Разработка легирующих флюсов для износостойкой наплавки деталей подвижного состава с использованием минерального сырья дальневосточного региона
Автор: Макиенко В.М., Атеняев А.В., Перваков Д.Г., Белоус Т.В.
Журнал: Журнал Сибирского федерального университета. Серия: Техника и технологии @technologies-sfu
Рубрика: Исследования. Проектирование. Опыт эксплуатации
Статья в выпуске: 8 т.16, 2023 года.
Бесплатный доступ
В работе приведены результаты исследований по разработке плавлено-керамических флюсов для износостойкой наплавки деталей подвижного состава. Разработана методика получения флюсов. Проведены теоретические расчеты и экспериментальные исследования, по результатам которых были получены флюсы (гранодиорит - 5,8 %, флюорит - 3,7 %, мрамор - 4,1 %, циркониевый концентрат - 4,9 %, ферромарганец - 19,6 %, титаномагнетит - 3,7 %, браунит - 1,2 %, шеелит - 2,1 %, графит - 5,5 %, феррохром - 28,9 %, АН22, или АН348А - 20,6 %). Требуемые свойства обеспечиваются за счет восстановления легирующих элементов и образования в наплавленном слое карбидов хрома (Cr7C 3), железа (Fe3C) и других веществ.
Шлаковая основа, минеральное сырье, сварочный флюс, сварочно-технологические свойства, твердость, износостойкость, рентгеноспектральный микроанализ, термодинамический расчет, металлургические процессы, легирующие элементы, карбиды
Короткий адрес: https://sciup.org/146282755
IDR: 146282755
Текст научной статьи Разработка легирующих флюсов для износостойкой наплавки деталей подвижного состава с использованием минерального сырья дальневосточного региона
Цитирование: Макиенко В. М. Разработка легирующих флюсов для износостойкой наплавки деталей подвижного состава с использованием минерального сырья Дальневосточного региона / В. М. Макиенко, А. В. Атеняев, Д. Г. Перваков, Т. В. Белоус // Журн. Сиб. федер. ун-та. Техника и технологии, 2023, 16(8). С. 956–966. EDN: KYKZDE состав компонентов в целях получения формируемых покрытий с требуемыми механическими и эксплуатационными свойствами.
Выбор компонентов Дальневосточного минерального сырья для шлаковой системы проводился на основе стандартных флюсов АН348А, АН22, а также по результатам предварительных экспериментов [1].
Анализ возможных химических реакций в шлаке выполнялся по результатам термодинамических расчетов (энергии Гиббса) [2] с использованием программы «Mathcad».
Предварительные расчеты оксидного состава шихты, основности и химической активности шлака выполнялись согласно методике [3].
Для получения рационального состава компонентов флюса проводились экспериментальные исследования, основанные на построении расчетных моделей и диаграмм, влияния состава флюса-шлака на качество и свойства формируемых покрытий [4]. При этом устанавливались зависимости между входными (состав шихты) и выходными (показатели качества и свойств) параметрами. Данная задача решалась с помощью экспериментально-статистических методов. В этом случае схема объекта исследования (электротермический процесс) представлена на рис. 1.
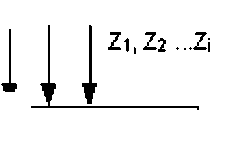
Объект исследований
Рис. 1. Схема объекта исследований
-
Fig. 1. Schematic diagram of the research object
При решении задач по созданию новых материалов с использованием минерального сырья при электродуговых процессах шлаковые системы наиболее полно описываются приведенным полиномом четвертого порядка:
у = 1 х 1+2 х 2+3 х 3+12 х 1 х 2+13 х 1 х 3+23 х 2 х 3+12 х 1 х 2( х 1– х 2)+ +13 х 1 х 3 ( х 1 – х 3 )+23 х 2 х 3 ( х 2 – х 3 )+12 х 1 х 2 ( х 1 – х 2 )2+13 х 1 х 3 ( х 1 – х 3 )2+ +23 х 2 х 3 ( х 2 – х 3 )2+1123 х 2 1 х 2 х 3 + 1223 х 1 х 2 2 х 3 + 1233 х 1 х 2 х 2 3 ,
где: x 1 , x 2 , x 3… х n – содержание компонентов смеси ( x i = 1), y 1 , y 2 , y 3 , y 123 и т.д. – значения откликов системы в узлах симплексной решётки, которые определяются опытным путем. По результатам полученных значений откликов получали математические зависимости, строили диаграммы влияния состава шихты на свойства формируемых покрытий .
