность будет расходоваться на деформацию растяжения материала, деформацию сжатия и на преодоление сил трения.
С учетом вышесказанного суммарный крутящий момент представим в следующем виде:

где Tраст – момент сил, вызывающих растяжение полимерного материала; T ñæ – момент сил, вызывающих сжимание полимерного материала; Tò – момент сил трения.
В процессе прохождения между зубчатыми валками полимерный материал подвергается деформациям растяжения и сжатия по всей толщине. Расчетная схема переработки полимера представлена на рисунке 2.
Полимерный материал с исходной толщиной h1 входит в зону действия зубчатых валков, имея на выходе из неё толщину h2 (рисунок 2). Для расчета разрабатываемого устройства следует предварительно определить деформацию полимерного материала, необходимую для получения ориентированной структуры. Процесс перехода аморфно-кристаллических полимеров из неориентированного состояния в высокоориентированное является одной из стадий расслоения полимерных отходов на элементы, которые можно использовать в качестве армирующих элементов композитных материалов [5, 6].
Примем следующие допущения:
– релаксация деформации отсутствует;
– область влияния на полимер – только в плоскости осей зубчатых валков.
Согласно [1] деформация полимерного материала в зубчатых валках происходит в два этапа: растяжение полимерного материала между двумя зубчатыми валками и изгиб полимерного материала на вершинах зубцов.
Таким образом, согласно рисунку 2, относительное растяжение можно определить из уравнения:
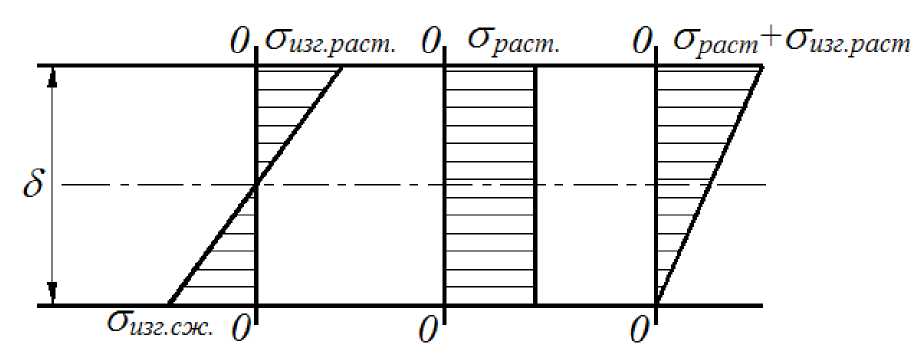
Рисунок 1 – Эпюра внутренних напряжений, возникающих в полимерном материале
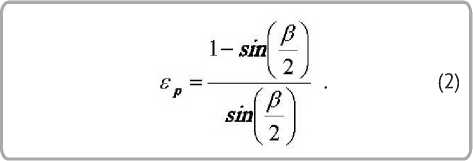
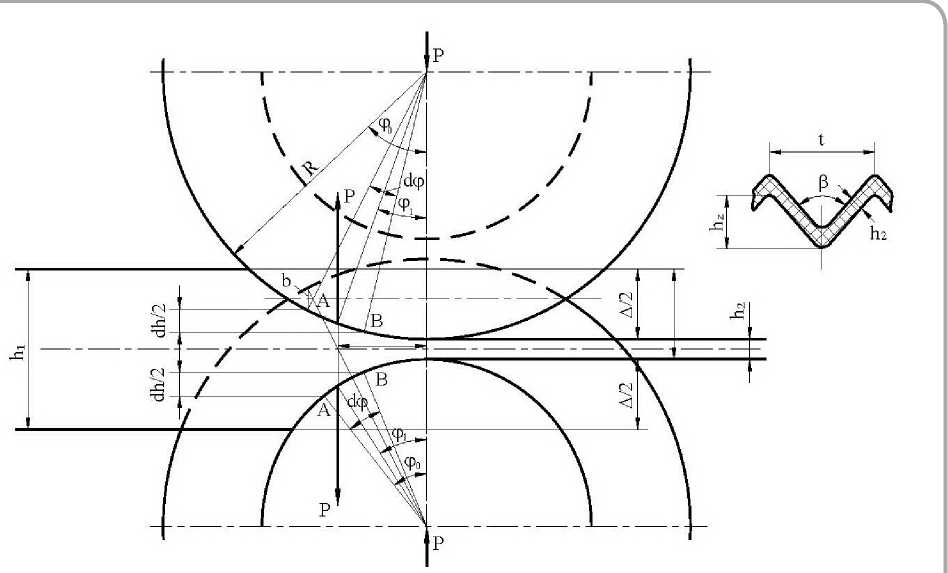
Рисунок 2 – Расчетная схема деформирования полимерного материала в зубчатых валках
Деформация растяжения, определённая с помощью (2), обеспечивает ориентированную структуру полимерного материала.
