Разработка технологии производства проволоки из специальных алюминиевых сплавов на основе способа литья в электромагнитный кристаллизатор и непрерывного прессования способом конформ
Автор: Авдулов А.А., Сергеев Н.В., Гудков И.С., Тимофеев В.Н., Горохов Ю.В., Авдулова Ю.С.
Журнал: Журнал Сибирского федерального университета. Серия: Техника и технологии @technologies-sfu
Статья в выпуске: 1 т.10, 2017 года.
Бесплатный доступ
Изложены перспективы использования специальных алюминиевых сплавов для производства бортовых проводов летательных аппаратов. Приведено описание плавильно-литейного комплекса с электромагнитным кристаллизатором для производства непрерывнолитых слитков малого сечения. Представлены преимущества электромагнитного литья, структуры и механические свойства слитков и проволоки из сплава 01417м. Предложена технологическая схема производства проволоки, включающая в себя литье непрерывной заготовки в электромагнитный кристаллизатор и ее последующую пластическую деформацию способом конформ. Приведены преимущества данной схемы и перспективы ее внедрения в промышленности.
Алюминиевые сплавы, бортовые провода, электромагнитный кристаллизатор, непрерывное прессование, конформ
Короткий адрес: https://sciup.org/146115184
IDR: 146115184 | DOI: 10.17516/1999-494X-2017-10-1-85-94
Текст научной статьи Разработка технологии производства проволоки из специальных алюминиевых сплавов на основе способа литья в электромагнитный кристаллизатор и непрерывного прессования способом конформ
дополнительно снизить вес БКС на 500 кг. Для сравнения: это больше половины экономии веса, полученного за счет изготовления из углеволокна центроплана (Central Torsion Box), на разработку которого были потрачены миллионы евро. В дальнейшем AIRBUS планирует использовать данное решение на A400M и A350XWB. Всего в А380 в 300 из 500 км проводов и кабелей используют алюминий вместо обычной меди в качестве электрического проводника, что позволило снизить вес БКС на 20 %. При этом в качестве проводниковой жилы приходится применять аналог отечественного сплава АМГ1, имеющего допустимую рабочую температуру только до 180 °С и существенно большее сопротивление по сравнению с чистым алюминием.
С 2005 г. в ходе реализации программы по импортозамещению АО «Особое конструкторское бюро кабельной промышленности» (ОКБ КП – головное предприятие в РФ, занимающееся разработкой и производством бортовых проводов) проводит ОКР по созданию серии облегченных кабельных изделий для авиационной техники с использованием новых отечественных изоляционных и проводниковых материалов. В настоящее время в АО «ОКБ КП» разработаны бортовые провода с токопроводящими жилами из алюминиевого сплава и комбинированной изоляции марок [1]:
-
- БК-36-448 и БКЭ-36-448 по ТУ 16.К76-236-2009 сечением от 4 до 95 мм2 с никелевым покрытием, рабочей температурой 200 °С;
-
- БФС-А и БФСЭ-А теплостойкие по ТУ 16-705.405-85 сечением от 4 до 95 мм2 без покрытия, рабочей температурой 250 °С.
Более высокая максимальная рабочая температура отечественных проводов по сравнению с зарубежными достигается за счет использования жилы из сплава алюминия с редкоземельными металлами 01417 [2, 3]. При освоении производства проволоки из сплава 01417 существующими технологиями было обнаружено, что из-за крупнозернистой и неоднородной микроструктуры производство проволоки малых диаметров экономически нецелесообразно (высокая обрывность при волочении).
Получение непрерывно-литой заготовки способом литья в электромагнитный кристаллизатор
Для решения проблемы получения качественной проволоки из сплава 01417 специалистами ООО «НПЦ Магнитной гидродинамики» совместно с сотрудниками Сибирского федерального унивеститета и ООО «АвиаСпецСплав» была разработана уникальная технология литья в электромагнитный кристаллизатор (ЭМК), которая позволяет получить проволоку из жаропрочных алюминиевых сплавов со структурой, сопоставимой со структурой гранул (порошковая металлургия). В отличие от работ З.Н. Гецелева [4] в электромагнитный кристаллизатор производится отливка слитков малого сечения (диаметр менее 20 мм). Сплав 01417 был доработан для возможности литья в электромагнитный и получил обозначение 01417м. При этом технология обеспечивает существенно более высокую производительность, низкую себестоимость, требуемые технические характеристики и высокое качество выпускаемой продукции.
