Ресурсосберегающие восстановительно-упрочняющие технологии - основа вторичного производства деталей машин
Автор: Черноиванов В.И., Лялякин В.П., Литовченко Н.Н.
Журнал: Вестник аграрной науки @vestnikogau
Рубрика: Ремонт и органиация технического сервиса
Статья в выпуске: 1 (16), 2009 года.
Бесплатный доступ
Задача разработки оборудования и технологий восстановления и упрочнения деталей с повышенным ресурсом может быть решена совершенствованием одного из самых прогрессивных методов восстановления деталей - электродуговой металлизации (ЭДМ). Одновременно с решением металлургических и технологических проблем в статье предложены пути конструктивного совершенствования металлизационного аппарата и разработ
Короткий адрес: https://sciup.org/147123360
IDR: 147123360
Текст научной статьи Ресурсосберегающие восстановительно-упрочняющие технологии - основа вторичного производства деталей машин
ГНУ ГОСНИТИ
РЕСУРСОСБЕРЕГАЮ Щ ИЕ ВОССТАНОВИТЕЛЬНО - УПРОЧНЯЮ Щ ИЕ ТЕХНОЛОГИИ – ОСНОВА ВТОРИЧНОГО ПРОИЗВОДСТВА ДЕТАЛЕЙ МАШИН
Задача разработки оборудования и технологий восстановления и упрочнения деталей с повышенным ресурсом может быть решена совершенствованием одного из самых прогрессивных методов восстановления деталей – электродуговой металлизации ( ЭДМ ). Одновременно с решением металлургических и технологических проблем в статье предложены пути конструктивного совершенствования металлизационного аппарата и разработка методов упрочнения , прежде всего , для деталей , работающих в условиях абразивного износа и больших нагрузок , то есть , в первую очередь , для рабочих деталей почвообрабатывающей техники .
В настоящее время в России и других промышленно развитых странах потребление природных ресурсов и использование техники достигли огромного масштаба .
Естественно , в таких условиях ресурсосберегающие технологии становятся объектом особого внимания и заинтересованности производителей техники и в сфере ее использования . Ситуация значительно усугубляется из - за роста дефицита и стоимости запасных частей вследствие отставания их выпуска от потребности , а также их ресурса , который в большинстве случаев возможно существенно повысить восстановительно - упрочняющими методами .
Для достижения существенного роста объемов восстановления деталей необходимо оснащение ремонтных предприятий , в первую очередь , первого , второго и третьего уровня специализации – современными , высокоэффективными методами и технологиями , оборудованием восстановления и упрочнения с целью реального увеличения их ресурса по износостойкости в 1,5…2,0 выше новых .
Только в этом случае можно поднять экономический интерес у предприятий вторичного производства ( восстановления и упрочнения деталей ), а также у потребителей их продукции .
Поэтому ГОСНИТИ считает одной из приоритетных задач в своих исследованиях – разработку оборудования и технологий восстановления и упрочнения деталей с повышенным ресурсом .
В течение последних 27 лет НИИ « РЕМДЕТАЛЬ » и ГОСНИТИ уделяли серьезное внимание совершенствованию одного из самых прогрессивных методов восстановления деталей – электродуговой металлизации ( ЭДМ ).
ЭДМ , являясь универсальным методом металлопокрытий , имеет широкую область применения ;
-
- для восстановления стальных , чугунных и из цветных металлов деталей цилиндрической и плоской формы , работающих в условиях трения скольжения и смазки и неподвижных посадок ;
-
- для устранения дефектов стального и чугунного литья ;
-
- для повышения жаростойкости стали алитированием ( покрытие алюминием , его диффузия в поверхностные слои стального изделия );
-
- для нанесения антифрикционных покрытий при изготовлении подшипников скольжения ;
-
- для нанесения псевдосплавов : алюминий - железо ( АЖ -50), медь - железо ( МЖ -50) и др .;
-
- для долговременной антикоррозионной защиты алюминием и цинком металлоконструкций с гарантией 20-25 лет в условиях атмосферы ;
-
- для защитно - декоративных целей с покрытием медью , бронзой , латунью , алюминием .
Габариты деталей не лимитируют применение ЭМ .
Большие положительные качества ЭДМ ( технологичность , простота , высокая производительность и износостойкость покрытий , отсутствие термоповодок , низкая стоимость и универсальность , стабильность усталостной прочности восстанавливаемых деталей ) не могли быть не замечены учеными и производственниками . ЭДМ , как любой метод металлопокрытий , имел недостатки , поэтому перед институтом стояла задача устранить недостатки ЭМ с целью широкой реализации ее применения .
