Разработка модели совершенствования системы контроля качества частиц порошка красящего пигмента
Автор: Комаров Т.И., Пузырева В.С., Чабаненко А.В.
Журнал: Известия Самарского научного центра Российской академии наук @izvestiya-ssc
Рубрика: Машиностроение и машиноведение
Статья в выпуске: 3 т.25, 2023 года.
Бесплатный доступ
Постановка задачи (актуальность работы). Чаще всего, производство лакокрасочных изделий состоит из основных этапов: от поступления в складские помещения до фасовки по коробкам. И контроль качества осуществляется на входе и на выходе. Однако при производстве лакокрасочных изделий необходимо внедрить промежуточный контроль на этапе перемола пигментного сырья в порошок тонкого помола, так как от размерного диапазона частиц порошка тонкого помола зависят основные качества готовой лакокрасочной продукции. ГОСТ 2093-82 рекомендует использование ситового анализа, который представляет собой механизм просеивания решетом от наиболее крупных размеров ячеек до наиболее мелких. Однако данный метод уступает более современным по скорости анализа на более чем 10 минут, по диапазону измерения частиц на 10-30% и по информативности анализа. Цель работы. Повышение качества лакокрасочных материалов посредством внедрения промежуточного контроля методом лазерной дифракции. Используемые методы. В представленной работе были применены такие методы, как математическое моделирование, метод идеализации и формализации процессов исследования лакокрасочных материалов. Новизна. В ходе работы были разработаны новые механизмы оценки и управления качеством частиц порошка красящего пигмента, а также новые способы повышения эффективности производства лакокрасочных материалов. В процессе исследования был проведен анализ технологического процесса. Результат. Итогом работы стала разработанная модель совершенствования системы контроля качества частиц порошка красящего пигмента. Практическая значимость. Разработанная модель повысит результативность текущих процессов производства лакокрасочных изделий посредством внедрения промежуточного контроля, что повысит прибыль организации и сократит издержки на качество.
Контроль, качество, пигмент, порошок тонкого помола, лазерная дифракция
Короткий адрес: https://sciup.org/148326929
IDR: 148326929 | DOI: 10.37313/1990-5378-2023-25-3-16-25
Текст научной статьи Разработка модели совершенствования системы контроля качества частиц порошка красящего пигмента
На данный момент даже в крупных компаниях, производящих лакокрасочную продукцию, недостаточно уделяют внимание контролю качества процесса измельчения пигмента до состояния порошка. Чаще всего оценка сводится к визуальному осмотру.
В соответствии с ГОСТ 2093-82 анализ формы и размера частиц рекомендуется производить ситовым методом, который представляет собой механизм просеивания решетом от наиболее крупных размеров ячеек до наиболее мелких. Проблема заключается в том, что такой метод дает очень скромное представление о составе порошка, а изображение частиц и вовсе не
Комаров Тимофей Игоревич, магистрант.
предусмотрено. Кроме того, недостатком является ограниченность исследуемого размерного ряда и отсутствие автоматических систем.
Таким образом, требуется найти, изучить и внедрить такой метод анализа, который бы дал полную информацию о частицах, действовал автоматически и являлся выгодным вложением в качество.
Процесс производства лакокрасочных изделий состоит из 11 основных этапов (рис. 1).
На рисунке 1 видно, что проверка качества осуществляется только на входе сырья и на выходе готовой продукции.
ГОСТ 9.032-74 предписывает определенные свойства готовой лакокрасочной продукции: отсутствие волнистости, неоднородности структуры, разнооттеночности. [2, с. 3]
Данные требования формируют необходимость в контроле качества основного составляющего лакокрасочной продукции – порошкового пигмента. При внедрении промежуточного контроля появляется возможность регулировать выполнение вышеуказанных требований (рис. 2).