В ООО «НПЦ Магнитной гидродинамики» создан опытно-промышленный литейный комплекс с электромагнитным кристаллизатором производительностью до 20 т в год непрерывнолитой заготовки диаметрам 8 мм (рис. 1). По тематике работы защищены три докторских – 87 – и пять кандидатских диссертаций. На опытно-промышленной установке получены слитки из сплава 01417м, обладающие высокими механическими и электрическими свойствами, сохраняющимися до температуры 250 °С. В партнёрстве с ОКБ КП и НПЦ «АвиаСпецСплав» из полученных слитков изготовлены провода для БКС самолетов-амфибий Бе-200, что позволило снизить вес машины на 1 т. Разработана технология волочения литой заготовки до диаметра 0,5 мм.
Суть технологии заключается в кристаллизации алюминиевого расплава в высокочастотном электромагнитном поле с непосредственной подачей охлаждающей воды на слиток. Вследствие этого происходит бесконтактное формирование слитка диаметром 8-12 мм со скоростью охлаждения свыше 1000 K/c и интенсивным магнитогидродинамическим воздействием на границе раздела фаз, что обеспечивает получение дисперсной структуры [5, 6].
На рис. 2 представлена принципиальная схема работы комплекса. В плавильной печи (1) осуществляется приготовление алюминиевого сплава, однородность по химическому составу и температуре обеспечивается путем использования электромагнитного перемешивателя (2). Расплав из плавильной печи (1) поступает в дозирующий лоток (3), где поддерживается заданная температура и уровень расплава. Через подающий носик лотка расплав продвигается в индуктор электромагнитного кристаллизатора (4), в котором геометрия слитка бесконтактно формируется высокочастотным электромагнитным полем. Охлаждающая жидкость из охладителя (5) непосредственно подается на заготовку, что обеспечивает высокую скорость охлаждения и позволяет получить непрерывно-литую заготовку (6). Заготовка далее с помощью отводного механизма выводится из кристаллизатора и наматывается в бухту.
Преимущества непрерывно-литых заготовок, полученных по технологии литья в электромагнитный кристаллизатор:
-
– слиток, полученный по технологии литья в электромагнитный кристаллизатор, имеет дендритный параметр в 100 раз меньше, чем в кристаллизаторе скольжения, и сопоставим со структурой гранул (рис. 3);
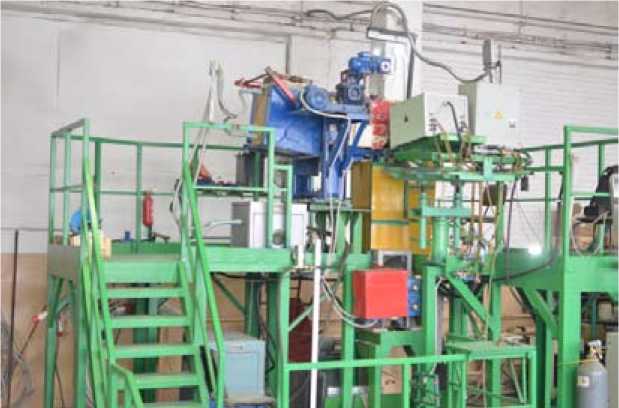
Рис. 1. Плавильно-литейный комплекс с электромагнитным кристаллизатором
– в слитках практически отсутствует дендритная ликвация;
– благодаря высокой скорости кристаллизации происходит расширение концентрационных областей твердых растворов, сдвиг эвтектических и перитектических точек, что
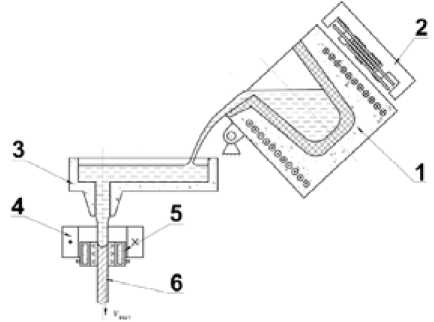
Рис. 2. Принципиальная схема комплекса с ЭМК
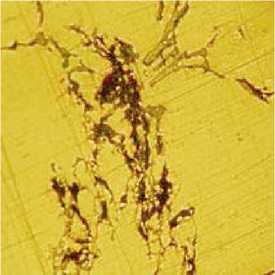
а
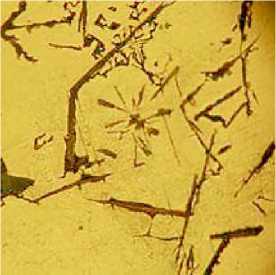
б
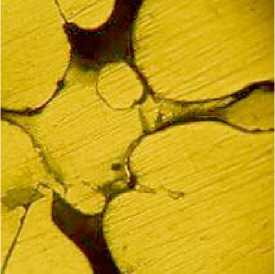
в
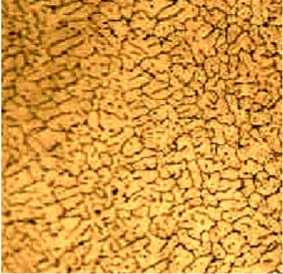
г
Рис. 3. Состояние сложнолегированного сплава: а – перед литьем, окисные плены; б – перед литьем, грубые первичные интерметаллиды; в – междендридная пористость; г – после литья в ЭМК, квазиэвтек-тическая структура без первичных интерметаллидов и оксидов позволяет обеспечить разработку новых сплавов и получение более высоких прочностных свойств в существующих сплавах;
-
- электромагнитное литье в отличие от гранульной технологии дает возможность получать изделия, уже готовые к дальнейшей переработке (нет необходимости производить обработку гранул, их спекание и т.д.);
-
– дальнейшая пластическая деформация заготовок приводит к образованию нанодис-персной эвтектики, что позволяет изготовить проволоку из специальных алюминиевых сплавов диаметром до 0,10 мм;
-
- уникальным свойством электромагнитного литья является отсутствие в изделиях неметаллических включений, что обеспечивает получение продукции высокого качества (рис. 3).