С другой стороны, деформация растяжения может быть определена согласно [4] следующим образом:
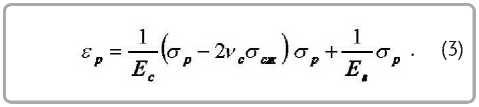
Подставив (3) в (2) и решив полученное выражение относительно β , получим
Из уравнения (4) можно определить угол профиля зубцов валкового устройства для переработки полимерных отходов, при котором обеспечивается ориентированная структура полимерного материала, проходящего между валками.
Полимерный материал между двумя зубцами принимает вид равнобедренного треугольника (рисунок 2). Высота этого треугольника равна hz , основа – t . Из рисунка 3 видно, что растяжение полимерного материала начинается на участке φ 0... φ 1 и заканчивается на участке φ 0...0 . Затем полимерный материал сжимается между боковыми поверхностями зубьев (участок φ 1...0 ), а на участке φ 0... φ 1 растягивается, что приводит к уменьшению толщины от начальной h1 до h1(1 – νɛp) .
Коэффициент Пуассона ν полимерного материала определяем согласно [3]
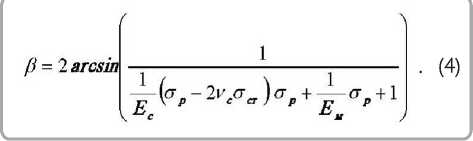
3EV-E 6EV
где E ν – модуль объемной упругости, который может быть представлен выражением [3]
, -5,(1 +v' )+2/2Е (1-2v 2Е (1 -/2\1-2v )
5V ~" ^* 3 |^ (l ^,2^ 2v X^ + v ) + J2 (1 + ^ X^ 2 v ) + 2E (1 2v Xl 2v )] , (6)
где χ – степень кристалличности (определяется типом кубической решетки упаковки сферолитов в материале [2]); Ec , νc – модуль упругости и коэффициент Пуассона сферолита (выбираются из справочной литературы); Eì , νì – модуль упругости и коэффициент Пуассона аморфной матрицы (выбираются из справочной литературы); E – модуль упругости полимерного материала сферолитного строения.
Модуль упругости E определяется выражением [6]
h1
6=22?--H cosy -1 + hz - 62 .(11)
(22?J
Из рисунка 2, учитывая (11), определим деформацию растяжения полимерного материала:
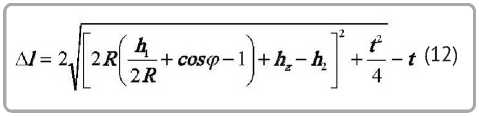

и относительную деформацию
Согласно рисунку 2, межосевое расстояние равно a = 2Ксо§фй + Д = R + Д + 2?- 6, , (8)
>
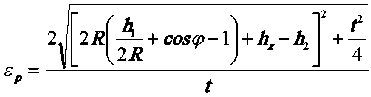
-1 . (13)
где R – радиус зубчатых валков.
Учитывая, что h2 – h1 = ɛСТh1 , из уравнения (8) определим угол, при котором полимерный
На рисунке 2 видно, что в результате прохождения полимерного материала между зубцом одного валка и впадиной другого, его толщина материал захватывается валками. В соответствии изменяется на величину

поэтому при расчете изменения толщины мате-
где ɛ ст – деформация сжатия полимерного материала.
