Simulation of a continuous ingots structure formation process
Автор: Kovalenko Oleg A., Dozhdikov Vladimir I.
Журнал: Журнал Сибирского федерального университета. Серия: Техника и технологии @technologies-sfu
Статья в выпуске: 3 т.10, 2017 года.
Бесплатный доступ
The presented results demonstrate the possibility of mathematical complex model in research of the temperature characteristics pattern changes in polymorphic transformations, isotherms of liquidus and solidus, and other parameters depending on the cooling conditions of the ingot. Shown the possibility of predicting parameters of a continuous ingot microstructure (distance between dendrites, size of the austenite and ferrite grains). Were made microstructure parameter calculations of the continuous steel ignot containing 0.17 % C, 0.62 % Si, 1.4 % Mn at various secondary cooling modes.
Continuous casting of steel, dendrite, austenite, grain size, structure formation
Короткий адрес: https://sciup.org/146115206
IDR: 146115206 | DOI: 10.17516/1999-494X-2017-10-3-346-351
Текст научной статьи Simulation of a continuous ingots structure formation process
The development of measurements aimed at improving the quality of continuously cast billets involves the use of mathematical modeling of the ingot formation. This can be achieved by minimizing the defects formed during solidification of the ingot at continuous casting machine (CC machine), and by ongoing research of metal structure management capabilities.
Results and discussion
As a tool for implementing this approach, a mathematical model can be used to determine the temperature field and structure parameters of a continuous ingot [1, 2]. Features of this model can be seen quite clearly from the results of the analysis. For example, formation process of a continuous ingot steel containing 0.17 % C, 0.62 % Si, 1.4 % Mn with various secondary cooling modes. The main parameters used in computational experiments are: casting steel temperature – 1535 °C, casting speed – 1 m/min, ingot thickness – 0, 250 m.
Fig. 1 shows one of the modules interface of the program used to determine liquidus and solidus temperatures according to the method used in the model [1]. For the case in question, they were as follows: – 1514.28 °C liquidus, solidus – 1479.76 °C. This module also determines the temperature of polymorphic transformations.
Changes in the surface temperature of the ingot in crystallizer were set using the experimental values of the heat flux through crystallizer walls [3] (Fig. 2).
Boundary conditions of changes in surface temperature functions at the secondary cooling zone over time were used as basic characteristics of the secondary cooling mode [4]:
T T ) = & - Т к ) .
1 -
Т коо

+ Т к ,
T H – T K – temperature difference at the beginning of the cooling process and at the end; °C; τ kon – cooling time of the ingot; n, m, c – parameters defining the type of dependence T (τ).
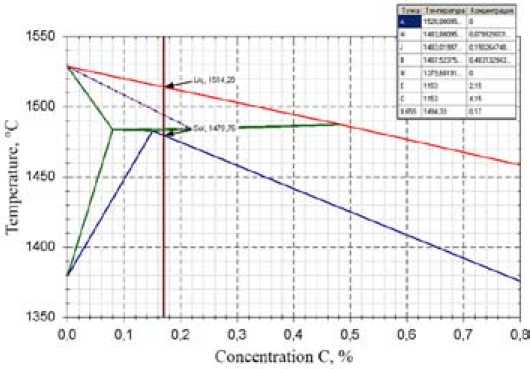
Fig. 1. The module interface of the program for the calculation of the temperature of the liquidus and solidus
The effect of secondary cooling intensity on the parameters of the ingot was examined by comparing the simulation of the formation process results of a continuous ingot using two cooling modes: intense and soft. For the first mode ingot surface after exiting the crystallizer was quenched to 700 °C followed by cooling to 600 °C. In the second mode, the surface temperature decreased gradually up to 600 ° as soon as the ingot was taken out of the crystallizer (Fig. 3).