Микроструктура литых заготовок из сплава 01417м однородна, дисперсна по всему сечению, в ней отсутствуют первичные интерметаллиды (рис 4). Микроструктура представляет собой α-твердый раствор, по границам дендритных ячеек которого располагается дисперсная эвтектика (a+AlnMe). Наименьший размер дендритной ячейки составил 4,1 мкм. Такая микроструктура свойственна сплавам Al-РЗМ, полученным с высокими скоростями охлаждения расплава (до 10 3 °С/с). Уровень прочностных свойств заготовок аналогичен свойствам горячепрессованных прутков из гранул сплава 01417м, причем отпрессованных с высоким коэффициентом вытяжки (µ=55). Физико-механические свойства литой заготовки и проволоки из сплава 01417м приведены в табл. 1.
Совмещение литья в ЭМК и непрерывного прессования в общей технологической цепи производства проволоки
При массовом выпуске продукции процесс непрерывного литья на плавильно-литейном комплексе с электромагнитным кристаллизатором может длиться от 6 до 9 ч, а в перспективе – до нескольких суток. Это обеспечивает производство цельных бухт непрерывнолитых заготовок. Цельная бухта большой массы (свыше 80 кг) более предпочтительна, так как при волочении сокращается количество технологических операций (зачистка, стыковка, сварка и т.п.). Поскольку формообразование слитка происходит в электромагнитном поле, то небольшие изменения технологических параметров могут привести к появлению дефектов литья (рис. 5 б, в, г ). При дальнейшей переработке слитка в проволоку путем во-
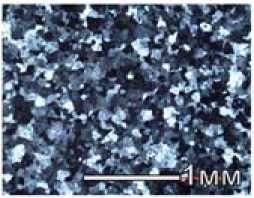
а
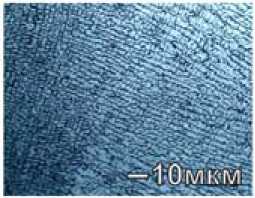
б
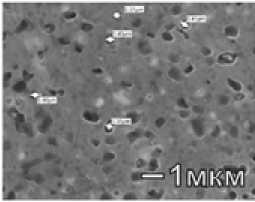
в
Рис. 4. Структуры изделий из сплава 01417м: а – макроструктура литой заготовки диаметром 8 мм; б – микроструктура литой заготовки диаметром 8 мм; в – микроструктура проволоки диаметром 0,5 мм
Таблица 1. Механические свойства прутков литой заготовки и проволоки из сплава 01417м
В настоящий момент стоит задача повышения качества выпускаемой продукции – стабилизации диаметра слитка, что позволит повысить технологичность переработки изделий в проволоку и начать массовое внедрение алюминиевых проводов в авиакосмической отрасли. Для этого предлагается перед отправкой литых слитков на волочильный завод производить их калибровку с последующей непрерывной экструзией способом конформ [7, 8], что даст возможность поставлять потребителю продукт более глубокой переработки – калиброванную проволоку диаметрам до 5 мм. При этом данный способ позволит перевести мелкодисперсную эвтектику (1-3 мкм) в литом слитке в нанодисперсное состояние (менее 100 нм), что, по заверению специалистов-металловедов, даст возможность получить при дальнейшем волочении проволоку диаметром до 0,1 мм.
Предлагаемая технологическая схема представлена на рис. 6. На первом этапе производится приготовление, очистка и литье сплава в электромагнитный кристаллизатор. В результате литья производится слиток диаметром 10-12 мм в бухте. Далее слиток подвергается калибровке в диаметр 10 мм. На последнем этапе переработки слиток поступает для непрерывного прессования способом конформ в проволоку диаметром 5 мм.
Для создания предложенной технологической схемы был разработан проект опытнопромышленной установки для калибровки слитка и непрерывной экструзии проволоки. Установка выполнена по модульному принципу и состоит из общей силовой рамы с мотор-редуктором и сменных модулей: модуля калибровочной клети (модуль Прокатка, рис. 7 а ) и модуля непрерывной экструзии (модуль Конформ, рис. 7б ).
