Разработка оптимальных технологических параметров селективного синтеза жидких и твердых углеводородов в реакторах трубчатого типа
Автор: Яковенко Р.Е., Нарочный Г.Б., Земляков Н.Д., Бакун В.Г., Савостьянов А.П.
Журнал: Известия Самарского научного центра Российской академии наук @izvestiya-ssc
Рубрика: Технологии добычи и переработки нефти и газа
Статья в выпуске: 4-4 т.13, 2011 года.
Бесплатный доступ
Определено влияние объемной скорости газа, давления, линейной скорости газа на селективность и производительность кобальтовых катализаторов по жидким и твердым углеводородам в трубчатом реакторе процесса синтеза Фишера-Тропша. Наибольшая производительность по переработке СО достигается при проведении процесса в проточном режиме при объемной скорости газа 1500 ч- 1 и давлении 1,5 МПа. Однако в этом случае образуется преимущественно метан, так как нарушается изотермичность каталитического слоя за счет большого выделения реакционного тепла. С использованием математической модели выполнены численные исследования процесса в проточно-циркуляционном режиме. Определено, что использование проточно-циркуляционного варианта технологической схемы позволяет достигнуть изотермичности по высоте слоя катализатора и обеспечить высокий выход и селективность по жидким и твердым углеводородам.
Синтез фишера-тропша, трубчатый реактор, изотермичность, кобальтовый катализатор, синтез-газ, производительность, селективность
Короткий адрес: https://sciup.org/148200275
IDR: 148200275
Текст научной статьи Разработка оптимальных технологических параметров селективного синтеза жидких и твердых углеводородов в реакторах трубчатого типа
представляют собой многокомпонентную смесь широкой фракции углеводородов с неявно выраженным максимумом. Выход и состав продуктов синтеза определяется свойствами катализатора и технологическими параметрами процесса: температура, давление, состав и объемная скорость газа (ОСГ).
Важной задачей при промышленном производстве синтетических углеводородов является повышение селективности и производительности процесса по заданной группе продуктов: газообразные углеводороды (С 1 -С 4 ), бензины (С 5 -С 10 ), дизельная фракция (С 11 -С 18 ), парафины и церезин (С 60+ ). Изменение селективности процесса часто происходит в условиях, не позволяющих объективно оценить влияние лишь одного исследуемого параметра, так как накладывается воздействие других факторов. Например, изменение условий синтеза путём повышения давления одновременно приводит к изменению реального времени контактирования и изменению характера диффузионных процессов внутри зерна катализатора [25]. Это, в свою очередь, влияет на селективность процесса.
Обычно для управления процессом ФТ используется априорная информация о степени влияния тех или иных технологических параметров на состояние процесса. Прогнозирование селективности и выхода различных продуктов в синтезе ФТ даже с применением математической модели – непростая задача. Очевидно, что проблема получения продукта с максимальным содержанием желаемой фракции углеводородов и достижение при этом наибольшей производительности процесса является актуальной при разработке и эксплуатации таких производств.
Состав продуктов синтеза углеводородов из СО и Н 2 определяется природой катализатора. На железных катализаторах при давлении 2,5-3,0 МПа и температуре 230-240°С образуются в основном олефины. На рутениевых катализаторах, активных при высоких давлениях 10-100 МПа и температуре 120-130°С, синтезируется полиметилен с молекулярной массой до 100000. Наиболее перспективными катализаторами синтеза углеводородов считаются кобальтовые системы, которые при давлении 0,1-3,0 МПа и температуре 160-230°С позволяют селективно получать предельные углеводороды линейного строения фракции С 9 -С 16 , которые являются аналогами керосина и дизельного топлива [6]. Пористая структура катализатора и гидродинамическая обстановка в реакторе определяют макрокинетические показатели процесса синтеза ФТ. Большинство результатов исследований подтверждают влияние диффузионных стадий и роль массопере-носа на изменение производительности и селективности процесса синтеза углеводородов. Массоперенос фактически изменяет условия, формирующие систему «катализатор – реакционная среда», и, соответственно, меняется селективность по отдельным группам углеводородов. Например, для увеличения селективности по С 60+ необходимо обеспечить перевод процесса в глубокую внутридиффузионную область [5]. Такой эффект обеспечивает мелкопористая структура катализатора. Однако в этом случае вероятно снижение скорости диффузии исходных реагентов и, как следствие, уменьшение производительности катализатора. Поэтому предпочтительно использовать структуру, имеющую би- или полидисперсный характер распределения пор по радиусам, включающую в себя крупные транспортные поры.
