Синтез красного железооксидного пигмента на основе конвертерного сталеплавильного шлака для строительной индустрии
Автор: Рузавин Андрей Андреевич
Рубрика: Строительные материалы и изделия
Статья в выпуске: 4 т.20, 2020 года.
Бесплатный доступ
В приведенной статье представлен способ получения красного железооксидного пигмента с применением в качестве железосодержащего основного компонента конвертерного сталеплавильного шлака без прохождения магнитной сепарации. Для осуществления данной задачи шлак подвергался предварительным операциям обработки с целью получения порошкообразного материала и удаления загрязняющих примесей, растворением железа и его соединений серной кислотой с образованием раствора сульфата железа (II) и дальнейшим термическим разложением при температуре 650 °С (copperas red process). Установлено, что полученный предложенным способом железооксидный пигмент состоит на 93-95 % из гематита α-Fe2O3, обладает высоким качеством и красящими характеристиками, предельно низким содержанием нежелательных веществ, ухудшающих его свойства. Фосфорный ангидрид (Р2О5), входивший в состав шлака, оказывал благоприятное влияние на процесс синтеза пигмента как добавка-минерализатор. Степени извлечения железа, кальция и магния при данном способе весьма высоки - 97, 99,3 и 97 % соответственно, что свидетельствует о высокой эффективности этого метода. Данное исследование имеет большое значение для строительной отрасли, особенно для области декоративных бетонов и растворов.
Железооксидные пигменты, свойства пигментов, сталеплавильный шлак, синтез, переработка промышленных отходов
Короткий адрес: https://sciup.org/147233725
IDR: 147233725 | DOI: 10.14529/build200403
Текст научной статьи Синтез красного железооксидного пигмента на основе конвертерного сталеплавильного шлака для строительной индустрии
Поиск возможных путей переработки промышленных отходов – одна из важнейших технических задач современной науки. Особенно данный вопрос касается шлаков, шламов, зол и прочих видов побочных продуктов различных производств, загрязняющих огромные земельные площади созданием большого количества отвалов, терриконов и отстойников. Наиболее активно решением этой проблемы занимаются строительная, химическая и металлургическая отрасли. Однако на текущий момент времени недостаточно изучены все возможные способы утилизации этих отходов.
Одним из достаточно молодых направлений в утилизации промышленных отходов является синтез железооксидных пигментов. Для получения качественных пигментов требуются отходы, содержащие как можно большее количество железа и его соединений и минимальное содержание нежелательных примесей. Поэтому в первую очередь подверглась изучению возможности переработки окалина, образующаяся при прокатке стали, состоящая на 70–74 % по массе из железа. Применяемая окалина в одном случае представляла собой чистый зернистый материал, требовавший только помола, а во втором случае – осадок из вторичных отстойников, загрязненный нефтепродуктами, поэтому в процессе синтеза подвергался многостадийной фильтрации. В обоих случаях применялась в качестве растворителя серная ки- слота, а синтез пигментов шел по направлениям термического разложения Fe2(SO4)3 и гидротермальной обработки смеси NaOH и Fe(OH)2, полученного из окисленного аммиаком (NH3·H2O) раствора Fe2(SO4)3. Полученные пигменты отличались высоким качеством (содержание α-Fe2O3в пигментах 95,3 и 98,7 % соответственно), сопоставимым с коммерческими образцами, произведенными по традиционной технологии [1, 2].
Другая вариация синтеза железооксидных пигментов включала применение в качестве исходных материалов промышленных шламов, имеющих в своем составе железо и его производные, количественно значительно изменяющиеся в широких пределах от 10 до 80 % для различных промышленных комплексов. Данные шламы, представляющие собой взвешенные в воде мелкодисперсные частицы, являются материалами, не требующими дополнительной физической обработки. Однако некоторые шламы необходимо подвергать нейтрализации или другим химическим процессам для дальнейшего применения. Шламы могут выступать в качестве зародышей для роста кристаллов взамен готовых, использующихся в классических методах, или применяться как исходное железосодержащее сырье; малая величина железа в шламе компенсируется введением железного металлолома в ходе синтеза. Например, для синтеза красного железооксидного пигмента шлам смешивался с 60 % H2SO4 в соотношении 1:1,2 с дальнейшим прокаливанием при 800 °С в течение 2 часов. Еще один пример: красный кислый шлам глиноземного производства (рН = 3) проходил нейтрализацию раствором NaOH до рН = 9 для получения кристаллических затравок, далее его смешивали с 98 % H2SO4 и железным скрапом до рН = 4 с образованием FeSO4·7H2O при непрерывной подаче воздуха с последующим выпадением в осадок оксида железа; осадок собирали, промывали, фильтровали, сушили и размалывали. Красные железооксидные пигменты, синтезированные с участием шламов, имели содержание основного оксида α-Fe2O3 более 95 %, что ставило их в один уровень с высококачественными немецкими образцами; также достигался положительный экономический эффект в уменьшении стоимости процесса на 30 % [3–5].
