Разработка метода оптимизации конструкторско-технологического проектирования агрегатов самолета с использованием информационных технологий
Автор: Мантусов М.Н., Ривин Г.Л.
Журнал: Известия Самарского научного центра Российской академии наук @izvestiya-ssc
Рубрика: Механика и машиностроение
Статья в выпуске: 3-2 т.11, 2009 года.
Бесплатный доступ
В статье авторы рассматривают метод оптимизации конструкторско-технологического проектирования, позволяющий снизить трудоемкость и длительность проектирования, повысить качество принимаемых решений с оптимизацией характеристик получаемой конструкции. Метод позволяет учесть основные факторы, влияющие на принятие конструкторско-технологических решений проектируемого изделия. В статье представлена логическая модель разрабатываемого метода и приведено его математическое описание.
Конструкторско-технологическое проектирование, трудоемкость, логическая модель, математическое описание
Короткий адрес: https://sciup.org/148198672
IDR: 148198672
Текст научной статьи Разработка метода оптимизации конструкторско-технологического проектирования агрегатов самолета с использованием информационных технологий
из которых только равносторонних уголков свыше ста видов. На предприятии существует перечень, где определены и используются хомуты, уплотнители, фланцевые соединения, арматуры и др., что в итоге составляет огромную информационную базу, для работы с которой требуется определенный уровень знаний и соответствующие временные затраты.
На современном этапе создания конкурентоспособной продукции возникает необходимость повышения эффективности и качества технических систем и, как следствие, эффективности и качества технологии ее создания.
Большинство исследователей проектов новой техники отмечают, что одной из важнейших проблем является сокращение сроков проектирования, а следовательно снижение степени морального старения техники, и соответственно сокращение затрат на проектирование и др. Это объясняется тем, что быстрое моральное старение является объективным фактором обусловленным научно-технической революцией (НТР).
Многочисленные исследования, проводимые в области проектирования подтверждают, что увеличить продолжительность жизненного цикла некоторых видов технических систем можно за счет сокращения сроков проектирования за счет внедрения систем автоматизации проектирования (САПР). При анализе трудоемкости этапов проектирования выделен этап — изготовление комплекта документации, который занимает от 50 до 80% времени. Следовательно, вывод такой, что внедрение соответствующих средств автоматизации, позволяет существенно снизить длительность основных этапов проектирования изделия.
Таким образом, необходима разработка и активное применение новых, передовых методов проектирования изделий с учетом использования современных технологий их изготовления включая сборку. Например, для снижения трудоемкости изготовления изделий на практике проектирования внедряются и используются методы автоматизированного расчета параметров технологических процессов, параллельно с этапом конструкторского проектирования по логической цепи “Исследование – Проектирование – Производство”. Очевидно, что лучше, если этот расчет будет производиться непосредственно на этапе проектирования изделия в автоматизированном режиме.
В связи с этим актуальное значение приобретает создание метода, позволяющего оптимизировать процесс разработки изделия на ранней стадии его проектирования с оценкой параметров технологического процесса его изготовления.
Разрабатываемый метод, основан на рациональном выборе элемента конструкции по выполняемой им функции с учетом технологических возможностей производства. Метод позволяет максимально уменьшить пространство допустимых решений, учесть как количественные, так и качественные показатели искомого элемента с учетом параметров технологического процесса его изготовления.
В качестве примера рассмотрим этапы проектирования соединения крышки люка кессона с панелью крыла (рис. 1).
В рассматриваемом примере по заданной функции “Соединить крышку (люка кессона) ”, которая ссылается на базу элементов созданной на основе тезауруса. Далее происходит отбор типа соединения, которое может выполнить эту функцию: болт – гайка, винт – гайка, сварное соединение, клеевое соединение, заклепочное соединение, резьбовое соединение и др. На каждое из отобранного типа соединений накладываются конструктивные ограничения (форма крышки, ширина обода крышки, длинна окружности обода, толщина крышки, толщина панели кессона в зоне соединения, соединение разъёмное, материал крышки, материал панели кессона, сопротивление нагрузке и тому подобное).