Изгиб полимерного материала определяется соотношением риала необходимо учитывать величину, которая является постоянной для определенного перерабатывающего устройства. Учитывая вышесказанное, перепишем (14) следующим образом:
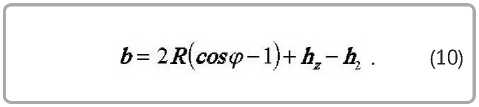
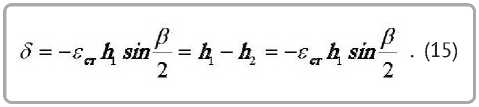
С учетом толщины материала выражение (10) принимает вид
Решая уравнение (15) относительно угла с учетом уравнений (8) и (9), получим следующее выражение:
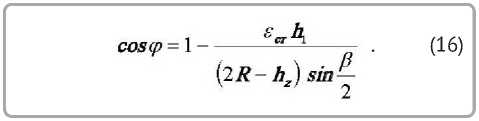
лата – ɛp = 0,93 ; для полипропиленовой пленки – ɛp = 0,78 [7].
Из уравнения (16) с учетом выражения (14) получим выражение для определения толщины полимерного материала при определенном угле вращения зубчатых валков:
При угле вращения зубчатых валков φ 1 расстояние между боковыми поверхностями зубьев будет равняться конечной толщине полимерного материала h2 , то есть h1(1 – νɛ p) . Тогда из уравнения (16) косинус угла φ 1 равен
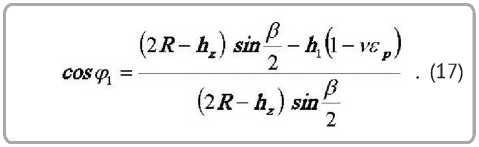
Результаты вычислений по формуле (17) представлены на рисунке 3.
По рисунку 3 можно определить, что разница между значениями углов вращения зубчатых валков, при которых заканчивается упругая и начинается пластическая деформация полимерных материалов, составляет величину меньше 10 . Таким образом, в дальнейших расчетах можно использовать значение угла вращения зубчатых валков, при котором начинается пластическая деформация полимерного материала. Так, для полиэтиленовой пленки это соответствует деформации ɛp = 0,85 ; для полиэтилентерефта-
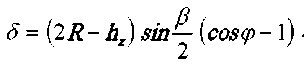
На рисунке 4 приведены графические зависимости толщины δ полимерного материала от угла вращения зубчатых валков φ при различных значениях угла профиля зубцов β .
На графиках можно видеть, что чем больше угол профиля зубьев, тем больший требуется угол вращения валков для получения заданной толщины полимерного материала, при которой начинается его пластическая деформация. А больший угол вращения зубчатых валков требует большего расхода электрической энергии.
Для обеспечения необходимого усилия прижатия полимерного материала к вершинам зубцов, при котором отсутствует скольжение материала по боковой поверхности зуба, необходимо, чтобы угол профиля был как можно меньше. Кроме того, как известно [4], чем меньше угол профиля зубьев, тем большей будет деформация полимерного материала.