Наименее исследованной областью утилизации промышленных отходов для получения железооксидных пигментов является применение в качестве основы технического камня, а именно сталеплавильных шлаков, не нашедших в современной практике массовой технологии переработки. Подавляющее большинство шлаков образуются при выплавке стали в конвертерах. В конвертерах в процессе перехода железа в сталь часть железа не очищается и не конвертируется в сталь, а включается в состав шлака. Поэтому содержание оксидов железа (FeO) в данном виде шлака может достигать 38 %. Кроме FeO шлаки содержат высшие оксиды железа Fe 3 O 4 и Fe 2 O 3 . Сера в шлаках находится в виде сульфидов или сульфатов Са, Мn и Fe. Оксиды, входящие в шлак, разделяют на три группы: кислотные (SiO 2 , P 2 O 5 , SO 2 , SO 3 ), основные (CaO, MgO, FeO), амфотерные (Аl2O3). При условии сохранения выплавки определенных видов стали, а также работы на руде одного месторождения можно достичь идентичного состава шлака от плавки к плавке – это одно из преимуществ конвертерного способа [6, 7].
Минералогический состав конвертерных шлаков зависит от химического состава, а также от скорости остывания. В отличие от доменного гранулированного шлака, подвергающегося резкому охлаждению, в результате чего образуется аморфная структура с большим количеством стекла, сталеплавильные шлаки преимущественно охлаждаются в естественных условиях, имея также низкое содержание кремнезема, что выражается в их высокой закристаллизованности. Резкое охлаждение не помогает решить эту проблему. Для шлаков характерен следующий минералогический состав: вюстит (Fe 1-x-y ,Mg x ,Mn y )O z , двухкальциевый силикат (2СаО·SiO 2 ), двухкальциевый феррит (2CaO·Fe 2 O 3 ), мервинит (3CaO·MgO·2SiO 2 ), оливин (2MgO·2FeO·SiO 2 ), периклаз (MgO), свободная СаО, редко трехкальциевый силикат (3CaO·SiO 2 ) [6–9].
Из вышесказанного можно заключить, что сталеплавильные шлаки могут быть исходным железосодержащим сырьем, подходящим для производства пигментов. Невысокий процент железа не является серьезным препятствием, так как в работе [10] была показана возможность получения качественных пигментов из сырья с содержанием Feвсего 16,1 %. Поэтому, принимая во внимание этот факт, а также большое количество сторонних примесей, главным маршрутом выполнения синтеза будет использование методов разделения и концентрирования. Следует отметить еще один недостаток при работе со шлаком – необходимость тонкого размола этого отхода для увеличения площади контакта и ускорения реакций в ходе синтеза пигментов. Несмотря на данные отрицательные моменты, все же в мировой практике предпринимались попытки получения пигментов на основе сталеплавильных шлаков. Так, например, для синтеза использовалась магнитная часть шлака (общее содержание Fe 32,61 %), которая размалывалась совместно с каменным углем (soft coal) в количестве 1 % от массы шлака, а затем подвергалась термообработке в тигле при температурном от 500 до 800 °С и временном от 10 до 50 мин интервалах. Полученный пигмент обладал низкой красящей способностью (56 г/м2), вероятно, по причине отсутствия первичной химической подготовки по очищению шлака от посторонних примесей. В другом исследовании сталеплавильный шлак (общее содержание Fe 33–45 %) тонко размалывали, очищали от примесей кальция с помощью уксусной кислоты и направляли на гидротермальную обработку с высоким давлением в 300 бар и температурой 300–500 °С; данные о свойствах пигмента отсутствуют. В обоих исследованиях проводили синтез черного железооксидного пигмента [11–13].
Наиболее рационально и экономически выгоднее производить из шлака красные железооксидные пигменты, так как доля их потребления в мире составляет 46 % от объема всех выпускаемых железооксидных пигментов и спрос на них неуклонно растет. Кроме того, красный железооксидный пигмент (минерал гематитα-Fe 2 O 3 ) – нерастворимое, наиболее стабильное и устойчивое соединение из всех оксидов и гидроксидов железа – инертно, поэтому стойко к колебаниям рН среды и погодным изменениям, обладает термостойкостью на воздухе вплоть до 1100 °С. Строительная индустрия потребляет около половины (22 %) производимых красных железооксидных пигментов, а с учетом лакокрасочных материалов – почти три четверти. Поэтому в данном изыскании будет рассмотрен синтез именно этого вида пигментов [14–16].
