Ресурсосберегающая технология производства строительных материалов на основе глинистого сырья и отходов деревообработки
Автор: Андреева А.В., Буренина О.Н.
Журнал: Известия Самарского научного центра Российской академии наук @izvestiya-ssc
Рубрика: Механика и промышленность
Статья в выпуске: 5-2 т.11, 2009 года.
Бесплатный доступ
Показана возможность использования глинистого сырья и отходов древесины для производства мелкоштучных строительных композиционных материалов, приведены результаты исследования прочности при сжатии композитов в зависимости от влажности исходного сырья, усилия прессования и предложена технология изготовления изделий строительного назначения методом полусухого прессования.
Полусухое прессование, глиносырцовые материалы, полимербетонные смеси
Короткий адрес: https://sciup.org/148198716
IDR: 148198716
Текст научной статьи Ресурсосберегающая технология производства строительных материалов на основе глинистого сырья и отходов деревообработки
Цель работы: рассмотрение двух подходов к улучшению характеристик водостойкости и теплозащитных свойств глиносырцовых материалов – добавки отходов деревообработки для улучшения теплозащитных свойств и добавки цемента для повышения водостойкости. Известно, что добавки опилок в глину существенно понижают теплопроводность глинокомпозита, однако ухудшают прочность. Одновременное введение в глину, кроме опилок, цемент может обеспечить сохранение прочности на уровне обычного глиносырцового материала.
Для проведения исследований использовалось глинистое сырье месторождения Ой-Бесс Республики Саха (Якутия), которое по данным рентгеноструктурного анализа характеризуется содержанием каолинит-гидрослю-дистых глин. Сырье обладает удовлетворительной формовочной способностью, имеет среднюю пластичность, характеризуется малой воздушной и общей усадкой. Результаты гранулометрического анализа глин показали, что в глинистом грунте имеется большое количество (до 51,9%) пылеватых частиц дисперсностью от 1 до 5 мкм, что обеспечивает заполнение промежутков между более крупными частицами и повышает связующую способность глинистого материала. Наличие тонкодисперсных частиц с размерами менее 1 мкм (16,7%) достаточно для изготовления из них материалов и изделий методом полусухого прессования, количество частиц с размерностью 500-5- мкм составляет до 31,4 % [3]. В качестве модифицирующей минеральной добавки использовали сухую бетонную смесь с полимерной фиброй «Ремстрим-100» производства ТД «Стрим» (Москва, Россия), которая обладает хорошей адгезией к бетону и металлу, водонепроницаема и долговечна в высокоагрессивных средах, не содержит металлических наполнителей и хлоридов, относится к гидроизоляционным, антикоррозионным материалам, хороший антисептик, применяется при ремонте гидротехнических сооружений и строительных элементов, портов или морских зон, механических цехов, при защите бетона от агрессивных сред, содержащих сульфаты, сульфиды и хлориды, при усилении фундамента зданий, при ремонте покрытий дороги взлетно-посадочных полос на аэродромах, и т.д.
В качестве органического заполнителя использовали древесные опилки от механической обработки древесины хвойных пород, которые соответствовали следующим требованиям: размеры опилок характеризовались полным прохождением через сито с размером отверстий 10 мм; содержание примесей коры в опилках не более 10 %, а хвои 5 % к сухой смеси заполнителя; опилки не имели видимых признаков плесени и гнили, а также примесей инородных материалов. Технология изготовления строительных композиционных материалов на основе древесных опилок и глинистого сырья методом полусухого прессования представлена на рис.1.
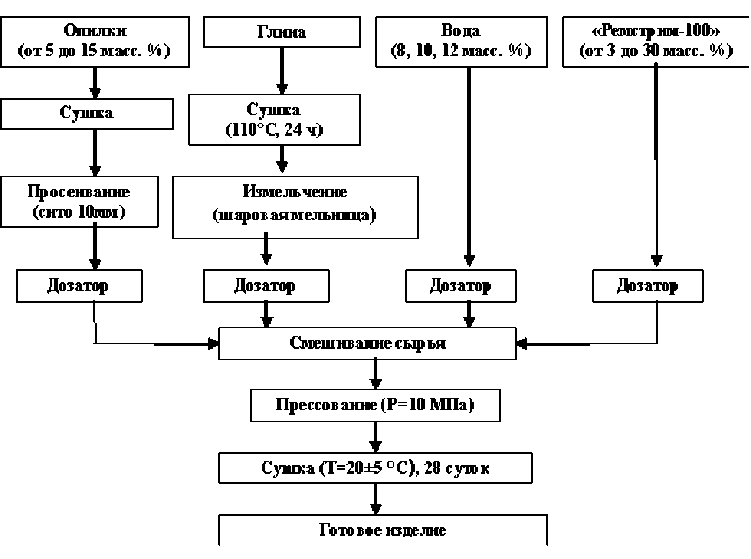
Рис. 1. Технологическая схема изготовления глиносырцовых изделий
Исследования образцов проводились по основным физико-механическим характеристикам строительных материалов, согласно действующих ГОСТ. Были проведены предварительные исследования по оценке влияния усилия прессования и формовочной влажности на прочность при сжатии материалов из исходного глинистого сырья. Было установлено, что оптимальное усилие прессования составляет 10 МПа и оптимальная формовочная влажность -12 масс.% (рис. 2, 3). Для проведения исследований были изготовлены цилиндрические образцы диаметром 54 мм на технологическом оборудовании, разработанном в Институте неметаллических материалов СО РАН [4]. Продолжительность сушки - 28 суток.
