Rock burst and actually effective bolting for rock burst prevention
Автор: Nguyen Ngoc Minh, Pham Duc Thang
Журнал: Горные науки и технологии @gornye-nauki-tekhnologii
Рубрика: Разработка месторождений полезных ископаемых
Статья в выпуске: 2, 2019 года.
Бесплатный доступ
Rock burst represents a very dangerous phenomenon in deep underground mining, as well as for underground structures in unfavourable conditions (great depth, high horizontal stress, proximity of major tectonic structures, etc.). The rock burst problem relates to the natural and mining conditions of the rock mass. The evaluation of rock burst is becoming increasingly important as mining activities reach greater depths. In the literature, rock burst assessment challenge was tackled by many researchers using various methods. However, no study providing review and comparison of different rock burst assessment methods is available. In this paper, rock burst classification is briefly summarized. This includes a classification based on rock burst type, and another classification based on rock burst severity. As an important method for rock burst prevention, some novel energy-absorbing bolts were developed. These bolts demonstrate constant resistance under both static and shock loads and large elongation ability enabling them to withstand large deformations of rock masses under rock burst-prone conditions. Among the novel energy absorbing bolts, Modified Cone Bolt (MCB) and Constant Resistance at Large Deformation (CRLD) Bolt are selected to be presented in this paper.
Rock burst, bolting, rock burst prevention, deep mines, shock loads, rock strain
Короткий адрес: https://sciup.org/140243548
IDR: 140243548 | DOI: 10.17073/2500-0632-2019-2-103-110
Текст научной статьи Rock burst and actually effective bolting for rock burst prevention
Rock burst is an unstable rock failure and one of the most hazardous problems in deep mines and civil tunnels. It is a sudden failure of rock in the form of rapid ejection of failed rocks, accompanied by the release of a large amount of energy [1]. Rock burst frequently occurs at excavation faces or in a working panel of an underground excavation at great depth. It can cause mechanical damage, delays of projects, and economic losses. As an example, hundreds of rock bursts occurred during the construction of the extra-long seven tunnels at the Jinping II hydropower station in China. On 28 November 2009, an extremely severe rock burst caused seven deaths and one injury, as well as total destruction of a tunnel boring machine (TBM) [2].
In the latest years, rock burst phenomena have been investigated by many researchers through theoretical, numerical, and experimental approaches [3]. Due to the complex nature of rock burst phenomenon, precise rock burst prediction is rather difficult. Since Cook et al. (1966) first proposed the method for evaluating the rock burst in mining conditions, a variety of methods, either elaborated or simplified, ranging from empirical to theoretical and mathematical approaches for predicting rock burst potential have been developed in the past few decades. However, due to the complexity of rock burst assessment systems, including multivariable and strong interference, there is no universally accepted method to predict the moment of rock burst, and the best we can achieve today is to identify rock burst hazard areas using empirical criteria, numerical models or personal experience [4].
In addition to understanding rock burst mechanisms, controlling rock burst damage is important for providing safety of mining opera- tions and underground structures. Rock support using bolts and anchors, providing fractured rock reinforcement and retaining, is an efficient measure for rock burst control in underground mining [5]. Researchers worldwide have developed some dynamic rockbolts [6, 7]. The MCB conebolt developed in Canada has been successfully used in Canadian hard rock mines and in some other countries. The "constant resistance at large deformation (CRLD)" bolt, developed by the State Key Laboratory for Geo-mechanics and Deep Underground Engineering at China University of Mining and Technology, Beijing (GDUE), is successfully tested in a coalmine in China to demonstrate the effectiveness of the CRLD cable [3].
This paper focuses on providing the reader with a complete review of rock burst classification and some dynamic rockbolts to control rock burst.
