Разработка ресурсосберегающей технологии получения крупногабаритных отливок из титановых сплавов
Автор: Деменок Анна Олеговна, Ганеев Альмир Амирович, Деменок Олег Борисович, Бакерин Сергей Васильевич, Кулаков Борис Алексеевич
Журнал: Вестник Южно-Уральского государственного университета. Серия: Металлургия @vestnik-susu-metallurgy
Рубрика: Литейное производство
Статья в выпуске: 2 т.15, 2015 года.
Бесплатный доступ
Целью работы является разработка ресурсосберегающей технологии получения крупногабаритных отливок из титановых сплавов деталей авиационного назначения центробежной заливкой в оболочковые формы с использованием связующих на водной основе. В работе приведена технология получения оболочковых форм на основе водного связующего Remasol с добавлением в огнеупорную суспензию 5 % АСД-4 для центробежного литья титановых сплавов. Проведены исследования по определению величины альфированного слоя на реальных отливках. Показана возможность использования оболочковых форм на основе водного связующего Remasol и комбинированных оболочковых форм для литья титановых сплавов. По результатам механических испытаний и исследований альфированного слоя разработана технология изготовления оболочковых форм для литья крупногабаритных отливок. Предложено использовать в качестве связующего для изготовления оболочковых форм связующее Remasol с добавлением в суспензию АСД-4 в количестве 5 %. Для проверки рекомендованных связующих материалов в реальных условиях по разработанной технологии были изготовлены керамические оболочковые формы отливок деталей и залиты совместно с формами, изготовленными по серийной технологии. Заливка блоков производилась в вакуумной электродуговой плавильно-заливочной установке 833Д сплавом ВТ20Л. Для того чтобы все блоки находились в одинаковых условиях, они были помещены в один контейнер. Заливка собранного контейнера проходила без отклонений от серийной технологии. Формы, изготовленные по разработанным технологиям, залились без разрушения. Визуально отливки, залитые в экспериментальные оболочковые формы после отделения керамики, не имели отличий от отливок, залитых в оболочковые формы, изготовленные по серийной технологии.
Оболочковая форма, связующие на водной основе, крупногабаритные отливки, центробежная заливка, альфированный слой, огнеупорная суспензия
Короткий адрес: https://sciup.org/147156933
IDR: 147156933
Текст научной статьи Разработка ресурсосберегающей технологии получения крупногабаритных отливок из титановых сплавов
Тенденция развития современного производства направлена на повышение качества, точности и эксплуатационной надежности литых изделий, получаемых методом литья по выплавляемым моделям. В авиастроении при изготовлении крупногабаритных отливок из титановых сплавов широкое распространение получили электрокорундовые формы.
Однако при использовании данной технологии на поверхности отливок образуется насыщенный примесями и отрицательно влияющий на характеристики изделия поверхностный альфиро-ванный слой, который необходимо удалять, особенно с деталей, работающих в условиях долговременных знакопеременных нагрузок и вибраций.
Целью работы является разработка ресурсосберегающей технологии получения крупногабаритных отливок из титановых сплавов деталей авиационного назначения центробежной заливкой в оболочковые формы с использованием связующих на водной основе.
В ходе ранее выполненной работы были проведены исследования различных связующих на водной основе: EHT Binder (США), Remаsol (Великобритания), Армосил разных модификаций (Россия, г. Казань).
На основе анализа проведенных исследований [1, 2] было установлено, что для достижения наилучших механических свойств необходимо соблюдать следующие условия:
-
1) прокаливание оболочковых керамических форм (для всех видов водных связующих) необходимо проводить при температуре ≥ 1200 °С;
-
2) для увеличения изгибной прочности форм необходимо в суспензию вводить 5 % (от массы наполнителя) алюминиевого порошка АСД-4 ТУ 1791-007-49421776-2011.
Исследования показали, что на образцах, изготовленных с использованием связующих EHT Binder, Армосил АМ, Армосил А, Армосил Ti, величина альфированного слоя на отливках сопоставима с величиной этого слоя на отливках полу- ченных в формах изготовленных на этилсиликатном связующем. При изготовлении оболочковых форм с использованием связующего Remasol, как с добавлением АСД, так и без АСД, на титановых отливках альфированный слой отсутствует.
По результатам механических испытаний и исследований альфированного слоя разработана технология изготовления оболочковых форм для литья крупногабаритных отливок. Предложено использовать в качестве связующего для изготовления оболочковых форм, связующее Remasol с добавлением в суспензию АСД-4 в количестве 5 %.
Для проверки рекомендованных связующих материалов в реальных условиях, по разработанной технологии были изготовлены керамические оболочковые формы отливок деталей и залиты совместно с формами, изготовленными по серийной технологии.
Для апробации разработанной технологии на основе связующего Remasol в условиях серийного производства отливок деталей были изготовлены три модельных блока (рис. 1).
Первый блок был облицован с использованием связующего на основе гидролизованного этил-силиката по технологии цеха титанового литья ОАО «УМПО».