Основным недостатком всегда считалась низкая адгезионно - когезионная прочность покрытия . Микроструктурный анализ позволил установить , что покрытия , полученные с применением проволок , содержащих высокий процент ( от 0,8 до 2,3 %) кремния и марганца , имеют наиболее пористую структуру за счет шлаков , не растворимых в железе , и , соответственно , наименьшие прочностные свойства по сравнению с покрытиями из материала проволок с меньшим содержанием раскислителей .
Из этого следует стратегический вывод : необходимо применять для ЭМ проволоки с как можно меньшим содержанием марганца и кремния . Только такой подход позволил избавить ЭМ от отслоений и выкрашиваний при больших удельных нагрузках , испытываемой поверхностью деталей при работе .
Вторым фактором , ограничивающим применение ЭМ , являлась невысокая по сравнению с наплавкой твердость покрытия . Из - за этого такие детали , как тормозные барабаны , коленчатые валы и ряд других деталей оставались долгое время за пределами возможности восстановления ЭМ .
При этом процесс ЭМ оставался трудоемким из - за двухоперационности нанесения покрытия : подслой – слой .
Таким образом , установив основные недостатки ЭМ , предстоял длительный период их устранения . Длительный потому , что одновременно с металлургическими и технологическими проблемами решались задачи по конструктивному совершенствованию металлизационного аппарата .
Из анализа проблем прочностных и износостойких свойств покрытий , очевидно , следовал вывод , что необходимо создание нового присадочного материала для ЭМ . Такой материал – порошковая проволока ПП - ММ 2, ПП - ММ 63, ПП - ММ 65, ПП - ТП -1, была разработана по нашему техническому заданию Мариупольским металлургическим институтом под руководством д . т . н . В . А . Роянова и д . т . н . В . Я . Зусина . Содержание феррохрома – 16…19% и алюминия 14…17% в порошковой проволоке обеспечивали высокую адгезионно когезионную прочность ( на отрыв до 50…60 и до 125 МПа на срез ) и твердость 50…58 HRC. Для сравнения адгезия покрытия из проволоки Ст .30 составляет 18…22 МПа .
Выполненные в Мариупольском металлургическом институте сравнительные испытания покрытий на абразивную стойкость по методике Бринелля - Хаворта показали , что износостойкость покрытия из порошковой проволоки ПП - ММ 65 в 3,84, ПП - ММ 63 в 5,46 раза выше , чем эталона – покрытия из цельнотянутой проволоки марки Св 06 Х 19 Н 9 Т и превышает износостойкость покрытия из цельнотянутой проволоки марки Св 07 Х 25 Н 13 в 2,9 раза . Значение средних скоростей износа при трении пары покрытий из проволоки ПП - ММ 65 составляет 0,026…0,028 мм / час , образцов из Ст . 30 при тех же условиях испытания составила 1,65 мм / час .
Таким образом , такая порошковая проволока сразу сняла все основные недостатки ЭМ , что дало возможность значительно упростить технологию , отказавшись от нанесения подслоя , и расширить номенклатуру восстанавливаемых деталей . В настоящее время стало возможным широко внедрять восстановление тормозных барабанов , тормозных дисков и коленчатых валов , обеспечивая ресурс не ниже новых .
При всех преимуществах порошковой проволоки она имеет не менее существенный недостаток – высокую цену . В настоящее время ее цена составляет около 150 тыс . рублей за тонну . Поэтому разработан альтернативный вариант порошковой проволоке – комбинацию из двух цельнотянутых ( углеродистой и хром никелевой ) проволок . Сравнительные испытания на адгезионно когезионную прочность и износостойкость покрытий показали сопоставимость результатов . Преимущества : стоимость цельнотянутых проволок по сравнению с ПП - ММ 2 в 2,5…4 раза ниже , стабильность горения дуги выше .
Совершенствование ЭДМ идет в ГОСНИТИ и в направлении разработки новых моделей металлизаторов со сверхзвуковым истечением гетерофазного потока, обеспечивающего повышение адгезионно-когезионной прочности в 1,5 раза и других физико-механических свойств ЭМ-покрытий, а также повысить коэффициент использования присадочного материала на 20%. В связи с повышением прочностных свойств ЭМ-покрытий стало возможным расширить номенклатуру восстанавливаемых деталей, например представилась возможность металлизировать коленчатые валы тяжелых двигателей, таких как КамАЗ -740 и тракторной техники, тормозные диски и диски сцепления, опоры коренных подшипников блоков цилиндров дизелей и другие.