Цель работы: синтезирование красного железооксидного пигмента на основе сталеплавильного шлака конвертерного способа производства.
Задачи: оценить потенциал сталеплавильного шлакаконвертерного способа производства как исходного сырья для получения красного железо- оксидного пигмента и определить характеристики получаемого пигмента.
Материалы:
– железосодержащий компонент: сталеплавильный шлак конвертерного способа производства в состоянии поставки (без прохождения магнитной сепарации); химический состав и некоторые характеристики шлака приведены в табл. 1 и табл. 2 соответственно, внешний вид шлака – на рис. 1;
-
– кислота уксусная ХЧ, соответствует ГОСТ 61-75, разбавленная до 35%-ной концентрации;
-
– кислота серная ХЧ, соответствует ГОСТ 4204-77, разбавленная до 25%-ной концентрации;
-
– гидроксид натрия ХЧ, соответствует ГОСТ 4328-77;
-
– вода водопроводная очищенная, соответствует ГОСТ 2874-82.
На первой стадии определялись минералогический качественный и количественный составы шлака с применением РФА на дифрактометре Ri-gaku Ultima IV с длиной волны 1,54056 Å Cu Kα1, СЭМ и ЭДС на растровом электронном микроскопе JEOL JSM-7001F. Размол шлака проводился в лабораторной шаровой мельнице. Синтез проходил в реакторе, снабженном мешалкой со скоростью вращения 100 об/мин. Для отделения нежелательных примесей (Ca и Mg) и максимально полного извлечения железа из шлака применялись химические методы разделения и концентрирования. В основе получения пигмента стоял процесс термического разложения сульфата железа (II) при температуре выше 600 °С (Copperas red process). Для термической обработки применялась муфельная печь с вытяжкой Снол-6/10. Минералогический состав и внешний вид частиц готового пигмента определялись на приборах, применявшихся на первой стадии. Укрывистость и маслоемкость пигмента устанавливали по ГОСТ 8784-75 «Материалы лакокрасочные. Методы определения укры-вистости» по визуальному методу и ГОСТ 21119.8-75 «Общие методы испытаний пигментов и наполнителей. Определение маслоемкости» по методу с помощью стеклянной палочки; истинную плотность – по пикнометрическому способу, ще-лочестойкость – в 5%-ном растворе NaOH на протяжении 24 часов со сравнением с исходными образцами, площадь удельной поверхности – на приборе ПСХ 12.
Таблица 1
Химический состав шлака
СаО |
SiO 2 |
Al 2 O 3 |
Fe 2 O 3 |
MgO |
Прочее |
44,26 |
12,5 |
0,57 |
34,19 |
7,04 |
1,44 |
Таблица 2
Краткая характеристика шлака
Происхождение шлака |
ПАО «ЧМК», г. Челябинск |
Форма |
Смесь зерен различной неправильной формы размером 1–40 мм |
Цвет |
От темно-серого до черного |
Истинная плотность, кг/м3 |
3600 |
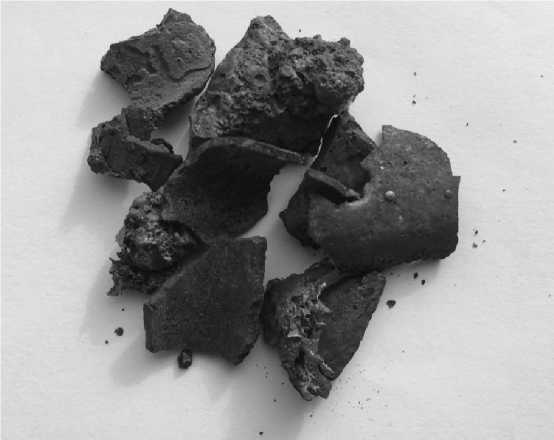
Рис. 1. Внешний вид сталеплавильного шлака
Результаты исследования
Шлак размалывался до максимально возможной удельной поверхности (для данного материала) – 3200 см2/г (рис. 2). Минералогический состав сталеплавильного шлака представлен следующими минералами: вюстит FeO – 18,6 %, сребродолскит
Ca2Fe2O5 – 34 %, ларнит Ca2SiO4 – 35,3 %, железо Fe – 5,9 %, магнетит Fe3O4 – 6,2 %; общее содержание Fe (данные ЭДС) – 18,77 % (табл. 3). Рентгенограмма дана на рис. 3; качественно минералогический состав шлака не изменялся, но изменялся количественно.