-
2. Rock burst classification
-
2.1. Classification based on rock burst type
A classification system was developed and applied worldwide to record and report rock bursts using the terms of induced bursts, residual bursts, inherent bursts, and combination bursts were adapted by Colson (1950) [8] based on the origin of the burst. Later scientists have been recognized and developed some new methods of rock burst classifications such as:
-
+ Ortlepp (1997) [9] made a distinction between the seismic source mechanism and the rock burst crushing mechanism, while Kaiser et al. (1992) [10] used the term "modes of failure", to describe the same cases, and a rock burst may be further classified by Kaiser et al. (1996) [11] as bulking, ejection, and seismically-induced caving ground based on the damage mechanism (See Fig. 1a);
Ж ГОРНЫЕ НАУКИ и ТЕХНОЛОГИИ
MINING SCIENCE AND TECHNOLOGY
Damage Mechanism
Block ejection
(b) rock ejection from seismic energy transfer
Severe
(a) rock bulking due to fracturing
Moderate
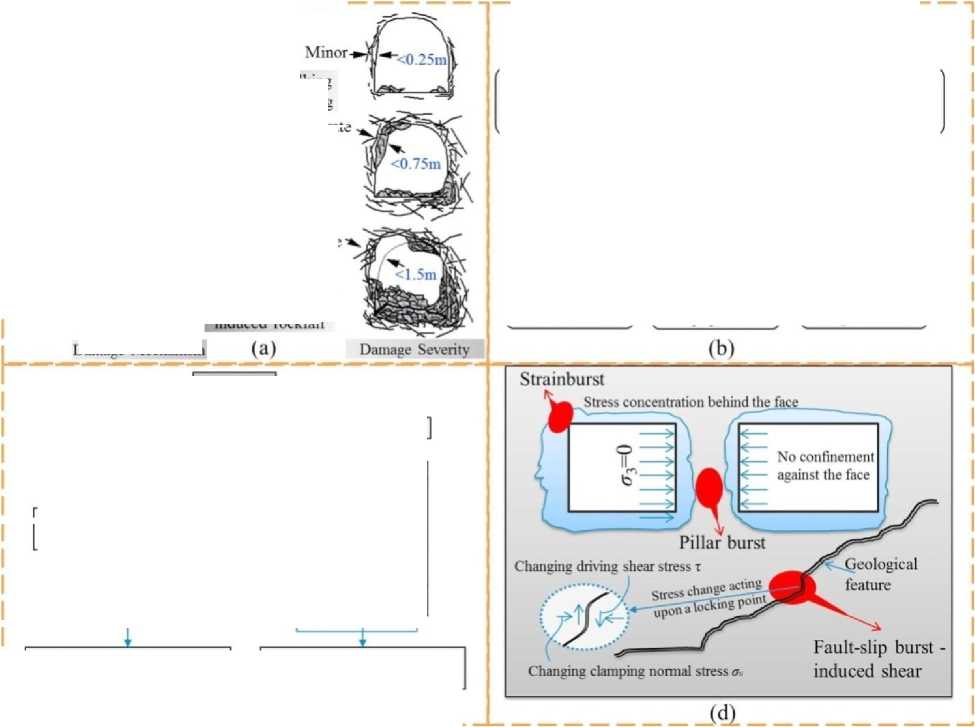
Experimental system on Expeerimental system on ______ strainbutsts _________ impact-induced burst
_(c)_ _
Fig. 1. Rock burst type classification: (a) by rock burst damage mechanism and damage severity; (b) by rock burst me- chanism; (c) by rock burst triggering mechanism; (d) by rock burst potential and confinement effect
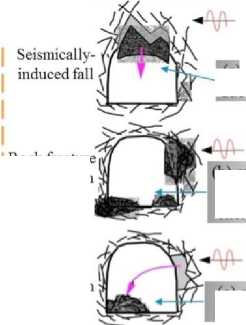
Rock fracture । with dilation
(c) seismically-induced rockfall
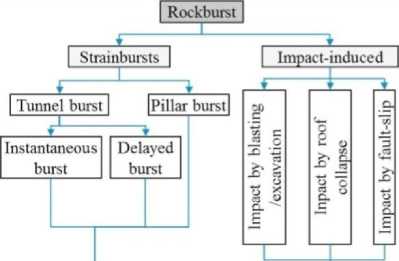
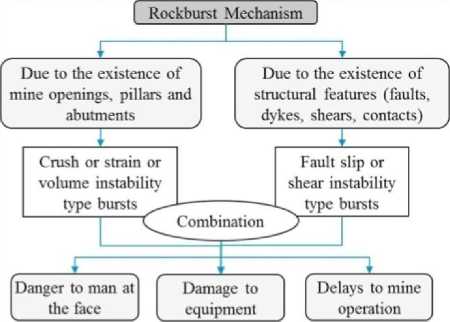
+ Rock burst mechanisms are grouped by Tang (2000) [12] into three broad categories: strainbursts, slip fault bursts and combined mechanism bursts (see Fig. 1b), and he pointed out that the majority of rock bursts are of the strainburst type in deep hard rock mines;
+ Based on stress paths and using experimental methods, He et al. (2012) [13] classified rock bursts into two major types: strainbursts and impact-induced bursts as shown in Fig. 1c. Strainburst: frequently encountered in tunnelling and mining environment; they are associated with pillar and room mining cavities. In relation to different stress paths and failure locations, strainbursts can be divided into three sub-types: instantaneous burst, delayed burst, and pillar burst. The impact-induced burst: after excavation, the surfaces of the cavities and the pillars may also suffer rock burst due to the impact waves generated by mining-induced disturbances. Based on generation mechanism, the im- pact-induced burst can be divided into three subtypes, i.e. the rock burst induced by blasting or excavation, by roof collapse, and by slip fault.