Второй блок облицовывали с использованием связующего на водной основе Remasol, по технологии литья по выплавляемым моделям. Окунанием модельного блока в суспензию с условной по вискозиметру В3-4 вязкостью 65–70 с на первых двух слоях и обсыпкой электрокорундом зернистостью М20; на последующих слоях – вязкостью 30–35 с с обсыпкой электрокорундом зернистостью М50. Сушка производилась на воздухе в течение 4 ч для первых двух слоев и 2 ч для последующих слоев. Облицованный блок приведен на рис. 2.
С целью возможности устранения альфиро-ванного слоя в условиях технологии серийного производства было предложено изготовить третий блок по следующей схеме:
-
– первые два слоя оболочковой формы были изготовлены на связующем Remasol по технологии второго блока;
– последующие слои оболочковой формы были изготовлены со связующим на основе гидролизованного этилсиликата по серийной технологии цеха титанового литья ОАО «УМПО».
Вытопка блоков производилась в расплаве модельной массы ЗГВ-101, нагретой до температуры (170±5) °С.
Прокаливание блоков производили в шахтной печи при температуре 1000 °С в течение 6 ч.
Заливка блоков производилась в вакуумной электродуговой плавильно-заливочной установке 833Д сплавом ВТ20Л. Для того чтобы все три блока находились в одинаковых условиях, они были помещены в один контейнер (рис. 3).
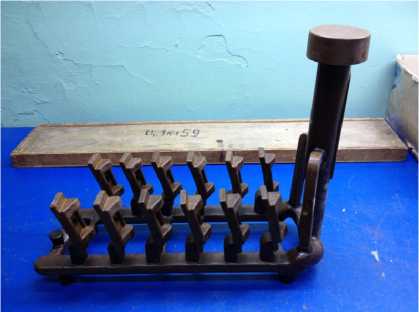
Рис. 1. Блок модельный
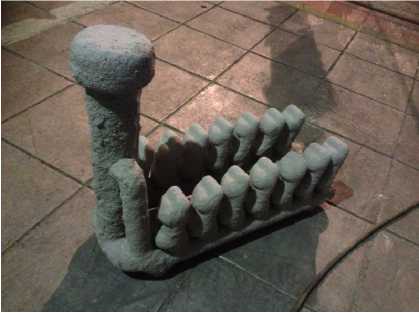
Рис. 2. Блок облицованный
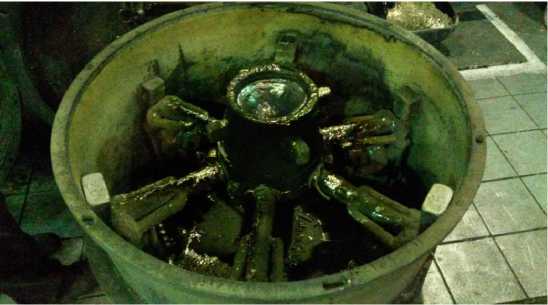
Рис. 3. Контейнер с залитыми блоками
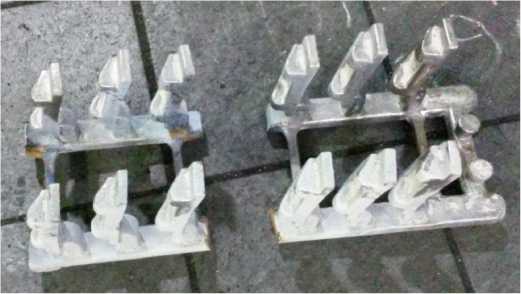
Рис. 4. Блок отливок после отбивки керамики

Рис. 5. Отливка после отрезки от литниково-питающей системы
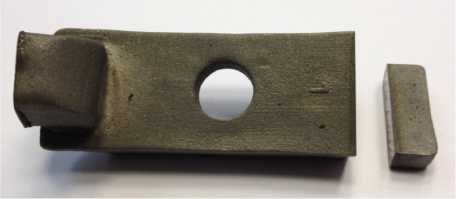
Рис. 6. Отрезанный образец для исследования альфированного слоя
Заливка собранного контейнера проходила без отклонений от серийной технологии. Формы, изготовленные по разработанным технологиям, залились без разрушения. Отливки, залитые в экспериментальные оболочковые формы после отделения керамики, не имели визуальных отличий от отливок, залитых в оболочковые формы, изготовленные по серийной технологии.
После отбивки керамики с каждого блока (рис. 4) отрезалось по одной отливке (рис. 5) и проводились исследования на наличие альфиро-ванного слоя.
Методика подготовки и исследования альфи-рованного слоя заключалась в следующем.
Образцы вырезались из отливки (рис. 6), в дальнейшем шлифовались до зеркального состояния поверхности. После образец протравливался смесью кислот следующего состава:
-
– 1 часть плавиковой кислоты;
-
– 1 часть азотной кислоты;
-
– 3 части дистиллированной воды.
Микроструктуру образцов исследовали на инвертированном оптическом микроскопе Olympus GX51.