Синтез пигмента шел по схеме, представленной на рис. 4. Массовые отношения реаген- тов (взяты к массе исходного шлакового порошка), температуры и время синтеза – все данные параметры установлены эмпирически. Излишне высокую вязкость смеси снижали введением дополнительных порций воды; перемешивание в реакторе происходило во время взаимодействия веществ и завершалось по его окончании. Для извлечения нежелательных примесей Ca и Mg, снижающих красящую способность и качество пигмента, в реактор к шлаку загружалась уксусная кислота 35%-ной концентрации. В ходе этого процесса в раствор полностью переходили Ca, Mg и частично Fe;
Таблица 3
Поэлементный состав шлака по данным ЭДС
Массовые доли |
O |
Mg |
Al |
Si |
P |
S |
Ca |
элементов, % |
35,8 |
3,31 |
0,42 |
5,04 |
0,87 |
0,06 |
30 |
Массовые доли |
Ti |
V |
Cr |
Мn |
Fe |
Сумма |
|
элементов, % |
1,14 |
1,47 |
0,47 |
2,64 |
18,77 |
100 |
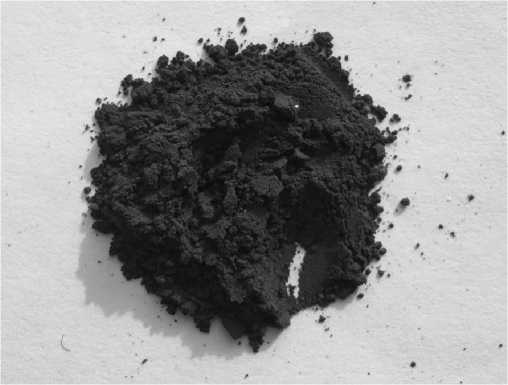
Рис. 2. Внешний вид шлакового порошка
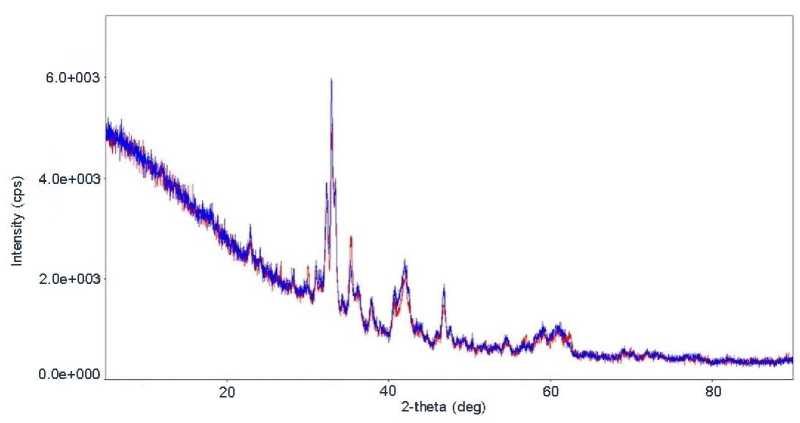
Рис. 3. Рентгенограмма сталеплавильного шлака
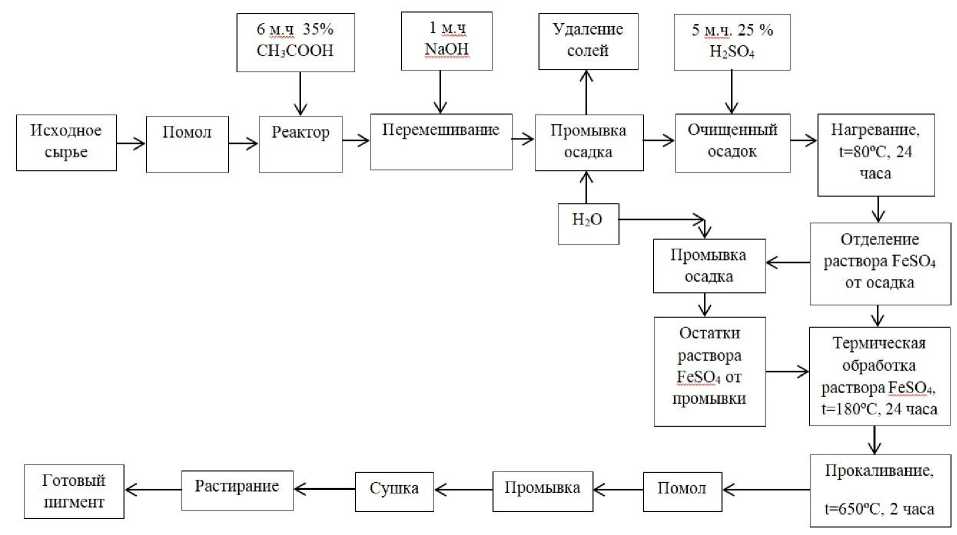
Рис. 4. Технологическая схема синтеза красного железооксидного пигмента
рН раствора 3. Имели место реакции:
(CaO, MgO) + 2CH 3 COOH →
→(Ca, Mg)CH 3 COOH + H 2 O, (1)
Fe + 2CH 3 COOH → Fe(CH 3 COOH) 2 + H 2 ↑. (2)
Отделение железа в растворе от уксусных солей кальция и магния проходило с участием NaOH и выпадением осадка в форме Fe(OH) 2 по реакции:
Fe(CH 3 COOH) 2 + 2NaOH →
→ 2NaCH 3 COOH + Fe(OH) 2 ↓. (3)
Водородный показатель раствора рН с 3 повышался до 8–9. В результате этих действий произошло максимально полное разделение нежелательных примесей, переведенных в раствор, от железа и его соединений, ушедших в осадок.