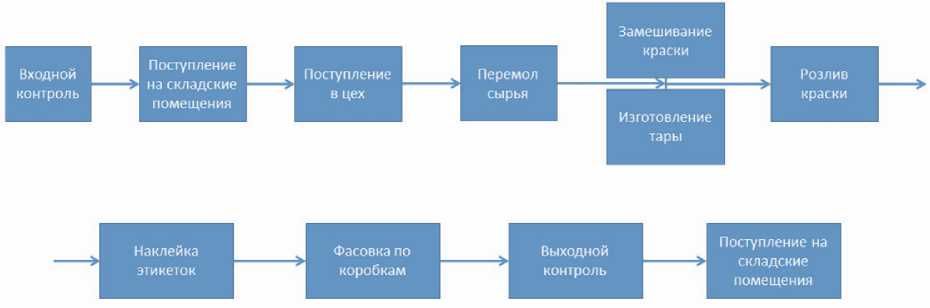
Рис. 1. Карта процессов для визуализации производства ЛКМ [1]
Fig. 1. Process map for visualization of paintwork production [1]
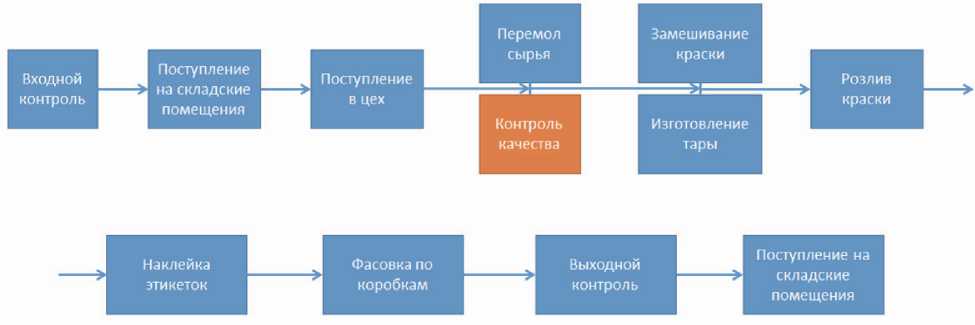
Рис. 2. Измененная карта процессов для визуализации производства ЛКМ Fig. 2. Modified process map for visualization of paintwork production
В соответствии с ГОСТ 2093-82 анализ формы и размера частиц рекомендуется производить ситовым методом, который представляет собой механизм просеивания решетом от наиболее крупных размеров ячеек до наиболее мелких (рис. 3).
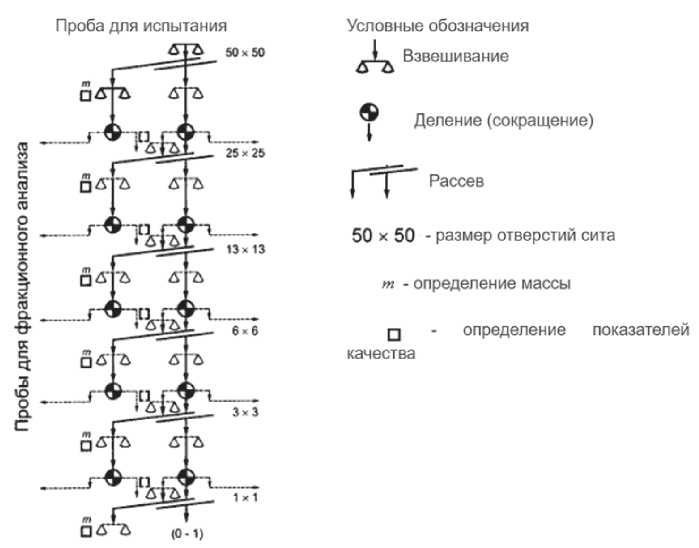
Рис. 3. Схема проведения ситового анализа по ГОСТ 2093-82 [3; с.4] Fig. 3. Scheme of sieve analysis according to GOST 2093-82
Проблема заключается в ограниченности исследуемого размерного ряда и в отсутствии автоматических систем. Кроме того, данный метод дает очень краткую информацию о составе порошка, а изображение частиц не предусмотрено. А, как было доказано, [4, с. 32-33] детальный анализ формы и размеров частиц позволяет определить, например, уровень прочности материала (рис. 4). [5]
На данный момент в России, кроме ситового анализа, существует еще несколько методов измерения и анализа частиц тонкого помола, среди которых: микроскопический метод, лазерная дифракция, динамический анализ и т.д. Компания «MICROTRAC» опубликовала данные о возможностях каждого метода анализа (рис. 5).
Сравнение характеристик методов анализа представлено в табл. 1.
Для частиц перемолотого пигмента необходим широкий диапазон измерения, скорость осуществления анализа и возможность анализа всех частиц. Наложив ограничения, продикто- ванные потребительскими ожиданиями, получим допустимые альтернативы (табл. 2).
Введем критерии для оценки: стоимость осуществления (К1), измеряемый диапазон (К2), полнота анализа (К3), сложность обучения сотрудников (К4), время измерений (К5).