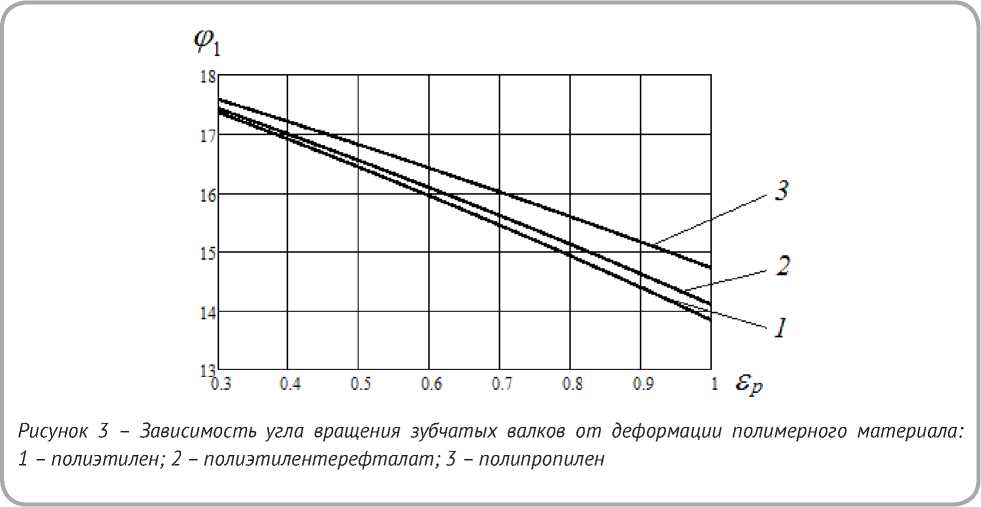
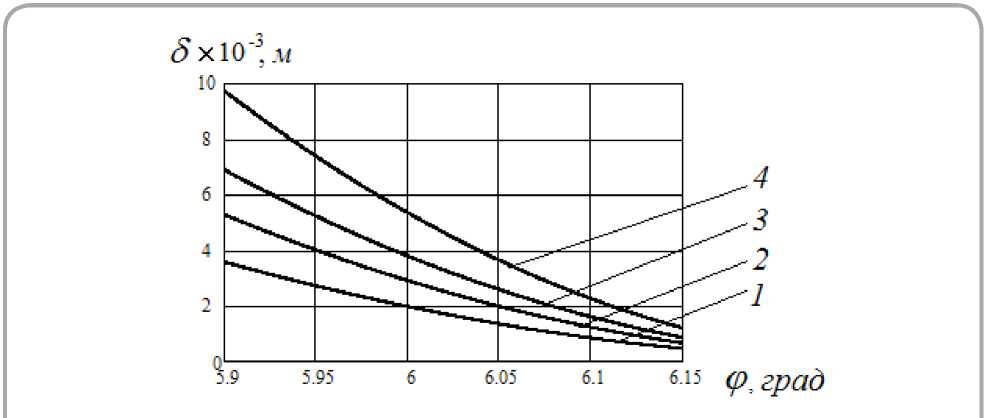
Рисунок 4 – Зависимость толщины полимерного материала от угла вращения зубчатых валков при значениях угла профиля зубьев: 1 – β = 300; 2 – β = 450; 3 – β = 600; 4 – β = 900
С другой стороны, угол профиля зубьев должен быть не менее критического значения, при котором возможно разрушение самих зубьев.
В дальнейшем будет проведен силовой расчет процесса деформации полимерного материала в зубчатых валках, который определит минимальное значение угла профиля зубцов.
При вращении зубчатых валков на угол d φ толщина полимерного материала изменится на dδ , то есть:
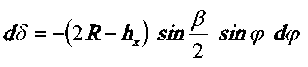
.
Относительную деформацию сжатия ɛ СТ определим из зависимости
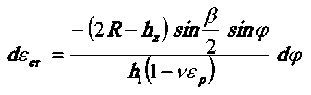
.
Проинтегрировав (20), получим
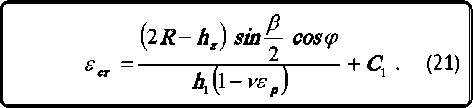
Для определения постоянной интегрирования воспользуемся начальными условиями деформации полимерного материала, то есть
ɛ ст = 0 при φ = φ 1 :
(21t-hz^ sin—
Ц =-- 7------г^- СО8фг . (22)
Подставив значение постоянной интегрирования в (21) получим выражение для определения максимальной относительной деформации сжатия полимерного материала при прохождении его между зубчатыми валками:
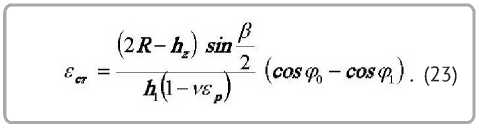
С целью фиксации полимерного материала в растянутом состоянии следует подвергнуть его сжатию, что можно осуществить, вращая зубчатые валки на угол от φ0 до φ1, где φ0 – угол, при котором начинается упругая деформация полимерного материала, а φ1 – угол, при котором заканчивается упругая и начинается пластическая деформация полимерного материала (определяются из уравнения (17)). При этом уменьшается прочность полимерного материала в направлении, перпендикулярном растяжению. Далее ослаблен полимерный материал пропус- кают между валками, имеющими профиль Рьоло.