Для ускорения процесса синтеза осадок не фильтровали, а промывали 5–7 раз очищенной водой в самом реакторе; первичный раствор солей ацетатов натрия, магния и кальция удаляли из реактора сливным патрубком. Промывание осуществляли до значения рН = 6. Далее к осадку добавляли 25%-ный раствор H 2 SO 4 , взятой с небольшим избытком с поправкой на колебание состава шлака; рН падал до 1. Реакция проходила в течение 24 часов при температуре 80 ºС:
(Fe,FeO,Fe(OH) 2 , Fe 3 O 4 ) + H 2 SO 4 →
→ Fe(SO 4 )‧nH 2 O. (4)
Водный раствор сульфата железа (II) так же, как и соли кальция, магния и натрия, удаляли сливным патрубком, промывку отработанного осадка проводили на месте – в реакторе – 5–6 раз до установления рН = 5–6, остатки от промывания, содержащие небольшие количества раствора сульфата железа, совмещали с первичным раствором этого соединения, помещали в термо- и кислотостойкую емкость и отправляли в муфельную печь на термообработку при температуре 180 °С в течение 24 часов с целью дегидратации раствора и получения твердого продукта. Далее температуру ступенчато повышали со скоростью 10 °С/мин до значения в 650 °С с прохождением изотермической выдержки при заданном режиме в течение 2 часов в окислительной воздушной среде:
Fe(SO 4 )‧nH 2 O → Fe(SO 4 ) + nH 2 O↑, (5) 4Fe(SO 4 ) + O 2 → 2Fe 2 O 3 + 4SO 3 ↑. (6)
Полученный материал размалывали в шаровой мельнице, промывали, сушили и растирали в готовый железооксидный пигмент (рис. 5).
По данным РФА минералогический состав пигмента следующий: гематит α-Fe2O3 – 93–95 %, псевдобрукит Fe 2 TiO 5 – 5–7 % (рис. 6); пики отчетливые, острые, высокой интенсивности, что говорит о наличии хорошо закристаллизованного материала и его точной идентификации. Титанат железа, псевдобрукит – минерал, обладающий орторомбической структурой и не ухудшающий качество пигмента, обладает коричневым или красновато-коричневым цветом, термостойкостью до 1200 °С; влияние минерала основывалось только в небольшом снижении плотности пигмента, так его плотность составляет 4400 кг/м3. Внешний облик кристаллов α-Fe 2 O 3 – скопления сферических частиц (сферолиты) размером около 0,09 мкм обеспечивает желтовато-красный (yellow-red) оттенок пигмента, несколько меньшую красящую способ-
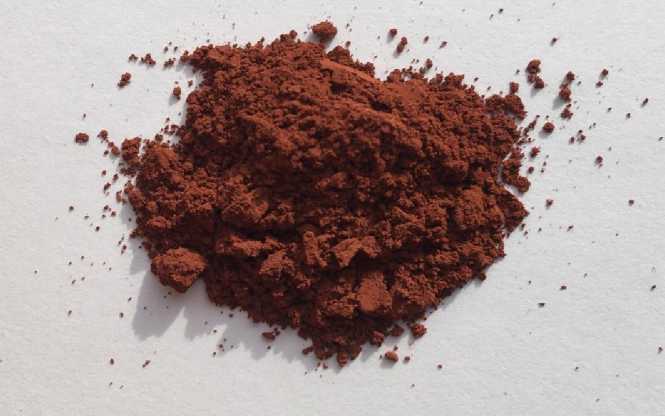
Рис. 5. Красный железооксидный пигмент на основе сталеплавильного шлака
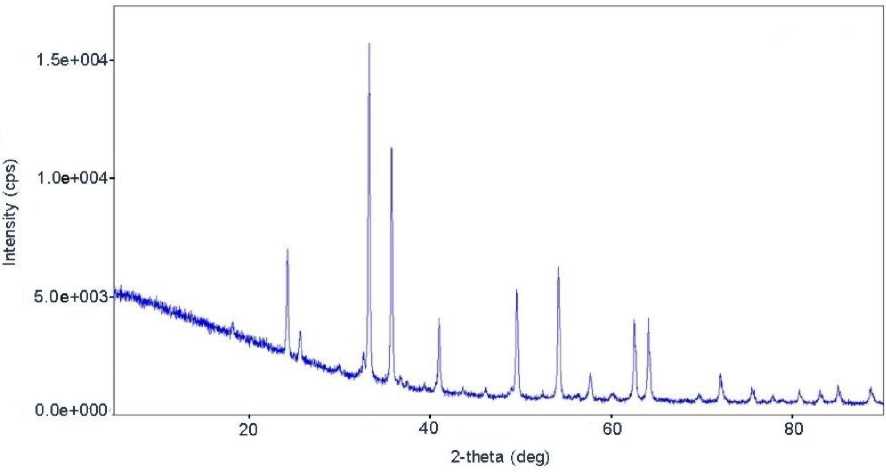
Рис. 6. Рентгенограмма красного железооксидного пигмента
ность, чем у пигментов с размером частиц 0,17 мкм, но высокую дисперсность [14, 17]. Микрофотографии пигмента представлены на рис. 7.