+ Based on the analysis of classification of the rock burst mechanisms conducted by Kaiser et al. (1996) [11] the manifestations of potential rock burst phenomena with high levels of strain energy, which are usually classified as strainburst, pillar burst or slip fault bursts (Castro et al., 2012 [14]), are illustrated in Fig. 1d.
2.2. Classification based on rock burst severity
Numerous research works concerning the potential of rock burst have been performed. For example, Russnes’s method (Russenes, 1974) [15], which classifies the rock burst intensity into four levels (none, weak, moderate, and severe based on noise, shape, and features of failure after rock burst); Tan’s method [16] which classifies rock burst into four groups based on the large number of laboratory tests and investiga-
Ж ГОРНЫЕ НАУКИ и ТЕХНОЛОГИИ
MINING SCIENCE AND TECHNOLOGY tions in situ, and considers mechanical characteristics, type and shape of the failure, intensity of breakdown failure, and the sound of the rock burst; Brauner’s method [17], which classifies rock burst into three groups based on the intensity of breakdown failure of the surrounding rock mass; the Canadian Rock burst Research Program’s (CRRP) [18] method, which classifies the severity of rock burst damage into minor, moderate, and major damage, and estimates the severity of rock burst damage based on observations and empirical evidences, the depth of the damage zone in the rock mass and geometric considerations. Recently a new rock burst classification method was introduced by Chen et al. (2013) [19] for quantitative evaluating rock burst intensity on the basis of the released energy of the rock burst, monitored by micro-seismic technique, and surrounding rock damage severity.
3. Rock burst support
Rock support in burst-prone rock mass differs from conventional rock support in shallow rock mass where controlling gravity-induced rock caving is the main concern. Rock support in burst-prone rock mass needs to resist dynamic loading and large rock dilation due to rock failure. Manystudies have been performed to address the rock burst problem [20]. These studies recommend and provide design of rock burst support to mitigate rock burst damage. MCB conebolt and CRLD bolt are proposed to control rock burst problem.
3.1. MCB conebolt
The concept of conebolt was firstly developed in South Africa. The conebolts were groutable yielding tendons developed by the Chamber of Mines Research Organization (COMRO) in 1987 [21] for use in cement grouted holes.