Путем попарного сравнения, выявим наиболее предпочтительную альтернативу (табл. 3).
Таким образом, наиболее предпочтительный метод – «Лазерная дифракция (сухая)» (А2) со взвешенной оценкой = 0,348.
Лазерная дифракция – это метод измерения частиц путем направления на них лазерного луча. Луч отражается от частицы под некоторым углом. Как раз данные об этом угле и позволяют определить размер анализируемой частицы. [7] Аппарат выглядит следующим образом (рис. 6).
Имея наиболее предпочтительный метод анализа частиц пигментного порошка тонкого помола, построим имитационную модель распределения частиц.
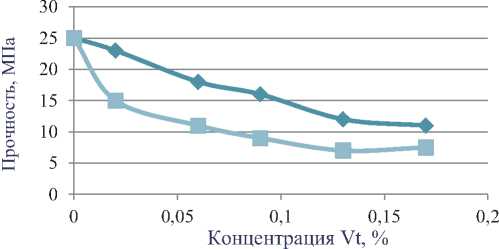
^^~ Размеры частиц 40-60 мкм
Размеры частиц 100-160 мкм
Рис. 4. Зависимость прочности композитов на основе СЭВА от содержания частиц SiO2 при разных размерах
Fig. 4. Dependence of the strength of CMEA-based composites on the content of SiO2 particles at different sizes
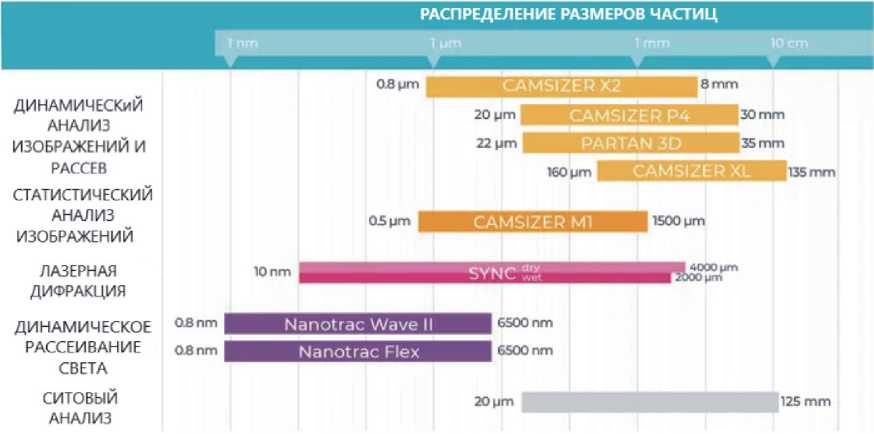
Рис. 5. Распределение частиц по размерам при данных методах анализа [6]
Fig. 5. Particle size distribution with these analysis methods [6]
Таблица 1 . Генерация альтернатив Table 1. Generation of alternatives
№ |
Наименование метода анализа |
Диапазон измерений, мкм |
Время измерения, мин |
Полнота анализа |
1 |
Динамический анализ |
0,8-80 |
20 |
Случайный анализ частиц (размер + форма) |
2 |
Анализ изображений и рассев |
20-30 |
15 |
Случайный анализ частиц (размер + форма) |
3 |
Статический анализ изображений |
0,5-1500 |
10 |
Анализ всех частиц (размер) |
4 |
Лазерная дифракция (сухая) |
0,01-4000 |
до 5 |
Анализ всех частиц (размер) |
5 |
Лазерная дифракция (влажная) |
0,01-2000 |
до 5 |
Анализ всех частиц (размер) |
6 |
Динамическое рассеивание света |
0,8-6,5 |
5-10 |
Случайный анализ частиц (размер) |
7 |
Ситовый анализ |
20-125000 |
5-10 |
Анализ всех частиц (размер) |