Существенную роль в процессе ФТ играет температура. Температурный интервал синтеза углеводородов определяется используемым катализатором. Селективность процесса значительно изменяется с повышением температуры в сторону понижения молекулярной массы углеводородов вплоть до метана. Регулирование этого параметра наиболее важно с позиций управления селективностью и производительностью процесса. Процесс ФТ протекает с большим тепловыделением. Отвод большого количества тепла в ходе синтеза представляет собой важнейшую проблему при проектировании и эксплуатации промышленных установок. Градиент температур наблюдается как в отдельной грануле катализатора, приводящий к локальным перегревам в зерне контакта, так и в слое контактной массы. Решить эту проблему до настоящего времени пытаются за счет оптимизации конструкции контактного аппарата, обеспечивающей специальную организацию каталитического слоя с целью снижения вероятности перегревов и снижения газодинамического сопротивления.
Разработаны трехфазные суспензионные реакторы (slurry reactor), реакторы с псевдоожиженным слоем катализатора, реакторы полочного типа (аксиальные и радиальные), а также трубчатые. Каждый тип реактора имеет свои достоинства и недостатки. Наибольшее распространение получили трубчатые реакторы, которые широко используются компаниями Shell, Sasol [7]. Катализатор в виде гранул помещается внутри труб, разделяющих реакционное пространство с катализатором и теплоноситель (вода-водяной пар), за счет нагревания которого осуществляется отвод тепла. Однако низкая теплопроводность катализатора приводит к значительным градиентам температур, как в самом слое, так и на границе катализатор – трубка. В результате существенно снижается точность измерения температуры, управление селективностью процесса, увеличивается вероятность закоксовывания и дезактивации катализатора. Сохраняется высокая опасность выхода из строя трубки целиком, что существенно снижает эффективность работы реактора в целом. Замена трубки представляет собой крайне трудную процедуру, требующую остановки работы всего реактора.
Повысить изотермичность слоя катализатора в трубчатом реакторе можно за счет увеличения турбулизации потока газа. При этом возрастут коэффициенты тепло- и массопере-дачи, увеличится конвективная составляющая теплопереноса. В работе [8] было показано, что за счет циркуляции прореагировавшего синтез-газа значительный рост коэффициента теплоотдачи происходит при объемной скорости газа (ОСГ) 5000ч-1 и выше. При этих условиях коэффициент теплоотдачи увеличивается в 10-15 раз.
Цель работы: определение области технологических параметров проведения процесса синтеза ФТ, в которой достигается максимальная производительность и селективность по жидким и твердым углеводородам в реакторе трубчатого типа.