The South African conebolts were first tested in Canada in 1994 [22] using cement grout and polyester resin (injected with quick-setting resin grout). The cement grouted conebolt had a maximum displacement of 240 mm and the loaddisplacement curve similar to that of steel stretching curve, indicating that there was insignificant cone movement during pull-out test. In resin grout testing, the conebolt could not shear through the resin and failed after about 100 mm of displacement only. But no mine in Canada systematically used the South African conebolts in its operation. The main reason was that the resin injection was not practical for use that time, and cement grouting was time consuming and required a third pass to screw in the bolts once the grout was cured.
The increase in quantity of violent ejection failures in 1999/2000 at Brunswick Mine in Canada led to the urgent development of complete yielding support system [23]. The South African conebolts were modified to satisfy resingrouting applications in Canada. Norand Inc. modified the conebolt head and added a blade for the purpose of resin mixing, and the new bolt was called Modified Cone Bolt (MCB). This new tendon can shear through the surrounding column of polyester resin grout. It is a smooth bar threaded at its outer end, with a forged cone and mixing blade at another end.
A close-up view of the rock burst support system installed at Brunswick Mine can be seen in Fig. 2. There was a distinct boundary in one drift (tunnel) that defined stable and unstable rock masses in Fig. 2. This boundary was called the "extreme edge" at the mine site. Beyond the extreme edge, there were only standard rock support systems installed. A series of rock burst events that occurred between October 13 and 17, 2000 severely damaged the rock mass where standard supports were installed, but the section which was supported by the rock burst support system suffered no damage.
The excellent performance of the MCB supported tunnel section allowed many people to speculate that the rock might not be prone to burst as the rest of the area. However, close onsite examination revealed that the MCB had fulfilled specific role in dissipating dynamic energy as some conebolts displaced as much as 180 mm [23]. Subsequent use of MCBs based rock support system at the mine site showed its excellent performance.
Ж ГОРНЫЕ НАУКИ и ТЕХНОЛОГИИ
MINING SCIENCE AND TECHNOLOGY
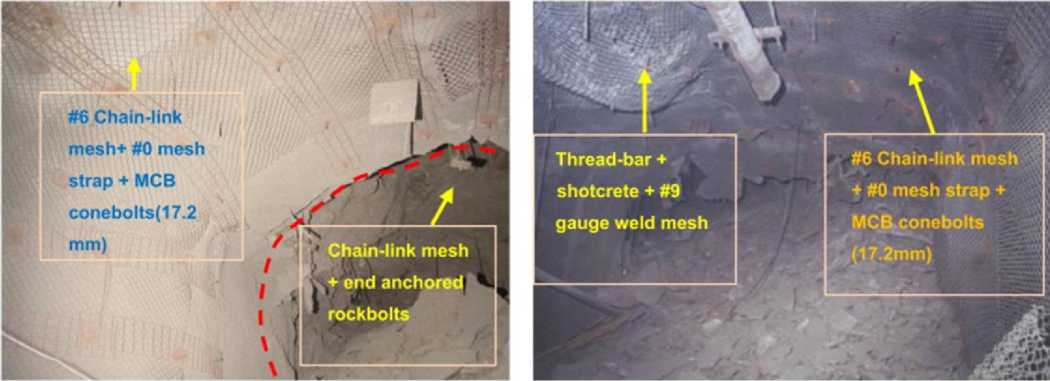
Fig. 2. Modified Cone Bolt (MCB) at Brunswick Mine
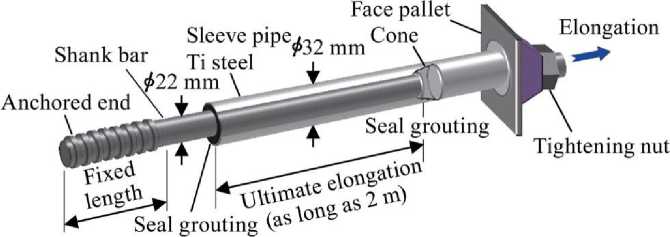
Fig. 3. Schematic of the three-dimensional view of CRLD bolt
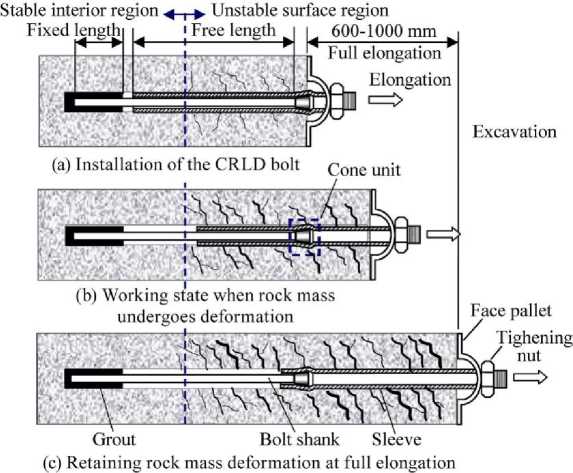
Fig. 4. Working principles of CRLD bolt
After the success at Brunswick Mine, MCBs have enjoyed slow but gradual acceptance by some Canadian mines having rock burst problems, and have been successfully applied in rock burst support systems.