Проведенная ЭДС показала, что общее содержание железаFeв образце составляет 53,05 % (табл. 4). Помимо этого установлено, что входящий в состав шлака фосфорный ангидрид P2O5, вводимый в расплав для его стабилизации на стадии шлакообразования в количестве до 1 %, является «встроенной» добавкой-минерализатором, препятствующей спеканию кристаллов пигмента при прокаливании, способствующей устойчивости поверхностного слоя и дисперсионного состава получаемого пигмента [7, 15]. Прочие элементы, по всей видимости, образуют твердые растворы с основной фазой.
Анализируя поэлементный состав осадка, образовавшегося в ходе синтеза пигмента, остаточное содержание железа составляло 0,6 %, что в отношении к исходному железу имело значение в 3 %, а отношение кальция и магния в пигменте к исходному в сырье – 0,7 и 3 % соответственно. Следовательно, степень извлечения по данному процессу железа – 97 %, кальция – 99,3 % и магния – 97 %, что доказало его эффективность.
Основные свойства пигмента как красителя весьма высоки, превосходят требования ГОСТ 8135-74 «Сурик железный. Технические условия». По своим характеристикам пигмент приближается к пигментам высочайшего качества европейского уровня (минимальное содержание основного оксида – 94 % [14]) (табл. 5).
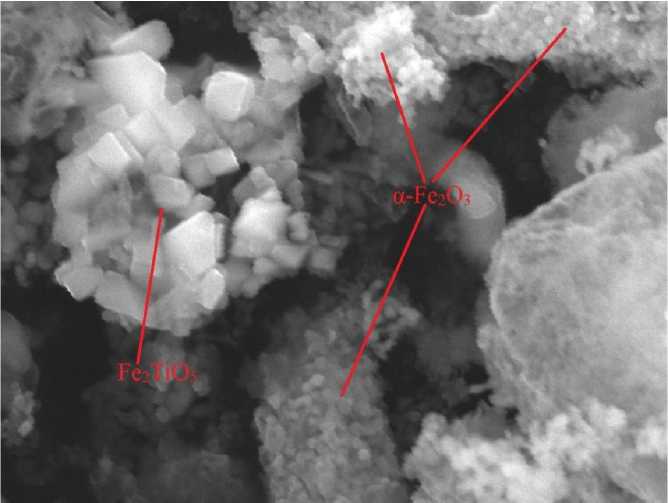
а)
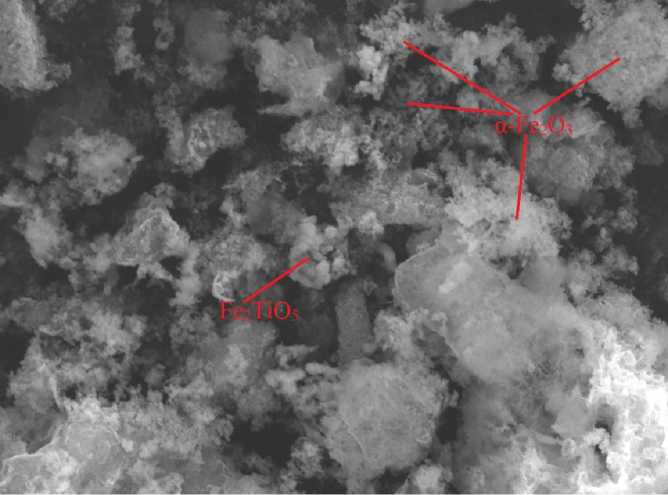
б)
Рис. 7. Микрофотографии пигмента, сделанные с помощью СЭМ: а – увеличение 20000 крат; б – увеличение 5000 крат
Поэлементный состав пигмента по данным ЭДС
Таблица 4
Массовые доли |
O |
Mg |
Al |
Si |
P |
S |
Ca |
элементов, % |
35,45 |
0,1 |
0,34 |
6,61 |
0,73 |
0,06 |
0,21 |
Массовые доли |
Ti |
V |
Cr |
Мn |
Fe |
Сумма |
|
элементов, % |
2,19 |
1,02 |
0,2 |
0,04 |
53,05 |
100 |
Таблица 5
Свойства красного железооксидного пигмента на основе сталеплавильного шлака
Содержание оксида железа α-Fe 2 O 3 , % |
93–95 |
Цвет |
красный |
Форма частиц |
сферолиты |
Площадь удельной поверхности, см2/г |
более 15000 |
рН водной суспензии |
5–6 |
Маслоемкость, г/100 г |
22 |
Укрывистость, г/м2 |
7,8 |
Плотность, кг/м3 |
4980 |
Щелочестойкость |
стоек |
Снижение укрывистости, равно как и снижение маслоемкости, объясняется примесью более крупных частиц псевдобрукитаи несколько низким содержанием железа (по сравнению с эталонными образцами) в пигменте; последний стоек в растворе NaOH 5%-ной концентрации, изменений в свойствах после данного испытания не выявлено. Масляная краска на основе данного пигмента представлена на рис. 8.