Результаты исследований и их анализ
Для разработки шлаковой основы были проведены исследования по определению составов флюорита, гранодиорита, мрамора, браунита, шеелитового, бадделеитового и датолитового концентратов, а также титаномагнетитового шлиха. Например, браунит используется в качестве шлакообразующего вещества. Результаты исследований браунита приведены на рис. 2.
Исследования морфологии элементного составов (рис. 2а) показали, что браунит является многокомпонентным веществом, содержащим элементы (марганец, кремний, алюминий, кальций и другие), используемые для производства сварочных материалов. Результатами фазового анализа установлено, что элементы в минеральном сырье находятся в виде оксидов, сульфидов и других соединений (например, MnSiO, Mn7O8(SiO4) Mn2O3).
Шлаковая основа разрабатывалась на базе стандартных флюсов АН22, АН348А и минерального сырья Дальневосточного региона. В этих целях были выбраны следующие компоненты: шлакообразующие (флюорит, гранодиорит, мрамор); стабилизирующие (титаномагнетит); легирующие (шеелит, браунит); связующие (жидкое стекло). Оксидный состав выбранного сырья приведен в табл. 1.
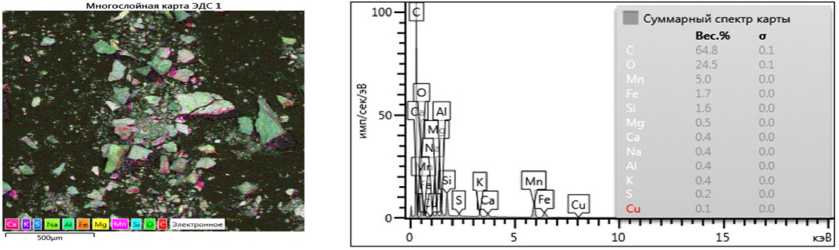
(а) Морфология браунита
(б) Элементный состав браунита
Рис. 2. Результаты исследований браунита
-
Fig. 2. Results of brownite research
Таблица 1. Состав минерального сырья Дальневосточного региона
Table 1. Composition of Mineral Resources of the Far Eastern Region
Наименование |
Оксидный состав, масс.% |
Флюорит |
92-СаF 2 ; 2,5-SiO 2 ; 2,5-СаО |
Гранодиорит |
63-SiO 2 ; 16-Al 2 O 3 ; 5,49-Fe 2 O 3 ; 5,1-СаО; 4,28-К 2 О; 3,3-Na 2 О |
Мрамор |
98-СаСО 3 |
Титаномагнетит |
22,57-FeTiO 3 ; 18,27-SiO 2 ; 1,41-Al 2 O 3 ; 13,97-Fe 2 O 3 ; 0,94-MnO; 1,81-CaO |
Шеелит |
59,5-WO 3 ; 2,9-SiO 2 ; 26,8 -СаО; 3,8-Fe 2 O 3 ; 1,6-MgO |
Браунит |
21,55-MnO; 25,45-SiO 2 ; 5,62-Al 2 O 3 ; 9,02-FeO; 15,47-CaСО 3 ; 4,34-MgO |
Для выбранного многокомпонентного минерального сырья был выполнен термодинамический расчет в целях установления возможного протекания химических реакций [5]. Результаты некоторых расчетов приведены на рис. 3 и 4.
