Селективное восстановление и пирометаллургическое извлечение железа из шламов медеплавильного производства
Автор: Потапов Кирилл Олегович, Рощин Василий Ефимович
Журнал: Вестник Южно-Уральского государственного университета. Серия: Металлургия @vestnik-susu-metallurgy
Статья в выпуске: 3 т.14, 2014 года.
Бесплатный доступ
Производство меди связано с образованием большого количества шлака, который в связи с повышенным содержанием в нем оксидов железа практически не используется в строительной промышленности. Извлечение железа из этих отходов позволит переработать накопившиеся шлаковые отвалы с получением двух товарных продуктов: сплавов на основе железа и строительного песка. Объектом исследования являлся шлак карабашского медеплавильного комбината после флотационного обезмеживания. Установлена принципиальная возможность твёрдофазного углеродотермического восстановления железа из легкоплавких шлаков медеплавильного производства с использованием в качестве восстановителя низкосортного энергетического угля и извлечения железа разделительной плавкой. Рассмотрены фазовый и химический составы шлаков, установлена температура начала плавления, установлен гранулометрический состав. Проведены эксперименты по восстановлению железа в печи Таммана двумя вариантами:1) восстановление железа из шлама кусковым углем; 2) восстановление брикетированных образцов, изготовленных из шлама и угля фракции менее 1 мм. Описаны особенности процесса при восстановлении по обоим вариантам. Степень металлизации составляет порядка 90 %. Восстановленный материал при помощи плавления разделяли на сплав на основе железа в виде компактного металла и шлак. В зависимости от условий разделительной плавки (температура, время, вид тигля) можно получить сталь,чугун или ферросилиций. Получаемый металл содержит около 1 % меди, содержание серы меняется от 0,1 до 2 % в зависимости от получаемого сплава. Получаемый при этом оксидный остаток в виде шлака с пониженным содержанием оксидов железа пригоден для использования в промышленности строительных материалов.
Твердофазное восстановление, шлаки медеплавильного производства, извлечение железа
Короткий адрес: https://sciup.org/147156881
IDR: 147156881
Текст научной статьи Селективное восстановление и пирометаллургическое извлечение железа из шламов медеплавильного производства
В районах с развитой цветной металлургией отвалы занимают сотни гектаров земли, в том числе плодородной. Только в окрестностях г. Карабаш Челябинской области скопилось около 30 млн т отвальных промышленных отходов, содержащих около 40 % железа. На содержание отвальных хозяйств ежегодно расходуются большие средства. Большой объём шлаков определяет актуальность проблемы их рационального использования. Хранение таких отходов требует огромных площадей и неблагоприятным образом сказывается на экологии. Их использование в строительной промышленности приводит не только к безвозвратной потере ценных компонентов, но и затруднено в связи с наличием в них оксидов тяжелых металлов.
Исследованиями комплексной переработки техногенных отходов, в том числе шлаков медного производства, на протяжении многих лет занимались не только ученые России, но и других стран. Однако ни одна технология комплексной переработки шлаков не была реализована. В связи с этим разработка способов использования отвальных шламов и шлаков, бедных по содержанию железа, является актуальной экономической и экологической задачей [1].
Целью данной работы является оценка технологических возможностей переработки железосодержащих техногенных отходов цветной металлургии для повышения эффективности металлургического производства и улучшения экологиче- ской обстановки вблизи медеплавильных предприятий.
Шлам от производства меди представляет собой порошок тонкой фракции. Он является относительно легкоплавким – температура начала плавления составляет примерно 1060 °С. В шламе присутствуют металлические частицы, содержащие медь, железо, сурьму и олово. Оксидная фаза представлена частицами железной шпинели и сложными силикатами, содержащими железо. В шпинели содержится относительно много серы, а в силикатной фазе – примесей цветных металлов. С учетом данных рентгеноструктурного анализа основные фазы шлама: фаялит 2FeO·SiO 2 , магнетит Fe 3 O 4 и пироксен СаFeSi 2 O 6 (рис. 1, а). Сера связана в сульфиды, содержащие медь, цинк, свинец, олово и сурьму. Для определения среднего состава исходный шлам расплавили и закалили (рис. 1, б). В табл. 1 приведены результаты исследований химического и минералогического составов шлама.