Определяемая по выражению (23) деформация сжатия е ст , которую обеспечивает устройство с вращающимися зубчатыми валками, не должна быть меньше значения деформации сжатия £ 2 , полученной из [8], которая обеспечивает пластическую деформацию в направлении, поперечном к направлению извлечения полимерного материала. В результате осуществляется фиксация растянутого полимерного материала.
На рисунке 5 приведена зависимость высоты зубьев hz от значения деформации сжатия г СТ при разных углах профиля зубьев для следующих полимерных материалов:
-
- полиэтилена ( E c = 1020 МПа, v c = 0,37 ; E ^ = 77 МПа, v ^ = 0,39 ; х = 0,68 );
-
– полиэтилентерефталата ( Ec = 8239 МПа, v c = 0,32 ; Бж = 2000 МПа, vm = 0,39 ; х = 0,40 );
-
- полипропилена ( E c = 2500 МПа, v c = 0,32 ; Бж = 92 МПа, v ^ = 0,45 ; х = 0,75 ).
Анализ результатов, представленных графическими зависимостями на рисунке 5, показывает, что для обеспечения фиксации предварительно ориентированной структуры полимерного материала необходимо определить такие конструкционные параметры устройства, при которых обеспечивается нужная деформация сжатия. Так, например, для фиксации вытянутой структуры полиэтиленовой пленки (рисунок 5 а ) согласно [8] необходимо обеспечить деформацию сжатия ɛ с = 0,65 , которая может быть создана валками диаметром D = 100 мм с высотой зубьев hz = 8 мм и углом профиля зубьев в = 30 0 . Кроме того, в зависимости от толщины полимерного материала, можно изменять зазор между зубчатыми валками. Это обеспечит требуемое значение деформации сжатия для полимерных отходов различной толщины.
Аналогичный анализ графиков выполняется для полиэтилентерефталата и полипропиленовой пленки (рисунок 5 б , в ).
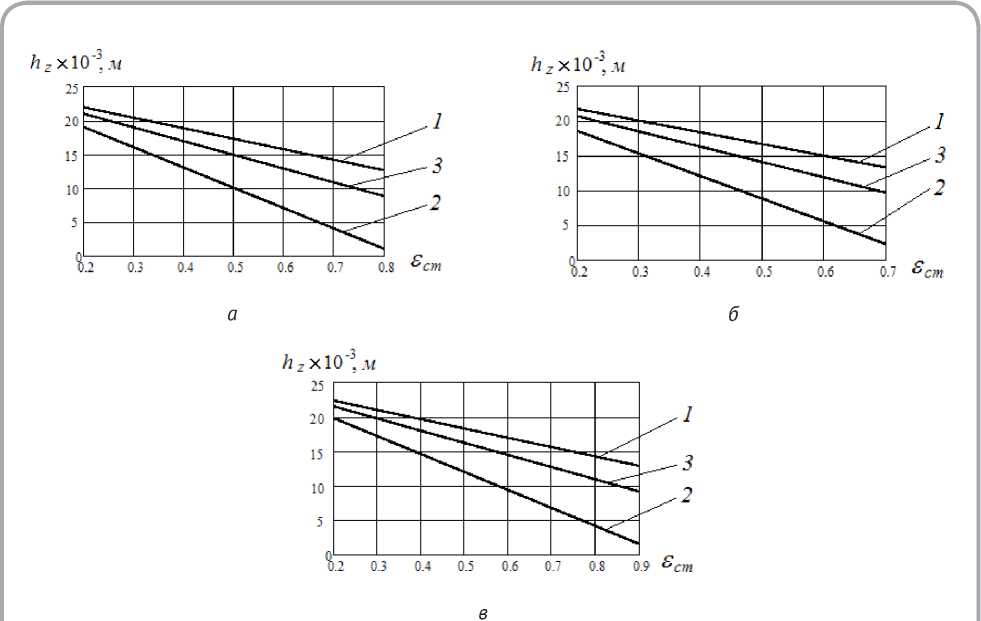
Рисунок 5 - Зависимость высоты зубьев h z от значения деформации сжатия £ СТ при значениях угла профиля зубьев 1 - в = 60 0 ; 2 - в = 30 0 ; 3 — в = 45 0 для различных материалов: а - полиэтиленовая пленка; б – полиэтилентерефталат; в – полипропиленовая пленка ________________________________________________________/
ВЫВОДЫ
При проектировании устройства для переработки полимерных отходов необходим предварительный расчет значений его основных параметров, таких как: диаметр зубчатых валков, высота зубьев, угол профиля зубьев, частота вращения валков, при которых обеспечивается ориентированная структура полимерного материала. Полученные значения этих параметров можно использовать для изготовления энергоэффективного перерабатывающего оборудования.
