Развитие технологии многодуговой сварки трубных сталей
Автор: Уланов Алексей Михайлович, Иванов Михаил Александрович
Журнал: Вестник Южно-Уральского государственного университета. Серия: Металлургия @vestnik-susu-metallurgy
Рубрика: Краткие сообщения
Статья в выпуске: 39 (298), 2012 года.
Бесплатный доступ
Рассмотрен хронологический процесс развития трубных сталей как в России, так и за рубежом, а вместе с ним становление и совершенствование сварочных технологий. Проведен анализ литературных источников по данному направлению.
Сварка под флюсом, технология сварки, многодуговая сварка, трубная сталь
Короткий адрес: https://sciup.org/147156749
IDR: 147156749
Текст краткого сообщения Развитие технологии многодуговой сварки трубных сталей
Бурное развитие сварочной техники в Советском Союзе началось в 30-x гг. прошлого века и продолжается сейчас в России непрерывными темпами. Россия, бесспорно, занимает одно из ведущих мест по объему применений и техническому совершенству сварки. В середине XX в. многодуговая сварка была развита и усовершенствована советскими инженерами и учеными и имела широкое применение при индустриализации Советского Союза, особенно в машиностроении и в строительстве.
Многодуговая сварка под флюсом в ее совершенном виде была широко разработана в теоретическом и практическом плане Е.О. Патоном и руководимым им коллективом Института электросварки Академии наук УССР, а также сотрудни- ками ЦНИИТМАШ, завода «Электрик» и ряда других институтов и передовых заводов.
Хронологию развития отечественных и зарубежных трубных сталей хорошо демонстрируют схемы, представленные на рис. 1. Концепция разработки трубных сталей предусматривает снижение содержание углерода; повышение чистоты металла по вредным примесям ( S ≤ 0,001 %, P ≤ 0,010); рациональное микролегирование; термомеханическую прокатку [1, 2]; снижение дефектности сварных швов [3]; повышение стойкости сварных труб против лавинных разрушений [4]; снижение остаточных сварочных напряжений [5].
Трубы класса прочности Х70 за рубежом применялись с 1970-х гг. во многих проектах и показали хорошие эксплуатационные свойства.
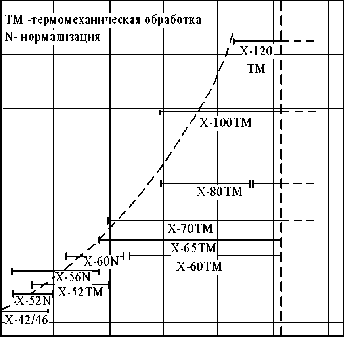
1950 1960 1970 1980 1» 2000 2010 Г@ды
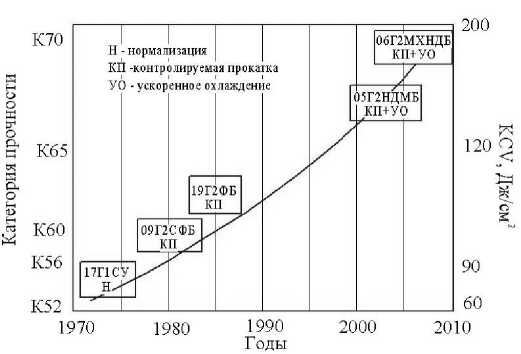
б)
Рис. 1. Разработка высокопрочных трубных сталей за рубежом (а), в России (б) [1, 2]
а)
Уланов А.М., Иванов М.А.
В России им примерно соответствуют стали класса прочности К60. Дальнейшим развитием является разработка труб класса прочности Х80, которые впервые были использованы за рубежом в середине 80-х гг. ХХ в. для строительства опытных участков трубопроводов. В середине 90-х гг. ХХ в. за рубежом были разработаны и началось апробирование труб класса прочности Х100 для строительства трубопроводов. В последнее десятилетие выдвинуты требования по повышению прочности труб до Х120.
В России в рамках проекта «Магистраль» разработаны трубные стали класса прочности Х80– Х100 марганцевой композиции легирования с небольшими добавками никеля, меди и молибдена, микролегирования титаном, ванадием и ниобием [6–9], отвечающие всем требованиям зарубежной нормативно-технической документации.
В целях улучшения свариваемости трубные стали класса прочности Х80–Х90 содержат менее 0,10 % углерода; 1,7–1,9 % марганца; до 0,5 % меди, молибдена и никеля; не более 0,12 % микролегирующих элементов, таких как ванадий, ниобий, титан.
Мощная закрытая флюсом дуга глубоко расплавляет основной металл, позволяет уменьшить разделку кромок под сварку, а также снижается доля участия электродного металла в образовании шва: в среднем наплавленный металл образуется на 2/3 за счет расплавления основного металла и лишь на 1/3 за счет электродного [10].
В России в 80-е гг. Челябинский трубопрокатный завод занимался исследованием трехдуговой сварки пластин из стали 17Г1С размерами 600 х 400 х 15,2 мм [11]. Применялась проволока СВ-08ГА диаметром 4 мм и флюс АН-60. Ток на трех дугах – соответственно 1300, 1200 и 1100 А; охлаждение водяное.
На Украине, в Академии наук [12] проводили исследования влияния термического цикла однодуговой и двухдуговой сварки в СО 2 на стойкость высоколегированной стали против образования холодных трещин.
Установлено, что термический цикл сварки существенно влияет на стойкость закаливающихся сталей против образования холодных трещин. При замедленном охлаждении сварных соединений в области температур превращения аустенита вероятность образования холодных трещин в зоне термического влияния значительно снижается. Было отмечено, что двухдуговая сварка в СО 2 обеспечивает благоприятную структуру сварного соединения при сварке стали 20ХГСНМ проволокой СВ-08ГСМТ при расстоянии между дугами 100 мм.