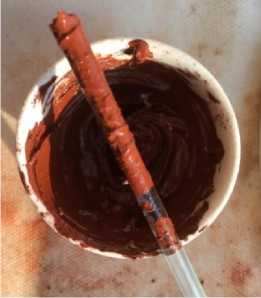
Рис. 8. Густотертая красная краска с применением синтезированного пигмента
Выводы
-
1. Продемонстрирована возможность получения высококачественного красного железооксидного пигмента на основе сталеплавильного шлака с содержанием α-Fe 2 O 3 93–95 % с эффективной утилизацией последнего.
-
2. Предложенный способ синтеза пигмента показал свою высокую результативность, о чем свидетельствовало низкое содержание нежелательных примесей в конечном продукте; некоторые включения в исходном сырье – фосфорный ангидрид P 2 O 5 – оказывали положительное воздействие на ход синтеза пигмента.
-
3. Практикой доказано теоретическое предположение о синтезе железооксидного пигмента с применением в качестве основного сырьевого компонента сталеплавильного шлака.
-
4. Красный железооксидный пигмент может быть пригоден для производства лакокрасочных материалов, керамики, декоративных разновидностей бетонов и растворов и пр.
-
5. Образовавшиеся в ходе цикла реакций побочные продукты – комплексный раствор ацетатов кальция, натрия и магния, а также не растворившийся в кислотах осадок, состоявший преимущественно из диоксида кремния, – могут быть применены в технологии бетона, как противоморозная и минеральная добавки соответственно.
Список литературы Синтез красного железооксидного пигмента на основе конвертерного сталеплавильного шлака для строительной индустрии
- Saiful Quddus, Lufor Rahman, Juliya Kha-man, Bristy Biswas, Nahid Sarmin, Samina Ahmed, Tahuran Neger. [Synthesis and Characterization of Pigment Grade Red Iron Oxide from Mill Scale]. International Research Journal of Pure and Applied Chemistry, Dhaka, Bangladesh, 2018, vol. 16(4), pp. 1-9. DOI: 10.9734/IRJPAC/2018/42935.
- Bo Liu, Shen-gen Zhang, De-an Pan, Chein-chi Chang. [Synthesis and Characterization of Micaceous Iron Oxide Pigment from Oily Cold Rolling Mill Sludge]. The Tenth International Conference on waste Management and Technology, Beijing, China, 2016, vol. 31, pp. 653-661. DOI: 10.1016/j.proenv.2016.02.121.
- Streltsova T.P., Lesovik V.S., Frolova M.A., Perkova M.V., Belikov D.A. [Natural Iron Oxide Pigments for the Construction Industry]. World Applied Sciences Journal, Belgorod, 2013, pp. 1-9. DOI: 10.5829/idosi.wasj.2013.25.02.7051.
- Wang Hongmin, Liu Manman. [Application and Progress of Chemical Iron Sludge]. Journal of Chemical and Pharmaceutical Research, Cangzhou, China, 2016, vol. 8(7), pp. 98-103.