Аналитические исследования влияния конструктивных параметров на деформацию растяжения и сжатия полимерного материала для обеспечения необходимой для дальнейшей переработки структуры материала позволили разработать рекомендации для переработки таких полимерного материалов:
– для переработки полиэтиленовой пленки необходимо, чтобы диаметр зубчатых валков составлял от 70 до 100 мм, рекомендуемая высота зубьев – 6 ... 8 мм, угол профиля зубьев – 30 ... 450º;
– для полиэтилентерефталата необходимо, чтобы диаметр зубчатых валков составлял от 60 до 120 мм, высота зубьев – 4 ... 6 мм, угол профиля зубьев – 40 ... 600º;
– для полипропиленовой пленки необходимо, чтобы диаметр зубчатых валков составлял от 90 до 130 мм, высота зубьев – 4 ... 8 мм, угол профиля зубьев – 45 ... 700º.
Таким образом, для переработки полимерных материалов, указанных выше, рекомендуется спроектировать устройство с вращающимися зубчатыми валками с такими конструктивными параметрами: диаметр валков D = 100 мм, высота зубьев hz = 6 мм, угол профиля зубьев β = 300 .
Список литературы Расчет основных параметров устройства для переработки полимерных отходов
- Бутко, А. Е. (2015), Украинский рынок утилизации полимерных отходов и ключевые тенденции его развития, Молодий вчений, 2015, № 2(17), С. 139-142.
- Базунова, М. В., Прочухан, Ю. А. (2008), Способы утилизации отходов полимеров, Вестник Башкирского университета, 2008, Т. 13, № 4, С. 875-885.
- Рубанка, М. М., Мiсяць, В. П. (2015), Вiдходи легкої промисловостi, способи переробки та областi подальшого використання, Вiсник Київського нацiонального унiверситету технологiй та дизайну, 2015, № 4, С. 34-39.
- Синюк, О. М. (2017), Визначення рацiональних конструкцiйних параметрiв пристроїв для переробки полiмерiв, Вiсник Тернопiльського нацiонального технiчного унiверситету, 2017, № 3, С. 42-49.
- Синюк, О. М., Скиба, М. Е. (2016), Моделювання змiни надмолекулярної структури полiмерних матерiалiв при орiєнтацiйнiй витяжцi, Вiсник Хмельницького нацiонального унiверситету, 2016, № 6, С. 45-52.
- Синюк, О. М. (2016), Визначення пружних властивостей аморфно -кристалiчних полiмерiв сферолiтної структури, Вiсник Вiнницького полiтехнiчного iнституту, 2016, № 6, С. 77-86.
- Ван Кревелен, Д. В. (1972), Свойства и химическое строение полимеров, Москва, Химия, 416 с.
- Синюк, О. М., Михайловський, А.Ю. (2017), Визначення ефективних пружних властивостей орiєнтованих полiмерiв в поперечному напрямку, Вiсник Хмельницького нацiонального унiверситету технологiй та дизайну, 2017, № 3, С. 29-38.