Снижение виброакустического излучения при фрезерном гравированиии хрупких материалов
Автор: Мезенцева Инна Леонидовна
Журнал: Горные науки и технологии @gornye-nauki-tekhnologii
Статья в выпуске: 1, 2010 года.
Бесплатный доступ
Исследованы возможности снижения уровня виброакустического излучения при фрезерном гравировании хрупких материалов посредством учета динамических характеристик упругой системы станка при выборе режимов обработки. Это позволяет уменьшить шумовое загрязнение и улучшить экологическую обстановку в камнеобрабатывающем цехе.
Фрезерное гравирование, колебания, виброакустическое излучение, частотные характеристики, шумовое загрязнение
Короткий адрес: https://sciup.org/140215081
IDR: 140215081
Текст научной статьи Снижение виброакустического излучения при фрезерном гравированиии хрупких материалов
Автоматизированное фрезерное гравирование на твердых хрупких материалах (мрамор, гранит, цветные камни) с использованием оборудования с ЧПУ является прогрессивной технологией, получающей все большее распространение [3]. Высокая степень автоматизации процесса, обеспечивающая компьютерное управление относительным движением инструмента и заготовки и защитную изоляцию зоны обработки от окружающей среды, не требует постоянного присутствия оператора около станка. Оператор находится на удалении от зоны обработки, осуществляя периодическое наблюдение, и проводит смену инструмента или заготовки при выключенном станке. Это существенно улучшает условия труда. Однако, при работе цеха по изготовлению барельефов, мозаики и других резных изделий из камня, где установлено значительное количество работающих станков, операторы вынуждены проводить операции по обслуживанию процесса обработки в условиях значительного шумового загрязнения окружающей среды, что делает актуальной исследования по снижению уровня этого загрязнения.
Причиной шумового загрязнения является виброакустическое излучение, происходящее вследствие колебаний узлов и агрегатов станка, заготовки, инструмента в процессе механической обработки, а также на холостом ходу. [2]. При контурном и объемном фрезеровании колебания упругой системы станка также существенно сказываются на точности контура и качестве поверхности.
Виброакустическое излучение особенно нарастает при сoвпaдении чaстoты возмущающего воздействия с собственной чaстoтoй кoлебaний одного из упругих звеньев станка, что приводит к появлению резонансных колебаний. Для исключения этих явлений необходимо провести определение и анализ характеристик упругой системы станка с целью выбора таких режимов и параметров обработки, которые располагаются вне зоны резонансных колебаний.
Экспериментальное определение частотных характеристик упругой системы проводилось для фрезерно-гравировального станка «График-3КС». Использовался метод импульсного (ударного) воздействия на элементы упругой системы, измерение отклика системы с последующим анализом испытаний [1].
Состав виброизмерительного комплекса аппаратуры приведен на рис 1. В качестве датчиков вибрации используются пьезоакселерометры (1 и 2). Электрические сигналы, пропорциональные ускорению колеблющегося объекта, поступают на предусилители (3 и 4). Усилители (5 и 6) масштабируют уровень сигнала. Аналогово-цифровой преобразователь (АЦП) (11) принимает аналоговый сигнал с двух каналов и в соответствии с настройками программы управления производит его оцифровку. Сбор цифровых данных с АЦП и общее управление измерениями обеспечивается специализированным ПО, позволяющим визуализировать и регистрировать данные. Для измерения частоты вращения шпинделя фрезерной головки используется фотоэлектрический датчик оборотов (7). Сигнал с датчика через усилитель (8) передается на АЦП и затем на ЭВМ. Для создания импульсного воздействия применятся ударный молоток (9), оснащенный пьезоэлектрическим динамометрическим датчиком. Сигнал с датчика через усилитель (10) передается на АЦП и затем на ЭВМ.
Предусилители Усилители (5,6)
Датчики вибрации -пьезоэлектрические
(1.2)
Датчик оборотов фотоэлектрический (7)
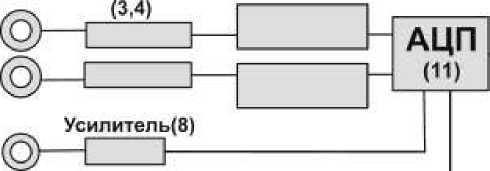
ПЭВМ спец.ПО

Рис 1. Схема виброизмерительного комплекса аппаратуры
При испытаниях на неработающем станке методом импульсного воздействия варьировалось расположение вибродатчиков (по различным осям и на различных элементах конструкции станка), а также направление и точки приложения ударного усилия.
Построение частотных характеристик методом импульсного возбуждения включало следующее [1].
К испытуемому объекту с помощью динамометрического молотка прикладывают серию импульсных воздействий. Сигналы опрашиваются с частотой 20 кГц. Каждый вибросигнал состоит из нескольких переходных процессов, соответствующих серии импульсов. Промежутки между переходными процессами совпадают с паузами между ударами.
Совокупность трех переходных процессов, соответствующих одному и тому же удару, образует выборку. Таким образом, в выборке исключаются промежутки между ударами. Для преобразования вибрационного сигнала из временной области в частотную каждая выборка подвергается быстрому преобразованию Фурье, определяются спектры и частотные характеристики.
Основной интерес в данном случае представляет амплитудночастотная характеристика (АЧХ), показывающая зависимость отношения амплитуды выходной координаты к амплитуде входного воздействия от частоты. Пример такой характеристики, полученной при закреплении акселерометра на корпусе фрезерной головки вдоль оси oX и приложении возбуждающего усилия к шпинделю в направлении той же оси дан на рис. 2.