Технология низкотемпературного твердофазного ( Т = 900…1050 °С) восстановления железа является более рациональной в сравнении с технологиями извлечения железа с плавлением всех исходных материалов. Твердофазное восстановление позволяет использовать в качестве восстановителя низкокачественный энергетический уголь, при этом металл не загрязняется углеродом и вредными примесями, содержащимися в энергетическом угле, в частности, серой. Поэтому селективно вос-
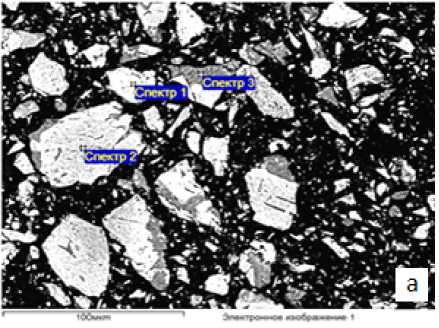
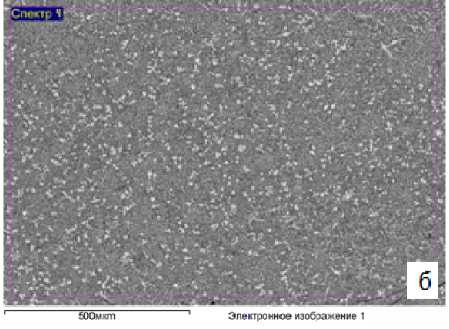
Рис. 1. Основные фазы исходного шлама (а) и вид шлама после расплавления и закалки (б)
Таблица 1
Химический и минеральный составы шлама
Экс пе рим енты пров оди л и по ра не е изл ож е нной методике [2, 3].
Восстановление проводили в печи Таммана, в качестве восстановителя использовали коркинский уголь. Температуру восстановления выбирали на 30…80 градусов ниже температуры начала плавления шлама. Полученные образцы заливали в эпоксидную смолу для изготовления микрошлифов. Шлиф изучали на оптических и на скани- рующем электронном микроскопе JEOL-7001F, снабжённом микрорентгеноспектральным анализатором. Рентгеноструктурный анализ проводили на дифрактометре ДРОН-4.
После выдержки при 980 °С в течение 1 ч появились корольки железа размером 5…20 мкм (рис. 2, белые вкрапления) с примесью до 2 % меди, но чистых по сере (< 0,1 %). При этом в шламе исчез магнетит, железо которого восстанавливалось в первую очередь. Химический состав восстановленного материала приведен в табл. 2.
После расплавления подвергнутого восстановительному обжигу шлама получили компактный слиток металла, содержащего 95 % Fe, 2 % Cu, 2 % S и шлак. Чистые по сере корольки металла

а)
б)
Рис. 2. Результаты восстановления в порошке при 980 °С в течение 1 ч (а) и в брикете при 1020 °С в течение 2 ч (б)
Таблица 2
Химический состав (мас. %) восстановленного материала
Дл я у с коре н ия проце с с а в о с с та новл е н ия про в оди л и брикетиров ание ш ла м а с уг л ем фра кц и и ме не е 1 м м . Из уче н ие бри к е тиров а н ны х обра з цов пока за л о, что с корос ть в ос ста новл е н ия в оз ра с та е т в 3… 4 ра з а , и при в ы де рж к е 1 ч и Т = 1030 °С со де рж ан и е ж е л е з а в окс и дн ой ча с т и сни ж а е тся до 10 %, а размер корольков с ос та в л яет 20… 50 м км . Уд в оен и е п родолжител ь н ос т и в ыде рж ки не пр и в ел о к сн иж ени ю с оде рж ан ия ж е л е з а в оксид ной ф а з е , что с в и де тел ьс тву ет о том , что проце с с в о сстановления остановился.
Отличие брикетированных образцов от порошковых проявилось при нагреве в корундовом тигле до температуры плавления для разделения на металл и шлак после восстановления. Во время такого нагрева до 1500 °С происходит дальнейший процесс восстановления, причем весьма активно, так что содержание железа в шлаке снижается до величины менее 1 %, а в металле появляется 0,7 % кремния (табл. 3 и 4). Возможность процесса восстановления здесь обусловливается наличем мелких частиц угля, оставшихся от первичного восстановления, а также появлением жидкой фазы, через которую может уходить газ.
На рис. 3 и 4 приведены результаты восстановления при 1020 °С (2 ч) в брикете с последующим нагревом до расплавления и разделения на металл и шлак в алундовом тигле.