Первой моделью нового сверхзвукового металлизатора стал ЭДМ -9 Ш Д ( рис . 1). Его особенности : универсальность ( ручной , станочный ), шаговый электродвигатель мощностью 40 Вт , автоматика пуска ( подача воздуха и электроэнергии ), масса 2,6 кг , регулировка скорости подачи проволоки плавная от 0,8 до 14,6 м / мин , производительность до 10 кг / час . В настоящее время готовится рабочая конструкторская документация на производство очередной новой модели сверхзвукового трехэлектродного металлизатора ЭДМ -3 ЭЛ , поднимающего метод ЭДМ на новый уровень получения высококачественных металлопокрытий для восстановления деталей и долговременной антикоррозионной защиты металлоконструкций алюминием и цинком .
ЭДМ -3 ЭЛ защищен патентом № 2254933 от 12.08.2005 г .
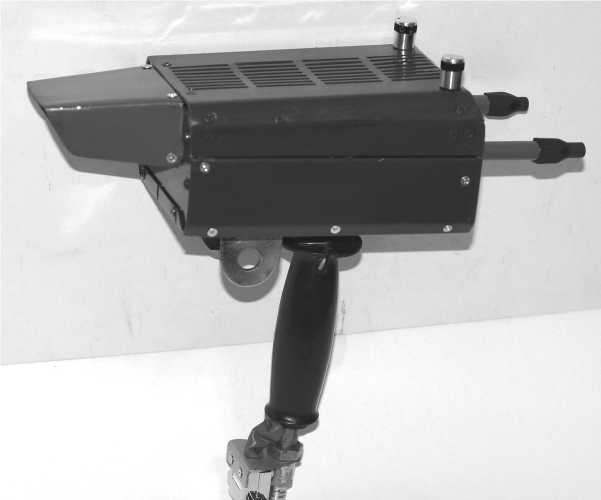
Рисунок 1 – ЭДМ -9 Ш Д
Преимущества ЭДМ -3 ЭЛ : принцип действия исключает все недостатки классической схемы двухэлектродных металлизаторов , от которых практически избавиться невозможно ; позволяет получение комбинированных покрытий , используя проволоки разных сортов , химических составов и диаметров ; может работать с одной проволокой или продолжать работать в случае прекращения подачи второй ; существенно расширяется диапазон по диаметру проволок от 1,0 до 3,0 мм .
Эти преимущества ЭДМ -3 ЭЛ позволят существенно расширить сферу использования электродуговой металлизации в различных областях промышленности .
Экономическая эффективность ЭДМ обеспечивается ощутимой разностью стоимости новых деталей и затрат на восстановление . Восстановление составляет 10…50% от стоимости новых деталей .
Изготовить детали машин – полдела . Вторая часть – ее упрочнение , то есть придание ей качеств , обеспечивающих работоспособность и требуемый ресурс . В идеале ресурс детали должен быть равным ресурсу машины в целом . К сожалению , это условие в основном не выполняется потому , что упрочнению уделялось и уделяется в настоящее время недостаточное внимание , хотя , казалось бы , создано и применяется много различных методов упрочнения . Но они или сложны , трудоемки и дорогостоящие или малоэффективны .
Перед специалистами ГОСНИТИ была поставлена задача разработать метод упрочнения , прежде всего , для деталей , работающих в условиях абразивного износа и больших нагрузок , то есть , в первую очередь , для рабочих деталей почвообрабатывающей техники .
Заводы - изготовители почвообрабатывающей техники не обеспечивают требуемую износостойкость деталей , вследствие чего в эксплуатации потребитель сталкивается с необходимостью частых заточек лезвийных поверхностей , что вызывает естественно вынужденные простои техники , а также значительное снижение долговечности деталей и связанные с этим ощутимые экономические потери .
Поэтому проблема повышения ресурса рабочих органов почвообрабатывающей техники стоит в сельскохозяйственном производстве особо остро .
Ни один из применяющихся в настоящее время в России методов упрочнения не решает эту проблему . Конкретно она состоит в создании метода упрочнения , обеспечивающего ресурс рабочих органов , соизмеримый с ресурсом техники в целом , а также в способности к импортозаменяемости .