3.2. CRLD bolt
Bolts provide a major method used in rock support in many practical situations. However, in high stressed rock masses and for large strain/deformation situations, bolts may be bro-
Ж ГОРНЫЕ НАУКИ и ТЕХНОЛОГИИ
MINING SCIENCE AND TECHNOLOGY ken if they are not able to adapt to the induced large deformations [24, 25]. So, a new constantresistance and large-deformation (CRLD) bolt was developed by GDUE to mitigate and control rock burst damage.
Fig. 3 shows schematically the structure of the CRLD bolt which consists of the following components: a piston-like cone installed on a bolt shank (rebar), sleeve pipe with its inner diameter slightly smaller than the large-end diameter of the cone, face plate and nut functioned as the retention device. The fixed length of the shank bar is bonded by grout.
Fig. 4 illustrates the supporting principle of the CRLD bolt over three different stages:
-
- Elastic deformation stage: at this stage, the deformation energy of the surrounding rocks impacts on the bolt rod in the bolt assembly through the baffle plate and inner anchorage segment. In the case of relative deformation of the surrounding rock where the axial force caused by the rock deformation is less than the rated constant resistance of the CRLD bolt, the bolt will not elongate. Instead, the bolt will resist the deformation and failure of the rock by solely relying on the elastic deformation of the constant-resistance element or bolt rod itself (Fig. 4a). In the figure, P 0 is generated by the cone-sleeve relative sliding and is the resistance of the bolt, pre-designed as function of elasticity of the sleeve and the structure of the cone.
– Structural deformation stage: at this stage, the axial force on the rod increases and may be equal to or greater than the rated constant resistance of the CRLD bolt. This leads to frictional-sliding displacement of the constantresistant body along the sleeve track, i.e., the CRLD bolt elongates. While elongating, the bolt keeps the constant-resistant characteristics and the deformation and failure of the rock mass is contained by its elongation, i.e. structural deformation of the constant-resistant element occurs (Fig. 4b).
Ultimate deformation stage: at this stage, the deformation energy of the rock mass in the abutment to the stope is fully released. The external loads will be lower than the rated constant resistance, and the constant-resistant body will stop sliding due to frictional drag. By this way, the surrounding rock mass is stabilized once again (Fig. 4c).
During development, the CRLD bolt has been tested both in situ and in laboratory conditions. The maximum extension of the CRLD rockbolt is about 1000 mm which should be able to accommodate the displacement of the rock mass adjacent to the deep underground excavations. Compared to existing large-deformation bolts and anchors, the CRLD bolt (CRLDB) has much longer extension length under the same external pulling forces, while its maximum loadcarrying capacity is much higher.