Происходит отбор элементов, удовлетворяющих всем конструктивным требованиям. На следующий этап отбора выходят соединения “болт – гайка” и “винт – гайка”, то есть элементы определенного промежутка ОСТов и промежутков типоразмеров (длина стержня, диаметр). Виды соединения не проходят на следующий этап, если они не удовлетворяют хотя бы одному из типов накладываемых ограничений. Например, на следующий этап не прошли “сварное соединение”, “клеевое соединение”, “заклепочное соединение”, “резьбовое соединение”. Сварное, как и клеевое соединения не удовлетворяют условию “соединение разъемное”, как отмечено выше, достаточно одного несоответствия накладываемым ограничениям и элемент автоматически исключается из операции дальнейшего отбора. Резьбовое соединение не удовлетворяет ограничению “форма крышки (овал)”, заклепочное соединение так же не удовлетворяет условию “соединение разъёмное”.
На этом же этапе на соединения накладываются технологические ограничения (ограничение доступа при монтаже, выход на аэродинамическую поверхность, выход на теоретический контур, база инструмента, оборудования, которые имеются на предприятии и т.д.).
В дальнейшем происходит отбор элементов, удовлетворяющих всем технологическим требованиям. Для этой цели подсистема синтеза конструкторско-технологических решений содержит базы данных, имеющихся на предприятии оборудования и оснастки, позволяющих эти решения реализовать. На следующий этап отбора выходит соединение “винт-гайка”, элементы определенного промежутка отраслевых стандартов и промежутков типоразмеров (длина стержня, диаметр) а так же их количество. На данном этапе болтовое соединение не соответствует требованию “аэродинамическая поверхность, выход на теоретический контур”, то есть головки крепежного элемента не должны выходить за контур обшивки.
Последний этап выбора “Ограничение по наименьшей массе”, где могут быть наложены ограничения по прочности, то есть может быть задано значение определенного усилия, которое должно выдерживать проектируемое изделие. Или, ограничение по работе в зоне интервала, каких-либо температур, где задаются значения температур и др. Такое ограничение назначается пользователем и может быть задано в зависимости от того, какой из параметров изделия более важен при его создании, в данном случае выбираются элементы с наименьшей массой. В итоге выбирается количество элементов позволяющих наиболее эффективно выполнить заданную функцию.
По выбранным элементам производится автоматизированный расчет параметров технологических процессов изготовления или применения элементов при помощи базы содержащей типовые технологические процессы, нормы расхода материалов и другие реквизиты. Так же определяется норма основных и вспомогательных материалов, инструмент, трудоёмкость и другие параметры технологического процесса с применением элементов.
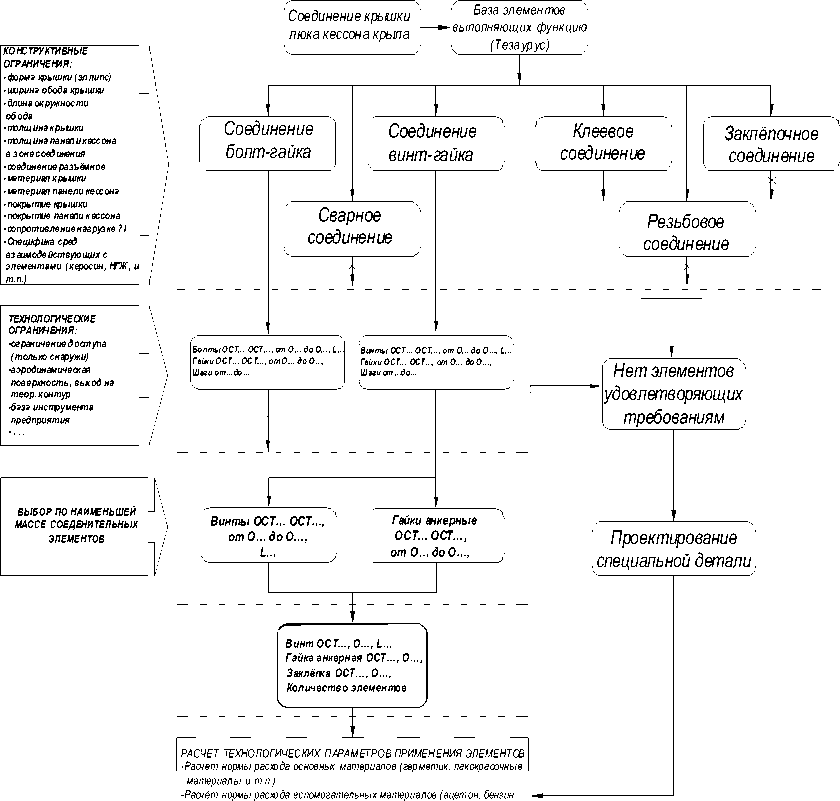
и т.п.)