The results of computational experiments are presented in Fig. 4. A characteristic feature of the first mode is smaller length zone of molten steel, two-phase region, of the growth zone of an austenitic-ferritic pearlitic structure. These results also follow the change in the cross section of the ingot structure as shown, for example, for coordinates processing of 10 meters from the axis of the meniscus (Fig. 5). So at a distance of 5 mm from the surface of ingot billet ferrite-pearlite structure already formed with a size of 21.36 microns ferrite grains at the surface and 26.93 mm at a distance of 5 mm. Deeper you can find austenite grains and ferritic grains formed at their boundaries. Austenite grain size at that portion (5-18 mm from the surface) is 1250-1480 microns. At a distance of 18-95 mm from the ingot surface is a zone with austenitic structure, the grain size gradually increases to 2368 micron at a distance of 60 mm
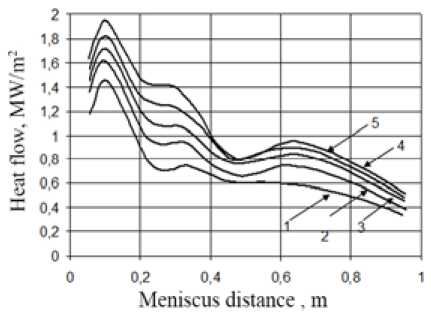
Fig. 2. The density distribution of the heat flow adjustment in the wide side of the crystallizers at a distance of 0.16 m from its center [2] (Pulling speed: 1 – 0.4 m/min, 2 – 0.6 m/min, 3 – 0.8 m/min, 4 – 1.0 m/min, 5-1,2 m/min)
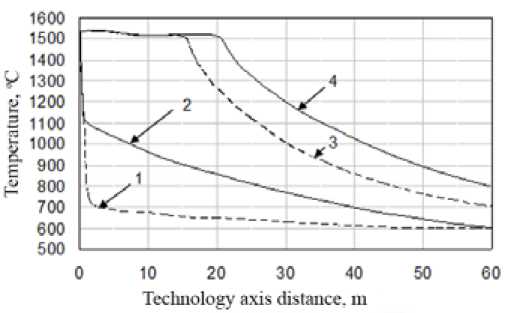
Fig. 3. Changes of the ingot temperature: 1, 3 – ingot surface and center temperature for the 1st cooling mode; 2, 4 – ingot surface and center temperature for the 2nd cooling mode
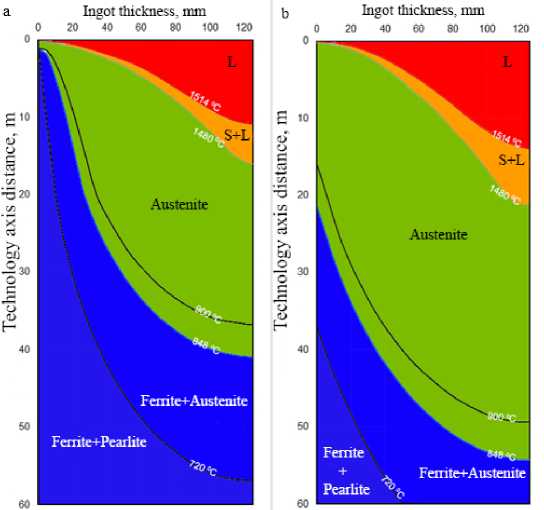
Fig. 4. Basic forming parameters of a continuous ingot: a – mode 1; b – mode 2
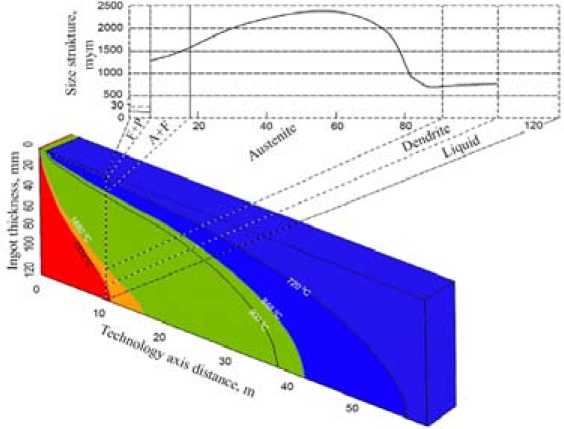
Fig. 5. Ingot change of structure parameters with thickness for the second mode and a 95 mm – 750 mm. The sharp increase in the grain size to 60 mm is associated with the processes of recrystallization occurring at high temperatures. Two-phase zone plot: 95-110 mm is characterized with a dendritic structure by dispersion of 700-745 microns, respectively.