Расчет энергии Гиббса показал, что окислительно-восстановительные процессы элементов шлаковой основы будут происходить при температуре от 3500 К до 7000 К. Однако при
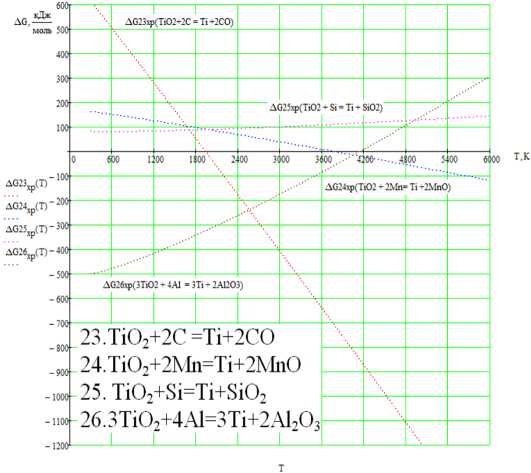
Рис. 3. Изменение свободной энергии Гиббса ( ДС^ ) от температуры для восстановительных реакций
-
Fig. 3. Variation of Gibbs ( AG°p ) free energy with temperature for reduction reactions
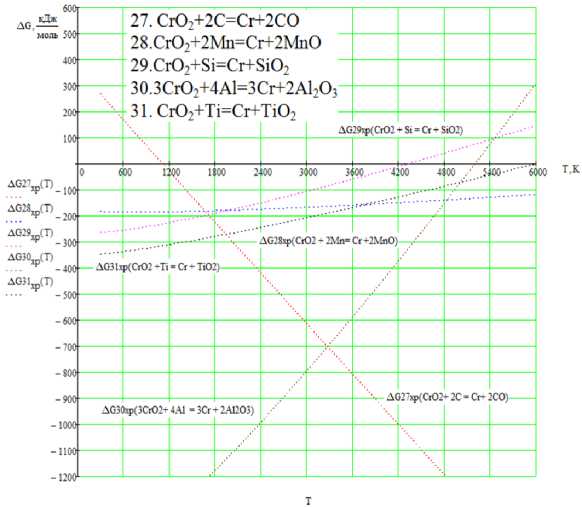
Рис. 4. Изменение свободной энергии Гиббса ( AG^ ) от температуры для восстановительных реакций
-
Fig. 4. Change in Gibbs free energy ( AG^ ) as a function of temperature for reduction reactions
– 960 –
взаимодействии оксидов с углеродом восстановление элементов идет при более низких температурах (например, для CrO 2 –1200 К, для TiO 2 –1800 К). Результаты расчета подтверждены экспериментальными исследованиями. При наплавке под шеелитовым концентратом в металле восстановилось 3,962 % вольфрама, при использовании титаномагнетита – 3,216 % титана, браунита – 0,459 % марганца.
На следующем этапе был проведен расчет процентного соотношения компонентов шихты, основности и химической активности шлака, состоящего из 50 % компонентов минерального сырья и 50 % стандартного флюса АН22, на основе уравнения 1.
Результаты расчета показали, что флюс, состоящий из 50 % компонентов минерального сырья Дальневосточного региона и 50 % стандартного флюса АН22, является основным (В=1,46) и малоактивным (А= 0,22). Данный флюс не оказывает окислительного воздействия на металл, снижает температуру плавления шлака и улучшает качество формирования шва. Кроме того, установлено, что исследуемый шлак обладает высокими технологическими свойствами и будет использован как основа для выбора рационального состава флюса, обеспечивающего требуемое качество формируемых покрытий. В этих целях были проведены исследования в соответствии со схемой (рис. 1), в которой входными (переменными) параметрами являлись: шлакообразующие (флюорит, гранодиорит, мрамор, браунит), X1; стабилизирующие (титаномагнетит), X2; легирующие и раскисляющие (шеелит), X3. Флюс АН22 являлся постоянным входным (сопутствующим) параметром. В качестве выходных критериев были приняты общая пористость (П) и зернистость (З).
По результатам экспериментальных исследований были составлены математические зависимости и диаграммы влияния компонентов шихты на критерии работоспособности флюса при электродуговом процессе. Анализ диаграмм позволил установить рациональный состав компонентов минерального сырья, обеспечивающий рациональные значения пористости и зернистости: Х1 (40 % шлакообразующие – флюорит 27,35 %; гранодиорит 42,38 %; мрамор 30,27 %); Х2 (44 % стабилизирующие – титаномагнетит 100 %); Х3 (16 % легирующие – шеелит 62,50 %; браунит 37,50 %).
На следующем этапе, используя данный состав, были выполнены опытные наплавки и проведены исследования в целях определения структуры и качества формируемых покрытий (рис. 5).
Из рис. 5 видно, что структура наплавленного металла феррито-перлитная, кристаллы имеют дендридное строение, что соответствует структуре металла при термических процессах. В зоне сплавления и в наплавленном металле дефекты отсутствуют.
Разработанный состав шлаковой основы обеспечивает высокое качество наплавленного металла и требуемые сварочно-технологические свойства (отделяемость шлака, стабильность горения дуги, формирование наплавленного слоя, склонность к образованию дефектов и другие).
На базе полученной шлаковой основы разрабатывались плавлено-керамические флюсы для восстановления изношенных поверхностей деталей, обеспечивающих твердость наплавляемого металла в широком диапазоне (250–500 НВ), ударную вязкость не менее 30 Дж/см2 и высокую износостойкость. В качестве входных параметров были приняты шлаковая основа, графит, ферромарганец, феррохром, циркониевый концентрат, выходными характеристиками являлись твердость, коэффициент износостойкости. По результатам эксперимента рассчитывались коэффициенты и строились уравнения для выходных параметров исследуемой системы.