На первом этапе экспериментально исследовано влияние объемной скорости газа и давления на производительность и селективность процесса ФТ в проточном режиме. Синтез проводили в присутствии кобальтового катализатора на носителе Al 2 O 3 размером 2-2,5 мм. Перед испытанием катализатор восстанавливали в токе водорода при температуре 400°С и объемной скорости 1000 ч-1 в течение 60 минут, доводя степень восстановления Со (соотношение металлического Со и общего содержания этого компонента в катализаторе) до 55%. Испытание катализатора осуществляли в трубчатом реакторе с внутренним диаметром 26 мм при давлениях 0,1-1,5 МПа и объемных скоростях газа от 100 ч-1 до 1500 ч-1. Объем
Технологии добычи и переработки нефти и газа загружаемого катализатора – 30 см3. При этом расход синтез-газа увеличивали пропорционально давлению с тем, чтобы время контактирования для каждого рабочего давления оставалось постоянным. Перед испытанием проводили разработку катализатора в токе синтез-газа (соотношение Н 2 /СО=2) при атмосферном давлении и объемной скорости газа 100 ч-1. Разработку начинали со 150°С; каждые 2 ч повышали температуру на 5-10 градусов до контракции (степень уменьшения объема синтез-газа в ходе реакции) не менее 40%. Испытания проводили при температуре синтез-газа на входе в реактор 2100С. Результаты исследований катализатора представлены в табл. 1-4 и на рис. 2-4.
Таблица 1. Влияние объемной скорости газа при различном давлении на показатели процесса ФТ
Давление, МПа |
ОСГ, ч-1 |
K, % |
К СО , % |
S CH4 , % |
S C5+ , % |
В С5+ , г С 5+ /нм3 |
W СО , дм3 СО/кг кат ·ч |
0,1 |
100 |
40,8 |
44,2 |
29,8 |
70,2 |
68,8 |
23,3 |
1,0 |
1000 |
70,5 |
95,8 |
72,3 |
23,5 |
47,8 |
443,3 |
1,5 |
1500 |
64,0 |
98 |
72,3 |
- |
- |
661,7 |
Обозначения: К – контракция, КСО – степень конверсии СО , SCH4 – селективность по метану, SC5+ – селективность по углеводородам С 5+ , В С5+ – выход углеводородов С 5+ в расчёте на пропущенный через реактор синтез-газ; WСО – производительность по СО
Анализ данных показывает, что с увеличением давления контракция синтез-газа и конверсия СО возрастает. Степень конверсии при давлении 1,0 и 1,5 МПа достигает 95,8% и 98,0%, соответственно. Производительность по СО возросла в 19 раз при увеличении объемной скорости до 1000 ч-1 и в 28 раз при увеличении объемной скорости до 1500 ч-1. При этом селективность и выход по углеводородам С5+ с ростом давления и объемной скорости газа снижается, а селективность по метану увеличивается (табл. 1). Это объясняется тем, что с ростом нагрузки на катализатор количество выделившегося тепла увеличивается, и градиент температур по слою возрастает (рис. 1). С увеличением производительности катализатора по СО изотермичность слоя нарушается. Так, при объемной скорости газа 1500 ч-1 и давлении 1,5МПа температура в верхней части слоя катализатора возросла до 2800С, что привело к увеличению селективности по метану и резкому снижению производительности по жидким углеводородам. Таким образом, высокая производительность по переработке СО не позволяет при данных технологических параметрах достигнуть высокой селективности по жидким и твердым углеводородам, так как не обеспечивается эффективный теплоотвод из зоны реакции. Снижение нагрузки по катализатору при фиксированном давлении (1,0 МПа) увеличивает селективность по углеводородам С5+. При снижении линейной скорости газа в 2 раза селективность по углеводородам возросла в 3,5 раза, а производительность по переработанному СО снизилась в 3 раза (табл. 2). При этом распределение температуры по длине слоя катализатора близко к изотермичному (рис. 1). Состав продуктов синтеза ФТ приведен в табл. 3, 4 и на рис. 2.