В состав установки входит разматывающее устройство для подачи исходного и калиброванного слитков в рабочие модули. Наматывающее устройство имеет собственный мотор-редуктор и механический укладчик проволоки, что обеспечивает плотную укладку проволоки в бухты с внутренним диаметром 650 мм. Полученные бухты после связки и маркировки являются товарной продукцией, готовой к отправке на волочильный завод.
Алюминиевый сплав в чушке
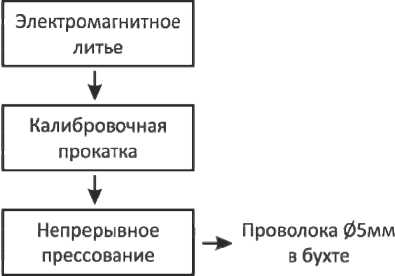
Рис. 6. Перспективная технологическая схема производства проволоки
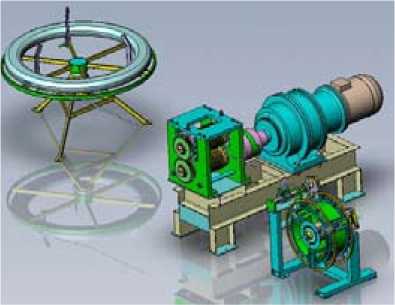
Рис. 7. Опытно-промышленная установка для калибровки слитка и непрерывной экструзии проволоки: а – с модулем конформ; б – с модулем прокатки
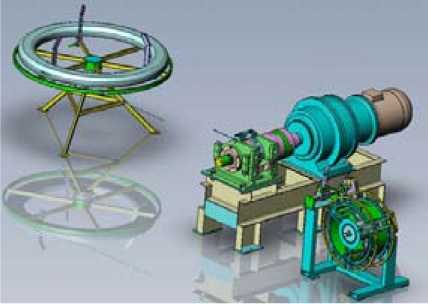
б
Заключение
Технологическая линия, включающая в свой состав комплекс для литья в электромагнитный кристаллизатор непрерывно-литых слитков малого сечения и установку для непрерывного прессования способом конформ, должна обеспечить производство высококачественной проволоки с дисперсной структурой и стабильными физико-механическими свойствами. Это даст возможность начать широкое внедрение в промышленности стандартных и специальных алюминиевых сплавов с мелкодисперсной структурой.
Работы по разработке технологии переработки литой заготовки в проволоку путем прокатки и непрерывного прессования выполнены в рамках проекта «Разработка технологии производства проволоки из специальных алюминиевых сплавов для нужд авиакосмической промышленности». Проект поддержан Правительством Красноярского края и КГАУ «Красноярский краевой фонд поддержки научной и научно-технической деятельности» по конкурсу научно-технических проектов, направленных на кооперацию учреждений и организаций научно-образовательного комплекса Красноярского края по заказу промышленных предприятий в 2016 г.
Исследование выполнено при финансовой поддержке Российского фонда фундаментальных исследований, Правительства Красноярского края, Красноярского краевого фонда поддержки научной и научно-технической деятельности в рамках научных проектов № 16-48-242018 и № 16-43-242013 р_офи_м.
Список литературы Разработка технологии производства проволоки из специальных алюминиевых сплавов на основе способа литья в электромагнитный кристаллизатор и непрерывного прессования способом конформ
- ОКБ КП . URL: http://www.okbkp.ru/(дата обращения: 01.09.2016).
- Добаткин В.И., Елагин В.И. Гранулируемые алюминиевые сплавы. М.: Металлургия, 1983, 176 с.
- Добаткин В.И., Елагин В.И. Быстрозакристаллизованные алюминиевые сплавы. М.: ВИЛС, 1995, 341 с.
- Гецелев З.Н. и др. Непрерывное литье в электромагнитный кристаллизатор. М.: Металлургия, 1983. 152 с.
- Первухин М.В. Электротехнология и оборудование для получения непрерывнолитых слитков в электромагнитном кристаллизаторе. Теория и практика: автореф. дис. … д-ра техн. наук: 05.09.10. Красноярск, 2012. 36 с.
- Бааке Э. и др. МГД-технологии в металлургии. Интенсивный курс Специализация IV. Спб.: Изд-во СПбГЭТУ «ЛЭТИ», 2013. 250с.
- Сидельников С.Б., Горохов Ю.В., Беляев С.В. Инновационные совмещенные технологии при обработке металлов. Журнал Сибирского федерального университета. Техника и технологии, 2015, 8(2), 185-191
- Горохов Ю.В., Шеркунов В.Г., Довженко Н.Н., Беляев С.В., Довженко И.Н. Основы проектирования процессов непрерывного прессования металлов. Красноярск: СФУ, 2013