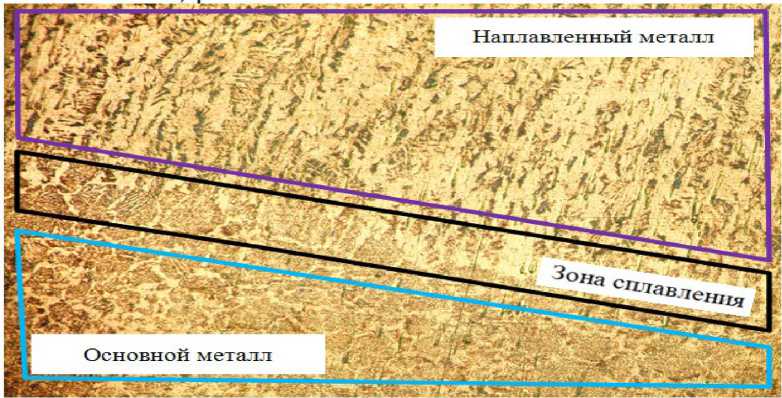
Рис. 5. Фотография микроструктуры наплавленного металла
Fig. 5. Photograph of the deposited metal microstructure
На основании полученных в результате экспериментов откликов системы рассчитывались коэффициенты полинома для каждого выходного параметра и строились уравнения регрессии.
По результатам расчета строилась совмещенная диаграмма влияния соотношения массовых долей входных параметров на свойства наплавленного металла (рис. 6).
По совмещенной диаграмме был выбран рациональный состав компонентов флюса в зависимости от требуемых свойств наплавленного металла и присвоена марка (АН22ПК-ДМС).
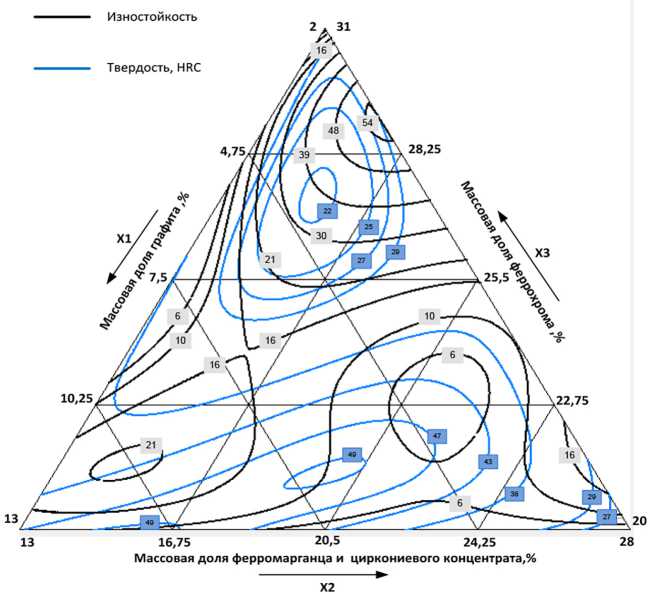
Рис. 6. Совмещенная диаграмма влияния соотношения компонентов флюса на критерии работоспособности (HRC, Кi)
Fig. 6. Combined graph of the influence of the flux components ratio on the performance criteria (HRC, Ki)
Состав плавлено-керамического флюса, обеспечивающего твердость наплавленного металла 47НRC, (масс.%): АН-22–20,6; гранодиорит – 5,8; флюорит – 3,7; мрамор – 4,1; титаномагне-тит – 3,7; браунит – 1,2; шеелит – 2,1; циркониевый концентрат – 4,9; ферромарганец – 19,6; графит – 5,5; феррохром – 28,9.
Далее выполнялись опытные наплавки с использованием выбранного по диаграмме состава минерального сырья, а также стандартных флюсов АН22 и АН348А. После наплавки проводились исследования состава, структуры и свойства наплавленных слоев. В качестве подложки использовалась сталь обыкновенного качества Ст3, электродная проволока – Св-08 диаметром 3 мм. Результаты исследования приведены в табл. 2 и 3, а также на рис. 7 и 8.