На просматриваемых микроструктурах отмечено изменение структуры по границам образца («игольчатые» зерна) и определена глубина проникновения в тело отливки.
Микроструктура полученных образцов из деталей залитых блоков приведена на рис. 7–9.
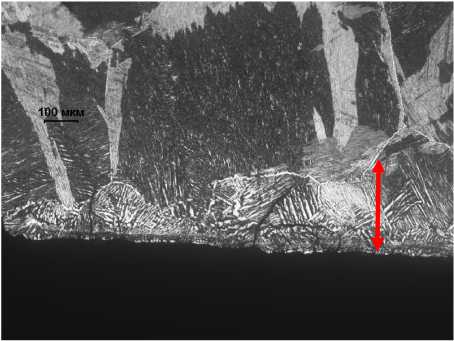
Рис. 7. Микроструктура образца отливки из блока, изготовленного со связующим на основе гидролизованного этилсиликата
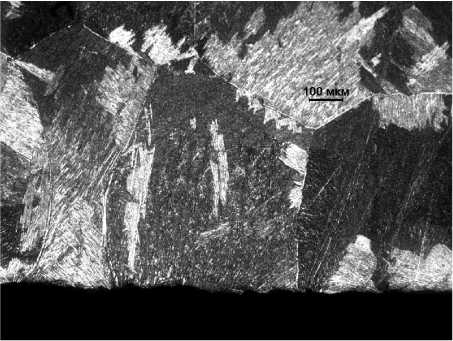
Рис. 8. Микроструктура образца отливки из блока, изготовленного со связующим Remasol
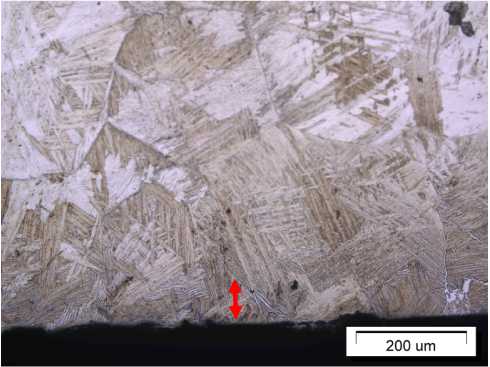
Рис. 9. Микроструктура образца отливки из блока, изготовленного комбинированным способом
Результаты измерений альфированного слоя
Связующее оболочковой формы |
Величина альфированного слоя, мкм |
Гидролизованный этилсиликат |
275 |
Remasol |
— |
Комбинированная форма |
76 |
Результаты измерений величины альфирован-ного слоя на основе различных связующих и результаты анализа металлографических исследований отливок, полученных в оболочковых формах на основе гидролизованного этилсиликата и связующего Remasol, приведены в таблице.
Из таблицы следует:
-
– на отливках, полученных в оболочковой форме на основе гидролизованного этилсиликата (см. рис. 7), наблюдается альфированный слой размером 275 мкм;
– на отливках, полученных в оболочковой форме на основе связующего Remasol (см. рис. 8), альфированный слой отсутствует, а в комбинированной форме (см. рис. 9), альфированный слой покрывает лишь часть поверхности образца (не более 30 % площади) и максимальная толщина его составляет 76 мкм.
Выводы
-
1. Разработана технология получения оболочковых форм на основе водного связующего Remasol с добавлением в огнеупорную суспензию 5 % АСД для центробежного литья титановых сплавов без альфированного слоя на поверхности отливок.
-
2. С целью импортозамещения проведены дополнительные исследования по использованию отечественного водного связующего Армосил АМ, позволившие предложить технологию получения оболочковых форм с добавлением в огнеупорную суспензию 5 % АСД для центробежного литья титановых сплавов.
-
3. Приведены исследования по использованию комбинированных оболочковых форм для центробежного литья – первые два слоя с использованием водного связующего Remasol, последующие слои на основе гидролизованного этил-силиката, позволившие уменьшить альфирован-ный слой титановых отливок и снизить их себестоимость.
-
4. Разработана ресурсосберегающая технология получения крупногабаритных отливок из титановых сплавов деталей авиационного назначения центробежной заливкой в оболочковые формы с использованием связующих на водной основе.
Проект выполнялся при поддержке Министерства образования и науки РФ. Договор от 12 февраля 2013 г. № 02.G25.31.0009.
Список литературы Разработка ресурсосберегающей технологии получения крупногабаритных отливок из титановых сплавов
- Исследовательские испытания технологического процесса производства крупногабаритных тонкостенных литых заготовок из титановых сплавов в части изготовления керамических литейных форм (корпус разделительный): отчет о НИР (промежуточ.): 27-13/ФГБОУ ВПО УГАТУ; рук. С.В. Бакерин; исполн.: А.А. Ганеев . -Уфа, 2014. -119 с.
- Углев, Н.П. Термомеханические свойства керамик для литья по выплавляемым моделям/Н.П. Углев, В.З. Пойлов, А.Л. Казанцев//Литейное производство. -2014. -№ 5. -С. 19-20.