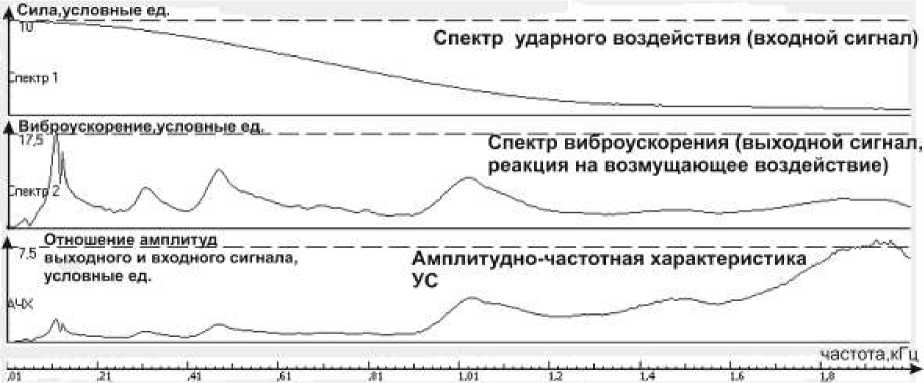
Рис 2. Пример АЧХ упругой системы фрезерно-гравировального станка
На графике АЧХ видны всплески амплитуды, которые соответствуют собственным частотам колебаний системы. В частности, по АЧХ на рис. 2 можно выявить собственные частоты колебаний шпинделя вдоль оси oX . Таким образом, построены графики АЧХ различных элементов упругой системы станка и определены их собственные частоты колебаний.
Следующая серия испытаний включала анализ спектров колебаний холостого хода и при резании.
При испытаниях на холостом ходу определялись радиальные колебания шпинделя фрезерной головки на различных частотах вращения.
При испытаниях в процессе резания определялись радиальные колебания шпинделя фрезерной головки и колебания стола станка (и соответственно, заготовки) в процессе резания концевым алмазным инструментом белого мрамора сорта Коелгинский.
На рис 3. приведен пример спектра виброускорения, зарегистрированного на фрезерной головке станка вдоль оси oX при резании мрамора.
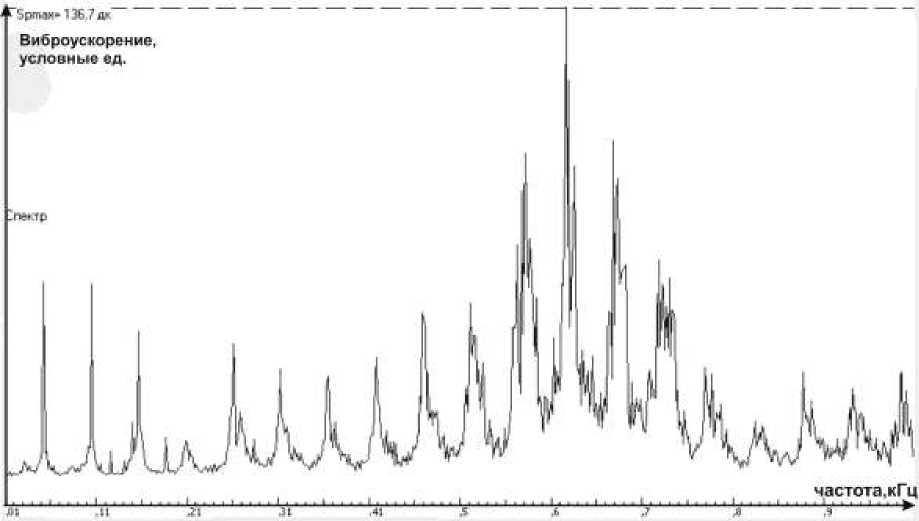
Рис 3. Пример спектра виброускорения на шпинделе фрезерногравировального станка
В полученных спектрах виброускорения при холостом ходе и при резании определялось, какие частотные составляющие доминируют и на сколько велики амплитуды колебаний на собственных частотах.
Проведенные исследования показали, что выявленные собственные частоты колебаний элементов упругой системы в ряде случаев значительно проявляются в спектрах холостого хода и при резании, что может привести к нежелательному возникновению резонансных колебаний.
Существенное увеличение амплитуды колебаний на собственных частотах связано, в том числе, с определенной скоростью вращения шпинделя.
Выявление собственных частот колебаний элементов упругой системы станка позволяет выбрать параметры обработки, в частности – частоты вращения шпинделя, таким образом, чтобы последние не попадали в одну из собственных частот упругой системы.
Проведенные исследования позволили выработать рекомендации по назначению режимов фрезерного гравирования, обеспечивающих снижение уровня виброакустического излучения при обработке художественных изделий из твердых хрупких материалов. Применение рекомендаций особенно эффективно при большом количестве работающего оборудования и позволяет улучшить экологическую обстановку в камнеобрабатывающем цехе.
Список литературы Снижение виброакустического излучения при фрезерном гравированиии хрупких материалов
- Автоматизированные динамические испытания станков: Методич. реком./Сост. Кочинев Н.А. -М.: ЭНИМС, 1990. -46 с.
- Козочкин М.П. Виброакустическая диагностика технологических процессов. -М.: Изд-во ИКФ «Каталог», 2005. -196 с.
- Миков И.Н., Мезенцева И.Л. Экспериментальное определение отдельных параметров обработки при объемном художественном гравировании по камню на станках с ЧПУ. -М.: Горный информационно-аналитический бюллетень, №9, 2007. -с. 263-267.