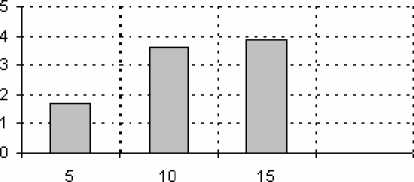
Усилие прессования, МПа
Рис. 2. Зависимость предела прочности при сжатии от давления прессования
Дальнейшие исследования были проведены на композиционных глиноопилочных образцах, изготовленных при оптимальной формовочной влажности 12 масс.% и давлении прессовании 10 МПа. Варьировалось со- держание опилок от 5 до 15 масc.%. Анализ полученных результатов показывает, что прочность при сжатии образцов снижается. При увеличении количества вводимых древесных опилок, наблюдается снижение прочности при сжатии образцов (рис. 4). Таким образом, было выбрано оптимальное количество вводимой добавки – 5 масc.% древесных опилок.
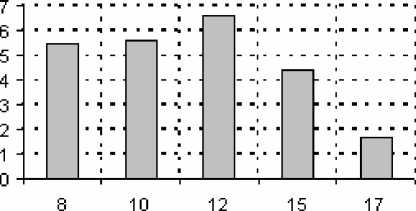
Формовочная влажность, %
Рис. 3. Зависимость предела прочности при сжатии от формовочной влажности
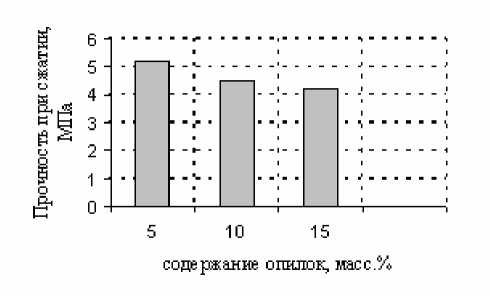
Рис. 4. Зависимость предела прочности при сжатии от содержания опилок
Следующим этапом исследования был выбор количества вводимой минеральной добавки – цемента, содержание которого варьировалось от 3 до 30 масc.% (рис. 5).
Анализ полученных результатов показал, что с увеличением количества вводимой добавки цемента до 30 масс.% прочность при сжатии увеличивается на 38%. Однако образцы, изготовленные с 3 масс.% цемента также обладают высокими прочностными показателями, и в целях экономии сырья было выбрано оптимальным наименьшее количество минеральной добавки. На основании полученных результатов были разработаны материалы следующего оптимального состава: глина – 80 масс.%, опилки – 5 масс.%, цемент – 3 масс.%, изготовленные при формовочной влажности 12 масс.% и давлении прессования 10 МПа. Прочность при сжатии разработанных материалов составляет 10,73 МПа, что на 36,6 % выше глиносырцового кирпича.
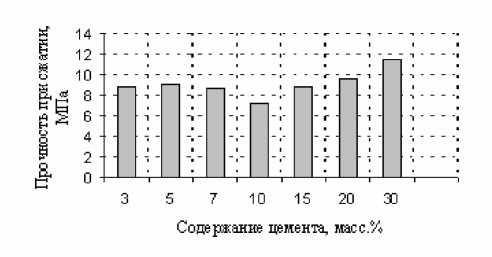
Рис. 5. Зависимость предела прочности при сжатии от содержания цемента
Выводы:
-
1. Определены оптимальные технологические параметры: усилие прессования – 10 МПа и формовочная влажность – 12 масс.%.
-
2. Установлено, что механические свойства композиционных материалов и изделий на основе глинистого сырья зависят от количества вводимых добавок. Лучшими свойствами обладают составы, содержащие 5 масс.% древесных опилок и 3 масс.% цемента, изготовленные при оптимальных технологических параметрах.
-
3. Предложена технология изготовления мелкоштучных композиционных строительных материалов и изделий на основе древесных опилок и глинистого сырья методом полусухого прессования, позволяющая получать качественные изделия, отвечающие требованиям строительного производства и частично решать проблему утилизации отходов из древесины.
Список литературы Ресурсосберегающая технология производства строительных материалов на основе глинистого сырья и отходов деревообработки
- Андреева, А.В. Технология изготовления строительных материалов на основе древесных опилок методом полусухого прессования/А.В. Андреева, О.Н. Буренина//Композиционные материалы в промышленности. Трубопроводы из полимерных композиционных материалов: изготовление, проектирование, строительство, эксплуатация: Материалы 29 междун. конф. и семинара 1-5 июня 2009 г. -Ялта-Киев: УИЦ «НАУКА. ТЕХНИКА. ТЕХНОЛОГИЯ», 2009. -С. 504-507.
- Лошанина, О.Н. Грунтобетон в малоэтажном домостроении Крайнего Севера./О.Н. Лошанина, А.Е. Местников//Повышение эффективности сельского строительства. Международный сборник научных трудов. -Новосибирск: НГАУ, 2000. -С.110-114.
- Андреева, А.В. Глиносырцовые строительные материалы с применением отходов деревообработки и полимербетонных смесей. -Композиционные материалы в промышленности. Трубопроводы из полимерных композиционных материалов: изготовление, проектирование, строительство, эксплуатация: Материалы 28 междунар. конф. и семинара 26-30 мая 2008 г. -Ялта-Киев: УИЦ «НАУКА. ТЕХНИКА. ТЕХНОЛОГИЯ», 2008. -С. 545-547.
- Попов, С.Н. Оборудование для полусухого прессования мелкоштучных строительных материалов/С.Н. Попов, И.И. Степанов, И.Н. Черский//Неметаллические материалы и конструкции для условий Севера. -Якутск: ЯНЦ СО РАН, 1996. -С.81-87.