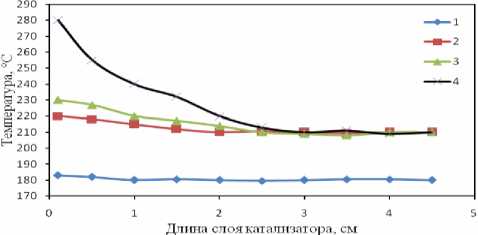
Рис. 1. Распределение температуры по длине слоя катализатора:
1 – ОСГ 100 ч-1, P = 0,1МПа; 2 – ОСГ 500 ч-1, P=1,0 МПа; 3 – ОСГ 1000 ч-1, P =1,0МПа; 4 – ОСГ 1500 ч-1, P =1,5 МПа
Таблица 2. Влияние линейной скорости газа на показатели процесса ФТ (Р=1,0 МПа)
Линейная скорость газа, ω·104м/с |
ОСГ, ч-1 |
Давление, МПа |
K, % |
К СО, % |
S CH4 , % |
S C5+ , % |
B С5+ , г С 5+ /нм3 |
W СО , л СО/кг кат ·ч |
8 |
500 |
1,0 |
57,6 |
67,9 |
16,9 |
83 |
119,7 |
150 |
16 |
1000 |
1,0 |
70,5 |
95,8 |
72,3 |
23,5 |
47,8 |
443,3 |
Таблица 3. Состав газовой фазы продуктов синтеза
ОСГ, ч-1 |
Давление, МПа |
Состав газовой фазы, % об. |
|||||
СО |
Н 2 |
СН 4 |
С 2 Н 6 |
С 3 Н 8 |
С 4 Н 10 |
||
100 |
0,1 |
31,7 |
56,7 |
9,0 |
0,0 |
0,0 |
0,6 |
500 |
1,0 |
28,4 |
61,3 |
10,2 |
0,0 |
0,0 |
0,0 |
1000 |
1,0 |
4,6 |
7,8 |
77,7 |
9,8 |
4,6 |
7,8 |
1500 |
1,5 |
0,7 |
6,8 |
82,3 |
5,6 |
0,7 |
6,8 |
Таблица 4. Фракционный состав продуктов синтеза при различных давлениях и ОСГ
ОСГ, ч-1 |
Давление, МПа |
Фракционный состав, % масс. |
||
С 5 -С 10 |
С 11 -С 19 |
С 19+ |
||
100 |
0,1 |
35,8 |
54,3 |
9,9 |
500 |
1,0 |
30,7 |
54,7 |
16,6 |
1000 |
1,0 |
14,1 |
74,5 |
11,4 |

а)
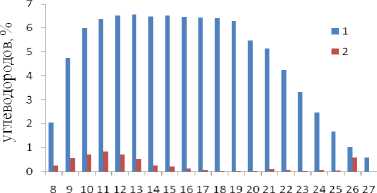
Углеродное число
б)
Рис. 2. Молекулярно-массовое распределение углеводородов в продуктах синтеза: а – при ОСГ 500 ч-1, Р = 1,0 МПа; б – при ОСГ 1000 ч-1, Р = 1,0 МПа; 1 – н-парафины; 2 – изопарафины
На рис. 3 показана зависимость производительности по СО от объемной скорости газа при различных давлениях. Кривая 2 соответствует проведению процесса при одинаковом времени контактирования. При этом наблюдается линейная зависимость. Точка на изломе линии 1 соответствует технологическим параметрам, при которых время контактирования увеличено в 2 раза (ОСГ 500 ч-1, P=1,0МПа) и, как следствие, уменьшается производительность по СО.
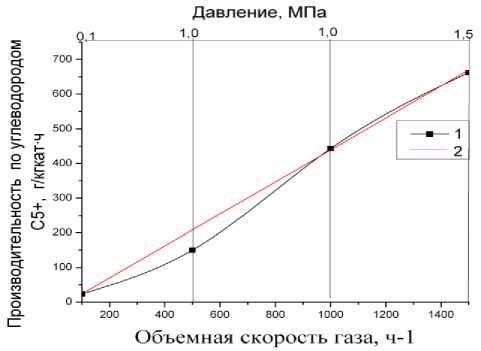
Рис. 3. Зависимость производительности по СО от объемной скорости газа при различном давлении: 1 – при разном времени контактирования; 2 –при постоянном времени контактирования
На рис. 4 представлена зависимость производительносити по С 5+ от объемной скорости газа при различных давлениях. Кривая 2 соответствует проведению процесса при одинаковом времени контактирования, кривая 1 – увеличению времени контактирования в 2 раза. При увеличении времени контактирования производительность по углеводородам С 5+ резко возрастает.