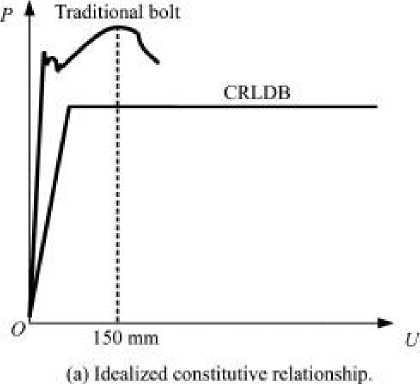
Fig. 5. Behavior of traditional bolt and CRLD bolt in tension tests
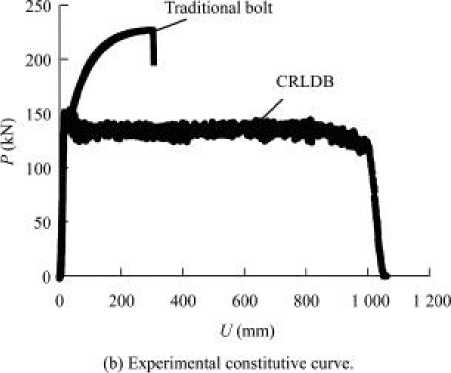
Ж ГОРНЫЕ НАУКИ и ТЕХНОЛОГИИ
MINING SCIENCE AND TECHNOLOGY
That is why the CRLDB is suitable for rocks and soils with large deformation. The built-in drag-adaptive regulator in the CRLDB can be adaptive to the external loading by preventing itself from being broken off in the case where the external load exceeds the allowable value. CRLDB demonstrates ideally elastoplastic behavior (Fig. 5a), and the behavior of the traditional bolt is also plotted herein for comparison. For detailed assessment of this new type of bolt, tension tests were carried out on a traditional bolt and CRLDB (Fig. 5b). At the same tensile loading level, the traditional bolt was broken with limited deformation length, whereas CRLDB showed much longer extensile length. CRLDB can bear shock for many times keeping good supporting performance. It is suitable for supporting in the burst-prone roadways [26].
4. Conclusion
This short review presents rock burst research status in the world, and highlights some of rock burst classification methods and novel energy-absorbing bolts for controlling rock burst.
Rock burst classification by type can be based on different parameters such as:
-
‒ Rock burst damage mechanism and damage severity;
-
‒ Rockburstmechanisms;
-
‒ Rockbursttriggeringmechanism; and
-
‒ Rock burst potential and the confinement effect.
Rock burst classification based on rock burst severity was introduced.
For rock burst control, new yieldable or energy absorbing bolt/cable (MCB conebolt and CRLD bolt) were developed which demonstrate constant resistance under static and dynamic loadings and have large elongation capacity. MCBs have proved their efficiency in resolving rock burst problems in Canada, and have been successfully applied worldwide. CRLD bolt was tested in a field experiment, and the experimental results demonstrated its good energy absorbing performance and the ability to contain large deformation of rock masses.
Ж ГОРНЫЕ НАУКИ и ТЕХНОЛОГИИ
MINING SCIENCE AND TECHNOLOGY
Список литературы Rock burst and actually effective bolting for rock burst prevention
- Amin M., Ming C. Numerical modeling of rock burst near fault zones in deep tunnels. Tunnelling and Underground Space Technology, 80, 2018, pp. 164-180.
- Xiao Y. X., Feng X. T., Li S. J., Feng G. L., Yub Y. Rock mass failure mechanisms during the evolution process of rock burst s in tunnels. International Journal of Rock Mechanics & Mining Sciences, 83, 2016,pp. 174-181.
- Man C. H., Fu Q. R., Dong Q. L., Rock burst mechanism research and its control. International Journal of Mining Science and Technology, 28, 2018, pp. 829-837.
- Jian Z., Xi B. L., Ha S. M. Evaluation method of rock burst: State-of-the-art literature review. Tunnelling and Underground Space Technology, 81, 2018, pp.632-659.
- Kaiser P. K., McCreath D., Tannant D. Rock burst research handbook, Vol. 2, 1996, pp.1990-1995.
- Cai M., Champaigne D. Influence of bolt-grout bonding on MCB conebolt performance. International Journal of Rock Mechanics and Mining Sciences, 49, 2012, pp.165-75.