Для реализации задачи необходимо , чтобы метод упрочнения отвечал критерию ( К т ) относительного значения микротвердостей упрочненной поверхности детали ( Н ) и абразива ( Н а )
К т = Н / Н а
То есть способность абразивных частиц внедряться в поверхностный слой и разрушать его при движении приближенно должна оцениваться по этому соотношению показателей микротвердостей взаимодействующих деталей и среды .
Отечественный ученый М . М . Тененбаум опытным путем установил , что критерий Кт должен быть в пределах 0,5…0,7. В этом случае ресурс рабочих органов будет приближен к ресурсу техники в целом .
В ГОСНИТИ выработана стратегия решения этой проблемы , заключающаяся в следующем :
Первое . Ставка сделана на разработку метода восстановления и упрочнения металлокерамическими покрытиями ( МКП ).
Второе . Метод прост , дешев , технологичен , не требующий сложного дорогостоящего оборудования .
Третье . Области применения – машиностроительные предприятия сельскохозяйственного значения , МТС , РТП , фермерские хозяйства в стационарных и нестационарных условиях .
Базой для реализации этого плана является созданный в лаборатории № 10 ГОСНИТИ скоростной электродуговой термодиффузионный метод и оборудование скоростного электродугового упрочнения , позволяющего получить в упрочненном поверхностном слое сложнофазную структуру , содержащую кроме термодиффузионных элементов ( углерода , бора и др .), но и металлокерамические образования . Происходящее в ходе упрочнения проплавление поверхностного слоя детали на глубину не менее 2 мм является необходимым для такого процесса условием , так как для МКП требуется стальная матрица .
Научный результат , выполненный в ГОСНИТИ работы по электродуговому упрочнению , оказался чрезвычайно обнадеживающим . Дело в том , что пасты , содержащие алюминий , буру или карбид бора обеспечивают высокую микротвердость – от 1114 до 1225 кгс / мм 2 ( примерно 98 HRC). Какая же фаза может обеспечить такую высокую твердость ?
Структурный анализ показал , что ею является интерметаллид – железная шпинель Fe*Al2O3, карбид бора и тригональная кристаллическая система расплавленного Al 2 O 3 ( корунд ), имеющая исключительно высокую твердость .
Учитывая , что при электродуговом упрочнении имеет место проплавление поверхностного слоя , можно сделать очень важный вывод , что образуется металлокерамическая структура , имеющая не только высокую твердость , но и такую же несущую прочность благодаря стальной матрице , удерживающей керамический компонент .
Практически благодаря выполненной научно экспериментальной работе мы оказались близки к нижнему пределу критерия упрочнения Кт . Он достиг значения 0,3. такой результат традиционными упрочняющими технологиями не получишь .
Для выполнения скоростного электродугового упрочнения в ГОСНИТИ создан аппарат ЭДУ -2, рисунок 2.
Традиционные термодиффузионные способы упрочнения насыщением стали углеродом , азотом , бором , хромом и другими элементами используются в стационарных условиях . Известно , что эти технологии энергоемкие и трудоемкие . Глубина упрочнения недостаточна для почвообрабатывающей техники , а для крупногабаритных деталей практически промышленные методы упрочнения непригодны .
В ГОСНИТИ разработан термодиффузионный метод упрочнения стали с использованием дугового разряда , в режимах прямой , косвенной дуги и короткого замыкания с использованием графитовых электродов диаметром 6…10 мм . Это более рациональный , несложный , комплексный метод уп рочнения и более дешевый - в три - четыре раза ниже стоимости применяемых способов .
Разработана технология и мобильное оборудование для скоростного электродугового упрочнения , предназначенного для использования , как в стационарных , так и в полевых условиях .
Термодиффузионное упрочнение стали с использованием дугового разряда ( ЭДУ ) является одним из самых интересных и перспективных направлений изучения .
Поверхностное термодиффузионное упрочнение с использованием дугового разряда привлекает большей простотой аппаратурного исполнения по сравнению с хорошо известными высококонцентрированными источниками энергии ( ВИЭ ). Процессы , происходящие при воздействии дугового разряда на металл , во многом аналогичны процессам при обработке другими ВИЭ , что касается теплообмена и фазово - структурных превращений .