I -Выбор инструмента
-Выбор оборудования
-Выбор приспособления
-Расчёт трудоёмкости
-Коректировка типового технологического процесса
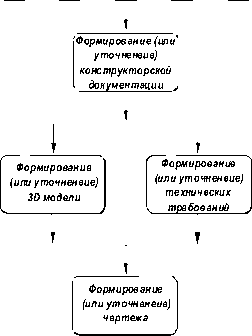
Рис. 1. Логическая модель оптимизации соединения крышки люка кессона с панелью крыла
В случае, если на первом или втором этапах отбора не выявлен ни один из элементов удовлетворяющий требованиям накладываемых ограничений, выявляется необходимость создания специальной детали, необходимой для выполнения данной функции.
После проектирования специальной детали (деталь, имеющая отличия от стандартных, будет изготавливаться по чертежу) проводится уточнение исходных данных для корректировки и расчета параметров технологического применения выбранных элементов и соответ- ственно сам расчет параметров технологических процессов.
Итогом всего цикла является подбор искомых элементов, оптимально выполняющих заданную функцию, с выпуском или корректировкой конструкторской и технологической документации.
В предлагаемом методе определяются соединение и элементы его, реализующие по выполняемой функции за счет наложения ограничений, то есть после проведения конструктивно – технологического анализа выбранной группы изделий. Такой анализ служит основой для подбора конкретного вида изделия, отвечающего всем накладываемым требованиям.
Для нахождения оптимального решения данной задачи необходимо сформулировать множество вариантов элементов, оценки которых по ряду параметров не могут превышать некоторой, заранее заданной величины [1]. Достаточно эффективно можно применять модификацию лексикографического морфологического метода или метод последовательных уступок. Морфологический принцип метода заключается в том, что формируются варианты элементов от каждого морфологического класса. Лексикографический принцип состоит в том, что каждый i и j -й элементы в составе отобранных, лексикографически предпочтительнее всех элементов, оставшихся к этому моменту в морфологических классах, из которых в ранее формируемый вариант не вошел ни один элемент.
Схема распределения на морфологические классы крышки люка кессона крыла представлена на рис. 2.
Такой обобщенный анализ конструкции элемента и технологии его соединения служит основой для выбора метода соединения конкретного изделия.
При выделении вариантов методом последовательных уступок допустимыми являются варианты со значениями параметров, не превышающими допустимого отклонения (“уступки”), в данном случае – это накладываемые ограничения:
X 1 ≤ a 1 , b 1 ,
X 2 ≤ a 2 , b 2 ,
X 3 ≤ a 3 , b 3 ,
(1) ..................,
Xn ≤ an,bn, где X1, X2, X3,…, Xn – типы соединений, способных выполнить заданную функцию;
a1, a2, a3,…, an – конструктивные ограничения ( длинна, ширина и т.д. );
b1, b2, b3,…, bn – ограничения, накладываемые используемой технологией на предприятии (накладываются требования использования определенного оборудования или инструмента для обеспечения выполнения необходимой операции с учетом требований точности и требований технических условий).
/ болтовое / заклёпочное / / винтовое / сварное / / резьбовое / клеевое /
I разъемное i iada^uai iiaj /
способ соединения
/ титановый / De3UHa 7
/ п> еаа _ ; резине ;
; алюминиевый Стеклопластик: , стальной сплав уалепластик / ; I металлы / i a i ад аёёй у / применяемые ; материалы ,
прочностные показатели
/ передача усилий
/ сопротивление разрыву
/ растяжение-сжатие
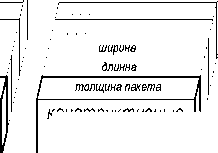
/ цинкование ‘Лакокрасочные / ‘хромирование: герметик : ‘анодирование / грунтовка / Неорганические; органические конструктивные / параметры ,
покрытия
Обобщенно функциональная модель соединения крышки люка кессона крыла
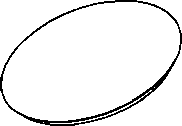
/ инструмент Оля / / разделки отверстий : / инструмент для / ' клепки / / тип инструмента /
/ автомат сварочный / / пресс клепальный / тип оборудования /
/ хим. травление
/ шлифование способы получения поверхности
/ внутришовная
/ поверхностная способы , герметизации /
/ двусторонний / односторонний доступ к соединению
Рис. 2. Морфология элемента - крышка люка кессона крыла
Таким образом, операция подбора элементов, выполняющих необходимую функцию, проводится в пять этапов:
-
1. Определение и задание выполняемой функции.