Таблица 2 . Допустимые альтернативы
Table 2. Acceptable alternatives
№ |
Наименование метода анализа |
Диапазон измерений, мкм |
Время измерения, мин |
Полнота анализа |
1 |
Статический анализ изображений |
0,5-1500 |
10 |
Анализ всех частиц (размер) |
2 |
Лазерная дифракция (сухая) |
0,01-4000 |
до 5 |
Анализ всех частиц (размер) |
3 |
Лазерная дифракция (влажная) |
0,01-2000 |
до 5 |
Анализ всех частиц (размер) |
4 |
Ситовый анализ |
20-125000 |
5-10 |
Анализ всех частиц (размер) |
Таблица 3 . Свертка альтернатив по критериям Table 3. Convolution of alternatives by criteria
Альтернативы |
Критерии |
Взвешенные оценки альтернатив |
||||
К 1 |
К |
К з |
К |
К |
||
А 1 |
0,070 |
0,093 |
0,206 |
0,446 |
0,182 |
0,182 |
А 2 |
0,274 |
0,401 |
0,449 |
0,160 |
0,347 |
0,348 |
А з |
0,171 |
0,335 |
0,172 |
0,104 |
0,273 |
0,217 |
А |
0,485 |
0,171 |
0,172 |
0,290 |
0,198 |
0,253 |
2 |
1 |
106,000 -I |
||||||||
Й 1 ЛЛЛ - |
||||||||
О 104,000 О- , У 1 Л9 ЛЛЛ - |
||||||||
2 102,000 со 5 5 й 1 лл ллл . |
1 |
|||||||
Он * 100,000 (D К ^ ОЙ ЛЛЛ - |
||||||||
Й у 78,000 - К Ь QA ЛЛЛ |
||||||||
£ о 76,000 - И" о У Q/1 ЛЛЛ - |
• |
• |
||||||
74,000 у о СП ЛЛЛ - |
• |
|||||||
у ^2,000 0Л ЛЛЛ - |
||||||||
70,000 ~1 ( |
1 |
2 |
3 |
4 |
5 |
6 |
7 |
8 |
Уровень затемнения, %
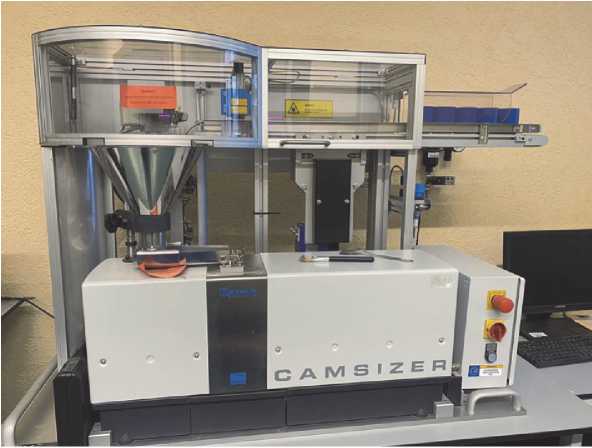
Рис. 6. Лазерный анализатор
Fig. 6. Laser analyzer
Рис. 7. Анализ размеров частиц по % затемнения [9; с.14] Fig. 7. Particle size analysis by % dimming
Дисперсия воспроизводимости для всего эксперимента рассчитывается по формуле (3).
Ошибка всего эксперимента вычисляется по
с2 _ с2 _A VN S'2
,
= 5 264 .
формуле (4).
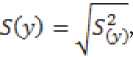

Таблица 4. Матрица планирования и результаты эксперимента Table 4. Planning matrix and experiment results
Планирование |
Выход |
||||||
N |
X0 |
X1 |
X2 |
X3 |
Y1 |
Y2 |
Y3 |
1 |
+ |
- |
- |
- |
93,01 |