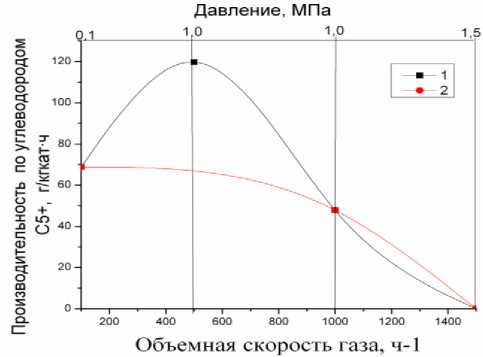
Рис. 4. Зависимость производительности по углеводородам С 5+ от объемной скорости газа: 1 – при разном времени контактирования; 2 – при постоянном времени контактирования
Из анализа экспериментальных данных следует, что наибольшая производительность по СО достигается при повышенном давлении и высокой объемной скорости газа (P=1,5 МПа, ОСГ 1500 ч-1). Однако при этих условиях существенно возрастает количество выделившегося реакционного тепла и при проведении процесса в трубчатом реакторе в проточном режиме трудно обеспечить эффективный теплоотвод, нарушается режим изотермичности работы реактора и снижается селективность по жидким и твердым углеводородам. Одним из решений проблемы отвода тепла из зоны реакции может быть увеличение линейной скорости газового потока в продольном сечении реактора без снижения производительности и селективности. Этого можно добиться за счет циркуляции непрореагировавшего газа.
С использованием математической модели (FT-model) произведены расчеты процесса синтеза ФТ в проточно-циркуляционном режиме. Исходные данные для расчёта характеристик лабораторного реактора: катализатор Co/ Al 2 O 3 , объемом 30 см3; диаметр трубки реактора 26 мм; температура на входе в реактор 1700С; температура хладагента 2200С; давление 2,0 МПа; ОСГ 1500 ч-1, кратность циркуляции 4. Для обеспечения заданной объемной скорости газа при выбранной кратности циркуляции расход по свежему газу составлял 9 дм3/ч. Результаты расчётов представлены в табл. 5-7 и на рис. 5.
Таблица 5. Влияние технологического режима на показатели процесса синтеза Фишера-Тропша
Технологический режим |
Степень превращения СО, % |
Селективность |
Выход по углеводородам С 5+ , г/нм3 |
Производительность по СО, дм3/кг кат ·ч |
|
по метану, % |
по углеводородам С 5+ , % |
||||
проточноциркуляционный |
57,7 |
12,3 |
83,3 |
108,2 |
390,9 |
проточный |
98,0 |
72,3 |
0,0 |
0,0 |
661,7 |
Проведение процесса синтеза ФТ в циркуляционном режиме позволяет проводить процесс в режиме близкому к изотермическому (рис. 5), при этом возрастает селективность по жидким и твердым углеводородам, снижается содержание метана. Снижение производительности по СО в проточно-циркуляционном режиме объясняется также стабилизацией температуры в слое катализатора. В проточном режиме, за счет резкого повышения температуры в лобовой части слоя катализатора, переработка синтез-газа осуществлялась до метана, чем и объяснятся более высокая производительность по СО. Соотношение в рециркулируемом газе Н 2 /СО близко к 2, что является оптимальным для проведения синтеза. В составе газовой фазы продуктов синтеза преобладают СО, Н 2 , СН 4 .