The change of the microstructure of the ingot along the continuous casting machine for the first mode shown in Fig. 6.
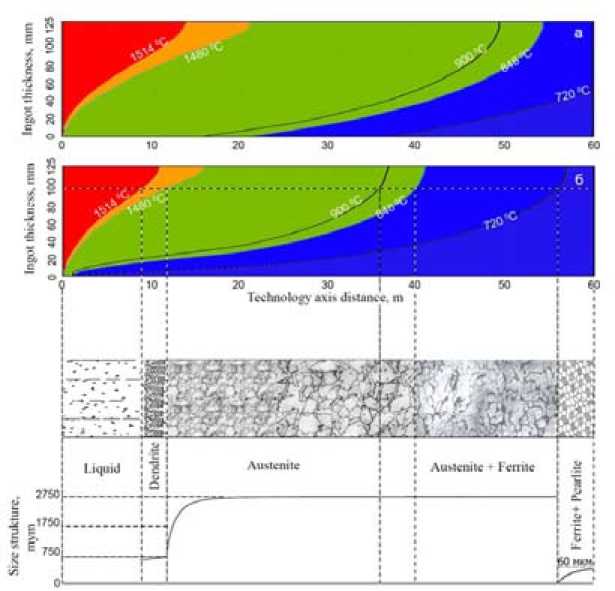
Fig. 6. Changing of the structure parameters along a vertical cross section of the ingot at a distance of 100 mm from the surface for the first cooling mode
Thus, at a distance of 100 mm from the surface of the ingot, the liquid phase is maintained up to 9.55 m. Then there is the field of liquid-solid phase, were the formation of a dendritic structure happens, which has an impact on the size of the austenite grains, formed below the peritectic transformation , temperature. For the current regime at a distance of 100 mm from the surface of the ingot, magnitude of interdendritic distance at the beginning of austenitic structure formation was 750 microns. Further, this size taken as an initial austenite grain in simulation during growth of austenite. The plot 11.8 m – 40.1 m in the technology axis – an area of austenitic structure. This rapid growth of austenite grains occurs to a mark of 19.7 m of the technology axis, further cooling does not significantly affect the increase in grain size. Below the AC3 temperature of the investigated steel (848 °C), which corresponds to around 40.1 m, ferrite released by the boundaries of the austenite grain. The final stage of steel microstructure formation is eutectoid transformation of austenite in the ferrite-cementite mix at 720 °C (56 m elevation). Ferrite grain size of the final structure in a given section is 60 microns.
Conclusions
The presented results demonstrate the possibility of mathematical complex model in research of the temperature characteristics pattern changes in polymorphic transformations, isotherms of liquidus and solidus, and other parameters depending on the cooling conditions of the ingot. All this makes it possible to obtain the microstructure characteristics, and with presence of contact functions at different points in the cross section and the mechanical properties of the ingot at a particular time. An extensive – 350 – set of input data (structural and technological parameters of casting, steel thermal parameters) used in the implemented model, allow user to get a set of quality characteristics of the structure and properties of continuous ingot needed to select the optimal conditions for the formation of the ingot in the casting of steel on a particular CC-machine.
Список литературы Simulation of a continuous ingots structure formation process
- Коваленко О.А., Дождиков В.И. Влияние параметров процесса формирования структуры непрерывного слитка на образование трещин. Научно-технический вестник Поволжья. Казань. 2012, 6, 271-274
- Коваленко О.А. Информационная система прогнозирования микроструктуры непрерывнолитого слитка. Всероссийский конкурс научно-исследовательских работ студентов и аспирантов в области информатики и информационных технологий: сб. науч. работ: в 3 т. Белгород: ИД «Белгород», 2012, 3, 245-250
- Дождиков В.И. Теплофизические особенности формирования непрерывного слитка в кристаллизаторе МНЛЗ. Липецк: ЛГТУ, 2007. 184 с
- Порядин С.В., Дождиков В.И. Определение параметров процесса управления охлаждением непрерывного слитка. Образование, наука, производство и управление сб. науч. и научно-методических. докладов всероссийской. Старый Оскол: СТИ НИТУ МИСиС, 2011, 1, 5963