96,80 |
91,00 |
2 |
+ |
+ |
- |
- |
95,20 |
97,90 |
91,50 |
3 |
+ |
- |
+ |
- |
97,90 |
98,00 |
93,58 |
4 |
+ |
+ |
+ |
- |
98,10 |
99,10 |
94,00 |
5 |
+ |
- |
- |
+ |
99,00 |
99,50 |
95,20 |
6 |
+ |
+ |
- |
+ |
102,00 |
101,90 |
99,50 |
7 |
+ |
- |
+ |
+ |
103,70 |
103,50 |
101,50 |
8 |
+ |
+ |
+ |
+ |
104,15 |
104,30 |
103,10 |
Таблица 5. Расчет значений Table 5. Calculation of values
N |
Планирование |
Выход |
У . |
у2 авоспр |
|||||||||
X0 |
X1 |
X2 |
X3 |
X1X2 |
X1X3 |
X2X3 |
X1X2X3 |
Y1 |
Y2 |
Y3 |
|||
1 |
+ |
- |
- |
- |
+ |
+ |
+ |
- |
93,01 |
96,80 |
91,00 |
93,60 |
8,67 |
2 |
+ |
+ |
- |
- |
- |
- |
+ |
+ |
95,20 |
97,90 |
91,50 |
94,87 |
10,32 |
3 |
+ |
- |
+ |
- |
- |
+ |
- |
+ |
97,90 |
98,00 |
93,58 |
96,49 |
6,37 |
4 |
+ |
+ |
+ |
- |
+ |
- |
- |
- |
98,10 |
99,10 |
94,00 |
97,07 |
7,30 |
5 |
+ |
- |
- |
+ |
+ |
- |
- |
+ |
99,00 |
99,50 |
95,20 |
97,90 |
5,53 |
6 |
+ |
+ |
- |
+ |
- |
+ |
- |
- |
102,00 |
101,90 |
99,50 |
101,13 |
2,00 |
7 |
+ |
- |
+ |
+ |
- |
- |
+ |
- |
103,00 |
102,00 |
101,00 |
102,00 |
1,48 |
8 |
+ |
+ |
+ |
+ |
+ |
+ |
+ |
+ |
104,15 |
104,30 |
103,10 |
103,85 |
0,43 |
Сумма: |
787,81 |
42,11 |
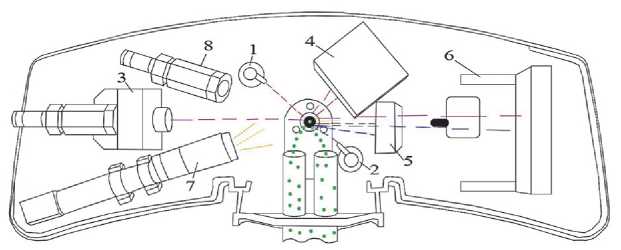
Рис. 9. Схематичное изображение оптической системы разработанного лазерного анализатора
Fig. 9. Schematic representation of the optical system of the developed laser analyzer
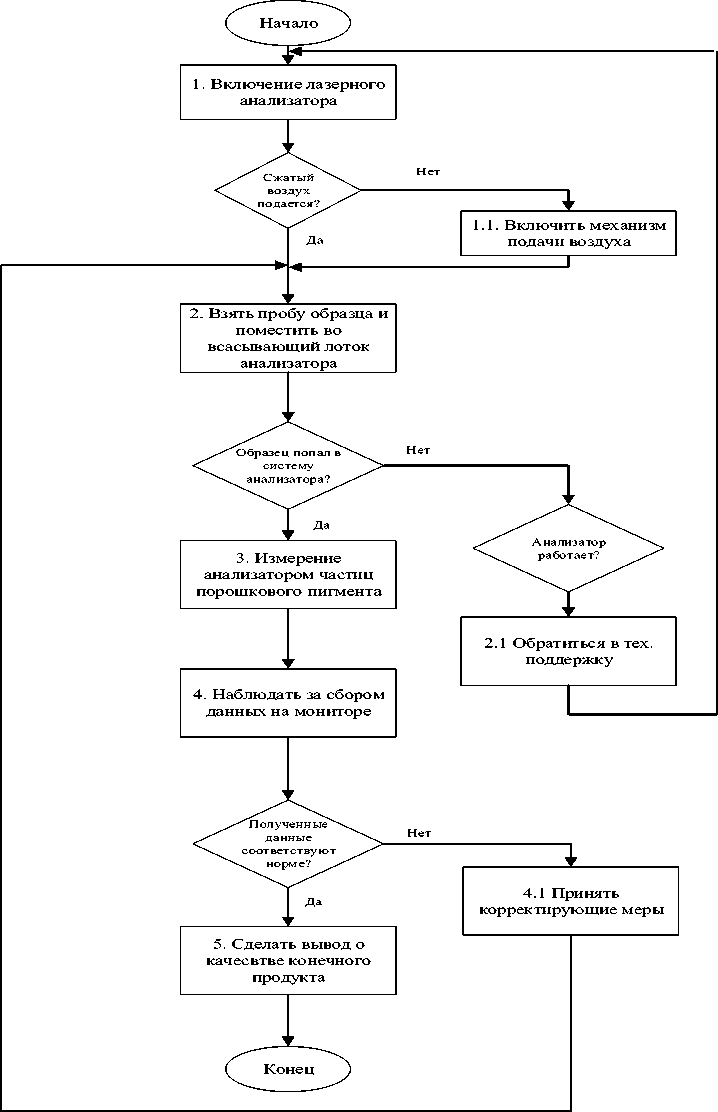
Рис. 10. Алгоритм процесса измерения
Fig. 10. Algorithm of the measurement process
Американская фармацевтическая компания «Review» опубликовала данные об измерениях размеров частиц пигментов разного предназначения при определенной степени затемнения (рис. 7). Было выяснено, что распределение частиц по размерам имеет нормально распределение. Значит, есть возможность построить функциональную эмпирическую модель, характеризующую это распределение.