Аппарат ЭДУ -2 предназначен для ускоренной цементации с твердостью до 60…65 HRC быстроизнашивающихся деталей , работающих в условиях абразивного износа и высоких нагрузок техники почвообрабатывающей , перерабатывающей , добывающей , строительной и других отраслей промышленности в полевых и стационарных условиях . При боронитроцементации твердость достигает 75…78 HRC.
Способ электродугового упрочнения ( ЭДУ ) основан на насыщении поверхности детали углеродом в процессе дугового разряда между угольными электродом ( косвенная дуга ), расположенными в непосредственной близости 3-8 мм от детали или между угольным электродом и деталью ( прямая дуга ). Другой способ упрочнения - в режиме короткого замыкания , то есть при непосредственном контакте электрода с поверхностью детали и постоянным его перемещении . После науглероживания выполняется закалка и низкотемпературный отпуск (1800 С ). ЭДУ может осуществлять также с помощью паст , что дает возможность получить борирование , нитроцементацию , сульфоционирование нанесение металлокерамических покрытий , а также одновременное упрочнение наплавляемых покрытий .
Во всех случаях идет процесс локального нагрева детали и угольного электрода . Последний испаряется с образованием ионов углерода , которые легко диффундируют в нагретый металл .
Благодаря быстротекучести процесса способ ЭДУ назван электродуговой скоростной цементацией .
Аппарат ЭДУ -2 предназначен для цементации , борирования , нитроцементации деталей почвообрабатывающей техники , перерабатывающей , добывающей , строительной и других отраслей промышленности . Возможные области применения скоростного электродугового упрочнения : почвообрабатывающая техника ( плуги , культиваторы , дисковые бороны и др .); льноперерабатывающее оборудование ; бильные планки ; мясоперерабатывающее оборудование , свеклорежущие ножи сахарных заводов ; строительные мелиоративные и машины по внесению удобрений ; горнодобывающая буровая и дорожно строительная техника ; метало - и деревообрабатывающий инструмент .
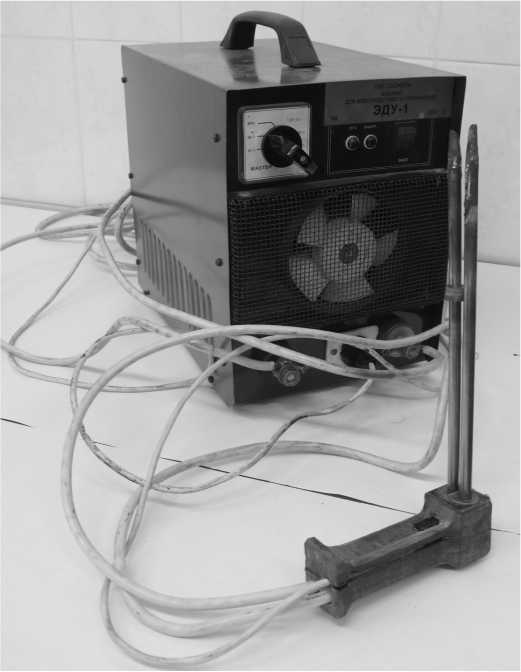
Рисунок 2 – Аппарат ЭДУ -2
Разработанные технологии и оборудование для скоростного электродугового упрочнения , предназначены для использования как в стационарных , так и в полевых условиях .
Выводы
-
1. Усовершенствован электродуговой металлизатор ЭДМ -3 ЭЛ : принцип действия исключает все недостатки классической схемы двухэлектродных металлизаторов , от которых практически избавиться невозможно ; позволяет получение комбинированных покрытий , используя проволоки разных сортов , химических составов и диаметров ; может работать с одной проволокой или продолжать работать в случае прекращения подачи второй ; существенно расширяется диапазон по диаметру проволок от 1,0 до 3,0 мм .
-
2. Преимущества ЭДМ -3 ЭЛ позволяют существенно расширить сферу использования электродуговой металлизации в различных областях промышленности .
-
3. Разработан более рациональный , несложный , комплексный метод упрочнения и более дешевый термодиффузионный метод упрочнения стали с использованием дугового разряда , в режимах прямой , косвенной дуги и короткого замыкания с использованием графитовых электродов диаметром 6…10 мм .
-
4. Созданный скоростной электродуговой термодиффузионный метод и оборудование скоростного электродугового упрочнения , позволяет получить в упрочненном поверхностном слое сложнофазную структуру , содержащую кроме термодиффузионных элементов ( углерода , бора и др .), но и металлокерамические образования .