- He M. C., Gong W. L., Wang J., Qi P., Tao Z. G., Du S., et al. Development of a novel energy-absorbing bolt with extraordinarily large elongation and constant resistance. International Journal of Rock Mechanics and Mining Sciences, 67, 2014, pp.29-42.
- Colson C. M. Rock burst s. Masters Theses. Missouri S&T, 1950, pp. 43-49.
- Ortlepp W. D. Rock fracture and rock burst s an illustrative study. Johannesburg, SAIMM Monogr., 1997, Ser. M9, 98.
- Kaiser P. K., Tannant D. D., Mccreath D. R., Jesenak R. Rock burst damage assessment procedure. In: Kaiser, P.K., McCreath, D.R. (Eds.), Rock Support in Mining and Underground Construction. Balkema, Rotterdam, 1992,pp. 639-647.
- Kaiser P. K., Tannant D. D., McCreath D. R. Canadian Rock burst Support Handbook.Geomechanics Research Centre, Laurentian University, Sudbury, Ontario, 1996, pp. 314.
- Tang B. Y. Rock burst control using distress blasting (Ph.D. thesis). McGill University, Montreal, Canada, 2000.
- He M. C., Xia H. M., Jia X. N., Gong W. L., Zhao F., Liang K.Y. Studies on classification, criteria and control of rock burst s. J. Rock Mech. Geotech. Eng., 4(2), 2012, pp. 97-114.
- Castro L. A. M., Bewick R. P., Carter T.G. In: An Overview of Numerical Modelling Applied to Deep Mining. Innovative Numerical Modelling in Geomechanics. CRC Press, 2012, pp. 393-414.
- Russenes B.F. Analysis of rock spalling for tunnels in steep valley sides. M.Sc. thesis, Norwegian Institute of Technology, Trondheim, Department of Geology, 1974.
- Tan Y.A. Rock bursting characteristics and structural effects of rock mass. Sci. Chin., 1992, Ser. B, 35(8), pp. 981-990.
- Brauner G. Rock burst in Coal Mines and Their Prevention. A. A. Balkema, Netherlands, 1994.
- Kaiser P. K., Tannant D. D., McCreath D.R. Canadian Rock burst Support Handbook. Geomechanics Research Centre, Laurentian University, Sudbury, Ontario, 1996, pp. 314.
- Chen B. R., Feng X. T., Li Q. P., Luo R. Z., Li S.J. Rock burst intensity classification based on the radiated energy with damage intensity at Jinping II hydropower station, China. Rock Mech. Rock Eng., 2013, 48(1), 289-303.
- Cai M., Champaigne D. Influence of bolt-grout bonding on MCB conebolt performance. International Journal of Rock Mechanics & Mining Sciences, 49, 2012, pp. 65-175.
- Jager A. J. Two new support units for the control of rock burst damage. Rock Support in Mining and Underground Construction, 1992, pp. 621-31.
- Tannant D. D., Buss B. W. Yielding rockbolt anchors for high convergence or rock burst conditions. In: Proceedings of the 47th Canadian Geotechnical Conference, 1994.
- Simser B., Andrieus P., Gaudreau D. Rock burst support at Noranda’s Brunswick Mine, Bathurst, New Brunswick. In: Hammah R, Bawden W, Curran J, Telesnicki M, editors. Proc NARMS 2002, vol. 1, University of Toronto Press, 2002, pp. 805-13.
- Manchao H., Chen L., Weili G., L.R.S., Shenglin L. Dynamic tests for a Constant-Resistance-Large-Deformation bolt using a modified SHTB system. Tunnelling and Underground Space Technology, 64, 2017, pp. 103-116.
- He M. C., Gong W., Wang J., Qi P., Tao Z., Du S. Development of a novel energy-absorbing bolt with extraordinarily large elongation and constant resistance. Int. J. Rock Mech. Min. Sci., 67, 2014, pp. 29-42.
- He M., Miao J., Li D., Wang C. Experimental study on rock burst processes of granite specimen at great depth. Chinese Journal of Rock Mechanics and Engineering, 2007, 26(5), pp. 865-876.