По химическому составу наплавленный металл с использованием флюсов АН22ПК-ДМС и АН348АПК-ДМС соответствует заэвтектоидной стали, легированной хромом, марганцем, вольфрамом и другими элементами. Содержание углерода в наплавленном слое более 1,4 %, хрома от 7,992 % до 9,374 %, марганца от 4,488 % до 8,326 %, вольфрама от 0,087 % до 1,746 %, что свидетельствует о возможном образовании карбидов, легированного цементита и других веществ в наплавленном слое.
Наплавленный металл имеет твердость 47–50 НRC, высокую износостойкость относительно стали 20 Кi 8,5–10. При этом значение ударной вязкости равно KCU 36–39 Дж/см2, что соответствует требованиям технических условий эксплуатации железнодорожного подвижного состава.
Таблица 2. Элементный состав металла, наплавленного опытными флюсами
Table 2. Elemental composition of metal clad with experimental fluxes
АН22ПК-ДМС
Концентрация элементов, %
C |
Al |
Si |
Ni |
Ti |
Cr |
Mn |
Zr |
W |
1,4–1,7 |
0,894 |
2,129 |
1,282 |
0,251 |
9,374 |
8,326 |
0,390 |
0,087 |
АН348АПК-ДМС |
||||||||
Концентрация элементов, % |
||||||||
C |
Al |
Si |
Ni |
Ti |
Cr |
Mn |
Zr |
W |
1,4–1,7 |
0,026 |
0,248 |
1,288 |
0,025 |
7,992 |
4,488 |
0,090 |
1,746 |
Таблица 3. Механические и эксплуатационные свойства наплавленного металла
Table 3. Mechanical and performance properties of the weld metal
Флюс |
Свойство |
Значение свойства |
АН22ПК-ДМС |
Твердость, НRС |
47 |
Коэффициент износостойкости относительно стали 20, (Кi) |
8,5 |
|
Ударная вязкость KCU, Дж/см2 (при температуре 20 °C) |
39 |
|
АН348АПК-ДМС |
Твердость, НRС |
50 |
Коэффициент износостойкости относительно стали 20, (Кi) |
10 |
|
Ударная вязкость KCU, Дж/см2 (при температуре 20 °C) |
36 |
Высокая твердость наплавленного слоя обусловлена образованием карбидов, легированного цементита и других соединений, что подтверждено металлографическими исследованиями.
На рис. 7 и 8 приведена микроструктура металла, наплавленного под флюсами АН22ПК-ДМС и АН348АПК-ДМС. Основной металл имеет феррито-перлитную структуру (содержание перлитной составляющей 20…25 %). Зона сплавления (шириной 55 мкм), имеет структуру сорбита с микротвердостью 230 HV. От зоны сплавления в наплавленный металл на глубину 15–20 мкм проникают дендриты, состоящие из сорбита.
Наплавленный слой имеет ячеисто-дендритную структуру, характерную для внутрикри-сталлического строения покрытий сплавов эвтектоидного типа. Из рисунков видно, что ячейки появляются не от самой границы сплавления зерен околошовной зоны, а на некотором расстоянии от нее. На более поздней стадии затвердевания образуются дендриты.
Структура слоя, наплавленного флюсом АН22ПК-ДМС, состоит из трёх фаз. Одна из фаз формирует округлые области (зерна), выстроенные в направлении роста дендритов. Структу-
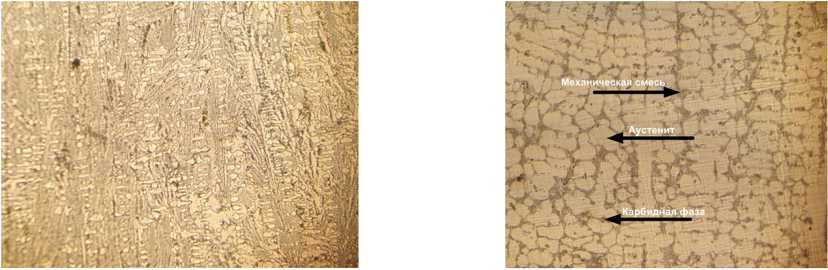
(а) (б)
Рис. 7. Микроструктура металла, наплавленного под флюсом АН22ПК-ДМС (а – наплавленный металл при увеличении х200, б – наплавленный металл при увеличении х400)
Fig. 7. Microstructure of metal clad under flux AN 22PK-DMS (a – clad metal at magnification x200, b – clad metal at magnification x400)
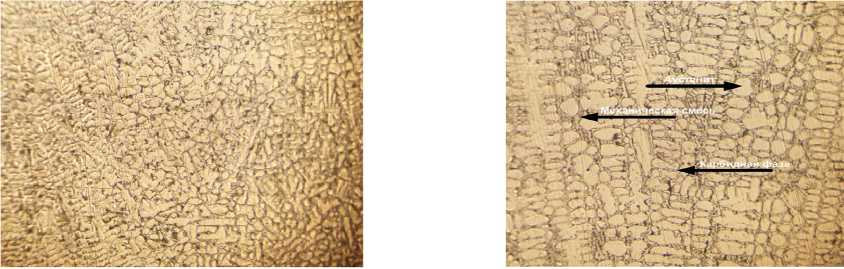
(а) (б)
Рис. 8. Микроструктура металла, наплавленного под флюсом АН348АПК-ДМС (а – наплавленный металл при увеличении х200, б – наплавленный металл при увеличении х400)