- Zhenguo Chen, Xiaojun Wang, Qilong Ge, Guanchao Guo. [Iron Oxide Wastewater Treatment and Recycling of Iron-Containing Sludge]. Journal of Cleaner Production, Guangzhou, China, 2015, vol. 87, pp. 558-566. DOI: 10.1016/j.jclepro.2014.10.057.
- Irem Zeynep Yildirim, Monica Prezzi. [Chemical, Mineralogical and Morphological Properties of Steel Slag]. Advances in Civil Engineering, 2011, pp. 1-13. DOI: 10.1155/2011/463638.
- Netinger Ivanka G., Bansode Samtinjay, Barisic Ivana, Fucic Aleksandra [Characteristics and Uses of Steel Slag in Building Construction. Scientific Book]. Elsevier-Springer, Zagreb, Croatia, 2016. 179 p.
- Zhu G., Hao Y., Xia C., Zhang Y., Hu T., Sun S. [Study on Cementitious Properties of Steel Slag]. Journal of Mining and Metallurgy, section B: Metallurgy, Beijing, China, 2013, vol. 49(2), pp. 217224. DOI: 10.2298/JMMB120810006Z.
- Wieslaw Kurdowski [Cement and Concrete Chemistry. Scientific book]. Krakow, Poland, Springer Science & Business Publ., 2014. 700 p.
- Epikhin A.N., Krylova A.V. [Preparation of Iron Oxide Pigments for Mineral Paints from Solid Iron-Containing Waste]. Russian Journal of Applied Chemistry, Moscow, Russia, 2003, vol. 76, no. 1, pp. 20-22. DOI: 10.1023/A:1023371228302.
- Cui Yuyuan, Jiang Maofa, Shi Peiyang, Liu Chengjun. [Experiment Research on Preparation Pigment Type Magnetic Iron Oxide Powder Utilizing Magnetic Separated Slag]. Advanced Materials Research, Shen Yang, China, 2013, vol. 683, pp. 595598. DOI: 10.4028/www.scientific.net/AMR.683.595.
- Camille Crouzet, Fabrice Brunet, German Montes-Hernandez, Nadir Recham, Nathaniel Findling, Jean-Henry Farrasse, Bruno Goffe. [Hydrothermal Valorization of Steel Slag. Part I: Coupled H2 Production and CO2 Sequestration]. Frontiers in Energy Research, Grenoble-Amiens-Marseille, France, 2017. pp. 1-12. DOI: 10.3389/fenrg.2017.00029.
- Crouzet Camille, Brunet Fabrice, Montes-Hernandez German, Recham Nadir , Auzende AnneLine, Findling Nathaniel, Magnin Valerie, Farrasse Jean-Henry, Goffe Bruno. [Hydrothermal Valorization of Steel Slag - Part II: Hydrogen and Nano-Magnetite Production]. Frontiers in Energy Research, Grenoble-Amiens-Marseille, France, 2017, pp. 1-15. DOI: 10.3389/feart.2017.00086.
- Buxbaum G., Pfaff G. [Industrial Inorganic Pigments. Scientific Book]. John Wiley & Sons Publ., Krefeld-Darmstadt, Germany, 2006. 315 p.
- Клещев Д.Г., Шейнкман А.И., Плетнев Р.Н. Влияние среды на фазовые и химические превращения в дисперсных системах: моногр. Изд-во Уральского отделения АН СССР, Свердловск, СССР, 1990. 248 с. [Kleshchev D.G., Sheynkman A.I., Pletnev R.N. Vliyaniye sredy na fazovyye i khimicheskiye prevrashcheniya v dispers-nykh sistemakh. [The Impact of the Medium on Phase and Chemical Transformations in Disperse Systems]. Sverdlovsk, Izd. Ural'skogo otdeleniya AN SSSR Publ., 1990. 248 p.]
- Woon H.S., Nicklane K., Ewe L.S., Lim K.P., Ismail I., Tan C.Y. [Synthesis and Characterization of Inorganic Color Pigment from Spent Acid]. 3rd International Science, Technology & Engineering Conference (ISTEC), Material Chemistry, Kajang-Serdang-Kualu Lumpur, Malaysia, 2018, vol. 21, iss. 9, pp. 2255-2260. DOI: 10.1063/1.5066986.
- Dondi Michele, Matteucci Francesco, Cruciani Giuseppe, Gasparotto Giorgio, Tobaldi David M. [Pseudobrookite Ceramic Pigments: Structural, Optical and Technological Properties]. Solid State Sciences, Faenza-Ferrara-Bologna, Italy, 2007, vol. 9, pp. 362369. DOI: 10.1016/j. solidstatesciences.2007.03.001.