Research of properties deformed semi-finished products from aluminum-zirconium alloys, obtained with using combined methods of casting and metal forming
Автор: Bespalov Vadim M., Sidelnikov Sergey B., Sidelnikov Andrei S.
Журнал: Журнал Сибирского федерального университета. Серия: Техника и технологии @technologies-sfu
Статья в выпуске: 8 т.7, 2014 года.
Бесплатный доступ
This article represent the results of research of mechanical and electrical properties of deformed semi-fifnished products from alloys system Al-Zr, obtained with using methods of combined casting-rolling, combined casting and rolling-extruding and drawing.
Combined processes, casting, rolling, extruding, drawing, electrical wire, mechanical and electrophysical properties
Короткий адрес: https://sciup.org/146114914
IDR: 146114914
Текст научной статьи Research of properties deformed semi-finished products from aluminum-zirconium alloys, obtained with using combined methods of casting and metal forming
Development and application of methods combined casting and rolling, and casting and rollingextrusion for obtaining deformed semi-finished products from high-strength aluminum alloys as a wire rod, bars and wire is currently one of the most promising areas of research. Their results will enable used in the future such semi-finished products for the manufacture of power wires for power transmission lines, having not only high strength but also heat resistance.
According to State Standard №13843-78 aluminum wire rod from alloys of technical aluminum marks А5Е and А7Е diameter 9,5 mm obtained on casting-rolling aggregates (CRA) must have a tensile strength σ В about 80-110 MPa and electrical resistivity 0,0282 Ohm∙mm2/m (1,7 times more than electrical resistivity of copper). Working temperature of rolled wire is 90 °C. The lack of electrical conductivity compared to copper wires can be offset by an increase of conductor size, but such strength and heat resistance is not enough to ensure reliable operation of the lines, excluding precipices. In this regard, recent studies aimed at finding ways to strengthening and improving the thermal stability of aluminum wire rod.
One of perspective directions is the study of alloys system Al-Zr. Based on the review of the scientific literature, presence of zirconium in aluminum alloy: significantly increases the strength of the alloy; prevents grain growth at elevated temperatures; improves weldability; prevents grain growth in areas near the weld; reduces susceptibility to corrosion under voltage; reduces the sensitivity to the cooling rate during hardening.
This paper shows a comparison the results of the mechanical characteristics and electrical resistivity of wire rod obtained by the classical method (CRA) at «IrkAF» JSC and rods obtained by method combined casting and rolling-extruding in laboratory conditions of FSAEI HPE «Siberian federal university» [1] from aluminum alloys with a similar chemical composition containing up to 0,15 % of zirconium [2].
Rods were obtained on experimental installation which working unit includes rolls diameter 200 mm; they form a closed caliber with dimensions 14×14 mm. At the exit of the rolls using hydraulic cylinder is preloaded matrix with caliber hole 9 mm.
Experiments were conducted using two technologies, in the first case used combined rollingextruding (CRE) of rod from billet cast in a mold with size 14×14 mm and in electromagnetic crystallizer diameter 15 mm (process EMC+CRE). In this case, billet heated to a temperature 550 °C, moved to the caliber of rolls, rolled up to the surface of the matrix and extruded through matrix to obtain rod diameter 9 mm.
In the second case was performed combined casting and rolling-extruding (CCRE). During the experiment the melt poured into the caliber of rotating rolls consistently crystallized, compressing by them and came out of the matrix in the form of rod specified size. Temperature of the melt at pouring was 750 °C according to conditions for obtaining factory wire rod presented in the work [3].
To estimate technological properties of rods and wire rods conducted cold drawing without intermediate annealing to obtain wire diameter 2 mm. Then performed a two-step annealing of metal first at a temperature 300 °C, then at a temperature 450 °C at a fixed holding time.
At each redivision sampled for the study of the mechanical properties and treated in accordance with the requirements of State Standard 1497-84. Testing of the samples was carried out on an electromechanical machine Walter + Bai AG LFM400 («Walter + Bai AG», Switzerland) with force 400 kN, with recording basic parameters ( σ В – tensile strength, MPa and δ – relative elongation, %).
The study results showed that the range of values of the billet ultimate tensile strength molded by casting into a mold is 60 – 65 MPa, and billets obtained in EMC – 100-110 MPa.
After heat treatment of cast billet and obtaining rod using method CRE depending on the casting method values σ в increase to 120 – 140 MPa, and after using methods CRA and CCRE – to 110 – 120 MPa. At the same rod tensile strength obtained by technology EMC+CRE higher on average by 7 %.