Матрица планирования эксперимента представлена в табл. 4.
Среднее значение параметра по параллельным опытам вычисляется по формуле (1).
где – число параллельных опытов в i-ой сточ-
ке матрицы планирования; – значение вы ходного параметра.
Дисперсия параллельных опытов вычисляется по формуле (2).
, (2)
где – число параллельных опытов в i-ой сточке матрицы планирования; – значение выходного параметра; – среднее значение параметра по параллельным опытам.
Все результаты внесены в табл. 5.
Из таблицы 5 видно, что для 2 и 8 опыта величина дисперсий больше/меньше остальных, поэтому была осуществлена проверка дисперсий с использованием критерия Кохрена.
Коэффициенты уравнения рассчитываются по формулам (5), (6), (7).
,(5)
,(6)
,(7)
где N – количество опытов.
После расчета всех коэффициентов уравнение регрессии принимает следующий вид:
у = 98,48 + 0,75^ + 1,6Х2 + 2,97Х3 -
.
После проверки статистической значимости коэффициентов с помощью t-критерия Стьюдента, выяснилось, что коэффициенты уравнения b12, b13, b23 и b123 оказались статистически не значимыми и уравнение регрессии принимает вид:
у = 98,48 + 0,75^ + 1,6Х2 + 2,97Х3
Для доказательства адекватности модели и оценки отклонений вычисленных по уравнениям регрессии значений функции был использован критерий Фишера F-критерий.
Таким образом, функциональная эмпирическая модель имеет следующий вид:
. (8)
Модель означает, что при задании факторов Х1, Х2, Х3 (степени затемнения для каждого из трех лазеров), частицы будут распределяться близ прямой, заданной данным уравнением. Можно сказать, что с увеличением значений факторов Х2 и Х3 (уровня затемнения на лазеров 2 и 3), то и значения результатов будут увеличиваться (так как коэффициенты b2 и b3 – положительны). А с увеличением фактора Х1, значения измерения будут уменьшаться, так как коэффициент b1 имеет отрицательное значение. [10;с.10-14]
Внешнее схематичное изображение установки представлено на рис. 8.
Исследуемый образец 1 устанавливается на лоток 2 и всасывается в систему анализатора.
Система доставки образца 3 направляет сжатый воздух 4 через встроенные сопла, обеспечивая «торможение» частиц материала перед подачей в измерительную ячейку 5.
Внутреннее схематичное изображение измерительной ячейки представлено на рис. 9.
Для измерения используются лазерные диоды и системы анализа изображений. Оптическая система состоит из трех диодных лазеров 1,2,3, трех постоянно включенных детекторов 4,5,6, находящихся в фиксированных точках. Лазерные детекторы улавливают свет, рассеянный под углом 165о. Одновременно отдельный светодиодный источник света 7 освещает кювету с образцом, высокоскоростная цифровая камера 8 фиксирует изображение частиц. Данные анализируются с помощью специального программного обеспечения, использующего функциональную эмпирическую модель (21), где Х1,Х2,Х3 – это факторы, влияющие на частицу.
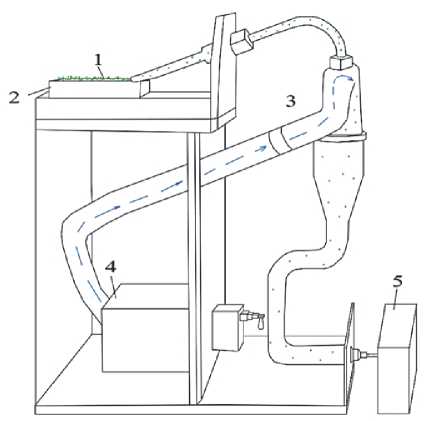
Рис. 8. Схематичное изображение разработанного лазерного анализатора Fig. 8. Schematic representation of the developed laser analyzer

-
3.1. Попадание исследуемого образца в измерительную ячейку
датчик
опадани
Сработал
автоматический
Нет
Да
3.2. Автоматическое включение детекторов в фиксированных точках
Детекторы
включены ?
