Разработка моделей функционирования и конструкций агрегата совмещенной прокатки-прессования для обработки цветных металлов и сплавов
Автор: Довженко И.Н., Довженко Н.Н., Сидельников С.Б.
Журнал: Журнал Сибирского федерального университета. Серия: Техника и технологии @technologies-sfu
Статья в выпуске: 8 т.7, 2014 года.
Бесплатный доступ
Проанализировано производство длинномерной продукции из цветных металлов и сплавов. Разработаны новые модели и предложены конструкции агрегатов совмещенной обработки.
Металлургия, цветные металлы, совмещенные процессы, прокатка, моделирование, прессование
Короткий адрес: https://sciup.org/146114915
IDR: 146114915
Текст научной статьи Разработка моделей функционирования и конструкций агрегата совмещенной прокатки-прессования для обработки цветных металлов и сплавов
With the continuous technological development and globalization of markets before the enterprises producers of metal products there is acute problem increase efficiency and provide release of competitive production. This problem is especially urgent in the production of long products from non-ferrous metals and alloys in the form of rods, wire and profiles of small cross-section.
Underlying of this work process of combined rolling-extruding (CRE) [1] has great potential for improving the efficiency of obtaining long products from non-ferrous metals and alloys.
Analysis of the scientific-technical and patent literature has shown that as basic for most continuous processes applies rolling, and ways to ensure the creation of active friction by movable walls of the instrument, for example, in the methods Conform, Extrolling and Lynex. Devices for the implementation of these methods work in conjunction with the aggregates of continuous casting billet, mostly rotor type. Most common in the industry have installs Holton Conform™ of company Outokumpu Holton Ltd. with wheels diameter 300, 400 and 500 mm, and also company BWE Ltd. Conform™ and Conklad™ with wheels diameter 285, 315, 350, 400, 550 mm and drive power from 100 to 500 kW. The maximum diameter of the billet is 25,5 mm from aluminum and 22 mm from copper. Approximately 75 % of working units Holton Conform™ intended for obtaining of aluminum products and 25 % from copper and copper alloys.
Despite the advantages of these units should be noted and shortcomings of the method Conform: high energy intensity of the process, as the costs of overcoming the friction forces on the surfaces of instrument assembly require for drive the use electric motors of high power; unevenness of deformation; sufficiently complicated construction of press unit and its cooling system. Thus, the driving power of installation CRE comparing to installation Conform at comparable diameters of the rolls and wheel lower for 3-4 times.
For the process CRE performed a complex of theoretical and experimental research, implemented protection of technical solutions in the form of patents, established pilot installations based on the rolling mills. However, there is a need of development constructions of industrial aggregates CRE as objects of modular continuous technology taking into account the advantages and lacking disadvantages of pilot units.
The analysis showed that the design of industrial aggregates CRE as objects of module technologies need to develop their structural and parametric descriptions using a set of project parameters and operational models.
One of the main factors determining the energy-power parameters of the process CRE is the coefficient of extraction during extrusion, and therefore were performed experimental studies on the installation CRE-200 for an alloy of lead with antimony, aluminum and its alloys and copper. On Figure 1 represented typical for the process CRE dependence of the forces on the matrix, rolls and moments (further index 1 – relates to roll with a ledge, index 2 – with cutting) during deformation in hot conditions at 470 оC of aluminum A7 in various calibers. Analysis of experimental data revealed the following general patterns of the process CRE: increase extraction increases the forces on the matrix which is characteristic of the extrusion process, and on the rolls due to increased boost pressure in the deformation zone from the force of extrusion; reduction in cross-sectional area of caliber at one and the same extract reduces the forces on the matrix; change in the force on the rolls is very sensitive to changes in the extrusion force; moment on the roll with cutting more than moment on the roll with a ledge, due to the difference in the contact area of the walls caliber with billet during deformation; there is a correlation relationship between the moments on the roll with a ledge and roll with cutting, and the rate of change Δ M 2 / Δ M 1 higher for of hot deformation conditions for alloy AD31 and copper than lead.
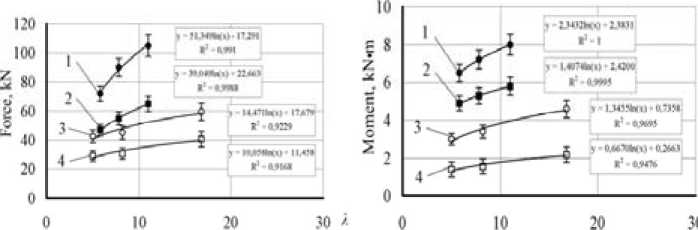
a
b
Fig. 1 Dependence of the forces on the matrix Р m and rolls Р r (a) from extraction λ during extruding the alloy А7 (1 – Р r , and 2 – Р m , caliber 13×22 mm; 3 – Р r and 4 – Р m , caliber 11×15 mm) and moments on the rolls М 1 and М 2 (b) with the same parameters (1 – М 2 and 2 – М 1 , caliber 13×22 mm; 3 – М 2 and 4 – М 1 , caliber 11×15 mm)
For process CRE implemented on the rolls of different diameters found that the length of the arc of capture, the pressure on the rolls, zone sizes crimping under the rolls and moments on the rolls are not the same.