-
2. Выбор элементов выполняющих эту функцию.
-
3. Отсеивание элементов, не удовлетворяющих конструктивным ограничениям.
-
4. Отсеивание элементов, не удовлетворяющих технологическим требованиям предприятия.
-
5. Окончательный выбор предложенного варианта (например, по наименьшей массе).
Графически это можно представить в виде схемы, изображенной на рис. 3.
Пусть задана функция Fi , которую выполняют множество элементов Xn , а на них накладываются ограничения в виде конструктивных параметров a1, a2, a3,…, an и технологических b1, b2, b3,…, bn . Из схемы видно, что на предпоследнем этапе может быть определенно наименьшее количество элементов Xi , удовлетворяющих всем требованиям. На заключительном этапе операции определения оптимального элемента накладывается последнее ограничение, в данном случае наименьшая масса. Последнее ограничение задается по желанию проектировщика, в зависимости от того какой из параметров изделия для него наиболее важен, наименьшая масса, наибольшая жесткость и др.
Чтобы получить варианты элементов удовлетворяющих всем ограничениям, кроме последнего, массового в данном случае, достаточно проверить их на соответствие этим ограничениям. Для этого надо сопоставить значения соответствующих параметров выбранных элементов со значениями рассматриваемых ограничений в диагональных матрицах. Например, по конструктивным ограничениям:
IX А =
I Xa\ =
b 1 b 2 b 3 100
bn X 1
0 X 2
0 X 3
1 X
a 1 a 2 a 3 100
аn X 1
0 X 2
0 X 3
1 Xi
Если | Xia | = 1 , то этот элемент может рассматриваться в дальнейшем выборе. Если же |X a | = 0 , то этот элемент исключается из дальнейшего рассмотрения.
Таким же способом проводится проверка на
соответствие технологическим ограничениям:
Если | Xib | = 1 , то этот элемент может рассматриваться в дальнейшем выборе. А если |X ib \ = 0 , то этот элемент исключается из дальнейшего рассмотрения.
В отличие от традиционных подходов такой метод основан на, так называемой, технологии сквозного инженеринга (Concurent Engineering), идея которой заключается в одновременном проектировании изделия, технологического процесса и производственной системы. Он рассматривает конструктивные и технологические параметры как ограничивающую систему в анализе необходимого элемента. Выбор элемента осуществляется на основе выполнения необходимой функции и базы конструкторско-технологических данных. Метод выбора вариантов решения определенных задач по функции носит целенаправленный характер и позволит уменьшить пространство допустимых решений при проектировании [2].
Для создания и упорядочивания базы элементов и их функций на практике принято использовать информационно – технологический тезаурус, который помимо конструктивно-технического и математического описания дает и функциональное описание элемента, на языке выполняемых функций и их отношений. В дальнейшей работе предполагается создать тезаурус крыла самолета, а на примере этого агрегата и его элементов разработать метод и математическую модель процедуры определения элемента по функции.
Данный подход является актуальным, так как на этапе развития методов создания проектов, параллельно с конструкторской разработкой, требуется проводить и технологические расчёты в кратчайшие сроки. Метод предназначен для снижения общей трудоёмкости и проектно – технологических процедур проектирования изделий.
Таким образом, метод определения элемента по выполняемой им функции обеспечивает выбор рациональных конструкторско-технологических решений по различным критериям (массе, прочности и так далее), а так же обеспечивает создание конструкторской и технологической документации для нужных вариантов конструкции.
Предлагаемый метод может использоваться
в любом производстве, а также при производстве конструкторского и технологического проектирования сложных изделий.
Список литературы Разработка метода оптимизации конструкторско-технологического проектирования агрегатов самолета с использованием информационных технологий
- Буланов И.М., Кравченко Е.Е. Совмещенное проектирование на ЭВМ тройников трубопроводов из композиционных материалов//Вестник МГТУ. Сер. Машиностроение. 2002. №2. С. 3-16.
- Попов П.М., Соколова О.Ф. Проектно-технологические и управленческие функции по конструкции самолетов (ЛА). Правила их формулирования: Учебное пособие -Ульяновск: УлГТУ, 2002. 247 с.