Нет
Да
3.3. Автоматическое
детекторы вручную
3.2.1. Включить
Датчик
исправен?
Датчик
включен ?
Нет
датчик вручную
Нет
3.1.2. Заменить
Да
3.1.1. Включить
датчик
3.1.3. Обратитесь в тех. поддержку
установление рассеяного света под углом 165°
Свет
установлен?
Да
3.4. Автоматическое включение 3-х
Нет
Детекторы
аботают ?
Да
Нет
3.2.2. Обратитесь в тех. поддержку
3.3.1. Установление
лазеров
Лазеры
включены ?
Нет
Да
3.5. Установление уровня затемнения каждого лазера в ПО в % задаем Х 1 ,Х 2 ,Х 3 Для уравнения регрессии:
у =98,48-0,75X 1 + 1,6X 2 +2,97X 3
рассеянного света вручную
Свет
становлен?
Нет
Да
3.3.2. Обратитесь в тех. поддержку
3.4.1. Включить
лазеры вручную
3.6 Автоматическое
включение высокоскоростной камеры
Камера
вкдючена ?
Лазеры
включены ?
Нет
Да
3.6.1 Включить
Да
камеру вручную
3.7. Измерение частиц порошкового пигмента лазерным анализатором
3.4.2. Обратитесь в тех. поддержку
3.8. Анализ полученных данных относительно линии регрессии
Камера
включена?
Нет
Да
3.6.2. Обратитесь в тех. поддержку
Рис. 11. Алгоритм процесса измерения лазерным анализатором
Fig. 11. Algorithm of the laser analyzer measurement process
В целом, общий алгоритм анализом методом лазерной дифракции представлен на рис. 10.
Алгоритм процесса измерения части порошкового пигмента представлен на рис.11.
ЗАКЛЮЧЕНИЕ
Таким образом, выполнить главные требования заинтересованных сторон механическим человеческим трудом не представляется возможным, поэтому необходимо прибегнуть к автоматизации, роботизации и цифровизации процесса анализа распределения по размерам частиц тонкого помола.
В ходе исследования была разработана модель совершенствования системы контроля качества частиц порошка красящего пигмента, с помощью которой производство получает точные данные о характеристиках и параметрах частиц. Система анализирует не только размер, но и предоставляет изображение исследуемых частиц, что позволяет повысить прибыль организации и сократит издержки на качество.
Список литературы Разработка модели совершенствования системы контроля качества частиц порошка красящего пигмента
- Мануленко, А.Ф. Технология лакокрасочных материалов и покрытий. Проектирование производств / А.Ф. Мануленко. - Минск: БГТУ, 2021. - 114 с.
- ГОСТ 9.032-74. Единая система защиты от коррозии и старения. Покрытия лакокрасочные. Группы, технические требования и обозначения. - М.: Стандартинформ, 1989. - 5 с.
- ГОСТ 2093-82. Ситовый метод определения гранулометрического состава. - М.: Стандартинформ, 2015. - 20 с.
- Десятков, A.В. Влияние размера частиц на механические свойства композитов на основе однородно деформирующегося полимера / A.В. Десятков. - М.: Академия естествознания, 2009. - Т.23. №5. - С. 32-33.
- Александров, А.А. Взаимосвязь между геометрическими параметрами зерен шлифовальных порошков, исследованная методами лазерной дифракции и оптической микроскопии / А.А. Александров // Современные научные исследования и инновации. - 2018. - № 5(85). - 8 с.
- Microtrac MRB: Сравнение методов определения размеров частиц - URL: https://www.microtrac.com/ru (дата обращения 29.11.2022).
- Фармакопея: Определение распределения частиц по размеру методом лазерной дифракции света. - URL: https://pharmacopoeia.ru (дата обращения 15.12.2022).
- Гарибей К., Олсон Э., Салсбери Дж. С. Понимание взаимосвязи между источниками красного и синего света при определении профилей распределения частиц по размерам. - URL: https://www.americanpharmaceuticalreview.com (дата обращения 29.01.2023).
- Пузырева, В.С. Исследование метода анализа распределения частиц тонкого помола / В.С. Пузырева. - Пенза: Молодые учёные России, 2021. - 338 с.
- Пузырева, В.С. Построение функциональной эмпирической модели распределения по размерам частиц тонкого помола / В.С. Пузырева. - Пенза: Фундаментальные и прикладные научные исследования, 2022. 222 с.