С целью увеличения скорости сварки продольных швов применяется многодуговая сварка под флюсом с использованием до пяти электродов. Это достигается комбинацией в сварочной ванне более одного электрода, что дает увеличение производительности по сравнению с однодуговой сваркой до пяти раз [13].
Ключевым свойством многодуговой сварки является получение швов без пористости и подрезов, с возможностью контроля формы шва при высокой силе сварочного тока и скорости сварки [14]. При этом используется комбинация с источником постоянного тока на первой дуге (DC) и переменного тока на остальных (AC) – комбинации DC–AC–AC–AC–AC, DC–AC–AC–AC. Подключение к ведущему электроду источника постоянного тока позволяет добиться увеличения проплавления при прочих равных условиях по сравнению с источником переменного тока. Также благодаря использованию данной комбинации источников происходит снижение погонной энергии для одной и той же толщины стенки, что становится особенно заметно при больших толщинах (рис. 2, а) [15].
Увеличение количества дуг позволяет снизить погонную энергию, что видно из рис. 2, б, на котором сравнивается сварка тремя и четырьмя электродами [15].
Таким образом, эволюционное увеличение количества дуг при многодуговой сварке оправда-
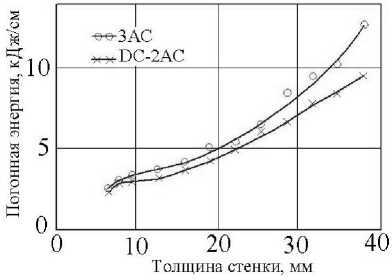
а)
Рис. 2. Влияние источника постоянного тока на погонную энергию [15] (а); погонная энергия при трех- и четырехдуговой сварке [15] (б)

Толщина стенки, мм
б)
но повышением производительности труда, скорости сварки, улучшением качества сварного шва.
Список литературы Развитие технологии многодуговой сварки трубных сталей
- Gray M. Niobium bearing steels in pipeline projects/M. Gray//Niobium science and technology: Proc. Int. Symposium on Niobium, Orlando, Florida, Dec. 2-5, 2001. -P. 23-45.
- Морозов Ю.Д. Стали для труб магистральных трубопроводов: состояние и тенденции развития/Ю.Д. Морозов, Л. И. Эфрон//Металлург. -2006. -№ 5. -С. 11-15.
- Пашков, Ю.И. Разработка классификатора дефектов для сварных труб/Ю.И. Пашков, B.А. Лупин, М.А. Иванов//Вестник ЮУрГУ. Серия «Металлургия». -2012. -Вып. 18. -№ 15 (274). -C. 37-40.
- Лупин В. А. Проблемы лавинных разрушений газопроводов из сварных труб и способы их предотвращения/В.А. Лупин, Ю.И. Пашков, М.А. Иванов//Вестник ЮУрГУ. Серия «Металлургия». -2012. -Вып. 18. -№ 15 (274). -С. 26-27.
- Пашков Ю.И. Остаточные сварочные напряжения и пути снижении стресс-коррозионных разрушений магистральных газопроводов/Ю. И. Пашков, М. А. Иванов, Р. Г. Губайдулин//Вестник ЮУрГУ. Серия «Металлургия». -2012. -Вып. 18. -№ 15 (274). -С. 28-30.
- Освоение производства штрипса К70 для труб большого диаметра на стане 5000/А.А. Немтинов, А.М. Корчагин, А.Г. Попков и др.//Металлург. -2008. -№ 11. -С. 61-67.
- Структура и свойства штрипса для труб большого диаметра из стали категории прочности Х80-Х100/Ю.Д. Морозов, А.М. Корчагин, В.В. Орлов и др.//Металлург. -2009. -№ 3. -С. 57-65.
- Исследование сопротивления деформированию и разрушению металла штрипса и труб категории прочности Х80, изготовленного методом ТМО/О.П. Виноградов, А.В. Ильин, В.В. Орлов и др.//Металлург. -2009. -№ 4. -С. 53-57.
- Ердаков И.Н. Ресурсосберегающий аспект в производстве литых плит из стали Гадфильда/И.Н. Ердаков//Заготовительные производства в машиностроении. -2011. -№ 11. -С. 3-5.
- Серенко А.Н. Температурные поля при многодуговой сварке с программированием режима/А.Н. Серенко, В.А. Шаферовский//Сварочное производство. -1922. -№ 7. -С. 23-24.
- Рудаков А. С. Длина ванны при многодуговой сварке под флюсом/А.С. Рудаков, А.К. Танчук//Вопросы сварочного производства. -Челябинск: ЧПИ. -1975. -№ 168. -С. 177-181.
- Влияние термического цикла двухдуговой сварки в СО2 на стойкость 20ХГСНМ против образования холодных трещин/С.Н. Гончаров, Н.З. Гуднев, Ю.А. Стеренбоген и др.//Автоматическая сварка -1982 -№ 7. -С. 14-15.
- Uttrachi G.D. Multiple electrode systems for submerged arc welding/G.D. Uttrachi//Welding journal. -1978. -May. -P. 15-22.
- Мельник С. С. Многодуговая автоматическая сварка стальных корпусных конструкций под слоем флюса АН-66/С.С. Мельник, Н.Д. Ксенз, В.В. Кухаренко//Сварочное производство. -1984. -№ 8. -С. 37-38.
- Four-wire submerged arc welding process with DC-AC power combination for production of high toughness line pipe/Z. Baba, M. Nagashima, M. Nakanishi et al.//Transactions ISIJ. -1986. -Vol. 26. -P. 373-378. Поступила в редакцию 7 сентября 2012 г