При плавлении восстановленных брикетов в графитовом тигле вместо стали получается чугун, а при определенных условиях – ферросилиций с содержанием кремния 10…13 % (рис. 5). По мере увеличения степени восстановления и переходе от стали к чугуну, а затем к ферросилицию значительно снижается содержание серы в металле. Если в стали содержание серы было 2 %, то в чугуне примерно 1 %, а в ферросилиции с содержанием 12 % – 0,1 % (табл. 5). Сера может быть удалена при обработке жидкого чугуна. Медь практически
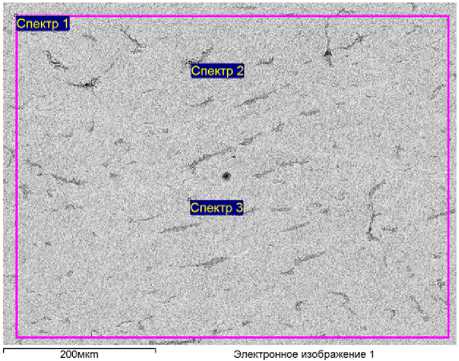
Рис. 3. Металл слитка
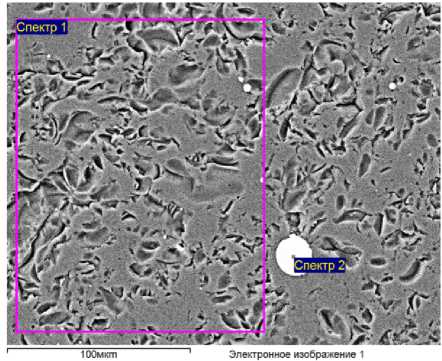
Рис. 4. Шлак слитка
Таблица 3
Таблица 4
Состав металла
Si |
S |
Fe |
Cu |
|
1 |
0,7 |
1,2 |
97, 1 |
1,0 |
2 |
0,1 |
23,0 |
72, 7 |
4,2 |
3 |
0,7 |
0,0 |
98, 5 |
0,8 |
Состав шлака
O |
Mg |
Al |
Si |
S |
Ca |
Fe |
Cu |
|
1 |
50 |
3,1 |
8,0 |
24,7 |
0,1 |
13,4 |
0,8 |
0,1 |
2 |
0 |
0,0 |
0,0 |
0,3 |
0,0 |
0,3 |
98,9 |
0,5 |
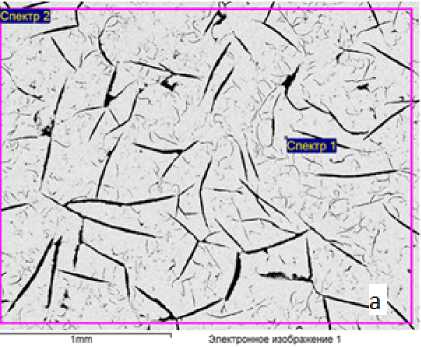
Рис. 5. Слитки чугуна (а) и ферросилиция (б) после расплавления восстановленных брикетов в графитовом тигле, мас. %
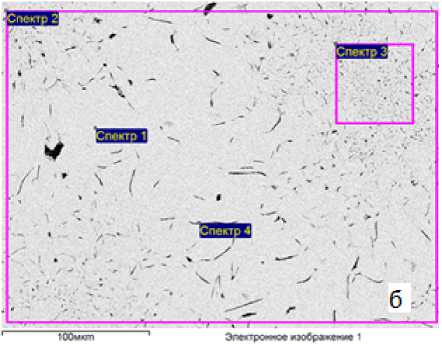
Таблица 5
Химический состав (мас. %) полученных вариантов слитков
Заключение
Твердофазное восстановление железа из шлаков медеплавильного производства с использованием в качестве восстановителя угля коркинского месторождения возможно при температуре около 1000 °С. Брикетирование ускоряет процесс в несколько раз (заканчивается за 1…2 ч). При этом металлизуется до 90 % железа. Остальное железо практически полностью восстанавливается при плавлении брикета, подвергнутого восстановительному обжигу.
В зависимости от условий плавки можно получить сталь, чугун, ферросилиций. Металл содержит 1 % меди, содержание серы в стали около 2 %, в чугуне около 1 %, а в ферросилиции с содержанием кремния 12 % – около 0,1 %.
После твердофазного восстановления и жидкофазного разделения содержание оксидов тяжелых металлов в получаемом шлаке снижается, что позволяет использовать его в качестве наполнителей для бетонов в строительной промышленности.
Список литературы Селективное восстановление и пирометаллургическое извлечение железа из шламов медеплавильного производства
- Санакулов, К.С. Переработка шлаков медного производства/К.С. Санакулов, А.С. Хасанов. -Ташкент: Фан. -2007. -238 с.
- Потапов, К.О. Твердофазное восстановление и извлечение железа из шлама медеплавильного производства/К.О. Потапов, В.Д. Поволоцкий, В.Е. Рощин//Современные проблемы электрометаллургии стали: материалы XV междунар. науч. конф.: в 2 ч. -Челябинск: ЮУрГУ. -2013.
- Рощин, В.Е. Физика химических реакций окисления и восстановления металлов в твердой фазе/В.Е. Рощин, А.В. Рощин//Современные металлические материалы и технологии (СММТ’2013): тр. междунар. науч.-техн. конф. -СПб.: Политехн. ун-т. -2013. -С. 225-231.