Fig. 8. Microstructure of metal clad under flux AN 348APK-DMS (a – clad metal at magnification x200, b – clad metal at magnification x400)
ра данной фазы состоит из аустенита (атлас нормальных микроструктур металлов и сплавов), имеющего микротвердость 250–300 HV. Другая фаза соответствует механической смеси (эвтектоид), состоящей из легированного цементита и аустенита (400–450 HV). В межзеренном пространстве расположена карбидная фаза (легированный цементит, 550–620 HV). По результатам исследования можно сделать вывод, что микроструктура слоя, наплавленного флюсом АН22ПК-ДМС, состоит из аустенита, эвтектоида и карбидной фазы.
Структура слоя, наплавленного флюсом АН348АПК-ДМС, состоит также из трёх фаз. Одна из фаз формирует округлые области (зерна), выстроенные в направлении роста дендритов (рис. 8б). Структура данной фазы состоит из аустенита, имеющего микротвердость 250– 300 HV. Вторая фаза соответствует механической смеси (эвтектоид) – легированный цементит и бейнит (400–450 HV). В межзеренном пространстве расположена карбидная фаза (легированный цементит, 550–650 HV). По результатам исследования можно сделать вывод, что микроструктура слоя, наплавленного флюсом АН348АПК-ДМС, состоит из аустенита, эвтектоида и карбидной фазы.
Выводы
Разработана методика получения флюсов, заключающаяся в предварительном расчете компонентов шлаковой основы ильменито-флюоритного типа, определении основности и химической активности шлака, термодинамическом анализе возможных химических реакций, а также экспериментальных исследований, позволяющих определить рациональный состав компонентов шлака. На основе разработанных уравнений и диаграмм выбран рациональный состав шлаковой основы – 40 % шлакообразующие вещества (флюорит 27,35 %; гранодиорит 42,38 %; мрамор 30,27 %), 44 % стабилизирующие (титаномагнетит 100 %), 16 % легирующие (шеелит 62,50 %; браунит 37,50 %), обеспечивающий высокое качество формируемых покрытий и требуемые технологические свойства. На базе полученной шлаковой основы разработаны плавлено-керамические флюсы (АН22ПК-ДМС, АН348АПК-ДМС), обеспечивающие требуемые технологические, механические и эксплуатационные свойства формируемых покрытий, которые обеспечиваются за счет восстановления легирующих элементов и образования карбидов и других веществ.
Список литературы Разработка легирующих флюсов для износостойкой наплавки деталей подвижного состава с использованием минерального сырья дальневосточного региона
- Макиенко В. М., Атеняев А. В. Разработка шлаковой основы флюсов ильменито-флюоритного типа с использованием минерального сырья Дальневосточного региона. Ползуновский вестник, 2020, 1. 130-139. EDN: LCVMRV
- Архипов Г. И. Минеральные ресурсы горнорудной промышленности Дальнего Востока. Обзор состояния и возможности развития. М.: Горная книга, 2011. 830. EDN: VQRTLA
- Потапов Н. Н. и др. Сварочные материалы для дуговой сварки: справочное пособие: В 2-х т. Т 1. Защитные газы и сварочные флюсы. М.: Машиностроение, 1989. 544.
- Неровный В. М. и др. Теория сварочных процессов. М.: МГТУ им. Н. Э. Баумана, 2007. 735.
- Зедгинидзе И. Г. Планирование эксперимента для исследования многокомпонентных систем. М.: Наука, 1976. 390.
- Макиенко В. М., Соколов П. В., Лукьянчук А. В., Атеняев А. В. Разработка сварочно-наплавочных флюсов на основе минерального сырья ДВ региона. Упрочняющие технологии и покрытия. 2019. 15(178). 442-448.