Analysis of the mechanical properties of the wire after drawing with degrees of deformation to 95 % (Fig. 1) showed that wire obtained from rods after CRE and EMC+CRE has higher strength characteristics (σ в = 210 – 220 MPa) compared with the wire obtained from rods after CRA and CCRE. Note also that the plastic properties higher in rods obtained after method CCRE.
It was also found that the presence of zirconium in aluminum alloy increases the thermal stability of semi-finished products. Conducted thermal testing showed that the values of tensile strength with increasing temperature up to 200 °C for rods obtained by method CRE decreases by 20 %, and for rods obtained by method CCRE – by 10 %.
Electrical resistance of the samples was measured using a millivoltmeter «Vitok» according to State Standard 7229-76. Results presented in Table 1.
According to results of investigations can be concluded:
Using zirconium as an alloying element in aluminum alloys containing up to 0,15 % allows in 1,5 times increase strength and improve the thermal stability of deformed semi-finished products compared to wire rod made of technical purity aluminum marks А5Е and А7Е.
For the production of deformed semi-finished products from aluminum alloys with higher strength properties necessary apply the method CRE with using billet obtained in electromagnetic crystallizer.
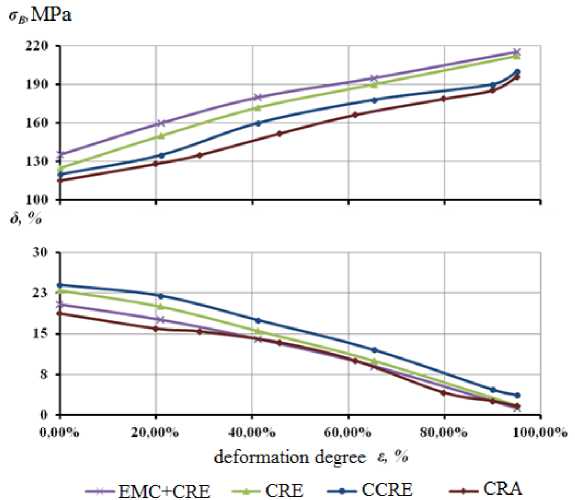
Fig. 1. Mechanical properties of deformed semi-finished products from alloys system Al – Zr depending on the processing methods: σ В – tensile strength; δ – relative elongation; ε – deformation degree
Table 1. The average values of the electrical resistivity of deformed semi-finished products obtained by different technologies
Method |
Characteristic |
σ в , MPa |
δ , % |
Electrical resistivity, Ohm∙mm2/m |
CRA |
Wire rod diameter 9,5 mm |
110 – 120 |
8,71 |
0,0305 – 0,0309 |
Wire diameter 2 mm |
190 – 200 |
1,55 |
0,0310 – 0,0320 |
|
Annealed wire diameter 2 mm |
60 – 70 |
20,83 |
0,0290 – 0,0307 |
|
CRE and EMC+CRE |
Rods diameter 9 mm |
120 – 140 |
17,0 |
0,0291 – 0,0309 |
Wire diameter 2 mm |
210 – 220 |
2,5 |
0,0296 – 0,0311 |
|
Annealed wire diameter 2 mm |
75 – 85 |
34 |
0,0288 – 0,0304 |
|
CCRE |
Rods diameter 9 mm |
110 – 120 |
24 |
0,0284 – 0,0298 |
Wire diameter 2 mm |
190 – 200 |
3,65 |
0,0285 – 0,0307 |
|
Annealed wire diameter 2 mm |
70 – 80 |
36 |
0,0275 – 0,0297 |
Technology CCRE compared with the classical methods (CRA) allows receiving deformed semifinished products with higher ductility and electrical conductivity. Values of the electrical resistivity for them are in the range 0,0285 – 0,0307 Ohm∙mm2/m.
Conducting a two-step annealing of wire obtained by cold drawing with deformation degree to 95 % makes it possible to recover the plastic properties of metal and reduce the value of the electrical resistivity to 0,0275 – 0,0297 Ohm∙mm2/m which is close to the values of the required State Standard.
Thus, to obtain the electrical wire rod from aluminum alloys with a high level of mechanical and electrical properties appropriate to apply methods of combined casting and rolling-extruding.
The studies were conducted in accordance with the contract №13G25.31.0083 with Russian Ministry of Education and UC RUSAL by topic «Development of technology for obtaining aluminum alloys with rare earth, transition metals and highly effective equipment for the production of electrical wire rod».