For the calculation temperature of press-article to the development solution of J.L. Sternik on the basis of one of the properties of integrals of the differential equation Fourier to account for the two-dimensional heat flow in the billet deformation in the form of bar and substitution of thermal characteristics for the alloy AD31 following equation was obtained
Т ид = Т 0 + 0,315 ( Y P. + А Т прок + А Т рас ) + А Т .р -
-2[То + 0,315(АТпрок +АТрас) + АТ.р -Тк]-[1 - exp(-1,5)]2, where Т0 - billet temperature, pex=as (^ ex, Tex)(1+1,4lnZ) - pressure of extruding, Z - extraction coefficient during extruding, ΔТrol, ΔТdec and ΔТfr – temperature increase accordingly from deformation during rolling, decompression and friction on the walls of caliber, Ре=vh0/а – Peclet number, Nu=ld1/h0 – Nusselt number, γ=Nu·Ре/(1+Nu·Ре), а – coefficient of thermal diffusivity, v – average velocity of sections in the deformation zone v=2ωR1R2/(R1+R2), and ω – rotational speed of the rolls.
For conditions R 1 =210 mm, R 2 =180 mm, λ=15,1, Т 0 =480 °С (alloy AD31) results of calculation by the above formula is shown in Fig. 2.
Analysis of simulation results showed, that with increasing rotational speed of the rolls of heat transfer time is reduced between the metal of billet and rolls. Accordingly decreases temperature drop in the billet of rolling and decompression zones which increases the product temperature at the outlet of the matrix.
Based on the results of studies proposed to use for aggregates CRE:
-
– box-like frame with console emplacement of rolls, diameter from 100 to 300 mm, providing rapid tool changing (rolls and matrix) to produce small batches of deformable alloys (aluminum АД1, silver SAg40 etc.) with the wide nomenclature;
-
– closed frame (the diameter of the work rolls 400 or 500 mm), providing greater stiffness and is designed to operate using a large cross-section billets with high performance, and also allows
Fig. 2 Calculated dependence of the temperature of the product Т prod output from the matrix of the speed of rolls n and temperature of the rolls T rol : 1 – 150 °С; 2 – 200 °С; 3 – 250 °С; 4 – 300 °С; 5 – 350 °С
b
Fig. 3 Configuration solution of aggregate CRE-300 (a) and construction of a combined unit of gear cage with console rolls (b): 1 – console roll; 2 – frame; 3 – bearing; 4 – sealing; 5 – fast coupling; 6 – gear wheel; 7
– matrix processing hardly-deformable alloys of aluminum and copper. Variant configuration solution of aggregate CRE-300 of frame type presented on Fig. 3.
The design of roll is combined using hard alloy ring and mounting system of company «Kark». Further, this version of the unit has been improved through the use of design combined unit gear cage with console rolls (Fig. 3b).
As a drive of the work rolls proposed to use modern motor reducers or hydraulic motor reducers does not require additional reducers which significantly reduces the overall dimensions of the unit CRE. For the production of press-articles from billets with a cross section 40×40 mm and more from aluminum alloys and copper developed construction of aggregate CRE-400 with the initial diameter of the rolls 400 mm (Fig. 4). As an analog of roll block is taken cage section rolling mill of construction USTU-UPI (Yekaterinburg).
Therefore, developed models and proposed the construction of aggregate CRE-400 which ensures that no overturning moment through the use of individual drive for each roll, high stiffness of system roll-matrix block and reliability. The results of the studies were used to create a physical model of the installation of combined processing for the production electrotechnical wire rod.
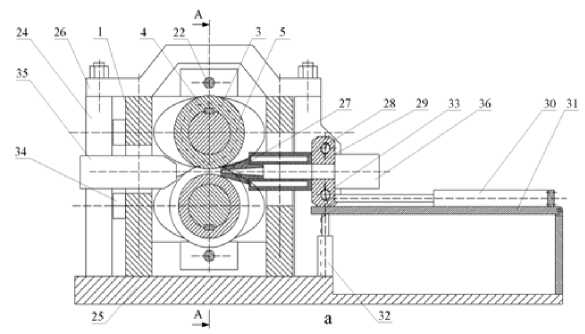
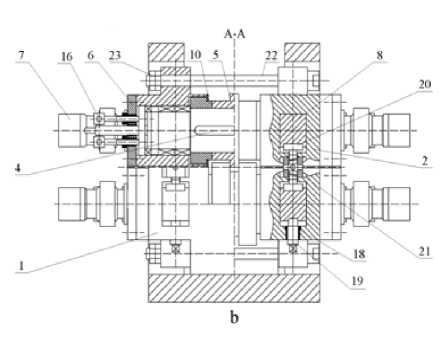
Fig. 4 The construction of aggregate CRE-400 (a) and cross-section in the plane of work rolls (b)