Сравнительный анализ состава жидких и твердых продуктов синтеза позволил установить, что при проведении процесса в проточноциркуляционном режиме в составе продуктов возрастает доля твердых углеводородов С19+. В фракционном составе углеводородов преобладают углеводороды фракции С11-С19. При переходе от проведения процесса в проточном режиме к проточно-циркуляционному возрастает доля углеводородов фракции С5-С10.
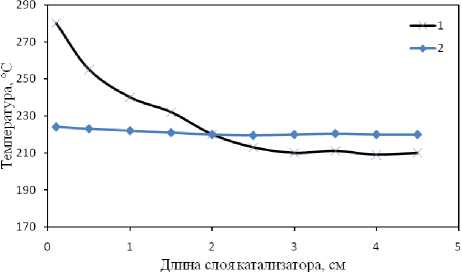
Рис. 5. Распределение температуры по длине слоя катализатора при различных технологических режимах: 1 – в проточном режиме; 2 – в проточно-циркуляционном режиме
Таблица 6. Состав газовой фазы продуктов синтеза в проточно-циркуляционном режиме |
2 3 |
|||||
Содержание, % об. |
||||||
СО |
Н 2 |
СН 4 |
С 2 Н 6 |
С 3 Н 8 |
С 4 Н 10 |
|
26,5 |
58,7 |
14,9 |
0,0 |
0,0 |
0,6 |
Таблица 7. Фракционный состав продуктов 4. синтеза в проточно-циркуляционном режиме
ОСГ, ч-1 |
Давление, МПа |
Фракционный состав, % масс. |
5 |
||
С 5 -С 10 |
С 11 -С 19 |
С 19+ |
|||
1500 |
2,0 |
37,4 |
43,4 |
18,6 |
Вывод: проведение процесса в проточно-циркуляционном режиме позволяет обеспечить изотермичность каталитического слоя, 6. снизить выход метана, повысить селективность и производительность по жидким и 7. твердым углеводородам.
Список литературы Разработка оптимальных технологических параметров селективного синтеза жидких и твердых углеводородов в реакторах трубчатого типа
- Крылова, А.Ю. Катализаторы синтеза Фишера-Тропша -ядро стратегии получения синтетических жидких топлив/А.Ю. Крылова//Российский конгресс по катализу Роскатализ. 2011. Т. 1. С. 39.
- Боресков, Г.К. Гетерогенный катализ. -М.: Наука, 1986. 304 с.
- Ермолаев, В.С. Исследование влияния капиллярной конденсации на процессы тепломассопереноса в зерне катализатора синтеза Фишера-Тропша/В.С. Ермолаев, В.З. Мордкович, И.Г. Соломоник//Теоретические основы химической технологии. 2010. Том 44, № 5. С. 516-520.
- Хасин, А.А. Контактные каталитически активные мембраны для процесса синтеза фишера-тропша/А.А. Хасин, А.Г. Сипатров, В.Н. Пармон//Серия Критические технологии. Мембраны. 2005. № 4 (28). С.6-15.
- Савостьянов, А.П. Селективный синтез жидких и твердых углеводородов из оксида углерода и водорода/А.П. Савостьянов, В.Г. Бакун, В.С. Будцов и др.//Южно-Рос. Гос. Техн. Ун-т (НПИ). -Новочеркасск: УПЦ "Набла" ЮРГТУ (НПИ), 2005. 164 с.
- Крылов, О.В. Синтез Фишера-Тропша//Катализ в промышленности. 2008. №1. С. 9-13.
- Хасин, А.А. Обзор технологий получения СЖТ, разработанных компаниями Shell и Sasol//Газохимия. 2008. № 4(3). С. 38-48.
- Савостьянов, А.П. Обоснование использования циркуляционных схем в синтезе углеводородов из СО и Н2/А.П. Савостьянов, Г.Б. Нарочный, Н.Д. Земляков, Р.Е. Яковенко//Известия Самарского научного центра Российской академии наук. 2010. Т. 12, № 4(3). С. 686-690.